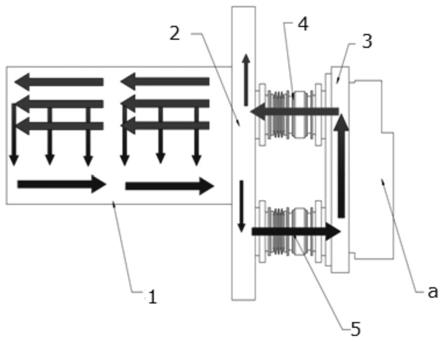
1.本发明涉及一种分离绝缘相变散热器及其散热方法。
背景技术:
2.伴随着电力电子、轨道交通、绿色能源、通讯、医疗设备等市场领域的电子元件的飞速发展:
①
电子器件的封装密度不断地提高,其热流密度不断地增大;
②
电子产品向微型化方向不断发展,功率更大而外形尺寸日益缩小;
③
电子产品散热需求越来越大。电子产品的这些发展趋势使得电子设备过热的问题越来越突出。
3.而电子设备的过热是电子产品失效(高温对电子产品的影响:绝缘性能退化;元器件损坏;材料的热老化;低熔点焊缝开裂、焊点脱落。且高温会降低电容器的使用寿命;使变压器、扼流圈绝缘材料的性能下降;还会造成焊点合金结构的变化—imc增厚,焊点变脆,机械强度降低;结温的升高会使晶体管的电流放大倍数迅速增加,导致集电极电流增加,又使结温进一步升高,最终导致元件失效)的主要原因之一,严重地限制了电子产品性能及可靠性的提高,也降低了设备的可靠性及工作寿命。因此电子设备内的温升必须予以控制,而运用良好的散热措施(散热技术、散热材料和性能优异的散热器)是解决散热问题的关键。
4.现在常规的风冷散热主要为强制风冷散热和自然对流散热,通过风扇等其它外力作用引起流体运动散热,称为强制对流散热;强制风冷散热常采用风扇强制流体流经散热器,通过流体与散热器的热交换将热量带出系统外。散热器多为铝挤型材散热器、压铸散热器或插翅、铲翅散热器。通过散热器材料自身传导将发热元件产生热量传递至翅片,并通过翅片与流过散热表面的空气流体,将热量交换散失掉,并通过空气对流将热量带出系统外。伴随发热元件发热量越来越大,热流密度越来越高,常规散热器由于材料和结构局限越来越难以满足散热需求。常规散热器,材料一般为铝或铝合金,通过铝挤及压铸成型,并通过nc加工完成结构形状。发热元件紧贴散热器基板,沿流道方向生成散热翅片(如图1所示,其中a为发热元件,b为基板,c为翅片)。根据散热需求设置翅片间距和高度及厚度;由于铝或铝合金材料导热系数在100~220w/m.k之间,与发热元件接触基板热传导能力及均温性较差,热温度场高温区主要集中在发热元件区域。且由于铝或铝合金材料导热性能较差,在翅片相对基板的z方向形成较大温度梯度。常规空气对流散热器热交换系数一般在5~25w/(m2*k),致使自然对流散热器的外形尺寸较大,重量较重,且由于常规自然对流散热器多为铝或铝合金材质,导热系数一般在10~220w/m.k,其热传导和热交换性能较差。且在电力电子、轨道交通、绿色能源、通讯、医疗设备等领域,出于安全性考虑散热器与电子器件间要实现绝缘耐压要求(》5000v)。
技术实现要素:
5.为解决以上现有技术存在的问题,本发明提出一种分离绝缘相变散热器及其散热方法。
6.本发明可通过以下技术方案予以实现:
7.本发明的一种分离绝缘相变散热器,包括相变功能基板组件、工质绝缘通道组件、相变换热器组件,其中,所述相变换热器组件由散热相变基板、相变翅片、换热翅片、换热器侧板组成;所述工质绝缘通道组件分为蒸汽绝缘通道和冷凝回流绝缘通道,所述功能相变基板组件由功能相变基板壳体、功能相变基板毛细结构、功能相变基板盖板组成。
8.进一步地,所述相变换热器组件为板式换热器或管式换热器。
9.进一步地,所述板式换热器或管式换热器的左右两端为换热器侧板,换热器侧板内设置若干所述相变翅片,所述相变翅片间设置若干换热翅片。
10.进一步地,所述相变翅片内留有相应蒸汽通道和工质冷凝液体流动通道,所述换热翅片为0.05~0.5mm厚铝波片。
11.进一步地,所述功能相变基板壳体采用铝或铝合金材料,通过cnc加工,铝挤成型并辅助nc加工而成,且设有不少于1个散热相变基板蒸汽通道孔,不少于1个散热相变基板冷凝液回流通道孔,并间隔设有若干功能相变基板支撑加强结构,其通过tig焊接与所述功能相变基板盖板及功能相变基板壳体焊接一体;所述相变换热器与功能相变基板盖板通过tig或mig密封焊接在一起。
12.进一步地,所述功能相变基板壳体内表面烧结有0.3~10mm球型颗粒的功能相变基板毛细结构,烧结毛细结构材料为铝或铝合金,烧结选用20~150目,烧结孔隙率10~90%。
13.进一步地,所述工质绝缘通道组件由散热器侧铝-不锈钢法兰,不锈钢波纹管,铜-不锈钢法兰,陶瓷组件,铜-不锈钢法兰,功能相变基板侧铝-不锈钢法兰依次密封焊接而成。
14.本发明还提出一种通过以上分离绝缘相变散热器实现的散热方法,包括:当电子元件工作运行发热时,热量传递至所述功能相变基板壳体表面,之后通过热传导将热量传递至所述功能相变基板壳体内表面所述功能相变基板毛细结构,所述功能相变基板毛细结构吸附相变工质吸收热量发生相变,由液态变为汽态;工质蒸汽沿功能相变基板蒸汽空腔流动,并流经蒸汽绝缘通道,流入相变换热器散热相变基板蒸汽空腔,并沿蒸汽空腔流动,后流入相变翅片蒸汽通道;经相变翅片热量均温传递给换热翅片,换热翅片与流经的空气流体进行热量交换,工质热量交换后相变冷却,由汽态变为液态,并通过毛细或重力流至换热翅片底部,并流回相变换热器的散热相变基板,并通过冷凝回流绝缘通道回流至功能相变基板,从而形成往复循环,将电子元件产生的热量带出系统外。
15.有益效果
16.本发明的分离绝缘相变散热器通过工质相变传热,充分利用了相变传热具有的高相变蒸发潜热、均温传热的物理特点,实现了功能相变基板和散热相变基板及相变翅片温度梯度分布的均温性,且有效降低了相变翅片垂直基板和流道方向温度梯度,从而改善了换热翅片表面温度,并使之分布更加均匀,大幅提升了换热器与空气流体的热交换效率。且蒸汽绝缘通道和冷凝回流绝缘通道实现了蒸汽与回流液体的分离,有利于改善相变传热性能,从而提升整个散热器的散热性能。另蒸汽绝缘通道和冷凝回流绝缘通道实现了从功能相变基板到散热相变基板的耐压绝缘(》5000v)需求。
附图说明
17.图1为现有的散热器结构示意图;
18.图2为本发明分离绝缘相变散热器的结构示意图;
19.图3为本发明分离绝缘相变散热器的侧视图;
20.图4为本发明中相变散热器的结构示意图;
21.图5为本发明中工质绝缘通道的结构示意图;
22.图6为本发明中功能相变基板的结构示意图;
23.图7为本发明中散热相变基板的结构示意图;
24.图8为本发明工作原理示意图。
具体实施方式
25.以下通过特定的具体实施例说明本发明的实施方式,本领域的技术人员可由本说明书所揭示的内容轻易地了解本发明的其他优点及功效。
26.如图2和3所示,本发明的一种分离绝缘相变散热器,由相变功能基板组件、工质绝缘通道组件、相变换热器组件三大功能模块组成。相变换热器组件由散热相变基板2、相变翅片1-2、换热翅片1-3、换热器侧板1-1及其它结构零件组成(如图4所示);工质绝缘通道组件分为蒸汽绝缘通道4和冷凝回流绝缘通道5,此组件由散热器侧铝-不锈钢法兰4-1,不锈钢波纹管4-2,铜-不锈钢法兰4-3,陶瓷组件4-4,铜-不锈钢法兰4-5,功能基板侧铝-不锈钢法兰4-6依次密封焊接而成(如图5所示);功能相变基板组件由功能相变基板壳体3-1、功能相变基板毛细结构3-2、功能相变基板支撑加强结构3-3、功能相变基板盖板3-4组成。
27.本实施例中,相变换热器组件可使用板式换热器(一体真空钎焊焊接而成)或管式换热器(气体保护钎焊而成),相变翅片1-2内留有相应蒸汽通道和工质冷凝液体流动通道。换热翅片1-3多为0.05~0.5mm厚铝波片,换热器左右两端为换热器侧板1-1。散热相变基板壳体2-2一般采用铝或铝合金材料,通过cnc加工,铝挤成型并辅助nc加工而成;散热相变基板壳体2-2加工不少于1个散热相变基板蒸汽通道孔2-3,且加工不少于1个散热相变基板冷凝回流通道孔2-4;并加工相应散热相变基板支撑加强结构2-5,后通过tig焊接将散热相变基板盖板2-1与散热相变基板支撑加强结构2-5焊接在一起(图7所示);之后将相变换热器与散热相变基板2通过tig或mig密封焊接在一起。密封后进行气压水检密封测试(测试压力》6.0kgf,保压》30min)。
28.本实施例中的工质绝缘通道组件的制作如下:
29.根据绝缘耐压要求选择不同外径(10~80mm)和厚度(2.0~20mm)的96白色氧化铝陶瓷管,在陶瓷管两端面进行金属化处理,金属化处理层厚度5μm~25μm;将金属化处理的陶瓷管两端通过真空钎焊将铜-不锈钢法兰的铜端侧密封焊接在一起,通过密封治具,进行氦质谱检漏,要求《1x10-8
mbar.l/s;之后通过tig或电子束或大功率激光,将密封焊接好铜-不锈钢法兰的陶瓷组件两侧的不锈钢端,与不锈钢波纹管(根据产品需求可在一端或两端焊接不锈钢波纹管)密封焊接在一起,之后将铝-不锈钢法兰的不锈钢端与不锈钢波纹管密封焊接在一起;再进行氦质谱密封检漏,要求《1x10-8
mbar.l/s。
30.功能相变基板壳体3-1一般采用铝或铝合金材料,通过cnc加工,铝挤成型并辅助nc加工而成;并加工不少于1个功能相变基板蒸汽通道孔3-5,且加工不少于1个功能相变基
板冷凝回流通道孔3-6;加工相应功能相变支撑加强结构3-3,并在功能相变基板壳体内表面烧结0.3~10mm球型颗粒厚度毛细结构,烧结毛细结构材料为铝或铝合金,烧结选用20~150目,烧结孔隙率10~90%。后通过tig焊接将功能相变基板壳体3-1与功能相变基板盖板3-4及功能相变支撑加强结构3-3焊接在一起(见图6所示)。
31.之后,将相变功能基板组件蒸汽通道孔3-5和冷凝回流通道孔3-6,通过tig或电子束或大功率激光,与工质绝缘通道组件的铝-不锈钢法兰4-6的铝法兰侧进行密封焊接。后将相变换热器组件的蒸汽通道孔2-3和冷凝回流通道孔2-4,通过tig或电子束或大功率激光,与工质绝缘陶瓷组件另一端的铝-不锈钢法兰4-1的铝法兰端进行密封焊接。通过工艺管进行氦质谱密封检漏,要求《1x10-8
mbar.l/s,后抽真空《1x10-3
pa,充灌工质,后通tig或电子束或大功率激光过密封工艺管。
32.如图8所示,本发明的分离绝缘相变散热器实现的散热方法,包括:当电子元件a工作运行发热时,热量传递至功能相变基板壳体3-1表面,之后通过热传导将热量传递至功能相变基板壳体3-1内表面功能相变基板毛细结构3-2,功能相变基板毛细结构3-2吸附相变工质吸收热量发生相变,由液态变为汽态;工质蒸汽沿功能相变基板蒸汽空腔流动,并流经蒸汽绝缘通道4,流入相变换热器散热相变基板蒸汽空腔,并沿蒸汽空腔流动,后流入相变翅片蒸汽通道;经相变翅片热量均温传递给换热翅片1-3,换热翅片与流经的空气流体进行热量交换,工质热量交换后相变冷却,由汽态变为液态,并通过毛细或重力流至换热翅片底部,并流回相变换热器的散热相变基板2,并通过冷凝回流绝缘通道5回流至功能相变基板3,从而形成往复循环,将电子元件产生的热量带出系统外。
33.以上所述仅为本发明的较佳实施例而已,并不用以限制本发明,凡在本发明的精神和原则之内所作的任何修改、等同替换和改进等,均应包含在本发明的保护范围之内。
再多了解一些
本文用于企业家、创业者技术爱好者查询,结果仅供参考。