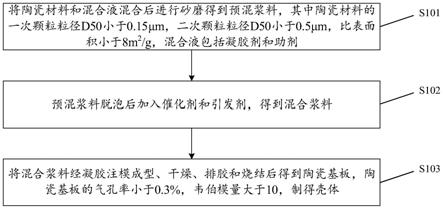
1.本技术属于电子产品技术领域,具体涉及壳体及其制备方法和电子设备。
背景技术:
2.陶瓷材料具有硬度高、韧性好、耐磨等优点,近年来常常应用于电子设备中。目前,陶瓷材料制得的产品内部缺陷较为严重,难以满足应用需求。因此,陶瓷产品的性能还有待于进一步提高。
技术实现要素:
3.鉴于此,本技术提供了一种壳体及其制备方法和电子设备。
4.第一方面,本技术提供了一种壳体,所述壳体包括陶瓷基板,所述陶瓷基板的气孔率小于0.3%,韦伯模量大于10。
5.第二方面,本技术提供了一种壳体的制备方法,包括:
6.将陶瓷材料和混合液混合后进行砂磨得到预混浆料,其中所述陶瓷材料的一次颗粒粒径d50小于0.15μm,二次颗粒粒径d50小于0.5μm,比表面积小于8m2/g,所述混合液包括凝胶剂和助剂水;
7.所述预混浆料脱泡后加入催化剂和引发剂,得到混合浆料;
8.所述混合浆料经凝胶注模成型、干燥、排胶和烧结后得到陶瓷基板,所述陶瓷基板的气孔率小于0.3%,韦伯模量大于10,制得壳体。
9.第三方面,本技术提供了一种电子设备,所述电子设备包括壳体,所述壳体包括陶瓷基板,所述陶瓷基板的气孔率小于0.3%,韦伯模量大于10。
10.本技术提供的壳体中陶瓷基板具有低气孔率并且强度一致性高,具有优异的性能,有利于壳体的应用;该壳体的制备方法操作简单,可以获得性能优异的陶瓷基板,从而提高壳体的性能;具有该壳体的电子设备不仅具有优异的机械性能,同时还具有陶瓷质感外观,提高了电子设备的产品竞争力。
附图说明
11.为了更清楚地说明本技术实施方式中的技术方案,下面将对本技术实施方式中所需要使用的附图进行说明。
12.图1为本技术一实施方式提供的壳体的制备方法流程示意图。
13.图2为本技术另一实施方式提供的壳体的制备方法流程示意图。
14.图3为本技术又一实施方式提供的壳体的制备方法流程示意图。
15.图4为本技术一实施方式提供的壳体的结构示意图。
16.图5为本技术另一实施方式提供的壳体的结构示意图。
17.图6为本技术一实施方式提供的电子设备的结构示意图。
18.图7为本技术一实施方式提供的电子设备的结构组成示意图。
19.图8为实施例1制得的陶瓷基板晶粒的显微镜形貌图。
20.图9为实施例2制得的陶瓷基板晶粒的显微镜形貌图。
21.图10为实施例3制得的陶瓷基板晶粒的显微镜形貌图。
22.图11为对比例1制得的陶瓷基板晶粒的显微镜形貌图。
23.图12为对比例2制得的陶瓷基板晶粒的显微镜形貌图。
具体实施方式
24.以下是本技术的优选实施方式,应当指出,对于本技术领域的普通技术人员来说,在不脱离本技术原理的前提下,还可以做出若干改进和润饰,这些改进和润饰也视为本技术的保护范围。
25.下文的公开提供了许多不同的实施方式或例子用来实现本技术的不同结构。为了简化本技术的公开,下文中对特定例子的部件和设置进行描述。当然,它们仅仅为示例,并且目的不在于限制本技术。此外,本技术可以在不同例子中重复参考数字和/或参考字母,这种重复是为了简化和清楚的目的,其本身不指示所讨论各种实施方式和/或设置之间的关系。此外,本技术提供了的各种特定的工艺和材料的例子,但是本领域普通技术人员可以意识到其他工艺的应用和/或其他材料的使用。
26.请参阅图1,为本技术一实施方式提供的壳体的制备方法流程示意图,包括:
27.s101:将陶瓷材料和混合液混合后进行砂磨得到预混浆料,其中陶瓷材料的一次颗粒粒径d50小于0.15μm,二次颗粒粒径d50小于0.5μm,比表面积小于8m2/g,混合液包括凝胶剂和助剂。
28.s102:预混浆料脱泡后加入催化剂和引发剂,得到混合浆料。
29.s103:将混合浆料经凝胶注模成型、干燥、排胶和烧结后得到陶瓷基板,陶瓷基板的气孔率小于0.3%,韦伯模量大于10,制得壳体。
30.本技术通过凝胶注模成型工艺制备陶瓷基板10,以获得壳体100;其中通过提供合适的一次颗粒粒径d50以及二次颗粒粒径d50和低比表面积的陶瓷材料,从而保证了其在混合浆料中的均匀分散,有利于避免团聚的发生,进而避免因团聚带来的内部缺陷,降低了陶瓷基板10的气孔率,提高了陶瓷基板10的强度一致性。可以理解的,气孔率越小,表明陶瓷基板10内部的气孔越少,内部缺陷更少,陶瓷基板10的气密性更好;韦伯模量(weibull modulus),也可以称之为韦布尔模数,反应了陶瓷基板10的四点弯曲强度值的离散性,数据越大,离散性越小,产品强度的缺陷越少,性能更加稳定。干压成型的陶瓷板内部孔洞多,注射成型需要专业的注射机器,流延成型只适合于制备平面状的陶瓷板,本技术通过凝胶注模成型工艺,从而可以极大地降低陶瓷基板10内部的孔隙,提高陶瓷基板10的性能,同时无需大型设备的使用,降低了制备成本,并且通过改变模具形状即可实现不同形状的陶瓷基板10的制作,外观形状可变性高,可以适用于多种应用场景,从而有利于壳体100的使用。
31.在s101中,通过将陶瓷材料和混合液混合、砂磨,获得预混浆料。在本技术中,陶瓷材料为无机物,混合液为含有机物的溶液。
32.在本技术实施方式中,陶瓷材料包括氧化锆,从而制得的陶瓷基板10为氧化锆陶瓷。氧化锆陶瓷具有优异的韧性、强度和硬度,提高了壳体100的力学性能和耐性,有利于其应用。在本技术中,氧化锆的一次颗粒粒径d50、二次颗粒粒径d50以及比表面积并不限定,
只要陶瓷材料的一次颗粒粒径d50小于0.15μm,二次颗粒粒径d50小于0.5μm,比表面积小于8m2/g即可。例如,氧化锆的一次颗粒粒径d50小于0.1μm,二次颗粒粒径d50小于0.25μm,比表面积小于20m2/g。其中,粒径d50为材料的累计粒度分布百分数达到50%时所对应的粒径,也称之为中位径或中值粒径。
33.在本技术实施例中,陶瓷材料包括氧化锆和氧化钇。其中,氧化钇作为稳定剂,有利于在陶瓷基板10中形成稳定、致密的四方相氧化锆,从而提高陶瓷基板10的结构稳定性,保证陶瓷基板10在制备和加工过程中不易发生开裂。在一实施例中,陶瓷材料中氧化钇的质量含量为2%-8%,既能够保证四方相氧化锆的形成和稳定存在,同时又不会影响陶瓷基板10的性能。具体的,陶瓷材料中氧化钇的质量含量可以但不限于为2%、3%、4%、5%、6%、7%或8%等。在一具体实施例中,陶瓷材料中氧化钇的质量含量为2%-4%。在另一具体实施例中,陶瓷材料中氧化钇的质量含量为4%-8%。
34.在本技术实施例中,陶瓷材料还可以包括氧化铪。其中,氧化铪是氧化锆粉体的共生物,氧化锆粉体中通常都含有少量氧化铪。具体的,陶瓷材料中氧化铪的质量含量可以但不限于小于或等于3%,如陶瓷材料中氧化铪的质量含量为0.1%、0.5%、1%、1.5%、2%或3%等。
35.在本技术实施例中,陶瓷材料还可以包括增强剂。通过添加增强剂,进一步促进烧结并提高陶瓷的断裂韧性,从而提升壳体100的性能。在一实施例中,增强剂可以包括氧化钛、氧化硅、氧化锗、氧化镁和氧化锌中的至少一种。上述无机材料可以作为增强剂有效提高陶瓷基板10的断裂韧性。在一实施例中,陶瓷材料中增强剂的质量含量小于或等于5%,既能够保证提升陶瓷基板10的断裂韧性,同时又可以避免含量过多影响陶瓷基板10的硬度。具体的,陶瓷材料中增强剂的质量含量可以但不限于为1%、2%、3%、4%或5%等。在一具体实施例中,陶瓷材料中增强剂的质量含量为0.5%-2%。在另一具体实施例中,陶瓷材料中增强剂的质量含量为3%-5%。
36.在本技术实施例中,陶瓷材料还可以包括染色剂。通过添加染色剂使陶瓷基板10呈现不同的色彩,改变陶瓷基板10的外观,从而扩大壳体100的应用场景。在一实施例中,染色剂可以但不限于为选自氧化铝、氧化锌、氧化钴、三氧化二铁、三氧化二铬、氧化镍、氧化锰、氧化铒、氧化钕、氧化镨、氧化铜、氧化钛、五氧化二铌、氧化钙、氧化硅、氧化铈、氧化钡、氧化镧、氧化铯、氧化铋、氧化锶、氧化镓、氧化镁、氧化钒、氧化锡,以及具有上述阳离子的其他化合物中的至少一种。例如,具有上述阳离子的其他化合物可以但不限于为硅酸镍、钒锆黄、铬铁矿、铝酸钴等。具体的,染色剂的材质可以根据陶瓷基板10所需的颜色进行选择。在一实施例中,陶瓷材料中染色剂的质量含量小于或等于5%,既能够保证使陶瓷基板10具有色彩外观,同时又可以避免含量过多影响陶瓷基板10的机械性能。具体的,陶瓷材料中染色剂的质量含量可以但不限于为0.5%、1%、2%、2.5%、3%、4%或5%等。在一具体实施例中,陶瓷材料中染色剂的质量含量为0.5%-2%。在另一具体实施例中,陶瓷材料中染色剂的质量含量为2.5%-5%。
37.在一实施例中,按质量含量计,陶瓷材料包括79%-98%的氧化锆、2%-8%的氧化钇、0%-3%的氧化铪、0%-5%的增强剂和0%-5%的染色剂。通过将上述物质混合,得到陶瓷材料。进一步的,按质量含量计,陶瓷材料包括79%-94.4%的氧化锆、2%-8%的氧化钇、0.1%-3%的氧化铪、3%-5%的增强剂和0.5%-5%的染色剂。
38.在本技术中,混合液包括凝胶剂和助剂,其中凝胶剂用于在凝胶注模成型过程中在催化剂和引发剂的作用下产生凝胶固化,以获得陶瓷基板10,助剂用于改善材料以及溶液的性能,有助于后续凝胶固化的进行。
39.在本技术实施方式中,凝胶剂包括有机单体和交联剂中的至少一种。可以理解的,若有机单体在催化剂和引发剂的作用下能够产生凝胶固化,则凝胶剂中无需交联剂的加入,若有机单体需要在交联剂、催化剂和引发剂的作用下才能够产生凝胶固化,则凝胶剂中需要加入有机单体和交联剂。
40.在本技术中,有机单体可以在引发剂、催化剂作用下发生原位聚合形成高分子三维网络结构,使液态的混合浆料发生凝胶固化,使得陶瓷材料发生原位粘结。在一实施例中,有机单体包括丙烯酰胺、甲基丙烯酰胺、二甲基丙烯酰胺、海因环氧树脂和异丁烯-马来酸酐共聚物中的至少一种。其中,若采用异丁烯-马来酸酐共聚物时,凝胶剂中可以不加交联剂。在一实施例中,有机单体的质量占陶瓷材料质量的1.5%-4%,如1.5%、2%、2.5%、3%、3.5%或4%等。有机单体含量过少,不利于三维网状结构的形成,不利于陶瓷材料的分散和固定;有机单体含量过多,形成的三维网状结构过多,容易提高陶瓷基板10的气孔率;上述含量的有机单体既保证了陶瓷材料的分散和固定,又不会增加陶瓷基板10的气孔率,有利于陶瓷基板10强度一致性的提升。在一具体实施例中,有机单体的质量占陶瓷材料质量的1.5%-2.5%。在又一具体实施例中,有机单体的质量占陶瓷材料质量的2.5%-4%。
41.在本技术中,交联剂能够促进单体交联形成三维网状结构,并影响交联程度。在一实施例中,交联剂包括亚甲基双丙烯酰胺和膦酰基丁烷三羧酸中的至少一种。在一实施例中,交联剂的质量占陶瓷材料质量的0.1%-0.4%,如0.1%、0.15%、0.2%、0.25%、0.3%、0.35%或0.4%等。交联剂含量过多,有机单体形成的聚合物的链长过短,不利于陶瓷材料的分散和固定;交联剂含量过少,有机单体形成的三维网状结构不完整,也不利于陶瓷生坯强度的提升;采用上述含量的交联剂能够有效促进有机单体发生交联,形成适宜的三维网状结构,有利于陶瓷生坯强度的提升。在一具体实施例中,交联剂的质量占陶瓷材料质量的0.1%-0.2%。在又一具体实施例中,交联剂的质量占陶瓷材料质量的0.2%-0.4%。
42.在本技术实施例中,有机单体和交联剂的质量比为(10-20):1。如此,有利于三维网状结构的形成,使陶瓷材料均匀分散在其中,提高陶瓷生坯的强度,还有利于陶瓷基板10强度一致性的提升。具体的,有机单体和交联剂的质量比可以但不限于为10、12、15、17、19或20等。在一实施例中,有机单体和交联剂的质量比可以为(10-15):1。在一实施例中,有机单体和交联剂的质量比可以为(15-20):1。
43.在本技术实施方式中,助剂包括分散剂、消泡剂、表面活性剂和ph调节剂中的至少一种。
44.在本技术中,分散剂用于促进陶瓷材料均匀分散在预混浆料中,分散剂能够吸附在陶瓷材料颗粒的表面,使颗粒表面形成高分子层,高分子链延展至预混浆料中,从而阻碍了陶瓷材料颗粒之间的接触,同时使陶瓷材料表面的zeta电位变化,也使得陶瓷材料之间的团聚效应减弱,进一步避免了团聚的发生。在一实施例中,分散剂包括聚丙烯酸铵、聚丙烯酸、聚丙烯酸钠、聚乙烯醇和柠檬酸铵中的至少一种。在一实施例中,分散剂的质量占陶瓷材料质量的0.2%-0.5%,如0.2%、0.25%、0.3%、0.35%、0.4%、0.45%或0.5%等。采用上述含量的分散剂能够有效促进陶瓷材料的分散,防止团聚的发生,同时保证预混浆料
的粘度。在一具体实施例中,分散剂的质量占陶瓷材料质量的0.2%-0.3%。在又一具体实施例中,分散剂的质量占陶瓷材料质量的0.4%-0.5%。
45.在本技术中,消泡剂用于抑制混合液以及预混浆料中泡沫的形成。在一实施例中,消泡剂包括正辛醇、丙三醇和甘油聚氧乙烯醚中的至少一种。在一实施例中,消泡剂的质量占所述陶瓷材料质量的0.01%-0.05%,如0.01%、0.015%、0.02%、0.025%、0.03%、0.04%或0.05%等。采用上述含量的消泡剂能够保证有效去除混合液以及预混浆料的泡沫。在一具体实施例中,消泡剂的质量占所述陶瓷材料质量的0.01%-0.025%。在又一具体实施例中,消泡剂的质量占所述陶瓷材料质量的0.03%-0.05%。
46.在本技术中,表面活性剂可以降低陶瓷材料的表面能,改善预混浆料的流变性,有助于提升预混浆料的固含量,降低预混浆料的粘度,提高预混浆料的稳定性。在一实施例中,表面活性剂包括三乙醇胺、二乙醇胺、聚乙二醇、乙二醇和脂肪醇聚氧乙烯醚中的至少一种。在一实施例中,表面活性剂的质量占陶瓷材料质量的0.1%-0.3%,如0.1%、0.15%、0.2%、0.25%或0.3%等。采用上述含量的表面活性剂能够有效改善预混浆料的流变性。在一具体实施例中,表面活性剂的质量占陶瓷材料质量的0.1%-0.2%。在又一具体实施例中,表面活性剂的质量占陶瓷材料质量的0.2%-0.3%。
47.在本技术中,ph调节剂用于调节混合液的ph。在一实施例中,混合液的ph为碱性,有利于使混合液与陶瓷材料混合时,陶瓷材料表面吸附氢氧根离子,使陶瓷材料表面呈负电性,增加了zeta电位的绝对值,使得陶瓷材料更好地分散在混合液中,防止团聚的发生,有利于提升陶瓷基板10的强度以及强度一致性。具体的,ph调节剂可以为碱性溶液,如氨水、氢氧化钠溶液等。在一实施例中,混合液的ph值为9-12。如此,可以有效防止陶瓷材料的团聚。具体的,混合液的ph值可以但不限于为9、10、11或12等。
48.在本技术实施方式中,混合液中含有水;水作为溶剂,用于分散凝胶剂、助剂,同时在预混浆料中起到分散陶瓷材料的作用,保证预混浆料的固含量,水的添加量根据预混浆料所需固含量进行添加。在本技术中,陶瓷材料和混合液的混合比例,可以根据预混浆料所需固含量进行选择。
49.在本技术中,将陶瓷材料和混合液混合后,经过砂磨即可获得预混浆料。通过砂磨改善陶瓷材料的物理性能,同时改善预混浆料的性能。在本技术实施方式中,砂磨包括将陶瓷材料、混合液与砂磨介质混合进行研磨。具体的,砂磨介质的粒径可以为0.1mm-2mm,如0.1mm、0.5mm、1mm、1.5mm或2mm等,砂磨介质可以但不限于为氧化锆珠等。在一实施例中,砂磨的温度为5℃-15℃(如5℃、8℃、10℃、13℃或15℃等),砂磨的时间为4h-12h(如4h、5h、8h、10h或12h等)。通过控制砂磨过程中的温度以及时长,从而保证可以对预混浆料的性能进行改善,有利于提升陶瓷基板10的性能。具体的,还可以将砂磨后的浆料进行过筛,其中筛网的目数可以但不限于为1500目。
50.在本技术中,固含量为浆料中固体物质的体积占比。在一实施例中,预混浆料的固含量为40%-60%,如40%、45%、50%、55%或60%。固含量过低,陶瓷材料含量少,不利于陶瓷基板10强度的提高,同时水和有机物含量多,容易使陶瓷基板10内部残留大量气孔,提高了陶瓷基板10的内部缺陷;固含量过高,陶瓷材料含量多,容易发生团聚,提高陶瓷基板10内部缺陷,仍然会影响陶瓷基板10的强度。在一具体实施例中,预混浆料的固含量为40%-50%。在另一具体实施例中,预混浆料的固含量为50%-60%。在一实施例中,预混浆
料的粘度小于1000mpa
·
s。预混浆料的粘度小,流动性好,有利于在注模过程中浆料快速均匀地填充在模具内,并且有利于浆料中气泡的排出,降低陶瓷基板10内部的缺陷,提高陶瓷基板10的机械性能。在一实施例中,预混浆料中固体的一次颗粒粒径d50小于0.15μm,二次颗粒粒径d50小于0.4μm,比表面积小于5m2/g。可以理解的,通过将预混浆料中的液体烘干后进行测量固体的一次颗粒粒径d50、二次颗粒粒径d50以及比表面积,其中固体即为陶瓷材料。
51.在s102中,通过将预混浆料进行脱泡,从而降低预混浆料中的气泡含量,保证陶瓷基板10的低气孔率,有利于提高陶瓷基板10的强度以及强度一致性。在一实施例中,脱泡包括在真空度小于或等于-70kpa下脱泡10min-60min(如10min、15min、20min、30min、45min或60min等)。在高真空度下脱泡较长时间,可以快速去除预混浆料中的气泡,极大地降低预混浆料中的气泡含量。
52.在本技术中,催化剂用于提高交联聚合反应速率,缩短凝胶固化时间。在一实施例中,催化剂包括四甲基乙二胺和二甲基苯胺中的至少一种。在一实施例中,催化剂的质量占陶瓷材料质量的0.1%-1%,如0.1%、0.25%、0.3%、0.5%、0.6%、0.7%、0.8%或1%等。催化剂含量过低,混合浆料凝胶固化时间过长,陶瓷材料会发生沉降,从而造成陶瓷生坯密度分布不均匀,在干燥、烧结过程中会发生变形,影响陶瓷基板10使用;催化剂含量过高,混合浆料凝胶固化时间过短,在注模过程中气泡无法排出,影响陶瓷基板10的性能;采用上述含量的催化剂能够保证避免出现上述不良,有利于陶瓷基板10性能的提升。在一具体实施例中,催化剂的质量占陶瓷材料质量的0.3%-0.5%。如此,能够保证凝胶固化时间在15min-20min,保证注模时间,又可以避免陶瓷材料发生沉降。在又一具体实施例中,催化剂的质量占陶瓷材料质量的0.6%-1%。
53.在本技术中,引发剂用于产生自由基,充足的自由基能够引发有机单体与交联剂的聚合反应,促进凝胶固化。在一实施例中,引发剂包括过硫酸铵、二氨基二丙胺和过氧化苯甲酰中的至少一种。在一实施例中,引发剂的质量占陶瓷材料质量的0.3%-1%,如0.3%、0.4%、0.5%、0.6%、0.7%、0.8%、0.9%或1%等。引发剂含量过低,有机单体无法完全参加凝胶固化反应,形成的三维网状结构骨架不完全;引发剂含量过高,聚合反应初期反应过快,不利于形成长链结构,影响陶瓷生坯的强度,容易在干燥、烧结过程中产生裂纹,影响陶瓷基板10的性能;采用上述含量的引发剂能够保证避免出现上述不良,有利于陶瓷基板10性能的提升。在一具体实施例中,引发剂的质量占陶瓷材料质量的0.5%-0.8%。如此,能够保证凝胶固化时间在15min-20min,保证注模时间,又可以避免陶瓷材料发生沉降。在又一具体实施例中,引发剂的质量占陶瓷材料质量的0.3%-0.4%。
54.在本技术中,在预混浆料脱泡后加入催化剂和引发剂,经搅拌均匀后即可得到混合浆料。其中搅拌时间不宜过长,否则会增加混合浆料的粘度,甚至开始发生凝胶固化。具体的,搅拌时间可以小于5min,如搅拌1min、2min、3min或4min等。在本技术中,催化剂和引发剂的加入不会过多影响预混浆料的固含量和粘度。在一实施例中,混合浆料的固含量为40%-60%,如40%、45%、50%、55%或60%。在一具体实施例中,混合浆料的固含量为40%-50%。在另一具体实施例中,混合浆料的固含量为50%-60%。在一实施例中,混合浆料的粘度小于1000mpa
·
s。在一实施例中,混合浆料中固体的一次颗粒粒径d50小于0.15μm,二次颗粒粒径d50小于0.5μm。可以理解的,通过将混合浆料中的液体烘干后进行测量固
体的一次颗粒粒径d50和二次颗粒粒径d50,其中固体即为陶瓷材料。
55.在s103中,混合浆料经凝胶注模成型后获得陶瓷预坯,陶瓷预坯经过干燥后得到陶瓷生坯,陶瓷生坯经排胶和烧结后得到陶瓷基板10。在一实施例中,凝胶注模成型的过程包括将混合浆料注入模具中,经固化、脱模后制得陶瓷预坯。可以理解的,通过将混合浆料注入模具有利于获得所需形状的陶瓷基板10。在一具体实施例中,可以利用自动注浆机将混合浆料注入模具中,浆料从模具进料口注入,浆料从排气口溢出后停止注浆,注浆全程时长短,避免影响凝胶固化的进行。具体的,注浆全程时长可以小于3min;模具的材质可以为玻璃、金属、塑胶中的至少一种,例如可以选择玻璃模具;模腔的表面粗糙度可以小于1μm,有利于降低陶瓷基板10的表面粗糙度,提高陶瓷基板10的表面质量。
56.在本技术一实施例中,凝胶注模成型的温度为30℃-90℃(如30℃、40℃、50℃、60℃、70℃、80℃或90℃等),时间为10min-30min(如10min、15min、20min、25min或30min等)。凝胶注模成型的温度过低,成型时间过长,陶瓷材料容易发生沉降,导致陶瓷预坯的密度分布不均匀,在干燥和烧结过程中会发生变形,影响陶瓷基板10的使用;凝胶注模成型的温度过高,成型时间过短,不利于混合浆料在模具中的均匀分布以及气泡的排出;采用上述凝胶注模成型条件,有利于凝胶固化的进行,同时负压有利于气泡的排出。在一实施例中,可以将混合浆料注入模具,模具的温度为30℃-90℃,模具的模腔的真空度为-100kpa~-10kpa(如-100kpa、-80kpa、-60kpa、-50kpa、-30kpa或-10kpa等),混合浆料在模具中静置固化10min-30min,制得陶瓷预坯。采用上述模腔的真空度,有利于混合浆料的注入以及气泡的排出。可选的,模具的温度为30℃-50℃,模具的模腔的真空度为-100kpa~-60kpa;或模具的温度为60℃-90℃,模具的模腔的真空度为-60kpa~-10kpa。
57.在本技术一实施例中,干燥工艺包括在湿度为70%-90%(如70%、75%、80%、85%或90%等)、30℃-50℃(如30℃、35℃、40℃、45℃或50℃等)下处理12h-24h(如12h、15h、17h、20h或22h等),再置于湿度20%-50%(如20%、25%、30%、40%或50%等)、80℃-120℃(如80℃、90℃、100℃、110℃或120℃等)下处理6h-12h(如6h、7h、8h、10h或11h等)。通过在较高湿度以及较低温度下进行干燥,使陶瓷预坯表层的水进行缓慢均匀地脱除,从而去除表层的自由水;再在低湿度以及较高温度下干燥,去除陶瓷预坯内部的自由水以及部分的吸附水,从而使陶瓷预坯整体得到干燥,获得陶瓷生坯;该陶瓷生坯的含水量低,同时表面无明显龟裂、起皮等问题,表面质量好。在一实施例中,干燥工艺包括在湿度为80%-90%、30℃-40℃下处理15h-20h,再置于湿度20%-30%、100℃-120℃下处理6h-10h。在另一实施例中,干燥工艺包括在湿度为70%-80%、40℃-50℃下处理12h-15h,再置于湿度30%-50%、80℃-100℃下处理10h-12h。
58.在本技术另一实施例中,干燥工艺包括在含亲水性有机溶剂的溶液中浸泡3h-12h(如3h、5h、8h、10h或12h等),浸泡温度为10℃-50℃(如10℃、20℃、30℃、40℃或50℃等);再在湿度为70%-90%(如70%、75%、80%、85%或90%等)、30℃-50℃(如30℃、35℃、40℃、45℃或50℃等)下处理12h-24h(如12h、15h、17h、20h或22h等);然后在湿度20%-50%(如20%、25%、30%、40%或50%等)、60℃-120℃(如60℃、70℃、80℃、90℃、100℃、110℃或120℃等)下处理6h-12h(如6h、7h、8h、10h或11h等)。通过在含亲水性有机溶剂的溶液中浸泡,使陶瓷预坯中的水分被亲水性有机溶剂置换处理,脱除陶瓷预坯表面的部分自由水;再在较高湿度以及较低温度下进行干燥,使陶瓷预坯表层的部分自由水以及吸附的含亲水性
有机溶剂脱除;最后在低湿度以及较高温度下干燥,去除陶瓷预坯内部的自由水以及部分的吸附水,从而使陶瓷预坯整体得到干燥,获得陶瓷生坯;该陶瓷生坯的含水量低,表面无龟裂、起皮等问题,表面质量佳。在一实施例中,含亲水性有机溶剂的溶液中含亲水性有机溶剂的质量含量为50%-100%(如50%、60%、70%、80%、90%或100%等),从而有利于将陶瓷预坯表面的自由水更多地置换出来。在一实施例中,含亲水性有机溶剂可以包括甲醇、乙醇、丙醇、甲乙酮和丙酮中的至少一种,从而有利于自由水的置换,同时又不会影响陶瓷生坯的性能。
59.在本技术中,干燥可以在恒湿恒温干燥箱中进行。在一实施例中,陶瓷生坯的含水率小于3%,即陶瓷生坯中水的质量占比小于3%,有利于陶瓷基板10性能的提升。具体的,陶瓷生坯的含水率小于2.5%、小于2%或小于1%等。
60.在一实施例中,排胶包括在400℃-600℃处理2h-4h,烧结包括在1300℃-1500℃处理1h-2h。具体的,排胶的温度可以但不限于400℃、450℃、500℃、550℃或600℃,排胶的时间可以但不限于为2h、2.5h、3h、3.5h或4h,以保证在排胶过程中,陶瓷生坯不会发生开裂;烧结的温度可以但不限于为1300℃、1350℃、1380℃、1400℃、1450℃、1470℃或1500℃,烧结的时间可以但不限于为1h、1.5h或2h,以保证陶瓷生坯内部结合强度和致密性的提高。通过排胶和烧结,去除陶瓷生坯中的有机成分,同时增强内部的致密性和结合强度,以提高陶瓷基板10的性能。
61.在本技术实施方式中,对陶瓷原料进行煅烧得到陶瓷材料。其中,陶瓷原料与陶瓷材料的材质相同,区别仅在于一次颗粒粒径、二次颗粒粒径以及颗粒的比表面积不同。
62.请参阅图2,为本技术另一实施方式提供的壳体的制备方法流程示意图,包括:
63.s201:氧化锆进行煅烧后与氧化钇、氧化铪、增强剂、染色剂混合,得到陶瓷材料,陶瓷材料的一次颗粒粒径d50小于0.15μm,二次颗粒粒径d50小于0.5μm,比表面积小于8m2/g。
64.s202:将陶瓷材料和混合液混合后进行砂磨得到预混浆料,混合液包括凝胶剂和助剂。
65.s203:预混浆料脱泡后加入催化剂和引发剂,得到混合浆料。
66.s204:混合浆料经凝胶注模成型、干燥、排胶和烧结后得到陶瓷基板,陶瓷基板的气孔率小于0.3%,韦伯模量大于10,制得壳体。
67.其中,s202、s203、s204参考s101、s102、s103的描述,在此不再赘述。
68.请参阅图3,为本技术又一实施方式提供的壳体的制备方法流程示意图,包括:
69.s301:氧化锆、氧化钇、氧化铪、增强剂和染色剂混合后进行煅烧,得到陶瓷材料,陶瓷材料的一次颗粒粒径d50小于0.15μm,二次颗粒粒径d50小于0.5μm,比表面积小于8m2/g。
70.s302:将陶瓷材料和混合液混合后进行砂磨得到预混浆料,混合液包括凝胶剂和助剂。
71.s303:预混浆料脱泡后加入催化剂和引发剂,得到混合浆料。
72.s304:混合浆料经凝胶注模成型、干燥、排胶和烧结后得到陶瓷基板,陶瓷基板的气孔率小于0.3%,韦伯模量大于10,制得壳体。
73.其中,s302、s303、s304参考s101、s102、s103的描述,在此不再赘述。
74.在本技术中,通过煅烧对颗粒进行了改性,降低了颗粒的比表面积同时改善了颗粒的一次颗粒粒径和二次颗粒粒径,使得陶瓷材料更容易在混合液中均匀分散,可以有效避免颗粒的团聚,从而形成高固含量、低粘度的预混浆料,进而有助于降低陶瓷基板10的内部缺陷,形成具有优异机械性能的陶瓷基板10;此外,煅烧能够将颗粒表面存在的有机杂质去除,避免有机杂质对陶瓷材料与混合液混合的影响,保证预混浆料的稳定性。在本技术实施方式中,煅烧的温度为300℃-600℃,时间为1h-2h。煅烧温度过低、时间过短,则达不到煅烧效果,无法降低颗粒的比表面积,无法完全去除有机杂质;煅烧温度过高、时间过长,则容易使颗粒之间形成硬团聚,反而增加了陶瓷基板10内部的缺陷,不利于陶瓷基板10性能的提升;因此,采用上述煅烧工艺既能够保证形成所需尺寸的陶瓷材料,同时还可以使颗粒均匀分散,有助于降低陶瓷基板10的内部缺陷,提升陶瓷基板10的机械性能。在本技术中,煅烧的温度可以但不限于为300℃、350℃、400℃、450℃、500℃、550℃或600℃等,煅烧的时间可以但不限于为60min、70min、80min、90min、100min、110min或120min等。在一实施例中,煅烧的温度为300℃-400℃,时间为1.5h-2h。在另一实施例中,煅烧的温度为500℃-600℃,时间为1h-1.5h。在又一实施例中,氧化锆进行煅烧后与氧化钇、氧化铪、增强剂、染色剂混合;或氧化锆、氧化钇、氧化铪、增强剂和染色剂混合后进行煅烧,得到陶瓷材料,其中,煅烧的温度为300℃-600℃,时间为1h-2h,得到的陶瓷材料的一次颗粒粒径d50小于0.15μm,二次颗粒粒径d50小于0.5μm,比表面积小于8m2/g,其中,氧化锆的比表面积大于陶瓷材料的比表面积。
75.在本技术实施方式中,可以对陶瓷基板10进行cnc加工、喷砂、抛光等处理,以获得所需形状、表面性能的陶瓷基板10;还可以陶瓷基板10进行镭雕、镀膜等处理,以改变陶瓷基板10的外观效果。在本技术实施例中,在陶瓷基板10的表面涂覆保护液,经固化后形成保护层20,制备壳体100。壳体100在使用过程中具有相对设置的内表面和外表面,保护层20位于外表面一侧,从而在壳体100的使用中起到保护作用。保护层20对陶瓷基板10起到保护作用。具体的,保护层20的厚度可以但不限于为5nm-20nm,如5nm、8nm、10nm、13nm、15nm、18nm或20nm等。在一实施例中,保护液可以包括防指纹剂和硬化液中的至少一种,以形成防指纹层和硬化层中的至少一层。具体的,硬化层的材质可以包括聚氨酯丙烯酸酯、有机硅树脂、全氟聚醚丙烯酸酯中的至少一种;抗指纹层的接触角可以大于105
°
,从而避免对其表面的污染,具有优异的抗指纹的性能;抗指纹层可以包括含氟化合物,如氟硅树脂、全氟聚醚、含氟丙烯酸酯等,抗指纹层还包括二氧化硅,通过添加二氧化硅进一步提升抗指纹层的耐摩擦性能。
76.在本技术中,陶瓷基板10的气孔率小于0.3%,韦伯模量大于10。通过上述方法制得的陶瓷基板10气孔率低,降低了内部缺陷,同时韦伯模量大,表明陶瓷基板10的强度离散性小,强度一致性高,性能优异。进一步的,陶瓷基板10的气孔率小于或等于0.15%,韦伯模量大于10.5。更进一步的,陶瓷基板10的气孔率小于或等于0.12%,韦伯模量大于12。在一实施例中,陶瓷基板10的四点抗弯强度大于1100mpa。可以理解的,陶瓷基板10的四点抗弯强度为多次测量的平均值。进一步的,陶瓷基板10的四点抗弯强度大于1150mpa。在一实施例中,陶瓷基板10的特征强度大于1150mpa,表明陶瓷基板10具有优异的机械性能且强度一致性高。进一步的,陶瓷基板10的特征强度大于1200mpa。在一实施例中,陶瓷基板10中晶粒粒径小于400nm。可以理解的,晶粒粒径为测量的平均值。陶瓷基板10中晶粒粒径细小,有利
于提高内部结构的致密性,进而提升陶瓷基板10的性能。进一步的,陶瓷基板10中晶粒粒径小于350nm。更进一步的,陶瓷基板10中晶粒粒径小于340nm。
77.在本技术中,根据gb/t 6569-2006《精细陶瓷弯曲强度试验方法》检测四点弯曲强度,本技术中的四点弯曲强度为多次检测的平均值,有效数据不小于32个;根据不小于32个的四点弯曲强度有效数据,采用minitab、weibull 模块等软件进行统计分析,陶瓷基板10在失效概率为63.2%时对应的四点弯曲强度;根据gb/t 40005-2021《精细陶瓷强度数据的韦布尔统计分析方法》获得韦伯模量,其中样本容量不小于32个,置信区间90%;通过扫描电镜拍照并进行统计,获得颗粒的一次颗粒粒径d50,其中统计的颗粒数量不小于100个;通过激光粒度分布仪获得颗粒的二次颗粒粒径d50;通过比表面积测试仪获得颗粒的比表面积;通过扫描电镜对陶瓷基板10截面拍照并进行统计,获得晶粒粒径,其中统计的晶粒数量不小于100个;根据gb/t 25995-2010《精细陶瓷密度和显气孔率试验方法》检测气孔率;通过含水率测定仪获得含水率。
78.在本技术中,陶瓷基板10的厚度和形状可以根据壳体100需要进行选择,壳体100可以作为电子设备200的外壳、中框、按键帽等,如作为手机、平板电脑、笔记本电脑、手表、mp3、mp4、gps导航仪、数码相机的外壳等。在本技术中,陶瓷基板10和壳体100可以为2d结构、2.5d结构、3d结构等。在一实施例中,壳体100作为手机后盖使用时,陶瓷基板10的厚度可以为0.5mm-1mm,如0.5mm、0.6mm、0.7mm、0.8mm、0.9mm或1mm等。
79.在本技术提供的壳体100的制备方法操作简单,可以获得性能优异的陶瓷基板10,从而提高壳体100的性能,有利于扩大壳体100的应用范围。
80.请参阅图4,为本技术一实施方式提供的壳体的结构示意图,壳体100包括陶瓷基板10,陶瓷基板10的气孔率小于0.3%,韦伯模量大于10。该陶瓷基板10的气孔率低,强度一致性高,具有优异的性能。
81.在本技术实施方式中,壳体100可以通过上述任一实施方式所述的壳体100的制备方法制得。
82.在本技术实施方式中,陶瓷基板10为氧化锆陶瓷。氧化锆陶瓷有利于提高壳体100的机械性能。在一实施例中,氧化锆陶瓷中氧化锆的质量含量为79%-98%。具体的,氧化锆陶瓷中氧化锆的质量含量可以但不限于为79%、80%、82%、85%、88%、90%、92%、95%或98%等。在一实施例中,陶瓷基板10中四方相氧化锆占氧化锆质量的70%以上,如此,有利于提高陶瓷基板10的结构稳定性以及机械性能。在一实施例中,氧化锆陶瓷还包括氧化钇、氧化铪、增强剂和染色剂中的至少一种。其中,氧化钇、氧化铪、增强剂和染色剂的含量、增强剂和染色剂材质的选择根据上述s101部分的描述,在此不再赘述。在一具体实施例中,按质量含量计,氧化锆陶瓷还包括2%-8%的氧化钇、0%-3%的氧化铪、0%-5%的增强剂和0%-5%的染色剂。
83.请参阅图5,为本技术另一实施方式提供的壳体的结构示意图,壳体100还包括保护层20,保护层20设置在陶瓷基板10的表面。在一实施例中,保护层20包括防指纹层和硬化层中的至少一层。
84.本技术还提供了一种电子设备200,包括上述任一实施方式中的壳体100。可以理解的,电子设备200可以但不限于为手机、平板电脑、笔记本电脑、手表、mp3、mp4、gps导航仪、数码相机等。请参阅图6,为本技术一实施方式提供的电子设备的结构示意图,其中,电
子设备200包括壳体100。该壳体100可以提升电子设备200的机械性能,并且电子设备200具有陶瓷质感的外观,具有优异的产品竞争力。请参阅图7,为本技术一实施方式提供的电子设备的结构组成示意图,电子设备200的结构可以包括rf电路210、存储器220、输入单元230、显示单元240、传感器250、音频电路260、wifi模块270、处理器280以及电源290等。其中,rf电路210、存储器220、输入单元230、显示单元240、传感器250、音频电路260、wifi模块270分别与处理器280连接;电源290用于为整个电子设备200提供电能。具体而言,rf电路210用于接发信号;存储器220用于存储数据指令信息;输入单元230用于输入信息,具体可以包括触控面板以及操作按键等其他输入设备;显示单元240可以包括显示屏等;传感器250包括红外传感器、激光传感器等,用于检测用户接近信号、距离信号等;扬声器261以及传声器262通过音频电路260与处理器280连接,用于接发声音信号;wifi模块270则用于接收和发射wifi信号;处理器280用于处理电子设备200的数据信息。
85.以下通过具体实施例及对比例对本技术提供的壳体的性能做进一步的说明。
86.实施例1
87.按质量含量计,陶瓷材料包括87.8%的氧化锆、5.2%的氧化钇、2%的氧化铪、1.5%的增强剂(包括0.5%的氧化钛、0.4%的氧化硅以及0.6%的氧化锗)和3.5%的染色剂(包括0.9%的氧化铝、0.8%的氧化锌、1%的氧化钴以及0.8%的二氧化三铁),其中,氧化锆的一次颗粒粒径d50为0.08μm,二次颗粒粒径d50为0.21μm,比表面积为12m2/g。将陶瓷材料在400℃煅烧2h,煅烧后的陶瓷材料的一次颗粒粒径d50为0.11μm,二次颗粒粒径d50为0.28μm,比表面积为6.5m2/g。
88.将有机单体甲基丙烯酰胺(添加量为陶瓷材料质量的1.5%)、有机单体二甲基丙烯酰胺(添加量为陶瓷材料质量的1%)、交联剂亚甲基双丙烯酰胺(添加量为陶瓷材料质量的0.2%)、分散剂聚丙烯酸铵(添加量为陶瓷材料质量的0.4%)、消泡剂正辛醇(添加量为陶瓷材料质量的0.02%)、表面活性剂三乙醇胺(添加量为陶瓷材料质量的0.1%)、表面活性剂脂肪醇聚氧乙烯醚(添加量为陶瓷材料质量的0.1%)加入去离子水中,然后加入ph调节剂氨水调节ph,得到混合液,混合液ph值为11。
89.将煅烧后的陶瓷材料和混合液混合经砂磨后得到预混浆料,预混浆料的固含量为55%,粘度为467mpa
·
s,一次颗粒粒径d50为0.11μm,二次颗粒粒径d50为0.32μm,比表面积为4.5m2/g。
90.在真空度-75kpa条件下,预混浆料脱泡30min,然后向预混浆料中加入催化剂四甲基乙二胺(添加量为陶瓷材料质量的0.4%)和引发剂过硫酸铵(添加量为陶瓷材料质量的0.6%),经搅拌得到混合浆料,混合浆料的固含量为54%,粘度为687mpa
·
s,一次颗粒粒径d50为0.11μm,二次颗粒粒径d50为0.34μm。
91.利用自动注浆机将混合浆料注入模具中,浆料从模具进料口注入,浆料从排气口溢出后停止注浆,模具温度为50℃,模腔的真空度为-75kpa,完成注浆后静置固化20min使混合浆料固化。然后将固化后的混合浆料脱模,得到陶瓷预坯。将陶瓷预坯置于湿度为85%、40℃下处理24h,再置于湿度40%、115℃下处理10h,得到陶瓷生坯,陶瓷生坯的含水率为2.5%。陶瓷生坯在600℃下排胶2h,再在1450℃下烧结1.5h,得到陶瓷基板,即为壳体。
92.请参阅图8,为陶瓷基板晶粒的显微镜形貌图,可以看出,晶粒粒径均匀、细小,整体组织致密,无气孔、裂纹等缺陷;同时对陶瓷基板的性能进行检测,其中,陶瓷基板的气孔
率为0.12%,平均晶粒粒径为342nm,四点抗弯强度为1147mpa,特征强度为1186mpa,韦伯模量为13.2。
93.实施例2
94.按质量含量计,陶瓷材料包括87.8%的氧化锆、5.2%的氧化钇、2%的氧化铪、1.5%的增强剂(包括0.5%的氧化钛、0.4%的氧化硅以及0.6%的氧化锗)和3.5%的染色剂(包括0.9%的氧化铝、0.8%的氧化锌、1%的氧化钴以及0.8%的二氧化三铁),其中,氧化锆的一次颗粒粒径d50为0.08μm,二次颗粒粒径d50为0.21μm,比表面积为12m2/g。将陶瓷材料在400℃煅烧2h,煅烧后的陶瓷材料的一次颗粒粒径d50为0.11μm,二次颗粒粒径d50为0.28μm,比表面积为6.5m2/g。
95.将有机单体二甲基丙烯酰胺(添加量为陶瓷材料质量的1%)、交联剂亚甲基双丙烯酰胺(添加量为陶瓷材料质量的0.2%)、分散剂聚丙烯酸铵(添加量为陶瓷材料质量的0.4%)、消泡剂正辛醇(添加量为陶瓷材料质量的0.02%)、表面活性剂三乙醇胺(添加量为陶瓷材料质量的0.1%)、表面活性剂脂肪醇聚氧乙烯醚(添加量为陶瓷材料质量的0.1%)加入去离子水中,然后加入ph调节剂氨水调节ph,得到混合液,混合液ph值为11。
96.将煅烧后的陶瓷材料和混合液混合经砂磨后得到预混浆料,预混浆料的固含量为55%,粘度为467mpa
·
s,一次颗粒粒径d50为0.11μm,二次颗粒粒径d50为0.32μm,比表面积为4.5m2/g。
97.在真空度-75kpa条件下,预混浆料脱泡30min,然后向预混浆料中加入催化剂四甲基乙二胺(添加量为陶瓷材料质量的0.4%)和引发剂过硫酸铵(添加量为陶瓷材料质量的0.6%),经搅拌得到混合浆料,混合浆料的固含量为54%,粘度为687mpa
·
s,一次颗粒粒径d50为0.11μm,二次颗粒粒径d50为0.34μm。
98.利用自动注浆机将混合浆料注入模具中,浆料从模具进料口注入,浆料从排气口溢出后停止注浆,模具温度为50℃,模腔的真空度为-75kpa,完成注浆后静置固化20min使混合浆料固化。然后将固化后的混合浆料脱模,得到陶瓷预坯。将陶瓷预坯置于湿度为85%、40℃下处理24h,再置于湿度40%、115℃下处理10h,得到陶瓷生坯,陶瓷生坯的含水率为2.4%。陶瓷生坯在600℃下排胶2h,再在1450℃下烧结1.5h,得到陶瓷基板,即为壳体。
99.请参阅图9,为陶瓷基板晶粒的显微镜形貌图,可以看出,晶粒粒径均匀、细小,整体组织致密,无明显气孔、裂纹等缺陷;同时对陶瓷基板的性能进行检测,其中,陶瓷基板的气孔率为0.18%,平均晶粒粒径为348nm,四点抗弯强度为1025mpa,特征强度为1062mpa,韦伯模量为10.2。
100.实施例3
101.按质量含量计,陶瓷材料包括90.2%的氧化锆、4.3%的氧化钇、2%的氧化铪、1.5%的增强剂(包括0.5%的氧化钛、0.4%的氧化硅以及0.6%的氧化锗)和2%的氧化铝染色剂,其中,氧化锆的一次颗粒粒径d50为0.06μm,二次颗粒粒径d50为0.2μm,比表面积为15m2/g。将陶瓷材料在500℃煅烧1h,煅烧后的陶瓷材料的一次颗粒粒径d50为0.09μm,二次颗粒粒径d50为0.32μm,比表面积为7.4m2/g。
102.将有机单体二甲基丙烯酰胺(添加量为陶瓷材料质量的2%)、交联剂亚甲基双丙烯酰胺(添加量为陶瓷材料质量的0.1%)、交联剂膦酰基丁烷三羧酸(添加量为陶瓷材料质量的0.05%)、分散剂聚丙烯酸铵(添加量为陶瓷材料质量的0.2%)、分散剂聚乙烯醇(添加
量为陶瓷材料质量的0.2%)、消泡剂甘油聚氧乙烯醚(添加量为陶瓷材料质量的0.02%)、表面活性剂二乙醇胺(添加量为陶瓷材料质量的0.2%)加入去离子水中,然后加入ph调节剂氨水调节ph,得到混合液,混合液ph值为12。
103.将煅烧后的陶瓷材料和混合液混合经砂磨后得到预混浆料,预混浆料的固含量为50%,粘度为724mpa
·
s,一次颗粒粒径d50为0.09μm,二次颗粒粒径d50为0.37μm,比表面积为4.5m2/g。
104.在真空度-75kpa条件下,预混浆料脱泡30min,然后向预混浆料中加入催化剂四甲基乙二胺(添加量为陶瓷材料质量的0.5%)、引发剂过硫酸铵(添加量为陶瓷材料质量的0.4%)和引发剂二氨基二丙胺(添加量为陶瓷材料质量的0.2%),经搅拌得到混合浆料,混合浆料的固含量为49%,粘度为904mpa
·
s,一次颗粒粒径d50为0.09μm,二次颗粒粒径d50为0.42μm。
105.利用自动注浆机将混合浆料注入模具中,浆料从模具进料口注入,浆料从排气口溢出后停止注浆,模具温度为60℃,模腔的真空度为-75kpa,完成注浆后静置固化20min使混合浆料固化。然后将固化后的混合浆料脱模,得到陶瓷预坯。将陶瓷预坯置于湿度为85%、40℃下处理24h,再置于湿度40%、115℃下处理10h,得到陶瓷生坯,陶瓷生坯的含水率为2.1%。陶瓷生坯在600℃下排胶2h,再在1420℃下烧结1.5h,得到陶瓷基板,即为壳体。
106.请参阅图10,为陶瓷基板晶粒的显微镜形貌图,可以看出,晶粒粒径均匀、细小,整体组织致密,无明显气孔、裂纹等缺陷;同时对陶瓷基板的性能进行检测,其中,陶瓷基板的气孔率为0.15%,平均晶粒粒径为320nm,四点抗弯强度为1171mpa,特征强度为1224mpa,韦伯模量为10.7。
107.对比例1
108.按质量含量计,陶瓷材料包括87.8%的氧化锆、5.2%的氧化钇、2%的氧化铪、1.5%的增强剂(包括0.5%的氧化钛、0.4%的氧化硅以及0.6%的氧化锗)和3.5%的染色剂(包括0.9%的氧化铝、0.8%的氧化锌、1%的氧化钴以及0.8%的二氧化三铁),其中,氧化锆的一次颗粒粒径d50为0.08μm,二次颗粒粒径d50为0.21μm,比表面积为12m2/g。
109.将有机单体甲基丙烯酰胺(添加量为陶瓷材料质量的1.5%)、有机单体二甲基丙烯酰胺(添加量为陶瓷材料质量的1%)、交联剂亚甲基双丙烯酰胺(添加量为陶瓷材料质量的0.2%)、分散剂聚丙烯酸铵(添加量为陶瓷材料质量的0.4%)、消泡剂正辛醇(添加量为陶瓷材料质量的0.02%)、表面活性剂三乙醇胺(添加量为陶瓷材料质量的0.1%)、表面活性剂脂肪醇聚氧乙烯醚(添加量为陶瓷材料质量的0.1%)加入去离子水中,然后加入ph调节剂氨水调节ph,得到混合液,混合液ph值为11。
110.将陶瓷材料和混合液混合经砂磨后得到预混浆料,预混浆料的固含量为55%,粘度为1480mpa
·
s,一次颗粒粒径d50为0.07μm,二次颗粒粒径d50为0.19μm,比表面积为10.8m2/g。
111.在真空度-75kpa条件下,预混浆料脱泡30min,然后向预混浆料中加入催化剂四甲基乙二胺(添加量为陶瓷材料质量的0.4%)和引发剂过硫酸铵(添加量为陶瓷材料质量的0.6%),经搅拌得到混合浆料,混合浆料的固含量为54%,粘度为1650mpa
·
s,一次颗粒粒径d50为0.07μm,二次颗粒粒径d50为0.28μm。
112.利用自动注浆机将混合浆料注入模具中,浆料从模具进料口注入,浆料从排气口
溢出后停止注浆,模具温度为50℃,模腔的真空度为-75kpa,完成注浆后静置固化20min使混合浆料固化。然后将固化后的混合浆料脱模,得到陶瓷预坯。将陶瓷预坯置于湿度为85%、40℃下处理24h,再置于湿度40%、115℃下处理10h,得到陶瓷生坯,陶瓷生坯的含水率为2.5%。陶瓷生坯在600℃下排胶2h,再在1450℃下烧结1.5h,得到陶瓷基板,即为壳体。
113.请参阅图11,为陶瓷基板晶粒的显微镜形貌图,可以看出整体组织不均匀,有异常长大的晶粒,有较多气孔;同时对陶瓷基板的性能进行检测,其中,陶瓷基板的气孔率为0.37%,平均晶粒粒径为307nm,最大晶粒粒径超过1μm,四点抗弯强度为740mpa,特征强度为810mpa,韦伯模量为5.4,强度数据离散性大。
114.对比例2
115.按质量含量计,陶瓷材料包括90.2%的氧化锆、4.3%的氧化钇、2%的氧化铪、1.5%的增强剂(包括0.5%的氧化钛、0.4%的氧化硅以及0.6%的氧化锗)和2%的氧化铝染色剂,其中,氧化锆的一次颗粒粒径d50为0.06μm,二次颗粒粒径d50为0.2μm,比表面积为15m2/g。将陶瓷材料在800℃煅烧2h,煅烧后的陶瓷材料的一次颗粒粒径d50为0.18μm,二次颗粒粒径d50为0.91μm,比表面积为3.4m2/g。
116.将有机单体二甲基丙烯酰胺(添加量为陶瓷材料质量的2%)、交联剂亚甲基双丙烯酰胺(添加量为陶瓷材料质量的0.1%)、交联剂膦酰基丁烷三羧酸(添加量为陶瓷材料质量的0.05%)、分散剂聚丙烯酸铵(添加量为陶瓷材料质量的0.2%)、分散剂聚乙烯醇(添加量为陶瓷材料质量的0.2%)、消泡剂甘油聚氧乙烯醚(添加量为陶瓷材料质量的0.02%)、表面活性剂二乙醇胺(添加量为陶瓷材料质量的0.2%)加入去离子水中,然后加入ph调节剂氨水调节ph,得到混合液,混合液ph值为12。
117.将煅烧后的陶瓷材料和混合液混合经砂磨后得到预混浆料,预混浆料的固含量为50%,粘度为210mpa
·
s,一次颗粒粒径d50为0.1μm,二次颗粒粒径d50为1.1μm,比表面积为3.1m2/g。
118.在真空度-75kpa条件下,预混浆料脱泡30min,然后向预混浆料中加入催化剂四甲基乙二胺(添加量为陶瓷材料质量的0.5%)、引发剂过硫酸铵(添加量为陶瓷材料质量的0.4%)和引发剂二氨基二丙胺(添加量为陶瓷材料质量的0.2%),经搅拌得到混合浆料,混合浆料的固含量为49%,粘度为410mpa
·
s,一次颗粒粒径d50为0.18μm,二次颗粒粒径d50为1.28μm。
119.利用自动注浆机将混合浆料注入模具中,浆料从模具进料口注入,浆料从排气口溢出后停止注浆,模具温度为60℃,模腔的真空度为-75kpa,完成注浆后静置固化20min使混合浆料固化。然后将固化后的混合浆料脱模,得到陶瓷预坯。将陶瓷预坯置于湿度为85%、40℃下处理24h,再置于湿度40%、115℃下处理10h,得到陶瓷生坯,陶瓷生坯的含水率为2%。陶瓷生坯在600℃下排胶2h,再在1420℃下烧结1.5h,得到陶瓷基板,即为壳体。
120.请参阅图12,为陶瓷基板晶粒的显微镜形貌图,可以看出整体组织不均匀,有异常长大的晶粒和气孔缺陷;同时对陶瓷基板的性能进行检测,其中,陶瓷基板的气孔率为0.57%,平均晶粒粒径为370nm,最大晶粒粒径超过1μm,四点抗弯强度为817mpa,特征强度为840mpa,韦伯模量为4.1,强度数据离散性大。由上述可以看出,相较于对比例,本技术提供方法制得的陶瓷基板的气孔率低、韦氏模量高,具有强度以及强度一致性佳,性能优异,更有利于壳体的应用。
121.以上对本技术实施方式所提供的内容进行了详细介绍,本文对本技术的原理及实施方式进行了阐述与说明,以上说明只是用于帮助理解本技术的方法及其核心思想;同时,对于本领域的一般技术人员,依据本技术的思想,在具体实施方式及应用范围上均会有改变之处,综上所述,本说明书内容不应理解为对本技术的限制。
再多了解一些
本文用于企业家、创业者技术爱好者查询,结果仅供参考。