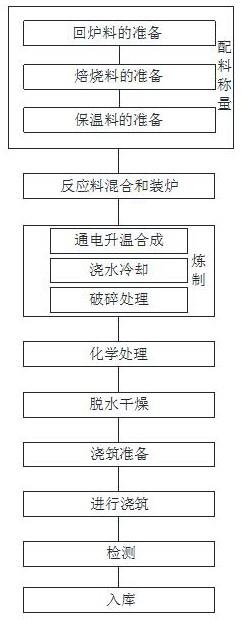
1.本技术涉及碳化硅陶瓷生产技术领域,尤其涉及一种碳化硅陶瓷真空浇筑工艺。
背景技术:
2.碳化硅陶瓷,具有抗氧化性强,耐磨性能好,硬度高,热稳定性好,高温强度大,热膨胀系数小,热导率大以及抗热震和耐化学腐蚀等优良特性。因此,已经在石油、化工、机械、航天、核能等领域大显身手,日益受到人们的重视,例如,sic陶瓷可用作各类轴承、滚珠、喷嘴、密封件、切削工具、燃汽涡轮机叶片、涡轮增压器转子、反射屏和火箭燃烧室内衬等等,真空浇注技术是指环氧树脂浇注从常压成型发展为真空成型。真空浇注成型使浇注料中的气泡可以更容易的排出,制品的内在质量和外观质量都得到较大提高,从而推动了输变电技术的发展,但这个时期用户的关注焦点主要是内在性能,而不太关注外观质量;如中国专利公开了: 一种碳化硅陶瓷,公开号:cn100497254c,兼顾利用热膨胀失配诱发微裂纹、裂纹偏转、裂纹桥联、拔出效应以及晶粒细化等有益的增韧因素;常见的碳化硅真空浇筑生产时存在铁铝镁杂质残留,影响成品质量,因此提出一种碳化硅陶瓷真空浇筑工艺。
技术实现要素:
3.本发明的目的在于提供一种碳化硅陶瓷真空浇筑工艺,以解决上述背景技术中提出的问题。
4.本技术实施例采用下述技术方案:一种碳化硅陶瓷真空浇筑工艺,包括s1:配料称量;碳化硅是一种无机物,化学式为sic,是用石英砂、石油焦、木屑和食盐作为原料通过电阻炉高温冶炼而成,碳化硅化学性能稳定、导热系数高、热膨胀系数小、耐磨性能好,sic陶瓷的优异性能与其独特结构密切相关。sic是共价键很强的化合物,sic中 si-c键的离子性仅12%左右,因此sic强度高、弹性模量大,具有优良的耐磨损性能,纯 sic不会被hci、hno3、h2so4和 hf等酸溶液以及naoh等碱溶液侵蚀,在空气中加热时易发生氧化,但氧化时表面形成的sio2会抑制氧的进一步扩散,故氧化速率并不高,在电性能方面,sic具有半导体性,少量杂质的引入会表现出良好的导电性,此外,sic还有优良的导热性,sic具有α和β两种晶型,β-sic的晶体结构为立方晶系,si和c分别组成面心立方晶格;α-sic存在着4h、15r和6h等100余种多型体,其中,6h多型体为工业应用上最为普遍的一种,在sic的多种型体之间存在着一定的热稳定性关系。在温度低于1600℃时,sic 以β-sic形式存在。当高于1600℃时,β-sic缓慢转变成α-sic的各种多型体,4h-sic在2000℃左右容易生成;15r和 6h多型体均需在2100℃以上的高温才易生成;对于6h-sic,即使温度超过2200℃,也是非常稳定的,sic中各种多型体之间的自由能相差很小,因此,微量杂质的固溶也会引起多型体之间的热稳定关系变化,碳化硅反应公式为sio2 3csic 2co,原料中的石英砂sio2纯度>99.5%,无烟煤的挥发量《4%,碳化硅冶炼炉的炉子功率为10000kw,每1kg的 sic电耗为6-7kw
·
h,生产周期升温时为26~36h,合成工艺中
配料的计算方程式为m=c/(c+sio2)
×
100,其中c为碳含量,sio2为二氧化硅含量,m=37.5,碳的加入量允许过量5%,加入食盐的目的是为了排除原料的铁、铝等杂质,加人木屑是便于排除生成的一氧化碳;s2:反应料混合和装炉;在炉底先铺上一层未反应料,然后添加新配料到约炉芯到炉底的二分之一高度,在其上面铺一层非晶形料,然后继续加配料至炉芯水平,炉芯放在配料制成的底盘上,中间略凸起以适应在炉役过程中出现的塌陷,炉芯上部铺放混好的配料,炉芯上部铺放混好的配料同时也放非品质料或生产未反应料,炉子装好后形成中间高、两边低的状态;s3:炼制;炉子装好后即可通电合成,以电流电压强度来控制反应过程,当炉温升到1600℃时,开始生成β-sic,从、2000℃开始转化成α-sic,2500℃全部转化成a-sic,合成时间为26~36h,冷却24h后可以浇水冷却,出炉后分层、分级拣选;s4:化学处理;先进行硫酸酸洗,除去合成料中的含铁、铝、钙和镁杂质,在沉淀池沉淀,沉淀后的污水进行污水中和后排出,最后进行沉渣处理,沉渣进行水洗过筛后重新作为保温料进行二次炼制;s5:脱水干燥;控制水分为2%~3%;s6:浇筑准备;第一步进行材料的预热和计量,第二步嵌件,进行预处理,嵌件涂覆粘结剂或半导电橡胶,第三步脱气,填料抽空干燥,固态环氧树脂熔化抽真空,固化剂抽真空,先将填料和环氧树脂一次混合抽真空,然后与固化剂混合;s7:进行浇筑,先进行前固化,浇注料在固化炉中固化成型,固化度至80%以上,第二步进行脱模装模,保持适当温度将产品卸模并快速装入下一模,第三步为后固化,脱模后的产品集中固化,提高固化度,释放内应力,第四步为后处理,清理产品浇口,合模缝及其它缺陷;s8:检测;质量检测,检测成品表面是否存在气孔、缩孔缩痕、裂纹和杂质,然后进行问题溯源和修正,气孔会影响碳化硅陶瓷的局部电场分布,缩孔缩痕会导致产品表面不光滑,裂纹会影响制品的耐电压和局部放电性能、力学性能,如果外表存在裂纹,内部可能会存在隐患,接线端子板类产品可能会产生气体泄露,由此说明,外观质量缺陷不只是外观质量差,且在一定程度上会影响到整机的性能,需要引起足够的重视,杂质的存在会影响电性能,实验表明密集或者大粒径的杂质会导致制品表面放电,局放增大。
5.优选的s101:回炉料的准备,sic>75%,sio2 si<15%,固定碳<6%,杂质<4%;s102:焙烧料的准备,焙烧料包括焦炭、木屑和食盐,以100t计,焦炭0~45kg,木屑35~55l,食盐3%~5%;s103:保温料的准备,保温料的焦炭与石英比为0.6;优选的,s301:通电升温合成;s302:浇水冷却;s303:破碎处理。
6.本技术实施例采用的上述至少一个技术方案能够达到以下有益效果:其一,在炉底先铺上一层未反应料,然后添加新配料到约炉芯到炉底的二分之一高度,在其上面铺一层非晶形料,然后继续加配料至炉芯水平,炉芯放在配料制成的底盘上,中间略凸起以适应在炉役过程中出现的塌陷,炉芯上部铺放混好的配料,炉芯上部铺放
混好的配料同时也放非品质料或生产未反应料,炉子装好后形成中间高、两边低的状态,提高炉内反应效果;其二,炉子装好后即可通电合成,以电流电压强度来控制反应过程,当炉温升到1600℃时,开始生成β-sic,从、2000℃开始转化成α-sic,2500℃全部转化成a-sic,合成时间为26~36h,冷却24h后可以浇水冷却,出炉后分层、分级拣选,经过通电升温、浇水冷却和破碎处理后,以去除铁铝钙镁杂质,提高质量;其三,破碎处理后的物料,先进行硫酸酸洗,除去合成料中的含铁、铝、钙和镁杂质,在沉淀池沉淀,沉淀后的污水进行污水中和后排出,最后进行沉渣处理,沉渣进行水洗过筛后重新作为保温料进行二次炼制,减小了浪费量;其四,进行浇筑时,先进行前固化,浇注料在固化炉中固化成型,固化度至80%以上,第二步进行脱模装模,保持适当温度将产品卸模并快速装入下一模,第三步为后固化,脱模后的产品集中固化,提高固化度,释放内应力,第四步为后处理,清理产品浇口,合模缝及其它缺陷。
附图说明
7.此处所说明的附图用来提供对本技术的进一步理解,构成本技术的一部分,本技术的示意性实施例及其说明用于解释本技术,并不构成对本技术的不当限定。在附图中:图1为本发明的整体流程示意图。
具体实施方式
8.为使本技术的目的、技术方案和优点更加清楚,下面将结合本技术具体实施例及相应的附图对本技术技术方案进行清楚、完整地描述。显然,所描述的实施例仅是本技术一部分实施例,而不是全部的实施例。基于本技术中的实施例,本领域普通技术人员在没有做出创造性劳动前提下所获得的所有其他实施例,都属于本技术保护的范围。
9.以下结合附图,详细说明本技术各实施例提供的技术方案。
10.请参阅图1,一种碳化硅陶瓷真空浇筑工艺,包括以下步骤:s1:配料称量;碳化硅是一种无机物,化学式为sic,是用石英砂、石油焦、木屑和食盐作为原料通过电阻炉高温冶炼而成,碳化硅化学性能稳定、导热系数高、热膨胀系数小、耐磨性能好,sic陶瓷的优异性能与其独特结构密切相关。sic是共价键很强的化合物,sic中 si-c键的离子性仅12%左右,因此sic强度高、弹性模量大,具有优良的耐磨损性能,纯 sic不会被hci、hno3、h2so4和 hf等酸溶液以及naoh等碱溶液侵蚀,在空气中加热时易发生氧化,但氧化时表面形成的sio2会抑制氧的进一步扩散,故氧化速率并不高,在电性能方面,sic具有半导体性,少量杂质的引入会表现出良好的导电性,此外,sic还有优良的导热性,sic具有α和β两种晶型,β-sic的晶体结构为立方晶系,si和c分别组成面心立方晶格;α-sic存在着4h、15r和6h等100余种多型体,其中,6h多型体为工业应用上最为普遍的一种,在sic的多种型体之间存在着一定的热稳定性关系。在温度低于1600℃时,sic 以β-sic形式存在。当高于1600℃时,β-sic缓慢转变成α-sic的各种多型体,4h-sic在2000℃左右容易生成;15r和 6h多型体均需在2100℃以上的高温才易生成;对于6h-sic,即使温度超过2200℃,也是非常稳定的,sic中各种多型体之间的自由能相差很小,因此,微量杂质的固溶也会
引起多型体之间的热稳定关系变化,碳化硅反应公式为sio2 3csic 2co,原料中的石英砂sio2纯度>99.5%,无烟煤的挥发量《4%,碳化硅冶炼炉的炉子功率为10000kw,每1kg的 sic电耗为6-7kw
·
h,生产周期升温时为26~36h,合成工艺中配料的计算方程式为m=c/(c+sio2)
×
100,其中c为碳含量,sio2为二氧化硅含量,m=37.5,碳的加入量允许过量5%,加入食盐的目的是为了排除原料的铁、铝等杂质,加人木屑是便于排除生成的一氧化碳;s101:回炉料的准备,sic>75%,sio2 si<15%,固定碳<6%,杂质<4%;s102:焙烧料的准备,焙烧料包括焦炭、木屑和食盐,以100t计,焦炭0~45kg,木屑35~55l,食盐3%~5%;s103:保温料的准备,保温料的焦炭与石英比为0.6;s2:反应料混合和装炉;在炉底先铺上一层未反应料,然后添加新配料到约炉芯到炉底的二分之一高度,在其上面铺一层非晶形料,然后继续加配料至炉芯水平,炉芯放在配料制成的底盘上,中间略凸起以适应在炉役过程中出现的塌陷,炉芯上部铺放混好的配料,炉芯上部铺放混好的配料同时也放非品质料或生产未反应料,炉子装好后形成中间高、两边低的状态;s3:炼制;炉子装好后即可通电合成,以电流电压强度来控制反应过程,当炉温升到1600℃时,开始生成β-sic,从、2000℃开始转化成α-sic,2500℃全部转化成a-sic,合成时间为26~36h,冷却24h后可以浇水冷却,出炉后分层、分级拣选;s301:通电升温合成;s302:浇水冷却;s303:破碎处理;s4:化学处理;先进行硫酸酸洗,除去合成料中的含铁、铝、钙和镁杂质,在沉淀池沉淀,沉淀后的污水进行污水中和后排出,最后进行沉渣处理,沉渣进行水洗过筛后重新作为保温料进行二次炼制;s5:脱水干燥;控制水分为2%~3%;s6:浇筑准备;第一步进行材料的预热和计量,第二步嵌件,进行预处理,嵌件涂覆粘结剂或半导电橡胶,第三步脱气,填料抽空干燥,固态环氧树脂熔化抽真空,固化剂抽真空,先将填料和环氧树脂一次混合抽真空,然后与固化剂混合;s7:进行浇筑;先进行前固化,浇注料在固化炉中固化成型,固化度至80%以上,第二步进行脱模装模,保持适当温度将产品卸模并快速装入下一模,第三步为后固化,脱模后的产品集中固化,提高固化度,释放内应力,第四步为后处理,清理产品浇口,合模缝及其它缺陷;s8:检测;质量检测,检测成品表面是否存在气孔、缩孔缩痕、裂纹和杂质,然后进行问题溯源和修正,气孔会影响碳化硅陶瓷的局部电场分布,缩孔缩痕会导致产品表面不光滑,裂纹会影响制品的耐电压和局部放电性能、力学性能,如果外表存在裂纹,内部可能会存在隐患,接线端子板类产品可能会产生气体泄露,由此说明,外观质量缺陷不只是外观质量差,且在一定程度上会影响到整机的性能,需要引起足够的重视,杂质的存在会影响电性能,实验表明密集或者大粒径的杂质会导致制品表面放电,局放增大;s9:入库,进行包装入库。
11.以上所述仅为本技术的实施例而已,并不用于限制本技术。对于本领域技术人员
来说,本技术可以有各种更改和变化。凡在本技术的精神和原理之内所作的任何修改、等同替换、改进等,均应包含在本技术的权利要求范围之内。
再多了解一些
本文用于企业家、创业者技术爱好者查询,结果仅供参考。