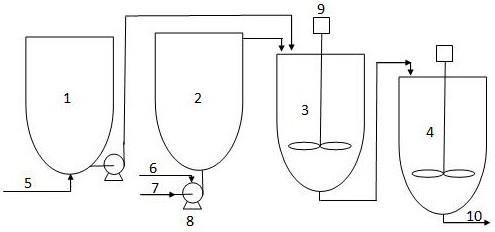
1.本发明涉及一种制备拟薄水铝石的方法,特别涉及一种连续制备拟薄水铝石的方法。
背景技术:
2.氧化铝有很多类型,如γ-al2o3、η-al2o3、θ-al2o3、δ-al2o3和α-al2o3等,其中γ-al2o3由于具有比表面积大、孔结构可调和热稳定性好的性质,在催化领域特别是催化加氢领域有着非常广泛的应用。制备γ-al2o3的通常方法是先制取拟薄水铝石,然后在一定温度下焙烧转化为γ-al2o3。拟薄水铝石在工业上一般有三种制备方法:(1)铝盐和碱的中和反应,如氯化铝法:alcl3 3nh4oh
→
al(oh)3 3nh4cl;(2)铝盐和铝酸盐的复分解反应,如硫酸铝法:al2(so4)3 6naalo2 12h2o
→
8al(oh)3 3na2so4。
3.(3)铝酸盐和酸的中和反应,如碳化法:2naalo2 co2 3h2o
→
2al(oh)3 na2co3;其中,氯化铝法在生产拟薄水铝石在过程中,操作环境差,且洗涤过程中洗涤水氨氮排放较高,满足不了目前环保要求;硫酸铝法生产的拟薄水铝石由于含有较高的硫酸根,在制成载体焙烧过程中,特别是高温焙烧过程中硫酸根分解成三氧化硫,对设备腐蚀也比较严重;碳化法制备拟薄水铝石过程绿色环保,且制备的拟薄水铝石无腐蚀性杂质。
4.cn101172631a公开了一种拟薄水铝石制备方法,该方法是将al2o3含量为70~130g/l、苛性比为1.3~1.6的偏铝酸钠稀释至al2o3含量为20~60g/l偏铝酸钠后,在温度15~45℃下能通入体积浓度为20~50%的二氧化碳进行碳化,碳化结束后再在80~100℃下老化制得拟薄水铝石。
5.cn106315642a公开了一种拟薄水铝石的制备方法和γ-氧化铝的制备方法,该方法是以浓度为5~40克/升的偏铝酸钠或铝酸钠溶液为原料,用二氧化碳含量大于30体积%的气体进行碳化,成胶过程的ph值控制在7~10,停留时间控制在2~60分钟,温度控制在30~95℃,成胶结束后在40~100℃温度下进行老化,时间为30~1000分钟,可以获得孔容在0.6毫升/克以上的γ-氧化铝。
6.以上碳化法得到的拟薄水铝石经焙烧后所得的氧化铝含有的酸性羟基的占比较低,且拟薄水铝石中三水铝石的质量含量较高,并且以上碳化法制备大孔拟薄水铝石需要采用氧化铝含量较低的偏铝酸钠原料,否则容易导致杂晶(比如丝钠铝石)的生成或是产品质量下降。并且,以上碳化法制备氧化铝均采用釜式、间歇生产,而所制备的氧化铝特别是制备大孔氧化铝时,外部环境对产品性质影响较大,这就导致了生产效率低、能耗大。
技术实现要素:
7.为克服现有技术中的缺点,本发明提供了一种连续制备拟薄水铝石的方法,采用
该方法制备拟薄水铝石的过程不受外部环境影响,其可实现连续生产;同时本发明的制备方法可采用较高氧化铝浓度的偏铝酸钠原料,生产效率大大提高,且该方法工艺简单、易操作。并且该方法制备得到的拟薄水铝石所含三水铝石的质量含量低,其经焙烧得到的氧化铝所含的酸性羟基占比高、具有适宜的大孔径和孔容,满足渣油加氢催化剂载体要求。
8.本发明提供了一种连续制备拟薄水铝石的方法,包括以下步骤:(1)分别配制低浓度含铝的碱性溶液和高浓度含铝的碱性溶液;(2)向第一反应釜中加入低浓度含铝的碱性溶液,通入含二氧化碳的混合气体i进行浅度碳化反应;(3)高浓度含铝的碱性溶液和含二氧化碳的混合气体ii混合后进入第二反应釜中,进行碳化反应,并控制第二反应釜内浆液的ph值;(4)当第二反应釜内浆液达到或高于其溢流口时,该浆液进入第三反应釜,同时并流加入步骤(2)得到的浆液进行反应,并控制第三反应釜内浆液的ph值;(5)当第三反应釜内浆液达到或高于其溢流口时,浆液进入老化罐,进行老化,老化结束后过滤,所得滤饼经洗涤、干燥,得到拟薄水铝石。
9.其中,步骤(1)中,所述含铝的碱性溶液为偏铝酸钠溶液或偏铝酸钾溶液中的一种或多种,优选偏铝酸钠溶液。
10.所述高浓度含铝的碱性溶液的苛性比为1.25~1.75,优选1.35~1.65;所述含高浓度含铝的碱性溶液的浓度以al2o3计为150~350gal2o3/l,优选160~250gal2o3/l。
11.所述低浓度含铝的碱性溶液的苛性比为1.15~1.35,优选1.25~1.35;所述低浓度含铝的碱性溶液的浓度以al2o3计为40~100gal2o3/l,优选50~80gal2o3/l。
12.步骤(2)中,所述向第一反应釜中加入的低浓度含铝的碱性溶液可以为反应釜体积的2/3~3/4。所述含二氧化碳的混合气体i可以为二氧化碳和空气的混合气体;所述含二氧化碳的混合气体i中二氧化碳所占体积分数为30%~60%。
13.步骤(2)中,所述浅度碳化为碳化后浆液ph值比碳化前溶液ph值下降0.5~1.5。
14.步骤(3)中,高浓度含铝的碱性溶液和含二氧化碳的混合气体ii的混合优选在气液混合泵中进行混合;所述气液混合泵为溶气泵、气水混合泵、混气泵、气液泵中的一种。
15.步骤(3)中,气液混合后由第二反应釜底部连续进入第二反应釜中。
16.步骤(3)中,所述含二氧化碳的气体ii可以为二氧化碳和空气的混合气体;所述含二氧化碳的混合气体ii中二氧化碳所占体积分数为50%~90%。
17.步骤(3)中,所述碳化反应为快速碳化反应,碳化反应的时间(即在第二反应釜内的停留时间)为1~5min;并控制第二反应釜内浆液的ph值为4.0~6.0。
18.步骤(3)中,所述碳化反应的初始反应温度一般为15~65℃,该反应为放热反应,体系温度逐渐升高,整个反应过程不需进行冷却保持低温,一般反应结束时浆液的温度为40~75℃。
19.步骤(4)中,所述第二反应釜内浆液进入第三反应釜前第三反应釜中加入底水,底水加入量为反应釜体积的1/10~1/5。
20.步骤(4)中,所述反应的温度为40℃~70℃,优选45℃~65℃。
21.步骤(4)中,所述反应在搅拌下进行。
22.步骤(4)中,通过调整步骤(2)浆液的流速控制反应釜内浆液ph值为8.5~9.5。
23.步骤(5)中,所述的老化罐优选为两个以上的老化罐并联,当一个老化罐收集好浆液后开始老化,浆液由另一个老化罐收集。
24.步骤(5)中,所述的老化的条件为:温度为50℃~95℃,时间为30min~120min。
25.步骤(5)中,所述的洗涤可采用本领域常规的洗涤方法,洗涤用水优选采用50℃~80℃的去离子水进行洗涤。
26.步骤(5)中,所述的干燥条件为:温度为100~150℃,时间为6~10小时。
27.本发明制备拟薄水铝石过程中,根据需要还可以加入助剂,如si、p、b或ti中的一种或几种,助剂的质量含量以氧化物计为所得拟薄水铝石的2%~6%。
28.本发明制备的拟薄水铝石中三水铝石含量小于1.5%,优选小于0.5%。
29.本发明制备的拟薄水铝石经焙烧,得到氧化铝,所得的氧化铝具有酸性羟基和碱性羟基,红外光谱中,所述酸性羟基峰在3670~3690cm-1
,所述碱性羟基峰在3770~3790cm-1
,所述酸性羟基峰与所述碱性羟基峰的峰面积比≥7.5。所述酸性羟基峰与所述碱性羟基峰的峰面积比优选为8.0:1~10.0:1。
30.所得氧化铝还具有如下性质:孔容为≥1.0ml/g,比表面积为280~340m2/g;孔分布如下:孔直径<6nm的孔的孔容占总孔容的≤5%,孔直径为6~15nm的孔的孔容占总孔容的65%~85%,孔直径>15nm的孔的孔容占总孔容的10%~25%。
31.所述焙烧的条件为:500~700℃焙烧3~6小时。
32.本发明另一方面提供了一种由上述方法制备的拟薄水铝石。
33.本发明另一方面提供了上述拟薄水铝石的应用。所述应用具体为制备渣油加氢催化剂,特别是制备渣油加氢脱硫催化剂。
34.本发明方法具有如下优点:(1)本发明高浓度含铝的碱性溶液优选先进入气液混合泵,同时气液混合泵的吸入口利用负压作用吸入含二氧化碳的混合气体ii,高速旋转的泵的叶轮将液体与气体混合、搅拌、加压,使气体与液体充分混合,制取高度溶解液,进入反应釜后压力迅速降低,并释放出混合气体进行快速碳化反应,即使在温度较高的情况下,可显著降低偏铝酸钠水解反应而减少三水氧化铝的生成,提高了合成拟薄水铝石的结晶度。
35.(2)本发明高浓度含铝的碱性溶液先与含二氧化碳的混合气体快速碳化反应并控制所得浆液的ph值,再与经浅度碳化的浆液进行反应,快速碳化生成的晶粒作为并流反应的晶核吸附浅度碳化生成的初级粒子,使得制备的拟薄水铝石晶粒大、且饱满、完整,形成较大的孔容和适宜的孔分布。
36.(3)本发明克服了传统拟薄水铝石制备过程中产品质量受环境影响及合成原料浓度低、生产效率低的缺点。
37.(4)本发明制备拟薄水铝石的方法,工艺简单、易操作,且该方法制备的拟薄水铝石经焙烧得到的氧化铝具有较大的孔容;另外,本发明的拟薄水铝石经焙烧所得的氧化铝所含的酸性羟基峰与所含的碱性羟基峰的峰面积比值大,即所含的酸性羟基占比更高,用于渣油加氢催化剂载体时具有更优异的催化性能。
附图说明
38.图1为本发明实施例连续制备拟薄水铝石的工艺流程图,其中,1为第一反应器,2
为第二反应器,3为第三反应器,4为老化罐,5为含二氧化碳的混合气体i入口,6为含二氧化碳的混合气体ii入口,7为高浓度含铝的碱性溶液入口,8为气液混合泵,9为搅拌器,10为老化后浆液出口;图2为实施例1、实施例2、实施例5、比较例1-3所得氧化铝的红外光谱图。
具体实施方式
39.下面结合实施例和附图对本发明的技术方案进行详细的说明。
40.本发明中,孔分布和比表面积是采用低温液氮吸附法分析;酸性羟基与碱性羟基采用采用美国nicolet 公司nicolet 870 型傅里叶变换红外光谱仪测定。对谱图波数3550~3850cm-1
部分进行分峰拟合,得到3670~3690cm-1
、3770~3790cm-1
处峰面积,再得到比值。
41.下面结合图1,对本发明具体的工艺流程说明如下:(1)分别配制低浓度含铝的碱性溶液和高浓度含铝的碱性溶液;(2)向第一反应釜1中加入反应釜体积2/3~3/4的低浓度含铝的碱性溶液,由入口5通入含二氧化碳的混合气体i,使碳化后浆液达到所需ph值;(3)高浓度含铝的碱性溶液通过入口7和含二氧化碳的混合气体ii通过入口6分别以一定的流速进入气液混合泵8,混合后由第二反应釜2底部连续进入第二反应釜2中,通过调整含二氧化碳混合气体ii流量使第二反应釜2内浆液的ph值快速降至所需ph值;(4)当第二反应釜2内浆液达到溢流口后,浆液由溢流口进入已加入底水、并加热至所需温度且已启动搅拌器9的第三反应釜3中,同时并流加入步骤(2)第一反应釜1中所得的浆液,通过调整步骤(2)浆液的流速控制第三反应釜3内浆液ph值;(5)当第三反应釜3内浆液达到或高于其溢流口时,浆液进入老化罐4进行浆液收集,收集好浆液的老化罐开始老化,浆液由另一个老化罐收集;老化结束后浆液老化后浆液出口流出,经过滤,所得滤饼经洗涤、干燥,得到本发明拟薄水铝石。
42.实施例1配制浓度以al2o3计为65gal2o3/l,苛性比为1.25的低浓度偏铝酸钠溶液和浓度以al2o3计浓度为165gal2o3/l,苛性比为1.40的高浓度偏铝酸钠溶液;向10.0l第一反应釜中加入温度为25℃的低浓度偏铝酸钠溶液7000ml,然后通入二氧化碳含量为40%(体积分数)的二氧化碳和空气混合气体,使低浓度偏铝酸钠溶液的ph值由13.8降至13.0。
43.温度为25℃的高浓度偏铝酸钠溶液以35ml/min的流速进入溶气泵,同时,向溶气泵中通入二氧化碳含量为75%(体积分数)的二氧化碳和空气混合气体,气、液经溶气泵混合后由第二反应釜底部连续进入第二反应釜中,控制碳化时间为3min,控制第二反应釜内浆液的ph值为5.5。
44.当第二反应釜内浆液达到溢流口后,浆液由溢流口进入已加底水1500ml、温度为60℃且已启动搅拌器的15l第三反应釜中,同时并流加入ph值降至13.0的低浓度偏铝酸钠溶液,通过调整ph值降至13.0的低浓度偏铝酸钠溶液的流速控制第三反应釜内浆液ph值为8.8,并保持第三反应釜内浆液温度60℃恒定。
45.当第三反应釜内浆液达到或高于溢流口时,浆液进入老化罐进行浆液收集,收集
好浆液的老化罐开始老化,浆液由另一个老化罐收集;老化温度为90℃,时间为90min。
46.老化结束后用75℃去离子水进行洗涤,洗涤结束后在120℃下干燥8小时。得到本发明拟薄水铝石a-1,其三水含量分析结果见表1。
47.将所得拟薄水铝石a-1再经600℃焙烧3小时,所得氧化铝a-1,其孔性质及红外光谱分峰拟合后酸性羟基与碱性羟基峰面积百分比见表1,红外光谱见图1。
48.实施例2其它同实施例1,只是高浓度偏铝酸钠溶液在第二反应釜进行碳化反应的初始温度为65℃,所用二氧化碳和空气的混合气体中二氧化碳占体积分数为65%,控制碳化时间为5mim,得到本发明拟薄水铝石a-2,其三水含量分析结果见表1。
49.将所得拟薄水铝石a-2再经600℃焙烧3小时,所得氧化铝a-2,其孔性质及红外光谱分峰拟合后酸性羟基与碱性羟基峰面积百分比见表1,红外光谱见图1。
50.实施例3其它同实施例1,只是低浓度偏铝酸钠溶液浓度改为55gal2o3/l,高浓度偏铝酸钠溶液浓度改为200gal2o3/l;老化结束后用60℃去离子水进行洗涤,得到本发明拟薄水铝石a-3,其三水含量分析结果见表1。
51.将所得拟薄水铝石a-3再经600℃焙烧3小时,所得氧化铝a-3,分析结果见表1。
52.实施例4其同实施例1,只是将高浓度偏铝酸钠浆液的流速改为40ml/min,高浓度偏铝酸钠溶液在第二反应釜进行碳化反应的初始温度为70℃;控制第三反应釜内浆液ph值为9.4,得到本发明拟薄水铝石a-4,其三水含量分析结果见表1。
53.将所得拟薄水铝石a-4再经600℃焙烧3小时,所得氧化铝a-4,分析结果见表1。
54.实施例5配制浓度以al2o3计为70gal2o3/l,苛性比为1.25的低深度偏铝酸钠溶液和浓度以al2o3计浓度为165gal2o3/l,苛性比为1.35的高浓度偏铝酸钠溶液;向10.0l第一反应釜中加入温度为25℃的低浓度偏铝酸钠溶液7000ml,然后通入二氧化碳含量为55%(体积分数)的二氧化碳和空气混合气体,使低浓度偏铝酸钠溶液的ph值由14.0降至12.7。
55.温度为25℃的高浓度偏铝酸钠溶液以35ml/min的流速进入溶气泵,同时,向溶气泵中通入二氧化碳含量为85%(体积分数)的二氧化碳和空气混合气体,气、液经溶气泵混合后由第二反应釜底部连续进入第二反应釜中,控制碳化时间为2min,控制第二反应釜内浆液的的ph值为4.5。
56.当第二反应釜内浆液达到溢流口后,浆液由溢流口进入已加底水1500ml、温度为70℃且已启动搅拌器的15l第三反应釜中,同时并流加入ph值降至12.7的低浓度偏铝酸钠溶液,通过调整ph值降至12.7的低浓度偏铝酸钠溶液的流速控制第三反应釜内浆液ph值为9.3,并保持第三反应釜内浆液温度70℃恒定。
57.当第三反应釜内浆液达到或高于溢流口时,浆液进入老化罐进行浆液收集,收集好浆液的老化罐开始老化,浆液由另一个老化罐收集;老化温度为90℃,时间为120min。
58.老化结束后用75℃去离子水进行洗涤,洗涤结束后在120℃下干燥8小时。得到本发明拟薄水铝石a-5,其三水含量分析结果见表1。
59.将所得拟薄水铝石a-5再经600℃焙烧3小时,所得氧化铝a-5,其孔性质及红外光谱分峰拟合后酸性羟基与碱性羟基峰面积百分比见表1,红外光谱见图1。
60.比较例1配制浓度以al2o3计为65gal2o3/l,苛性比为1.20的偏铝酸钠溶液;温度为25℃的偏铝酸钠溶液以35ml/min的流速连续由反应釜底部进入反应釜中,同时,由反应釜底部通入二氧化碳含量为75%(体积分数)的二氧化碳和空气混合气体,控制碳化时间为45min,控制体系的ph值为8.8。
61.当反应釜内浆液达到或高于溢流口时,浆液进入过滤、洗涤装置,用75℃去离子水进行洗涤,洗涤结束后在120℃下干燥8小时。得到拟薄水铝石f-1,其三水含量分析结果见表1。
62.将所得拟薄水铝石f-1再经600℃焙烧3小时,所得氧化铝f-1,其孔性质及红外光谱分峰拟合后酸性羟基与碱性羟基峰面积百分比见表1,红外光谱见图1。
63.比较例2配制浓度以al2o3计为65gal2o3/l的硫酸铝溶液,配制浓度以al2o3计浓度为165gal2o3/l,苛性比为1.40的偏铝酸钠溶液;向15l第一反应釜中加入底水1500ml,启动搅拌和加热装置,当温度达到60℃时,以35ml/min的流速向第一反应釜中加入硫酸铝溶液,同时并流加入偏铝酸钠溶液,通过调整偏铝酸钠溶液的流量,控制反应釜浆液ph值为5.5,并保持反应釜内浆液温度60℃恒定。
64.当反应釜内浆液达到溢流口后,浆液由溢流口进入第二反应釜中,同时并流加入偏铝酸钠溶液,通过调整偏铝酸钠溶液的流速控制第二反应釜内浆液ph值为8.8,并保持第二反应釜内浆液温度60℃恒定。
65.当第二反应釜内浆液达到或高于溢流口时,浆液进入老化罐进行浆液收集,收集好浆液的老化罐开始老化,浆液由另一个老化罐收集;老化温度为90℃,时间为90min。
66.老化结束后用75℃去离子水进行洗涤,洗涤结束后在120℃下干燥8小时。得到拟薄水铝石f-2,其三水含量分析结果见表1。
67.将所得拟薄水铝石f-2再经600℃焙烧3小时,所得氧化铝f-2,其孔性质及红外光谱分峰拟合后酸性羟基与碱性羟基峰面积百分比见表1,红外光谱见图1。
68.比较例3配制浓度以al2o3计为65gal2o3/l,苛性比为1.25的低深度偏铝酸钠溶液和浓度以al2o3计浓度为165gal2o3/l,苛性比为1.40的高浓度偏铝酸钠溶液;向10.0l第一反应釜中加入温度为25℃的低浓度偏铝酸钠溶液7000ml,然后通入二氧化碳含量为40%(体积分数)的二氧化碳和空气混合气体,使低浓度偏铝酸钠溶液的ph值由13.8降至11.5。
69.温度为25℃的高浓度偏铝酸钠溶液以35ml/min的流速进入溶气泵,同时,向溶气泵中通入二氧化碳含量为75%(体积分数)的二氧化碳和空气混合气体,气、液经溶气泵混合后由第二反应釜底部连续进入第二反应釜中,控制碳化时间为40min,控制体系的ph值为5.5。
70.当第二反应釜内浆液达到溢流口后,浆液由溢流口进入已加底水1500ml、温度为60℃且已启动搅拌器的15l第三反应釜中,同时并流加入ph值降至11.5的低浓度偏铝酸钠
溶液,通过调整ph值降至11.5的低浓度偏铝酸钠溶液的流速控制第三反应釜内浆液ph值为8.8,并保持第三反应釜内浆液温度60℃恒定。
71.当第三反应釜内浆液达到或高于溢流口时,浆液进入老化罐进行浆液收集,收集好浆液的老化罐开始老化,浆液由另一个老化罐收集;老化温度为90℃,时间为90min。
72.老化结束后用75℃去离子水进行洗涤,洗涤结束后在120℃下干燥8小时。得到拟薄水铝石f-3,其三水含量分析结果见表1。
73.将所得拟薄水铝石f-3再经600℃焙烧3小时,所得氧化铝f-3,其孔性质及红外光谱分峰拟合后酸性羟基与碱性羟基峰面积百分比见表1,红外光谱见图1。
74.实施例6称取实施例1制备的拟薄水铝石150g,加入3g田菁粉,4.5g质量浓度为65%的硝酸和270g去离子水,混捏后挤条成型,在120℃下干燥6小时,再在700℃下焙烧3小时得到催化剂载体。
75.将载体浸渍mo-ni-p溶液,在120℃下干燥6小时,经450℃焙烧3小时得到催化剂a
c-1,催化剂性质见表2,催化剂评价结果见表4。
76.实施例7其它同实施例6,只是将拟薄水铝石改为实施例5制备的拟薄水铝石,制得的催化剂a
c-5性质见表2,催化剂评价结果见表4。
77.比较例4称取比较例1制备的拟薄水铝石150g,加入3g田菁粉,4.5g质量浓度为65%的硝酸和270g去离子水,混捏后挤条成型,在120℃下干燥6小时,再在700℃下焙烧3小时得到催化剂载体。
78.将载体浸渍mo-ni-p溶液,在120℃下干燥6小时,经450℃焙烧3小时得到催化剂f
c-1,催化剂性质见表2,催化剂评价结果见表4。
79.比较例5其它同比较例4,只是将拟薄水铝石改为比较例2制备的拟薄水铝石,制得的催化剂f
c-2性质见表2,催化剂评价结果见表4。
80.比较例6其它同比较例4,只是将拟薄水铝石改为比较例3制备的拟薄水铝石,制得的催化剂f
c-3性质见表2,催化剂评价结果见表4。
81.表1拟薄水铝石及氧化铝分析结果
编号a-1/a-1a-2/a-2a-3/a-3a-4/a-4a-5/a-5f-1/f-1f-2/f-2f-3/f-3拟薄水铝石
ꢀꢀꢀꢀꢀꢀꢀꢀ
三水铝石含量,wt%未检出未检出未检出未检出未检出3.311.102.73氧化铝
ꢀꢀꢀꢀꢀꢀꢀꢀ
孔容,ml/g1.161.081.121.161.120.830.960.98比表面积,m2/g335310320328319355364332平均孔径,nm13.913.914.014.114.09.410.511.8孔分布,%
ꢀꢀꢀꢀꢀꢀꢀꢀ
<6nm4.04.34.44.24.528.615.813.06~15nm75.575.575.274.774.949.263.966.6>15nm20.520.220.421.120.622.220.320.4酸性羟基/碱性羟基8.238.218.138.218.176.235.186.37
注:表1中“酸性羟基/碱性羟基”表示:酸性羟基峰与所述碱性羟基峰的峰面积比。
82.表2实施例和比较例制备的催化剂性质催化剂编号a
c-1a
c-5f
c-1f
c-2f
c-3孔容,ml/g0.8120.8090.6490.7250.7105比表面积,m2/g245240258261255平均孔直径,nm13.313.510.111.111.1孔分布,%
ꢀꢀꢀꢀꢀ
《6.0nm5.45.327.216.113.16.0-15.0nm78.578.455.967.470.8》15.0nm16.116.316.916.516.1金属含量,wt%
ꢀꢀꢀꢀꢀ
moo316.216.516.516.316.1nio3.73.94.13.94.0将制备的催化剂在中型渣油加氢处理装置上进行活性评价,其中渣油的性质及评价条件如表3,评价结果如表4。
83.表3原料油性质及评价条件原料油性质 s,wt%3.12n,wt%0.31残炭,wt.70金属(ni v),mg/kg72.20评价条件 液时体积空速,h-1
0.54反应温度,℃385入口压力,mpa14.7氢油体积比1000表4本发明实施例和比较例制备的催化剂评价结果催化剂编号a
c-1a
c-5f
c-1f
c-2f
c-3脱除率,wt%
ꢀꢀꢀꢀꢀ
脱硫率82.883.073.273.975.3脱残炭率60.160.248.149.350.2脱ni v率62.863.251.952.354.7
再多了解一些
本文用于企业家、创业者技术爱好者查询,结果仅供参考。