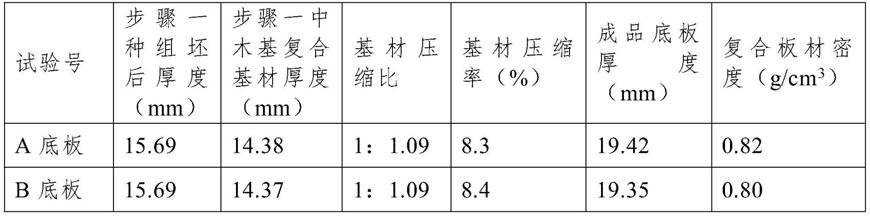
1.本发明属于人造板技术领域,具体涉及一种轻质减震型动车/地铁车厢底板的制备方法。
背景技术:
2.随着人们生活品质不断提高,舒适安静的体验与绿色低碳的模式已成为建筑居住、交通出行、体育运动和城市观光等诸多领域场景的迫切需求。利用竹材等生物基材料,开展减振抗噪新产品的设计与制造,符合“两碳”目标和绿色高质量发展的理念。竹质复合阻尼材料在一定程度上可替代木材和橡胶解决生产生活中振动噪音的污染,满足了人们对美化生活环境的要求。特别是竹材交通领域中应用日益广泛,如轻量化地铁和动车车厢底板、远洋货轮的集装箱地板、低voc轿车次构件和汽车的装饰材与次构件。动车用地板要求板材具有阻燃、轻质和减振的特点。竹质复合阻尼材料应用于高速列车的地板或海运集装箱地板,能缓解动车车身和远洋巨轮分别受列车速度的变化和海浪冲击而产生的噪音,有效提高运输的安全性和舒适度
3.竹子是我国特色资源,3~5年即可成材;且竹纤维强韧性好、比强度和比模量高;同时竹材又是环保节能材料,相同建筑面积竹材的能耗是混凝土的1/8、钢材的1/50。竹材的梯度结构和复杂组分赋予其天然的减震阻尼性能,并可通过与其他材料复合形成高性能、轻量化的绿色阻尼功能材料。作为一种天然生物材料,竹材具有厘米级竹节与节间复合结构、毫米级竹纤维束与薄壁组织两相结构、微米级维管束多孔结构以及纳米级纤维素分子链结构。上述结构特征,从宏观尺度到分子尺度的自相似特征赋予竹材高强高韧性能和阻尼功能。
技术实现要素:
4.本发明所要解决的技术问题在于针对上述现有技术的不足,提供了一种轻质减震型动车/地铁车厢底板的制备方法。该制备方法通过热压和冷压相结合的方法,将木质单板a、木质单板b和木质单板c、无纺布、竹炭板等材料按照一定的组坯顺序进行复合,制得复合板材,该复合板材不仅具有较好的阻尼减震性能,对能量的内耗吸收增大,而且通过对表层木质单板a进行阻燃和耐候等功能化处理,可以大大拓宽木质复合材料在动车和地铁等交通领域的应用范围。
5.为解决上述技术问题,本发明采用的技术方案是:一种轻质减震型动车/地铁车厢底板的制备方法,其特征在于,该方法包括以下步骤:
6.步骤一、从上到下按木质单板a、木质单板b、无纺布或隔音橡胶板、木质单板a、木质单板b、木质单板a、木质单板c、木质单板b、无纺布、木质单板a、木质单板b、木质单板a的顺序组坯,然后热压成型,得到木基复合基材;
7.所述木质单板a和木质单板b组坯之前依次进行阻燃处理和涂热固性胶粘剂;所述木质单板c组坯之前涂热固性胶粘剂;
8.组坯之前所述无纺布提前浸渍热固性胶粘剂,再沥干表面热固性胶粘剂后,干燥至含水率8%-12%;
9.步骤二、首先将竹炭板的一侧表面砂光,然后单面辊涂聚氨酯热熔胶,将涂胶后的竹炭板和步骤一中得到的木基复合基材冷压成型,得到竹基复合板材;
10.步骤三、在步骤二中得到的竹基复合板材的最外层白蜡木单板外均匀喷涂胺盐化合物的醇溶液,获得均匀的导电性,然后在30kv~50kv静电电压下均匀喷涂雾化的氨基醇酸涂料粉末,再在温度为100℃~180℃的条件下固化5min~30min,形成0.2~1mm厚的防护涂层,得到轻质减震型动车/地铁车厢底板。
11.优选地,步骤一中热压成型的条件:温度为145℃~155℃、压力为1~1.5mpa,时间30~45min。
12.优选地,步骤一中木质单板a为白蜡木单板、桦木单板、榉木单板和桉木单板;木质单板b为杨木单板、桉木单板、白桉木单板或法国泡桐木单板;木质单板c为橡胶木单板、桦木单板、榉木单板或相思木单板;所述木质单板a的厚度为0.8~1.5mm;木质单板b的厚度为1.5-1.7mm;木质单板c的厚度为1.2~1.7mm;步骤三中所述竹炭板的厚度为3.0~4.5mm,所述隔音橡胶板的厚度是2mm。
13.更优选地,所述木质单板a优选桦木单板,第二为白蜡木单板,第三选榉木单板;木质单板b为优选杨木单板、第二白桉木单板,第三选桉木单板;木质单板c为优选橡胶木单板,第二选西南桦木单板,第三选榉木木单板或相思木木单板
14.优选地,步骤一中木质单板a、木质单板b和木质单板c的木质纹理均为横纹或者顺纹,且要求木质单板a和木质单板c的木质纹理相同,与木质单板b的木质纹理相异。
15.优选地,步骤一中所述阻燃处理的过程为:将木质单板a和木质单板b置于温度为6~45℃、浓度为10%~20%的阻燃剂水溶液中浸渍10~30min,然后放入55~65℃的烘箱中或自然干燥至单板的含水率为8%~12%。
16.优选地,步骤一中所述热固性胶粘剂为酚醛树脂胶粘剂。
17.优选地,步骤一中组坯之前时木质单板a、木质单板b和木质单板c采用双面辊压涂固含量为30%~55%的酚醛树脂胶粘剂,所述木质单板a和木质单板b的涂胶量均为150~300g/m2,所述木质单板c的涂胶量为40~80g/m2;所述无纺布提前浸渍的热固性胶粘剂为固含量为45%~55%的酚醛树脂胶粘剂;所述隔音橡胶板的施胶量为80~120g/m2。
18.优选地,步骤二中冷压成型的条件为:压力为1.5~2.0mpa,常温下冷压3h。
19.优选地,步骤二中所述聚氨酯热熔胶的涂胶量为40g/m2。
20.优选地,步骤三中所述胺盐化合物的醇溶液具体为:由醇酸树脂、氨基树脂、二氧化钛和硅油混合而成,所述醇酸树脂、氨基树脂、二氧化钛和硅油的质量比为(4~8):(1~3):(2~4):(0.01~0.03)。优选地,步骤三中所述胺盐化合物的醇溶液具体为:由醇酸树脂、氨基树脂、二氧化钛和硅油混合而成,所述醇酸树脂、氨基树脂、二氧化钛和硅油的质量比为(4~8):(1~3):(2~4):(0.01~0.03);所述氨基醇酸涂料中的氨基树脂改善了醇酸树脂的硬度、光泽、烘干速度以及耐碱、耐油性能,而醇酸树脂则改善了氨基树脂的脆性、附着力,最终增加底板表面的耐老化,抗龟裂性能,配合二氧化钛进行着色和硅油溶解分散各原料,喷涂厚度均匀,涂料利用率高、工作效率高,装饰效果好。
21.本发明与现有技术相比具有以下优点:
22.1、本发明将竹炭板与多种木质单板按一定的顺序组坯通过热压和冷压制成竹基复合板材,由于木质材料多孔隙结构及橡胶板的阻尼作用的原因导致本发明的底板具有良好的减震阻尼。由于采用较多的木单板可以减轻底板的重量,方便安装。本发明还通过对表层材料进行功能化改良,使其具有耐磨、抗静电等性能,并且所用的木质单板a和木质单板b在组坯之前进行阻燃处理,使制备的底板具有阻燃性能,达到动车、地铁车厢使用的标准。因此,本发明制备的底板将不同硬度和功能材料的性能进行合理结合,具有可设计性强,重量轻、阻燃和表观质量好,尺寸稳定性好等诸多优点。
23.2、本发明包括上表层木质单板a采用耐磨阻燃无机功能化处理,底层采用竹炭板,其具有吸潮、吸voc的功能,芯层采用轻质的木质单板b与阻尼减震的木质单板c以及无纺布复合,为动车/地铁用轻量化功能化板材制造提供一种新的绿色低碳加工技术,弥补了动车或者地铁上地板防滑减震、轻量化以及吸voc性能上的不足,提高安装效率、减少成本。
24.下面通过附图和实施例对本发明的技术方案作进一步的详细说明。
附图说明
25.图1是本发明实施例1制备的轻质减震型动车/地铁车厢底板的侧视图。
26.图2是本发明实施例1制备的轻质减震型动车/地铁车厢底板的的各阶模态分析图。
具体实施方式
27.实施例1
28.本实施例轻质减震型动车/地铁车厢底板的制备方法包括以下步骤:
29.步骤一、从上到下按木质单板a、木质单板b、无纺布、木质单板a、木质单板b、木质单板a、木质单板c、木质单板b、无纺布、木质单板a、木质单板b、木质单板a的顺序组坯,在温度为150℃、压力为1.25mpa的条件下热压40min成型,得到木基复合基材;其中在热压成型时最外层的木质单板a的外侧贴有浸渍纸;
30.所述木质单板a选用白蜡木单板,木质单板b选用杨木单板,木质单板c选用橡胶木单板;
31.所述木质单板a(白蜡木单板)和木质单板b(杨木单板)组坯之前依次进行阻燃处理和涂热固性胶粘剂,热固性胶粘剂为酚醛树脂胶粘剂;具体地:所述白蜡木单板、杨木单板均提前经过阻燃处理,阻燃处理过程为:将白蜡木单板和杨木单板置于温度为25℃、浓度为15%的6503#阻燃剂的水溶液中浸渍20min,然后放入60℃的烘箱中或自然干燥至单板的含水率为10%,备用;组坯时已经经过阻燃处理的白蜡木单板和杨木单板采用双面辊压涂固含量为42%的酚醛树脂胶粘剂(酚醛树脂胶粘剂简写为pf胶),涂胶量为225g/m2;
32.所述木质单板c(橡胶木单板)组坯之前涂热固性胶粘剂,具体地:橡胶木单板采用手工双面涂固含量为42%的pf胶,涂胶量为60g/m2;
33.组坯之前所述无纺布提前浸渍热固性胶粘剂,再沥干表面热固性胶粘剂后,干燥至含水率10%,热固性胶粘剂为酚醛树脂胶粘剂;具体地:所述无纺布提前浸渍固含量为50%的pf胶,浸胶时间10min,沥干表面胶粘剂后,干燥至含水率10%,备用;
34.步骤二、首先将竹炭板的一侧表面砂光,然后手工单面辊涂聚氨酯热熔胶,涂胶量
为40g/m2,将涂胶后的竹炭板和步骤一中得到的木基复合基材在压力为1.75mpa、常温25℃下冷压3h成型,得到竹基复合板材;
35.步骤三、在步骤二中得到的竹基复合板材的最外层白蜡木单板外均匀喷涂胺盐化合物的醇溶液,获得均匀的导电性,然后在40kv静电电压下均匀喷涂雾化的氨基醇酸涂料粉末,再在温度为140℃的条件下固化18min,形成0.6mm厚的防护涂层,得到轻质减震型动车/地铁车厢底板。所述胺盐化合物的醇溶液具体为:由醇酸树脂、氨基树脂、二氧化钛和硅油混合而成,所述醇酸树脂、氨基树脂、二氧化钛和硅油的质量比为6:2:3:0.02;所述氨基醇酸涂料中的氨基树脂改善了醇酸树脂的硬度、光泽、烘干速度以及耐碱、耐油性能,而醇酸树脂则改善了氨基树脂的脆性、附着力,最终增加底板表面的耐老化,抗龟裂性能,配合二氧化钛进行着色和硅油溶解分散各原料,喷涂厚度均匀,涂料利用率高、工作效率高,装饰效果好。
36.本实施例中,所述白蜡木单板和橡胶木单板的木质纹理均为顺纹,杨木单板的木质纹理为横纹。
37.所述顺纹的白蜡木单板由市场购买的多张规格为1.2mm厚、幅面为840
×
1270mm、密度为0.42g/cm3、含水量低于7%的白蜡木板经规格裁制配料、顺纹铣斜边、涂酚醛树脂胶通过组坯热压斜接拼宽为1250
×
1270mm幅面的顺纹单板而成;拼宽顺纹单板经手工横纹铣斜边后再涂胶热压进行斜接接长,拼接成幅面为1250
×
1900mm的顺纹的白蜡木单板备用。
38.所述顺纹的橡胶木单板由市场购买的多张规格为1.7mm厚、幅面为1270
×
615mm、密度为0.62g/cm3、含水量低于7%的橡胶木板经规格裁制配料、手工顺纹铣斜边、涂酚醛树脂胶胶通过组坯热压斜接而成,加工为1900
×
615mm幅面的顺纹单板。
39.所述横纹的杨木单板由市场购买的多张规格为1.6mm厚、幅面为630
×
1270mm、密度为0.42g/cm3、含水量低于7%的杨木板横纹铣斜边、涂酚醛树脂胶胶通过组坯热压斜接拼宽为1250
×
1270mm幅面的顺纹单板而成。
40.本实施例中,所述无纺布的厚度为0.67mm。选用的规格3mm厚的竹炭板(福建炭都科技有限公司,单面砂光后),幅面为1220
×
1870mm,密度为0.85g/cm3。
41.采用本实施例公开的方法,制备了两块结构相同的底板,该底板的密度为12.0kg/m2,误差不超过3%,分别定义为a底板和b底板,a底板进行检测,b底板作为试验留样。对制备的底板的密度、胶合强度、静曲强度、动载荷试验条件下的破坏载荷(顺纹)、板面握钉力、耐沸水煮性能、表面燃烧性能。
42.所述胶合强度检测试件预处理方法:gb/t 17657-2013,一类板,煮—干—煮。
43.本实施例制备的轻质减震型动车/地铁车厢底板用复合板材的实验结果。
44.表1本实施例a底板和b底板步骤中的热压压缩情况、厚度和密度
[0045][0046]
表2本实施例制备的a底板的静曲强度、弹性模量(方法:gb/t 17657-2013)
[0047][0048]
表3本实施例制备的a底板的表面燃烧性能、耐沸水煮性能(gb/t 17657-2013)
[0049]
试验号(a)检测值标准值结果判定表面燃烧性能(级)ba、b合格耐沸水煮性能(级)5≥4合格
[0050]
表4本实施例制备的a底板的胶合强度、板面握钉力(方法:gb/t 17657-2013)
[0051]
试验号(a)检测值标准值结果判定胶合强度(mpa)1.83≥1.0合格板面握钉力(kn)2.04≥1500合格
[0052]
表5本实施例制备的a底板的燃烧和阻尼性能(gb/t 17657-2013)
[0053][0054]
表6本实施例制备的a底板的不同应力水平下疲劳破坏次数
[0055][0056]
经检测,本实施例制备的底板符合350km/h动车对底板的各项要求。
[0057]
实施例2
[0058]
本实施例轻质减震型动车/地铁车厢底板的制备方法包括以下步骤:
[0059]
步骤一、从上到下按木质单板a、木质单板b、隔音橡胶板、木质单板a、木质单板b、木质单板a、木质单板c、木质单板b、无纺布、木质单板a、木质单板b、木质单板a的顺序组坯,在温度为145℃、压力为1mpa的条件下热压45min成型,得到木基复合基材;其中在热压成型时最外层的木质单板a的外侧贴有棕干纸;
[0060]
所述木质单板a为桦木单板,木质单板b为白桉木单板,木质单板c为西南桦木单
板;
[0061]
所述木质单板a(桦木单板)和木质单板b(白桉木单板)组坯之前依次进行阻燃处理和涂热固性胶粘剂,热固性胶粘剂为酚醛树脂胶粘剂;具体地:所述木质单板a和木质单板b均提前经过阻燃处理,阻燃处理过程为:将木质单板a和木质单板b置于温度为45℃、浓度为10%的6503#阻燃剂的水溶液中浸渍10min,然后放入55℃的烘箱中或自然干燥至单板的含水率为12%,备用;组坯时已经经过阻燃处理的木质单板a和木质单板b采用双面辊压涂固含量为30%的pf胶,涂胶量为300g/m2;
[0062]
所述木质单板c(西南桦木单板)组坯之前涂热固性胶粘剂,具体地:木质单板c采用手工双面涂固含量为30%的pf胶,涂胶量为80g/m2;
[0063]
组坯时所述隔音橡胶板涂饰固含量为30%的pf胶的涂胶量为100g/m2,也可以选择80~120g/m2其他数值的涂胶量;
[0064]
组坯之前所述无纺布提前浸渍固含量为45%的pf胶,浸胶时间10min,沥干表面胶粘剂后,干燥至含水率12%,备用;
[0065]
步骤二、首先将竹炭板的一侧表面砂光,然后手工单面辊涂聚氨酯热熔胶,涂胶量为40g/m2,将涂胶后的竹炭板和步骤一中得到的木基复合基材在压力为1.5mpa、常温25℃下冷压3h成型,得到竹基复合板材;
[0066]
步骤三、在步骤二中得到的竹基复合板材的最外层白蜡木单板外均匀喷涂胺盐化合物的醇溶液,获得均匀的导电性,然后在30kv静电电压下均匀喷涂雾化的氨基醇酸涂料粉末,再在温度为100℃的条件下固化30min,形成0.2mm厚的防护涂层,得到轻质减震型动车/地铁车厢底板。所述胺盐化合物的醇溶液具体为:由醇酸树脂、氨基树脂、二氧化钛和硅油混合而成,所述醇酸树脂、氨基树脂、二氧化钛和硅油的质量比为4:1:2:0.01;所述氨基醇酸涂料中的氨基树脂改善了醇酸树脂的硬度、光泽、烘干速度以及耐碱、耐油性能,而醇酸树脂则改善了氨基树脂的脆性、附着力,最终增加底板表面的耐老化,抗龟裂性能,配合二氧化钛进行着色和硅油溶解分散各原料,喷涂厚度均匀,涂料利用率高、工作效率高,装饰效果好。
[0067]
本实施例中,所述木质单板a为桦木单板,木质单板b为白桉木单板,木质单板c为西南桦木单板。
[0068]
本实施例中,所述木质单板a和木质单板c的木质纹理均为顺纹,木质单板b的木质纹理为横纹。桦木单板的厚度是0.8mm,幅面是840
×
1270mm;白桉木单板的厚度是1.7mm,幅面是1250
×
1270mm;西南桦木单板的厚度是1.2mm,幅面是840
×
1270mm,隔音橡胶板2mm,密度为1.52g/cm3;所述竹炭板的厚度为4.5mm;无纺布与实施例1相同。
[0069]
经检测,本实施例制备的底板的厚度为19mm,静曲强度为57.6mpa,弹性模量为5.45gpa,胶合强度为1.73mpa,板面握钉力为1.95kn,表面燃烧性能和耐沸水煮性能高于标准值为合格,耐火等级为难燃,阻尼性能满足地铁或动车对底板的要求,不同应力水平下疲劳破坏次数满足地铁或者动车底板的要求。
[0070]
实施例3
[0071]
本实施例轻质减震型动车/地铁车厢底板的制备方法包括以下步骤:
[0072]
步骤一、从上到下按木质单板a、木质单板b、无纺布、木质单板a、木质单板b、木质单板a、木质单板c、木质单板b、无纺布、木质单板a、木质单板b、木质单板a的顺序组坯,在温
度为155℃、压力为1.5mpa的条件下热压30min成型,得到木基复合基材;其中在热压成型时最外层的木质单板a的外侧贴有棕干纸;
[0073]
所述木质单板a为榉木单板,木质单板b为桉木单板,木质单板c为榉木单板;
[0074]
所述木质单板a(榉木单板)和木质单板b(桉木单板)组坯之前依次进行阻燃处理和涂热固性胶粘剂,热固性胶粘剂为酚醛树脂胶粘剂;具体地:所述木质单板a和木质单板b均提前经过阻燃处理,阻燃处理过程为:将木质单板a和木质单板b置于温度为6℃、浓度为20%的6503#阻燃剂的水溶液中浸渍30min,然后放入65℃的烘箱中或自然干燥至单板的含水率为8%,备用;组坯时已经经过阻燃处理的木质单板a和木质单板b采用双面辊压涂固含量为55%的pf胶,涂胶量为150g/m2;
[0075]
所述木质单板c(榉木)组坯之前涂热固性胶粘剂,具体地:木质单板c采用手工双面涂固含量为55%的pf胶,涂胶量为40g/m2;
[0076]
组坯之前所述无纺布提前浸渍固含量为55%的pf胶,浸胶时间浸胶时间5min,沥干表面胶粘剂后,干燥至含水率8%备用;
[0077]
步骤二、首先将竹炭板的一侧表面砂光,然后手工单面辊涂聚氨酯热熔胶,涂胶量为40g/m2,将涂胶后的竹炭板和步骤一中得到的木基复合基材在压力为2.0mpa、常温25℃下冷压3h成型,得到竹基复合板材;
[0078]
步骤三、在步骤二中得到的竹基复合板材的最外层白蜡木单板外均匀喷涂胺盐化合物的醇溶液,获得均匀的导电性,然后在50kv静电电压下均匀喷涂雾化的氨基醇酸涂料粉末,再在温度为180℃的条件下固化5minmin,形成1mm厚的防护涂层,得到轻质减震型动车/地铁车厢底板。所述胺盐化合物的醇溶液具体为:由醇酸树脂、氨基树脂、二氧化钛和硅油混合而成,所述醇酸树脂、氨基树脂、二氧化钛和硅油的质量比为8:3:4:0.04;所述氨基醇酸涂料中的氨基树脂改善了醇酸树脂的硬度、光泽、烘干速度以及耐碱、耐油性能,而醇酸树脂则改善了氨基树脂的脆性、附着力,最终增加底板表面的耐老化,抗龟裂性能,配合二氧化钛进行着色和硅油溶解分散各原料,喷涂厚度均匀,涂料利用率高、工作效率高,装饰效果好。
[0079]
本实施例中,所述木质单板a为榉木单板,木质单板b为桉木单板,木质单板c为榉木单板。
[0080]
本实施例中,所述木质单板a和木质单板c的木质纹理均为顺纹,木质单板b的木质纹理为横纹。作为木质单板a的榉木单板的厚度是1.2mm,幅面是840
×
1270mm;桉木单板的厚度是1.5mm,幅面是1250
×
1270mm;作为木质单板c的榉木单板的厚度是1.5mm,幅面是840
×
1270mm;所述竹炭板的厚度为2mm;无纺布与实施例1相同。
[0081]
经检测,本实施例制备的底板的厚度为19mm,静曲强度为56.6mpa,弹性模量为5.45gpa,胶合强度为1.75mpa,板面握钉力为2.01kn,表面燃烧性能和耐沸水煮性能高于标准值为合格,耐火等级为难燃,阻尼性能满足地铁或动车对底板的要求,不同应力水平下疲劳破坏次数满足地铁或者动车底板的要求。
[0082]
实施例4
[0083]
本实施例轻质减震型动车/地铁车厢底板的制备方法包括以下步骤:
[0084]
步骤一、从上到下按木质单板a、木质单板b、无纺布、木质单板a、木质单板b、木质单板a、木质单板c、木质单板b、无纺布、木质单板a、木质单板b、木质单板a的顺序组坯,在温
度为145℃、压力为1mpa的条件下热压45min成型,得到木基复合基材;其中在热压成型时最外层的木质单板a的外侧贴有棕干纸;
[0085]
本实施例中,所述木质单板a为桉木单板,木质单板b为法国泡桐木单板,木质单板c相思木单板;
[0086]
所述木质单板a(桉木单板)和木质单板b(法国泡桐木单板)组坯之前依次进行阻燃处理和涂热固性胶粘剂;具体地:所述木质单板a和木质单板b均提前经过阻燃处理,阻燃处理过程为:将木质单板a和木质单板b置于温度为30℃、浓度为15%的6503#阻燃剂的水溶液中浸渍20min,然后放入60℃的烘箱中或自然干燥至单板的含水率为9%,备用;组坯时已经经过阻燃处理的木质单板a和木质单板b采用双面辊压涂固含量为40%的pf胶,涂胶量为230g/m2;
[0087]
所述木质单板c(相思木单板)组坯之前涂热固性胶粘剂,具体地:木质单板c采用手工双面涂固含量为45%的pf胶,涂胶量为70g/m2;
[0088]
组坯之前所述无纺布提前浸渍固含量为48%的pf胶,浸胶时间浸胶时间12min,沥干表面胶粘剂后,干燥至含水率9%备用;
[0089]
步骤二、首先将竹炭板的一侧表面砂光,然后手工单面辊涂聚氨酯热熔胶,涂胶量为40g/m2,将涂胶后的竹炭板和步骤一中得到的木基复合基材在压力为1.6mpa、常温25℃下冷压3h成型,得到竹基复合板材;
[0090]
步骤三、在步骤二中得到的竹基复合板材的最外层白蜡木单板外均匀喷涂胺盐化合物的醇溶液,获得均匀的导电性,然后在35kv静电电压下均匀喷涂雾化的氨基醇酸涂料粉末,再在温度为150℃的条件下固化20min,形成0.8mm厚的防护涂层,得到轻质减震型动车/地铁车厢底板。所述胺盐化合物的醇溶液具体为:由醇酸树脂、氨基树脂、二氧化钛和硅油混合而成,所述醇酸树脂、氨基树脂、二氧化钛和硅油的质量比为5:2:3:0.015;所述氨基醇酸涂料中的氨基树脂改善了醇酸树脂的硬度、光泽、烘干速度以及耐碱、耐油性能,而醇酸树脂则改善了氨基树脂的脆性、附着力,最终增加底板表面的耐老化,抗龟裂性能,配合二氧化钛进行着色和硅油溶解分散各原料,喷涂厚度均匀,涂料利用率高、工作效率高,装饰效果好。
[0091]
本实施例中,所述木质单板a为桉木单板,木质单板b为法国泡桐木单板,木质单板c相思木单板;
[0092]
本实施例中,所述木质单板a和木质单板c的木质纹理均为顺纹,木质单板b的木质纹理为横纹。本实施例中,所述木质单板a和木质单板c的木质纹理均为顺纹,木质单板b的木质纹理为横纹。桉木单板的厚度是1.5mm,幅面是840
×
1270mm;法国泡桐木木单板的厚度是1.5mm,幅面是1250
×
1270mm;相思木单板的厚度是1.2mm,幅面是840
×
1270mm;所述竹炭板的厚度为3.5mm;无纺布与实施例1相同。
[0093]
经检测,本实施例制备的底板的厚度为19mm,静曲强度为58.4mpa,弹性模量为5.60gpa,胶合强度为1.79mpa,板面握钉力为2.05kn,表面燃烧性能和耐沸水煮性能高于标准值为合格,耐火等级为难燃,阻尼性能满足地铁或动车对底板的要求,不同应力水平下疲劳破坏次数满足地铁或者动车底板的要求。
[0094]
实施例1-4中所用的不同木材的板材、隔音橡胶板、竹炭板和无纺布均来自市购。
[0095]
以上所述,仅是本发明的较佳实施例,并非对本发明作任何限制。凡是根据发明技
术实质对以上实施例所作的任何简单修改、变更以及等效变化,均仍属于本发明技术方案的保护范围内。
再多了解一些
本文用于企业家、创业者技术爱好者查询,结果仅供参考。