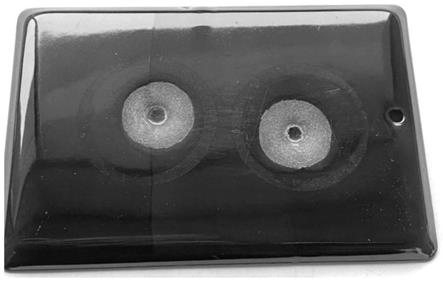
1.本发明属于搪瓷技术领域,具体涉及一种不含硝酸盐环保型钢板搪瓷低温耐酸底釉、制备方法及应用。
背景技术:
2.搪瓷瓷釉主要由长石、石英等耐火原料和硼砂、硝酸钠、硝酸钾、纯碱等易熔化工原料以及有色金属氧化物等特征原料,按照一定比例配合,经高温熔融,急剧冷却成粒状或片状的硼硅酸盐玻璃体制备而成。
3.搪瓷釉中引入硝酸盐(硝酸钠、硝酸钾等)作为氧化剂和助熔剂已经是业内人士的共识,在传统搪瓷理论中是必不可少的搪瓷釉原料。到目前为止,还没有一种安全、无色、价格合理既有氧化性又有助熔性原料替代硝酸盐。长期以来的生产实践证明,硝酸盐(特别是碱金属硝酸盐)的确是搪瓷釉中必不可以少的原料。
4.搪瓷瓷釉在高温熔制过程中,各原料之间进行着一系列复杂的物理化学反应。其中硝酸盐在高温下分解产生大量的氮氧化物,污染大气环境。氮氧化物超过国家排放标准40多倍,如果采用转炉生产,氮氧化物瞬间释放浓度超过国家标准几十万倍。众所周知,氮氧化物是空气中产生酸雨的主要因素,随着人们的环保意识增强,硝酸盐在搪瓷釉生产中释放的氮氧化物对环境的危害愈发引起各方高度的关注。
5.因此,氮氧化物达标排放、改善环境是企业刻不容缓的社会责任和社会经济发展的必然趋势,也是企业生存的必然选择。本技术人从2018年起就开始研究搪瓷釉料中去硝酸盐的用量,保证在不影响产品性能的前提下,尽可能不用或者少用硝酸盐,加上其它措施,使搪瓷瓷釉生产过程中的废气达标排放。
6.减少搪瓷瓷釉生产过程中氮氧化物的排放主要有三条技术路线:一是从源头去除或降低硝酸盐的使用,二是排除熔制过程中空气在高温状态下产生的氮氧化物,三是从治理设施上减少氮氧化物的排放,从而达到国家排放标准。
7.在此之前,也有在搪瓷瓷釉配方中单纯去掉硝酸盐的技术研究,但如果纯粹只是为了去硝酸盐而去硝酸盐,直接面临的结果是需要一定程度上牺牲产品的品质,这是因为对应的硝酸盐的助熔性和氧化性会没有得到相应的补充,即:一方面瓷釉配方中助熔剂减少了,直接影响瓷釉产品的瓷面平整性、流平性和膨胀系数;另一方面,由于硝酸盐具有氧化性,在瓷釉熔制过程中,去掉硝酸盐会导致瓷釉配方中的部分金属氧化物被还原,从而瓷釉发色以及密着性能会受到影响。
8.从助熔剂的角度考虑,以复合盐来替代硝酸盐作为瓷釉的原料配方,使用传统的熔制工艺进行熔制,有望使助熔效果得到替代。但是,去掉硝酸盐的使用会导致在瓷釉熔制过程中的氧化气氛减少,从而造成相应的金属氧化物部分被还原,这对瓷釉产品的色相和密着都会有影响。因此,去掉硝酸盐后,要保持瓷釉产品的原有性能,必须同时兼顾助熔效果和氧化效果的补充。
9.硝酸盐在搪瓷中的具体应用主要是硝酸钠和硝酸钾,在高温条件下,硝酸盐具有
良好的氧化作用,从而能够确保在熔制过程中氧化物不被还原成单质,同时,常见的硝酸盐硝酸钠和硝酸钾在高温下分解后的产物na2o和k2o具有很好的助熔作用。
10.目前已有部分去硝酸盐的研究探索。中国发明cn201810677390.4提供了一种磷硅酸盐搪瓷的制备技术,中国发明cn201010608133.9公开了一种高韧性搪瓷釉料,以它们为代表,均是探索直接用各种氧化物混合后进行熔制得到搪瓷产品,从而避免硝酸盐的使用。这对于理论研究而言或许是行得通的。然而在现有技术条件下,na2o和k2o没有工业化的产品,且其活性极其活跃,稳定性差,难以稳定存储。因此,直接以氧化钠、氧化钾等氧化物作为原料,目前无法实现产业化生产,因而不具有实用性。中国发明cn201310166353.4公开了一种用于搪瓷的抗高低温的瓷釉料,其配方中也不涉及硝酸盐的使用,但该发明为提升产品品质和降低烧结点,引入了重金属铅的使用,这完全违背了日常应用的安全性要求,也是行业禁止的,同时,其还涉及较大量的硫酸盐的使用,硫酸根的存在,即使含量很低,都极可能导致急冷环节发生爆炸,从而违背了安全生产的基本要求。此外,其配方中硼酸盐的含量较低,达不到搪瓷行业的基本要求。也就是说,该发明声称能够用于搪瓷,实际上即使不考虑前述缺陷也达不到搪瓷的条件。中国发明cn201711361365.7公开了一种亚光砂纹搪瓷釉核心釉料及生产方法,其所述的核心釉料看似不涉及硝酸盐的使用,但其本质为一种消光剂,需要与真正的釉料结合使用达到釉料的消光目的,不是独立的釉料,不可单独使用。此外,在“无硝酸盐搪瓷釉的初步实践”(谢学新,成都市新津金卧牛实业有限公司,玻璃与搪瓷.2007,35(1).)中,为了强化氧化作用,该文献采用了加大空气流量的方法,尽管没有涉及硝酸盐的使用,但其出发点并不是为了减少氮氧化物,而是为了解决含ti面釉的充分氧化问题,出于这个目的,其通过加大空气流量的技术手段来实现。然而,空气流量增大,会对熔制炉有明显的降温作用,为了使得熔制炉温度达到要求,需要增加能耗提升熔制炉的反应温度,且空气中含有大量的氮气,在高温作用下,通入大量空气会导致更多氮氧化物的生成。研究实践表明,空烧熔制炉会导致氮氧化物的含量超过国家排放标准的2倍以上。如果大流量通入空气,其结果更是可想而知。因此,该文献虽然避免了硝酸盐的使用,但最终反而加剧了氮氧化物的产生,与降低或消除氮氧化物的目的背道而驰。
11.综上所述,在搪瓷研究中,去掉硝酸盐提升环境效益的同时,又能保持搪瓷产品的优良品质,既意义重大又任务艰巨。
技术实现要素:
12.为了解决上述技术问题,本发明提供一种既解决搪瓷釉料生产过程中排放氮氧化物污染环境的问题,又能保证瓷釉原有的理化性能保持不变的不含硝酸盐环保型钢板搪瓷低温耐酸底釉、制备方法及应用。
13.本发明采用的技术方案是:一种不含硝酸盐环保型钢板搪瓷低温耐酸底釉,其配方由如下按质量份计的组份构成:石英47-51份,零水硼砂20-25份,纯碱 7-9份,氧化锰2.2-2.4份,氧化镍0.5-0.7份,氧化钴0.7-0.9份,碳酸钙4.5-5.5份,氟硅酸钠1.5-2.5份,钛白粉1.5-2.5份,钾长石1.2-1.8份,碳酸锂4-6份,萤石1.5-2.0份。
14.上述的不含硝酸盐环保型钢板搪瓷低温耐酸底釉中,石英中sio2的质量占比≥99.5%,钾长石中sio2的质量占比≥71%,萤石中氟化钙的质量占比≥95%,钛白粉中二氧化钛的质量占比≥99.0%,氧化钴中co的质量占比≥71%,氧化镍中ni的质量占比≥71%,其他
原料为工业级纯度。
15.一种上述的不含硝酸盐环保型钢板搪瓷低温耐酸底釉的制备方法,包括如下步骤:(1)按如下各组分的质量份称取原料;石英47-51份,零水硼砂20-25份,纯碱 7-9份,氧化锰2.2-2.4份,氧化镍0.5-0.7份,氧化钴0.7-0.9份,碳酸钙4.5-5.5份,氟硅酸钠1.5-2.5份,钛白粉1.5-2.5份,钾长石1.2-1.8份,碳酸锂4-6份,萤石1.5-2.0份;(2)将步骤(1)所述原料搅拌混合均匀;(3)将混合均匀后的物料加入熔制炉中熔制,熔制时熔制炉中采用纯氧环境,温度控制在1230
±
10℃;(4)待步骤(3)所述物料完全熔融后得到硼硅酸盐玻璃体,将熔融的硼硅酸盐玻璃体打钎,并快速拉成 1.2~1.5米的玻璃丝进行检测,检测要求是:在玻璃丝的1米内无节即为熔制完成;(5)将熔制好的硼硅酸盐玻璃体急冷,即得产品。
16.上述的不含硝酸盐环保型钢板搪瓷低温耐酸底釉的制备方法中,步骤(5)中所述急冷是采用水淬或压片的工艺方法。
17.一种上述不含硝酸盐环保型钢板搪瓷低温耐酸底釉的应用,应用于以钢板为基体的坯件上,成品的烧成温度为760-790℃。
18.本发明防止生产过程中排放氮氧化物的原理如下:以传统含硝酸盐钢板搪瓷瓷釉中常用的硝酸钠为例,硝酸盐在搪瓷釉生产中的化学反应为:硝酸盐在加热时分解,生成亚硝酸盐,并放出氧气,从而防止了金属氧化物在熔制时产生还原反应,使金属氧化物向低价态转变,甚至被还原为单质金属,由此改变搪瓷釉的成份和物理化学性能及工艺性能。
19.高温或者放电,都可以使氮气和氧气化合为no
x
。关于no
x
的生成机理是高温下空气中的n2氧化形成no,其生成速度与气体浓度、燃烧温度有很大关系。实践表明,温度达到1000℃以上,空烧熔制炉也会导致含量较高的氮氧化物生成。因此,本发明采用纯氧替代空气,一方面可以增加熔制过程中的氧化气氛,另一方面使燃烧过程中产生的氮氧化物零排放。
20.另一方面,本发明配方中通过调整非硝酸盐助熔剂的组分和用量,从而使搪瓷瓷釉中即使没有硝酸盐的助熔,也能够使熔制按照要求完成。这是本发明中关键技术创新点,即去除硝酸盐后,搪瓷釉中的助熔性仍然能够得到保证。
21.与现有技术相比,本发明的有益效果是:本发明将搪瓷釉料去硝酸盐化,并能实现产业化,既解决了搪瓷釉料生产过程中
排放氮氧化物污染环境的问题,又能保证瓷釉原有的理化性能保持不变。实验实践证明,当本发明申请人搪瓷釉料生产厂家80%的产品已经实现了不含硝酸盐,剩余近20%的产品尽管还做不到完全去除硝酸盐的使用,但也能保证硝酸盐的使用量降低50%以上。硝酸盐的使用量由原来的年使用量800吨降低到100吨左右,下降率接近85%。仅去硝酸盐一项每年直接减少氮氧化物排放量500吨,还不包括空气中氮气转化为氮氧化物的排放量。并且,去硝酸盐后产品的性能(瓷面、密着、流动度、耐酸、光泽)等方面均没有变化,达到国家搪瓷制品质量检测要求。因此,本发明技术方案具有极其重要的环保作用、社会效益和推广应用意义。
附图说明
22.图1是本发明的钢板搪瓷低温耐酸底釉应用于钢板制成的瓷釉打板的照片。
23.图2-4分别是本发明的钢板搪瓷低温耐酸底釉应用的检测报告1-3页。
具体实施方式
24.下面结合具体实施例对本发明作进一步详细的描述。
25.本发明实施例中所用设备为:配料:采用全自动配料、混合系统。该系统为全自动化电脑控制,具有称量准确、混合均匀、配料效率高的特点。
26.熔制:采用自动加料系统、纯氧燃烧系统、自动出料系统。由于去除硝酸盐后,氧化剂的作用也去除了,所以我们改进熔炉的燃烧条件,改为纯氧燃烧,使其虽然去除硝酸盐后,但氧化剂的作用同样达到要求。这也是该发明中关键的一点即去除硝酸盐,但氧化剂的性能没有改变。
27.包装:采用自动包装系统。
28.实施例1(1)按如下各组分的质量份称取原料:石英49.2kg,零水硼砂24.1kg,纯碱 7.0kg,氧化锰2.3kg,氧化镍0.6kg,氧化钴0.8kg,碳酸钙5.3kg,氟硅酸钠1.9kg,钛白粉2.0kg,钾长石1.2kg,碳酸锂4.4kg,萤石1.7kg。
29.石英中sio2的质量占比≥99.5%,钾长石中sio2的质量占比≥71%,萤石中氟化钙的质量占比≥95%,钛白粉中二氧化钛的质量占比≥99.0%,氧化钴中co的质量占比≥71%,氧化镍中ni的质量占比≥71%,其他原料为工业级纯度。
30.(2)将上述原料搅拌混合均匀。
31.(3)将混合均匀后的物料加入熔制炉中熔制,采用纯氧燃烧方式,温度控制在1230
±
10℃熔制。
32.(4)待上述物料完全熔融后得到硼硅酸盐玻璃体,将熔融的硼硅酸盐玻璃体打钎,并快速拉成 1.2~1.5米的玻璃丝进行检测,检测要求是:在玻璃丝的1米内无节即为熔制完成。
33.(5)将熔制好的硼硅酸盐玻璃体水淬,即得产品。
34.实施例2本实施例与实施例1的制备过程基本相同,不同之处在于:步骤(1)中各组分的质
量份是:石英49.2kg,零水硼砂21.9kg,纯碱 7.4kg,氧化锰2.3kg,氧化镍0.6kg,氧化钴0.8kg,碳酸钙5.0kg,氟硅酸钠2.0kg,钛白粉2.0kg,钾长石1.5kg,碳酸锂4.4kg,萤石1.7kg。
35.步骤(5)中,将熔制好的硼硅酸盐玻璃体急冷是采用压片的工艺方法。
36.实施例3本实施例与实施例1的制备过程基本相同,不同之处在于:步骤(1)中各组分的质量份是:石英49.2kg,零水硼砂20.8kg,纯碱 7.7kg,氧化锰2.3kg,氧化镍0.6kg,氧化钴0.8kg,碳酸钙4.7kg,氟硅酸钠2.5kg,钛白粉2.0kg,钾长石1.8kg,碳酸锂4.4kg,萤石1.7kg。
37.实施例4本实施例与实施例1的制备过程基本相同,不同之处在于:步骤(1)中各组分的质量份是:石英47kg,零水硼砂25kg,纯碱 9kg,氧化锰2.2kg,氧化镍0.5kg,氧化钴0.9kg,碳酸钙5.5kg,氟硅酸钠1.5kg,钛白粉2.5kg,钾长石1.8kg,碳酸锂4kg,萤石1.5kg。
38.实施例5本实施例与实施例1的制备过程基本相同,不同之处在于:步骤(1)中各组分的质量份是:石英51kg,零水硼砂20kg,纯碱 7.7kg,氧化锰2.4kg,氧化镍0.7kg,氧化钴0.7kg,碳酸钙4.5kg,氟硅酸钠2kg,钛白粉1.5kg,钾长石1.8kg,碳酸锂6kg,萤石2kg。
39.本发明制备的产品应用于以钢板为基体的坯件上,成品的烧成温度为760-790℃。
40.图1是本发明实施例2制备的钢板搪瓷低温耐酸底釉应用于钢板制成的瓷釉打板的照片。其瓷面平整细腻,密着ⅰ级,耐酸双a级,颜色均匀美观,色相完全达到了用户的要求。
41.图2-4为本发明实施例2制备的钢板搪瓷低温耐酸底釉应用的检测报告的1-3页。检测单位为国家眼镜与玻璃检测中心。
42.实验及检测结果证明,采用本发明方法生产的不含硝酸盐环保型钢板搪瓷低温耐酸底釉,在制备过程中无氮氧化物产生,所得产品的各项性能(瓷面、光泽、白度、色相、烧成温度)等都满足钢板搪瓷低温耐酸底釉要求,实现了环保型钢板搪瓷低温耐酸底釉去除硝酸盐的目的,从根本上解决了现有钢板搪瓷低温耐酸底釉在生产加工过程中产生氮氧化物(no
x
)气体排放污染环境的技术难题。
再多了解一些
本文用于企业家、创业者技术爱好者查询,结果仅供参考。