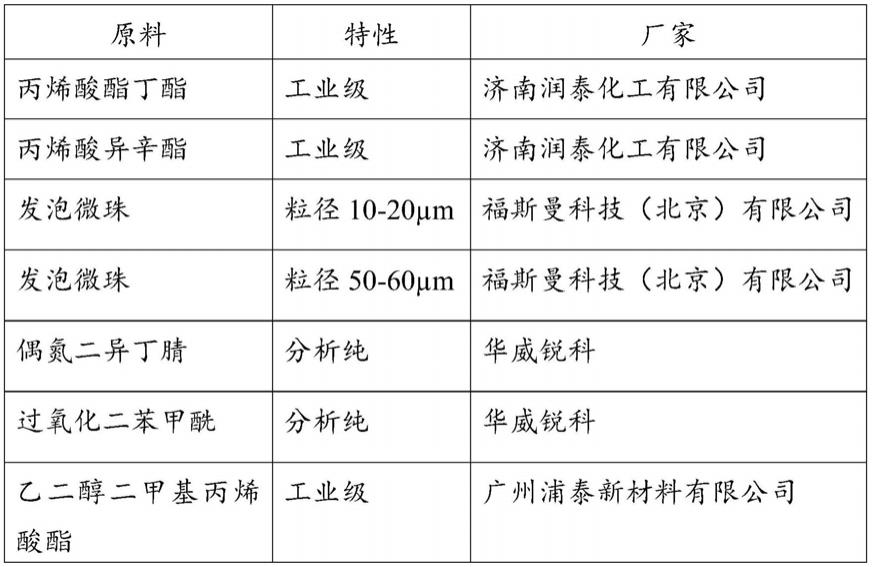
1.本发明涉及高分子材料技术领域,具体涉及一种聚丙烯酸酯泡棉及其制备方法、应用。
背景技术:
2.随着电子产品的飞速发展,作为人机交互的显示技术发挥着越来越重要的作用,oled屏幕的应用也越来越广泛。oled屏幕,特别是g-oled(玻璃基材)屏幕在跌落或碰撞时容易开裂造成产品失效。一种有效提升抗跌落能力的方法是在oled屏幕背面与壳体之间添加一层缓冲泡棉,减少oled屏幕在受到冲击时的变形,降低屏幕破裂的概率。
3.聚丙烯酸酯泡棉由于具有自吸性,是这类缓冲应用的较优选择。根据碰撞方式的不同可以将oled屏幕所受的冲击分为点冲击和面冲击。在受到点冲击时,由于受力面积较小,聚丙烯酸酯泡棉的泡孔易被破坏,此时泡棉吸能主要依靠泡孔壁的抗剪切作用,这就需要泡棉的质地较硬、受到冲击时变形较小;在受到面冲击时,由于受力面积较大,聚丙烯酸酯泡棉的泡孔不容易破裂,此时泡棉吸能主要依赖于泡孔的弹性形变,这就需要泡棉的质地较软,受到冲击时变形较大。然而,oled屏幕在实际应用过程中面临的冲击是多样的,现有的聚丙烯酸酯泡棉难以同时兼顾点冲击和面冲击能量吸收均达到较高的水平。
4.鉴于此,目前亟待提出一种聚丙烯酸酯泡棉,能够实现同时具有较高的点冲击和面冲击能量吸收性能。
技术实现要素:
5.本发明要解决的技术问题是提供一种聚丙烯酸酯泡棉,解决现有技术中聚丙烯酸酯泡棉的难以同时兼顾点冲击和面冲击能量吸收均达到较高水平的问题。
6.为解决上述技术问题,本发明的技术方案如下:
7.一种聚丙烯酸酯泡棉,包括如下原料:丙烯酸酯单体、引发剂、交联剂、发泡微珠;其中,所述发泡微珠为两种粒径的发泡微珠混合而成。
8.优选地,所述发泡微珠为粒径在10-20μm和粒径在50-60μm的两种粒径的发泡微珠混合而成。
9.优选地,所述聚丙烯酸酯泡棉,包括如下重量份的原料:每100份的丙烯酸酯单体,引发剂0.1-0.3份,交联剂1-2份,发泡微珠1-3份。
10.优选地,所述丙烯酸酯单体为丙烯酸丁酯、丙烯酸乙酯、丙烯酸正辛酯、丙烯酸异辛酯、丙烯酸异丁酯、丙烯酸正丙酯、甲基丙烯酸正丁酯、丙烯酸甲酯、甲基丙烯酸乙酯、甲基丙烯酸甲酯、甲基丙烯酸异冰片酯中的一种或多种。
11.优选地,所述的引发剂为偶氮二异丁腈、过氧化苯甲酰、叔丁基过氧化六氢对苯二酸酯、偶氮二异庚腈、偶氮二异戊腈中的一种或多种。
12.优选地,所述交联剂为二丙烯酸酯类交联剂、多异氰酸酯类交联剂的一种或多种。其中,所述二丙烯酸酯类交联剂包括但不限于乙二醇二甲基丙烯酸酯、端乙烯基聚氨酯、端
乙烯基聚环氧丙烷、端乙烯基环氧乙烷。所述多异氰酸酯类交联剂包括但不限于二苯基甲烷-4,4'-二异氰酸酯(mdi)、聚合mdi、氢化mdi。
13.本发明还提供一种聚丙烯酸酯泡棉的制备方法,包括如下步骤:取丙烯酸酯单体、引发剂、交联剂、发泡微珠,混合均匀,反应得到聚丙烯酸酯泡棉。
14.优选地,所述的聚丙烯酸酯泡棉的制备方法,包括如下步骤:按重量份取丙烯酸酯单体、引发剂、交联剂、发泡微珠,混合均匀,先进行预聚合反应,再将得到的预聚合物涂布于离型膜上,进行聚合反应,得到聚丙烯酸酯泡棉。
15.优选地,所述预聚合反应的反应温度为70-80℃,反应时间为1-1.5h;所述聚合反应的反应温度为70-90℃。
16.本发明还提出所述的聚丙烯酸酯泡棉在缓冲减震材料中的应用。
17.本发明的上述方案至少包括以下有益效果:
18.(1)本发明的聚丙烯酸酯泡棉,采用两种粒径的发泡微珠复配,尤其是粒径在10-20μm范围内的发泡微珠和粒径在50-60μm的范围内的发泡微珠配合使用,其中,粒径为10-20μm范围内的发泡微珠,粒径较小,形成的闭孔型聚丙烯酸酯泡棉孔壁较厚,在受到点冲击时,孔壁较厚的孔径小的泡棉吸收点冲击的能量较多,即孔径小的闭孔型聚丙烯酸酯泡棉具有较高的点冲击能量吸收。粒径为50-60μm范围内的发泡微珠,粒径较大,形成的闭孔型聚丙烯酸酯泡棉孔壁较薄,在受到面冲击时,孔壁较薄的孔径大的泡棉吸收面冲击的能量较多,即孔径大的闭孔型聚丙烯酸酯泡棉具有较高的面冲击能量吸收。适宜比例的大小微珠使得到的聚丙烯酸酯泡棉大孔径、小孔径的泡孔交替分布,兼具较高的点与面冲击能量吸收率,能在各种冲击情况下,有效吸收冲击能量,表现出优异的缓冲减震性能,在将其应用于oled屏幕的缓冲泡棉时,可更好地保护oled屏幕不受破坏。另外,当异氰酸酯类交联剂和发泡微珠表面羟基反生化学反应,生成高键合强度的氨基甲酸酯键,使得泡棉在受到能量冲击后,微珠和树脂界面不发生滑脱,因此所生产的泡棉产品在多次冲击后仍能够提供有效的防护,延长oled屏幕使用寿命。
19.(2)本发明的聚丙烯酸酯泡棉制备过程简单,反应条件温和,适于大规模生产。
具体实施方式
20.本发明各实施例中未注明具体条件者,按照常规条件或制造商建议的条件进行。所用试剂或仪器未注明生产厂商者,均为可以通过市购获得的常规产品,以下仅提供本发明实施例所使用的部分试剂,不同厂家、型号的原料并不影响本发明技术方案的实施及技术效果的实现。
[0021][0022][0023]
实施例1
[0024]
本实施例的聚丙烯酸酯泡棉,包括如下重量份的原料:丙烯酸酯单体100份,引发剂0.3份,交联剂1份,发泡微珠3份。其中,所述丙烯酸酯单体为丙烯酸酯丁酯与丙烯酸异辛酯按照65:35的重量比混合而成;所述引发剂为偶氮二异丁腈;所述交联剂为乙二醇二甲基丙烯酸酯;所述发泡微珠为粒径在10-20μm的发泡微珠和粒径在50-60μm的发泡微珠按照1:1的重量比混合而成。
[0025]
本实施例所述的聚丙烯酸酯泡棉的制备方法如下:
[0026]
按重量份取丙烯酸酯单体、引发剂、交联剂、发泡微珠,混合均匀,混合物先在70℃下进行1h的预聚合反应,再将得到的预聚合物涂布于离型膜上,并置于80℃的鼓风烘箱中进行聚合反应,使得发泡微珠膨胀,得到聚丙烯酸酯泡棉。
[0027]
实施例2
[0028]
本实施例的聚丙烯酸酯泡棉,包括如下重量份的原料:丙烯酸酯单体100份,引发剂0.3份,交联剂1.5份,发泡微珠3份。其中,所述丙烯酸酯单体为丙烯酸乙酯与丙烯酸正辛酯按照55:45的重量比混合而成;所述引发剂为过氧化苯甲酰;所述交联剂为mdi;所述发泡微珠为粒径在10-20μm的发泡微珠和粒径在50-60μm的发泡微珠按照1:1的重量比混合而成。
[0029]
本实施例所述的聚丙烯酸酯泡棉的制备方法如下:
[0030]
按重量份取丙烯酸酯单体、引发剂、交联剂、发泡微珠,混合均匀,混合物先在80℃下进行1.5h的预聚合反应,再将得到的预聚合物涂布于离型膜上,并置于80℃的鼓风烘箱中进行聚合反应,使得发泡微珠膨胀,得到聚丙烯酸酯泡棉。
[0031]
实施例3
[0032]
本实施例的聚丙烯酸酯泡棉,包括如下重量份的原料:丙烯酸酯单体100份,引发剂0.2份,交联剂2份,发泡微珠3份。其中,所述丙烯酸酯单体为丙烯酸异丁酯、丙烯酸正丙酯、甲基丙烯酸正丁酯按照1:2:2的重量比混合而成;所述引发剂为氢化mdi;所述交联剂为乙二醇二甲基丙烯酸酯;所述发泡微珠为粒径在10-20μm的发泡微珠和粒径在50-60μm的发泡微珠按照1:1的重量比混合而成。
[0033]
本实施例所述的聚丙烯酸酯泡棉的制备方法如下:
[0034]
按重量份取丙烯酸酯单体、引发剂、交联剂、发泡微珠,混合均匀,混合物先在75℃下进行1h的预聚合反应,再将得到的预聚合物涂布于离型膜上,并置于70℃的鼓风烘箱中进行聚合反应,使得发泡微珠膨胀,得到聚丙烯酸酯泡棉。
[0035]
实施例4
[0036]
本实施例的聚丙烯酸酯泡棉,包括如下重量份的原料:丙烯酸酯单体100份,引发剂0.1份,交联剂2份,发泡微珠3份。其中,所述丙烯酸酯单体为丙烯酸甲酯;所述引发剂为偶氮二异庚腈;所述交联剂为乙二醇二甲基丙烯酸酯;所述发泡微珠为粒径在10-20μm的发泡微珠和粒径在50-60μm的发泡微珠按照1:1的重量比混合而成。
[0037]
本实施例所述的聚丙烯酸酯泡棉的制备方法如下:
[0038]
按重量份取丙烯酸酯单体、引发剂、交联剂、发泡微珠,混合均匀,混合物先在80℃下进行1.5h的预聚合反应,再将得到的预聚合物涂布于离型膜上,并置于100℃的鼓风烘箱中进行聚合反应,使得发泡微珠膨胀,得到聚丙烯酸酯泡棉。
[0039]
实施例5
[0040]
本实施例的聚丙烯酸酯泡棉,包括如下重量份的原料:丙烯酸酯单体100份,引发剂0.2份,交联剂2份,发泡微珠1份。其中,所述丙烯酸酯单体为甲基丙烯酸乙酯、甲基丙烯酸甲酯、甲基丙烯酸异冰片酯按照2:3:1的重量比混合而成;所述引发剂为偶氮二异戊腈与偶氮二异庚腈按照1:1的重量比混合而成;所述交联剂为乙二醇二甲基丙烯酸酯;所述发泡微珠为粒径在10-20μm的发泡微珠和粒径在50-60μm的发泡微珠按照1:1的重量比混合而成。
[0041]
本实施例所述的聚丙烯酸酯泡棉的制备方法如下:
[0042]
按重量份取丙烯酸酯单体、引发剂、交联剂、发泡微珠,混合均匀,混合物先在80℃下进行1.5h的预聚合反应,再将得到的预聚合物涂布于离型膜上,并置于80℃的鼓风烘箱中进行聚合反应,使得发泡微珠膨胀,得到聚丙烯酸酯泡棉。
[0043]
实施例6
[0044]
本实施例与实施例2的聚丙烯酸酯泡棉采用相同的原料,并采用相同的制备方法制备得到。区别仅在于,所述发泡微珠为粒径在10-20μm的发泡微珠和粒径在50-60μm的发泡微珠按照1:2的重量比混合而成。
[0045]
实施例7
[0046]
本实施例与实施例2的聚丙烯酸酯泡棉采用相同的原料,并采用相同的制备方法制备得到。区别仅在于,本实施例中,所述发泡微珠为粒径在10-20μm的发泡微珠和粒径在50-60μm的发泡微珠按照2:1的重量比混合而成。
[0047]
对比例1
[0048]
本对比例与实施例2的聚丙烯酸酯泡棉采用相同的原料,并采用相同的制备方法
制备得到。区别仅在于,本对比例中,所述发泡微珠为粒径在10-20μm的发泡微珠。
[0049]
对比例2
[0050]
本实施例与实施例2的聚丙烯酸酯泡棉采用相同的原料,并采用相同的制备方法制备得到。区别仅在于,本对比例中,所述发泡微珠为粒径在50-60μm的发泡微珠。
[0051]
对比例3
[0052]
本实施例与实施例2的聚丙烯酸酯泡棉采用相同的原料,并采用相同的制备方法制备得到。区别仅在于,本对比例中,所述发泡微珠为粒径在5-10μm的发泡微珠。
[0053]
对比例4
[0054]
本实施例与实施例2的聚丙烯酸酯泡棉采用相同的原料,并采用相同的制备方法制备得到。区别仅在于,本对比例中,所述发泡微珠为粒径在60-100μm的发泡微珠。
[0055]
效果对比例
[0056]
为验证本发明所述的聚丙烯酸酯泡棉的技术效果,进行以下试验:
[0057]
取实施例1-7、对比例1-4中制备得到的聚丙烯酸酯泡棉,裁剪为100mm*100mm*0.1mm的尺寸贴于落球冲击测试仪传感器,使用4.3g钢球在10cm高度砸落,测试得到能量值为g1;之后撕除泡棉直接砸落试能量值为g0;(g
0-g1)/g0得到点冲击能量吸收率。
[0058]
裁剪为100mm*100mm*0.1mm的尺寸贴于100mm*100mm*10mm的钨钢板上,泡棉面接触落球冲击测试仪传感器,使用30g钢球在30cm高度砸落,测试得到能量值为j1;之后撕除泡棉,单纯钨钢板测试能量值为j0;(j
0-j1)/j0得到面冲击能量吸收率。
[0059]
经实验,结果如下:
[0060][0061]
由上述实验结果可知,实施例1、2的聚丙烯酸酯泡棉点冲击能量吸收、面冲击能量吸收均效果较优,尤其是实施例2采用交联剂mdi,与大、小粒径的发泡微珠结合强度高,可
更好地保持特定尺寸的大孔径、小孔径的泡孔交替分布形态的稳定性,从而表现出优异的点冲击、面冲击能量吸收效果。另外,通过实施例1-5与实施例6、7的对比,以及与对比例1-4的对比可见,所述发泡微珠为粒径在10-20μm的发泡微珠和粒径在50-60μm的发泡微珠按照1:1的重量比混合时,效果最优。
[0062]
由技术常识可知,本发明可以通过其它的不脱离其精神实质或必要特征的实施方案来实现。因此,上述公开的实施方案,就各方面而言,都只是举例说明,并不是仅有的。所有在本发明范围内或在等同于本发明的范围内的改变均被本发明包含。
再多了解一些
本文用于企业家、创业者技术爱好者查询,结果仅供参考。