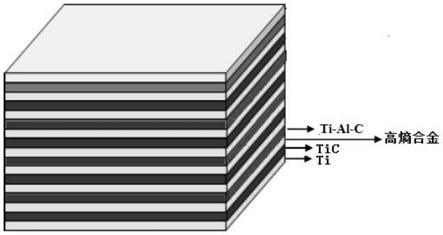
1.本发明涉及合金材料技术领域,特别涉及一种高熵合金及其制备方法和耐磨抗氧化涂层及其制备方法。
背景技术:
2.max相(m是过渡族金属元素,a主要是第三或第四主族元素,x是c或n)是一种三元层状高性能陶瓷材料,在max相晶体结构中,m和x原子通常以强的共价键和离子键结合,而m与a或m与m之间通常以弱共价键和金属键结合。其独特的晶体结构和键合方式使得max相兼具金属和陶瓷的特性。ti2alc是一种新型的max相,具有层状结构和六方晶系的三元碳化物晶格,因其具有低密度、低热膨胀系数、室温弹性模量高、高抗氧化和抗腐蚀性等优点而被备受关注。
3.近年来,随着科学技术的发展,人们对材料性能的要求越发苛刻。例如,飞机祸轮发动机的叶片,使用温度越高,推重比越大,效率越高,提高高温合金的使用温度一直是航空领域的一个重要课题。在高温合金等金属表面镀制高温防护涂层为实现提高高温合金的使用温度开辟了一条途径。与金属cr、sic和fecral涂层类似,ti2alc max相涂层被认为是最有潜力的高温防护材料候选材料之一。
4.高温防护涂层是现代工业中非常重要的一类涂层,需具有良好的抗高温氧化和耐磨性能。然而,ti2alcmax相一般为六方结构,层与层之间易发生滑移而产生位错,进而产生一定的塑性变形。其层状结构在发生准塑性变形的过程中会产生类似于金属塑性变形时的流线,为位错的堆垛和移动。因此,与传统陶瓷相比,ti2alc也具有一般max陶瓷材料的缺点,比如常温下摩擦系数高、磨损量大,硬度值较小且其硬度具有各向异性等缺点,限制了其在宽温度范围内的摩擦磨损应用。
技术实现要素:
5.有鉴于此,本发明目的在于提供一种高熵合金及其制备方法和耐磨抗氧化涂层及其制备方法。本发明提供的高熵合金与ti2alc复合,能够使涂层具有优异的抗高温氧化性,而且在常温及高温(1000℃)下均具有良好的耐磨性能。
6.为了实现上述发明目的,本发明提供以下技术方案:
7.本发明提供了一种高熵合金,所述高熵合金包括以下原子百分比的组分:al 15~25%、cr 10~20%、fe 10~20%、ti 10~20%、mo 10~20%、nb 10~20%、w 10~20%与re 0~10%,其中,re为稀土且re的原子百分比不为0。
8.优选地,所述re为y、ce和la中的一种或几种。
9.本发明提供了以上技术方案所述高熵合金的制备方法,包括以下步骤:
10.(1)将al、cr、fe、ti、mo、nb、w和稀土按照高熵合金的组成配比混合后依次进行球磨、过筛和干燥,得到混合金属粉末;
11.(2)将所述混合金属粉末依次进行氢氮还原和退火,得到除氧混合金属粉末;
12.(3)将所述除氧混合金属粉末进行等离子熔覆,得到熔覆层;将所述熔覆层进行退火,得到高熵合金。
13.优选地,所述步骤(2)中氢氮还原的温度为300~400℃,时间为3~4h;所述氢氮还原中氢气与氮气的体积比1:6~1:19。
14.本发明提供了一种耐磨抗氧化涂层,自下而上,包括依次层叠设置的底层、过渡层和复合层;所述底层为ti层,所述过渡层为tic层;所述复合层为高熵合金和ti2alc的交替叠加层,所述复合层的最下层为高熵合金,最上层为ti2alc,所述高熵合金为以上技术方案所述高熵合金或以上技术方案所述制备方法制备得到的高熵合金。
15.优选地,所述底层的厚度为20~200nm;所述过渡层的厚度为30~400nm;所述高熵合金的单层厚度为0.2~0.9μm,所述高熵合金的单层厚度与ti2alc的单层厚度之比为1:(1~4),所述高熵合金的层数为3~11层,所述ti2alc的层数为3~11层。
16.本发明提供了以上技术方案所述耐磨抗氧化涂层的制备方法,包括以下步骤:
17.将基体进行离子束刻蚀,在刻蚀的基体表面自下而上依次沉积ti层和tic层,然后在所述tic层表面交替沉积所述高熵合金和ti2alc,得到涂层预样品;所述沉积ti层、tic层和高熵合金采用电弧离子镀沉积法,所述沉积ti2alc采用磁控溅射沉积法;
18.将所述涂层预样品在保护气氛下进行退火,得到所述耐磨抗氧化涂层。
19.优选地,所述沉积ti层以钛靶为靶材,以氩气为工作气体;所述沉积ti层的电弧电流为50~100a,基底偏压为-60~-200v,工作气压为0.6~2.0pa,沉积时间为5~30min。
20.优选地,所述沉积tic层以钛靶为靶材,以ch4为反应气体,以氩气为工作气体,所述ch4的流量为40~60sccm,所述氩气的流量为200sccm;所述沉积tic层的电弧电流为50~100a,基底偏压为-80~-150v,工作气压为3~6pa,沉积时间为15~35min。
21.优选地,所述沉积高熵合金以高熵合金为靶材,以氩气为工作气体,所述氩气的流量为40~100sccm;所述沉积高熵合金的电流为60~100a,基底偏压优选为-80~-300v,工作气压为0.8~2.0pa,单层沉积时间为15~30min;
22.所述沉积ti2alc以tial合金为靶材,以碳氢反应气为反应气体,以氩气为工作气体,所述氩气的流量为100~300sccm,所述碳氢反应气的流量为10~30sccm,所述碳氢反应气的流量为碳氢反应气和氩气流量之和的5~15%;所述沉积ti2alc的电弧电流为40~100a,磁控电流为5~10a,基底偏压为-100~-300v,工作气压为2~5pa,单层沉积时间为20~40min;
23.所述沉积高熵合金和ti2alc的总沉积时间为90~300min。
24.优选地,所述退火的温度为600~900℃,时间为2~24h,升温至退火的温度的升温速率为4~8k/min;所述保护气氛为氩气,压强为0.1~0.5x103pa。
25.本发明提供了一种高熵合金,所述高熵合金包括以下原子百分比的组分:al 15~25%、cr 10~20%、fe 10~20%、ti 10~20%、mo 10~20%、nb 10~20%、w 10~20%与re 0~10%,其中,re为稀土且re的原子百分比不为0。在本发明中,所述高熵合金中掺杂少量的稀土,所述稀土的作用为:能够与o、s等元素结合,净化材料;形成第二相起到异质形核的作用,促进柱状晶向等轴化转变,钉扎晶界长大,细化晶粒,提高高熵合金的熔覆质量和力学性能;提高熔覆高熵合金时熔池流动性,降低气孔等缺陷;所述高熵合金中al的加入不仅降低了高熵合金的密度,而且提高了高熵合金在高温下的耐磨性和抗氧化性;nb的添加
减小了氧化物中的氧空位,而且减少了氧化膜中的孔洞,从而改善了高熵合金的抗氧化性能;mo和cr的添加可以细化第二相片层组织,保证合金具有较高的抗氧化、蠕变抗力和良好的高温性能;nb和w在高熵合金熔覆过程中,形成第二相,而第二相本身具有高的硬度和模量,能增强材料抵抗变形的能力;同时第二相的形成可以细化高熵合金的晶粒,起到间接强化的效果,而细小的第二相还可以起到钉扎基面位错的效果,从而实现强化;ti和mo元素可以形成moo3、tio2具有层状结构的magneli相,起到润滑作用,降低摩擦系数,提高复合层的耐磨性。因此,本发明提供的高熵合金具有良好的熔覆质量,高硬度和优异的耐磨性能,且具有较好的抗氧化性。
26.本发明提供了一种耐磨抗氧化涂层,自下而上,包括依次层叠设置的底层、过渡层和复合层;所述底层为ti层,所述过渡层为tic层;所述复合层为高熵合金和ti2alc的交替叠加层,所述复合层的最下层为高熵合金,最上层为ti2alc,所述高熵合金为以上技术方案所述的高熵合金。本发明提供的耐磨抗氧化涂层中,底层(ti层)能够提高基体表面的光洁度,增强基体表面的附着力;过渡层(tic层)能够增强膜-基结合力,并阻止后续退火过程中复合涂层和基底之间的元素互扩散;复合层中致密的高熵合金层能够显著提高复合层的耐磨性,ti2alc具有良好的抗高温氧化性能,且所述高熵合金和ti2alc的交替叠加,这种结构特点能够阻断柱状晶的贯穿性生长,阻止贯穿性缺陷存在,有利于减少涂层沉积过程中柱状晶的数量,改善涂层的综合性能。本发明提供的涂层具有优异的抗高温氧化性,在常温及高温(1000℃)下均具有良好的耐磨性能,而且高熵合金涂层具有无序结构和鸡尾酒效应,使得复合涂层间界面的润湿性和相容性更好,从而有利于提高膜基结合力。
附图说明
27.图1是本发明中高熵合金靶材熔覆制备扫描示意图;
28.图2是本发明中耐磨抗氧化涂层的结构示意图;
29.图3是实施例1制备的耐磨抗氧化涂层中高熵合金/ti-al-c复合层的sem形貌图;
30.图4是实施例1制备的耐磨抗氧化涂层中复合层退火后的xrd图;
31.图5是实施例1制备的耐磨抗氧化涂层在不同磨损试验温度下复合层摩擦系数与时间(s)的关系曲线;
32.图6是实施例1与对比例1~2制备的涂层磨损率随温度变化图;
33.图7是实施例1与对比例1~2制备的涂层在800℃下氧化表面形貌图,图7中(a)表示实施例1制备的涂层在800℃下氧化表面形貌图,(b)表示对比例1制备的涂层在800℃下氧化表面形貌图,(c)表示对比例2制备的涂层在800℃下氧化表面形貌图。
具体实施方式
34.本发明提供了一种高熵合金,所述高熵合金包括以下原子百分比的组分:al 15~25%、cr 10~20%、fe 10~20%、ti 10~20%、mo 10~20%、nb 10~20%、w 10~20%与re 0~10%,其中,re为稀土且re的原子百分比不为0。在本发明中,所述al的原子百分比优选为20~25%,所述cr的原子百分比优选为10~15%,所述fe的原子百分比优选为10~15%,所述ti的原子百分比优选为10~15%,所述mo的原子百分比优选为10~15%,所述nb的原子百分比优选为10~15%,所述w的原子百分比优选为10~15%,所述re的原子百分比
优选为4~5%。发明提供的高熵合金具有高硬度和优异的耐磨性,且具有较好的抗氧化性。
35.本发明提供了以上技术方案所述高熵合金的制备方法,包括以下步骤:
36.(1)将al、cr、fe、ti、mo、nb、w和稀土按照高熵合金的组成配比混合后依次进行球磨、过筛和干燥,得到混合金属粉末;
37.(2)将所述混合金属粉末依次进行氢氮还原和退火,得到除氧混合金属粉末;
38.(3)将所述除氧混合金属粉末进行等离子熔覆,得到熔覆层;将所述熔覆层进行退火,得到高熵合金。
39.本发明将al、cr、fe、ti、mo、nb、w和稀土按照高熵合金的组成配比混合后依次进行球磨、过筛和干燥,得到混合金属粉末。在本发明中,所述球磨的转速优选为100~400r/min,更优选为200~300r/min,所述球磨的时间优选为4~12h,更优选为5~10h;所述过筛优选为过100~200目筛;所述干燥优选在真空干燥,所述真空干燥的温度优选为100~200℃。
40.得到混合金属粉末后,本发明将所述混合金属粉末依次进行氢氮还原和退火,得到除氧混合金属粉末。在本发明中,所述氢氮还原的温度优选为300~400℃,时间优选为3~4h;所述氢氮还原中氢气和氮气的体积比优选为1:6~1:19,优选为1:10~1:16;所述氮氢还原优选在钢带式还原炉中进行;通过所述氢氮还原,减少金属粉末的含氧量,提高金属粉末的纯度。在本发明中,所述退火的温度优选为150~250℃,更优选为180~220℃,保温时间优选为2~6h,更优选为2~3h;退火后,随炉冷却;通过所述退火,去除金属粉末的内应力。
41.得到除氧混合金属粉末后,本发明将所述除氧混合金属粉末进行等离子熔覆,得到熔覆层;将所述熔覆层进行退火,得到高熵合金。在本发明中,所述等离子熔覆具体为将所述除氧混合金属粉末置入等离子熔覆送粉器,进行等离子熔覆。在本发明中,所述等离子熔覆优选采用等离子转移弧焊法进行熔覆;所述熔覆的弧电流优选为90~120a,更优选为100~115a;行走速度优选为3~10mm/min,更优选为6mm/min;送粉量优选为30~50%,更优选为35%;离子气流量优选为1.0~2.0l/min,更优选为1.5l/min;保护气体流量优选为10~20l/min,更优选为15l/min;送粉气流量优选为1.5~3.0l/min,更优选为2.5l/min;振幅宽度优选为15~20mm,更优选为16~18mm;搭接率优选为20~25%,更优选为22~24%。在本发明中,所述熔覆优选为多道多层熔覆,熔覆扫描路线如图1所示,n 1层熔覆起点为n层的熔覆终点。在本发明中,所述退火优选在真空条件下进行,所述退火的温度优选为500~700℃,更优选为600℃;通过所述退火,消除熔覆层内应力,提高熔覆层质量。本发明优选将所述高熵合金制备成高熵合金靶材,以备后用;当制备高熵合金靶材时,所述熔覆的熔覆基体优选为钛合金板,所述钛合金板的厚度优选为10~20mm,更优选为15mm;所述熔覆层的长度优选为150~200mm,宽度优选为150~200mm,厚度优选为5~15mm;所退火后,将所述熔覆基体和高熵合金熔覆层利用数控加工成圆柱状的高熵合金靶材;所述圆柱状的直径优选为128mm,高优选为15mm。
42.本发明提供了一种耐磨抗氧化涂层,如图2所示,自下而上,包括依次层叠设置的底层、过渡层和复合层;所述底层为ti层,所述过渡层为tic层;所述复合层为高熵合金和ti2alc的交替叠加层,所述复合层的最下层为高熵合金,最上层为ti2alc,所述高熵合金为以上技术方案所述的高熵合金。在本发明中,所述底层的厚度优选为20~200nm,更优选为
80~120nm;所述底层能够提高基体表面的光洁度,增强基体表面的附着力。在本发明中,所述过渡层的厚度优选为30~400nm,更优选为150~300nm;所述过渡层能够增强膜-基结合力,并阻止后续退火过程中复合涂层和基底之间的元素互扩散。在本发明中,所述高熵合金的单层厚度优选为0.2~0.9μm,更优选为0.3~0.6μm;所述高熵合金的单层厚度与ti2alc的单层厚度之比优选为1:(1~4),更优选为1:(1.5~2.0);所述高熵合金的层数优选为3~11层,更优选为4~9层;所述ti2alc的层数优选为3~11层,更优选为4~9层;所述高熵合金层能够显著提高复合层的耐磨性,所述ti2alc具有良好的抗高温氧化性能;所述高熵合金和ti2alc的交替叠加有利于减少涂层沉积过程中柱状晶的数量,改善涂层的综合性能。在本发明中,所述耐磨抗氧化涂层可以表示为ti/tic/高熵合金
/
ti2alc。本发明提供的涂层具有优异的抗高温氧化性,在常温及高温(1000℃)下均具有良好的耐磨性能,且膜基结合力强。
43.本发明提供了以上技术方案所述耐磨抗氧化涂层的制备方法,包括以下步骤:
44.将基体进行离子束刻蚀,在刻蚀的基体表面自下而上依次沉积ti层和tic层,然后在所述tic层表面交替沉积所述高熵合金和ti2alc,得到涂层预样品;所述沉积ti层、tic层和高熵合金采用电弧离子镀沉积法,所述沉积ti2alc采用磁控溅射沉积法;
45.将所述涂层预样品在保护气氛下进行退火,得到所述耐磨抗氧化涂层。
46.本发明将基体进行离子束刻蚀。在本发明中,所述基体优选为钛合金,所述钛合金优选为tc4钛合金。在进行离子束刻蚀前,本发明优选先将基体依次进行抛光、清洗和干燥;所述清洗优选为分别采用丙酮和酒精进行超声清洗;所述采用丙酮进行超声清洗的时间优选为10~20min,所述采用酒精进行超声清洗的时间优选为10~20min。在本发明中,所述离子束刻蚀优选采用ar离子束,ar气流量优选为40sccm,ar气纯度优选为99.999%以上;所述离子束刻蚀优选在真空度为3.0
×
10-3
pa以下时进行,基底偏压优选为-200~-400v,更优选为-300v,离子源的电流为0.1~0.3a,更优选为0.2a,刻蚀的时间优选为15~40min,更优选为25min。
47.离子束刻蚀后,本发明在刻蚀的基体表面自下而上依次沉积ti层和tic层;所述沉积ti层和tic层采用电弧离子镀沉积法。在本发明中,所述沉积ti层优选以钛靶为靶材,以氩气为工作气体;所述沉积ti层的电弧电流优选为50~100a,更优选为70a;基底偏压优选为-60~-200v,更优选为-120v;工作气压优选为0.6~2.0pa,更优选为1.0~1.2pa;沉积时间优选为5~30min,更优选为10min。在本发明中,所述沉积tic层优选以钛靶为靶材,以ch4为反应气体,以氩气为工作气体,所述ch4的纯度优选为99.999%,流量优选为40~60sccm,更优选为50sccm;所述氩气的流量优选为200sccm。在本发明中,所述沉积tic层的电弧电流优选为50~100a,更优选为70a;基底偏压优选为-80~-150v,更优选为-100~-120v;工作气压优选为3~6pa,更优选为4pa;沉积时间优选为15~35min,更优选为20~30min。
48.沉积ti层和tic层后,本发明在所述tic层表面交替沉积所述高熵合金和ti2alc,得到涂层预样品;所述沉积高熵合金采用电弧离子镀沉积法,所述沉积ti2alc采用磁控溅射沉积法。在本发明中,所述沉积高熵合金以高熵合金为靶材,以氩气为工作气体,所述氩气的流量优选为40~100sccm,更优选为60~80sccm。在本发明中,所述沉积高熵合金的电流优选为60~100a,更优选为80a;基底偏压优选为-80~-300v,更优选为-180~-220v;工作气压优选为0.8~2.0pa,更优选为1.0~1.5pa;单层沉积时间优选为15~30min,更优选
为20min。在本发明中,所述沉积ti2alc以tial合金为靶材,以碳氢反应气为反应气体,以氩气为工作气体;所述氩气的流量优选为100~300sccm,更优选为200sccm;所述碳氢反应气优选为甲烷和/或乙炔,所述碳氢反应气的流量优选为10~30sccm,更优选为15sccm;所述碳氢反应气的流量优选为碳氢反应气和氩气流量之和的5~15%,更优选为6.5~12%。本发明对所述作为靶材的tial合金的来源没有特别的要求,采用市售商品即可。在本发明中,所述沉积ti2alc的电弧电流优选为40~100a,更优选为60a;磁控电流优选为5~10a,更优选为8a;基底偏压优选为-100~-300v,更优选为-200v;工作气压优选为2~5pa,更优选为3.5pa;单层沉积时间优选为20~40min,更优选为30min。在本发明中,所述沉积高熵合金和ti2alc的总沉积时间优选为90~300min,更优选为150~300min。在本发明中,所述交替沉积高熵合金和ti2alc的具体操作优选为:将沉积有ti层和tic层的基体材料置于样品架上,在所述样品架自传的条件下,在所述tic层表面旋转交替沉积高熵合金和ti2alc,得到涂层预样品。
49.得到涂层预样品后,本发明将所述涂层预样品在保护气氛下进行退火,得到所述耐磨抗氧化涂层。在本发明中,所述退火的温度优选为600~900℃,更优选为750~900℃,时间优选为2~24h,更优选为12h;升温至退火的温度的升温速率优选为4~8k/min,更优选为5k/min;所述退火的冷却方式为随炉冷却;所述保护气氛优选为氩气,压强优选为0.1~0.5x103pa,更优选为0.3x103pa。通过所述退火,提高ti2alc层的结晶度,减少薄膜间应力,实现复合涂层定型。
50.下面结合实施例对本发明提供的高熵合金及其制备方法和耐磨抗氧化涂层及其制备方法进行详细的说明,但是不能把它们理解为对本发明保护范围的限定。
51.实施例1
52.(1)高熵合金靶的制备:
53.将al、cr、fe、ti、mo、nb、w和ce按照原子百分比al 25%、cr 11.67%、fe 11.67%、ti 11.67%、mo 11.67%、nb 11.67%、w 11.67%和ce 5%进行配比混合,放入球磨罐中,以300r/min的速度进行8h球磨,用150目筛网过筛,在120℃真空干燥,得到混合金属粉末;
54.将得到的混合金属粉末置于钢带式还原炉进行氢氮还原,还原温度为350℃,还原时间为3.5小时,氢氮混合气体中氢气和氮气的体积比1:16,在温度为200℃的条件下保温3h,然后随炉冷却,得到除氧混合金属粉末;
55.将除氧混合金属粉末利用等离子转移弧焊技术熔覆,弧电流为100a;熔覆行走速度为6mm/min;送粉量为35%;离子气流量为1.5l/min;保护气体流量为15l/min;送粉气流量为2.5l/min;振幅宽度优选为18mm;搭接率为22%;熔覆的方式为多道多层熔覆,熔覆扫描路线见图1所示;熔覆基体为钛合金,厚度为15mm,高熵合金熔覆层的长度为182mm,宽度为154mm,厚度为8.3mm;
56.得到高熵合金熔覆层后,在真空炉内退火,退火温度选择为600℃;最后将熔覆基体和高熵合金熔覆层利用数控机加工成圆柱状状的高熵合金靶。
57.(2)耐磨抗氧化涂层的制备(以tc4钛合金为基体,以ti靶、步骤(1)制备的高熵合金靶作为电弧靶材,以tial合金靶作为磁控溅射靶材):
58.将抛光的基体在丙酮、酒精中分别超声波清洗15min后,在100℃干燥箱中干燥。然后将干燥后的基体悬挂在镀膜室的样品支架上。启动电源,开启真空泵,罗茨泵,将腔体真
空抽至3.0x10-3
pa。首先向真空腔体中通入氩气,氩气流量为40sccm,基体偏压为-300v,离子源的电流为0.2a,利用电离的氩离子对基体进行氩离子轰击25min;
59.采用电弧离子镀技术在预处理后的基体表面沉积ti底层,靶材为ti靶,电弧电流为70a,沉积气体为ar气,工作气压为1.2pa,基底负偏压为-120v,沉积时间为10min,沉积厚度约为115nm;接着再通入ch4,沉积tic过渡层,ar气流量为200sccm,ch4气流量为50sccm,电弧电流为70a,基底偏压为-120v,工作气压为4pa,沉积时间为25min,厚度约为273nm,得到过渡层;
60.采用电弧离子镀和磁控溅射复合技术在过渡层表面旋转交替循环层叠沉积高熵合金层和ti-al-c层(ti2alc层),沉积高熵合金层的靶材为高熵合金靶,沉积气体为氩气,氩气流量为70sccm,弧电流为80a,基底负偏压为-200v,工作气压为1.2pa,单层沉积时间为20min,沉积厚度约为0.57μm;沉积层数为6层;沉积ti-al-c层的靶材为tial合金靶,沉积气体为ar和ch4混合气体,氩气流量为200sccm,ch4气流量为15sccm,电弧电流为60a,磁控电流为8a,基体负偏压为-200v,工作气压为3.5pa,沉积时间为30min,厚度约为0.81μm;沉积层数为6层;得到涂层预样品,总的厚度约为8.61μm。
61.在氩气保护条件下对涂层预样品进行热处理,ar气气压为0.3mpa,退火温度为750℃,退火时间为12h,得到耐磨抗氧化涂层。
62.图3是制备得到的耐磨抗氧化涂层的截面sem形貌。从图3中可以看出,高熵合金单层与ti-al-c层厚度比约为1:1.5。
63.图4是耐磨抗氧化涂层经750℃/12h退火后,涂层表面xrd衍射分析图。从图4中可以看出,退火后复合涂层中ti2alc衍射峰比较强,这说明退火处理后提高了ti-al-c层的结晶度,ti2alc相含量提高较明显,此外,涂层中还存在少量的ti3alc、tic、bcc以及β等物相。
64.图5是耐磨抗氧化涂层在不同磨损试验温度下涂层摩擦系数与时间(s)的关系曲线。从图5中可以看出室温下摩擦系数为0.63,随着温度的升高,摩擦系数稳定在0.45左右,当温度升高至1000℃时,涂层摩擦系数达到0.30。这可能是因为形成稳定的致密的氧化物,提高了涂层耐磨抗氧化能力。
65.耐磨抗氧化涂层的磨损率随温度的变化如图6所示。从图6中可以看出,随着温度升高,复合涂层表现出优异的耐磨性,1000℃时,其磨损率几乎无变化,达到极低1.51
×
10-6
mm3/n
·
mm。
66.耐磨抗氧化涂层在800℃下氧化表面形貌图如图7中(a)所示。从图7中(a)可以看出,高温氧化状态下,复合涂层出现一层致密的氧化物,从而提高涂层的抗氧化性能。
67.耐磨抗氧化涂层随着氧化温度的提升,其氧化增重呈抛物线关系,耐磨抗氧化涂层氧化抛物线速率常数见表1所示。从表1中可知,在800℃时,复合层的氧化抛物线速率常数为2.76
×
10-8
kg2·
m-4
·
s-1
,超过900℃时,其氧化抛物线速率常数提高了一个数量级达到1.54
×
10-7
kg2·
m-4
·
s-1
,但继续升温后,其氧化抛物线速率常数提升变缓,1000℃时仅为8.03
×
10-7
kg2·
m-4
·
s-1
。这说明复合层具有良好的高温抗氧化性能。
68.对比例1
69.对比例1和实施例1的制备方法相同,不同之处在于:采用电弧离子镀技术在过渡层表面只沉积高熵合金层,沉积厚度约为6.75μm。该涂层磨损率随温度变化如图6所示,从图6中可以看出,低中温的磨损率比实施例1略高,但1000℃高温磨损率与实施例1复合涂层
相当,为1.76
×
10-6
mm3/n
·
mm。另外,该涂层在800℃氧化后,表面出现疏松的氧化物,见图7中(b),这说明与实施例1相比,该涂层氧化性能要差得多。该涂层氧化抛物线速率常数见表1所示,从表1中可知,该涂层氧化抛物线速率常数800℃时为3.29
×
10-7
kg2·
m-4
·
s-1
,900℃时为2.61
×
10-6
kg2·
m-4
·
s-1
,1000℃时为3.93
×
10-5
kg2·
m-4
·
s-1
,这也进一步说明该涂层高温抗氧化性能相对较差。
70.对比例2
71.对比例2和实施例1的制备方法相同,不同之处在于:采用电弧离子镀和磁控溅射复合技术在过渡层表面只沉积ti2alc层,沉积厚度约为7.05μm。该涂层磨损率率随温度变化见图6所示,从图6中可以看出,该涂层低中温的磨损率比实施例1和对比例1均高,但1000℃后的高温磨损率与实施例1和对比例1一样达到相同的数量级,为9.87
×
10-6
mm3/n
·
m,这可能是因为高温状态下,该涂层氧化后表面形成了致密坚硬的氧化物提高了其耐磨性。另外,该涂层在800℃氧化后,表面形成致密的氧化物,见图7中(c),这说明该涂层氧化性能较好。该涂层的氧化抛物线速率常数见表1所示,从表1中可知,该涂层氧化抛物线速率常数800℃时为5.06
×
10-8
kg2·
m-4
·
s-1
,900℃时为6.37
×
10-7
kg2·
m-4
·
s-1
,1000℃时为8.91
×
10-7
kg2·
m-4
·
s-1
。
72.表1不同温度下实施例1和对比例1~2涂层的氧化抛物线速率常数
[0073][0074][0075]
实施例2
[0076]
(1)高熵合金靶的制备:将实施例1中的ce替换为la,其余与实施例1相同。
[0077]
(2)耐磨抗氧化涂层的制备:以tc4钛合金为基体,以ti靶,以高熵合金靶作为电弧靶材,以tial合金靶作为磁控溅射靶材。制备方法与实施例1相同,获得ti/tic/高熵合金层/ti2alc复合涂层,该复合涂层的厚度为7.56μm,在1000℃下的磨损率为1.81
×
10-6
mm3/n
·
mm,1000℃下的氧化抛物线速率常数为8.57
×
10-7
kg2·
m-4
·
s-1
。
[0078]
实施例3
[0079]
(1)高熵合金靶的制备:将实施例1中的ce替换为y,其余与实施例1相同。
[0080]
(2)耐磨抗氧化涂层的制备:
[0081]
以tc4钛合金为基体,以ti靶,以高熵合金靶作为电弧靶材,以tial合金靶作为磁控溅射靶材。制备方法与实施例1相同,获得ti/tic/高熵合金层/ti2alc复合涂层,该复合涂层的厚度为7.72μm,在1000℃下的磨损率为1.48
×
10-6
mm3/n
·
mm,1000℃下的氧化抛物
线速率常数为7.86
×
10-7
kg2·
m-4
·
s-1
。
[0082]
由以上实施例可以看出,本发明提供的耐磨抗氧化涂层涂层具有优异的抗高温氧化性,而且在常温及高温(1000℃)下均具有良好的耐磨性能。
[0083]
以上所述仅是本发明的优选实施方式,应当指出,对于本技术领域的普通技术人员来说,在不脱离本发明原理的前提下,还可以做出若干改进和润饰,这些改进和润饰也应视为本发明的保护范围。
再多了解一些
本文用于企业家、创业者技术爱好者查询,结果仅供参考。