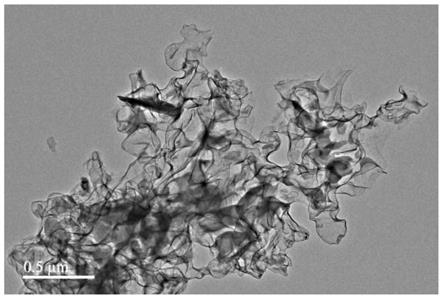
1.本发明属于高分子材料技术领域,特别是涉及一种薄绸状掺氮炭的制备方法。
背景技术:
2.随着我国对绿色新能源的发展和应用日益迫切,电极材料的需求和发展也层出不穷。碳质材料由于具有优良的物理化学稳定性和不错的导电性,在电极材料中始终占有一席之地。活性碳质材料发展较为成熟,长期以来作为电容电极材料被广泛应用。随着石墨烯的发现,科研人员大都将目光凝聚在石墨烯类材料的开发、改性,并将其应用于电化学储能元器件中。石墨烯成为了超级电容器或锂离子电子容器中的明星电极材料。
3.活性炭长期以来大都以煤基或生物质为碳前驱体,通过物理或化学活化造孔,来获得具有不同比表面积的活性炭。然而得到的均为微孔,大功率充放电时,内部的孔道无法得到有效的利用。
4.目前石墨烯或碳纳米片的制备方法多集中于机械剥离、化学剥离和气相沉积法,其中气相沉积法已经得以初步工业化。其中机械剥离无法实现规模化制备,化学剥离需要使用强酸和强氧化性物质,对设备要求高,且危险性较大,试剂容易造成环境污染。气相沉积法通常用小分子气态碳源如甲烷、乙烯、丙烯等,造价昂贵且存在易燃易爆危险性。其次,需要使用大量的模板剂,对模板剂的回收利用又是一个新的挑战。
5.掺杂可以提高碳质材料的导电性和浸润性,通常对碳材料的掺杂都通过将碳材料和杂原子前驱体混合,高温煅烧获得,步骤繁琐,且需要再次经过纯化。
6.因此,寻找一个工艺简单,成本低,环境友好的薄层掺氮炭的制备方法是很有必要的。
技术实现要素:
7.目前薄层石墨烯造价较高,且容易聚并,不利于电解液的传输和离子储存,导致其无法发挥出全部的容量。活性炭孔结构丰富,但是其导电性不足,且丰富的体相孔在大电流时得不到有效的利用。高品质活性炭造价较高。本发明以一种步骤简单的环境友好的方式制备薄绸状掺氮多孔炭,降低成本,简化工艺的同时解决了石墨烯的聚并问题和活性炭孔的高效利用问题,同时还具有良好的导电性和优良的浸润性,满足其作为锂电负极或其他大功率储能元器件的需要。
8.为解决上述技术问题,本发明采用的一个技术方案是:一种薄绸状掺氮炭的制备方法,包括以下步骤:
9.(1)将高温自流动性的碳前驱体粉末重油残渣与石墨相氮化碳直接机械混合;
10.(2)或将液态的廉价碳前驱体与石墨相氮化碳粉末直接搅拌混合成粘稠状;
11.(3)将上述混合物质高温煅烧,在此过程中,碳前驱体借助流动性自包覆在模板表面并裂解碳化,冷却后直接得到薄绸状掺氮炭。
12.进一步地说,所用石墨相氮化碳粉末的制备方法为:将尿素或三聚氰胺置于马弗
炉中,慢速升温至550℃煅烧2~4h,得到淡黄色的石墨相氮化碳。
13.进一步地说,所述步骤(3)中,高温煅烧的环境为在氮气的保护下。
14.进一步地说,所述步骤(1)中,碳前驱体粉末重油残渣为沥青。
15.进一步地说,所述步骤(2)中,液态的廉价碳前驱体为煤焦油或渣油。
16.进一步地说,在所述步骤(1)中,通过混合装置实现碳前驱体粉末重油残渣与石墨相氮化碳的机械混合。
17.进一步地说,所述混合装置包括:
18.立式混合罐,所述立式混合罐顶端呈敞口式设置;
19.搅拌机构,所述搅拌机构安装于所述立式混合罐底端。
20.进一步地说,所述搅拌机构包括:
21.搅拌座,所述搅拌座固定安装于所述立式混合罐底端;
22.转动室,所述转动室设于所述搅拌座内;
23.气囊安装室,两个所述气囊安装室以所述转动室为中心对称设于所述搅拌座内;
24.搅拌轴,所述搅拌轴位于所述立式混合罐内,所述搅拌轴底端穿设所述立式混合罐底端,并伸入所述转动室内;
25.搅拌杆,所述搅拌杆位于所述立式混合罐内,多个所述搅拌杆均匀连接于所述搅拌轴上;
26.搅拌电机,所述搅拌电机安装于所述转动室内底部;
27.永磁棒,所述永磁棒位于所述转动室内,所述永磁棒一端与所述搅拌轴底端连接,所述永磁棒另一端与所述搅拌电机输出端连接;
28.带阀进气口,两个所述带阀进气口对向开设于所述搅拌座侧端,所述带阀进气口连通于所述气囊安装室内,所述带阀进气口上安装有单向阀;
29.带阀出气口,多个所述带阀出气口分布于所述搅拌座顶端,所述带阀出气口连通于所述气囊安装室和立式混合罐底端之间,所述带阀出气口上安装有单向阀;
30.外弹性囊体,所述外弹性囊体安装于所述气囊安装室内,所述外弹性囊体内填充有导热油;
31.内弹性囊体,所述内弹性囊体固定安装于所述外弹性囊体内顶部和底部之间;
32.贮气囊体,两个所述贮气囊体对向安装于所述转动室内壁上,所述永磁棒位于两个所述贮气囊体之间;
33.永磁板,所述永磁板嵌设于所述贮气囊体靠近永磁棒端,所述永磁板适配所述永磁棒设置;
34.气管,所述气管一端伸入所述转动室内,并与所述贮气囊体连通,所述气管另一端伸入所述气囊安装室内,并穿设所述外弹性囊体、与内弹性囊体连通;
35.摩擦盘,所述摩擦盘位于所述转动室内,所述摩擦盘固定连接于所述搅拌电机输出端;
36.摩擦块,两个所述摩擦块对向安装于所述转动室内壁上,所述摩擦块位于所述贮气囊体下方,所述摩擦盘位于两个所述摩擦块之间,所述摩擦盘贴靠所述摩擦块设置,所述摩擦块内设空腔,所述空腔内储存有导热油;
37.带阀进油管,所述带阀进油管一端伸入所述气囊安装室内,并与所述外弹性囊体
连通,所述带阀进油管另一端伸入所述转动室内,并连通于所述摩擦块的空腔中,所述带阀进油管上安装有单向阀;
38.带阀出油管,所述带阀出油管一端伸入所述气囊安装室内,并与所述外弹性囊体远离带阀进油管端连通,所述带阀出油管另一端伸入所述转动室内,并连通于所述摩擦块的空腔中,所述带阀出油管贴设于所述气囊安装室内顶部,并串联各所述带阀出气口设置,所述带阀出油管上安装有单向阀。
39.进一步地说,所述立式混合罐顶端安装有密封盖,所述搅拌座底端安装有行走轮。
40.本发明的有益效果至少具有以下几点:
41.1、本发明以高温下具有自流动性的廉价碳前驱体为碳源,以石墨相氮化碳同时作为模板和氮源,混合方式简单,直接物理混合,无需借助其他介质直接混合,避免了其他有机溶剂如甲苯、丙酮甚至水性介质的使用,节约成本,大大降低了环境污染,同时节约了烘干过程所需的能源消耗。
42.2、本发明虽然是模板法制备薄层碳,但是不需要对碳材料进行后处理,步骤十分简单;
43.3、本发明制备的薄绸状掺氮碳,在电化学储能,电催化领域均有着很大的应用潜力。
44.4、本发明中自流动性的碳前驱体不仅限于本发明中所用的沥青,煤焦油。一切常温或者高温下具有流动性的前驱体均属于本案范畴;
45.5、本发明中使用的常规高温煅烧手段,其他类似的加热手段也有可能获得与本案类似的效果,均属于本案保护范围,如等离子体辅助煅烧,石墨炉煅烧,红外炉煅烧,微波加热等等。
46.6、本发明中碳前驱体粉末重油残渣与石墨相氮化碳自立式混合罐顶端送入立式混合罐内,搅拌电机工作,进而带动安装于搅拌电机输出端的摩擦盘、和永磁棒在转动室内转动,以及与搅拌电机输出端连接的搅拌轴在立式混合罐内转动,搅拌轴带动搅拌杆在立式混合罐内转动,从而对碳前驱体粉末重油残渣与石墨相氮化碳进行搅拌混合,永磁棒在两个贮气囊体之间转动,从而使永磁棒的两极交替式与两个贮气囊体中的永磁板接触,举例来说,当永磁棒的n极与左边的贮气囊体中的永磁板异性相吸时,永磁棒的s极与右边的贮气囊体中的永磁板同性相斥,此时,左边的贮气囊体在磁性作用下体积被拽大,左边气囊安装室内的内弹性囊体体积缩小,拽动左边气囊安装室内的外弹性囊体体积缩小,外弹性囊体内的导热油被压入左边气囊安装室内的带阀出油管中,且外弹性囊体在左边气囊安装室内体积占比减小,气流自带阀进气口吸入左边气囊安装室内,相反地,右边的贮气囊体在磁性作用下体积被缩小,右边气囊安装室内的内弹性囊体体积变大,撑起左边气囊安装室内的外弹性囊体体积变大,摩擦块内空腔中的导热油自带阀进油管吸入右边的外弹性囊体中,且外弹性囊体在右边气囊安装室内体积占比增大,将右边气囊安装室内气流自带阀出气口送入立式混合罐中,摩擦盘贴靠摩擦块转动时,使摩擦块的空腔内导热油带有热量,带热量导热油自带阀进油管依次经过外弹性囊体、带阀出油管回流到擦块的空腔内,并在带阀出油管内与自带阀出气口送入立式混合罐进行换热,从而使带热量气流自立式混合罐底端送入立式混合罐内,增加了碳前驱体粉末重油残渣与石墨相氮化碳在立式混合罐内流动性的同时,对碳前驱体粉末重油残渣与石墨相氮化碳进行一定的烘干,防止两者粘结在一
块,影响搅拌效果。
附图说明
47.图1是实施例1制得的薄绸状掺氮多孔碳透射电镜图;
48.图2是实施例1制得的薄绸状掺氮多孔碳扫描电镜图;
49.图3是实施例1制得的薄绸状掺氮多孔碳在100ma/g到8a/g下的倍率性能图;
50.图4是实施例1制得的薄绸状掺氮多孔碳在2a/g下的循环图;
51.图5是实施例2制得的薄绸状掺氮多孔碳扫描电镜图;
52.图6是对比例1制得的富氮多孔石墨烯的扫描电镜及透射电镜图;
53.图7是本发明中混合装置结构示意图;
54.图8是本发明中转动室放大图。
55.图中:11.立式混合罐;12.搅拌机构;13.搅拌座;14.转动室;15.气囊安装室;16.搅拌轴;17.搅拌杆;18.搅拌电机;19.永磁棒;10.带阀进气口;21.带阀出气口;22.外弹性囊体;23.内弹性囊体;24.贮气囊体;25.永磁板;26.气管;27.摩擦盘;28.摩擦块;29.带阀进油管;20.带阀出油管。
具体实施方式
56.下面结合附图对本发明的较佳实施例进行详细阐述,以使本发明的优点和特征能更易于被本领域技术人员理解,从而对本发明的保护范围做出更为清楚明确的界定。
57.实施例1:
58.将5g粉碎到200目的沥青粉与由5g尿素制备的石墨相氮化碳直接于粉碎机中快速粉碎混合;
59.将上述混合料置于瓷舟中,在高温炉中氮气保护下850℃煅烧1h,降至室温后取出,得到薄绸状掺氮多孔炭。
60.制得的薄绸状掺氮多孔炭的比表面积为692m2/g,氮含量为8.6wt%。透射电镜照片见图1,扫描电镜照片见图2。
61.其作为锂离子电池负极,在100ma/g到8a/g下的倍率性能如图3所示。初步测试表明,在2a/g电流密度下循环600圈无衰减,电池一直处于缓慢活化状态,循环曲线见图4。
62.实施例2:
63.将5g粉碎到200目的沥青粉与由10g尿素制备的石墨相氮化碳直接于粉碎机中快速粉碎混合;
64.将上述混合料置于瓷舟中,在高温炉中氮气保护下850℃煅烧1h,降至室温后取出,得到薄绸状掺氮多孔炭。
65.制得的薄绸状掺氮多孔炭氮比表面积为885m2/g,氮含量为10.8wt%。形貌与实施例1类似。透射电镜照片见图5。
66.对比例1:
67.引用杨旺等人的专利(公布号cn 107416806a),采用等离子体增强化学气相沉积法,以气态碳源甲烷在石墨相氮化碳模板上低温裂解制备多孔石墨烯。首先,低压下向管式炉中通入ar/h2混合气,升温至550℃,然后通入一定的甲烷,开启射频电源(plasma功率
300w),借助等离子体低温裂解2h。反应完成后,关闭碳源和等离子体,继续通入ar和h2,升温至750℃煅烧1h去除模板。自然冷却后得到低密度富氮多孔石墨烯。比表面积为959m2/g,氮含量11.7wt%。其扫描电镜及透射电镜观察到的形貌见图6。
68.实施例3:
69.将5g粉碎到500目的沥青粉与由10g尿素制备的石墨相氮化碳直接于粉碎机中快速粉碎混合;
70.将上述混合料置于瓷舟中,在高温炉中氮气保护下850℃煅烧1h;降至室温后取出;得到薄绸状掺氮多孔炭。
71.制得的薄绸状掺氮多孔炭氮比表面积为801m2/g,氮含量为10.2wt%。形貌与实施例2类似。
72.实施例4:
73.将20g煤焦油与10g尿素于瓷舟中搅拌成糊状,在高温炉中氮气保护下850℃煅烧1h,降至室温后取出,得到薄绸状掺氮多孔炭。
74.制得的薄绸状掺氮多孔炭氮比表面积为759m2/g,氮含量为9.86wt%。形貌与实施例1类似。
75.实施例5:
76.将50g减压渣油与10g尿素于瓷舟中搅拌成糊状,在高温炉中氮气保护下850℃煅烧1h,降至室温后取出,得到薄绸状掺氮多孔炭。
77.制得的薄绸状掺氮多孔炭氮比表面积为637m2/g,氮含量为10.5wt%。形貌与实施例1类似。
78.实施例6:
79.如图7、图8所示,作为本发明的可选实施例,在所述步骤(1)中,通过混合装置实现碳前驱体粉末重油残渣与石墨相氮化碳的机械混合。
80.在本实施例中,所述混合装置包括:
81.立式混合罐11,所述立式混合罐11顶端呈敞口式设置;
82.搅拌机构12,所述搅拌机构12安装于所述立式混合罐11底端。
83.在本实施例中,所述搅拌机构12包括:
84.搅拌座13,所述搅拌座13固定安装于所述立式混合罐11底端;
85.转动室14,所述转动室14设于所述搅拌座13内;
86.气囊安装室15,两个所述气囊安装室15以所述转动室14为中心对称设于所述搅拌座13内;
87.搅拌轴16,所述搅拌轴16位于所述立式混合罐11内,所述搅拌轴16底端穿设所述立式混合罐11底端,并伸入所述转动室14内;
88.搅拌杆17,所述搅拌杆17位于所述立式混合罐11内,多个所述搅拌杆17均匀连接于所述搅拌轴16上;
89.搅拌电机18,所述搅拌电机18安装于所述转动室14内底部;
90.永磁棒19,所述永磁棒19位于所述转动室14内,所述永磁棒19一端与所述搅拌轴16底端连接,所述永磁棒19另一端与所述搅拌电机18输出端连接;
91.带阀进气口10,两个所述带阀进气口10对向开设于所述搅拌座13侧端,所述带阀
进气口10连通于所述气囊安装室15内,所述带阀进气口10上安装有单向阀;
92.带阀出气口21,多个所述带阀出气口21分布于所述搅拌座13顶端,所述带阀出气口21连通于所述气囊安装室15和立式混合罐11底端之间,所述带阀出气口21上安装有单向阀;
93.外弹性囊体22,所述外弹性囊体22安装于所述气囊安装室15内,所述外弹性囊体22内填充有导热油;
94.内弹性囊体23,所述内弹性囊体23固定安装于所述外弹性囊体22内顶部和底部之间;
95.贮气囊体24,两个所述贮气囊体24对向安装于所述转动室14内壁上,所述永磁棒19位于两个所述贮气囊体24之间;
96.永磁板25,所述永磁板25嵌设于所述贮气囊体24靠近永磁棒19端,所述永磁板25适配所述永磁棒19设置;
97.气管26,所述气管26一端伸入所述转动室14内,并与所述贮气囊体24连通,所述气管26另一端伸入所述气囊安装室15内,并穿设所述外弹性囊体22、与内弹性囊体23连通;
98.摩擦盘27,所述摩擦盘27位于所述转动室14内,所述摩擦盘27固定连接于所述搅拌电机18输出端;
99.摩擦块28,两个所述摩擦块28对向安装于所述转动室14内壁上,所述摩擦块28位于所述贮气囊体24下方,所述摩擦盘27位于两个所述摩擦块28之间,所述摩擦盘27贴靠所述摩擦块28设置,所述摩擦块28内设空腔,所述空腔内储存有导热油;
100.带阀进油管29,所述带阀进油管29一端伸入所述气囊安装室15内,并与所述外弹性囊体22连通,所述带阀进油管29另一端伸入所述转动室14内,并连通于所述摩擦块28的空腔中,所述带阀进油管29上安装有单向阀;
101.带阀出油管20,所述带阀出油管20一端伸入所述气囊安装室15内,并与所述外弹性囊体22远离带阀进油管29端连通,所述带阀出油管20另一端伸入所述转动室14内,并连通于所述摩擦块28的空腔中,所述带阀出油管20贴设于所述气囊安装室15内顶部,并串联各所述带阀出气口21设置,所述带阀出油管20上安装有单向阀。
102.上述技术方案的工作原理和有益效果为:
103.碳前驱体粉末重油残渣与石墨相氮化碳自立式混合罐11顶端送入立式混合罐11内,搅拌电机18工作,进而带动安装于搅拌电机18输出端的摩擦盘27、和永磁棒19在转动室14内转动,以及与搅拌电机18输出端连接的搅拌轴16在立式混合罐11内转动,搅拌轴16带动搅拌杆17在立式混合罐11内转动,从而对碳前驱体粉末重油残渣与石墨相氮化碳进行搅拌混合,永磁棒19在两个贮气囊体24之间转动,从而使永磁棒19的两极交替式与两个贮气囊体24中的永磁板25接触,举例来说,当永磁棒19的n极与左边的贮气囊体24中的永磁板25异性相吸时,永磁棒19的s极与右边的贮气囊体24中的永磁板25同性相斥,此时,左边的贮气囊体24在磁性作用下体积被拽大,左边气囊安装室15内的内弹性囊体23体积缩小,拽动左边气囊安装室15内的外弹性囊体22体积缩小,外弹性囊体22内的导热油被压入左边气囊安装室15内的带阀出油管20中,且外弹性囊体22在左边气囊安装室15内体积占比减小,气流自带阀进气口10吸入左边气囊安装室15内,相反地,右边的贮气囊体24在磁性作用下体积被缩小,右边气囊安装室15内的内弹性囊体23体积变大,撑起左边气囊安装室15内的外
弹性囊体22体积变大,摩擦块28内空腔中的导热油自带阀进油管29吸入右边的外弹性囊体22中,且外弹性囊体22在右边气囊安装室15内体积占比增大,将右边气囊安装室15内气流自带阀出气口21送入立式混合罐11中,摩擦盘27贴靠摩擦块28转动时,使摩擦块28的空腔内导热油带有热量,带热量导热油自带阀进油管29依次经过外弹性囊体22、带阀出油管20回流到擦块28的空腔内,并在带阀出油管20内与自带阀出气口21送入立式混合罐11进行换热,从而使带热量气流自立式混合罐11底端送入立式混合罐11内,增加了碳前驱体粉末重油残渣与石墨相氮化碳在立式混合罐11内流动性的同时,对碳前驱体粉末重油残渣与石墨相氮化碳进行一定的烘干,防止两者粘结在一块,影响搅拌效果。
104.以上所述仅为本发明的实施例,并非因此限制本发明的专利范围,凡是利用本发明说明书及附图内容所作的等效结构变换,或直接或间接运用在其他相关的技术领域,均同理包括在本发明的专利保护范围内。
再多了解一些
本文用于企业家、创业者技术爱好者查询,结果仅供参考。