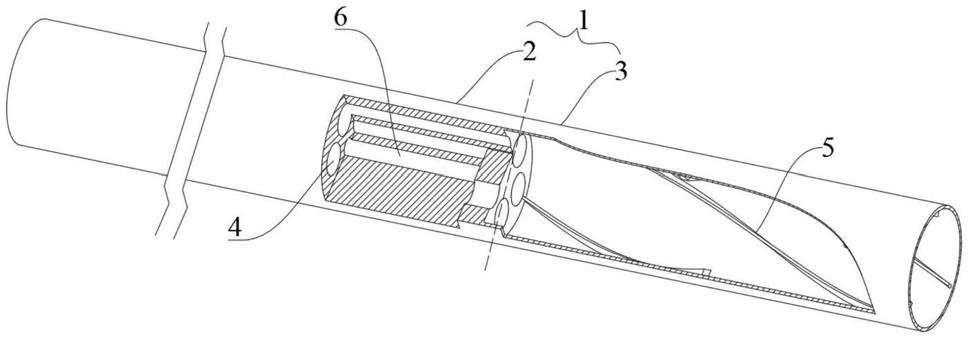
1.本发明属于炭化设备领域,具体涉及一种用于干馏热解法炭化的炭化炉炉体。
背景技术:
2.现有的连续炭化炉多为单筒式炭化炉,单筒式炭化受热面积小、炭化效率低,物料磨损严重,得率低,产量小。物料因用多筒式炭化炉进行炭化,物料在炉内可均匀分布在每个筒体,物料受热面积增大,受热时间增长,使物料能均匀充分吸热。物料的堆积高度降低,从而减少物料与物料之间的磨损,降低在炉体转动过程中物料的滑动速度从而降低物料的冲击力,使物料在未强化阶段,减少物料的破损。多筒式炭化炉在炭化物料的质量,得率和产量上均有所提高。
技术实现要素:
3.本发明需要解决的技术问题是:1.提供一种多筒段与单筒段结合的炭化炉炉体结构,物料自多筒段流向单筒段,高温烟气自单筒段流向多筒段,将炭化分成中低温炭化(多筒段)与高温全面炭化(单筒段)两部分,在多筒段,将原本铺设在一个单筒段内的物料分布在多个物料通道(多筒段),能够增加受热面积,受热时间,降低料层厚度,提高炭化效率和得率,单筒段设有螺旋叶片,进一步的加快物料的行进速度和全面炭化。
4.2.优化多筒段的各通道及通道之间的尺寸,减少炉体自重,防止炉体运转坍塌,延长旋转支撑件的使用寿命。
5.为了解决上述问题,本发明提供了一种新的技术方案,本发明是通过以下技术方案实现的,一种用于干馏热解法炭化的炭化炉炉体,包括炭化炉本体,炭化炉本体为圆筒形结构,炭化炉本体倾斜设置,并且设置有旋转支撑机构,炭化炉本体包括一体成型的多筒段与单筒段,多筒段高于单筒段,多筒段包括若干个嵌入炭化炉本体的筒状物料通道,物料通的中心位于炭化炉本体的圆心与圆周之间,均布于炭化炉本体内,并且其中轴与炭化炉本体轴平行,若干个物料之间填充有耐火材料。多筒段与单筒段相结合的优势在于,在多筒段,将原本铺设在一个单筒段内的物料分布在多个物料通道(多筒段),能够增加受热面积,受热时间,降低料层厚度,提高炭化效率和得率。
6.进一步地,炭化炉本体内径为1.5m~2.2m,物料通道的内径为250mm~700mm。炉体过小达不到所需的生产规模,炉体过大对旋转支撑件要求过高,增加制造成本以及后期维护成本。
7.进一步地,物料通道个数为3个~8个,每个物料通道外圆周之间的间距为100mm~200mm。若物料通道过少,则达不到炭化效率的目的,若物料通道过多则会缩减各物料通道之间的间距,而各个物料通道之间的耐火可塑料与耐火浇筑料强度不够,容易发生坍塌。
8.进一步地,多筒段中心为中空的筒形中心孔,并且两端封闭,中心孔的外圆周与物
料通道外圆周之间的间距为100mm~200mm。中空的结构能够减少炉体的自重。
9.进一步地,单筒段内壁设置有螺旋叶片,螺旋叶片不仅能够加速物料的传输速度,并且能在翻转过程中将物料翻起,使物料能够更加充分的炭化。
10.本发明的有益效果为:1.将原本铺设在一个单筒段内的物料分布在多个物料通道(多筒段),能够增加受热面积,受热时间,降低料层厚度,提高炭化效率和得率,后有回到单筒段,单筒段设有螺旋叶片,进一步的加快物料的行进速度和全面炭化。这种多筒段与单筒段结合的炭化炉炉体结构提高了物料的质量和产量。
11.2.优化了多筒段的各通道及通道之间的尺寸,减少炉体自重,延长旋转支撑件的使用寿命。
12.3.炉体本体设置为中空的结构能够减少炉体自重,延长使用寿命。
13.4.单筒段内壁的螺旋叶片不仅能够推进物料的前进,并且能够将物料翻起,使炭化更加充分。
附图说明
14.图1为本发明实施例的整体示意图;图2为本发明实施例一的多筒段切面视图;图3为本发明实施例二的多筒段切面视图;图4为本发明实施例三的多筒段切面视图。
15.图中:1、炭化炉本体;2、多筒段;3、单筒段;4、物料通道;5、螺旋叶片;6、中心孔;7、减重孔。
具体实施方式
16.实施例一:如图1-图2所示:一种用于干馏热解法炭化的炭化炉炉体,包括炭化炉本体,炭化炉本体为圆筒形结构,炭化炉本体倾斜设置,并且设置有旋转支撑机构,炭化炉本体包括一体成型的多筒段2与单筒段3,多筒段2高于单筒段3,炉体最外层为筒形碳钢壁,碳钢壁的内壁上覆盖有有陶瓷纤维布或保温岩棉等其他保温材料,在此基础上,采用耐火浇筑料或可塑料成型多筒结构形成多筒段2和单筒段3,并且在单筒段3内壁上成型螺旋结构。
17.多筒段2包括3个筒状物料通道4,物料通的中心位于炭化炉本体的圆心与圆周之间,均布于炭化炉本体内(绕炭化炉本体周周圆周阵列),并且其中轴与炭化炉本体轴平行,若干个物料之间填充有耐火浇筑料或耐火可塑料。多筒段2与单筒段3相结合的优势在于,若全部设置为多筒段2,则势必会增加炉体的自重,增加旋转支撑件的负荷。除此之外,物料的炭化时间是一定的,全部设为多筒段2,则物料行进的速度慢,反之就会加快炉体的转速,导致物料翻滚滑行次数增加,增加了磨损,降低的得率,对旋转支撑件的寿命也是大大缩短。
18.炭化炉本体1内径为1.72m,物料通道4总共有3个, 物料通道4的内径为320mm,每个物料通道4外圆周之间的间距为200mm。多筒段2长度为11m,单筒段3长度为8m。
19.单筒段3内壁设置有3条螺旋叶片5,螺旋叶片5不仅能够加速物料的传输速度,并且能在翻转过程中将物料翻起,使物料能够更加充分的炭化。
20.实施例二:如图3所示,实施例二与实施例一相比,结构大体相似,其区别特征在于炭化炉本体内有中心孔6,并且中心孔6两端是封闭的,并且物料通道4的数量以及相关尺寸不同,具体的,炭化炉本体内径为2.2m,物料通道4总共有5个,物料通道4直径为550mm,每个物料通道4外圆周之间的间距为180mm,每个物料通道4外圆周与中心孔6外圆周之间的间距为180mm。
21.实施例三:如图4所示,实施例三与实施例二相比,结构大体相似,其区别特征在于炭化炉本体周边均布有减重孔7,减重孔7与中心孔6相似,两端为封闭的,并且物料通道4的数量以及相关尺寸不同,具体的,炭化炉本体内径为1.76m,物料通道4总共有6个,物料通道4直径为470mm,每个物料通道4外圆周之间的间距为100mm,每个物料通道4外圆周与中心孔6外圆周之间的间距为100mm。
技术特征:
1.一种用于干馏热解法炭化的炭化炉炉体,包括炭化炉本体(1),所述炭化炉本体(1)为圆筒形结构,所述炭化炉本体(1)倾斜设置,并且设置有旋转支撑机构,其特征在于,所述炭化炉本体(1)包括一体成型的多筒段(2)与单筒段(3),所述多筒段(2)高于所述单筒段(3),所述多筒段(2)包括若干个嵌入所述炭化炉本体(1)的筒状物料通道(4),所述物料通的中心位于所述炭化炉本体(1)的圆心与圆周之间,均布于所述炭化炉本体(1)内,并且其中轴与所述炭化炉本体(1)轴平行,若干个所述物料之间填充有耐火材料。2.如权利要求1所述的一种用于干馏热解法炭化的炭化炉炉体,其特征在于,所述炭化炉本体(1)内径与所述物料通道(4)的内径为的比值为:3:1~9:1。3.如权利要求1所述的一种用于干馏热解法炭化的炭化炉炉体,其特征在于,所述物料通道(4)个数为3个~8个,每个物料通道(4)的外径与各物料通道外圆周之间的间距比值为5:1~5:2。4.如权利要求1所述的一种用于干馏热解法炭化的炭化炉炉体,其特征在于,所述多筒段(2)中心为中空的筒形中心孔(6),并且两端封闭,所述中心孔(6)的外圆周与所述物料通道(4)外圆周之间的间距为与各物料通道外圆周之间间距相同。5.如权利要求1-3条任意一项所述的一种用于干馏热解法炭化的炭化炉炉体,其特征在于,所述单筒段(3)内壁设置有螺旋叶片(5)。
技术总结
本发明属于炭化设备领域,具体涉及一种用于干馏热解法炭化的炭化炉炉体。包括炭化炉本体,炭化炉本体为圆筒形结构,炭化炉本体倾斜设置,并且设置有旋转支撑机构,炭化炉本体包括一体成型的多筒段与单筒段,多筒段高于单筒段,多筒段包括若干个嵌入炭化炉本体的筒状物料通道,多筒段与单筒段相结合的优势在于,在多筒段,将原本铺设在一个单筒段内的物料分布在多个物料通道,能够降低料层厚度,增加受热面积,提高炭化效率。单筒段设有螺旋叶片,进一步的加快物料的行进速度和全面炭化。物料在多筒段经过预热干燥阶段,热解阶段,固化阶段后进入单筒段,单筒段设有螺旋叶片,进一步的加快物料的行进速度和全面炭化。快物料的行进速度和全面炭化。快物料的行进速度和全面炭化。
技术研发人员:胡建军 雍波 胡家荣
受保护的技术使用者:宁夏亘瑞宏建筑安装有限公司
技术研发日:2022.01.27
技术公布日:2022/4/29
再多了解一些
本文用于企业家、创业者技术爱好者查询,结果仅供参考。