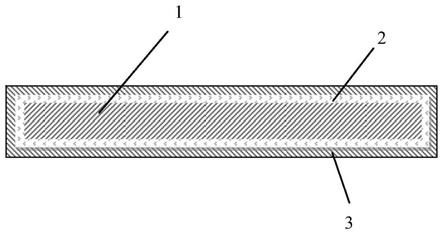
1.本发明涉及一种敷有金属钛-铜层的金刚石/铜复合材料热沉及其制备方法,属于热管理材料技术领域。
背景技术:
2.金刚石/铜复合材料作为第四代电子封装材料具有高导热、低膨胀的特性,此类材料的热导率高大于550w/mk,密度低于5.0g/cm3,是理想的散热材料,但是由于材料中含有较硬的金刚石和较软的铜相,加工后的器件表面粗糙度ra很难达到1微米以内,这大大影响后期焊料的铺展。为了改善表面粗糙度通常在金刚石/铜热沉表面化学镀镍,但是镍较硬,不易二次精磨,最主要的镍层热导率低。因此,本发明选择一种复合镀覆工艺,来解决以上难题,且希望这层金属热导率尽量高,并易于二次加工,从而可通过二次加工达到降低热沉表面粗糙度的目的。
技术实现要素:
3.针对以上存在的问题,本发明提供一种敷有金属钛-铜层的金刚石/铜复合材料热沉,该热沉可用于银铜钎焊,焊料铺展性好,焊透率高,结合强度好,充分发挥热沉的优异散热性能。
4.一种敷有金属钛-铜层的金刚石/铜复合材料热沉,包括金刚石/铜复合材料热沉,所述热沉的表面从内到外依次设置金属钛层和铜层,金属钛层和铜层的厚度在数微米至数百微米之间。
5.进一步地,涂有金属钛-铜层的金刚石/铜复合材料热沉表面钛层厚度为1-5微米,铜层厚度大于10微米;优选为40-110微米。
6.进一步地,铜层为金属铜或铜合金层,铜合金可以是cu-ti、cu-cr、cu-b等合金。
7.进一步地,钛层通过真空微蒸发镀或磁控溅射工艺镀覆。
8.进一步地,所述的金刚石/铜复合材料的组成为金刚石体积含量为20%-80%,金刚石粒度为20-300微米。
9.上述表面敷有金属钛-铜层的金刚石/铜复合材料热沉的制备方法,包括如下步骤:
10.(1)在金刚石/铜复合材料热沉表面通过真空微蒸发镀或磁控溅射工艺镀覆钛层;
11.(2)将步骤(1)中的热沉片浸入铜或铜合金熔液中,静止一段时间后,从铜或铜合金熔液中移出;
12.(3)移出金属熔液的热沉片垂直放置,自然冷却,即制备得到表面涂有钛-铜的金刚石/铜复合材料热沉片。
13.上述方法中涂覆或镀覆钛层和铜层的工艺步骤在真空或惰性气体保护环境中进行。
14.步骤(2)中,所述铜或铜合金熔液的温度在1100-1300℃;热沉片在铜或铜合金熔液中浸没静止的时间为20-40min。
15.本发明的有益效果是,通过在金刚石/铜复合材料热沉表面涂敷钛-铜来改善表面的粗糙度,可将原来的表面粗糙度ra由1微米降低到粗糙度低于0.5微米,大大提高后期焊料的铺展性,从而提高芯片的焊透率,充分发挥金刚石/铜复合材料的高导热散热性能。
16.本发明中选用了钛打底,钛与金刚石/铜复合材料中金刚石和铜两相的结合均较好,既通过ti层提高金属层与金刚石/铜基体间的结合力,同时ti层也易于外层铜合金结合;并且可以在浸渍铜或铜合金时,易与金属熔液结合,结合强度高。同时选择的铜元素的热导率高,大大降低镀层对热沉导热性的影响,且后期铜易加工,加工表面光洁度高。
附图说明
17.图1为敷有金属钛-铜层的金刚石/铜复合材料热沉制备方法流程图。
18.图2为实施例1制备敷有金属钛-铜层的金刚石/铜复合材料热沉剖面结构示意图。
19.主要附图标记说明:
[0020]1ꢀꢀꢀꢀ
金刚石/铜复合材料热沉
ꢀꢀꢀꢀꢀꢀꢀꢀꢀꢀ2ꢀꢀꢀꢀ
钛层
[0021]3ꢀꢀꢀꢀ
铜或铜合金层
具体实施方式
[0022]
如图1所示,敷有金属钛-铜层的金刚石/铜复合材料热沉制备时,首先,将金刚石/铜复合材料热沉通过真空微蒸发镀或磁控溅射镀覆钛层,钛层厚度控制在1-5微米之间。然后将带有钛层的金刚石/铜复合材料热沉浸入铜或铜合金的熔液中,通过调整熔液的温度、浸入时间,控制铜或铜合金的镀覆厚度,厚度大于10微米,将热沉移出金属熔液,并垂直放置,自然冷却,得到敷有金属钛-铜层的金刚石/铜复合材料热沉。整个镀覆工艺在真空或惰性气体中进行。其中铜合金可以是cu-ti、cu-cr、cu-b等合金。
[0023]
如图2所示,本发明的敷有金属钛-铜层的金刚石/铜复合材料热沉,由高导热的金刚石/铜复合材料热沉1、镀覆的钛层2和铜或铜合金层3构成。金刚石/铜复合材料热沉形状、厚度任选,钛层厚度为1-5微米,铜或铜合金厚度大于10微米。
[0024]
实施例1:
[0025]
选用10*10*1的金刚石/铜复合材料热沉,采用真空微蒸发镀工艺在热沉表面镀钛,钛层厚度为1微米,然后将热沉片浸入真空熔炼的铜cu-b熔液中,铜液温度为1100℃,静置30min,移出熔液后,垂直放置,自然冷却,镀覆的铜层厚度为100-110微米。得到覆金属钛-铜层的金刚石/铜复合材料热沉,表面可二次精抛,表面ra小于0.2微米。
[0026]
实施例2:
[0027]
选用10*10*2的金刚石/铜复合材料热沉,采用磁控溅射工艺在热沉表面镀钛,钛层厚度为1.5微米,然后将热沉片浸入真空熔炼的铜熔液中,铜液温度为1200℃,静置20min,移出熔液后,垂直放置,自然冷却,镀覆的铜层厚度为50-55微米。得到覆金属钛-铜层的金刚石/铜复合材料热沉表面光洁度高,ra小于0.4微米。
[0028]
实施例3:
[0029]
选用140*32*2的金刚石/铜复合材料热沉,采用真空微蒸发镀工艺在热沉表面镀
钛,钛层厚度为4微米,然后将热沉片浸入真空熔炼的cu-cr熔液中,铜液温度为1250℃,静置40min,移出熔液后,垂直放置,自然冷却,镀覆的铜层厚度为60-70微米。得到覆金属钛-铜层的金刚石/铜复合材料热沉表面二次精抛后,ra小于0.2微米。
[0030]
实施例4:
[0031]
选用20*10*1.5的金刚石/铜复合材料热沉,采用磁控溅射工艺热沉表面镀钛,钛层厚度为2微米,然后将热沉片浸入真空熔炼的cu-ti熔液中,铜液温度为1300℃,静置20min,移出熔液后,垂直放置,自然冷却,镀覆的铜层厚度为40-50微米。得到覆金属钛-铜层的金刚石/铜复合材料热沉表面光洁度高,ra小于0.3微米。
[0032]
本发明的金刚石/铜热沉表面涂有一层金属钛层和铜层,厚度在数微米至数百微米之间。首先在金刚石/铜复合材料热沉表面通过真空微蒸发镀或磁控溅射工艺镀覆钛层,然后浸入铜或铜合金熔液中,静止一段时间后从铜或铜合金熔液中移出,自然冷却即得到敷有金属钛-铜层的金刚石/铜复合材料热沉。本发明制备的金刚石/铜复合材料热沉表面金属层均匀,结合强度高,且热沉表面粗糙度低,更满足后续工程应用的焊接需要,更易发挥高导热材料的优异性能。
技术特征:
1.一种敷有金属钛-铜层的金刚石/铜复合材料热沉,其特征在于:包括金刚石/铜复合材料热沉,所述热沉的表面从内到外依次设置钛层和铜层,钛层和铜层的厚度在数微米至数百微米之间。2.根据权利要求1所述的敷有金属钛-铜层的金刚石/铜复合材料热沉,其特征在于:所述的钛层厚度为1-5微米,铜层厚度大于10微米。3.根据权利要求2所述的敷有金属钛-铜层的金刚石/铜复合材料热沉,其特征在于:所述的铜层厚度为40-110微米。4.根据权利要求3所述的敷有金属钛-铜层的金刚石/铜复合材料热沉,其特征在于:所述的铜层为金属铜或铜合金层。5.根据权利要求4所述的敷有金属钛-铜层的金刚石/铜复合材料热沉,其特征在于:所述的铜合金为cu-ti、cu-cr或cu-b合金。6.根据权利要求1所述的敷有金属钛-铜层的金刚石/铜复合材料热沉,其特征在于:所述的钛层通过真空微蒸发镀或磁控溅射工艺镀覆。7.根据权利要求1-6所述的敷有金属钛-铜层的金刚石/铜复合材料热沉的制备方法,包括如下步骤:(1)在金刚石/铜复合材料热沉表面通过真空微蒸发镀或磁控溅射工艺镀覆钛层;(2)将步骤(1)中的热沉浸入铜或铜合金熔液中,静止一段时间后,从铜或铜合金熔液中移出;(3)移出金属熔液的热沉垂直放置,自然冷却,即制备得到表面涂有钛-铜的金刚石/铜复合材料热沉片。8.根据权利要求7所述的敷有金属钛-铜层的金刚石/铜复合材料热沉的制备方法,其特征在于:制备钛层和铜层的工艺在真空或惰性气体保护环境中进行。9.根据权利要求7所述的敷有金属钛-铜层的金刚石/铜复合材料热沉的制备方法,其特征在于:所述的铜或铜合金熔液的温度为1100-1300℃。10.根据权利要求7所述的敷有金属钛-铜层的金刚石/铜复合材料热沉的制备方法,其特征在于:所述的热沉在铜或铜合金熔液中浸没静止的时间为20-40min。
技术总结
本发明涉及一种敷有金属钛-铜层的金刚石/铜复合材料热沉及其制备方法,属于热管理材料技术领域。该敷有金属钛-铜层的金刚石/铜复合材料热沉,包括金刚石/铜复合材料热沉,热沉的表面从内到外依次设置钛层和铜层,钛层和铜层的厚度在数微米至数百微米之间。首先在金刚石/铜复合材料热沉表面通过真空微蒸发镀或磁控溅射工艺镀覆钛层,然后浸入铜或铜合金熔液中,静止一段时间后从铜或铜合金熔液中移出,自然冷却即得到敷有金属钛-铜层的金刚石/铜复合材料热沉。本发明制备的金刚石/铜复合材料热沉表面金属层均匀,结合强度高,且热沉表面粗糙度低,更满足后续工程应用的焊接需要,更易发挥高导热材料的优异性能。更易发挥高导热材料的优异性能。更易发挥高导热材料的优异性能。
技术研发人员:张习敏 郭宏 谢忠南 黄树晖 解浩峰 黄国杰 李增德
受保护的技术使用者:有研工程技术研究院有限公司
技术研发日:2020.11.25
技术公布日:2022/5/31
再多了解一些
本文用于企业家、创业者技术爱好者查询,结果仅供参考。