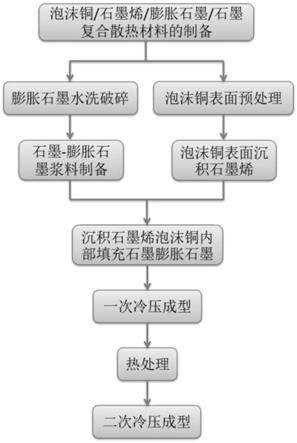
1.本发明涉及散热材料制备技术领域。具体地说是一种泡沫铜-石墨烯-膨胀石墨-石墨复合散热材料及其制备方法。
背景技术:
2.近年来,随着科技迅速发展、电子产品更新换代速度逐渐加快,传统的金属基复合材料已经难以满足电子产品散热需求,在高铁动车等高速运行的列车驱动部分中,制动处摩擦部分需要满足散热快、强度性能高、摩擦性能好的需求。而传统的铜制模块存在重量大、生产成本高等缺点。
3.金属基复合材料因其兼具有金属基体和无机填充物的优势,在电子封装、滑动受电等众多领域具有很大的应用潜力。以金属铜为基体,石墨作为无机物制备的铜/石墨复合材料因具有较高的导热性以及较低的膨胀系数,成为极具潜力的电子封装材料。但现有的金属基复合材料在使用或制备过程中还存在缺陷,比如铜与碳材料的界面浸润性差、由于碳材料的掺入导致散热材料的强度不足,或者为保证其力学性能满足要求,散热材料重量大、成本高,或者所制备得到的散热材料在垂直面内导热性差等。
技术实现要素:
4.为此,本发明所要解决的技术问题在于提供一种质量轻、垂直面内导热性能好、散热能力强、力学及耐磨性能佳的泡沫铜-石墨烯-膨胀石墨-石墨复合散热材料及其制备方法,以解决当前复合散热材料垂直面内导热性能差、铜与碳材料界面浸润性差以及力学性能不理想等问题。
5.为解决上述技术问题,本发明提供如下技术方案:
6.一种泡沫铜-石墨烯-膨胀石墨-石墨复合散热材料的制备方法,包括如下步骤:
7.步骤a:将泡沫铜进行预处理,在预处理后的所述泡沫铜表面负载改性氧化石墨烯,得到表面负载改性氧化石墨烯泡沫铜;
8.步骤b:将石墨粉末和膨胀石墨粉末充分混合后,得到混合粉末;将所述混合粉末填充到所述表面负载改性氧化石墨烯泡沫铜内部孔隙中,得到复合散热材料前驱体;向表面负载改性氧化石墨烯泡沫铜内部孔隙中填充石墨与膨胀石墨,一方面可以降低复合材料中铜的含量,使其在降低复合材料摩擦系数的同时,极大地降低复合材料的生产成本;一方面有助于提高复合材料的面内导热性能:膨胀石墨通过泡沫铜孔洞相互连接,可以保证较高的面内导热系数。之所以选择石墨粉末和膨胀石墨粉末混合作为填充原料,是因为:若单独采用石墨对泡沫铜进行填充:石墨具有较好的润滑性,在泡沫铜孔洞中的成块性能较差,易发生掉粉现象,且单独填充石墨会由于石墨层内导热能力差而使制备得到的复合散热材料的面内导热性能不理想;另外,单独填充石墨对复合散热材料的强度和力学性能也有不利影响。若单独采用膨胀石墨对泡沫铜进行填充:虽然膨胀石墨层内导热能力强,膨胀石墨
在压合成片时,其面内导热系数非常高,但由于膨胀石墨较为蓬松,在泡沫铜内部填充时,填充密度比较低,难以将材料压密实,导致复合材料内部容易出现孔洞,从而降低复合材料的导热性能,同时还会提高复合材料中铜的含量,因此在单独填充膨胀石墨时,需要对膨胀石墨进行较为严格的破碎处理;但过度地破碎处理会破坏膨胀石墨的层内结构,从而影响其面内及垂直面内导热性能;而将膨胀石墨和石墨混合填充:石墨为颗粒状,进行适当破碎后的膨胀石墨呈片状;石墨粉的加入可以使颗粒状的石墨填充到膨胀石墨在泡沫铜内部搭接形成的孔洞中,使得复合材料填充密度高,且在石墨、膨胀石墨和泡沫铜三者的相互协同作用下,使得复合散热材料具有面内及垂直面内导热性好、机械强度高和耐磨性好的特性。
9.步骤c:将所述复合散热材料前驱体采用冷压的方式压制成型,得到复合散热材料预制块;
10.步骤d:将所述复合散热材料预制块进行热处理,得到复合散热中间材料;
11.步骤e:将所述复合散热中间材料进行二次冷压,得到泡沫铜-石墨烯-膨胀石墨-石墨复合散热材料。采用先冷压成型,然后热处理,最后进行二次冷压成型得到的复合散热材料,相比直接热压成型得到的复合散热材料,其面内及垂直面内导热性能更好;且只需冷压机和热处理炉就能完成,且热处理炉可同时处理多个产品,具有设备简单、价格低廉,容易实现连续式生产的优势;而热压设备一般比较昂贵,其单次处理产品的数量较少,并需要抽真空、保温、保压,生产效率非常低。
12.上述泡沫铜-石墨烯-膨胀石墨-石墨复合散热材料的制备方法,步骤a中,所述泡沫铜的孔隙密度为20~40ppi,所述泡沫铜的孔隙率大于或等于90%,所述泡沫铜的厚度为1~100mm;泡沫铜的孔隙密度若过大,石墨及膨胀石墨填入困难,复合材料块体会形成大量孔洞,导热性能较低;若泡沫铜孔隙密度过小,复合材料中铜含量降低,冷压时容易压裂,且会降低材料的力学性能,同时其垂直与面内的导热性能也会降低。所述改性氧化石墨烯的粒径为50~70μm,该粒径范围内的改性氧化石墨烯负载效果较好;若直接使用氧化石墨烯进行负载,则氧化石墨烯的大量含氧官能团会影响声子导热,造成复合材料导热性能的降低;另外,进行热处理有利于去除改性氧化石墨烯表面残留的含氧官能团,有助于提高复合材料的导热性能。
13.上述泡沫铜-石墨烯-膨胀石墨-石墨复合散热材料的制备方法,所述改性氧化石墨烯的制备方法为:
14.(1)制备氧化石墨烯:将石墨置于冰浴条件下,向石墨中依次加入质量分数为98wt%的浓硫酸和质量分数为98wt%浓磷酸,混合均匀后边搅拌边分次加入高锰酸钾,搅拌均匀后在水浴条件下充分反应,将水浴反应结束后得到的混合反应体系降至室温,并将其转移至冰浴条件下;在冰浴条件下,向所述混合反应体系中加入去离子水,然后逐滴滴加质量分数为30wt%的过氧化氢至所述混合反应体系变为金黄色,然后离心并将离心得到的沉淀物水洗至其上清液的ph为6~7,最后将水洗后的沉淀物进行冷冻干燥,即得到氧化石墨烯;
15.(2)由氧化石墨烯制备改性氧化石墨烯:将氧化石墨烯粉末分散到n,n-二甲基甲酰胺中,然后加入γ-氨丙基三乙氧基硅烷,在常温下进行磁力搅拌使其充分反应,反应结束后抽滤,并用n,n-二甲基甲酰胺进行洗涤,得到γ-氨丙基三乙氧基硅烷修饰氧化石墨烯;将所述γ-氨丙基三乙氧基硅烷修饰氧化石墨烯和水合肼依次加入到n,n-二甲基甲酰
胺中,加热并进行机械搅拌使其充分反应,反应结束后冷却至室温,抽滤并用n,n-二甲基甲酰胺洗涤,干燥后即得到所述改性氧化石墨烯。
16.上述泡沫铜-石墨烯-膨胀石墨-石墨复合散热材料的制备方法,步骤a中,表面负载改性氧化石墨烯处理的方式为物理沉积法;所述物理沉积法的操作方法为:先将所述泡沫铜浸渍于改性氧化石墨烯分散液中,然后用超声沉积的方式将所述改性氧化石墨烯沉积到所述泡沫铜表面,最后将浸渍后的所述泡沫铜取出烘干;重复所述物理沉积法的操作过程3~5次。
17.上述泡沫铜-石墨烯-膨胀石墨-石墨复合散热材料的制备方法,单次超声沉积的时间为8~15min,烘干温度为60~70℃,烘干时间为10~15min;
18.所述改性氧化石墨烯分散液中所述改性氧化石墨烯的质量体积比浓度为1~5mg/ml,所述改性氧化石墨烯分散液的制备方法为:将所述改性氧化石墨烯加入到酒精丙酮混合液中,先超声分散0.8~1.2h,然后磁力搅拌0.8~1.2h;所述酒精丙酮混合液由体积比为1:1的无水乙醇和丙酮混合而成。之所以采用酒精丙酮混合液作为分散溶剂,是由于石墨烯在体积比为1:1的酒精丙酮混合液中具有更好的分散性,同时将其沉积于泡沫铜时得到的石墨烯沉积层分布也较为均匀。
19.上述泡沫铜-石墨烯-膨胀石墨-石墨复合散热材料的制备方法,步骤b中,采用真空抽滤的方式将所述混合粉末填充在泡沫铜内部孔隙中;所述混合粉末中,所述膨胀石墨粉末与所述石墨粉末的质量之比为1:8~1:12,由于石墨粉末自身的导热能力较差,充填过多会影响复合散热材料的散热性,因此,石墨粉的添加量以能够将膨胀石墨在泡沫铜内部搭接形成的孔洞填满为标准,试验中证明,当膨胀石墨粉末与所述石墨粉末的质量之比为1:8~1:12范围内时,既能保证将膨胀石墨在泡沫铜内部搭接形成的孔洞填满,又可以将石墨对复合散热材料导热性能的不利影响降至最低;所述石墨粉末的平均粒径为106~150μm,所述石墨粉末的层间距为0.3~0.4nm;所述膨胀石墨粉末的平均粒径为150~300μm,所述膨胀石墨粉末的膨胀体积大于或等于330ml/g。在填充泡沫铜空隙时,石墨粉末和膨胀石墨粉末的粒径过大,会造成填充不充分,复合材料块体内部会形成孔洞;若粒径太小,则接触界面增加,影响复合材料的导热性能。另外,石墨粉末的粒径要配合膨胀石墨粉末的粒径,若石墨粉末粒径过大,不能有效填充膨胀石墨搭接形成的孔洞,起不到消除复合材料内部孔洞的作用;若石墨粉末粒径太小,一是压块时成块性较差,容易漏粉,再就是接触界面增多,导热性能下降。而当石墨粉末和膨胀石墨粉末粒径在上述范围内时,填充后得到的复合材料的面内及垂直面内导热性能最好。
20.上述泡沫铜-石墨烯-膨胀石墨-石墨复合散热材料的制备方法,步骤b的具体操作方法为:先将所述膨胀石墨粉末球磨4h,然后按照所述膨胀石墨粉末与所述石墨粉末质量之比为1:10的比例进行混合,得到所述混合粉末;将所述混合粉末均匀地分散到n-甲基吡咯烷酮中,进行磁力搅拌3h,得到石墨-膨胀石墨浆料;所述石墨-膨胀石墨浆料中,所述混合粉末与n-甲基吡咯烷酮的质量之比为1:5~10;然后将所述表面负载改性氧化石墨烯泡沫铜置于抽滤装置中,采取少量多次的方法将所述石墨-膨胀石墨浆料倒在所述表面负载改性氧化石墨烯泡沫铜上,使所述石墨-膨胀石墨浆料在抽滤装置的作用下均匀填充到所述表面负载改性氧化石墨烯泡沫铜内部;抽滤填充完毕后,在150℃条件下真空干燥24h,以除去多余的有机溶剂,即得到所述复合散热材料前驱体;
21.或者,步骤b的具体操作方法为:先按照所述膨胀石墨粉末与所述石墨粉末质量之比为1:10的比例进行混合,得到所述混合粉末;将所述混合粉末均匀地分散到n-甲基吡咯烷酮中,进行磁力搅拌48h,得到石墨-膨胀石墨浆料;所述石墨-膨胀石墨浆料中,所述混合粉末与n-甲基吡咯烷酮的质量之比为1:5~10;然后将所述表面负载改性氧化石墨烯泡沫铜置于抽滤装置中,采取少量多次的方法将所述石墨-膨胀石墨浆料倒在所述表面负载改性氧化石墨烯泡沫铜上,使所述石墨-膨胀石墨浆料在抽滤装置的作用下均匀填充到所述表面负载改性氧化石墨烯泡沫铜内部;抽滤填充完毕后,在150℃条件下真空干燥24h,以除去多余的有机溶剂,即得到所述复合散热材料前驱体。
22.上述泡沫铜-石墨烯-膨胀石墨-石墨复合散热材料的制备方法,步骤c中,冷压压力为100~150mpa,保压时间为5~10min;在冷压压力为100~150mpa情况下,复合材料可以被很好地压成块体材料,成块性能较好;压力过大对设备的要求较高,增加设备的投入,压力过小,得到的复合材料压实密度低,成块性不好,容易漏粉;
23.步骤d中,热处理的条件为:在氩气气氛下进行热处理,处理温度为850~950℃,处理时间为1.5~2.5h;在此热处理的条件下,改性氧化石墨烯表面残留的含氧官能团能被有效的去除,同时膨胀石墨层间的氧也能被有效的去除,有效提高声子传热,从而提高材料的面内及垂直面内导热性能;另外,热处理温度不宜过高,由于铜的熔点为1080℃,热处理温度太高容易接近铜的熔点,造成泡沫铜的局部熔化,并且造成能耗增加,生产成本增加;
24.步骤e中,二次冷压的压力为200~300mpa,保压时间为5~10min;在冷压压力为200~300mpa的条件下,可将热处理导致复合材料内部形成的微孔洞很好的压合,有利于进一步提高复合材料的导热系数。当压力大于300mpa,与200~300mpa的压力相比,对导热性能的影响不大,但是对设备的要求较高,增加设备的投入;但若压力过小(小于200mpa时),则不能有效消除复合材料内部因热处理而形成的微孔洞,故不能很好的提高导热系数。
25.上述泡沫铜-石墨烯-膨胀石墨-石墨复合散热材料的制备方法,步骤a中,所述泡沫铜的预处理方法为:将所述泡沫铜依次用丙酮和质量分数为10wt%的盐酸溶液分别清洗10min,然后用去离子水冲洗,并置于真空干燥箱中在60℃条件下干燥1h。
26.泡沫铜-石墨烯-膨胀石墨-石墨复合散热材料,采用上述泡沫铜-石墨烯-膨胀石墨-石墨复合散热材料的制备方法制备得到;所述复合散热材料中铜的质量分数为30~40wt%,所述复合散热材料的面内导热系数为720~800w/(m
·
k),垂直面内导热系数为350~400w/(m
·
k),密度为5~6g/cm3,抗弯强度为25~30mpa。
27.本发明的技术方案取得了如下有益的技术效果:
28.本发明以泡沫铜为骨架,制备泡沫铜-石墨烯-膨胀石墨-石墨复合散热材料。该材料内部的泡沫铜骨架可以保持复合散热材料内三维网络结构,保留完整的铜传热通路,提升散热片在垂直面内方向的导热性能,同时为散热材料提供一定的强度;该材料具备的通孔结构也可以使得碳材料在泡沫铜内部形成连续结构,保证其面内具备较高的热传导性能。另外,在复合散热材料中填充膨胀石墨可以极大地提升复合材料的导热性能,同时与石墨粉混合可以解决因填实密度低而导热效果不佳的问题。在制备复合散热材料时,利用自制氧化石墨烯改性后得到的改性氧化石墨烯对泡沫铜表面进行改性氧化石墨烯的表面负载处理,可以有效改善铜基体与石墨材料之间润湿性差的问题,从而提升界面结合力、降低界面热阻。本发明制备的泡沫铜-石墨烯-膨胀石墨-石墨复合散热材料既能够满足应用所
需的散热性能,又可以满足设备所需强度性能及摩擦性能。
29.本发明解决了碳材料垂直面内导热性能差的问题,同时提高了泡沫铜与碳材料界面浸润性,增强碳材料填充物与铜骨架之间的结合力,在提升复合散热片的导热性能的同时还提高了其力学性能。采用本发明的制备方法所制备的泡沫铜-石墨烯-膨胀石墨-石墨复合散热材料较于市面所购买的商业超高导热石墨纸相比,在铜的质量分数为30~40wt%,且其面内导热系数相近【720~800w/(m
·
k)】的情况下,而在垂直面内方向上其导热能力为商业超高导热石墨纸的30余倍,具有与紫铜相同的导热系数。同时本发明制备石墨复合材料生产过程简单,通过在泡沫铜表面浸渍沉积石墨烯的方式,使泡沫铜表面负载改性氧化石墨烯,并将其作为泡沫铜与石墨和膨胀石墨的中间层,解决铜-碳材料界面之间浸润性差的问题;通过两次冷压成型,消除了几种材料间的微孔洞与间隙,极大地提高了复合材料中石墨材料与泡沫铜之间的结合力,使复合散热材料的导热性能得到极大的提升。
30.本发明中,泡沫铜-石墨烯-膨胀石墨-石墨复合散热材料的面内导热系数可达776.8w/(m
·
k),垂直面内的导热系数可达392.7w/(m
·
k);另外,本发明的制备工艺极大地增强了石墨烯/膨胀石墨/石墨填充材料与铜骨架之间的结合力,增强了复合散热材料的力学性能,使得其体积密度达到为5.3g/cm3,抗弯强度达到为26.9mpa,其耐磨性最高约为商业导热石墨纸1.3倍。本发明通过严谨的加工步骤、制备方法简单高效,使成品复合散热材料在减轻散热材料整体质量、提升其散热能力的前提下,还具有力学性能优异的优点,整体散热效果好,使用寿命长,符合实际应用要求,同时极大地降低了散热元件的生产成本。
附图说明
31.图1本发明泡沫铜-石墨烯-膨胀石墨-石墨复合材料制备工艺流程示意图;
32.图2本发明实施例2制备得到的复合材料实拍图;
33.图3本发明实施例2制备得到的复合材料实物横截面照片;
34.图4本发明实施例2制备得到的复合材料垂直面内导热性能曲线图;
35.图5在荷载为3n的条件下,不同泡沫铜原料制备得到的复合散热材料其摩擦系数与磨损量对比结果图。
具体实施方式
36.本发明泡沫铜-石墨烯-膨胀石墨-石墨复合材料制备工艺流程如图1所示,下面结合实施例对本发明的制备方法做进一步说明。
37.实施例1
38.本实施例中,泡沫铜-石墨烯-膨胀石墨-石墨复合散热材料的制备方法,其特征在于,包括如下步骤:
39.步骤a:将泡沫铜进行预处理,在预处理后的泡沫铜表面负载改性氧化石墨烯,得到表面负载改性氧化石墨烯泡沫铜;本实施例所用泡沫铜的孔隙密度为20ppi,泡沫铜的孔隙率大于90%,泡沫铜的厚度为10mm,泡沫铜的直径为30mm;
40.泡沫铜的预处理方法:将泡沫铜依次用丙酮和质量分数为10wt%的盐酸溶液分别清洗10min,然后用去离子水冲洗,并置于真空干燥箱中在60℃条件下干燥1h;预处理可去除泡沫铜表面油渍和氧化物等;
41.所用改性氧化石墨烯为采用本实施例自制的氧化石墨烯进行改性得到,即:将自制的氧化石墨烯溶解于n,n-二甲基甲酰胺dmf中,利用γ-氨丙基三乙氧基硅烷kh550对其进行改性,改性后利用水合肼n2h4·
h2o对其进行还原,得到改性氧化石墨烯;本实施例制备得到的所述改性氧化石墨烯的粒径在50~70μm之间。
42.本实施例中,改性氧化石墨烯的制备方法为:
43.(1)制备氧化石墨烯:将1.5g石墨加入烧杯中,冰浴条件下依次加入150ml质量分数98wt%的浓硫酸、50ml质量分数为98wt%的浓磷酸,混合均匀后,边搅拌边少量多次加入15g高锰酸钾,然后在60℃条件下水浴8h,使其充分反应,取出降至室温后,在冰浴条件下加入去离子水至400ml,然后逐滴滴加质量分数为30wt%的过氧化氢至溶液变为金黄色,然后离心并将离心得到的沉淀物水洗至其上清液的ph为6~7,最后将水洗后的沉淀物进行冷冻干燥,即得到氧化石墨烯粉末。
44.(2)由氧化石墨烯制备改性氧化石墨烯:取0.1g步骤(1)中自制的氧化石墨烯粉末,将其分散到100ml n,n-二甲基甲酰胺dmf中,然后倒入250ml三口瓶里,加入0.1gγ-氨丙基三乙氧基硅烷kh550,磁力搅拌下(800rpm)常温反应12h,抽滤后,用n,n-二甲基甲酰胺dmf多次洗涤,得到γ-氨丙基三乙氧基硅烷kh550修饰的氧化石墨烯;然后取0.1gγ-氨丙基三乙氧基硅烷kh550修饰的氧化石墨烯,转移到250ml三口瓶中,并加入0.2g水合肼n2h4·
h2o和100ml n,n-二甲基甲酰胺dmf,加热到80℃后,机械搅拌(200rpm)反应12h,冷却至室温,然后抽滤并用n,n-二甲基甲酰胺dmf多次洗涤,最后在40℃真空干燥后得到改性氧化石墨烯。
45.表面负载改性氧化石墨烯处理的方式为物理沉积法,即:先将泡沫铜浸渍于改性氧化石墨烯分散液中,然后用超声沉积的方式超声沉积10min,将改性氧化石墨烯沉积到泡沫铜表面,最后将浸渍后的泡沫铜取出在60℃条件下真空干燥15min进行烘干;重复上述物理沉积法的操作过程4次,泡沫铜的质量不再增加,即得到表面负载改性氧化石墨烯泡沫铜;
46.改性氧化石墨烯分散液中改性氧化石墨烯的质量体积比浓度为1mg/ml,改性氧化石墨烯分散液的制备方法为:将改性氧化石墨烯加入到酒精丙酮混合液中,先超声分散1h,然后磁力搅拌1h;所述酒精丙酮混合液由体积比为1:1的无水乙醇和丙酮混合而成。
47.步骤b:将石墨粉末和膨胀石墨粉末充分混合后,得到混合粉末;将所述混合粉末填充到所述表面负载改性氧化石墨烯泡沫铜内部孔隙中,得到复合散热材料前驱体;膨胀石墨粉末和石墨粉末的质量之比为1:10;所用膨胀石墨粉末和石墨粉末的纯度均为99.9wt%;所述石墨粉末的平均粒径为106μm,所述石墨粉末的层间距为0.3~0.4nm;所述膨胀石墨粉末的平均粒径为150μm,所述膨胀石墨粉末的膨胀体积为330ml/g;
48.采用真空抽滤的方式将混合粉末填充到表面负载改性氧化石墨烯泡沫铜内部空隙中,具体操作方法为:先将膨胀石墨粉末水洗破碎,即采用球磨4h的方式进行破碎【球磨可以减小膨胀石墨的粒径,球磨后,膨胀石墨从原来的蠕虫状变为片状,且其平均粒径减小至50μm,可更好填充到泡沫铜芯部孔隙】,然后按照膨胀石墨粉末与石墨粉末质量之比为1:10的比例进行混合,得到混合粉末;将混合粉末均匀地分散到250ml的n-甲基吡咯烷酮中,进行磁力搅拌3h,得到石墨-膨胀石墨浆料;所述石墨-膨胀石墨浆料中,所述混合粉末与n-甲基吡咯烷酮的质量之比为1:10;然后采用真空抽滤的方式将石墨-膨胀石墨浆料填充在
表面负载改性氧化石墨烯泡沫铜内部孔隙中,填充时,将表面负载改性氧化石墨烯泡沫铜置于抽滤装置中,采取少量多次的方法将石墨-膨胀石墨浆料倒在所述表面负载改性氧化石墨烯泡沫铜上,使所述石墨-膨胀石墨浆料在抽滤装置的作用下均匀完整地填充到表面负载改性氧化石墨烯泡沫铜内部,抽滤填充完毕后,在150℃条件下真空干燥24h,以除去多余的有机溶剂,即得到复合散热材料前驱体;
49.步骤c:将所述复合散热材料前驱体采用冷压的方式压制成型,得到复合散热材料预制块;本实施例采用φ30mm模具在100mpa压力下保压10min压制成片(在其他一些实施例中,可将该复合散热材料根据实际使用需求,加工成各种形状);
50.步骤d:将所述复合散热材料预制块进行热处理,得到复合散热中间材料;热处理条件为:在ar2气氛下900℃烧结2h,以去除残留在石墨内部的n-甲基吡咯烷酮;在热处理过程中,残留有机溶剂的挥发将使得复合散热片内部形成孔洞空隙,降低复合散热片性能,因此需要进行二次冷压。
51.步骤e:将所述复合散热中间材料进行二次冷压,得到泡沫铜-石墨烯-膨胀石墨-石墨复合散热材料;二次冷压的条件为:室温下在200mpa压力下保压10min,有利于将热处理过程中形成的内部孔洞空隙消除,提升复合散热片的致密度。
52.本实施例制备得到的泡沫铜-石墨烯-膨胀石墨-石墨复合散热材料中铜的质量分数为39wt%,该复合散热材料的整体密度为5.28g/cm3,其面内导热系数为737.6w/(m
·
k),垂直面内的导热系数为384w/(m
·
k),抗弯强度为24.5mpa。
53.实施例2
54.本实施例中,泡沫铜-石墨烯-膨胀石墨-石墨复合散热材料的制备方法,其特征在于,包括如下步骤:
55.步骤a:将泡沫铜进行预处理,在预处理后的泡沫铜表面负载改性氧化石墨烯,得到表面负载改性氧化石墨烯泡沫铜;本实施例所用泡沫铜的孔密度为20ppi,泡沫铜的孔隙率大于90%,泡沫铜的厚度为10mm,泡沫铜的直径为30mm;
56.泡沫铜的预处理方法:将泡沫铜依次用丙酮和质量分数为10wt%的盐酸溶液分别清洗10min,然后用去离子水冲洗,并置于真空干燥箱中在60℃条件下干燥1h;预处理可去除泡沫铜表面油渍和氧化物等;
57.所用改性氧化石墨烯为采用本实施例自制的氧化石墨烯进行改性得到,即:将自制的氧化石墨烯溶解于n,n-二甲基甲酰胺dmf中,利用γ-氨丙基三乙氧基硅烷kh550对其进行改性,改性后利用水合肼n2h4·
h2o对其进行还原,得到改性氧化石墨烯;本实施例制备得到的所述改性氧化石墨烯的粒径在50~70μm之间;本实施所用改性氧化石墨烯的制备方法与实施例1相同。
58.表面负载改性氧化石墨烯处理的方式为物理沉积法,即:先将泡沫铜浸渍于改性氧化石墨烯分散液中,然后用超声沉积的方式超声沉积10min,将改性氧化石墨烯沉积到泡沫铜表面,最后将浸渍后的泡沫铜取出在60℃条件下真空干燥15min;重复上述物理沉积法的操作过程3次,泡沫铜的质量不再增加,即得到表面负载改性氧化石墨烯泡沫铜;表面负载改性氧化石墨烯处理后,改性氧化石墨烯作为中间层,可以增强膨胀石墨-石墨粉体与泡沫铜之间的结合力,解决泡沫铜与碳材料界面浸润性差的问题;
59.改性氧化石墨烯分散液中改性氧化石墨烯的质量分数为1mg/ml,改性氧化石墨烯
分散液的制备方法为:将改性氧化石墨烯加入到酒精丙酮混合液中,先超声分散1h,然后磁力搅拌1h;所述酒精丙酮混合液由体积比为1:1的无水乙醇和丙酮混合而成。
60.步骤b:将石墨粉末和膨胀石墨粉末充分混合后,得到混合粉末;将所述混合粉末填充到所述表面负载改性氧化石墨烯泡沫铜内部孔隙中,得到复合散热材料前驱体;膨胀石墨粉末与石墨粉末的质量之比为1:10;所用膨胀石墨粉末和石墨粉末的纯度均为99.9wt%;所述石墨粉末的平均粒径为106μm,所述石墨粉末的层间距为0.3~0.4nm;所述膨胀石墨粉末的平均粒径为150μm,所述膨胀石墨粉末的膨胀体积为330ml/g;
61.采用真空抽滤的方式将混合粉末填充到表面负载改性氧化石墨烯泡沫铜内部空隙中,具体操作方法为:先按照膨胀石墨粉末与石墨粉末质量之比为1:10的比例进行混合,得到混合粉末;将混合粉末均匀地分散到250ml的n-甲基吡咯烷酮中,进行磁力搅拌48h,得到石墨-膨胀石墨浆料;所述石墨-膨胀石墨浆料中,所述混合粉末与n-甲基吡咯烷酮的质量之比为1:10;然后采用真空抽滤的方式将石墨-膨胀石墨浆料填充在表面负载改性氧化石墨烯泡沫铜内部孔隙中,填充时,将表面负载改性氧化石墨烯泡沫铜置于抽滤装置中,采取少量多次的方法将石墨-膨胀石墨浆料倒在所述表面负载改性氧化石墨烯泡沫铜上,使所述石墨-膨胀石墨浆料在抽滤装置的作用下均匀完整地填充到表面负载改性氧化石墨烯泡沫铜内部,抽滤填充完毕后,在150℃条件下真空干燥24h,以除去多余的有机溶剂,即得到复合散热材料前驱体;本步骤与实施例1中膨胀石墨的球磨法破碎处理方法不同,采用磁力搅拌48小时的处理方法相较于球磨法而言,同样可以将膨胀石墨破碎成片层状,但破碎后得到的膨胀石墨的平均粒径保持在140μm,因此,相对于实施例1而言本实施例的膨胀石墨其片层结构比较完整、面内导热性能更好;
62.步骤c:将所述复合散热材料前驱体采用冷压的方式压制成型,得到复合散热材料预制块;本实施例采用φ30mm模具在100mpa压力下保压10min压制成片;
63.步骤d:将所述复合散热材料预制块进行热处理,得到复合散热中间材料;热处理条件为:在氩气气氛下900℃烧结2h,以去除残留在石墨内部的n-甲基吡咯烷酮;在热处理过程中,残留有机溶剂的挥发将使得复合散热片内部形成孔洞空隙,降低复合散热片性能,因此需要进行二次冷压。
64.步骤e:将所述复合散热中间材料进行二次冷压,得到泡沫铜-石墨烯-膨胀石墨-石墨复合散热材料;二次冷压的条件为:室温下在200mpa压力下保压10min,有利于将热处理过程中形成的内部孔洞空隙消除,提升复合散热片的致密度。
65.图2为本实施例制备得到的复合材料实拍图,从图2中可以看出泡沫铜呈网状结构,均匀分布于复合材料整个面内,形成一个相互连通的骨架结构,同时复合材料表面光滑,外形规则,结构紧密;图3为本实施例制备得到的复合材料实物横截面照片,从图3中可以看出复合材料内部结构紧密,无微孔洞存在;泡沫铜骨架之上而下均匀分布于复合材料内部,贯穿复合材料,保证垂直于面内的导热性能;同时内部填充的石墨及膨胀石墨保持相互连通状态,可有效地发挥膨胀石墨面内高导热的特性,从而使得复合材料面内与垂直面内具有高的导热系数;图4为不同沉积工艺条件下复合材料垂直面内导热性能曲线图,从图4中可以看出复合材料垂直面内的导热系数可达到392.7w/(m
·
k)。
66.本实施例制备得到的泡沫铜-石墨烯-膨胀石墨-石墨复合散热材料中铜的质量分数为39wt%,该复合散热材料的整体密度为5.39g/cm3,其面内导热系数约776.8w/(m
·
k),
垂直面内的导热系数约392.7w/(m
·
k),抗弯强度为26.9mpa。
67.对比例1
68.本对比例采用孔隙密度为10ppi、孔隙率大于90%、厚度为10mm且直径为30mm的泡沫铜为原料,其它原料均与实施例2相同,采用实施例2中泡沫铜-石墨烯-膨胀石墨-石墨复合散热材料的制备方法,制备得到了复合散热材料。
69.对比例2
70.本对比例采用孔隙密度为40ppi、孔隙率大于90%、厚度为10mm且直径为30mm的泡沫铜为原料,其它原料均与实施例2相同,采用实施例2中泡沫铜-石墨烯-膨胀石墨-石墨复合散热材料的制备方法,制备得到了复合散热材料。
71.在载荷为3n下,测定孔隙密度不同【10ppi(对比例1)、20ppi(实施例2)、40ppi(对比例2)】的泡沫铜原料制备得到的复合散热材料的摩擦系数与磨损量,并以商业导热石墨纸(孔隙密度为0ppi)为对比试样,结果如图5所示。
72.从图5中可以看出,泡沫铜的孔隙密度为20ppi时,制备得到的复合散热材料的摩擦系数为0.136,此时泡沫铜骨架可以为复合散热材料形成足够的硬度支撑,可以防止在摩擦过程中形成片层剥离,导致摩擦系数较高,且石墨可以在摩擦过程中在复合材料表面形成足够的石墨润滑膜,因此减磨效果最好;当泡沫铜的孔隙密度为40ppi时,制备得到的复合散热材料的摩擦系数为0.152,此时复合散热材料的泡沫铜表面积比较大,在摩擦过程中不足以形成完整的润滑膜,而铜本身摩擦系数高于石墨,所以摩擦系数有所升高。从图中还可以看出,复合散热材料的磨损量则随泡沫铜的孔隙密度增加而减小,且均小于纯石墨片(商业导热石墨纸)9.3mg的磨损量,且泡沫铜孔隙密度为40ppi所制备的复合散热材料且磨损量降低至6.4mg,相对于商业导热石墨纸降低了31.2%;这是因为泡沫铜可减少石墨在摩擦过程中形成的疲劳脱落,随孔隙密度的增加,泡沫铜在复合散热材料表层的面积比增加,从而使复合散热材料形成更加紧密的三维互穿结构,因此其磨损量逐渐降低。
73.显然,上述实施例仅仅是为清楚地说明所作的举例,而并非对实施方式的限定。对于所属领域的普通技术人员来说,在上述说明的基础上还可以做出其它不同形式的变化或变动。这里无需也无法对所有的实施方式予以穷举。而由此所引伸出的显而易见的变化或变动仍处于本专利申请权利要求的保护范围之中。
再多了解一些
本文用于企业家、创业者技术爱好者查询,结果仅供参考。