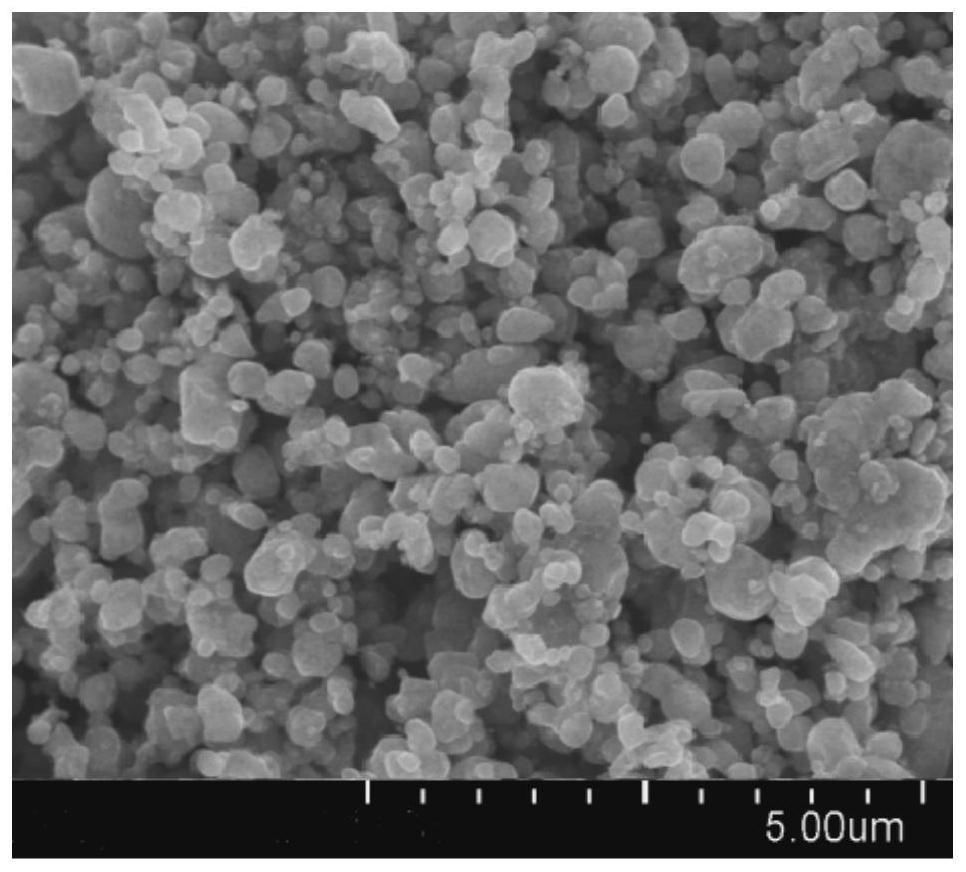
1.本发明涉及锂电池材料回收技术领域,具体涉及一种磷酸铁锂废粉的处理方法及碳包覆磷酸铁锂。
背景技术:
2.传统废旧磷酸铁锂废粉的回收工艺主要分为两种:(1)只回收锂,制备得到碳酸锂,磷铁渣作为尾矿堆放;(2)同时回收锂铁磷元素,制备得到碳酸锂和粗制磷酸铁,杂质含量较高。例如,专利文献cn112441571a公开了一种高铝磷酸铁锂废料的回收方法制备碳酸锂产品;专利文献cn113880064a公开一种低耗磷酸处理高杂磷酸铁锂废粉的方法,可以制备高纯度的磷酸铁;专利文献cn112410556a公开一种磷酸铁锂废粉料的回收方法,可以制备获得碳酸锂、磷酸铁粉末;专利文献cn113443640a公开了一种利用磷酸铁锂电池正负极废粉制备电池级碳酸锂和电池级磷酸铁的方法,可以制备电池级碳酸锂产品和电池级磷酸铁产品;专利文献cn112794300a公开了一种废旧磷酸铁锂电池正极片的分离回收再生方法,通过煅烧、筛分、碱液处理、添加铁源/锂源/磷源化合物、二次煅烧得到新的磷酸铁锂材料;专利文献cn109095481b公开了一种磷酸铁锂废粉的综合回收方法,通过氧化焙烧、反酸浸出、净化除磷酸根、除钙镁、合成等工艺步骤;专利文献cn109256595b公开了一种磷酸铁锂废粉火法直接修复制备电池级磷酸铁锂的方法,通过氧化焙烧、配料、球磨、干燥、烧结、筛分除铁得到电池级磷酸铁锂产品。
3.但是上述专利技术虽然公开了磷酸铁锂废粉处理方法,能够实现对磷酸铁锂废粉的处理,但是无法同时解决铜、铝、重金属等杂质元素超标的问题,因此对铁锂废粉有着特定的要求。而目前市面上的铁锂废粉主要是通过将磷酸铁锂废旧电芯粉碎分级得到,普遍同时含有较多的铜、铝、重金属等杂质元素,用上述处理方法无法得到合格磷酸铁锂产品。此外,上述公开的磷酸铁锂废粉处理方法,普遍采用分步提取的工艺,即分别提取锂盐和铁磷盐,而后再用锂盐和铁磷盐合成磷酸铁锂;因而整体工序冗长,磷酸铁锂的制备成本较高,不利于产业化应用。
技术实现要素:
4.基于此,本发明提供一种磷酸铁锂废粉的处理方法及碳包覆磷酸铁锂成品,通过碱浸、酸溶、除铜、除重金属、除铝解决了杂质元素超标的问题;同时,采用水热法直接合成磷酸铁锂,省去了提锂和提铁磷的过程,使得磷酸铁锂的制备成本降低。
5.本发明采用如下技术方案:
6.本发明提供一种磷酸铁锂废粉的处理方法,包括如下步骤:采用oh-浓度1~5mol/l的碱溶液浸泡磷酸铁锂废粉,其中磷酸铁锂废粉与碱溶液的质量比为1:(2~5),待溶液中无气泡产生后过滤,得到碱浸黑粉;而后用h
浓度3~10mol/l的酸浸泡碱浸黑粉;固液分离除渣(主要含碳粉、石墨粉、铜屑等),得含锂铁磷第一浸出液;调节所述第一浸出液的ph至1.5~3.5,得第二浸出液;向所述第二浸出液中加入铁粉,与铜离子发生置换反应,固液分
离,得海绵铜和第三浸出液;向所述第三浸出液中加入重金属捕捉剂,搅拌反应,固液分离除渣,得第四浸出液;向所述第四浸出液中加入氟化盐,搅拌反应,固液分离除渣,得第五浸出液;向所述第五浸出液中加入磷源、铁源和锂源,调整溶液中p、fe、li物质的量之比为(1~1.05):1:(1.5~3),得到铁锂合成前液;将所述铁锂合成前液的ph调至7~9,加热至120~180℃,加压至0.3~0.8mpa,保温保压反应4~7h,得到磷酸铁锂前驱体浆料;采用压滤机对所述磷酸铁锂前驱体浆料进行固液分离,得到磷酸铁锂滤饼,采用纯水对磷酸铁锂滤饼洗涤,洗涤至漂洗水电导≤200us/cm,然后采用真空干燥烘干至水分≤1%,得到磷酸铁锂前驱体粉末;向磷酸铁锂前驱体粉末中加入碳源,分散均匀,在高温惰性氛围下烧结制备得到碳包覆磷酸铁锂产品。
7.在其中一些实施例中,h
浓度3~10mol/l的酸为盐酸或硫酸。优选为h
浓度5~8mol/l的盐酸或硫酸。
8.在其中一些实施例中,酸与磷酸铁锂废粉的液固比为(2~5):1,浸出温度为20~60℃,浸出时间2~6h。
9.在其中一些实施例中,所述采用h
浓度为3~10mol/l的酸浸泡磷酸铁锂废粉的过程还包括采用惰性气体保护以防止亚铁氧化的步骤。
10.在其中一些实施例中,所述铁锂合成前液中还含有葡萄糖或抗坏血酸,以防止亚铁离子的氧化。
11.在其中一些实施例中,制备所述第二浸出液所采用的ph调节剂选自铁粉、碳酸(氢)钠、碳酸(氢)铵、液碱中的至少一种。
12.在其中一些实施例中,所述铁粉的摩尔量为超过与所述第二浸出液中铜离子反应计量比的10~15%。
13.在其中一些实施例中,所述重金属捕捉剂选自硫化钠、硫化钾、硫化铵中的至少一种。加入量按照浸出液中重金属捕捉剂含量0.2~0.6g/l计算。
14.在其中一些实施例中,所述氟化盐的加入摩尔量为所述第四浸出液中铝离子含量的300~350%。
15.在其中一些实施例中,所述磷源选自磷酸、磷酸一铵、磷酸二铵、磷酸钠中的至少一种。
16.在其中一些实施例中,所述铁源选自硫酸亚铁、氯化亚铁中的至少一种。
17.在其中一些实施例中,所述锂源选自硫酸锂、氯化锂、碳酸锂、磷酸锂中的至少一种。
18.在其中一些实施例中,所述碳源选自葡萄糖或者蔗糖。
19.在其中一些实施例中,所述碳源的加入量按照铁锂产品中碳含量1.4~1.8wt%,烧结保温温度700~750℃,保温时间3~6h。
20.本发明还提供由上述磷酸铁锂废粉的处理方法制备获得的磷酸铁锂成品,碳含量1.4~1.8%,振实密度0.8~1.2g/cm3,比表面积15
±
2m2/g,放电比容量≥155mah/g。
21.本发明的有益效果是:
22.与现有技术相比,本发明磷酸铁锂废粉的处理方法首先采用碱液浸泡将磷酸铁锂废粉中的al浸出,过滤得到碱浸黑粉,而后采用酸浸将磷酸铁锂浸出,过滤便可除去碳粉、石墨粉和铜屑,滤液中残存的少量cu
2
、重金属离子和al
3
,则分别通过加入铁粉、重金属捕
捉剂和氟化盐除去,进而得到杂质含量极低的磷酸铁锂浸出液;而后调节浸出液中铁磷锂的比例,直接采用水热法工艺合成磷酸铁锂前驱体,然后再通过碳包覆、烧结制备得到碳包覆磷酸铁锂成品,省去了提锂和提铁磷的过程,直接制备得到高附加值的碳包覆磷酸铁锂产品。
附图说明
23.图1为实施例1制备的碳包覆磷酸铁锂成品sem照片。
24.图2为实施例1制备的碳包覆磷酸铁锂成品xrd图。
具体实施方式
25.下面结合具体实施例对本发明作进一步的详细说明,以使本领域的技术人员更加清楚地理解本发明。
26.以下各实施例,仅用于说明本发明,但不止用来限制本发明的范围。基于本发明中的具体实施例,本领域普通技术人员在没有做出创造性劳动的情况下,所获得的其他所有实施例,都属于本发明的保护范围。
27.在本发明实施例中,若无特殊说明,所有原料组分均为本领域技术人员熟知的市售产品;在本发明实施例中,若未具体指明,所用的技术手段均为本领域技术人员所熟知的常规手段。
28.磷酸铁锂废粉:外购废旧铁锂电芯粉碎分级得到。
29.成分检测说明:含铁24.1%,含磷13.4%,含锂3.0%,含碳32.3%,含铝1.1%,含铜0.7%。
30.实施例1
31.本实施例提供一种磷酸铁锂废粉的处理方法,包括如下步骤:
32.s1,称取500g磷酸铁锂废粉,加入3mol/l的naoh溶液1500g,搅拌,待溶液中不再产生气泡后过滤,得到碱浸黑粉,而后加入1500g硫酸溶液进行浸出,硫酸溶液的氢离子浓度为5mol/l,在30℃条件下搅拌浸出3h,过滤后得到主要含碳粉、石墨粉、铜屑等的滤渣以及含锂铁磷的第一浸出液,测得锂的浸出率为91.24%。浸出过程采用高纯氮气保护,使环境处于微正压状态,以减少浸出过程中的亚铁氧化,从而减少磷酸铁的生成,降低铁损失。
33.s2,向步骤s1获得的含锂铁磷的第一浸出液中加入碳酸钠,调节溶液ph至2.0,得第二浸出液。然后检测溶液中铜离子含量,按照铜离子与铁粉反应计量比过量10%加入铁粉,将铜离子还原为海绵铜,过滤得到除铜浸出液,记为第三浸出液。
34.s3,向除铜浸出液(第三浸出液)中加入硫化钠,加入量按照浸出液中硫化钠浓度0.3g/l计算,过滤得到除重金属浸出液,记为第四浸出液。
35.s4,取样第四浸出液,检测其中的铝含量,加入氟化钠,加入量为溶液中铝离子含量的330%,搅拌反应30min,过滤得到除铝浸出液,记为第五浸出液。
36.s5,取样第五浸出液,检测溶液中锂铁磷的含量,分别以硫酸锂为锂源、硫酸亚铁为铁源、磷酸为磷源,调整溶液中n(p/fe/li)=1.03:1:2,得到铁锂合成前液。另外,铁锂合成前液中还含有一定量的葡萄糖,以防止亚铁离子的氧化。
37.s6,向步骤s5的合成前液中加入液碱,调节溶液ph至8,加温至130℃,加压至
0.4mpa,保温保压反应5h,得到磷酸铁锂前驱体浆料。固液分离得到磷酸铁锂前驱体滤饼,然后采用纯水洗涤至电导≤200us/cm,采用真空干燥烘干至水分≤1%,得到磷酸铁锂前驱体粉末。
38.s7,向磷酸铁锂前驱体粉末中加入葡萄糖(成品碳含量按照1.5wt%),充分混匀后在氮气氛围,720℃条件下保温4h,烧结制备得到碳包覆磷酸铁锂产品。
39.实施例2
40.本实施例提供一种磷酸铁锂废粉的处理方法,其与实施例1的工艺步骤基本相同,区别仅在于:在步骤s1中加入的酸为盐酸,在30℃条件下搅拌浸出3h,锂的浸出率为99.37%。
41.实施例3
42.本实施例提供一种磷酸铁锂废粉的处理方法,其与实施例1的工艺步骤基本相同,区别仅在于:在步骤s2中按照铜离子与铁粉反应计量比过量15%加入铁粉。步骤s3中重金属捕捉剂为硫化铵,加入量按照浸出液中硫化铵浓度0.5g/l计算。
43.实施例4
44.本实施例提供一种磷酸铁锂废粉的处理方法,其与实施例1的工艺步骤基本相同,区别仅在于:向步骤s5的合成前液中加入氨水,调节溶液ph至8,加温至170℃,加压至0.6mpa,保温保压反应5h,得到磷酸铁锂前驱体浆料。
45.对比例1
46.本对比例提供一种磷酸铁锂废粉的处理方法,其与实施例1的工艺步骤基本相同,区别仅在于:采用氢氧化钠溶液浸提磷酸铁锂废粉,锂的浸出率为3.48%。
47.对比例2
48.本对比例提供一种磷酸铁锂废粉的处理方法,其与实施例1的工艺步骤基本相同,区别仅在于:省去步骤s2除铜工序。
49.对比例3
50.本对比例提供一种磷酸铁锂废粉的处理方法,其与实施例1的工艺步骤基本相同,区别仅在于:省去步骤s3除重金属工序。
51.对比例4
52.本对比例提供一种磷酸铁锂废粉的处理方法,其与实施例1的工艺步骤基本相同,区别仅在于:省去步骤s4除铝工序。
53.对比例5
54.本对比例提供一种磷酸铁锂废粉的处理方法,其与实施例1的工艺步骤基本相同,区别仅在于:烧结保温温度600℃,保温时间2h。
55.分别对实施例1至4以及对比例1至5制备的磷酸铁锂进行材料性能和电性能检测,检测结果见下表1:
56.表1检测性能统计表
[0057][0058]
由表1可知,实施例1~4制备出的磷酸铁锂碳含量在1.5~1.7%,振实密度在0.9~1.1g/cm3,比表面积在14~16m2/g,铝含量低于20ppm,铜含量低于10ppm,镍和锌含量低于5ppm,充电比容量大于159mah/g,放电比容量大于155mah/g,首效大于97%。
[0059]
对比例1采用氢氧化钠溶液浸出电池粉,锂的浸出率极低,故而无法进行后续验证。对比例2由于没有除铜,浸出液中的铜离子只能在除重金属时除去,但由于浸出液中铜离子浓度过高,而硫化钠加入量不足,导致铜离子含量过高;同时由于铜离子消耗了大量的硫化钠,导致重金属离子ni、zn无法去除干净。对比例3无除重金属工序,导致重金属离子ni、zn无法去除,ni、zn含量过高;而铜离子在除铜工序后无法进一步去除,导致铜离子含量相较于实施例1偏高。cu、ni、zn等重金属杂质含量高,会导致电池自放电高,极化增大,一致性和安全性变差,故而对比例2和对比例3的放电克容量偏低。对比例4无除铝工序,导致产品铝含量严重超标,无法满足客户的要求。对比例5制备磷酸铁锂时,烧结温度过低,保温时间过短,导致碳源无法充分烧结,包覆碳石墨化程度低,碳含量和比表面积较高,振实密度较低,电性能较差。
[0060]
另外,值得说明的是,发明人团队经过大量研究发现:
[0061]
(1)采用h
浓度3~10mol/l的酸浸泡碱浸黑粉,能够获得同步碳粉、石墨粉、铜屑等;当h
浓度低于3mol/l,会导致电池粉的浸出速度过慢,浸出时间过长,在相同时间内锂的浸出率偏低;当h
浓度高于10mol/l,会导致酸的用量过大,同时第一浸出液的ph值过低,步骤s2中调节ph时会消耗大量的ph调节剂,生产成本偏高。
[0062]
(2)第二浸出液的ph优选1.5~3.5,则铁粉与铜离子发生置换反应的效果比较好。若ph低于1.5,则铁粉会与h
反应,不仅产生氢气,而且还会导致铁粉的消耗量增大。若ph高于3.5,则容易产生磷酸亚铁的沉淀,导致铁、磷大量损失,影响回收率。
[0063]
(3)除铜时加入铁粉的摩尔量优选为超过与第二浸出液中铜离子反应计量比的10~15%。若铁粉加入量低于反应计量比的10%,则铜离子反应不完全,无法将铜离子去除干净;若铁粉加入量高于反应计量比的15%,则铁粉过多,反应完成后残留铁粉过多,造成铁粉浪费。
[0064]
(4)重金属捕捉剂加入量按照浸出液中重金属捕捉剂含量0.2~0.6g/l计算。若浸出液中重金属捕捉剂含量低于0.2g/l,则无法将浸出液中的重金属离子除去干净;若浸出液中重金属捕捉剂含量高于0.6g/l,则重金属捕捉剂过多,造成重金属捕捉剂浪费。
[0065]
(5)氟化盐的加入摩尔量为所述第四浸出液中铝离子含量的300~350%。若氟化盐的加入摩尔量低于所述第四浸出液中铝离子含量的300%,则无法将第四浸出液中铝离
子彻底去除;若氟化盐的加入摩尔量高于所述第四浸出液中铝离子含量的350%,则氟化盐的加入量过多,造成氟化盐的浪费。
[0066]
本发明与现有提取磷酸铁和碳酸锂的工艺相比,对于废旧电池粉的兼容性更好,能够处理高铝、高铜、高重金属杂质的废旧电池粉,且利用水热法工艺将废旧磷酸铁锂电池粉直接回收制备成合格的磷酸铁锂材料,简化缩短了回收工序,有利于降低回收成本和产业化应用。
[0067]
在此有必要指出的是,以上实施例仅限于对本发明的技术方案做进一步的阐述和说明,并不是对本发明的技术方案的进一步的限制,本发明的方法仅为较佳的实施方案,并非用于限定本发明的保护范围。凡在本发明的精神和原则之内,所作的任何修改、等同替换、改进等,均应包含在本发明的保护范围之内。
再多了解一些
本文用于企业家、创业者技术爱好者查询,结果仅供参考。