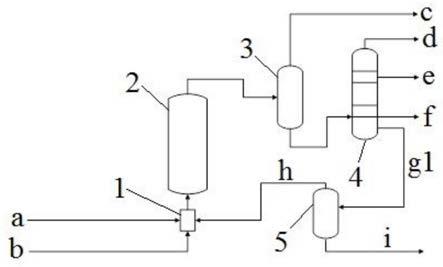
1.本发明属于石油加工领域,具体涉及一种重油轻质化方法。
背景技术:
2.随着石油资源不断地重质化与劣质化,重质油已经成为炼油厂的重要原料,将劣质重油资源高效转化加工生产更多的清洁轻质油品,成为应对石油资源短缺的重要途径。根据加工过程中油品碳氢质量比的变化,可以将重质油轻质化工艺分为加氢与脱碳两类,其中,脱碳工艺主要包括催化裂化、延迟焦化等过程,是现阶段重质油轻质化的主要加工工艺,约占全部重质油加工量的83%,然而,焦炭产率高、重质油中宝贵的碳原子难以被充分利用是该工艺存在的一大主要问题;加氢工艺约占全部重质油加工量的17%,相对于脱碳工艺,加氢工艺基本可以实现对重质油中碳原子的100%利用,因此也逐渐成为重质油轻质化的主要发展趋势。
3.目前,重质油加氢工艺主要包括固定床加氢、沸腾床加氢和悬浮床加氢工艺,作为行业内的通识认知,固定床加氢工艺一般要求原料油中总金属含量不高于150ppm(μg/g)、残炭值不高于15%、沥青质含量不高于5%,其原料适应性有限;沸腾床加氢工艺需要连续置换反应器内的部分催化剂,存在工程装备复杂、操作稳定性差等难题;悬浮床加氢工艺可以加工性质相对更差的劣质重油,相对其他加氢工艺,其具有转化深度较大、轻质油收率较高、脱残炭率和脱金属率较高等优势。
4.悬浮床加氢工艺是指通过调节流体流速带动一定颗粒粒度的催化剂运动,形成气、液、固三相床层,从而使氢气、原料油和催化剂接触而完成加氢裂化反应的加氢工艺,作为现阶段针对重油加氢的主流研究方向,研究者对悬浮床加氢工艺做了较多的研究和探索,目前也已有一些关于悬浮床加氢工艺的报道。
5.美国专利文献us2011303580a1公开了一种於浆加氢裂化方法,该方法中,将一种或多种烃类原料和包含载体的於浆加氢裂化催化剂合并,作为於浆加氢裂化反应区的进料;将於浆加氢反应区的流出物(产物)分馏,以得到轻度减压粗柴油、重度减压粗柴油、包含沥青和於浆加氢裂化催化剂的混合物料;从至少一部分的於浆加氢裂化催化剂中分离出沥青,分离后得到的於浆加氢裂化催化剂包含在悬浮液中;将悬浮液循环返回至於浆加氢裂化反应区。该工艺的目的主要在于提高沥青的利用率,由此提出了上述在真空蒸馏后从於浆加氢催化剂中分离沥青的方案,虽然该工艺能够在一定程度上实现对重质油的轻质化,但存在着单程转化率低、尾油循环量大以及能耗高、操作成本高等缺陷。
6.另有美国专利文献us2016122663a1公开了一种集成的於浆加氢裂化工艺,该工艺中,将重质残余烃原料和氢气流引入於浆加氢裂化区,在於浆加氢裂化条件下,重质残余烃原料在有光泽的加氢裂化催化剂作用下加氢裂化,形成於浆加氢裂化流出物(产物),将至少一部分所述流出物引入馏分油加氢处理器的第一端,并向该第一端补充氢气,在加氢处理条件下对所述至少一部分流出物进行加氢处理,生成的加氢处理产物从与第一端相对的第二端流出馏分油加氢处理器,然后将加氢处理产物分离成液体流和气体流,将至少一部
分含有氢气的气体流循环返回至於浆加氢裂化区。该工艺同样存在着工艺流程复杂、转化率有限等问题。
7.中国专利文献cn001239929a公开了一种采用多金属液体催化剂的常压重油悬浮床加氢工艺,其方案中,经充分混合并加热后的浆料由底部进入悬浮床加氢裂化反应器,反应器的顶部流出物则进入高温高压分离系统进行分离,汽相物流进入在线固定床加氢精制反应器,而液相物则进入低压分离系统,低压分离系统的液相物也进入在先固定床加氢精制反应器,经固定床加氢精制后的物流最后再进入常规分离系统进行分离而得出各种产品。该工艺联合采用悬浮床加氢裂化反应器和固定床加氢精制反应器并需要配合至少三级分离系统(高温高压分离系统、低压分离系统、常规分离系统等)实现对重质油的轻质化,整个工艺系统及流程复杂,能耗较高及成本较高。
8.中国专利文献cn107892941b公开了一种重油悬浮床加氢裂化方法,该方法中,将劣质重油悬浮床加氢催化剂与劣质重油混合均匀后进入悬浮床加氢反应器,然后将反应器升温至320~500℃进行加氢反应,反应压力为5~20mpa,时间为0.5-4h,氢油体积比为100-2000,空速为0.2-4.0h-1
;其中,所述的加氢催化剂由氧化锌粉末(含量为10-56wt%)和流化后的矿石组分粉末组成,或者,该加氢催化剂由氧化锌粉末(含量为10-56wt%)、硫化后的矿石组分粉末和硫化后的微介孔铁酸镧(含量为0.2-8wt%)组成。该方法通过改进加氢催化剂实现对重油原料轻质化效果的提升,但其对催化剂的特殊要求也增加了其整个工艺流程的成本及复杂程度,实际工业化应用具有较大的限制性。
9.通过加氢工艺实现重油的轻质化,无论是哪种加氢工艺,体系物料所遵循的共性机理都在于,氢气首先分散并溶解到重油中,然后被溶解或分散在重油中的加氢催化剂所活化,进而与重油中的待反应组分反应,实现对重油的加氢轻质化。该过程中,实现重质油原料、氢气与催化剂三者的充分接触,对于保障重质油加氢的高效进行至关重要,也是各种加氢工艺实施过程中所面临难题的共性本质。以悬浮床加氢工艺为例进行说明,氢气以气泡形式进入悬浮床加氢反应器后,需要经气泡-重质油相界面传递到液相的重质油中,再被溶解(油溶性或水溶性的均相催化剂)或分散(固体颗粒状的非均相催化剂)在重质油中的催化剂所活化,在一定的操作压力(传质推动力)下,氢气气泡与重油之间的相界面面积决定了氢气向重油中的传质速率,而目前的悬浮床加氢反应器中分散于重油的氢气气泡尺寸普遍不低于5mm,并不能为氢气向重油中的传递提供足够的相界面面积,且由于气泡较大,其在重油中的浮力也较大,上升快,停留时间短,导致氢气没有充足的时间与重油接触反应,难以及时补充足够多可以迅速捕捉重油受热所产生的大分子自由基的氢基自由基,易引起重油大分子自由基相互碰撞,引发叠合,甚至结焦,因此,目前悬浮床加氢工艺实施往往在较大操作压力(大部分大于18mpa)下进行,以此增加氢气向重油中的传质推动力,缓解上述氢气与重油接触反应差、易结焦等问题,而较大的操作压力往往对设备、操作过程等要求较高,导致悬浮床加氢工艺的工业化应用非常受限。
10.实际上,上述悬浮床等加氢工艺普遍面临着难以实现重油、氢气、催化剂三者充分接触的共性问题,这也是导致该些工艺存在操作压力大、条件苛刻等缺陷的本质原因,虽然诸如上述报道的悬浮床加氢工艺通过联合采用多个反应器和/或改进催化剂等方式可以实现对重油的有效转化或在一定程度上降低悬浮床反应器的操作压力等条件,但该些工艺普遍面临着整个工艺流程复杂等问题,工业化应用受限。
11.因此,开发新型重油轻质化工艺,在保证甚至提高重油转化率的同时,降低操作压力、简化工艺流程,提升其工业实用性,已成为本领域技术人员亟待解决的技术难题。
技术实现要素:
12.本发明所要解决的技术问题是提供一种重油轻质化方法,该方法可实现重油的高效转化,且工艺流程简单,工业实用性强。
13.本发明提供一种重油轻质化方法,包括:使氢气与混有催化剂的重油原料进入加氢反应器内进行加氢反应,得到加氢反应产物;对得到的加氢反应产物实施分馏,得到轻质油品和尾油;对所述尾油实施萃取处理,使得到的萃取油返回加氢反应器内参与所述加氢反应,形成循环;其中,实现加氢反应的体系为氢气以尺寸不大于500微米的气泡分散于加氢反应器内的油相中的弥散体系。
14.本发明提供的重油轻质化方法,采用加氢反应器对重油原料进行轻质化,并使氢气以尺寸不大于500微米的气泡分散于加氢反应器内的油相中,在加氢反应器内的反应状态下,形成以包括重油原料的油相(液相)为连续相、催化剂及高度分散的微米尺度(不大于500微米)的氢气气泡为离散相的弥散体系(亦可以称为弥散流形态,本发明将具有该体系或形态的反应器称为弥散床加氢反应器),在该弥散体系状态下进行加氢反应,可以使重油原料、催化剂、氢气三者之间充分接触,显著提高重油原料的转化率及轻质化产物收率,并可抑制重油原料的缩合生焦,同时由于各原料充分接触,还可以使加氢反应在较低的操作压力等条件下进行,使得反应条件更加缓和,节约能耗及成本;此外,在上述弥散体系的基础上,对尾油进行萃取处理,使萃取油返回加氢反应器内形成循环,在实现对重油原料深度裂化的同时,还可以避免由于尾油中含有较多较难转化的沥青质及焦炭等物质而导致的催化剂快速失活等问题,从而进一步保证了整个轻质化系统的稳定运行。
15.可以理解,于上述油相中分散的氢气气泡类似于球形,上述尺寸一般是指氢气气泡的直径,其测定和控制方法均为惯常手段。本发明可采用本领域常规物料微分散或气泡发生方法使氢气以尺寸不大于500微米的气泡形式分散于油相中,比如具体可以采用本领域常规气泡产生装置(或称微元发生装置)对进料(如氢气与重油原料和/或尾油)进行微分散处理,使进入加氢反应器内的氢气与包括重油原料的油相以上述弥散体系进行加氢反应。
16.一般情况下,可以使气相与液相一起流经微元发生装置,形成气相(如氢气)以气泡形式分散于液相(如重油原料或重油原料与萃取油的混合物)中的微元分散体系,或者,也可以使气相单独通过微元发生装置进料,气相(如下述单独进料部分的氢气)单独进料时,微元发生装置(如下述第三微元发生装置)一般可埋入液相中,或者说,气相通过微元发生装置进入加氢反应器的入口嵌入至加氢反应器的内部,与液相(如下述第二微元分散体系中的油相)接触,从而利于气相从微元发生装置进入加氢反应器后形成分散于液相中的气泡。
17.具体地,在本发明的一实施方式中,可以使氢气与包括重油原料的油相经第一微元发生装置分散处理得到的氢气以尺寸不大于500微米的气泡分散于油相中的第一微元分散体系进入加氢反应器内形成上述弥散体系(即反应器内的弥散体系是由上述第一微元分散体系进入加氢反应器内形成)。具体实施时,可以使第一微元分散体系从加氢反应器的顶
部、中部、底部的某一处或几处进入加氢反应器内,在轻质化过程中,其中的气相(主要是氢气、裂化气、产物油气等)与液相(混有催化剂的重油原料、生成的轻质油品等)的主体流动方向可以相同(均顺重力场或均逆重力场)或相反(气相顺重力场同时液相逆重力场,或者,气相逆重力场同时液相顺重力场)。作为一种优选实施方案,一般可以使第一微元分散体系从加氢反应器的顶部或底部进入加氢反应器内,在本发明的工艺条件下,加氢反应器内的液相以及夹杂在其中的反应产生的焦炭等固相物料的主体流动形式接近理想平推流,利于反应的进行及整体系统的运行稳定性。
18.或者,在另一实施方式中,可以使一部分氢气(记为a1部分氢气)与包括重油原料的油相经第二微元发生装置分散处理得到的氢气以尺寸不大于500微米的气泡分散于所述油相中的第二微元分散体系进入加氢反应器内,同时使剩余部分氢气(记为a2部分氢气)经第三微元发生装置处理进入加氢反应器内与所述第二微元分散体系共同形成所述弥散体系(即剩余部分氢气经第三微元发生装置处理进入加氢反应器内形成尺寸不大于500微米的气泡分散于第二微元分散体系中的油相中,形成上述弥散体系)。具体来说,第二微元发生装置先将一部分氢气以尺寸不大于500微米的气泡分散于重油原料中,形成上述第二微元分散体系,然后进料;第三微元发生装置将剩余部分氢气(即单独进料部分的氢气)以尺寸不大于500微米的气泡分散于进入加氢反应器内的第二微元分散体系中的重油原料中,从而形成上述弥散体系。其中,一般可以控制a1部分氢气占氢气总进料量(质量)的10%-90%,进一步可以为20%-50%或20%-40%,如在一具体实施例中,可以使占氢气总进料量30%的氢气(即a1部分氢气)与包括重油原料的油相经第二微元发生装置分散处理形成第二微元分散体系,该第二微元分散体系进入加氢反应器内,同时使剩余的70%氢气(即a2部分氢气)经第三微元发生装置处理进入加氢反应器内与第二微元分散体系共同形成上述弥散体系;上述第二微元分散体系和a2部分氢气可以从加氢反应器的顶部、中部、底部进入加氢反应器内,其具体进入位置可以相同或不同。
19.具体地,上述微元发生装置(即第一微元发生装置、第二微元发生装置、第三微元发生装置)比如可以选自微孔陶瓷膜微元发生装置、文丘里式微元发生装置、超声波空化装置中的至少一种,一般可以通过选用一定孔径的微孔陶瓷膜微元发生装置、或者调整文丘里式微元发生装置/超声波空化装置的气速等条件(或参数)实现对形成的氢气气泡尺寸的调控,例如,采用孔直径为100μm的微孔陶瓷膜微元发生装置(其中的微孔陶瓷膜的孔直径为100μm)产生气泡时,气相通过微孔陶瓷膜进入液相形成气泡,一般认为所形成气泡的尺寸平均也为100μm左右;而采用文丘里式微元发生装置(或超声波空化装置)产生气泡时,气相的气速越大,所形成的气泡尺寸越大,反之亦然,通过气速可以控制形成特定尺寸的气泡。
20.综合考虑轻质化效果、系统运行稳定性、操作难易程度等因素,在本发明的一实施方式中,上述氢气气泡的尺寸一般具体可以为10-500μm,进一步可以为50-350μm,比如可以为100-300μm或150-250μm等。
21.根据本发明的研究,上述轻质化过程中,联合采用微元发生装置和加氢反应器,整个重油轻质化系统简单、易操作,且能够显著提高对重油原料的轻质化效果。
22.经进一步研究,上述加氢反应器的条件(即加氢反应条件)可以为:操作压力为6~15mpa,进一步可以为8~15mpa或8~13mpa,反应温度为420~480℃,进一步可以为450~
470℃,重时空速为0.1~1.5h-1
,进一步可以为0.2~0.8h-1
,氢油比为600~2500nm3/m3,进一步可以为800-2000nm3/m3,更进一步可以为1000~2000nm3/m3,比如可以为1000-1500nm3/m3,该条件利于重油原料的加氢反应,提高转化率,同时也利于保证整个系统运行的稳定性。
23.进一步地,上述混有催化剂的重油原料中,催化剂占重油原料的质量比可以为0.5~3.0%,进一步可以为0.8~2.3%,比如可以为0.8~1.5%或1~1.3%。
24.上述催化剂可以是本领域常规具有加氢活性和/或具有抑制结焦特性的加氢催化剂,比如可以选自均相加氢催化剂和非均相加氢催化剂中的至少一种,其中,均相加氢催化剂可以选自油溶性催化剂和水溶性催化剂中的至少一种,非均相加氢催化剂的组成原料包括载体和负载于载体的金属组分(记为第一金属组分),载体可以选自煤粉和活性炭中的至少一种,金属组分可以选自fe、co、mo、zn等中的至少一种。
25.在本发明的一优选实施方式中,所用催化剂可以包括上述非均相加氢催化剂,在本发明的工艺条件下,该催化剂能够达到优异的催化效果,且具有原料便宜易得、制备简单、成本低等优点,在产业上具有重大的实用意义。
26.进一步地,上述非均相加氢催化剂中,第一金属组分的质量含量(质量分数)可以为1~10%,利于进一步提高重油原料的轻质化效果。
27.当然,本发明也可以采用均相加氢催化剂,或者均相加氢催化剂和非均相加氢催化剂的混合。具体地,上述油溶性催化剂可以是有机酸盐和有机金属化合物等中的至少一种,有机酸盐比如可以选自环烷酸盐、c2以上的脂肪酸盐、柠檬酸盐、芳香酸盐、酒石酸盐、脂肪基取代的甲酸盐、脂肪基取代的磷酸盐等中的一种或几种,有机金属化合物比如可以是乙酰丙酮化合物、羰基化合物、(磺化)酞菁化合物、环戊二烯基化合物、edta化合物、卟啉类化合物、腈类化合物等有机化合物与金属形成的有机金属化合物中的一种或几种;上述水溶性催化剂可以包括络合物和/或无机盐,所述络合物比如可以是杂多酸、羰基化合物与金属组分(记为第二金属组分)形成的络合物中的至少一种,所述杂多酸比如可以是磷钼酸、高钼酸、磷钨酸、磷钒酸、硅钼酸、硅钨酸、硅钒酸、硫代钼酸等中的一种或几种,第二金属组分可以选自mo、fe、ni、co等中的至少一种,所述无机盐比如可以选自杂多酸盐(如上述杂多酸形成的盐等)以及含有金属组分(记为第三金属组分)的硫酸盐、盐酸盐、碳酸盐、碱式碳酸盐、硝酸盐等中的至少一种,上述杂多酸盐一般具体可以是杂多酸铵盐或碱金属盐等,第三金属组分具体可以选自mo、fe、ni、co等中的至少一种。
28.上述过程中,当所用催化剂为均相加氢催化剂时,加氢反应器内的弥散体系是气-液二相体系;当所用催化剂含有非均相加氢催化剂(即所用催化剂为非均相加氢催化剂,或者为均相加氢催化剂和非均相加氢催化剂的混合物)时,上述弥散体系是气-液-固三相体系(但由于催化剂的用量一般较少(即固相较少),也可称为气-液拟二相体系)。
29.本发明可采用本领域常规方法使催化剂混于重油原料中,以形成上述混有催化剂的重油原料,对此不做特别限制。具体实施时,一般使催化剂尽可能均匀地分散或溶于重油原料中,比如当采用非均相加氢催化剂等不能溶于重油原料中的催化剂时,可以使其形成微米尺度(如和上述氢气气泡尺寸相当)的固体颗粒等微元结构均匀分散于重油原料中,利于加氢反应器内形成以重油为连续相、以高度分散的微米尺度的氢气气泡和催化剂颗粒为离散相的均匀分布的弥散体系,更利于反应的进行及轻质化效果。
30.本发明中,上述尾油可以是从加氢反应产物中分离出的馏程>350℃或>500℃的馏分油,该类馏分油中含有较多的难易转化的沥青质、焦炭等物质,采用合适的萃取溶剂对其进行萃取,可以分别得到脱除大部分沥青质等非理想组分的萃取油和含有该些非理想组分的萃余油,使萃取油返回加氢反应器内循环加工,利于提高重油原料的转化率以及轻质化系统的稳定运行,萃余油尾渣可以外甩处理,如作为燃料或用于提取金属元素的原料等。
31.根据本发明的研究,上述萃取溶剂一般可以包括c1-c5的烃类溶剂,比如可以包括丙烷、丁烷、戊烷中的一种或几种的混合物。
32.经进一步研究,上述萃取处理的温度可以为50-190℃;和/或,萃取处理的压力可以为3-4mpa;和/或,萃取处理时,萃取溶剂与尾油的体积比(即溶剂比)可以为6-8:1。具体地,在本发明的优选实施方式中,采用丙烷作为萃取溶剂时,萃取处理的温度可以为50-90℃,比如可以为50-80℃或50-70℃或60-70℃;采用丁烷作为萃取溶剂时,萃取处理的温度可以为100-140℃;采用戊烷作为萃取溶剂时,萃取处理的温度可以为50-190℃,比如可以为100-180℃或150-180℃或160-170℃。
33.一般情况下,来自加氢反应器的加氢反应产物主要是含有包括轻质油品和尾油的馏分油以及裂化气、焦炭、未反应完的氢气的混合物,具体实施时,可以使从加氢反应器流出(或输出)的加氢反应产物先进入气液分离器等装置进行气液分离,分别得到气相组分(主要是裂化气和氢气的混合气)和液相组分(馏分油以及夹杂在其中的少量焦炭等);再使液相组分进入分馏塔(蒸馏塔)等装置进行分馏处理,获得汽油馏分(<200℃馏分段)、柴油馏分(200~350℃馏分段)、蜡油馏分(350~500℃馏分段)等轻质油品和尾油(>500℃馏分段),或者,获得汽油馏分(<200℃馏分段)、柴油馏分(200~350℃馏分段)等轻质油品和尾油(>350℃馏分段);其中,可以进一步分离出上述气相组分中的氢气(循环氢),使其与新鲜氢气混合后循环利用;加氢反应产物可以从加氢反应器的顶部、中部、底部中的某一位置处流出。当然,本发明中,加氢反应产物也可以从加氢反应器的顶部、中部、底部等中的多个位置流出,各个位置所流出的产物一般可以具有不同的馏分分布(相当于加氢反应器对加氢反应产物进行了初步的分馏处理),后续也可以再进一步经气液分离等处理进行精制。
34.上述气液分离器具体可以是热高分、热低分、冷高分、冷低分中的一种或几种的组合,可采用本领域常规方法将其与加氢反应器、分馏塔等进行组装。本发明的加氢反应器可以是本领域常规加氢反应器,比如可以是没有任何内构件的耐高压空筒装置,也可以是带有一段或多段环流内构件或其他形式内构件的耐高压反应装置等。
35.进一步地,上述轻质化过程中,返回加氢反应器的萃取油与重油原料的质量比可以为0.1-0.7:1,进一步可以为0.2-0.5:1。
36.本发明方法尤其可针对具有残炭值较高、重金属(如镍(ni)、钒(v)等)含量较高以及硫、氮含量较高等特点的重油原料进行轻质化,在一实施方式中,重油原料的康氏残炭值(ccr)大于10wt%,和/或,重金属总含量高于150μg/g。具体地,上述重油原料比如可以是稠油、超稠油、油砂沥青、常压重油、减压渣油、fcc油浆、溶剂脱油沥青等劣质重油以及煤热解或液化过程产生的重质焦油和渣油、油页岩干馏产生的重质油、生物质中低温热解液体产物等衍生劣质重油中的一种或几种的混合物。
37.本发明的实施,至少具有如下有益效果:
38.本发明提供的轻质化方法,是一种采用微米尺度的微元分散体系所驱动的新型重
油加氢工艺,相对于现有悬浮床等加氢工艺,本发明兼具重油原料转化率高(高达85%甚至90%以上)、操作压力等条件缓和不苛刻、工艺流程简单等优势,且具有易操作、成本低等优点,利于工业化生产和应用。
附图说明
39.图1为本发明一实施例的重油轻质化工艺流程图;
40.图2为本发明另一实施例的重油轻质化工艺流程图;
41.附图标记说明:
42.1:微元发生装置;2:加氢反应器;3:气液分离器;4:蒸馏塔;5:萃取塔;a:氢气;b:混有催化剂的重油原料;c:裂化气与氢气的混合气;d:汽油馏分;e:柴油馏分;f:蜡油馏分;g1、g2:尾油;h:萃取油;i:萃余油。
具体实施方式
43.下面结合实施例,更具体地说明本发明的内容。应当理解,本发明的实施并不局限于下面的实施例,对本发明所做的任何形式上的变通和/或改变都将落入本发明保护范围。
44.实施例1
45.本实施例提供一种重油轻质化方法,如图1所示,使氢气a与混有催化剂的重油原料b进入文丘里式微元发生装置1内进行分散处理,得到氢气以平均尺寸不大于500微米的气泡分散于重油原料中的微元分散体系;该微元分散体系从加氢反应器的顶部进入加氢反应器2进行加氢反应(加氢反应器内的加氢反应体系为氢气以不大于500微米的气泡分散于油相中的弥散体系),得到加氢反应产物;加氢反应产物进入气液分离器3中进行气液分离,分别得到气相组分(裂化气和氢气的混合气c)和液相组分;液相组分进入蒸馏塔4内进行分馏,分别得到<200℃的汽油馏分d、200~350℃的柴油馏分e、350~500℃的蜡油馏分f和>500℃的尾油g1;尾油g1进入萃取塔5,与萃取溶剂接触进行萃取处理,分别得到萃取油h和萃余油i,使萃取油h返回微元发生装置1参与上述分散处理,形成循环。其中,分离出混合气c中的氢气,将其与新鲜氢气混合循环利用。
46.实施例2
47.如图2所示,本实施例提供的重油轻质化方法与实施例1的区别在于:液相组分进入蒸馏塔4内进行分馏,分别得到<200℃的汽油馏分d、200~350℃的柴油馏分e和>350℃的尾油g2。其余条件均与实施例1相同。
48.应用实施例1
49.以下试验例1和2、对比例1和2中,所用重油原料为减压渣油,其性质如表1所示;所用催化剂均为由活性炭(炭粉)负载铁元素形成的非均相催化剂,该催化剂中,铁元素的质量分数为5%。
50.试验例1和试验例2
51.采用实施例1的重油轻质化方法进行试验例1和试验例2,加氢反应器内弥散体系的氢气气泡尺寸(微元尺度)、操作压力、反应温度、空速、氢油比、催化剂占重油原料的质量比(催化剂添加量)等条件如表2所示,加氢反应的产物中的产品分布如表3所示;其中,对尾油g1进行萃取处理的条件为:所用的萃取溶剂为戊烷,萃取温度为165℃,压力为3.5mpa,溶
剂比为6:1;返回加氢反应器2的萃取油与重油原料的质量比为0.2:1。
52.对比例1和对比例2
53.采用常规悬浮床加氢工艺对上述重油原料进行轻质化处理(均无对尾油进行萃取处理),悬浮床反应器内分散于重油原料中的氢气气泡尺寸(微元尺度)、操作压力、反应温度、空速、氢油比、催化剂占重油原料的质量比(催化剂添加量)等条件如表2所示,加氢反应的产物中的产品分布如表3所示。
54.表1重油原料性质
[0055][0056]
表2反应条件
[0057]
项目试验例1试验例2对比例1对比例2微元尺度,μm21050050005000操作压力,mpa13131322反应温度,℃457457457459重时空速,h-1
0.40.40.40.4氢油比,nm3/m31200120012002278催化剂添加量,wt%1.21.21.21.2
[0058]
表3主要产品分布
[0059][0060]
应用实施例2
[0061]
以下试验例3和4、对比例3和4中,所用重油原料为新疆减压渣油,其性质如表4所示;所用催化剂均为由活性炭(炭粉)负载铁元素形成的非均相催化剂,该催化剂中,铁元素
的质量分数为5%。
[0062]
试验例3和试验例4
[0063]
采用实施例2的重油轻质化方法进行试验例3和试验例4,加氢反应器内弥散体系的氢气气泡尺寸(微元尺度)、操作压力、反应温度、空速、氢油比、催化剂占重油原料的质量比(催化剂添加量)等条件如表5所示,加氢反应的产物中的产品分布如表6所示;其中,对尾油g2进行萃取处理的条件为:所用的萃取溶剂为丙烷,萃取温度为65℃,压力为3.43mpa,溶剂比为6:1;返回加氢反应器2的萃取油与重油原料的质量比为0.2:1。
[0064]
对比例3和对比例4
[0065]
采用常规悬浮床加氢工艺对上述重油原料进行轻质化处理(均无对尾油进行萃取处理),悬浮床反应器内分散于重油原料中的氢气气泡尺寸(微元尺度)、操作压力、反应温度、空速、氢油比、催化剂占重油原料的质量比(催化剂添加量)等条件如表5所示,加氢反应的产物中的产品分布如表6所示。
[0066]
表4重油原料性质
[0067][0068]
表5反应条件
[0069]
项目试验例1试验例2对比例1对比例2微元尺度,μm21050050005000操作压力,mpa13131322反应温度,℃457457457459重时空速,h-1
0.40.40.50.5氢油比,nm3/m31200120012002278催化剂添加量,wt%1.21.21.21.2
[0070]
表6主要产品分布
[0071][0072]
结果显示,在较低的氢油比(1200nm3/m3)、操作压力(13mpa)等条件下,试验例1-4能达到优异的轻质化效果,重油原料转化率高达87%以上,远高于传统悬浮床工艺(如对比例1和3);传统悬浮床加氢工艺在较低的压力、氢油比等条件下,轻质化效果非常差,若要提高轻质化效果,往往需要如对比例2和4这样的高压(22mpa)、高氢油比(2278nm3/m3)条件,进一步通过试验例1和对比例2、试验例3和对比例4表明,试验例1和3在远低于对比例2和4的氢油比、操作压力等条件下,仍然能够达到与对比例2和4相当的重油原料转化率,同时具有更低的焦炭收率,说明了本发明的重油轻质化方法能够大幅降低操作压力、氢油比等条件,相对于常规悬浮床等加氢工艺具有非常明显的优势;此外,试验例1-4的轻质化过程中,整个系统运行稳定,并还具有工艺流程简单、易操作等优点,进一步保证了本发明重油轻质化方法的工业实用性。
再多了解一些
本文用于企业家、创业者技术爱好者查询,结果仅供参考。