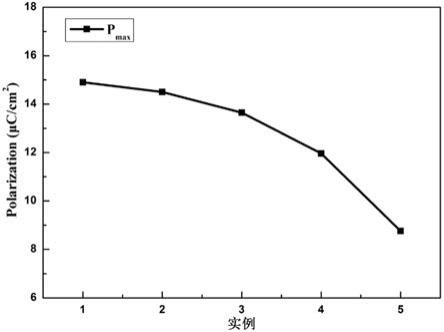
1.本发明涉及高储能密度和高储能效率电解质陶瓷材料技术领域,具体的是一种高储能密度和高储能效率的复合陶瓷材料制备方法。
背景技术:
2.固态介质电容器因其高功率密度和超快充放电速率而受到人们的高度关注。然而其储能密度往往较小,且往往易受储能效率以及热稳定性的制约。低储能效率意味着更多的电能被转化为热能,从而容易引起电容器在服役中失效。因此,设计和开发同时具有高储能密度、高效率和稳定的储能介质材料就至关重要。
3.近年来,国内外一直围绕铁电、反铁电材料的多尺度结构设计以及电学性能调控等方面,特别是针对领域内人们广泛关注的若干关键性基础问题和技术难题,开展了一系列系统性的研究工作。线性电介质材料(al2o3)具有较高的击穿场强、高的储能效率但饱和极化强度太低,导致总的能量储存密度和可释放的能量存储密度都很低,铁电材料(batio3、pbzr
x
ti
1-x
o3)虽然饱和极化强度很大,但剩余极化强度往往也很大,且击穿场强较低,导致了可释放的能量存储密度和储能效率都很小,所以线性电介质材料和铁电材料均不是理想的储能材料。弛豫铁电材料(xpb(mg
1/3
nb
2/3
)o
3-(1-x)pbtio3等)电滞回线较“瘦”,具有较高的储能效率,但是储能密度较小;反铁电材料(如pbzro3、agnbo3等)虽然放电储能密度较大,但是由于反铁电-铁电相变产生的电滞损耗大,导致储能效率低,大的电滞损耗不但浪费能源还会使器件发热,影响器件的使用寿命。
4.研究发现,弛豫铁电材料储能效率较高,但储能密度低,而反铁电材料耐压强度高,储能密度高,但储能效率低,因此制备出兼具弛豫铁电材料高储能效率和反铁电体高储能密度优点的反铁电弛豫复合陶瓷材料是未来的研究方向。
5.华中科技大学的范鹏远首先制备出弛豫铁电相0.94(na
0.82k0.18
)
1/2
bi
1/2
tio3–
0.06fenbo4(nkbt
–
fn)和反铁电相0.96nanbo3–
0.04cazro3(nn
–
cz),再将两者复合,制备出高性能弛豫/反铁电复合材料,其储能密度达到2.85j/cm
3 ,储能效率为80%。合肥工业大学左如忠教授采用弛豫铁电相(bi
0.5
na
0.5
)tio3和反铁电nanbo3制备出(bnt-nn)弛豫反铁电陶瓷材料,其电储能密度值为7.02 j/cm3,储能效率η为85%。
6.研究发现采用传统固相合成技术将弛豫铁电和反铁电材料复合,能够通过局域随机场来调控反铁电陶瓷的电畴尺寸,不仅能够有效提高反铁电-铁电相变的驱动电场,提高充电储能密度,还可以降低充放电过程中的极化滞后性而显著提高储能效率。
7.但在固相合成过程中,弛豫铁电材料和反铁电材料复合后,如果直接将它们进行简单的复合(混合、成型、烧结),在高温下不可避免地会出现严重的两相间扩散行为,导致不能保持原有的弛豫铁电材料和反铁电材料本身的特性,并且由于反应产生杂相导致储能效率下降,同时两相反应容易导致耐压强度降低,以致无法达成实验设计的预期目标。
8.在此基础上,本发明提供一种高储能密度和高储能效率的复合陶瓷材料制备方法来解决此问题。
技术实现要素:
9.针对上述情况,为克服现有技术之缺陷,本发明提供一种高储能密度和高储能效率的复合陶瓷材料制备方法,有效解决了现有反铁电材料和弛豫铁电材料在高温合成时,容易造成两相反应产生杂相,使复合后储能效率下降,耐压强度降低的问题。
10.一种高储能密度和高储能效率的复合陶瓷材料制备方法,其特征在于,包括以下步骤:1)、分别将pbo、hfo2和sno2按照化学式pb(hf
0.45
sn
0.55
)
0.995
o3(phs)进行配料后,球磨混合及烘干后形成phs粉体;2)、分别将bi2o3、na2co3、tio2、batio3、pr2o3按照化学式0.93bi
0.5
na
0.5
tio
3-0.07batio
3-1.3%pr(bnt-bt-p)进行配料后,球磨混合及烘干后形成bnt-bt-p粉体;3)、分别将phs粉体和bnt-bt-p粉体放入坩埚,在空气气氛中进行预烧;4)、将bnt-bt-p预烧粉体倒入球磨罐球磨后烘干,过筛得到bnt-bt-p预烧细粉体;5)、将异丙醇铝溶入乙二醇中,采用磁力搅拌器搅拌,再与乙酰丙酮进行混合球磨,最后再加入乙酸,形成氧化铝透明溶胶;6)、将bnt-bt-p预烧细粉体与氧化铝溶胶按照0.5wt%al2o3 99.5wt%bnt-bt-p比例进行混合球磨,加热烘干,再在高温下热处理得到氧化铝包覆的bnt-bt-p粉体(bnt-bt-p@al2o3);7)、将phs粉体和bnt-bt-p@al2o3粉体倒入球磨罐球磨后烘干;8)、将已烘干的phs粉体和bnt-bt-p@al2o3粉体进行造粒过筛后压制成圆片,并将圆片烧结以得到复合陶瓷材料。
11.优选的,在所述步骤1)、2)、4)、6)、7)中,球磨是在无水乙醇下进行,烘干温度为80℃,步骤1)、2)、4)和7)中,球磨时间为4h,步骤6)中,球磨时间为36h。
12.优选的,所述反铁电相pb(hf
0.45
sn
0.55
)
0.995
o3(phs)粉体是由pbo、hfo2和sno2按照化学式pb(hf
0.45
sn
0.55
)
0.995
o3进行配料。
13.优选的,在所述步骤3)中,预烧要求是pb(hf
0.45
sn
0.55
)
0.995
o3粉体和0.93bi
0.5
na
0.5
tio
3-0.07batio
3-1.3%pr粉体在空气中850℃保温 3 h。
14.优选的,在所述步骤5)中,搅拌温度均为80℃,搅拌时间为30 min。
15.优选的,在所述步骤6)中,加热烘干温度为60℃,保温时间4 h。
16.优选的,在所述步骤6)中,热处理温度为600℃,保温时间为2 h。
17.优选的,在所述步骤8)中,圆片压制的压力为100~150mpa。
18.优选的,在所述步骤8)中,圆片为直径10mm且厚度约为1mm的圆片生胚。
19.优选的,在所述步骤8)中,烧结要求为在空气中1180℃~1220℃烧结3h,烧结过程中升温速率及降温速率均为3~5℃/min。
20.本发明与现有技术相比具备如下技术效果。
21.1、通过采用氧化铝对弛豫铁电材料0.93bi
0.5
na
0.5
tio
3-0.07batio
3-1.3%pr粉体进行包覆后再与反铁电pb(hf
0.45
sn
0.55
)
0.995
o3粉体进行混合,利用氧化铝的绝缘性,可大幅度提高耐压强度,从而增大储能密度。
22.2、通过采用氧化铝对弛豫铁电材料0.93bi
0.5
na
0.5
tio
3-0.07batio
3-1.3%pr粉体进行包覆后再与反铁电pb(hf
0.45
sn
0.55
)
0.995
o3粉体进行混合,在高温合成时可有效降低反铁电
材料与弛豫材料之间的反应,使复合材料兼具铁电弛豫体和反铁电体的优点,且在室温下具有较高的储能效率。
附图说明
23.图1为本发明包覆了氧化铝的弛豫铁电材料0.93bi
0.5
na
0.5
tio
3-0.07batio
3-1.3%pr(bnt-bt-p@al2o3)粉体透射电镜图。
24.图2为本发明包覆了氧化铝的弛豫铁电材料0.93bi
0.5
na
0.5
tio
3-0.07batio
3-1.3%pr(bnt-bt-p@al2o3)粉体的示意图。
25.图3为本发明实例三复合陶瓷材料的表面形貌图。
26.图4为本发明实例一、二、三、四和五的电滞回线图谱。
27.图5为本发明实例一、二、三、四和五的最大极化强度。
具体实施方式
28.有关本发明的前述及其他技术内容、特点与功效,在以下配合参考附图1至图5对实施例的详细说明中,将可清楚的呈现。以下实施例中所提到的内容,均是以说明书附图为参考。
29.下面将参照附图描述本发明的各示例性的实施例。
30.本发明公开了一种高储能密度和高储能效率的复合陶瓷材料制备方法,该复合陶瓷由反铁电相pb(hf
0.45
sn
0.55
)
0.995
o3(phs)粉体和包覆了氧化铝的弛豫铁电相0.93bi
0.5
na
0.5
tio
3-0.07batio
3-1.3%pr(bnt-bt-p)粉体按照化学式所制成,其中,反铁电相pb(hf
0.45
sn
0.55
)
0.995
o3(phs)粉体是由pbo、hfo2和sno2按照化学式pb(hf
0.45
sn
0.55
)
0.995
o3进行配料后混合而成,所述包覆了氧化铝的弛豫铁电相0.93bi
0.5
na
0.5
tio
3-0.07batio
3-1.3%pr (bnt-bt-p)粉体,首先是由bi2o3、na2co3、tio2、batio3、pr2o3按照化学式0.93bi
0.5
na
0.5
tio
3-0.07batio
3-1.3%pr进行配料混合而成,再在表面进行氧化铝的包覆。最后将反铁电相phs粉体和包覆了氧化铝的弛豫铁电相bnt-bt-p@al2o3粉体进行混合,其中包覆了氧化铝的弛豫铁电相bnt-bt-p@al2o3粉体占材料总质量的10wt%-30wt%。
31.其中包覆了氧化铝的弛豫铁电相0.93bi
0.5
na
0.5
tio
3-0.07batio
3-1.3%pr (bnt-bt-p@al2o3)粉体,按照0.5wt%al2o3 99.5wt%0.93bi
0.5
na
0.5
tio
3-0.07batio
3-1.3%pr比例进行混合,氧化铝厚度约为5nm。氧化铝的包覆,能够有效增加耐压强度,同时降低两相高温时的反应扩散,保障复合材料的高储能密度及高储能效率。
32.对于复合陶瓷材料的制备方法,包括以下制备步骤:步骤一,分别将pbo、hfo2和sno2按照化学式pb(hf
0.45
sn
0.55
)
0.995
o3进行配料,将配料得到的混合物在无水乙醇介质下进行球磨混合4h得到料浆,再将料浆放入烘箱内在80℃下烘干,过60目钢筛,最后形成pb(hf
0.45
sn
0.55
)
0.995
o3粉体。
33.步骤二,分别将bi2o3、na2co3、tio2、batio3、pr2o3按照化学式0.93bi
0.5
na
0.5
tio
3-0.07batio
3-1.3%pr进行配料,将配料得到的混合物在无水乙醇介质下进行球磨混合4h得到料浆,再将料浆放入烘箱内在80℃下烘干,过60目钢筛,最后形成0.93bi
0.5
na
0.5
tio
3-0.07batio
3-1.3%pr粉体。
34.步骤三,分别将步骤一和步骤二中所得到的pb(hf
0.45
sn
0.55
)
0.995
o3粉体和
0.93bi
0.5
na
0.5
tio
3-0.07batio
3-1.3%pr粉体放入坩埚,在空气气氛中进行预烧,具体条件为850℃保温3h。
35.步骤四,将步骤三中得到的0.93bi
0.5
na
0.5
tio
3-0.07batio
3-1.3%pr预烧粉体在无水乙醇介质下进行球磨混合4h得到料浆,再将料浆放入烘箱内在80℃下烘干,过60目钢筛,最后形成0.93bi
0.5
na
0.5
tio
3-0.07batio
3-1.3%pr预烧细粉体。
36.步骤五,将0.02mol异丙醇铝溶解进50ml乙二醇中,采用磁力搅拌器在80℃下搅拌30min,再与0.02mol乙酰丙酮进行混合球磨30min,最后在80℃下,加入10ml乙酸,形成氧化铝透明溶胶。
37.步骤六,将步骤四中得到的0.93bi
0.5
na
0.5
tio
3-0.07batio
3-1.3%pr预烧细粉体与步骤五中的氧化铝透明溶胶按照0.5wt%al2o3 99.5wt%0.93bi
0.5
na
0.5
tio
3-0.07batio
3-1.3%pr比例进行球磨混合36h得到料浆,再放入烘箱内在80℃下烘干,过60目钢筛,最后再放入坩埚,在空气气氛中进行预烧,具体条件为600℃保温2h,得到氧化铝包覆的0.93bi
0.5
na
0.5
tio3‑ꢀ
0.07batio
3-1.3%pr粉体(bnt-bt-p@al2o3);步骤七,将步骤三中的pb(hf
0.45
sn
0.55
)
0.995
o3预烧粉体和步骤六中氧化铝包覆的bnt-bt-p@al2o3粉体以不同的质量比混合,如1/9,2/8,3/7等,倒入装有无水乙醇的球磨罐中球磨4h后放入烘箱内在80℃下烘干;步骤八,将已烘干的pb(hf
0.45
sn
0.55
)
0.995
o3粉体和bnt-bt-p@al2o3混合粉体进行造粒烧结,具体为,添加pva作为用于造粒的粘合剂,并通过60目的钢筛。之后,在100~150mpa的压力下压制为直径10mm且厚度约1mm的圆片生胚。所压制的圆片在1180~1220℃烧结3h。烧结过程中的升温速率和降温速率均为3~5℃/min,之后经过打磨和表面抛光后刷银电极,最后得到复合陶瓷材料。
38.具体实施例一。
39.本实施例为制备单相反铁电pb(hf
0.45
sn
0.55
)
0.995
o3材料,包括以下步骤:(1)使用pbo、hfo2和sno2为原料,按照化学式pb(hf
0.45
sn
0.55
)
0.995
o3进行配料;(2)使用无水乙醇为介质,将上一步得到的混合物球磨4h后在80℃下烘干;(3)将烘干后的混合物粉体进行预烧,具体的操作为将混合物粉体在空气中于850℃煅烧3h,升降温速率为3.5℃/min,得到pb(hf
0.45
sn
0.55
)
0.995
o3预烧粉体;(4)将pb(hf
0.45
sn
0.55
)
0.995
o3预烧粉体干燥后,进行造粒、压片和烧结。具体步骤为,添加pva作为用于造粒的粘合剂,并通过60目的筛子。然后在100mpa的压力下压制出直径为10mm且厚度约1mm的柱状生胚。压制的生胚在常压空气气氛中于1200℃高温烧结3h,升降温速率为3.5℃/min,得到致密的pb(hf
0.45
sn
0.55
)
0.995
o3单相反铁电陶瓷。将烧结后的陶瓷用平面磨床磨平,然后手工抛光,并双面刷上银电极后在550℃空气中烧银。
40.具体实施例二。
41.本实施例为制备pb(hf
0.45
sn
0.55
)
0.995
o3(phs)含量为90wt%,0.93bi
0.5
na
0.5
tio
3-0.07batio
3-1.3%pr(未包覆al2o3)含量为10wt%的复合陶瓷材料,包括以下步骤:(1)使用pbo、hfo2和sno2为原料,按照化学式pb(hf
0.45
sn
0.55
)
0.995
o3进行配料;使用无水乙醇为介质,将上一步得到的混合物球磨4h后在80℃下烘干;将烘干后的混合物粉体进行预烧,具体的操作为将混合物粉体在空气中于850℃煅烧3h,升降温速率为3.5℃/min,得到pb(hf
0.45
sn
0.55
)
0.995
o3预烧粉体;
(2)使用bi2o3、na2co3、tio2、batio3、pr2o3为原料,按照化学式0.93bi
0.5
na
0.5
tio
3-0.07batio
3-1.3%pr进行配料;使用无水乙醇为介质,将上一步得到的混合物球磨4h后在80℃下烘干;将烘干后的混合物粉体进行预烧,具体的操作为将混合物粉体在空气中于850℃煅烧3h,升降温速率为3.5℃/min,得到0.93bi
0.5
na
0.5
tio
3-0.07batio
3-1.3%pr预烧粉体;(3)将pb(hf
0.45
sn
0.55
)
0.995
o3粉体和0.93bi
0.5
na
0.5
tio
3-0.07batio
3-1.3%pr粉体以90:10的质量比混合,将混合的粉体球磨4h;(4)将上述混合粉末干燥后,进行造粒、压片和烧结。具体步骤为,添加pva作为用于造粒的粘合剂,并通过60目的筛子。然后在100mpa的压力下压制出直径为10mm且厚度约1mm的柱状生胚。压制的生胚在常压空气气氛中于1200℃高温烧结3h,升降温速率为3.5℃/min,得到致密的phs/bnt-bt-p复相陶瓷。将烧结后的陶瓷用平面磨床磨平,然后手工抛光,并双面刷上银电极后在550℃空气中烧银。
42.具体实施例三。
43.本实施例为制备pb(hf
0.45
sn
0.55
)
0.995
o3(phs)含量为90wt%,0.93bi
0.5
na
0.5
tio
3-0.07batio
3-1.3%pr(包覆al2o3)含量为10wt%的复合陶瓷材料,包括以下步骤:(1)使用pbo、hfo2和sno2为原料,按照化学式pb(hf
0.45
sn
0.55
)
0.995
o3进行配料;使用无水乙醇为介质,将上一步得到的混合物球磨4h后在80℃下烘干;将烘干后的混合物粉体进行预烧,具体的操作为将混合物粉体在空气中于850℃煅烧3h,升降温速率为3.5℃/min,得到pb(hf
0.45
sn
0.55
)
0.995
o3预烧粉体;(2)使用bi2o3、na2co3、tio2、batio3、pr2o3为原料,按照化学式0.93bi
0.5
na
0.5
tio
3-0.07batio
3-1.3%pr进行配料;使用无水乙醇为介质,将上一步得到的混合物球磨4h后在80℃下烘干;将烘干后的混合物粉体进行预烧,具体的操作为将混合物粉体在空气中于850℃煅烧3h,升降温速率为3.5℃/min,得到0.93bi
0.5
na
0.5
tio
3-0.07batio
3-1.3%pr预烧粉体;(3)制备氧化铝透明溶胶,将0.02mol异丙醇铝溶解进50ml乙二醇中,采用磁力搅拌器在80℃下搅拌30分钟,再与0.02mol乙酰丙酮进行混合球磨30分钟,最后在80℃下,加入10ml乙酸,形成氧化铝透明溶胶;(4)将0.93bi
0.5
na
0.5
tio
3-0.07batio
3-1.3%pr预烧粉体与氧化铝溶胶按照0.5wt%al2o3 99.5wt%0.93bi
0.5
na
0.5
tio
3-0.07batio
3-1.3%pr比例进行球磨混合36h得到料浆,再放入烘箱内在80℃下烘干,过60目钢筛,最后再放入坩埚,在空气气氛中于600℃煅烧2h,得到氧化铝包覆的0.93bi
0.5
na
0.5
tio
3-0.07batio
3-1.3%pr粉体(bnt-bt-p@al2o3);(5)将pb(hf
0.45
sn
0.55
)
0.995
o3粉体和al2o3包覆的0.93bi
0.5
na
0.5
tio
3-0.07batio
3-1.3%pr(bnt-bt-p@al2o3)粉体以90:10的质量比混合,将混合的粉体球磨4h;(6)将上述混合粉末干燥后,进行造粒、压片和烧结。具体步骤为,添加pva作为用于造粒的粘合剂,并通过60目的筛子。然后在100mpa的压力下压制出直径为10mm且厚度约1mm的柱状生胚。压制的生胚在常压空气气氛中于1200℃高温烧结3h,升降温速率为3.5℃/min,得到致密的pb(hf
0.45
sn
0.55
)
0.995
o3/0.93bi
0.5
na
0.5
tio
3-0.07batio
3-1.3%pr@al2o3复相陶瓷。将烧结后的陶瓷用平面磨床磨平,然后手工抛光,并双面刷上银电极后在550℃空气中烧银。
44.具体实施例四。
45.本实施例于实施例三的制备方法相同,不同点在于:
pb(hf
0.45
sn
0.55
)
0.995
o3粉体和al2o3包覆的0.93bi
0.5
na
0.5
tio
3-0.07batio
3-1.3%pr(bnt-bt-p@al2o3)粉体以80:20的质量比混合。
46.具体实施例五本实施例于实施例三的制备方法相同,不同点在于:pb(hf
0.45
sn
0.55
)
0.995
o3粉体和al2o3包覆的0.93bi
0.5
na
0.5
tio
3-0.07batio
3-1.3%pr(bnt-bt-p@al2o3)粉体以70:30的质量比混合。
47.实施例三、四和五中包覆了氧化铝的弛豫铁电相0.93bi
0.5
na
0.5
tio
3-0.07batio
3-1.3%pr (bnt-bt-p@al2o3)粉体透射电镜图和结构示意图如图1和图2所示。由图1可以看出,氧化铝很好的包覆在bnt-bt-p粉体表面,形成图2类似的核壳结构。在两相复合烧结过程中,氧化铝能够有效削弱反铁电和弛豫铁电两相之间的反应,保留反铁电和弛豫铁电两相的优势,使复合材料兼具弛豫铁电体高储能效率和反铁电体高储能密度优点。
48.实施例四中复合陶瓷材料的表面微观形貌如图3所示,其中大颗粒为pb(hf
0.45
sn
0.55
)
0.995
o3,小颗粒为包覆了氧化铝的弛豫铁电相0.93bi
0.5
na
0.5
tio
3-0.07batio
3-1.3%pr (bnt-bt-p@al2o3),从图中可以清楚的看出,复合陶瓷中均具有致密的微观结构,其中复合陶瓷存在明显的两相结构。bnt-bt-p@al2o3颗粒均匀分布在基体中,一方面,使复合材料兼具弛豫铁电体高储能效率和反铁电体高储能密度优点,另一方面利用al2o3的高击穿场强,对电场分布产生扭曲,承担较高的局域电场,有助于复合陶瓷获得高的耐压强度,从而获得高的储能密度。
49.对实施例一至五进行铁电性能测试(测试温度为室温,测试频率为100hz,每组样品至少测试10次以保证结果的可靠性)。其结果如图4所示,图5为实例一、二、三、四和五的最大极化强度。
50.从图4可以看出,实施例一为明显的反铁电相,具有较大的储能密度,中等的储能效率。
51.实施例二为pb(hf
0.45
sn
0.55
)
0.995
o3(phs)含量为90wt%,0.93bi
0.5
na
0.5
tio
3-0.07batio
3-1.3%pr(未包覆al2o3)含量为10wt%的复合陶瓷材料,由图中可以看出,击穿场强由单相反铁电材料的158kv/cm降低到120kv/cm,同时电滞回线反铁电的标志明显消失,说明高温合成时反铁电和弛豫铁电材料两相之间发生反应,产生了杂相,从而降低了击穿场强,同时影响了性能。
52.实施例三、四、五均为pb(hf
0.45
sn
0.55
)
0.995
o3粉体和al2o3包覆的0.93bi
0.5
na
0.5
tio
3-0.07batio
3-1.3%pr(bnt-bt-p@al2o3)粉体复合的陶瓷材料,由图4可以看出耐压强度明显得到提高,且电滞回线变细,说明高温下al2o3的包覆能够有效削弱两相反应,提高击穿场强,同时提高储能特性。由图5可以看出,随着bnt-bt-p质量分数的增加,极化强度逐渐下降。
53.复合陶瓷的储能密度和储能效率可以通过极化-电场(p-e)曲线计算得到。其结果如下:实施例一至五所制备得到复合陶瓷材料的储能性能。
54.由表格可以看出,复合陶瓷在制备时,相比实施例二中未包覆氧化铝的复合陶瓷,包覆氧化铝后phs/bnt-bt-p@al2o3的击穿场强提高了将近2倍,储能密度提高了2倍左右,并具有90%以上的储能效率,这显示出采用此方法制备的复合陶瓷材料在高性能储能电容器方面具有广阔的应用背景。实施例五中,由于bnt-bt-p@al2o3复合比例较大,导致极化强度降低,从而使复合陶瓷材料储能密度下降。
55.本发明的目的,主要针对反铁电材料和弛豫铁电材料在高温合成时,容易造成两相反应产生杂相,使复合后储能效率下降,耐压强度降低的缺点,通过在弛豫铁电材料外包覆一层氧化铝,一方面在复合时避免两相扩散反应,另一方面利用氧化铝的高耐压特性,可以同时提高复合陶瓷材料的耐压强度和储能效率。
56.本发明目的在于提高储能效率,增大耐压强度。本发明制备的储能复合材料具有较高的储能密度,较大的耐压强度,较高的储能效率,适用于固态介质电容器。
57.以上仅为本发明的较佳实施例而已,并不用于限制本发明,凡在本发明的精神和原则之内所作的任何修改、等同替换和改进等,均应包含在本发明的保护范围之内。
再多了解一些
本文用于企业家、创业者技术爱好者查询,结果仅供参考。