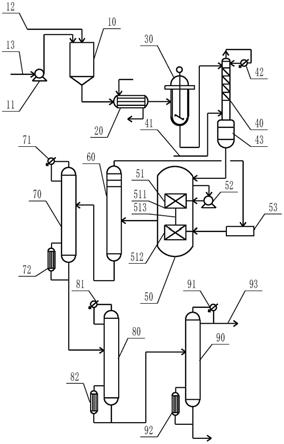
1.本发明属于丁二醇的生产技术领域,具体而言,涉及一种1,4-丁二醇的微界面制备系统。
背景技术:
2.1,4-丁二醇是甲醇系列产品链之一,是一种重要的基本有机化工和精细化工原料,生产商在生产1,4-丁二醇的过程中,一般都不以1,4-丁二醇为最终产品,而是注重1,4-丁二醇衍生物的延伸,1,4-丁二醇衍生物是附加价值较高的精细化工产品,广泛用做溶剂、医药、化妆品、增塑剂、固化剂、农药、除莠剂、泡沫人造革、纤维和工程塑料等方面;由于1,4-丁二醇产品的用途广泛,用量大,因此,1,4-丁二醇的生产技术就需要不断提高。
3.1,4-丁二醇的生产方法主要包括:(1)以甲醛和乙炔为原料的reppe法(炔醛法);(2)以丁二烯和醋酸为原料的丁二烯乙酰氧基化法;(3)以环氧丙烷/丙烯醇为原料的环氧丙烷法;(4)以正丁烷/顺酐为原料的davy法。由于国内丁二烯及环氧丙烷较为短缺,采用这两种方法生产1,4-丁二醇尚未成熟,根据资源优势选择生产方法,在国内主要是reppe法(炔醛法)。
4.reppe法的生产工艺流程主要包括甲醛工段、炔化工段、加氢工段和产品精馏工段,甲醛工段主要是原料甲醇和空气在催化剂的作用下生成甲醛;炔化工段主要是乙炔与甲醛水溶液在催化剂作用下进行炔醛反应生成精1,4-丁炔二醇;加氢工段主要是在一定压力下将1,4-丁炔二醇和氢气在催化剂作用下生成粗1,4-丁二醇;产品精馏工段主要是对1,4-丁二醇进行精馏处理得到高纯度1,4-丁二醇产品。
5.加氢工段的反应是将1,4-丁炔二醇和氢气生成粗1,4-丁二醇,随着反应的进行,反应容器内剩余未反应的1,4-丁炔二醇与生成的粗1,4-丁二醇形成浆液,氢气需要混在浆液中与剩余的1,4-丁炔二醇反应,而氢气进入浆液后容易形成气泡,与浆液混合不均匀,就会导致反应不充分,1,4-丁二醇的产量就会下降。
6.现有技术中,为了提高氢气与丁炔二醇的混合效果,使反应更充分,以提高1,4-丁二醇的产量,加氢工段主要采用两段加氢的方法:一段加氢采用带搅拌的淤浆床反应器,反应温度50~60℃,反应压力1.5~3.0mpa;二段加氢采用固定床高压1,4-丁二醇反应器,反应温度110~165℃,反应压力7~30mpa。两段加氢法一般采用搅拌或者鼓泡的方式,而传统的搅拌桨或鼓泡塔反应器中只能产生厘米或大毫米尺度的湍流涡,因此,即使再加大搅拌电机功率,其大部分能量也只能转化为热能,而不能转变成为小气泡生成所需的表面能,导致氢气与丁炔二醇混合不均匀;同时,为了进一步促进反应充分进行,加氢过程中增加催化剂的用量。
7.但是现有技术加氢工段仍然存在如下问题:
8.1、为了促进加氢工段的反应,生产商都会加大催化剂的量,提高了生产成本。
9.2、由于加大了加氢工段催化剂的量,经常出现催化剂反应不完全的现象,剩余的催化剂造成浪费,且进入后续系统后,会影响后续系统的正常生产。
10.3、氢气与浆液混合过程中,仍然会存在搅拌死角,氢气、催化剂与浆液仍然存在搅拌不均匀的问题,致使加氢工段反应不充分,影响1,4-丁二醇的产量。
11.4、搅拌并不能打破或者不能完全打破氢气的气泡,氢气就无法与浆液混合均匀。
12.有鉴于此,特提出本发明。
技术实现要素:
13.本发明的第一目的在于提供一种1,4-丁二醇的微界面制备系统,通过气液联动式微界面发生器将氢气分散破碎为氢气微气泡,提高气液两相传质面积,还因为气液联动式微界面发生器本身带有循环搅拌的功能,使得加氢反应时氢气可以更好地与混合液进行反应,加氢反应更充分。
14.本发明的第二目的在于一种1,4-丁二醇的微界面制备方法,该方法节约了成本,提高了反应效率。
15.为了实现上述技术目的,本发明提供了以下技术方案:
16.本发明提供了一种1,4-丁二醇的微界面制备系统,包括用以将甲醇和顺酐混合的混合罐,所述混合罐连接有甲醇进料管道和顺酐进料管道,所述混合罐依次连接用以加热混合原料的换热器、单酯化反应器、双酯化反应器、加氢反应器、闪蒸塔、甲醇精馏塔、顺丁烯二酸二甲酯精馏塔和1,4-丁二醇精馏塔,所述1,4-丁二醇精馏塔开设有产物出口;
17.所述加氢反应器的内部设置有气液联动式微界面发生器,所述气液联动式微界面发生器连接有氢气进气管道和循环泵。
18.本发明通过设置了气液联动式微界面发生器将氢气分散破碎为氢气微气泡,氢气微气泡与顺丁烯二酸二甲酯之间反应增大了相界传质面积,提高了反应效率。其中气液联动式微界面发生器分为液动式微界面发生器和气动式微界面发生器,液动式微界面发生器的外边连接有循环泵,循环泵将液态物料抽吸加压后返回至液动式微界面发生器,液动式微界面发生器通过连通管道将液态物料压缩进气动式微界面发生器,这样可以有效地缓解气动式微界面发生器被顺丁烯二酸二甲酯堵塞气孔的问题,同时也提高了反应效率。
19.优选的,所述气液联动式微界面发生器包括气动式微界面发生器和液动式微界面发生器,所述气动式微界面发生器设置在所述加氢反应器的底部,所述液动式微界面发生器设置在所述气动式微界面发生器的正上方。
20.优选的,所述气动式微界面发生器和所述液动式微界面发生器之间设置有连通管道。
21.优选的,所述气动式微界面发生器连接有氢气进气管道,所述液动式微界面发生器连接有循环泵。
22.优选的,所述闪蒸塔的顶部连接有氢气回收通道,所述氢气回收通道连接有所述氢气进气管道。
23.优选的,所述所述双酯化反应器中设置有催化剂床层。
24.优选的,所述双酯化反应器连接有甲醇补料管道。
25.优选的,所述甲醇进料管道上设置有用以将甲醇吸入所述混合罐的进料泵。
26.本领域所属技术人员可以理解的是,本发明所采用的微界面发生器在本发明人在先专利中已有体现,如申请号cn201610641119.6、cn201610641251.7、cn201710766435.0、
cn106187660、cn105903425a、cn109437390a、cn205833127u及cn207581700u的专利。在先专利cn201610641119.6中详细介绍了微米气泡发生器(即微界面发生器)的具体产品结构和工作原理,该申请文件中记载了“微米气泡发生器包括本体和二次破碎件、本体内具有空腔,本体上设有与空腔连通的进口,空腔的相对的第一端和第二端均敞开,其中空腔的横截面积从空腔的中部向空腔的第一端和第二端减小;二次破碎件设在空腔的第一端和第二端中的至少一个处,二次破碎件的一部分设在空腔内,二次破碎件与空腔两端敞开的通孔之间形成一个环形通道。微米气泡发生器还包括进气管和进液管。”从该申请文件中公开的具体结构可以知晓其具体工作原理为:液体通过进液管切向进入微米气泡发生器内,超高速旋转并切割气体,使气体气泡破碎成微米级别的微气泡,从而提高液相与气相之间的传质面积,而且该专利中的微米气泡发生器属于气动式微界面发生器。
27.另外,在先专利201610641251.7中有记载一次气泡破碎器具有循环液进口、循环气进口和气液混合物出口,二次气泡破碎器则是将进料口与气液混合物出口连通,说明气泡破碎器都是需要气液混合进入,另外从后面的附图中可知,一次气泡破碎器主要是利用循环液作为动力,所以其实一次气泡破碎器属于液动式微界面发生器,二次气泡破碎器是将气液混合物同时通入到椭圆形的旋转球中进行旋转,从而在旋转的过程中实现气泡破碎,所以二次气泡破碎器实际上是属于气液联动式微界面发生器。其实,无论是液动式微界面发生器,还是气液联动式微界面发生器,都属于微界面发生器的一种具体形式,然而本发明所采用的微界面发生器并不局限于上述几种形式,在先专利中所记载的气泡破碎器的具体结构只是本发明微界面发生器可采用的其中一种形式而已。
28.此外,在先专利201710766435.0中记载到“气泡破碎器的原理就是高速射流以达到气体相互碰撞”,并且也阐述了其可以用于微界面强化反应器,验证本身气泡破碎器与微界面发生器之间的关联性;而且在先专利cn106187660中对于气泡破碎器的具体结构也有相关的记载,具体见说明书中第[0031]-[0041]段,以及附图部分,其对气泡破碎器s-2的具体工作原理有详细的阐述,气泡破碎器顶部是液相进口,侧面是气相进口,通过从顶部进来的液相提供卷吸动力,从而达到粉碎成超细气泡的效果,附图中也可见气泡破碎器呈锥形的结构,上部的直径比下部的直径要大,也是为了液相能够更好的提供卷吸动力。
[0029]
由于在先专利申请的初期,微界面发生器才刚研发出来,所以早期命名为微米气泡发生器(cn201610641119.6)、气泡破碎器(201710766435.0)等,随着不断技术改进,后期更名为微界面发生器,现在本发明中的微界面发生器相当于之前的微米气泡发生器、气泡破碎器等,只是名称不一样。综上所述,本发明的微界面发生器属于现有技术。
[0030]
另外,本发明还提供了一种1,4-丁二醇的微界面制备方法,包括如下步骤:
31.甲醇和顺酐酯化反应生成顺丁烯二酸二甲酯,之后顺丁烯二酸二甲酯进行加氢反应,最后精馏纯化产物得到1,4-丁二醇。
[0032]
优选的,其特征在于,加氢反应的温度为160-220℃,压力为3-5mpa。
[0033]
与现有技术相比,本发明的优点在于:
[0034]
1、通过设置了气液联动式微界面发生器,将氢气分散破碎为氢气微气泡,提高了相界传质面积,提高了反应效率;
[0035]
2、气液联动式微界面发生器将氢气与液态物料充分混合,提高了反应效率;
[0036]
3、加氢反应时降低了温度和压力,节约了生产过程中的能耗。
附图说明
[0037]
通过阅读下文优选实施方式的详细描述,各种其他的优点和益处对于本领域普通技术人员将变得清楚明了。附图仅用于示出优选实施方式的目的,而并不认为是对本发明的限制。而且在整个附图中,用相同的参考符号表示相同的部件。在附图中:
[0038]
图1为1,4-丁二醇的微界面制备系统的结构示意图;
[0039]
其中:
[0040]
10-混合罐;11-进料泵;
[0041]
12-顺酐进料管道;13-甲醇进料管道;
[0042]
20-换热器;30-单酯化反应器;
[0043]
40-双酯化反应器;41-甲醇补料管道;
[0044]
42-第一冷凝器;43-催化剂床层;
[0045]
50-加氢反应器;51-气液联动式微界面发生器;
[0046]
511-液动式微界面发生器;512-气动式微界面发生器;
[0047]
513-连通管道;52-循环泵;
[0048]
53-氢气进气管道;60-闪蒸塔;
[0049]
70-甲醇精馏塔;71-第二冷凝器;
[0050]
72-第一再沸器;80-顺丁烯二酸二甲酯精馏塔;
[0051]
81-第三冷凝器;82-第二再沸器;
[0052]
90-1,4-丁二醇精馏塔;91-第四冷凝器;
[0053]
92-第三再沸器;93-产物出口。
具体实施方式
[0054]
下面将结合附图和具体实施方式对本发明的技术方案进行清楚、完整地描述,但是本领域技术人员将会理解,下列所描述的实施例是本发明一部分实施例,而不是全部的实施例,仅用于说明本发明,而不应视为限制本发明的范围。基于本发明中的实施例,本领域普通技术人员在没有做出创造性劳动前提下所获得的所有其他实施例,都属于本发明保护的范围。实施例中未注明具体条件者,按照常规条件或制造商建议的条件进行。所用试剂或仪器未注明生产厂商者,均为可以通过市售购买获得的常规产品。
[0055]
在本发明的描述中,需要说明的是,术语“中心”、“上”、“下”、“左”、“右”、“竖直”、“水平”、“内”、“外”等指示的方位或位置关系为基于附图所示的方位或位置关系,仅是为了便于描述本发明和简化描述,而不是指示或暗示所指的装置或元件必须具有特定的方位、以特定的方位构造和操作,因此不能理解为对本发明的限制。此外,术语“第一”、“第二”、“第三”仅用于描述目的,而不能理解为指示或暗示相对重要性。
[0056]
在本发明的描述中,需要说明的是,除非另有明确的规定和限定,术语“安装”、“相连”、“连接”应做广义理解,例如,可以是固定连接,也可以是可拆卸连接,或一体地连接;可以是机械连接,也可以是电连接;可以是直接相连,也可以通过中间媒介间接相连,可以是两个元件内部的连通。对于本领域的普通技术人员而言,可以具体情况理解上述术语在本发明中的具体含义。
[0057]
为了更加清晰的对本发明中的技术方案进行阐述,下面以具体实施例的形式进行
说明。
[0058]
实施例1
[0059]
参阅图1所示,为本发明提供的1,4-丁二醇的微界面制备系统的结构示意图,其中包括混合罐10、换热器20、单酯化反应器30、双酯化反应器40、加氢反应器50、闪蒸塔60、甲醇精馏塔70、顺丁烯二酸二甲酯精馏塔80和1,4-丁二醇精馏塔90。
[0060]
甲醇通过进料泵11和甲醇进料管道13被输送至混合罐10,顺酐通过顺酐进料管道12被输送至混合罐10,在混合罐10里甲醇与顺酐充分混合,之后混合物料被送往换热器20,换热器20的一端输送低压蒸汽,另一端排出换热后的工艺水。被加热到75℃的混合物料被送往单酯化反应器30。
[0061]
这时单酯化反应器30内部主要物料为顺丁烯二酸单甲酯,具体来说约有85%的顺酐转化为顺丁烯二酸单甲酯、其中12%的顺丁烯二酸单甲酯转化为顺丁烯二酸二甲酯,单酯化反应器30中还含有未反应的顺酐和甲醇。
[0062]
单酯化反应器30出来的混合物全部输送至双酯化反应器40,双酯化反应器40内部设置有催化剂床层43,其中催化剂为dnw-i型离子交换树脂。双酯化反应器40连接有甲醇补料管道41、第一冷凝器42,这样反应区和分离区就在同一个反应器中进行。此时几乎所有的顺酐转化为顺丁烯二酸二甲酯。顺丁烯二酸单甲酯和甲醇在催化剂床层43中发生反应,这样就精馏出顺丁烯二酸二甲酯。
[0063]
之后单酯化反应器30进入到加氢反应器50中,加氢反应器50中设置有气液联动式微界面发生器51,其中气液联动式微界面发生器51包括液动式微界面发生器511和气动式微界面发生器512,液动式微界面发生器511设置在气动式微界面发生器512的正上方,并且通过连通管道513相接。液动式微界面发生器511外部连接有循环泵52,气动式微界面发生器512连接有氢气进气管道53。这时候顺丁烯二酸二甲酯与氢气微气泡、催化剂cu/mac-41反应,生成γ-丁内酯、1,4-丁二醇,四氢呋喃。反应压力在3mpa,反应温度在160℃。从加氢反应器50出来的物料进入闪蒸塔60之后分离出氢气并返回至加氢反应器50。
[0064]
之后物料经过甲醇精馏塔70,甲醇精馏塔70上有第二冷凝器71和第一再沸器72,分离出甲醇,在进入顺丁烯二酸二甲酯精馏塔80,顺丁烯二酸二甲酯精馏塔80上有第三冷凝器81和第二再沸器82,分离出顺丁烯二酸二甲酯,
[0065]
之后物料在经过1,4-丁二醇精馏塔90,1,4-丁二醇精馏塔90上有第四冷凝器91和第三再沸器92,精馏出的1,4-丁二醇精馏塔90从产物出口93出来,收集并保存。
[0066]
甲醇和顺酐酯化反应生成顺丁烯二酸二甲酯,之后顺丁烯二酸二甲酯进行加氢反应,最后精馏纯化产物得到1,4-丁二醇。
[0067]
加氢反应的温度为160℃,压力为3mpa。
[0068]
实施例2
[0069]
其他操作步骤与实施例1相同,区别仅在于:加氢反应器内部仅有气动式微界面发生器。
[0070]
实施例3
[0071]
其他操作步骤与实施例1相同,区别仅在于:加氢反应器内部仅有液动式微界面发生器。
[0072]
实施例4
[0073]
其他操作步骤与实施例1相同,区别仅在于:气动式微界面发生器和液动式微界面发生器之间没有连通通道。
[0074]
对比例1
[0075]
其他操作步骤与实施例1相同,区别仅在于:加氢反应器内部不设置任何微界面发生器。
[0076]
通过对比上述实施例1-4与对比例1之后得到如下数据:
[0077][0078]
通过实施例1与实施例2-4相比,加氢反应器设置的不是气液联动式微界面发生器,而只是单一气动式微界面发生器、液动式微界面发生器,这样会降低1,4-丁二醇的反应效率,提高加氢反应的温度及压力,增大了反应的能耗。
[0079]
本发明通过设置了气液联动式微界面发生器将氢气分散破碎为氢气微气泡,氢气微气泡与顺丁烯二酸二甲酯之间反应增大了相界传质面积,提高了反应效率。其中气液联动式微界面发生器分为液动式微界面发生器和气动式微界面发生器,液动式微界面发生器的外边连接有循环泵,循环泵将液态物料抽吸加压后返回至液动式微界面发生器,液动式微界面发生器通过连通管道将液态物料压缩进气动式微界面发生器,这样可以有效地缓解气动式微界面发生器被顺丁烯二酸二甲酯堵塞气孔的问题,同时也提高了反应效率。
[0080]
最后应说明的是:以上各实施例仅用以说明本发明的技术方案,而非对其限制;尽管参照前述各实施例对本发明进行了详细的说明,本领域的普通技术人员应当理解:其依然可以对前述各实施例所记载的技术方案进行修改,或者对其中部分或者全部技术特征进行等同替换;而这些修改或者替换,并不使相应技术方案的本质脱离本发明各实施例技术方案的范围。
再多了解一些
本文用于企业家、创业者技术爱好者查询,结果仅供参考。