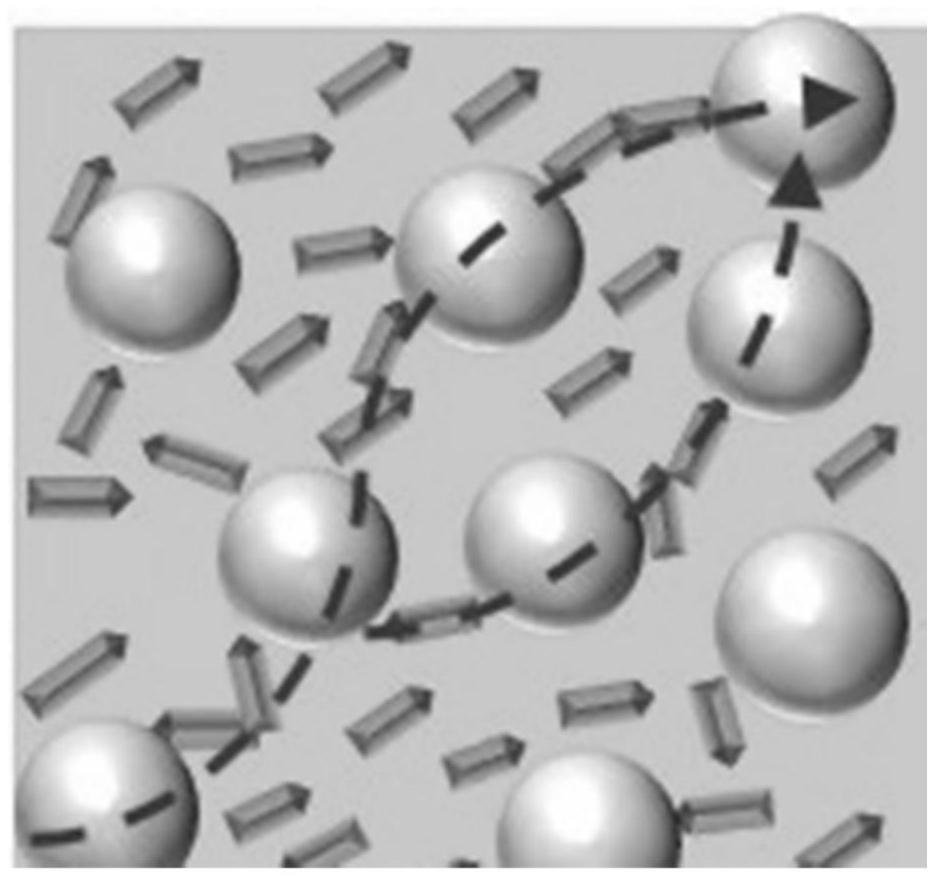
1.本发明属于电子封装材料领域,尤其涉及热界面材料的设计及制备。
背景技术:
2.随着电子器件向高集成化、小型化的快速发展,存在大量的热积累,导致系统过热,进一步降低器件的使用寿命。利用高导热性的绝缘材料提高电子器件的散热能力是目前一种潜在的途径。环氧树脂是一种常用的封装材料,它具有重量轻、适应性强、耐疲劳、耐腐蚀、电气绝缘性能好等优点。但与金属和陶瓷相比,环氧树脂的导热系数较低,约为0.3wm-1
k-1
,不能满足高散热的需要。在这种情况下,陶瓷材料填充环氧基体是一种更有前途的方法。
3.氧化铝(al2o3)由于其优异的介电性能和特别低的成本,被认为是应用最广泛的导热填料之一。但其本征热导率低(~30w-1
k-1
),而且填充的固体含量过高时,粉体分散不均匀,这限制了其作为单一填料的广泛应用。研究表明,复合材料中两种填料的结合可以使最终材料具有互补或定制的性能。有文献报道,yk kim等人采用al2o3球与bn纳米片的杂化提高了单球形al2o3颗粒在环氧基体中的导热能力,导热系数达到3.6wm-1
k-1
,但其使用bn纳米颗粒容易聚集,而且价格较昂贵。氮化硅作为一种结构陶瓷材料,具有高导热性、抗氧化性、低热膨胀系数和高弯曲强度等优异的综合物理性能,这使得它作为一种高导热填料受到了特别的关注,如t kusunose等人采用氮化硅纳米线提高了环氧树脂的热导率,但是原料氮化硅纳米线成本高,需要严格工艺控制;如cn1935926a中提及采用β-si3n4粉体或β-si3n4与氧化硅、氧化铝、氮化铝、氮化硼等陶瓷混合粉体作为填料粉加入环氧树脂来制备高热导电子封装材料,得到高热导率材料,但是材料中所用的β相氮化硅的粒径范围跨度太大,容易造成分散不均匀的问题,而且β相氮化硅与氧化铝粉体混合后未提高材料的热导率,协同作用未显现出来,因此未达到混合填料的目的。
技术实现要素:
4.本发明提供一种具有热导网络的β-si3n4/al2o3/环氧树脂热界面材料,利用球形al2o3和β-si3n4在环氧树脂中协同作用,降低填料的用量,构建导热网络,提高热导率。
5.本发明提供技术方案如下:
6.一种具有热导网络的热界面材料,其特征在于,所述热界面材料包括β-si3n4、al2o3、环氧树脂,其中,所述热导网络由al2o3球形颗粒和β-si3n4颗粒构成,al2o3球形颗粒均匀分散于环氧树脂中,构成热导网络的热导位点;β-si3n4颗粒均匀分散在相邻al2o3球形颗粒中,构成热导网络的热导流向;两个相邻al2o3球形颗粒中平均分布2到20个β-si3n4颗粒。
7.优选的,所述al2o3球形颗粒为微米级,优选直径为70-120μm之间,优选为120μm。
8.优选的,所述β-si3n4颗粒为棒状,优选粒径在10-25μm之间,优选为18μm。
9.优选的,所述β-si3n4与所述球形al2o3按照m(β-si3n4)/m(al2o3)=0.5-0.75的
比率加入环氧树脂中。
10.优选的,所述热界面材料中β-si3n4与al2o3混合物的固相含量为20-52.5vol%。
11.优选的,所述热界面材料中环氧树脂的含量为30.7-55.5vol%。
12.提供一种具有热导网络的热界面材料的制备工艺,包括如下步骤:
13.1)制备环氧基体:在环氧树脂中加入偶联剂和触变剂,制备环氧树脂基体;
14.2)β-si3n4和al2o3分散在环氧树脂基体中:将β-si3n4和球形al2o3粉末进行干燥预处理;将预处理后的β-si3n4和al2o3混合物通过重力混合法分散在环氧树脂基体中,得到混合液;
15.3)固化反应:将固化剂加入到混合液中得到固化混合液;将固化混合液置于硅胶模具中,在室温下固化5-24h,40℃下固化2-6h,即得到具有热导网络的热界面材料。
16.优选的,β-si3n4和al2o3混合物在步骤3)中所述固化混合液的体积占比为20-52.5vol%;环氧树脂在所述固化混合液体积占比为30.7-55.5vol%;偶联剂在所述固化混合液体积占比为1.4-3.6vol%;触变剂在所述固化混合液体积占比为0.2-0.4vol%;固化剂在所述的固化混合液体积占比为12.7-22.6vol%。
17.优选的,步骤2)中β-si3n4和al2o3混合物中β-si3n4和al2o3的比例为m(β-si3n4)/m(al2o3)=0.5-0.75。
18.优选的,步骤2)中重力混合法优选自转速度为1500-2000rpm,公转速度为750-1200rpm,混合时间为2-10min。
19.优选的,按照环氧树脂与固化剂的质量比为3:1的比例加入固化剂。
20.优选的,所述环氧树脂选自双酚a环氧树脂、双酚f型环氧树脂;偶联剂选自kh550、kh560、kh570。
21.优选的,所述al2o3球形颗粒为微米级,优选直径为70-120μm之间,更优选为120μm。
22.优选的,所述β-si3n4颗粒为棒状,优选粒径在10-25μm之间,更优选为18μm。
23.本发明的有益效果:
24.本发明采用球形al2o3和β-si3n4在环氧基体中协同作用,一方面提高了填料的固含量,另一方面也促进了导热网络的形成,如图1所示,球形al2o3均匀分散在环氧基体中,颗粒间距大约为20-80μm,而相对较小尺寸的β-si3n4颗粒均匀地分布在相邻的al2o3球之间,填充了球形al2o3颗粒之间的间隙,起到了连接球形氧化铝颗粒的“桥梁”作用,使得两个相邻al2o3球形颗粒中平均分布2到20个β-si3n4颗粒,从而减小了al2o3颗粒之间的界面热阻,最终提高了热导率,最高热导率高达2.2wm-1
k-1
,比纯环氧高约898%。
25.同时,研究发现,具有热导网络的β-si3n
4/
al2o3/环氧树脂复合材料的介电常数随着固含量的增加而增加,但增加幅度不大,与纯环氧树脂的介电常数接近,大致为6.5;此外,复合材料的介电损耗大约在10-2-10-3
之间。
26.因此,本发明制备得到的具有热导网络的β-si3n4/al2o3/环氧树脂热界面材料在保持绝缘性的同时,具有较高的热导率,能够用于电子设备的散热。而且原料成本低、工艺简单易操作,有利于工业化生产。
附图说明
27.图1.本发明制备的热界面材料的断裂形貌图;
28.图2.本发明制备的热界面材料的热导网络示意图;
29.图3.(a)β-si3n4和al2o3混合物填充量为40vol%时,不同的β-si3n
4 al2o3质量比例的复合材料的热导变化图;(b)β-si3n4/al2o3质量比为3/4时,不同β-si3n4/al2o3混合物固含量的热界面材料的热导率变化图;
30.图4.不同固含量的热界面材料的介电常数和介电损耗。
具体实施方式
31.实施例1
32.首先,组内自制的长径18μm的棒状β-si3n4和商用120μm的球形al2o3粉末放入真空烘箱去除多余水分;然后,在占总体积的40.4vol%的双酚f型环氧树脂中加入2.7vol%偶联剂kh560和触变剂酰胺蜡0.3vol%制备环氧树脂基体;将已烘干的体积分数为40vol%的β-si3n4和球形al2o3混合物按照m(β-si3n4)/m(al2o3)=3/4的比率,通过重力混合法分散在环氧基体中,混合物以2000rpm的自转速度、1000rpm的公转速度混合10min;之后,将16.0vol%的固化剂聚醚胺d230和0.6vol%的促进剂2,4,6-三(二甲胺基甲基)苯酚(dmp-30)加入到混合液中;最后,将混合料倒入硅胶模具,室温固化8h,40℃后固化2h,即得到β-si3n4/al2o3/环氧树脂复合材料,热导率为0.97wm-1
k-1
。从断裂形貌看,球形al2o3均匀分散在环氧基体中,颗粒间距大约为40μm,而相对较小尺寸的β-si3n4颗粒均匀地分布在相邻的al2o3球之间,两个相邻al2o3球形颗粒中平均分布10个β-si3n4颗粒,填充了球形al2o3颗粒之间的间隙,起到了连接球形氧化铝颗粒的“桥梁”作用。
33.实施例2
34.首先,组内自制的10μm的棒状β-si3n4和商用80μm的球形al2o3粉末放入真空烘箱去除多余水分;然后,在40.4vol%环氧树脂中加入2.7vol%偶联剂kh560和0.3vol%触变剂酰胺蜡制备环氧树脂基体;将已烘干的体积分数为40vol%的β-si3n4和球形al2o3混合物按照m(β-si3n4)/m(al2o3)=1/2的比率,通过重力混合法分散在环氧基体中,混合物以1500rpm的自转速度、1000rpm的公转速度混合10min;之后,将总计16.6vol%的固化剂聚酰胺加入到混合液中;最后,将混合料倒入硅胶模具,室温固化16h,40℃后固化2h,即得到β-si3n4/al2o3/环氧树脂复合材料,热导率为0.8wm-1
k-1
。断裂形貌看,球形al2o3均匀分散在环氧基体中,颗粒间距大约为50μm,两个相邻al2o3球形颗粒中平均分布15个β-si3n4颗粒。
35.实施例3
36.首先,组内自制的18μm的棒状β-si3n4和商用100μm的球形al2o3粉末放入真空烘箱去除多余水分;然后,在40.4vol%环氧树脂中加入2.7vol%偶联剂和0.3vol%触变剂酰胺蜡制备环氧树脂基体;将已烘干的体积分数为40vol%的β-si3n4和球形al2o3混合物按照m(β-si3n4)/m(al2o3)=2/3的比率,通过重力混合法分散在环氧基体中,混合物以2000rpm的自转速度、1000rpm的公转速度混合10min;之后,将总计16.6vol%的固化剂聚酰胺加入到混合液中;最后,将混合料倒入硅胶模具,室温固化10h,40℃后固化3h,即得到β-si3n4/al2o3/环氧树脂复合材料,热导率为0.91wm-1
k-1
。断裂形貌看,球形al2o3均匀分散在环氧基体中,颗粒间距大约为45μm,两个相邻al2o3球形颗粒中平均分布13个β-si3n4颗粒。
37.实施例4
38.首先,组内自制的25μm的棒状β-si3n4和商用120μm的球形al2o3粉末放入真空烘箱
去除多余水分;然后,在30.9vol%的环氧树脂中加入3.6vol%偶联剂kh560和0.4vol%触变剂酰胺蜡制备环氧树脂基体;将已烘干的体积分数为52.5vol%的β-si3n4和球形al2o3混合物按照m(β-si3n4)/m(al2o3)=3/4的比率,通过重力混合法分散在环氧基体中,混合物以2000rpm的自转速度、750rpm的公转速度混合2min;之后,将总计12.6vol%的固化剂聚酰胺加入到混合液中;最后,将混合料倒入硅胶模具,室温固化8h,40℃后固化6h,即得到β-si3n4/al2o3/环氧树脂复合材料,热导率为2.2wm-1
k-1
。断裂形貌看,球形al2o3均匀分散在环氧基体中,颗粒间距大约为20μm,两个相邻al2o3球形颗粒中平均分布20个β-si3n4颗粒。
39.实施例5
40.首先,组内自制的18μm的棒状β-si3n4和商用120μm的球形al2o3粉末放入真空烘箱去除多余水分;然后,在48vol%环氧树脂中加入2vol%偶联剂kh560和0.3vol%触变剂酰胺蜡制备环氧树脂基体;将已烘干的体积分数为30.1vol%的β-si3n4和球形al2o3混合物按照m(β-si3n4)/m(al2o3)=3/4的比率,通过重力混合法分散在环氧基体中,混合物以2000rpm的自转速度、1000rpm的公转速度混合8min;之后,将19.1vol%的固化剂聚醚胺d230和0.6vol%的促进剂2,4,6-三(二甲胺基甲基)苯酚(dmp-30)加入到混合液中;最后,将混合料倒入硅胶模具,室温固化8h,40℃后固化2h,即得到低固含量β-si3n4/al2o3/环氧树脂复合材料,热导率为0.82wm-1
k-1
。断裂形貌看,球形al2o3均匀分散在环氧基体中,颗粒间距大约为50μm,两个相邻al2o3球形颗粒中平均分布11个β-si3n4颗粒。
41.实施例6
42.首先,组内自制的18μm的棒状β-si3n4和商用70μm的球形al2o3粉末放入真空烘箱去除多余水分;然后,在55.5vol%环氧树脂中加入1.4vol%偶联剂kh560和0.2vol%触变剂酰胺蜡制备环氧树脂基体;将已烘干的体积分数为20.1vol%的β-si3n4和球形al2o3混合物按照m(β-si3n4)/m(al2o3)=3/4的比率,通过重力混合法分散在环氧基体中,混合物以2000rpm的自转速度、1000rpm的公转速度混合5min;之后,将22.0vol%的固化剂聚醚胺d230和0.6vol%的促进剂2,4,6-三(二甲胺基甲基)苯酚(dmp-30)加入到混合液中;最后,将混合料倒入硅胶模具,室温固化24h,40℃后固化2h,即得到β-si3n4/al2o3/环氧树脂复合材料,热导率为0.76wm-1
k-1
。断裂形貌看,球形al2o3均匀分散在环氧基体中,颗粒间距大约为80μm,两个相邻al2o3球形颗粒中平均分布2个β-si3n4颗粒。
43.实施例7
44.首先,将商用120μm的球形al2o3粉末放入真空烘箱去除多余水分;然后,在39.9vol%环氧树脂中加入2.95vol%偶联剂kh560和0.35vol%触变剂酰胺蜡制备环氧树脂基体;将已烘干的40.5vol%的球形al2o3混合物通过重力混合法分散在环氧基体中,混合物以~2000rpm的自转速度、~1000rpm的公转速度混合10min;之后,将总计16.3vol%的固化剂聚酰胺加入到混合液中;最后,将混合料倒入硅胶模具,室温固化8h,40℃后固化2h,即得到al2o3/环氧树脂复合材料,热导率为0.55wm-1
k-1
。
再多了解一些
本文用于企业家、创业者技术爱好者查询,结果仅供参考。