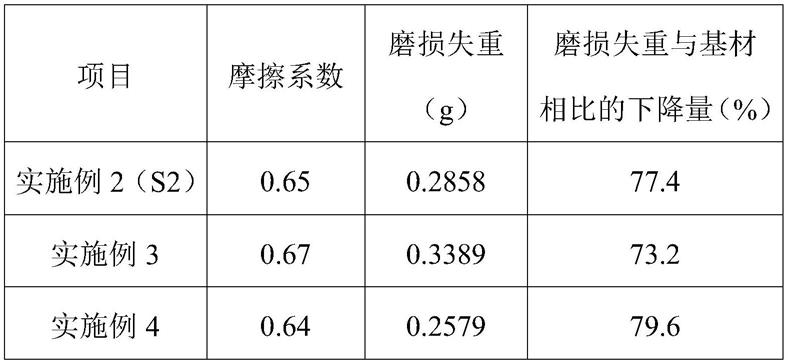
1.本发明属于激光熔覆技术领域,具体涉及一种铁基合金粉末、激光熔覆涂层及其制备方法。
背景技术:
2.激光熔覆是一种新型的表面改性技术,是将高功率密度的激光束作为热源,熔化预置在基材表面的或同步送入的粉末,同时熔化一定的基材表面,经凝固后在基材表面形成具有良好冶金结合的涂层。熔化的金属基材表面形成浅的熔池,粉末材料一般采用预置涂覆于金属基材表面或同步送入的方式进入熔池。熔池及熔化的粉末材料随后冷却凝固后在金属基材表面形成涂层。
3.随着激光技术的发展,激光熔覆技术已被广泛的应用于机械零部件表面的改性。目前煤炭掘进机等重要机械零部件由于复杂的工况条件,对耐磨损和抗腐蚀性能兼具的高性能涂层具有迫切的需求。耐磨损性能需要材料具有较高的强度,通常需要在金属基复合材料中添加一定量的第二相增强颗粒。然而颗粒的添加使得涂层的韧性有所降低,且第二相与基体之间具有一定的物理性质差异,会引起较大的裂纹倾向;同时,第二相颗粒往往与金属基体具有一定的电位差,会形成原电池腐蚀降低材料耐腐蚀性能;第二相颗粒与基体的界面区域也会因为微缺陷、元素偏析等造成材料耐腐蚀性能的恶化。
技术实现要素:
4.本发明的目的在于克服现有技术中的不足,提供一种铁基合金粉末、激光熔覆涂层及其制备方法,采用铁基合金粉末和激光熔覆工艺所形成的激光熔覆涂层能够实现耐磨损、抗腐蚀和抗开裂三种性能的良好平衡。
5.本发明提供了如下的技术方案:
6.第一方面,提供一种铁基合金粉末,由以下质量百分含量的元素组成:c为1.5-3.0%,si为0.5-1.5%,cr为16-18%,ni为1-4%,mo为1-3%,mn为0.2-1%,nb和v总量为0.2-1%,其余为fe。
7.进一步的,由以下质量百分含量的元素组成:c为2.0%,si为0.75%,cr为17%,ni为3%,mo为2%,mn为1%,nb和v总量为1%,其余为fe。
8.进一步的,所述铁基合金粉末的粒径为53-150μm,以保证粉末的流动性获得良好的送进质量。粉末粒径过小则其流动性很差,无法利用同轴送粉方式送进;粉末粒径过大则在送进过程中易飞溅损失。
9.第二方面,提供一种第一方面所述的铁基合金粉末的制备方法,采用气雾化方法制备。
10.第三方面,提供一种激光熔覆涂层的制备方法,包括:采用激光熔覆机,以氩气为保护气,以激光为热源,以锥形粉束方式送粉,控制扫描速度、激光功率和送粉速率,利用激光束产生的热量熔化基材表面和第一方面所述的铁基合金粉末,在基材表面形成单道熔覆
层,重复前述步骤获得多道熔覆层。
11.进一步的,激光熔覆时控制扫描速度为2-7mm/s。
12.进一步的,激光熔覆时控制激光功率为1-5kw。
13.进一步的,激光熔覆时控制送粉速率为10-20g/min。
14.在所述扫描速度、激光功率和送粉速率的参数控制下才能实现良好的涂层成型效果。若扫描速度过小或激光功率过大,则涂层稀释率较高,涂层成分会受到基板成分的污染,记作状况(1);反之,若扫描速度过大或激光功率过小,涂层的层厚较薄,工艺效率较低,甚者会造成涂层与基板未实现冶金结合,记作状况(2)。此外,若送粉速率过低,会造成相对热输入过大,产生与状况(1)相似的问题;若送粉速率过大,会造成粉末的大量浪费,且一定程度会产生状况(2)中的问题。
15.进一步的,单道熔覆层的厚度为1-1.5mm,基材稀释率为3-5%。单道熔覆层的厚度越厚则工艺的效率越高,有利于实际的生产作业,但是单道熔覆厚度增大会增加熔覆层内气孔与裂纹产生的倾向,从而使得涂层性能降低,因此,在熔覆层中不产生缺陷的情况下,单道熔覆层厚度越厚越好。稀释率过高,则基体中的化学元素会进入熔覆层内,使得熔覆层中的化学成分与粉末成分产生偏差,从而影响熔覆层的性能与使用,因此,在熔覆层与基体形成冶金结合的情况下,稀释率越低越好。
16.第四方面,提供一种第三方面所述的方法制备获得的激光熔覆涂层。
17.与现有技术相比,本发明的有益效果是:
18.(1)本发明提供的铁基合金粉末中添加了适量的nb和v,一方面,作为耐火元素nb和v会在共晶组织处偏析,使得共晶反应发生在具有高密度随机堆积结构的多组分合金体系中,有助于液相形成细小共晶,细小的共晶尺寸有助于在强化材料的同时最大幅度保留材料的塑性,可以有效抑制材料在激光熔覆过程中的开裂;另一方面,相较于cr元素,nb和v元素与碳元素具有更高的热力学亲和力,可以部分替代cr元素与碳元素进行反应,从而降低晶界贫cr带来的腐蚀性能恶化;
19.(2)本发明提供的铁基合金粉末中添加了一定含量的si元素和mn元素,在激光熔覆快冷的工艺条件下,si和mn元素在晶界处偏析,可以降低共晶区奥氏体的ms温度,进而降低马氏体转变的驱动力,因此,共晶区马氏体相变的驱动力低于初生凝固奥氏体,残余奥氏体存在于共晶区,残余奥氏体本身作为韧性相一定程度上保持了材料的塑韧性,此外,残余奥氏体存在于第二相与基体的结合区域,在电位和热膨胀系数方面实现了马氏体与第二相间的过渡,减弱了局部电偶腐蚀的倾向,提高了材料的耐腐蚀性能;
20.(3)本发明提供的激光熔覆涂层为马氏体 共晶碳化物 残余奥氏体的涂层组织形式;一方面,利用特殊的合金成分和激光熔覆工艺,获得了传统材料难以获得的m
23
c6型碳化物,保证了涂层的硬度与耐磨损性能,且该类型碳化物本身的韧性较好,与马氏体基体之间的电位差较小,有利于涂层的抗开裂与耐腐蚀性能;另一方面,共晶区域含有少量的残余奥氏体包裹碳化物,保证了涂层具有一定的抗开裂能力,奥氏体在共晶碳化物与马氏体基体间形成电位差过渡,可明显减弱局部原电池的形成趋势;以上理想组织形式使得涂层突破了传统耐磨损性能和耐腐蚀性能难以平衡的技术难题;
21.(4)采用本发明提供的激光熔覆涂层的制备方法,一方面,能够获得较小的基材稀释率(3-5%)和较大的单道熔覆涂层厚度(1-1.5mm),使得实际激光熔覆工艺具有较高的效
率,涂层的铁基合金粉末成分得到了良好的保证,涂层与基材间也实现了紧密的冶金结合;另一方面,使制备出的涂层在拥有高性能的同时,表面与内部没有裂纹、气孔等缺陷。
附图说明
22.图1是实施例2中激光熔覆涂层的横截面宏观形貌图;
23.图2是实施例2中激光熔覆涂层的微观组织形貌图;
24.图3是对比试验例中s1-s4四种激光熔覆涂层的微观金相组织图;
25.图4是对比试验例中s1-s4四种激光熔覆涂层的ebsd相分布图;
26.图5是对比试验例中s1-s4四种激光熔覆涂层和基材的磨损性能图;
27.图6是s4激光熔覆涂层凝固裂纹的ebsd:(a)相图,(b)ipf图,(c)晶界图,(d)kam图;
28.图7是对比试验例中s1-s4四种激光熔覆涂层和基材的耐腐蚀性能图。
具体实施方式
29.下面结合附图对本发明作进一步描述。以下实施例仅用于更加清楚地说明本发明的技术方案,而不能以此来限制本发明的保护范围。
30.实施例1
31.1.制备铁基合金粉末
32.采用气雾化方法制备铁基合金粉末,所述铁基合金粉末由以下质量百分含量的元素组成:c为1.5-3.0%,si为0.5-1.5%,cr为16-18%,ni为1-4%,mo为1-3%,mn为0.2-1%,nb和v总量为0.2-1%,其余为fe。所述铁基合金粉末的粒径为53-150μm。
33.2.制备激光熔覆涂层
34.采用激光熔覆机,以氩气为保护气,以激光为热源,以锥形粉束方式送粉,控制扫描速度为2-7mm/s、激光功率为1-5kw、送粉速率为10-20g/min,利用激光束产生的热量熔化基材表面和步骤1.1中的铁基合金粉末,在基材表面形成单道熔覆层,重复前述步骤获得多道熔覆层,即激光熔覆涂层。其中,单道熔覆层的厚度为1-1.5mm,基材稀释率为3-5%。
35.实施例2
36.1.制备铁基合金粉末
37.具体方法与实施例1中的步骤1相同,区别点在于,所述铁基合金粉末的组成为:c为2.0%、si为0.75%、cr为17%、ni为3%、mo为2%、mn为1%,nb和v总量为1%,其余为fe,铁基合金粉末的粒径为53-150μm。
38.2.制备激光熔覆涂层
39.具体方法与实施例1中的步骤2相同,区别点在于,选用42crmo钢为基板,基板尺寸为200mm
×
80mm
×
20mm,基板表面在熔覆之前用砂轮机打磨,而后用丙酮清洗;选用8kw高功率半导体激光熔覆系统(laserline ldf-8000),控制扫描速度4mm/s,激光功率2kw,送粉速率约12g/min,获得两道熔覆层的激光熔覆涂层。
40.如图1所示,本实施例获得的激光熔覆涂层厚度在3mm左右,涂层内无裂纹、气孔、夹杂等缺陷,涂层与基体之间结合良好。此外,经测定基材稀释率为3.7%,涂层的硬度为59hrc。
41.如图2所示,本实施例获得的激光熔覆涂层的微观组织为马氏体 共晶碳化物 残余奥氏体的组织形式,能够实现耐磨损、抗腐蚀和抗开裂三种性能的良好平衡。
42.实施例3
43.1.制备铁基合金粉末
44.具体方法与实施例2中的步骤1相同,区别点在于,所述铁基合金粉末的组成为:c为1.5%、si为1.5%、cr为16%、ni为4%、mo为3%、mn为1%,nb和v总量为0.2%,其余为fe,铁基合金粉末的粒径为53-150μm。
45.2.制备激光熔覆涂层
46.具体方法与实施例2中的步骤2相同,区别点在于,激光熔覆时控制扫描速度6mm/s,激光功率3kw,送粉速率约15g/min,获得单道熔覆层的激光熔覆涂层,涂层厚度为1.2mm,基材稀释率为2.1%,涂层的硬度为55hrc。
47.实施例4
48.1.制备铁基合金粉末
49.具体方法与实施例2中的步骤1相同,区别点在于,所述铁基合金粉末的组成为:c为3.0%、si为0.5%、cr为18%、ni为1%、mo为1%、mn为0.2%,nb和v总量为1%,其余为fe,铁基合金粉末的粒径为53-150μm。
50.2.制备激光熔覆涂层
51.具体方法与实施例2中的步骤2相同,区别点在于,激光熔覆时控制扫描速度2mm/s,激光功率1kw,送粉速率约10g/min,获得单道熔覆层的激光熔覆涂层,涂层厚度为1.0mm,基材稀释率为4.8%,涂层的硬度为61hrc。
52.对比试验例
53.取两种国产商用粉末以及一种进口粉末作为对比合金粉末,对比合金粉末采用实施例2步骤2的方法制备激光熔覆涂层,分别记为s1、s3和s4,将实施例2制备的激光熔覆涂层记为s2。
54.一、涂层微观组织比较
55.如图3所示为四种激光熔覆涂层的金相组织,根据结果可以看出,四种铁基合金粉末的激光熔覆涂层均得到了马氏体 碳化物第二相的微观组织形式,熔覆层组织均呈现出典型的树枝晶特征,但在碳化物的含量以及涂层晶粒尺寸大小方面具有一定的差异。相比较而言,s2激光熔覆涂层的晶粒最为细小,碳化物含量也较高。
56.如图4所示,利用ebsd技术进一步对四种涂层的微观组织进行表征分析。其中黑色区域代表马氏体组织,浅灰色区域代表残余奥氏体,深灰色区域代表碳化物硬质相。从图中可以看出,几种激光熔覆涂层均呈现出明显的马氏体组织特征,从而使涂层整体具有较高的硬度和耐磨损性能;残余奥氏体和碳化物相主要倾向于分布在涂层组织的晶界区域,残余奥氏体的存在可以有效调控马氏体组织的塑韧性,使得涂层在具有较高硬度的同时,保有一定的抗开裂能力;碳化物作为硬质相,其作用主要是提升涂层的硬度和耐磨损性能。具体来看,在s1涂层中晶界残余奥氏体的含量较高而碳化物的含量相对较低,该涂层的塑韧性和抗开裂能力最好,但由于较低的碳化物含量,硬度和耐磨损性能会有所不足。在s4涂层中,晶界几乎完全为碳化物,该涂层具有很高的硬度和耐磨损性能,但残余奥氏体的缺失使得该涂层的塑韧性和抗开裂能力较差。在s3涂层中,晶界碳化物的含量依然很高,使得该涂
层的塑韧性和抗开裂能力仍然是有所不足的。而在s2涂层中,晶界处的残余奥氏体和碳化物含量实现了较好的平衡,该涂层具有综合良好的抗开裂能力和耐磨损性能。
57.二、耐磨损性能比较
58.选用刚玉陶瓷为摩擦副对实施例2-4、3个对比例和42crmo基材进行摩擦磨损试验,试验载荷50n,转速200rpm,试验时间为60min。
59.表1各激光熔覆涂层和基材的摩擦系数和磨损失重数据
[0060][0061][0062]
表1为各激光熔覆涂层和42crmo基材的摩擦系数和磨损失重数据,图5为s1-s4四种涂层和42crmo基材的摩擦系数和磨损失重量比较图。由表1和图5可知,六种涂层的耐磨损性能均明显好于42crmo基材,涂层耐磨损性能显著高于基板的主要原因在于其硬度的大幅提升。其中s4涂层的耐磨性最好,但在s4涂层中极易产生凝固裂纹(如图6所示),尽管其磨损性能较好但并不是适宜的涂层材料,产生凝固裂纹主要与凝固区间的凝固范围和低熔点共晶的含量有关,由于凝固区较宽,凝固过程较慢,有利于形成大量枝晶,枝晶生长形成网状,阻碍了液态金属的流动,易导致凝固裂纹;同时与s1、s2和s3涂层相比,s4涂层中的低熔点共晶含量较高,而低熔点共晶的存在是导致凝固裂纹的重要原因之一。而s2和s3涂层的耐磨性要略高于s1。s2涂层和s3涂层相比,具有略低的磨损量和略高的摩擦系数,实施例3、4和实施例2(s2)性能类似,而工程应用中磨损量指标更为重要,因此认为实施例3-4涂层的耐磨损性能相对较好。
[0063]
三、耐腐蚀性能比较
[0064]
对实施例2-4、3个对比例和42crmo基材进行中性盐雾试验,选用2.5%的nacl溶液,试验总时长为1500小时。
[0065]
表2各激光熔覆涂层和基材的腐蚀量
[0066][0067]
表2为各激光熔覆涂层和42crmo基材的腐蚀量,图7为s1-s4四种涂层和42crmo基材腐蚀失重量比较图。由表2和图7可知,实施例2(s2)、实施例3和实施例4具有较小的腐蚀失重量,而42crmo基材具有最大的腐蚀失重量。从该数据来讲,本发明提供的铁剂合金粉末较现有商用粉末的耐腐蚀性能具有明显提升。
[0068]
以上所述仅是本发明的优选实施方式,应当指出,对于本技术领域的普通技术人员来说,在不脱离本发明技术原理的前提下,还可以做出若干改进和变形,这些改进和变形也应视为本发明的保护范围。
再多了解一些
本文用于企业家、创业者技术爱好者查询,结果仅供参考。