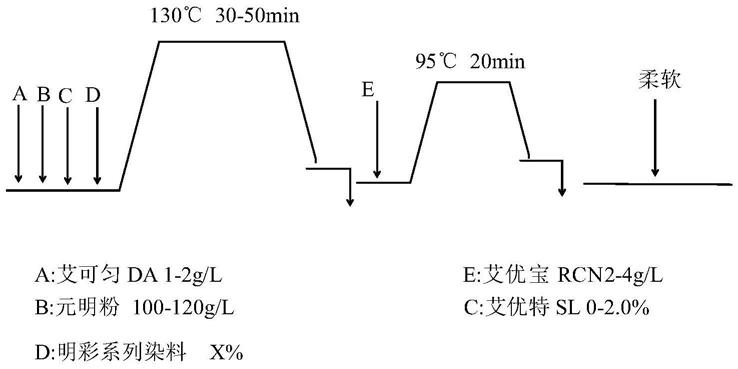
1.本公开属于纺织化学领域,尤其设置到一种涤棉织物一浴一步的染色方法,该染色方法能够显著的缩短传统涤棉染色时间,以及显著的减少排液次数,染色过程环境友好。
背景技术:
2.传统的涤棉织物是由棉纤维和涤纶纤维通过混纺方式制备获得,该织物进而具备了棉纤维的吸湿透气的性能以及涤纶纤维的挺括耐久性能,进而该织物的市场需求量极大。但是涤棉织物中的棉纤维和聚酯纤维是两种完全不同的化学结构,因此,在染色性能上差异明显。传统的对棉纤维的染色可以使用直接染料、活性染料、蒽醌染料等,但是对于涤纶纤维的染色,主要是分散染料;同时,两种纤维的染色条件也是不同的,对于棉纤维的染色,染色温度在100℃以下即可,但是对于聚酯纤维的染色条件,其必须在高温高压条件下染色,染色温度达到130℃。
3.基于棉纤维和涤纶纤维的性质,对于涤棉织物的染色分为一浴两步法、两浴两步法和一浴一步法,具体的一浴两步法是或者两浴法都是先对涤棉织物中的棉纤维进行染色,染色温度大概是60℃,对棉纤维染色完成后进行水洗,之后升温到130℃,对涤纶纤维进行染,之后进行后续的水洗处理。而一浴一步法染色,则是在染色的过程中加入染化料,之后升温至一定的温度,保温进行染色,在该染色条件下,同时对涤纶纤维和棉纤维进行附着上色,染色完成后进行皂洗水洗等操作。相较而言,一浴一步染色方法染色效率高,与一浴二步发相比,省略了染棉后的水洗过程,同时染色时间缩短,但是由于染浴中同的染化料性质不同,因此染色的均匀性和色牢度会受到较大影响,染色容易造成色差。
4.现有技术中,如公开号为:cn109505147a的发明专利公开一种新型的涤棉一浴一步染色方法,具体步骤如下:20-30℃情况下,在水中加入分散染料,染色25-35分钟;保持常温不变,在溶液中加入坎特缸差消除剂,浸泡30-35分钟;在溶液中加入活性染料以1-2.5℃/min加热到60℃,维持 10-20分钟;接着加入纯碱,在60℃下保温40-60分钟,将温度以2.5-3.5℃ /min的温度加热到130℃下保温30-50分钟;以2.5-3.5℃/min的温度降温到60℃,加一浴皂洗剂浸泡10-20分钟,再将温度降至20-30℃进行清洗。但是该工艺的所有时间远超过到270min,如果算上水洗时间,至少在6个小时之上,同时该专利的工艺来看,其首先还是在低温条件下对棉纤维进行染色,之后在高温条件下进一步的染色,其相对于传统的一浴二步法能显著的缩短染色时间。虽然其在时间上显著缩短,但是由于工艺信息,难以确认其染色效果。
5.基于现有技术中存在的涤纶染色所存在的能耗高、效率低以及染色品质问题,本公开提供了一种新型涤棉织物一浴一步染色方法,该染色方法用以解决传统染色的能耗、污染、效能以及染色均匀性问题。
技术实现要素:
6.本公开旨在提供一种涤棉织物一浴一步染色方法,所述染色方法的相较于传统涤
棉染色方法而言,具有染色效率高、染色均匀、能耗少、染后废液排放少等优势。
7.具体的,本公开的构思在于提供一种涤棉织物一浴一步染色方法,包括首先在高温条件下进行染色,使涤纶纤维和棉纤维同时染色,后续工艺中,重新升温对棉织物进行调整染色,该染色方法能够保证染色均匀和色牢度。
8.本公开的另一构思在于,染色工艺中对涤棉织物染色完后进行溢流冲洗,染浴中的染液不用排放,之后进行棉织物的皂洗调色(固色),可以减少染液排放,染色环境友好性优势明显。
9.本公开的另一构思在于,染色工艺在完成棉染色后,直接水洗即可进行柔软出缸,染色的废液排放减少、效率提高。
10.本公开的另一构思在于,染色工艺中涤棉同浴染色,其中涤纶在碱性条件下染色,得到的织物柔然性更好。
11.本公开的另一构思还在于,染色工艺将涤棉织物的染色前处理、染涤纶、染棉合并为一步完成,进一步的将染色的效率进行提高。
12.本公开的另一构思还在于,染色工艺中染色助剂的用量显著降低,在染色废液的排放中,cod的含量显著降低。
13.本公开的另一构思在于,染色工艺中使用的染料为分散染料与活性染料的复配,在染色工艺中,活性染料和分散染料配比方便,操作简便。
14.本公开的另一构思还在于,在涤棉织物染色后,使用阴离子型的皂洗剂对涤棉织物进行皂洗调色(固色),能够确保涤棉织物的染色均匀和色牢度提高。
15.本公开的另一构思还在于,染色工艺的加料次数显著减少,排液量显著减少。
16.具体的,本公开涉及一种涤棉织物一浴一步染色方法,其特征在于,包括如下操作步骤:
17.步骤(1)染化料调配;
18.具体的,染缸中加入染色助剂和染料;
19.所述的染色助剂为元明粉;
20.所述的元明粉为70-130g/l;
21.更具体的,所述的元明粉用量根据染色深度进行调整;
22.进一步的,当染色深度小于0.2%,元明粉的用量为70-90g/l;
23.当染色深度为0.2-0.5%,元明粉的用量为90-105g/l;
24.当染色深度为0.5-1%,元明粉的用量为105-120g/l;
25.当染色深度大于1%,元明粉的用量为120-130g/l;
26.更具体的,当深度大于1%,元明粉的用量为120g/l。
27.此处需要说明的是染色深度主要是在染色过程中染料的加入用量,本公开后续的对于染色深度的都沿用此处的解释。
28.本公开使用的染色助剂主要为元明粉,并且在染色进行前加入该染色助剂,该染色助剂在染色过程中,一部分能够对涤棉织物进行前处理,减少织物上的油脂和杂质,另一方面在染色过程中,元明粉是一种电解质,而棉织物在染浴中带有负电荷,元明粉的加入能够改善染浴的电荷性,降低棉纤维的zeta 电位,促进活性染料向棉纤维的吸附,进而能够明显的缩短染色时间。
29.但,
30.元明粉具有快速的将染料吸附到棉纤维上效果,并在一定高温条件下,染料能够迅速的扩散到纤维内部,但是本公开的染色工艺的构思之一是在高温条件下对涤纶和棉同时进行染色,染料的活性较高,如果棉的上染不均匀,必然造成染色疵点和不均匀,因为,本公开对染染色助剂的加入量进行严格的控制,通过染色的深度,来控制染色助剂的用量,确保在高温条件下染棉的过程能够均匀,提高染色后织物的品质。
31.更在于,本发明所使用的元明粉的用量与染料有直接的关系,具体的说明见后续对染料的说明。
32.进一步的,本公开在染缸中加入染料;
33.所述的染料,所述的染料为分散染料和活性染料复配获得;
34.所述的复配染料适合不配比,调色方便;
35.所述的活性染料具有多个活性基团;
36.所述的活性基团包括卤代均三嗪基、卤代嘧啶基、乙烯砜基、羧基吡啶均三嗪基、膦酸基中的至少两种。
37.所述的代均三嗪基为一氯均三嗪、二氯均三嗪中的一种;
38.针对本公开的染色工艺,本公开对原料进行了特定的限定,尤其是活性染料,需要保证该染料在高温条件先能够具有较好的稳定性、上染性、匀染性,因此,本公开使用的活性染料至少包括两种活性基团的活性染料。
39.同时,
40.该多活性基团的活性染料在染色过程中,由于分子量的扩大,染料结构的变化,上染速度受到较大的限制,在基于前述的染色助剂条件下,能够在高温的条件下,保证合适的吸附和在纤维内部扩散性能,达到高温条件下能够均匀染色效果。
41.另外,本公开所使用的活性染料,在高温条件下的稳定性优良,水解率较低。
42.更进一步的,所述的染料的用量为0-5%,优选为0-4%。
43.在一些实施例中,所述的染料为明彩系列染料;
44.所述明彩系列染料包括明彩t系列和明彩c系列。
45.其中所述的明彩t系列为分散染料,明彩c系列为活性染料;
46.更具体的,所述的明彩t系列单色染色的皂洗牢度大于4-5级,测试标准为iso105-c03;
47.所述的明彩t系列的摩擦牢度大于3-4级,测试标准为iso105-x12;
48.所述的明彩t系列的日晒牢度大于5级,测试标准为iso 105-b01;
49.所述的明彩t系列的升华牢度大于3级,优选的大于4级,测试条件180℃, 30s。
50.更具体的,所述的明彩c系列单色染色的皂洗牢度大于4-5级,测试标准为iso105-c03;
51.所述的明彩c系列的摩擦牢度大于3-4级,测试标准为iso105-x12;
52.所述的明彩c系列的日晒牢度大于5级,测试标准为iso 105-b01;
53.所述的明彩c系列的汗渍牢度大于3级,优选的大于4级,测试标准iso 105-e04。
54.更进一步的,所述的明彩t系列和明彩c系列的配伍性优异。
55.更进一步,在步骤(1)中,本公开无需加入碱液和/或酸。
56.在传统一浴二步法染涤棉的过程中,首先是对涤纶部分进行染色,在染色过程中会加入酸,染色完后,保证涤纶在高温条件下不发生水解,在涤纶部分染色完成后,需要对染液进行调节。而本公开在染色过程中,由于涤纶和棉织物是同时染色,而活性染料的染色条件不能在酸性条件下进行,因此,本公开在步骤(1)中无需加入碱液和/或酸,在染色过程中,由于涤纶的水解情况,染浴会呈现弱碱性。
57.在一些实施例中,步骤(1)中的染色助剂还能够包括染色稳定剂。
58.具体的,所述的染色稳定剂为艾优特sl,艾优宝wdn;该助剂由山东艾文生物科技有限公司提供;
59.更进一步的,所述的染色稳定剂用量为0-2%,优选的为0.1-0.5%
60.优选的,所述的染色稳定剂的用量根据染色的深度进行控制,具体的,当染色深度为中深色时,染色稳定剂的用量为0.1-0.6%;
61.优选的,当染色深度为2%,染色稳定剂的用量为0.1-0.4%;
62.优选的,当染色深度为2-4%,染色稳定剂的用量为0.3-0.6%;
63.优选的,当染色深度4%,染色稳定剂的用量0.4-0.6%;
64.当染色深度为特深色时,染色稳定剂的用量为0.6-2.0%。
65.在一些实施例中,所述的染色稳定剂对于处理涤棉织物时,织物中棉的含量也会影响到染色稳定剂的用量,当棉的含量越多,染色稳定剂的用量越多。
66.具体的,t/c面料的整体光稳定剂用量要大于cvc面料。
67.染色稳定剂的加入,用于对染料的结构和吸附进行更稳定,主要是由于本公开的方案针对涤棉两种组分纤维均是在高温条件下进行上染,而活性染料由于化学结构活泼,高温条件下结构容易被破坏,染色稳定剂在一定程度下能够稳定活性染料的结构,保证染色后的织物显色效果优良。
68.另一方面,在染色时工作液呈碱性,涤纶纤维中的低分子副产物会迅速水解,而稳定剂的作用可以是的该水解产物不易形成低聚物,避免织物沾污;而在碱性条件下涤纶织物有一定的剥皮现象,会使涤纶织物手感更柔软。
69.在一些实施例中,步骤(1)中还包括加入前处理剂。
70.所述的前处理剂为艾可匀系列、艾丽尼系列中的一种或多种,上述前处理剂均出自于山东艾文生物科技有限公司。
71.进一步的,所述的艾可匀系列包括艾可匀da、艾可匀tc;所述的艾丽尼系列包括艾丽尼oz。
72.本公开使用前处理剂,该前处理剂在染色前加入到染缸,并且无需前处理后对染缸中的液体进行排放,该前处理剂随着温度的升高,能够高效的,在染色温度条件前,尤其是在染料对织物进行吸附和扩散条件前能够快速的处理掉涤棉织物中的杂质和油脂。
73.更进一步的,所述的前处理剂能够在染色温度对涤棉织物进行前处理。
74.优选的在低于130℃前进行前处理,更优选的在低于100℃进行前处理,更优选的在低于80℃前进行前处理。
75.所述的前处理剂在染色温度条件前失去活性。
76.进一步的,所述的前处理剂的用量为0.5-4g/l;优选为1-3g/l;
77.本公开使用前处理剂为艾可匀da,该处理剂高效快速的对涤棉织物进行前处理,
并且能够在高温条件下自动失去活性,确保染料向纤维吸附和扩散的过程中,前处理不对染色过程产生影响。
78.在一些实施例中,在加入前述的染化助剂加入的温度为20-60℃,所述的化料时间为10-20min。
79.在一些实施例中,步骤(1)中还加入待染色织物。
80.加入待染色织物为在化料完成后加入,所述的待染色织物为涤棉织物。
81.所述的涤棉织物为t/c涤棉织物,或cvc涤棉织物;
82.进一步的,所述的染色织物与染浴的浴比为1:5-1:20;优选的1:7-1:15;更优选的为1:8-1:12,更优选的为1:10。
83.在一些实施例中,所述的染色工艺包步骤(2)升温;
84.具体的,括对染缸中的染液进行升温,升温的速率为1-2.5℃/min。
85.本公开中,由于染浴中包括分散染料和活性染料,同时还包括前处理,因此,同时要保证前处理剂对涤棉织物的处理过程,如果升温速度过快,则前处理剂处理不急,染色效果会受到影响,过升温速度过慢,则会影响到染色效率,同时也会影响到染料向纤维的吸附,本公开发现在升温速率为1-2.5℃/min的条件下,染色效果较佳。
86.在一些实施例中,本工艺还包括步骤(3)上染染色;
87.更进一步的,升温至125-135℃,保温染色25-50min,染料对织物进行上染,后溢流冲洗。
88.所述升温至125-135℃的过程中,染料向棉纤维和涤纶纤维上染迁移。
89.在一些实施例中,可以在升温至125-135℃前,升温至50-80℃,保温 20-30℃,染料对织物进行上染;
90.所述的升温至50-80℃,主要是针对棉纤维进行上染。
91.本公开在步骤(3)中,保温20-50min的条件下,能够保证染料向织物的充分吸收和扩散,保证良好的上染率。
92.在染色完成后对织物进行溢流冲洗,溢流冲洗能够将织物上的浮色冲洗掉,有利于后续的皂洗效果。
93.进一步的,溢流冲洗后的温度降低到30-60℃。
94.在一些实施例中,染色工艺还包括步骤(4)皂洗;
95.具体的,在溢流冲洗完成后染缸中加入皂洗剂进行皂洗。
96.所述的皂洗剂用于对活性染料染色后的棉纤维进行皂洗,调色,由于活性染料的染料水解问题,一般情况是需要在碱性条件下在棉纤维上固色,而本公开的染色时在高温条件下进行,并且考虑到涤纶的水解问题,本公开并未加入碱液,而是选择了具有多活性基团的活性染料,该染料能够在中性条件下具有较佳的上染性能,但是在高温条件下,尤其是在130℃左右的染色条件下,染色介质(水)的分子活性活跃,也会使得活性染料发生一定的水解,而水解的染料是无法与棉发生化学反应而与棉纤维发生固着,进而会造成色牢度不佳的问题。
97.虽然本公开在染色过程中发现了这种问题,在染色前加入了染色稳定剂,在一定条件下能够有效的减小活性染料的水解,但是活性染料的水解也是无法完全阻止。
98.为了提高染色效果,本公开在染色过程完成后,仍然在溢流清洗后还加入了皂洗
剂,并进一步的对棉纤维进行皂洗调色(固色),将纤维上的浮色洗去,并提高染料的固着效果,从而达到较好的染色均匀性和色牢度。
99.优选的,本公开步骤(4)所使用的皂洗剂为山东艾文生物科技有限公司提供。
100.更具体的,所述的皂洗剂为艾可洁jx-g或艾优宝rcn。
101.在一些实施例中,所述的皂洗剂用量为1-5g/l,优选的为2-4g/l。
102.在一些实施例中,染色工艺还包括,步骤(4)加入皂洗剂后,对染缸的温度进行升温皂洗调色、固色,升温速率为1-3.5℃;升温至80-98℃,皂洗时间为10-30min。
103.在一些实施例中,染色工艺还包括,步骤(4)皂洗可以包括多个独立的皂洗步骤,具体的,可以包括两个皂洗步骤。
104.在一些实施例中,染色工艺还包括步骤(5)后处理,在皂洗完成后,将染液排放,并进行后处理。
105.所述的后处理包括柔软、抗菌等功能性整理。
106.在一些实施例中,本公开的染色工艺相较于传统工艺而言,成本显著降低,尤其是能耗和时间以及助剂成本。
107.具体的,染色时间约为5-7h;
108.能耗节约30%以上;
109.染色助剂成本节约20%以上。
110.本公开的有益效果在于,本公开使用一浴一步染色方法,尤其是使用染涤条件下进行染色,使活性染料和分散染料同时向涤棉织物染色,显著的降低了染色时间,相对于传统的涤棉染色,染色时间显著缩短,全工艺染色时间为6小时左右,相对于传统的12小时,缩短6小时左右。
111.另外一些有益效果在于,本公开一浴一步涤纶染色方法中所使用的染料进行了选择,所使用的染料体系的配伍性优良,明彩t系列和明彩c 系列配方稳定,易操作,效率高,调涤方便,互不影响色牢度,色光纯正。有卓越的洗水色牢度、日晒色牢度、摩擦色牢度、耐水泡色牢度和汗渍色牢度。
112.另外一些有益效果在于,本公开的一浴一步涤纶染色方法,在染缸开始即加入了前处理剂,在对涤棉织物进行染色前即能够完成涤棉织物的前处理,同时在染色条件下,该前处理剂不会对染色效果产生影响,这种前处理剂的加入,高效的缩短了涤棉织物的前处理时间。
113.另外一些有益效果在于,本公开的一浴一步涤纶染色方法,在染色完成后,对染色后的织物进行皂洗处理,所述的皂洗可以一次性皂洗,也可以多次进行皂洗处理。
114.另外一些有益效果还在于,本公开的整体的染色工艺,能够缩短染色时间大约6小时,能耗能够减少30%以上,染色成本节约20%以上。
附图说明
115.为了更清楚地说明本技术实施例或现有技术中的技术方案,下面将对实施例中所进行的实验进行说明和附图展示,对于本领域普通技术人员来讲,还可以根据这些附图获得其他的附图。
116.图1:本公开的一个具体实施例的涤棉一浴一步染色工艺;
117.图2:本公开的另一个具体实施例的涤棉一浴一步染色工艺;
118.图3:本公开的又一个具体实施例的涤棉一浴一步染色工艺;
119.图4:明彩系列单色染色效果;
120.图5:明彩t和明彩c在浅色、中色、深色的配伍性染色图;
121.图6:明彩t和明彩c在浅色、中色、深色的配伍性染色后织物的性能测试图;
122.图7:传统的一浴二步发染色工艺图;
123.图8:本公开的涤棉一浴一步染色工艺的成本测算图;
具体实施方式
124.为了使本领域的技术人员更好地理解本公开的技术方案,下面将结合附图对本公开作进一步的详细介绍。
125.本公开首先对本公开所使用的名词或试剂进行说明,
126.本公开的工艺是一种全新的工艺,改变原有的一浴二步法涤棉染色工艺。
127.本公开使用的染料、前处理剂、皂洗剂均由山东艾文生物科技有限公司提供;
128.本公开使用的染料为明彩t系列和明彩c系列。
129.本公开使用的前处理剂为艾可匀系列、艾丽尼系列;
130.其中,艾可匀系列包括艾可匀da、艾可匀tc;艾丽尼系列包括艾丽尼oz。
131.本公开使用的染色稳定剂为山东艾文生物科技有限公司提供;,
132.其中,染色稳定剂包括艾优特sl,艾优宝wdn。
133.本公开使用的皂洗剂为山东艾文生物科技有限公司提供;
134.其中,皂洗剂包括艾可洁jx-g或艾优宝rcn。
135.本公开所使用的上述试剂都是市面在售产品,本领域的技术人员可以联系上述生产商并可以购买上述试剂,因此,本公开对上述产品名称的使用是清楚的。
136.在一些实施例中,本公开了一种涤棉织物一浴一步染色工艺方法,具体的参见图1,包括如下步骤:
137.(1)染化料调配
138.首先在40℃条件下加入染化料,包括元明粉100-120g/l,染色稳定剂艾特优sl 0-2.0%,前处理剂艾可匀da 1-2g/l,明彩系列染料。
139.所述的染料根据需要的颜色可以进行调整,后续对于染料的染色,尤其的配伍性染色工艺中,即根据本公开实施例的方法进行染色获得。
140.染化料在40℃的条件下化料,化料时间为20min,化料完成后加入涤棉织物,涤棉织物的浴比为1:7-1:20。
141.步骤(2),之后升温,升温速率为1℃/min;
142.步骤(3),染色,升温至130℃,染色30min,染色完成后降温,溢流冲洗。
143.步骤(4),皂洗
144.溢流冲洗后,加入皂洗剂,皂洗剂为艾优宝rcn,用量2-4%,之后升温至95℃,皂洗调色固色20min.
145.步骤(5)后处理,在皂洗完成后,将染液排放,并进行后处理。
146.后处理为水洗、柔软处理。
147.在一些实施例中,根据上一实施例,本公开实施例可以对上述实施例中的前处理进行替换为艾丽尼oz,艾可匀tc。
148.在一些实施例中,根据上一实施例,本公开实施例可以对上述实施例中的皂洗剂替换为艾可洁jx-g。
149.在一些实施例中,根据上一实施例,本公开实施例可以对上述实施例中的染色稳定剂替换为艾优宝wdn。
150.在一些实施例中,根据上一实施例,本公开可以进行两次皂洗,具体的染色工艺可以参见附图2,该染色工艺用时360min,即6个小时。
151.其中附图2的工艺流程,本领域的技术人员根据前述实施例可以足以理解具体操作。
152.在一些实施例中,具体参见附图3的工艺流程,本领域的技术人员根据前述实施例可以足以理解具体操作。
153.在一些实施例中,本公开还对明彩t和明彩c两个系列的染料进行单一的染色实验,染色效果参见图4,其中染色浴比为1:10,对染色后的织物进行染色性能测试,测试包括所述的明彩系列单色染色的皂洗牢度大于 4-5级,测试标准为iso105-c03;
154.明彩系列的摩擦牢度测试标准为iso105-x12;
155.明彩系列的日晒牢度测试标准为iso 105-b01;
156.明彩系列的升华牢度测试条件180℃,30s。
157.明彩系列的摩擦牢度测试标准为iso105-x12;
158.明彩系列的日晒牢度测试标准为iso 105-b01;
159.明彩系列的汗渍牢度测试标准iso 105-e04。
160.明彩t系列单色染色的皂洗牢度大于4-5级,摩擦牢度大于3-4级,日晒牢度大于5级,升华牢度大于3级,优选的大于4级。
161.所述的明彩c系列单色染色的皂洗牢度大于4-5级,摩擦牢度大于3-4级,日晒牢度大于5级,汗渍牢度大于3级,优选的大于4级。
162.从两种染料的染色后的颜色效果来看,明彩c和明彩t两个系列染料对织物染色后的颜色十分接近,可以看出,明彩c和明彩t两个系列的染料的配伍性优异,可以混合染色,染出颜色均一的涤棉织物。
163.在一些实施例中,本公开使用两种染料进行配伍,并进一步的对织物进行深色、中色和浅色的染色,染色织物为65/35的t/c涤纶织物,浴比为1:10,染色温度为130℃。
164.其中一个实施例的浅色的配方为明彩克斯黄t-hf/明彩克斯红t-hr /明彩克斯蓝t-hb各0.1%;明彩素黄c-ay/明彩素红c-ar/明彩素蓝 c-ab各0.1%。
165.其中一个实施例的中色的配方为明彩克斯黄t-hf/明彩克斯红t-hr /明彩克斯蓝t-hb各0.3%;明彩素黄c-ay/明彩素红c-ar/明彩素蓝 c-ab各0.3%。
166.其中一个实施例的深色配方为明彩克斯橙t-e/明彩克斯红玉t-2r/ 明彩克斯藏青t-nf各0.7%;明彩素橙c-e/明彩素红玉c-2r/明彩素藏青 c-nf各0.7%。
167.从两种染料的染色后的颜色效果来看,明彩c和明彩t两个系列染料对织物染色后的颜色十分接近,可以看出,明彩c和明彩t两个系列的染料的配伍性优异,可以混合染色,染出颜色均一的涤棉织物。
168.染色的结果见图5(配伍性)。
169.可见,对于浅色、中色、深色的染色,其染色的均匀性优良,并不存在色差,尤其是深色的染色,效果非常优异。
170.在一些实施例中,本公开还对上一实施例获得的浅色、重色、深色织物进行色牢度测试,具体测试结果件图6;
171.其中,皂洗牢度4-5级,摩擦牢度4级,日晒牢度6级,酸性汗渍牢度 4-5级,碱性汗渍牢度4-5级,升华牢度4级。
172.可见,本公开使用的染料的配伍性能优异。
173.在一些实施例中,对于传统的涤棉染色参见附图7,具体的操作是首先对织物进行前处理,包括去油(前处理)步骤,加入前处理剂,主要是碱性或表面活性剂,之后进行升温,升温至98℃,保温15min,对织物上的油脂和杂质去除。
174.前处理完成后降温水洗,排液,之后加入分散染料,升温到130℃,染色30分钟左右,对涤纶进行染色,染色完成后进行水洗、酸洗等一些列的过程。
175.对涤纶组分染色完成后,之后加入活性染料和其他助剂,助剂包括元明粉和纯碱,对涤棉织物中的棉纤维进行染色,升温至60-90℃,染色完成后,进行水洗,皂洗等工艺。
176.在一个实施例中,将本公开的一个实施例,参见附图1的实施例,与本公开的另一实施例,参见附图7的实施例进行比对,得到两个实施例的费用成本,具体的可参见附图8。
177.从图8的测算可以看出,平均每一缸的染色过程中,相对于传统的工艺而言,本公开的时间节约5-6小时,能耗能够降低100-1500元/缸,助剂成本能够节约300-400/缸。
178.以上只通过说明的方式描述了本公开的某些示范性实施例,毋庸置疑,对于本领域的普通技术人员,在不偏离本公开的精神和范围的情况下,可以用各种不同的方式对所描述的实施例进行修正。因此,上述附图和描述在本质上是说明性的,不应理解为对本公开权利要求保护范围的限制。
再多了解一些
本文用于企业家、创业者技术爱好者查询,结果仅供参考。