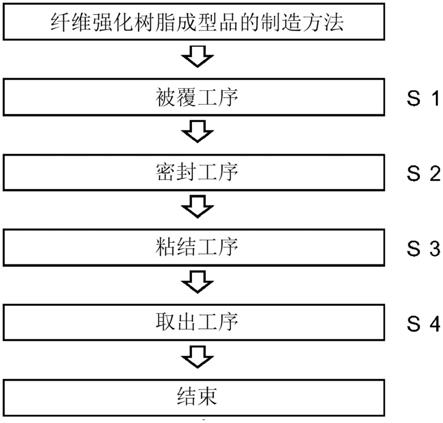
1.本发明涉及一种纤维强化树脂成型品的制造方法以及纤维强化树脂成型品。
背景技术:
2.通过向树脂原料中混合碳纤维、玻璃纤维等纤维来增强树脂成型品的强度。经纤维强化的树脂成型品例如通过压制成型法、热压釜(autoclave)法来制造。
3.在压制成型法(rtm法)中,通过将片状纤维品配置于与将要制造的树脂成型品的形状对应的雌雄一对模具之间,将树脂成分注入至腔体并进行固化,从而得到纤维强化树脂成型品。
4.在热压釜法中,通过如下方式得到纤维强化树脂成型品:将预浸料配置于与制造的成型品对应的模具之上,将该模具和预浸料放入至气密性的袋子,将每个该袋子放入至热压釜,加压并对袋内进行减压,由此一边使模具与预浸料紧贴一边进行加热而使预浸料中的热固性树脂固化。
5.此外,作为改善了压制成型法、热压釜法的方法,在专利文献1公开了一种无需热压机、热压釜等装置的、纤维强化树脂成型品的制造方法。在该方法中,将纤维强化树脂基体材料配置于模具的内表面,向配置有该纤维强化树脂基体材料的模具的芯空间部填充包括热膨胀性囊的粉体混合物并密闭模具后,对纤维强化树脂基体材料与模具的内表面之间的空气进行排气,接着进行加热。
6.现有技术文献
7.专利文献
8.专利文献1:专利第6405433号公报
技术实现要素:
9.发明所要解决的问题
10.然而,这些方法存在以下问题:由于如上所述、均需要高价的模具而不适于便宜的制品的制造,此外,加工工序中需要工夫。
11.本发明是鉴于上述的问题而完成的发明,本发明的目的在于提供一种能容易地制造纤维强化树脂成型品的方法以及通过该方法得到的纤维强化树脂成型品。
12.用于解决问题的方案
13.为了达成所述目的,本发明的第一观点的纤维强化树脂成型品的制造方法包括:
14.被覆工序,利用含有强化用纤维和基体树脂的片状的纤维强化树脂基体材料被覆立体造型物的至少一部分,得到层叠体;
15.密封工序,将所述层叠体和粉体以所述粉体存在于软质气密容器的内侧面与所述层叠体之间的方式填充至具备排气口的所述软质气密容器的内部并进行密封;
16.粘结工序,通过对密封了的所述软质气密容器进行排气而使所述立体造型物与所述纤维强化树脂基体材料成为紧贴的状态,在该状态下,对所述软质气密容器内进行加热
来使所述纤维强化树脂基体材料与所述立体造型物粘结;以及
17.取出工序,从所述软质气密容器取出所述立体造型物和所粘结的所述纤维强化树脂基体材料的复合体,并且去掉所述粉体,得到纤维强化树脂成型品。
18.优选的是,所述粉体为包含多种粉体的混合物。
19.优选的是,在所述密封工序中,进一步将热膨胀材料填充至所述软质气密容器内。
20.优选的是,所述强化用纤维为碳纤维。
21.优选的是,所述立体造型物为通过3d打印而造型出的立体造型物。
22.本发明的第二观点的纤维强化树脂成型品为立体造型物与纤维强化树脂基体材料粘结的纤维强化树脂成型品,
23.就所述纤维强化树脂基体材料而言,
24.利用含有强化用纤维和基体树脂的片状的所述纤维强化树脂基体材料被覆所述立体造型物的至少一部分,得到层叠体,
25.将所述层叠体和粉体以所述粉体存在于软质气密容器的内侧面与所述层叠体之间的方式填充至具备排气口的软质气密容器的内部并进行密封,
26.通过对密封了的所述软质气密容器进行排气而使所述立体造型物与所述纤维强化树脂基体材料成为紧贴的状态,对所述软质气密容器内进行加热,由此,所述立体造型物与所述纤维强化树脂基体材料粘结。
27.优选的是,所述立体造型物为通过3d打印而造型出的立体造型物。
28.优选的是,所述强化用纤维为碳纤维。
29.发明效果
30.根据本发明的纤维强化树脂成型品的制造方法,能容易地得到高强度的纤维强化树脂成型品。
附图说明
31.图1是第一个实施方式的纤维强化树脂成型品的制造方法的流程图。
32.图2是示出第一个实施方式的被覆工序的概略图。
33.图3是示出第一个实施方式的层叠体的概略图。
34.图4是示出第一个实施方式的密封工序的概略图。
35.图5是示出第一个实施方式的粘结工序的排气的概略图。
36.图6是示出第一个实施方式的粘结工序的概略图。
37.图7是示出第一个实施方式的取出工序的概略图。
38.图8是实施例的立体造型物和纤维强化树脂成型品的照片。
39.图9是示出实施例的被覆工序的概略图。
40.图10是示出实施例的密封工序的概略图。
41.图11是示出实施例的密封工序的概略图。
42.图12是示出实施例的密封工序的概略图。
43.图13是示出实施例的密封工序的概略图。
44.图14是示出实施例中粘结工序的排气的概略图。
具体实施方式
45.参照附图对本发明的一个实施方式的纤维强化树脂成型品的制造方法进行说明,但本发明不限于此。
46.如图1所示,本制造方法至少包括被覆工序s1、密封工序s2、粘结工序s3以及取出工序s4。以下对各工序进行详细说明。
47.(被覆工序s1)
48.在被覆工序s1中,如图2所示,通过利用含有强化用纤维2和基体树脂3的片状的纤维强化树脂基体材料4被覆立体造型物1的至少一部分,得到如图3所示那样的层叠体5。
49.立体造型物1是成为纤维强化树脂成型品的形状的基础的构件,只要是不会因被覆工序s1、密封工序s2以及粘结工序s3而变形的程度的强度即可,组成、形状没有特别限定。作为组成,可列举出树脂、陶瓷、纸、金属、木质材料等。就立体造型物1的形状而言,可以是如图2所示那样的、有空洞部分的形状,但优选为具有后述的在密封工序s2中向空洞部分填充粉体的出入口的形状。出于以下点而优选:当立体造型物1具有空洞部分时得到的纤维强化树脂成型品的轻型化。
50.立体造型物1不受其制造方法限定,但例如优选的是,通过3d打印来造型。通过3d打印来造型,也能对如具有空洞部分那样的立体形状、二连环形状这样难以通过以往的模具来成型的复杂的形状进行成型。此外,也适于少量生产。
51.纤维强化树脂基体材料4为含有强化用纤维2和基体树脂3的片状材料。
52.强化用纤维2可以在纤维强化树脂基体材料4中纤维方向沿一个方向排列,也可以以平纹织、斜纹织、缎纹织等织物状存在,也可以无秩序地分散。
53.作为强化用纤维2,只要是不会因粘结工序s3的加热温度而劣化的纤维即可,没有特别限定,可列举出碳纤维、碳纳米管、石墨烯片、纤维素纳米纤维、玻璃纤维、矿物纤维等。不过,其中,出于得到的纤维强化树脂成型品的强度方面,优选碳纤维。强化用纤维2的尺寸没有特别限定,但例如可以使用纤维长为数百nm以上且数mm以下的纤维。
54.强化用纤维2可以单独使用一种或者组合使用多种。
55.基体树脂3只要是在被覆工序s1中具有柔软性并能在粘结工序s3中粘结的树脂即可,没有特别限定,其中,例如可列举出环氧树脂、不饱和聚酯、酚醛树脂等热固性树脂的半固化树脂、聚偏二氯乙烯系树脂、丙烯酸系树脂、an系共聚物系树脂等热塑性树脂。
56.基体树脂3在纤维强化树脂基体材料4中以基体(基料)的形式存在于纤维与纤维之间、纤维的周围。
57.作为纤维强化树脂基体材料4,可以使用使基体树脂3浸渍强化用纤维2并制为片状的、作为预浸料而市面销售的材料。预浸料为使热固性树脂浸渍强化用纤维并进行加热或干燥而使其呈半固化状态的树脂的片材、或者使熔融的热塑性树脂浸渍强化用纤维并对该热塑性树脂进行固化而成的片材。例如,可以使用作为碳纤维增强塑料(carbon fiber reinforced plastic:cfrp)的热固性树脂预浸料的东丽卡(注册商标)、作为cfrp的热塑性树脂预浸料的日铁化学材料株式会社的热塑性预浸料(tepreg(注册商标))等各种预浸料。纤维强化树脂基体材料4的厚度没有特别限定,但例如为0.07mm以上且0.2mm以下。
58.纤维强化树脂基体材料4的层叠数可以适当选择,可以为单层也可以为多层。
59.纤维强化树脂基体材料4可以使用预先通过超声波切割机等切割来使其与立体造
型物1的形状、凹凸相对应而得到的材料。
60.在利用纤维强化树脂基体材料4被覆立体造型物1时,在立体造型物1形成空筒部分,具有外侧面和内侧面的情况下,可以根据所需的强度来被覆外侧面和内侧面中的任一方或者两面。
61.当在立体造型物1与纤维强化树脂基体材料4直接接触了的状态下进行被覆时,可以在后述的粘结工序s3中将立体造型物1与纤维强化树脂基体材料4粘结。此外,通过在立体造型物1与纤维强化树脂基体材料4之间部分地设置离型层或在纤维强化树脂基体材料4集中褶皱而被覆等,也能在立体造型物1与固化了的纤维强化树脂基体材料4之间部分地产生空间,以免粘结。非粘结部分能设为纤维强化树脂成型品14的可动部。
62.(密封工序s2)
63.在密封工序s2中,如图4所示,将层叠体5和粉体8以粉体8存在于软质气密容器7的内侧面与所述层叠体5之间存在的方式填充至具备排气口6的软质气密容器7的内部并进行密封。
64.就软质气密容器7而言,为能收纳层叠体5和粉体8的大小,只要是具备能在软质气密容器7的外侧和内侧传递压力的柔软性的材质即可,没有特别限定。例如可以使用如图4所示那样的耐热性塑料袋、关闭管的一端的管容器等。袋口成为层叠体5和粉体8的出入口,并且通过夹住管关闭而作为排气口6发挥功能。这样,可以将层叠体5等的出入口作为排气口6共用,但也可以在与层叠体5等的出入口不同的部分另行设置排气口6。
65.粉体8只要具有流动性和热传导性即可,其大小、形状、材质没有特别限定。作为粉体8,例如可以使用平均粒径1μm~200μm的有机粉体或者无机粉体。粉体8可以单独使用一种,或者也可以使用粒径、形状等不同的多种粉体8。当使用包含粒径不同的多种粉体的混合物来作为粉体8时,在软质气密容器7中的填充性优异,并且能在脱气时减少所携带的粉体8,因此优选。
66.在密封工序s2中,除了填充粉体8以外,还可以填充其他构件。作为其他构件,可列举出短纤维、热膨胀材料等。
67.在使用短纤维的情况下,优选的是,纤维径为1μm~20μm并且切割为长度0.5mm~5mm的短纤维。
68.作为热膨胀材料,可列举出热膨胀性微囊。当使用热膨胀材料时,在固化工序s3时,热膨胀材料因热发生膨胀,使软质气密容器7的中的压力升高,而能提高纤维强化树脂基体材料4的对立体造型物1的形状的追随性。热膨胀材料可以与粉体8均匀地混合来使用。此外,出于再利用粉体8的观点,优选的是,用具有伸缩性的包装膜包装热膨胀材料等并制成杆(stick)形状,并与粉体8一起配置于软质气密容器7内。
69.可以在层叠体5与粉体8之间配置薄的纸等离型材料。通过配置离型材料,取出工序s4中的粉体8的去除变得容易。作为离型材料,可使用氟树脂膜、硅膜等膜类。
70.作为将层叠体5和粉体8以粉体8存在于软质气密容器7的内侧面与层叠体5之间的方式填充至软质气密容器7并进行密封的方法,例如,将层叠体5放入至软质气密容器7,并将粉体8填充至层叠体5的空筒部分和层叠体5的周围,将管夹入至层叠体5和粉体8的出入口(排气口6)并进行密封(参照图4)。
71.(粘结工序s3)
72.在粘结工序s3中,如图5所示,通过对密封了的软质气密容器7进行排气而使立体造型物1与纤维强化树脂基体材料4成为紧贴的状态,在该状态下,对软质气密容器7内进行加热来使纤维强化树脂基体材料4与立体造型物1粘结。
73.当从密封了的软质气密容器7的排气口6对气体9(空气)进行排气时,软质气密容器7因外部气压10而收缩,该外部气压10通过软质气密容器7和粉体8来使立体造型物1与纤维强化树脂基体材料4紧贴。通过存在粉体8来防止立体造型物1的凸部分与软质气密容器7直接接触,并且将外部气压10均等地传至纤维强化树脂基体材料4的包括凹部分的整个面,来填埋立体造型物1与纤维强化树脂基体材料4之间的间隙并使其紧贴。粉体8传递压力和热,并且在排气时作为气体流路发挥功能。
74.排气可以通过减压泵11等从排气口6直接进行,但优选的是,如图5所示,在减压泵11与排气口6之间设置对所携带的粉体8进行捕捉的捕集器12。
75.软质气密容器7内的加热如图6所示,可以将立体造型物1与纤维强化树脂基体材料4紧贴了的状态的软质气密容器7放入至烘箱13来进行。此外,也可以将加热器配置于软质气密容器7的内部来进行加热。
76.加热温度只要是纤维强化树脂基体材料4粘结的温度即可,没有特别限定,可以根据使用的基体树脂3的种类来适当选择。例如,能设为常温以上且200℃以下。
77.前述的排气优选也在加热中也进行。虽然在纤维强化树脂基体材料4的粘结时有时会产生气体,但通过对该气体进行排气能保持立体造型物1与纤维强化树脂基体材料4的紧贴。
78.通过纤维强化树脂基体材料4粘结,而成为层叠体5的立体造型物1与纤维强化树脂基体材料4呈一体的复合体14。
79.(取出工序s4)
80.在取出工序s4中,如图7所示,从软质气密容器7取出立体造型物1与纤维强化树脂基体材料4的复合体14并且去掉粉体8,得到纤维强化树脂成型品14。
81.去掉的粉体8、软质气密容器7可以再利用。
82.纤维强化树脂成型品14中的纤维强化树脂基体材料4由于立体造型物1的表面凹凸的锚固效果等而牢固地粘结于立体造型物1。因此,纤维强化树脂成型品14中的立体造型物1虽然无需去掉,但也可以通过研磨等来去除。
83.纤维强化树脂成型品14以立体造型物1的形状就那样具备所使用的纤维强化树脂的强度,因此,能制造各种形状、大小的部件,能用于定制的医疗用具、机器人的部件等各种用途。
84.(实施例)
85.对本发明的实施例进行说明,但本发明不限于此。需要说明的是,在此,使用热固化性树脂来作为基体树脂,在粘结工序中,通过对热固化性树脂进行固化来将立体造型物与纤维强化树脂基体材料粘结。
86.此外,虽然示出利用一个软质气密容器来成型一个纤维强化树脂成型品的例子,但本发明不限于此,也可以用一个软质气密容器来成型多个纤维强化树脂成型品。
87.通过3d打印而造型出图8(左)所示的假指装接用具的形状的立体造型物1。该假指装接用具能套在手指上并能在缺口部分15处弯折。
88.接着,将片状的cfrp(carbon fiber reinforced plastic:碳纤维增强塑料)预浸料与立体造型物1的形状相对应地加工成筒状,准备出纤维强化树脂基体材料4。通过将立体造型物1插入至纤维强化树脂基体材料4,将纤维强化树脂基体材料4被覆于立体造型物1,得到了层叠体5(参照图9)。
89.利用薄的包装材料(离型材料16)包装层叠体5(参照图10)。接着,将粉体8填充至立体造型物1的内侧并进行密封,制作出捆包物17(参照图11)。粉体8为平均粒径1μm~200μm的无机粉体,是与纤维径为1μm~20μm并且切为长度0.5mm~5mm的短纤维的混合物。
90.接着,将三个热膨胀材料18均等地配置于捆包物17的周围,与粉体8一起,利用薄的包装材料(离型材料19)包装,制作出捆包物20(参照图12)。热膨胀材料18为将热膨胀性微囊填充至具有伸缩性的包装膜并包装为杆状的材料。
91.接着,将捆包物20放入软质气密容器7(参照图13)。软质气密容器7为具有气密性的耐热片并具备排气口6。在捆包物20的周围填充粉体8,将软管21穿过排气口6并关闭(参照图13)。将该软管21经由捕集器12与减压泵11连接,对气体9进行排气来减压(参照图14)。
92.通过减压,立体造型物1与纤维强化树脂基体材料4之间的间隙消失,并且经由粉体8,外部气压均等地施加于纤维强化树脂基体材料4,立体造型物1与纤维强化树脂基体材料4彼此紧贴。
93.接着,将软质气密容器7放入至烘箱,一边对软质气密容器7进行减压一边进行加热,使纤维强化树脂基体材料4固化(未图示)。
94.接着,从软质气密容器7取出立体造型物1与纤维强化树脂基体材料4的复合体,去掉粉体8,得到纤维强化树脂成型品14(未图示)。
95.在图8示出了立体造型物1(左)和纤维强化树脂成型品14(右)。需要说明的是,图8的纤维强化树脂成型品14为在粘结后将纤维强化树脂基体材料4的与立体造型物1的缺口部分15对应的部分切除而成的构件。纤维强化树脂成型品14的缺口部分22与立体造型物1同样地,示出了弯折性。纤维强化树脂成型品14轻量并具备源自纤维强化树脂基体材料4的强度。
96.本发明能在不脱离本发明的广义的精神和范围的情况下进行各种实施方式和变形。此外,上述的实施方式用于对该发明进行说明,并不对本发明的范围进行限定。即,本发明的范围通过权利要求范围进行示出,而不是实施方式。然后,在权利要求范围内和与其同等的发明的意义的范围内施行的各种变形应当认为在该发明的范围内。
97.本技术基于在2019年9月5日申请的日本专利申请特愿2019-162348号。将日本专利申请特愿2019-162348号的说明书、权利要求范围以及附图整体作为参照引入本说明书中。
98.附图标记说明:
99.1:立体造型物;2:强化用纤维;3:基体树脂;4:纤维强化树脂基体材料;5:层叠体;6:排气口;7:软质气密容器;8:粉体;9:气体;10:外部气压;11:减压泵;12:捕集器;13:烘箱;14:复合体(纤维强化树脂成型品);15:缺口部分;16:离型材料;17:捆包物;18:热膨胀材料;19:离型材料;20:捆包物;21:软管;22:缺口部分;s1:被覆工序;s2:密封工序;s3:粘结工序;s4:取出工序。
再多了解一些
本文用于企业家、创业者技术爱好者查询,结果仅供参考。