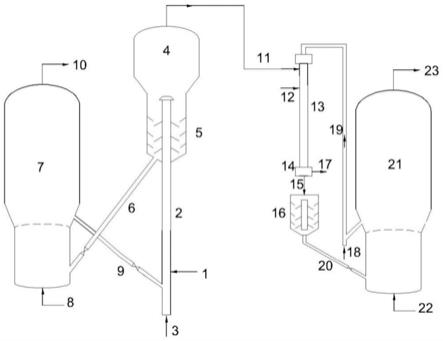
1.本发明涉及一种原油制取低碳烯烃和芳烃的方法。
背景技术:
2.近年来,我国炼油产业获得了长足的发展,炼油能力显著提升。截至2019年底,全国炼油能力达到8.6亿吨,产能利用率仅76%,产能过剩现象严重。预计到2025年,国内还将新增炼油能力2.1亿吨/年,产能过剩将更为严重。另一方面,随着我国逐渐进入经济新常态,经济告别高增速,汽柴油等燃油需求进入瓶颈期,加之我国新能源产业的发展,电动汽车推广力度不断加大,成品油未来市场空间有限,炼厂由油品转向低碳烯烃和芳烃等化工品的生产为大势所趋。催化裂解技术是由石油原料生产低碳烯烃和芳烃的有效方法。
3.中国专利cn110724551a提出了一种采用稀相输送床和湍流流化床进行催化裂解的方法和系统,该方法是将预热后的重油与催化剂在输送发生一次反应,生成第一油气产物和半待生催化剂,而后将半待生催化剂和第一油气产物进行湍流床反应。该方法可以提高提高重油与催化剂的反应深度,并且具有干气和焦炭收率低,产品分布好的特点。
4.中国专利cn110724561a公开了一种生产丙烯和轻芳烃的催化裂解方法和系统,该专利指出,将轻质原料与催化剂在稀相输送床下反应,生成第一反应产物和半待生催化剂,而后将第一反应产物和半待生催化剂进行密相流化床反应;而后将重油在另一快速流化床中进行油剂接触反应,最后从轻重油反应得到的油气产物中分离获得低碳烯烃和芳烃。
5.中国专利cn200710120105公开一种制取低碳烯烃和轻芳烃的方法,该方法按照原来裂化难以程度注入变径提升管的不同部位,可以获得较高的乙烯丙烯和轻芳烃收率。
6.美国专利us2002195373公开了一种使用下行反应器进行催化裂解生产低碳烯烃的方法,该方法将原料油在550~650℃,大剂油比(15以上)和短停留时间(0.5s以下)下,将在低氢转移活性催化剂的条件下进行快速裂解反应,尽量保留中间产物,从而获得较高的低碳烯烃收率。
7.中国专利cn110724558a公开了一种生产丙烯和高辛烷值汽油的催化裂解方法和系统,该专利中将原料油分为优质重油和劣质重油,优质重油进行稀相输送床和密相流化床的串联反应,劣质重油进行通入另一快速流化床进行反应,方法和系统进行催化裂解的焦炭和干气产率低,低碳烯烃和高辛烷值汽油产率高。
8.中国专利cn109575982a将原料分为轻组分和重组分,分别在不同的反应器进行催化裂解反应,轻质原料的反应温度为600~800℃,重质原料的反应温度为500~780℃,该方法具有单程转化率高,烯烃的选择性高的特点。
9.从现有技术看,现有的催化裂解方法制取低碳烯烃和芳烃方法,在使用重油为原料时,通过调整催化剂与油品的接触状态和流化状态,达到较高的低碳烯烃和芳烃收率,对于使用原油为原料时,往往采取轻质组分和重质组分分离的方法,在同一催化剂体系下,将轻质组分和重质组分通入不同的反应器下,轻质组分使用高温操作条件,克服轻质组分裂解活性较低的问题,而重质组分本身容易裂解,则使用稍低反应温度。
10.催化裂解技术本身对原料要求比较高,需要原料中有较高的氢含量,并且要求原料中镍、钒等重金属含量、沥青质以及残炭等杂质的含量较低。因此,现有的催化裂解技术和以催化裂解技术为核心的油品制取低碳烯烃和芳烃的技术,均需要石蜡基属性的原料。
11.对于中间基属性的原料,其氢含量较低,残炭、沥青质、重金属含量均较高,无法使用以上述所列专利为代表的催化裂解的方法进行低碳烯烃和芳烃生产。而世界范围内,特别是国内所产原油,石蜡基属性原油产量占比较小,资源稀缺,大量开采可获得的原油是中间基属性和环烷中间基的原油。因此有必要开发一种能够适用于中间基属性原油制取低碳烯烃和芳烃的方法,使之能够满足以中间基原油为原料的大多数炼油企业的需求。
技术实现要素:
12.本发明所要解决的技术问题是提供一种用于中间基原油制取低碳烯烃和芳烃的方法。
13.为了实现该目的,本发明采用如下技术方案予以实现:
14.一种原油制取低碳烯烃和芳烃的方法,该方法包括:
15.1)将原油预热至120~300℃后,从提升管反应器进料喷嘴处喷入,原油与第一催化剂进行接触,在反应压力0.04~0.7mpa,反应温度420~520℃,反应时间0.3~18.5s,水油比(0.03~0.55):1,剂油比(3.8~15.0):1条件下,发生第一催化反应,反应结束后,进行油剂分离,获得第一油气产物和结焦失活的第一催化剂,失活的第一催化剂经水蒸气汽提后,送入第一再生器,通入含氧气体进行烧焦再生,获得第一烟气,第一催化剂再生后循环使用;
16.2)将获得的第一油气产物以气相状态全部引入下行床反应器中,与第二催化剂进行接触,在反应压力0.04~0.65mpa,反应温度520~660℃,反应时间0.2~3.0s,水油比(0.10~0.55):1,剂油比(5.0~21.0):1条件下,发生第二催化反应,反应结束后,经油剂分离,获得第二油气产物和结焦失活的第二催化剂,失活的第二催化,经水蒸气汽提后,送入第二再生器,通入空气烧焦再生,获得第二烟气,第二催化剂再生后循环使用,第二油气产物进入到后续分离装置,获得低碳烯烃、轻质芳烃、重质芳烃;
17.所述第一催化剂由基质、载体、粘结剂、活性组分构成,以干基为基准,基质为高岭土、硅藻土、埃洛石中的一种或几种,含量8~50%,载体无定型硅酸铝氧化物、氧化硅、氧化铝、氧化钛中的一种或几种,含量5~45%,粘结剂为铝溶胶、硅溶胶粘结剂中的一种或两种,含量2~14%,活性组分为氧化铁、氧化镍、氧化钾、氧化钙、氧化镁、氧化钠、氧化锰、氧化铈、氧化镓、氧化钒、高硅分子筛、介孔分子筛中的一种或几种以氧化物计10~30%,所述催化剂中介孔孔体积占总孔体积的比例为25.5~100%,介孔孔容占总孔容比例为20~100%;
18.所述第二催化剂,以高岭土、蒙脱土、埃洛石中的一种或几种作为基质,含量15~55%,以拟薄水铝石、硅溶胶、铝溶胶中的一种或几种作为粘结剂,含量10~25%,以mfi分子筛以及y型分子筛,beta分子筛、alpo~5分子筛中的一种或几种为活性组分,mfi分子筛含量为10~30%,其余分子筛含量为2~15%。
19.本发明所述的原油制取低碳烯烃和芳烃的方法中,所述原料油为中间基原油,具体的,所述中间基原油为原油中第一关键组分和第二关键组分中任一组分属于中间基属性
的原油。
20.所述原油可以还包括掺入一定量的脱沥青油、加氢裂化尾油、页岩油、常压渣油、减压渣油、减压蜡油。
21.优选的,所述原油密度范围为0.80~0.98g/cm3,残炭值为0.1~15%,镍和钒含量为0~1000mg/kg。
22.优选的,所述后续分离装置包含分馏塔和气体分离装置、芳烃抽提装置,选取第二油气产物中初馏点~80℃馏分,优选45~65℃馏分,总量的30~80%,优选45~70%,作为第一回炼组分,选取170~280℃馏分,优选185~245℃馏分,总量的35~75%,优选45~65%,作为第二回炼组分。
23.优选的,将第一回炼组分以及第二回炼组分中的任意一种或者两种的混合组分,送入到下行床反应器进行回炼。
24.优选的,所述上行床反应器包括稀相输送床提升管反应器、密相输送床提升管反应器,等径或者扩径的提升管反应器。
25.优选的,所述mfi型分子筛制备方法为,以硅铝比为30~80的zsm-5分子筛为晶种,晶种占所合成分子筛干基重量的0.5~3.0%,依次加入大孔拟薄水铝石、正丁胺和水玻璃,按照(sio2):n(al2o3):n(正丁胺):n(naoh):n(h2o)=1:0.01~0.35:0.19~0.42:0.05~0.50:30进行配比,在55~65℃进行成胶,在70~85℃下老化2~14h,在120℃下晶化6~10h,而后在165~180℃下晶化10~14h,采用ni、p、fe元素对分子筛进行化学改性,以干基计,ni以氧化物计含量为0.3~1.2%,p以氧化物计含量为1.0~4.5%,fe以氧化物计含0.8~2.5%。
26.优选的,所述的y型分子筛以la、ce、p、zn进行改性,la和ce以离子交换形式负载,负载后,在450~550℃条件下,焙烧1~3.5h,而后在400~520℃下水蒸气含量为33~47%的气氛中老化1.5~4.5h,p和zn浸渍形式负载,负载后在500~635℃条件下,焙烧2~5.5h,以干基计,la以氧化物计含量为1.1~4.8%,ce以氧化物计含量为0.8~3.5%,p以氧化物计含0.3~2.2%,zn以氧化物计含0.5~1.7%。
27.优选的,所述的通入第一再生器含氧气体是空气、富氧空气或氧气中的一种,所述的催化剂再生方式为单段再生、两段再生以及湍动床、快速床或输送床再生的一种。
28.优选的,水蒸气和含氧气体的质量比为0~0.45:1,第一再烟气为常规烟气或者含co2的合成气。
29.本发明的方法与现有技术相比,具有如下有益效果:
30.1)本发明方法将原油先在提升管中接触第一催化剂,第一催化剂不以强酸性y分子筛为活性组分,极大幅度降低了原油中重金属对分子筛结构的破坏作用,此外,也可以极大程度避免沥青质和残炭等导致酸性分子筛催化剂快速结焦,失去活性的缺点,同时含有丰富的介孔结构满足大分子扩散,适于处理高重金属含量、高沥青质高残炭含量的中间基原油。
31.2)本发明方法先将原油中的大分子进行浅度裂化,从而生成大量富含烯烃的油气产物,再与与第二催化剂发生反应第二催化反应。由于第一油气产物基本不含有重金属和残炭可以最大化发挥第二催化剂的催化剂作用;第二催化反应的反应温度较高,有利于第一油气产物最大限度生产低碳烯烃和芳烃产物。此外,原油中的大分子经过第一催化剂的
反应,大部分转化为汽油或者柴油分子量范围内组分,利于第二催化剂消除扩散作用,将第一油气产物最大化转化为低碳烯烃和芳烃产品。
附图说明
32.图1为本发明原油制取低碳烯烃和芳烃的工艺流程示意图。
33.图中,1原油,2提升管反应器,3预提升气,4沉降器,5汽提器ⅰ,6第一待生剂输送斜管,7第一再生器,8含氧气体,9第一再生剂输送斜管,10第一烟气,11第一油气产物,12回炼组分进料,13下行床反应器,14卧式旋风分离器,15第二待生剂,16汽提器ⅱ,17第二油气产物,18提升气,19第二再生剂输送立管,20第二待生剂输送斜管,21第二再生器,22烧焦空气,23第二烟气
具体实施方式
34.下面通过具体实施例对本发明技术方案作进一步说明。
35.实施例
36.本例所用第一催化剂制备过程如下。将高岭土与水混合打浆,而后加入氧化铝,氧化硅,氧化钛充分混合,而后加入铝溶胶粘结剂,而后加入硝酸铁、硝酸铈、硝酸钙、硝酸钒,控制固含量在28%,以氧化物干基计,高岭土、氧化铝、二氧化硅、氧化钛、铝溶胶以及氧化铁、氧化铈、氧化钙、氧化钒的比例为41.0%,17.1%,19.2%、5.1%、4.5%以及2.2%、5.0%、3.9%,2.0%,将混合好的浆液进行喷雾成型为催化剂。
37.成型后的催化剂在520℃下焙烧2h,而后将硝酸钾、硝酸锰和磷酸的混合液浸渍到焙烧后的催化剂上,以氧化物干基计,氧化钾、氧化锰和五氧化二磷分别占催化剂重量的1.4%,1.8%和2.3%。将浸渍后的催化剂烘干,在500℃条件下焙烧1.5h,获得成品催化剂。所制催化剂中介孔孔体积占总孔体积的比例为46.3%,介孔孔容占总孔容比例为63.1%。
38.第二催化剂制备过程如下。将高岭土与水混合打浆,加入拟薄水铝石充分混合,加入适量盐酸溶液,而后加入铝溶胶,充分混合后,加入mfi型分子筛,y分子筛,alpo-5分子筛,充分混合后,控制固含量为25%。以氧化物干基计,高岭土、拟薄水铝石、铝溶胶、mfi型分子筛、y分子筛以及alpo-5分子筛的比例为39.0%,19.7%,5.2%,23.5%,5.0%、7.6%,将混合好的浆液进行喷雾成型为催化剂。
39.所用mfi分子筛制备过程:以硅铝比为60的zsm-5分子筛为晶种,晶种占所合成分子筛干基重量的1.5%,依次加入大孔拟薄水铝石、正丁胺和水玻璃,按照(sio2):n(al2o3):n(正丁胺):n(naoh):n(h2o)=1:0.25:0.25:0.35:30进行配比,在58℃进行成胶,在80℃下老化5h,在120℃下晶化8h,而后在175℃下晶化12h,采用ni、p、fe元素对分子筛进行化学改性,以干基计,ni以氧化物计含量为1.0%,p以氧化物计含量为1.5%,fe以氧化物计含1.8%。
40.所述的y型分子筛以la、ce、p、zn进行改性,la和ce以离子交换形式负载,负载后,在450~550℃条件下,焙烧1~3.5h,而后在400~520℃下水蒸气含量为33~47%的气氛中老化1.5~4.5h,p和zn浸渍形式负载,负载后在500~635℃条件下,焙烧2~5.5h,以干基计,la以氧化物计含量为1.5%,ce以氧化物计含量为3.0%,p以氧化物计含1.5%,zn以氧化物计含1.2%。
41.所用原油性质见标表1,该原油属于中间基原油。
42.表1
43.项目数值密度,20℃,g/cm30.9334残炭,m%4.6碳含量,m%86.70氢含量,m%12.42氮含量,m%0.31硫含量,m%0.57重金属含量,μg/g 镍10.4钒3.5馏程,℃ 10%19530%31450%40670%48990%681
44.将表1所述性质的原油1预热至221℃后,从提升管进料喷嘴处喷入提升管反应器2,原油与第一催化剂进行接触,在反应压力0.25mpa,反应温度475℃,反应时间2.2s,水油比0.12:1,剂油比6.5:1条件下,发生第一催化反应,反应结束后,经油剂分离,获得第一油气产物11和结焦失活的第一待生催化剂,第一待生催化剂在汽提器ⅰ5内经水蒸气汽提,去除催化剂上残存的油气产物后,经第一待生剂输送斜管6送入第一再生器7,通入含氧气体,在731℃条件下进行烧焦再生,获得第一烟气10,第一催化剂再生后循环使用。
45.通入第一再生器10的含氧气体为空气和水蒸汽的混合气体,水蒸气和含氧气体的质量比为0.1:1,再生形式为待前置烧焦罐的两段再生。获得第一烟气为含co2的合成气。
46.将获得的第一油气产物11以气相状态全部引入下行床反应器13中,与第二催化剂进行接触,在反应压力0.31mpa,反应温度645℃,反应时间0.7s,水油比0.18:1,剂油比14.2:1条件下,发生第二催化反应,反应结束后,经油剂分离,获得第二油气产物17和结焦失活的第二催化剂,失活的第二催化剂,经水蒸气汽提,除去催化剂上残存的油气产物后,送入第二再生器21,通入在空气在680℃条件下进行烧焦再生,获得第二烟气,再生后的第二催化剂循环使用。
47.第二油气产物17送入后续分离装置,在分馏塔内,分馏为包含乙烯、丙烯、丁烯的气体组分,富含c6~c9轻质芳烃大的汽油组分,富含2~4环重质芳烃的重组分,富含轻质芳烃大的汽油组分经精制后,进行芳烃抽提,获得轻质芳烃产物,重组分经精制后获得可用于生产碳材料的2~4环重质芳烃产物。
48.将分馏塔内获得的43~70℃组分以及180~240℃组分,混合后送入下行床反应器进行回炼。
49.表2是以该中间基原油为原料的产物分布结果,表2
[0050][0051][0052]
由表中可以看到,乙烯收率达到5.8%,丙烯和丁烯的收率可达16.3%和14.6%,汽油中轻芳烃的收率为21.4%,重质芳烃收率为14.5%。在本发明提供的方法下,以渤中中间基原油为原料,可以获得72.8%的低碳烯烃和芳烃收率。
[0053]
以上实施例为本发明代表性实施方式,本发明不局限于上述实施例中的具体细节,在本发明的技术构思范围内,可以对本发明的技术路线进行简单变型和催化剂配方调整,这些简单的变型和调整均在本发明的保护范围之内。
再多了解一些
本文用于企业家、创业者技术爱好者查询,结果仅供参考。