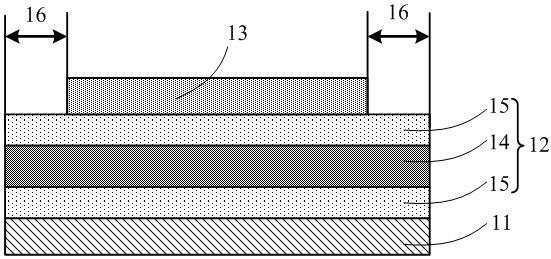
1.本技术涉及电化学技术领域,特别是涉及一种电化学装置和电子装置。
背景技术:
2.现有技术中,提高电化学装置安全性能主要是从提高电极组件的自身强度出发,降低电极组件的破损,或者由破损而引发的电极短路的概率。例如,可以采用高强度、高延展金属集流体,高粘性、高韧性的正极材料层和/或负极材料层,或者是高强度、高延展性的隔膜等方式。但是,这些方式对电极组件自身强度的改善均很有限,并且会明显增加电化学装置的成本,因此上述方法的应用受限。
3.现有技术中,另一种方式是采用双面胶将电极组件和外包装粘接固定,来减少跌落时电极组件在外包装内的晃动,提高电化学装置安全性能。但是,现有的双面胶一般采用聚对苯二甲酸乙二酯(pet)或聚丙烯(pp)等作为基材,其自身强度较低,相对较软。在钝器直接作用下的钝性力冲击(dent,简称钝刺)下,电极组件容易受破损,而破损容易引发电极短路,从而影响电化学装置的安全性能。
技术实现要素:
4.本技术的目的在于提供一种电化学装置和电子装置,以提高电极组件的抗变形、抗跌落以及抗钝刺能力,从而提升电化学装置的安全性能。具体技术方案如下:本技术的第一方面提供了一种电化学装置,其包含电极组件、外包装和双面胶,所述双面胶设于所述电极组件和所述外包装之间;所述双面胶包含粘结层、复合层、热熔层,所述复合层设于所述粘结层和所述热熔层之间,所述复合层的抗拉强度≥500mpa,断裂伸长率≥15%。发明人发现,通过将双面胶设于电极组件和外包装之间,使双面胶将电极组件和外包装粘接固定,从而使电极组件、双面胶和外包装形成一个整体,减少跌落过程中电极组件与外包装之间的晃动。发明人还发现,通过将双面胶设计为粘结层、复合层、热熔层的三层结构,将所述复合层设于所述粘结层和所述热熔层之间,并调控位于双面胶中间的复合层的抗拉强度≥500mpa,断裂伸长率≥15%,以使双面胶中复合层的机械强度得到提高,进而提高双面胶的机械强度。这样,双面胶对电极组件最外层的保护加强,能够降低电极组件在跌落或钝性力冲击下受到破损的风险,提高电极组件的钝刺承受极限力,以使电极组件的抗变形、抗跌落以及抗钝刺能力均得以提高,从而提升电化学装置的安全性能。
5.在本技术的一种实施方案中,所述复合层包含基材层和分别位于所述基材层两个表面上的绝缘层;所述基材层的材料包含金属复合材料;所述绝缘层的材料包含聚酰胺、聚丙烯、聚乙烯或聚对苯二甲酸乙二酯中的至少一种。通过将双面胶中间的复合层设计为包含基材层和分别位于所述基材层两个表面上的绝缘层这样的结构,并选用金属复合材料为基材层,可以提高双面胶中复合层的机械强度,增强对电极组件最外层的保护能力。绝缘层设置于基材层的两个表面,可以有效防止基材层裸露,或与电极组件表面的正/负极集流体接触而形成短路,从而提升电化学装置的安全性能。通过选用上述材料为绝缘层,可以有效
防止基材层与电极组件表面的正/负极集流体接触而形成短路,从而提升电化学装置的安全性能。
6.在本技术的一种实施方案中,所述金属复合材料包含不锈钢、铝合金、钛合金或镍合金中的至少一种。通过选用上述金属复合材料为基材层,有利于提高双面胶中复合层的机械强度,对电极组件最外层铝箔形成加强保护,从而提升电化学装置的安全性能。
7.在本技术的一种实施方案中,所述复合层的厚度为10
µ
m至30
µ
m,所述基材层的厚度为5
µ
m至20
µ
m,所述绝缘层的厚度为2
µ
m至10
µ
m。通过调控复合层的厚度,以及复合层中基材层和绝缘层的厚度在上述各自的范围内,有利于提高双面胶中复合层的机械强度,增强对电极组件最外层的保护能力;并且加强绝缘层对基材层的保护作用,以及提升绝缘层防止基材层与电极组件表面的正/负极集流体接触而形成短路的能力,从而提升电化学装置的安全性能。
8.在本技术的一种实施方案中,所述双面胶的总厚度为20
µ
m至50
µ
m,所述粘结层的厚度为5
µ
m至15
µ
m,所述热熔层的厚度为5
µ
m至15
µ
m。通过调控双面胶的总厚度、粘结层的厚度以及热熔层的厚度在上述各自的范围内,有利于提升电化学装置的安全性能。
9.在本技术的一种实施方案中,所述粘结层包含聚甲基丙烯酸甲酯、苯乙烯-异戊二烯-苯乙烯嵌段共聚物、聚乙烯、聚丙烯或聚酰胺中的至少一种;所述粘结层与所述电极组件的外表面粘接,粘结力为0.1n/mm至1.0n/mm。通过选用上述材料为粘结层,粘结层与电极组件的外表面粘接,调控粘结层与电极组件的外表面之间的粘结力在上述范围内,有利于提升电化学装置的安全性能。
10.在本技术的一种实施方案中,所述热熔层包含聚甲基丙烯酸甲酯、苯乙烯-异戊二烯-苯乙烯嵌段共聚物、聚乙烯、聚丙烯或聚酰胺中的至少一种;所述热熔层与所述外包装的内表面粘接,粘结力为0.1n/mm至1.0n/mm。通过选用上述材料为热熔层,热熔层与外包装的内表面粘接,调控热熔层与外包装间的粘结力在上述范围内,有利于提升电化学装置的安全性能。
11.在本技术的一种实施方案中,靠近所述热熔层一侧的所述复合层的表面上包含两个等宽度的不涂胶区域,所述热熔层与所述不涂胶区域的宽度之和等于所述复合层的宽度,所述不涂胶区域的宽度占复合层宽度的10%至40%。通过调控不涂胶宽度占复合层宽度的比例在上述范围内,可以使双面胶将电极组件和外包装粘接固定,减少跌落过程中电极组件与外包装之间的晃动,并且,可以有效缓解在电极组件在跌落触地瞬间受到的冲击力度,从而改善电化学装置的跌落通过率。
12.在本技术的一种实施方案中,所述双面胶粘接于所述电极组件外表面的面积与所述电极组件的外表面总面积的比例为30%至90%。通过调控双面胶粘接于电极组件外表面的面积与电极组件的外表面总面积的比例在上述范围内,可以使双面胶将电极组件和外包装粘接固定,减少跌落过程中电极组件与外包装之间的晃动,有利于提升电化学装置的安全性能。
13.本技术的第二方面提供了一种电子装置,其包含本技术的第一方面的任一种实施方案所述的电化学装置。
14.本技术的有益效果:本技术提供了一种电化学装置和电子装置,其中,电化学装置包含电极组件、外包
装和双面胶,所述双面胶设于所述电极组件和所述外包装之间;所述双面胶包含粘结层、复合层、热熔层,所述复合层设于所述粘结层和所述热熔层之间,所述复合层的抗拉强度≥500mpa,断裂伸长率≥15%。通过将双面胶设于电极组件和外包装之间,使双面胶将电极组件和外包装粘接固定,从而使电极组件、双面胶和外包装形成一个整体,减少跌落过程中电极组件与外包装之间的晃动。进一步地,通过将双面胶设计为粘结层、复合层、热熔层的三层结构,并调控位于双面胶中间的复合层的抗拉强度≥500mpa,断裂伸长率≥15%,以使双面胶中复合层的机械强度得到提高,进而提高双面胶的机械强度。这样,双面胶对电极组件最外层的保护加强,能够降低电极组件在跌落或钝性力冲击下受到破损的风险,提高电极组件的钝刺承受极限力,以使电极组件的抗变形、抗跌落以及抗钝刺能力均得以提高,从而提升电化学装置的安全性能。
15.当然,实施本技术的任一产品或方法并不一定需要同时达到以上所述的所有优点。
附图说明
16.为了更清楚地说明本技术和现有技术中的技术方案,下面将对实施例和现有技术描述中所需要使用的附图作简单地介绍,显而易见地,下面描述中的附图仅仅是本技术的一些实施例,对于本领域普通技术人员来讲,还可以根据这些附图获得其他的实施例。
17.图1为本技术一种实施方案的双面胶结构示意图;图2为图1的双面胶的右视图;图3为图2的双面胶的俯视图;图4为本技术一种实施方案的双面胶粘接于电极组件外表面的示意图;图5为现有技术的双面胶结构示意图。
18.附图标记说明:1-双面胶;11-粘结层;12-复合层;13-热熔层;14-基材层;15-绝缘层;16-不涂胶区域;2-离型纸;3-电极组件;31-正极极耳;32-负极极耳。
具体实施方式
19.为使本技术的目的、技术方案及优点更加清楚明白,以下参照附图和实施例,对本技术进一步详细说明。显然,所描述的实施例仅仅是本技术一部分实施例,而不是全部的实施例。基于本技术中的实施例,本领域普通技术人员所获得的所有其他技术方案,都属于本技术保护的范围。
20.需要说明的是,本技术的具体实施方式中,以锂离子电池作为电化学装置的例子来解释本技术,但是本技术的电化学装置并不仅限于锂离子电池。
21.本技术的第一方面提供了一种电化学装置,其包含电极组件、外包装和双面胶,所述双面胶设于所述电极组件和所述外包装之间;所述双面胶包含粘结层、复合层、热熔层,所述复合层设于所述粘结层和所述热熔层之间,所述复合层的抗拉强度≥500mpa,断裂伸长率≥15%。
22.发明人发现,通过将双面胶设于电极组件和外包装之间,使双面胶将电极组件和外包装粘接固定,从而使电极组件、双面胶和外包装形成一个整体,减少跌落过程中电极组
件与外包装之间的晃动。发明人还发现,通过将双面胶设计为粘结层、复合层、热熔层的三层结构,将所述复合层设于所述粘结层和所述热熔层之间,并调控位于双面胶中间的复合层的抗拉强度≥500mpa,断裂伸长率≥15%,以使双面胶中复合层的机械强度得到提高,进而提高双面胶的机械强度。这样,双面胶对电极组件最外层的保护加强,能够降低电极组件在跌落或钝性力冲击下受到破损的风险,提高电极组件的钝刺承受极限力,以使电极组件的抗变形、抗跌落以及抗钝刺能力均得以提高,从而提升电化学装置的安全性能。
23.例如,复合层的抗拉强度可以是500mpa、600mpa、700mpa、800mpa、1000mpa或为其间的任意范围,又或为其以上范围;复合层的断裂伸长率可以是15%、16%、17%、18%、19%、20%或为其间的任意范围,又或为其以上范围。当复合层的抗拉强度过小时,例如,复合层的抗拉强度《500mpa,即复合层的抗拉强度不够,保护电极组件在跌落或钝性力冲击下不受破损的能力较弱。当复合层的断裂伸长率过小时,例如,复合层的断裂伸长率《15%,复合层较脆,在跌落或钝性力冲击下,双面胶的复合层容易脆断,使电极组件在外力冲击下容易发生破损,引发短路问题,进而影响电化学装置的安全性能。
24.在本技术的一种实施方案中,所述复合层包含基材层和分别位于所述基材层两个表面上的绝缘层,所述基材层的材料包含金属复合材料;所述绝缘层的材料包含聚酰胺、聚丙烯、聚乙烯或聚对苯二甲酸乙二酯中的至少一种。上述聚酰胺为本领域技术人员熟知的尼龙材料。通过将双面胶中间的复合层设计为包含基材层和分别位于所述基材层两个表面上的绝缘层这样的结构,并选用金属复合材料为基材层,可以提高双面胶中复合层的机械强度,增强对电极组件最外层的保护能力。绝缘层设置于基材层的两个表面,可以有效防止基材层裸露,或与电极组件表面的正/负极集流体接触而形成短路,从而提升电化学装置的安全性能。通过选用上述材料为绝缘层,可以有效防止基材层与电极组件表面的正/负极集流体接触而形成短路,从而提升电化学装置的安全性能。
25.在本技术的一种实施方案中,所述金属复合材料包含不锈钢、铝合金、钛合金、镁合金或镍合金中的至少一种。通过选用上述金属复合材料为基材层,有利于提高双面胶中复合层的机械强度,例如抗拉强度和断裂伸长率,对电极组件最外层铝箔形成加强保护,从而提升电化学装置的安全性能。
26.在本技术的一种实施方案中,所述复合层的厚度为10
µ
m至30
µ
m,所述基材层的厚度为5
µ
m至20
µ
m,所述绝缘层的厚度为2
µ
m至10
µ
m。在本技术中,所述复合层的厚度为d1,所述基材层的厚度为d
1-1
,所述绝缘层的厚度为d
1-2
。复合层的厚度为基材层与两个绝缘层的厚度之和。通过调控复合层的厚度d1、基材层的厚度d
1-1
和绝缘层的厚度d
1-2
在上述各自的范围内,有利于提高双面胶中复合层的机械强度,增强双面胶对电极组件最外层的保护能力,以及提升绝缘层防止基材层与电极组件表面的正/负极集流体接触而形成短路的能力,从而提升电化学装置的安全性能。
27.例如,所述复合层的厚度d1可以是10
µ
m、15
µ
m、20
µ
m、25
µ
m、30
µ
m或为其间的任意范围,其中,所述基材层的厚度为d
1-1
可以是5
µ
m、10
µ
m、15
µ
m、20
µ
m或为其间的任意范围,所述绝缘层的厚度d
1-2
可以是2
µ
m、5
µ
m、7
µ
m、10
µ
m或为其间的任意范围。当d
1-1
过小时,例如,d
1-1
《5
µ
m,即基材层的厚度过小时,基材层的机械强度降低,如抗拉强度和断裂伸长率降低,电极组件在跌落或钝性力冲击下受到破损的可能性增大。而当d
1-2
过小时,例如,d
1-2
《2
µ
m,即绝缘层的厚度过小时,基材层容易裸露,裸露的基材层将与电极组件表面的正极集流体或负
极集流体接触形成短路。并且,当d
1-1
过大时,保持复合层的厚度d1在上述范围内,则d
1-2
容易过小,例如,d
1-1
》27
µ
m,且d1=30
µ
m,则d
1-2
《2
µ
m;则绝缘层的厚度过小,基材层容易裸露,与电极组件表面的正/负极集流体接触而形成短路。而当d
1-2
过大时,保持复合层厚度d1在上述范围内,则d
1-1
容易过小,例如, d
1-2
》13
µ
m,且d1=30
µ
m,则d
1-1
《5
µ
m,也导致了基材层的厚度过小,基材层机械强度低。当复合层的厚度d1过小时,例如,d1《10
µ
m,则说明复合层的基材层厚度d
1-1
或绝缘层厚度d
1-2
较小,同样容易出现上述问题;当复合层的厚度d1过大时,例如,d1》30
µ
m,可能导致双面胶的总厚度过大,使电化学装置的体积增大,从而降低电化学装置的能量密度。
28.在本技术的一种实施方案中,所述双面胶的总厚度为20
µ
m至50
µ
m,所述粘结层的厚度为5
µ
m至15
µ
m,所述热熔层的厚度为5
µ
m至15
µ
m。在本技术中,所述双面胶的总厚度为d,所述粘结层的厚度为d2,所述热熔层的厚度为d3。所述双面胶的总厚度为复合层、粘结层和热熔层的厚度之和。通过调控双面胶的总厚度、粘结层的厚度以及热熔层的厚度在上述各自的范围内,有利于提升电化学装置的安全性能。
29.例如,所述双面胶的总厚度d可以是20
µ
m、30
µ
m、40
µ
m、50
µ
m或为其间的任意范围,其中,所述粘结层的厚度d2可以是5
µ
m、10
µ
m、15
µ
m或为其间的任意范围,所述热熔层的厚度d3可以是5
µ
m、10
µ
m、15
µ
m或为其间的任意范围。当粘结层的厚度d2过小时,例如,d2《5
µ
m,粘结层的厚度过小,可能导致粘结力度不够,电极组件与外包装之间固定不牢。而当热熔层的厚度d3过小时,例如,d3《5
µ
m,热熔层的厚度过小,同样可能导致粘结力度不够,从而容易导致电极组件破损以及由此引发的短路问题。而当双面胶的总厚度d过小时,例如,d《20
µ
m,双面胶可能不足以完全填充电极组件与外包装之间的空间,从而导致电极组件与外包装之间固定不牢。当双面胶的总厚度d过大,即粘结层的厚度d2和/或热熔层的厚度d3过大时,例如,d》50
µ
m,双面胶的总厚度过大,使电化学装置的体积增大,从而降低电化学装置的能量密度。
30.在本技术的一种实施方案中,所述粘结层的材料包含聚甲基丙烯酸甲酯、苯乙烯-异戊二烯-苯乙烯嵌段共聚物、聚乙烯、聚丙烯或聚酰胺中的至少一种;所述粘结层与所述电极组件的外表面粘接,粘结力为0.1n/mm至1.0n/mm。上述聚甲基丙烯酸甲酯为本领域技术人员熟知的亚克力材料,上述苯乙烯-异戊二烯-苯乙烯嵌段共聚物为本领域技术人员熟知的sis橡胶材料,上述聚酰胺为本领域技术人员熟知的尼龙材料。通过选用上述材料为双面胶的粘结层,与电极组件的外表面粘接,并调控其粘结力在上述范围内,有利于提升电化学装置的安全性能。
31.例如,所述粘结层与所述电极组件的外表面粘接,其粘结力可以为0.1n/mm、0.3n/mm、0.5n/mm、0.7n/mm、1.0n/mm或为其间的任意范围。当粘结层的粘结力过小时,例如,粘结层的粘结力《0.1n/mm,粘结层与电极组件的外表面之间的粘结力度不够,造成电极组件与外包装之间固定不牢,跌落时电极组件容易在外包装内晃动,造成电极组件破损,并引发的短路问题。当粘结层的粘结力过大时,例如,粘结层的粘结力》1.0n/mm,跌落剪切作用易引起铝箔撕裂,造成电极组件与外包装之间固定失效,导致电极组件容在外包装内晃动,造成电极组件破损,并引发短路的问题。
32.在本技术的一种实施方案中,所述热熔层的材料包含聚甲基丙烯酸甲酯、苯乙烯-异戊二烯-苯乙烯嵌段共聚物、聚乙烯、聚丙烯或聚酰胺中的至少一种;所述热熔层与所述
外包装的内表面粘接,粘结力为0.1n/mm至1.0n/mm。上述聚甲基丙烯酸甲酯为本领域技术人员熟知的亚克力材料,上述苯乙烯-异戊二烯-苯乙烯嵌段共聚物为本领域技术人员熟知的sis橡胶材料,上述聚酰胺为本领域技术人员熟知的尼龙材料。通过选用上述材料为双面胶的热熔层,并调控热熔层与外包装的内表面粘接的粘结力在上述范围内,有利于提升电化学装置的安全性能。
33.例如,所述热熔层与所述外包装的内表面粘接,其粘结力可以为0.1n/mm、0.3n/mm、0.5n/mm、0.7n/mm、1.0n/mm或为其间的任意范围。当热熔层的粘结力过小时,例如,热熔层的粘结力为《0.1n/mm,热熔层与外包装的内表面之间的粘结力度不够,造成电极组件与外包装之间固定不牢,跌落时电极组件容易在外包装内晃动,造成电极组件破损,并引发的短路问题。当热熔层的粘结力过大时,例如,热熔层的粘结力为》1.0n/mm,跌落剪切作用易引起铝箔撕裂,造成电极组件与外包装之间固定失效,导致电极组件容在外包装内晃动,造成电极组件破损,并引发短路的问题。
34.图1示出了本技术一种实施方案的双面胶的示意图。可以看到,双面胶1可以成卷绕状存储,通过离型纸2避免卷绕时双面胶1粘接在一起。图2为图1的右视图。可以看到,双面胶1包括粘结层11、复合层12以及热熔层13,复合层12设于粘结层11与热熔层13之间。复合层12包含基材层14和分别位于基材层14两个表面上的绝缘层15。
35.在本技术的一种实施方案中,靠近所述热熔层一侧的所述复合层的表面上包含两个等宽度的不涂胶区域,所述热熔层与所述不涂胶区域的宽度之和等于所述复合层的宽度,所述不涂胶区域的宽度占复合层宽度的10%至40%。
36.在本技术中,如图2所示,双面胶1中靠近粘结层11的一侧的复合层12表面(也即绝缘层15表面)被粘结层11完全覆盖,则粘结层11的宽度等于复合层12的宽度。而靠近热熔层13一侧的复合层12的表面上只有远离复合层12边缘的中间区域被热熔层13覆盖,靠近复合层12边缘的两边区域因未被热熔层13覆盖而裸露,称为不涂胶区域16。
37.图3为图2所示双面胶的俯视图。从图3可以看到,构成任一个不涂胶区域16的两个边缘,其一为复合层12的一侧边缘,另一是热熔层13中靠近前述复合层12边缘的一侧边缘,则任一个不涂胶区域16的宽度,为构成此不涂胶区域16的热熔层13的边缘与复合层12的边缘之间的距离。热熔层13与两个不涂胶区域16的宽度之和等于复合层12的宽度。
38.在本技术中,不涂胶区域的宽度占复合层宽度的比例为x(%),简称为不涂胶比例,x(%)。需要说明,上述“不涂胶区域的宽度占复合层宽度的比例为x(%)”中的“不涂胶区域的宽度”是指,复合层的表面上的两个等宽度的不涂胶区域的宽度之和。
39.例如,不涂胶区域的宽度占复合层宽度的比例x可以为10%、20%、30%、40%或为其间的任意范围。当x过小时,例如,x《10%,不涂胶区域的宽度过小,电极组件在跌落触地瞬间无法有效缓解受到的冲击力度,难以有效保护电极组件,从而影响电化学装置的安全性能。当x过大时,例如,x》40%,热熔层的宽度过小,电极组件和外包装之间粘接固定效果较差,将影响电化学装置的安全性能。通过设计靠近所述热熔层一侧的所述复合层的表面上包含两个等宽度的不涂胶区域,并调控不涂胶区域的宽度占复合层宽度的比例x(%)在上述范围内,可以使双面胶将电极组件和外包装粘接固定,减少跌落过程中电极组件与外包装之间的晃动,并且,可以有效缓解在电极组件在跌落触地瞬间受到的冲击力度,从而改善电化学装置的跌落通过率。
40.在本技术的一种实施方案中,所述双面胶粘接于所述电极组件外表面的面积与所述电极组件的外表面总面积的比例为30%至90%。
41.在本技术中,所述双面胶粘接于所述电极组件外表面的面积与所述电极组件的外表面总面积的比例为y(%),简称为粘结比例,y(%)。图4示出了本技术一种实施方案的双面胶粘接于电极组件的外表面的示意图。参见图3和图4,可以看到,双面胶1贴在电极组件3的外表面上,电极组件3还包括正极极耳31和负极极耳32。由于双面胶1的粘结层与电极组件3的外表面粘接,而热熔层13和不涂胶区16的复合层12表面裸露出来,经热压,热熔层13形成粘结力后,可与外包装(未图示)内表面粘接,从而将电极组件3与外包装粘接固定,形成一个整体。在本技术中,所述电极组件外表面的面积还包含从电极组件内引出的极耳的外表面面积。
42.例如,粘结比例y可以为30%、40%、50%、60%、70%、80%、90%或为其间的任意范围。当y过小时,例如,y《30%,双面胶粘接于电极组件外表面的面积比例过小,一方面,将电极组件和外包装之间粘接固定效果较差,跌落过程中电极组件容易在外包装内部晃动;另一方面,粘接面积过小,胶纸无法有效覆盖极耳位置,极耳容易被钝刺刺穿,同时极耳上裸露的毛刺也容易刺破隔膜,从而导致电极组件破损,引发短路问题,影响电化学装置的安全性能。当y过大时,例如,y》90%,双面胶粘接于电极组件外表面的面积与电极组件的外表面总面积的比例过大,即粘结比例过大,胶纸边缘离电极组件边缘太近,易造成铝箔撕裂。通过将所述双面胶粘接于所述电极组件外表面的面积与所述电极组件的外表面总面积的比例y,当粘结比例y调控到上述范围时,不仅使电极组件与外包装粘接固定良好,改善电极组件的抗跌落和抗钝刺能力,还改善了电化学装置的极耳区域的抗钝刺能力,从而避免了电化学装置的内部缺陷和短路,能够进一步提升电化学装置的安全性能。
43.在本技术中,所述粘结层与所述电极组件外表面的粘接方式,没有特别限制,只要能够实现本技术目的即可。例如,常温下粘结层即可与所述电极组件的外表面粘接。
44.在本技术中,所述热熔层与所述外包装内表面的粘接方式,没有特别限制,只要能够实现本技术目的即可。例如,热熔层经热压后形成粘结力,与所述外包装粘接,热压的条件没有特别限制,只要能够实现本技术目的即可。例如,热压的条件为温度≥65℃,压力≥0.5mpa,时间≥20min。
45.本技术对不锈钢没有特别限制,只要能够实现本技术目的即可,例如,不锈钢选自铁素体型不锈钢、马氏体型不锈钢、奥氏体型不锈钢、奥氏体-铁素体型不锈钢或沉淀硬化型不锈钢。其中,奥氏体型不锈钢可以选自牌号为201、202、301、304、316、309或321的不锈钢材料。
46.本技术对铝合金没有特别限制,只要能够实现本技术目的即可,例如,铝合金可以选自牌号为7a04、2a02或2a12的铝合金材料。
47.本技术对钛合金没有特别限制,只要能够实现本技术目的即可,例如,钛合金可以选自牌号为ta5、ta7、ta9、ta16、tb2、tb5、tc4、tc6、tc11、tc16、tc17、tc18或tc19的钛合金材料。
48.本技术对镍合金没有特别限制,只要能够实现本技术目的即可,例如,镍合金可以选自牌号为ns322、ns336、ns8096、ns341、ns441或gh3625的镍合金材料。
49.本技术对聚酰胺(pa),即尼龙材料没有特别限制,只要能够实现本技术目的即可,
例如,尼龙材料可以选自尼龙1010、尼龙6、尼龙66、尼龙610、尼龙11、尼龙12、尼龙46或尼龙7材料。又例如,尼龙6可以选自牌号为8202c、8233g、b33l、bl1320、bl1340、bl2280、bl2750或bl3350的尼龙6材料。尼龙66可以选自牌号为nb6630g、nb6615g、fr6630gv0、cv-15、epr27、2730g、2700f或2130g的尼龙66材料。
50.本技术对聚乙烯(pe)没有特别限制,只要能够实现本技术目的即可,例如,聚乙烯材料可以选自高密度聚乙烯(hdpe),高密度聚乙烯(hdpe)可以选自牌号为5200b、2200j、5000s、6070、2911、2908、5000s、5070、5502或tr144的高密度聚乙烯材料。
51.本技术对聚丙烯(pp)没有特别限制,只要能够实现本技术目的即可,例如,聚丙烯(pp)可以选自均聚聚丙烯、无规共聚聚丙烯或嵌段共聚聚丙烯。其中,均聚聚丙烯为由单一的丙烯单体聚合而成的聚丙烯,均聚聚丙烯可以选自牌号为ypf-3008、f800e或c1007的均聚聚丙烯材料。无规共聚聚丙烯可以选自单体乙烯含量为1%-5%的丙烯-乙烯共聚物。嵌段共聚聚丙烯可以选自单体乙烯含量为5%-20%的丙烯-乙烯嵌段共聚物。
52.本技术对聚对苯二甲酸乙二酯(pet)没有特别限制,只要能够实现本技术目的即可,例如,聚对苯二甲酸乙二酯(pet)的分子量可以为20000至30000。
53.本技术对聚甲基丙烯酸甲酯,即亚克力没有特别限制,只要能够实现本技术目的即可,例如,亚克力的分子量可以为50000至160000。
54.本技术对苯乙烯-异戊二烯-苯乙烯嵌段共聚物,即sis橡胶没有特别限制,只要能够实现本技术目的即可,例如,sis橡胶可以选自牌号为1105、1106、1124、1126或1209的sis橡胶材料。
55.本技术对双面胶的制备方法没有特别限制,只要能够实现本技术目的即可。例如,可以采用以下制备方法制备本技术的双面胶:采用热复合的方式,将基材层的两个表面分别与两个相同的绝缘层复合在一起,得到如图1至图2所示的复合层;然后将选用本技术的粘结层材料分散于有机溶剂中,得到粘结层胶水,将制备的粘结层胶水涂覆于复合层的一个表面上,高温烘干,在复合层的该表面上形成粘结层,其中,所述有机溶剂选自甲苯/二甲苯;再将选用本技术的热熔层材料分散于有机溶剂中,得到热熔层胶水,将热熔层胶水只涂覆于复合层的另一个表面的涂胶区域(即除不涂胶区域以外的区域)上,如图3所示的不涂胶区域不涂覆热熔层胶水,高温烘干,在复合层的另一表面形成热熔层,制备得到如图1至图3所示的双面胶,其中,所述有机溶剂选自甲苯/二甲苯;最后将制备的双面胶的粘结层或热熔层面附于离型纸或离型膜上收卷,形成如图1所示的双面胶带。
56.在本技术中,所述电极组件还包括正极极片、负极极片、隔离膜,隔离膜位于正极极片和负极极片之间,用以分隔正极极片和负极极片,防止电化学装置内部短路,允许电解液离子自由通过,完成电化学充放电过程的作用。本技术对正极极片、负极极片和隔离膜没有特别限制,只要能够实现本技术目的即可。
57.在本技术中,所述外包装没有特别限制,只要能够实现本技术目的即可。例如,外包装可以包括铝塑膜、铝壳、钢壳或塑料壳中的至少一种。所述外包装的形状可以包括方形或圆柱形中的至少一种。
58.在本技术中,所述电化学装置的制备过程为本领域技术人员所熟知的,本技术没有特别的限制。例如,可以包括但不限于以下步骤:将正极极片、隔离膜和负极极片按顺序
堆叠,并根据需要将其卷绕得到卷绕结构的电极组件;在电极组件的外表面贴上本技术的双面胶;再将粘接有双面胶的电极组件放入外包装内,热压,使双面胶的热熔层形成粘结力与外包装粘接,电极组件与外包装粘接固定,使电极组件、双面胶和外包装形成一个整体;最后将电解液注入外包装并封口,得到电化学装置。或者,将正极极片、隔离膜和负极极片按顺序堆叠,然后用胶带将整个叠片结构的四个角固定好得到叠片结构的电极组件;在电极组件的外表面贴上本技术的双面胶;将粘接有双面胶的电极组件置入外包装内,热压,使热熔层形成粘结力,将双面胶与外包装粘接,电极组件与外包装粘接固定,使电极组件、双面胶和外包装形成一个整体;最后将电解液注入外包装内并封口,得到电化学装置。此外,也可以根据需要将防过电流元件、导板等置于外包装中,从而防止电化学装置内部的压力上升、过充放电。
59.本技术的电化学装置没有特别限制,其可以包括发生电化学反应的任何装置。在一些实施方案中,电化学装置可以包括但不限于:锂金属二次电池、锂离子电池(锂离子二次电池)、锂聚合物二次电池或锂离子聚合物二次电池等。
60.本技术的第二方面提供了一种电子装置,其包含本技术的第一方面的任一种实施方案所述的电化学装置。因此,该电子装置具有良好的安全性能。
61.本技术的电子装置没有特别限定,其可以是用于现有技术中已知的任何电子装置。在一些实施例中,电子装置可以包括,但不限于,笔记本电脑、笔输入型计算机、移动电脑、电子书播放器、便携式电话、便携式传真机、便携式复印机、便携式打印机、头戴式立体声耳机、录像机、液晶电视、手提式清洁器、便携cd机、迷你光盘、收发机、电子记事本、计算器、存储卡、便携式录音机、收音机、备用电源、电机、汽车、摩托车、助力自行车、自行车、照明器具、玩具、游戏机、钟表、电动工具、闪光灯、照相机、家庭用大型蓄电池和锂离子电容器等。
实施例
62.以下,举出实施例及对比例来对本技术的实施方式进行更具体地说明。各种的试验及评价按照下述的方法进行。
63.测试方法和设备:抗拉强度和断裂伸长率的测试参考astm d897-08: standard test method for tensile properties of adhesive bonds标准,采用胶黏剂拉伸剪切试验机,对实施例中的双面胶进行抗拉强度和断裂伸长率的测试。测试方法如下:取200mm长,宽度为10mm(小于10mm取原宽幅)的双面胶(边缘应光滑无缺口)作为测试样品,在测试样品的两端贴上50mm长、20mm宽的纸、胶带或其他材料作为标记物,标记物的边缘作为标线,测量此时两条平行的标线间距离,得到初始标线间距离为100mm。在环境温度25
±
2℃,相对湿度50-80%的测试环境下,将制得的测试样品平整地置于夹持器中,并使夹持器恰好夹持在上述两条平行的标线上,则夹持距离与初始标线间距离相同,为100mm。适当拧紧夹持器,以防止测试样品在拉伸过程中打滑或断裂在夹持器处。保持测试样品的受力方向与胶黏剂拉伸剪切试验机施力方向一致,以300mm /min的速度对测试样品进行加载,使测试样品拉伸至断裂,记录拉伸过程中的载荷-位移曲线,输出位移曲线和数
据。然后测量断裂后上述两条平行的标线间距离,得到断裂时标线间距离。进行3次平行测试实验,最后取平均值作为该项测试的结果。
64.其中,抗拉强度和断裂伸长率的计算公式如下:抗拉强度=最大载荷/测试样品的宽度;断裂伸长率=断裂时标线间距离/初始标线间距离-1。
65.粘结力测试参照180
º
剥离力测试过程,采用胶黏剂拉伸剪切试验机,对双面胶的粘结层与电极组件外表面之间的粘结力,以及双面胶的热熔层与外包装内表面之间的粘结力进行测试,测试方法如下:取200mm长,宽度为20mm(小于20mm取原宽幅)的双面胶(边缘应光滑无缺口),常温下将所取的双面胶的粘结层与铝(al)箔粘接,然后,在所取的双面胶的热熔层侧盖上铝塑膜外包装,热压激活使热熔层与铝塑膜外包装形成粘接;最后将上述双面胶在85℃的电解液中浸泡4h,取出,并用无尘纸擦掉试样表面的电解液,制备得到测试样品。
66.在环境温度25
±
2℃,相对湿度50-80%的测试环境下,将制备的测试样品的铝箔面用3m双面胶贴于钢板上,人为从测试样品的粘结层与铝箔之间,或者热熔层与铝塑膜外包装之间剥开,以露出测试粘结层或热熔层的粘结力的粘结界面。将钢板平整地置于其中一个夹持器中,然后将测试样品的粘结界面上离开钢板的一端翻转180
º
后,用专用延伸胶带将此端粘接于另一个夹持器上,保持测试样品的粘结界面上离开钢板的一端与固定在钢板的一端的两端面间的夹角为180
º
;再适当拧紧两个夹持器,以防止测试样品在测试过程中打滑。保持钢板上的测试样品的受力方向与试验机施力方向一致,使测试样品的粘结界面上离开钢板的一端以180
º
与固定在钢板的一端慢慢完全剥离,记录上述180
º
剥离过程中的载荷-位移曲线,输出位移曲线和数据。进行3次平行测试实验,最后取平均值作为该项测试的结果。
67.其中,粘结力的计算公式为:粘结力=平均拉力/测试样品的宽度。
68.跌落测试跌落测试,又称drop测试。将锂离子电池从1.5m处的高度自由跌落,以自由跌落后呈立方体型的锂离子电池的六个平面和四个顶角均触地一次,作为一轮drop实验。一个锂离子电池至多经过6轮drop实验。若在6轮drop实验中锂离子电池均未出现爆炸或起火现象,并且,6轮drop实验后,若锂离子电池的电压降<50mv,则该锂离子电池通过drop测试。其中,电压降通过用万能电压表置于锂离子电池的极耳处分别读取在drop测试前后的电压值测得的。
69.其中,电压降、drop通过率的计算公式为:电压降=drop测试前的电压值-drop测试后的电压值;drop通过率=通过drop测试后的电池数量/测试的电池数量。
70.铝箔撕裂率测试按照上述drop测试的方法,进行6轮drop实验后,拆解锂离子电池,计量drop测试后锂离子电池中正极铝箔撕裂的电池数量,其中,铝箔撕裂率的计算公式为:
铝箔撕裂率=drop测试后的铝箔撕裂的电池数量/测试的电池数量。
71.钝刺测试钝刺测试,又称dent测试。用直径为6mm平头钉,分别作用在锂离子电池的六个平面的面中心位置和1个正极极耳和1个负极极耳处,均以300n/min速度逐渐增加压力,直至锂离子电池的六个平面的面中心位置和1个正极极耳和1个负极极耳处均被钉穿一次,作为一轮dent实验。每次击穿瞬间的作用力即为该次的dent极限力。若锂离子电池上述一轮dent实验中不爆炸,不起火,并且每次dent极限力>1500n,则该锂离子电池通过dent测试。
72.其中,dent通过率的计算公式为:dent通过率=通过dent测试的电池数量/测试的电池数量。
73.实施例1《双面胶的制备》将材料为铝合金,厚度d
1-1
为11μm的基材层与材料为聚乙烯,厚度为d
1-2
为2μm的两个绝缘层在130-140℃下进行热复合,得到复合层;然后将粘结层材料亚克力分散于甲苯溶剂中,得到固含量为10-20%的粘结层胶水,将制备的粘结层胶水涂覆于复合层的一个表面上,120℃下高温烘干5-10min,在复合层的该表面上形成厚度为5μm的粘结层;再将热熔层材料亚克力分散于甲苯溶剂中,得到固含量为10-20 %的热熔层胶水,将热熔层胶水涂覆于复合层的另一个表面的涂胶区域上(即除如图3所示的不涂胶区域16以外的区域),120℃下高温烘干5-10min,在复合层的另一表面形成厚度为5μm的热熔层,制备得到如图1至图3所示的双面胶,其中,双面胶的总厚度d为25μm,不涂胶比例x为12%。最后将制备的双面胶的粘结层或热熔层附于离型纸或离型膜上收卷,形成如图1所示的双面胶带。
74.《锂离子电池的制备》常温下将上述制备得到的双面胶的粘结层粘接在型号为456587(生产厂商:宁德新能源科技有限公司(atl))的锂离子电池的电极组件外表面,其中,电极组件外表面为制备电极组件时作为最外层的正极集流体铝箔的外表面,得到图4所示的贴有双面胶1的电极组件3。然后将贴有双面胶的电极组件放入铝塑膜外包装内,在温度75℃,压力0.5mpa下热压20min,使双面胶的热熔层形成粘结力,与铝塑膜外包装的内表面粘接。其中,粘结比例y为45%。干燥后注入电解液,经过真空封装、静置、化成、脱气、切边等工序得到厚/宽/高分别为5.2mm、63mm、76mm的锂离子电池。其中,化成条件是以0.02c恒流充电到3.3v,再以0.1c恒流充电到4.3v。
75.实施例2至实施例9除了各制备参数和性能参数如表1和表2所示以外,其余与实施例1相同。
76.实施例10至实施例19除了各制备参数和性能参数如表3和表4所示以外,其余与实施例1相同。
77.实施例20至实施例29除了各制备参数和性能参数如表5和表6所示以外,其余与实施例1相同。
78.实施例30至实施例39除了各制备参数和性能参数如表7和表8所示以外,其余与实施例1相同。
79.对比例1至对比例4除了各制备参数和性能参数如表1和表2所示以外,其余与实施例1相同。
80.实施例1的双面胶结构如图1至图3所示,双面胶1包含粘结层11、热熔层13以及设于粘结层11和热熔层13之间的复合层12。复合层12包含基材层14和分别位于基材层14两个表面上的绝缘层15。双面胶1中靠近热熔层13一侧的复合层12的表面上包含两个等宽度的不涂胶区域16。
81.对比例1的双面胶结构如图5所示。可以看到,对比例1 的双面胶只包含粘结层11、基材层14和热熔层13,而不含绝缘层和不涂胶区域。
82.各实施例和对比例的制备参数及性能参数如表1至表8所示。
83.表1注:表1中
ꢀ“‑”
表示不存在对应参数或物质。
84.表2
注:表2中
ꢀ“‑”
表示不存在对应参数或物质。
85.表3表4
ꢀ
表5表6
表7表8
从实施例1至实施例4,以及对比例1至对比例4可以看出,将双面胶设于电极组件和外包装之间,使电极组件和铝塑膜外包装粘接固定,从而使电极组件、双面胶和铝塑膜外包装形成一个整体,减少跌落过程中电极组件与外包装之间的晃动。进一步地,通过将双面胶设计为粘结层、复合层、热熔层的三层结构,复合层包括基材层和两层绝缘层,并调控位于双面胶中间的复合层的抗拉强度≥500mpa,断裂伸长率≥15%,可以提升电极组件抗跌落以及抗钝刺能力,锂离子电池的drop通过率和dent通过率更高,铝箔撕裂率更低,锂离子电池具有更好的安全性能。
86.并且,对比例1至对比例3中,基材层为聚对苯二甲酸乙二醇酯、聚酰亚胺或聚丙烯的低强度聚合物,对比例4 中,基材层材料容易脆断,其断裂伸长率仅有10%,而实施例1至实施例4中,基材层选用本技术范围内的金属复合材料,提供给双面胶较高的抗拉强度和断裂伸长率,能够增强对电极组件最外层的保护力度,从而使锂离子电池具有良好的安全性能。
87.从实施例5至实施例9可以看出,双面胶将电极组件和外包装粘接固定时,在双面胶中间的复合层的抗拉强度≥500mpa,断裂伸长率≥15%的基础上,调控复合层的厚度d1在本技术范围内的锂离子电池,具有较高的drop通过率和dent通过率、较低的铝箔撕裂率,锂离子电池具有良好的安全性能。
88.从实施例10至实施例14可以看出,双面胶将电极组件和外包装粘接固定时,在双面胶中间的复合层的抗拉强度≥500mpa,断裂伸长率≥15%的基础上,当粘结层选用本技术范围内的材料,双面胶与电极组件的外表面之间的粘结力为0.1n/mm至1.0n/mm时,电极组件与外包装之间粘接固定效果良好,锂离子电池具有较高的drop通过率和dent通过率、较低的铝箔撕裂率,锂离子电池具有良好的安全性能。
89.从实施例15至实施例19可以看出,双面胶将电极组件和外包装粘接固定时,在双面胶中间的复合层的抗拉强度≥500mpa,断裂伸长率≥15%的基础上,调控粘结层的厚度d2为5
µ
m至15
µ
m,双面胶与电极组件的外表面之间的粘结力为0.1n/mm至1.0n/mm时,电极组件
与外包装之间粘接固定效果良好,锂离子电池具有较高的drop通过率和dent通过率、较低的铝箔撕裂率,锂离子电池具有良好的安全性能。
90.从实施例20至实施例24可以看出,双面胶将电极组件和外包装粘接固定时,在双面胶中间的复合层的抗拉强度≥500mpa,断裂伸长率≥15%的基础上,当热熔层选用本技术范围内的材料,双面胶与铝塑膜外包装之间的粘结力为0.1n/mm至1.0n/mm时,电极组件与外包装之间粘接固定效果良好,锂离子电池具有较高的drop通过率和dent通过率、较低的铝箔撕裂率,锂离子电池具有良好的安全性能。
91.从实施例25至实施例29可以看出,在双面胶中间的复合层的抗拉强度≥500mpa,断裂伸长率≥15%的基础上,调控所述热熔层的厚度d3为5
µ
m至15
µ
m,双面胶与铝塑膜外包装之间的粘结力为0.1n/mm至1.0n/mm,电极组件与外包装之间粘接固定效果良好,锂离子电池具有较高的drop通过率和dent通过率、较低的铝箔撕裂率,锂离子电池具有良好的安全性能。
92.从实施例30至实施例34可以看出,在双面胶中间的复合层的抗拉强度≥500mpa,断裂伸长率≥15%的基础上,调控不涂胶区域的宽度占复合层宽度的比例,即不涂胶比例x为10%至40%时,锂离子电池具有较高的drop通过率和dent通过率、较低的铝箔撕裂率,锂离子电池具有良好的安全性能。
93.从实施例35至实施例39可以看出,在双面胶中间的复合层的抗拉强度≥500mpa,断裂伸长率≥15%的基础上,调控双面胶粘接于电极组件外表面的面积与电极组件的外表面总面积的比例,即粘结比例y调控在30%至90%,锂离子电池具有较高的drop通过率和dent通过率、较低的铝箔撕裂率,锂离子电池具有良好的安全性能。并且,粘结比例y从30%增加至90%时,锂离子电池的drop通过率明显增加,改善了锂离子电池的安全性能。
94.以上所述仅为本技术的较佳实施例,并非用于限定本技术保护范围。凡在本技术的精神和原则之内所作的任何修改、等同替换、改进等,均包含在本技术的保护范围内。
再多了解一些
本文用于企业家、创业者技术爱好者查询,结果仅供参考。