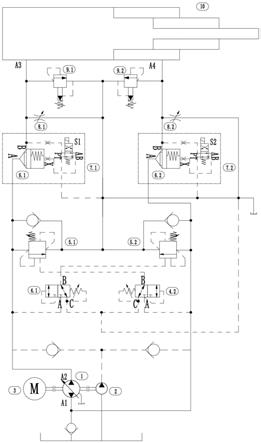
1.本发明属于液压传动领域,具体涉及一种闭式泵控快速起竖系统。
背景技术:
2.随着我国工程机械行业的巨大发展,有效降低负载起竖工作中的能耗具有重要意义。在负载起竖过程中,液压驱动利用液压存储压力能实现大规模能量传递,产生巨大推力,十分适用于大型工程机械这样的重载操作工况。在传统的开式阀控起竖回路中,传动原理为,液压泵在伺服电机的驱动下,从油箱吸油产生压力,液压油经过各类控制阀,最后到达液压缸推动负载,最后回到油箱,系统的压力、执行机构的速度和方向依靠各类的液压阀来控制。郭绍波公开了《一种多缸协同起竖液压系统》,采用开式阀控起竖回路控制双作用液压缸,起竖速度和回平速度明显提高,缩短了发射时间,但是该液压系统较为复杂,从而导致液压系统的整体体积较大,并且起竖和回平过程中节流损失较大。开式阀控快速起竖系统有明显的缺点,一是油液容易泄露,液压油在经由各类阀时,由于管道与阀的接口处可能的密封失效,很容易产生油液的泄露,在负载起竖过程中存在安全隐患;二是效率问题,在整个液压系统中,一般伺服电机和液压泵的损失约占10%,而液压阀的损失为40%~60%,最终到达执行机构的只有30%~50%,效率较低;三是整个液压系统的体积问题,在传统液压系统中所有元件需通过管路连接,使得液压系统体积增大,占用空间,增加负重。
技术实现要素:
3.本发明的目的在于提供一种闭式泵控快速起竖系统,此液压系统可实现负载快速起竖,并且与传统的开式阀控液压系统相比较,具有效率更高,体积更小,重量更轻的特点。
4.实现本发明目的的技术解决方案为:一种闭式泵控快速起竖系统,包括液压泵、齿轮泵、伺服电机、第一液控换向阀、第二液控换向阀、第一平衡阀、第二平衡阀、第一两通插装阀、第二两通插装阀、第一电磁换向阀、第二电磁换向阀、第一节流阀、第二节流阀、第一溢流阀、第二溢流阀、液压缸。
5.油箱的设计主要考虑液压缸正反腔容积差,起到补油的作用。液压泵为变量泵,伺服电机和液压泵之间直接连接,作为液压系统的动力源向整个系统提供动力。齿轮泵与液压泵同轴连接,齿轮泵和油箱的设计主要考虑液压缸正反腔容积差,起到补油的作用上述所有阀类元件均可集成一体化到一个液压阀块内,不需要繁杂的管路连接。集成后的阀块直接与液压缸和液压泵相连,由伺服电机提供动力,大大缩小了整个液压系统的体积。
6.本发明与现有技术相比,其显著优点是:采用闭式回路设计,基于“电驱液传”的原理,以伺服电机驱动液压泵,液压泵通过集成阀块驱动液压缸,液压缸的换向由切换液压泵斜盘的正负倾角来完成,构成流体传动闭式循环,兼具传统液压驱动和直接电力驱动作动器的优点,对外仅包括供电接口和机械安装接口。液压自锁模块及卸荷模块的使用最大限度的提高了安全性。所提供的液压系统能够实现负载垂直起竖时间更短,同时保证起竖过
程中平稳可靠,提高整个液压系统的效率,占用空间更小。
附图说明
7.图1 是本发明的闭式泵控快速起竖液压系统原理图。
具体实施方式
8.下面结合附图1及具体实施例对本发明作进一步详细说明。
9.结合图1,一种闭式泵控快速起竖系统,包括液压泵1、齿轮泵2、伺服电机3、第一液控换向阀4.1、第二液控换向阀4.2、第一平衡阀5.1、第二平衡阀5.2、第一两通插装阀6.1、第二两通插装阀6.2、第一电磁换向阀7.1、第二电磁换向阀7.2、第一节流阀8.1、第二节流阀8.2、第一溢流阀9.1、第二溢流阀9.2、液压缸10。
10.液压泵1、齿轮泵2与伺服电机3同轴依次联接。液压泵1为变排量液压泵,其上设有第一接口a1和第二接口a2。所述液压缸10设有第三接口a3和第四接口a4 ,液压泵1的第二接口a2分别通过单向阀与齿轮泵2的出油口、第一液控换向阀4.1的接口a、第一平衡阀5.1的进油口、第一两通插装阀6.1的接口a连通,第一两通插装阀6.1的接口b通过管道分别与第一电磁换向阀7.1接口p、第一节流阀8.1接口、第一溢流阀9.1进油口、液压缸10的第三接口a3连通,液压泵1的接口a1通过单向阀分别与齿轮泵2的出油口、第二液控换向阀4.2的接口a、第二平衡阀5.2的进油口、第二两通插装阀6.2的接口a连通,第二两通插装阀6.2的接口b分别通过管道与第二电磁换向阀7.2接口p、第二节流阀8.2接口、第二溢流阀9.2进油口、液压缸10的第四接口a4连通,液压泵1的第一接口a1通过单向阀、第一节流阀8.1接口、第二节流阀8.2接口、第一溢流阀9.1出油口、第二溢流阀9.2出油口、第一电磁换向阀7.1的接口t、第二电磁换向阀7.2的接口t、第一平衡阀5.1出油口、第二平衡阀5.2出油口 、第一液控换向阀4.1的接口c、第二液控换向阀4.2的接口c、齿轮泵2的吸油口分别与油箱相连通,第一电磁换向阀7.1的接口a与第一两通插装阀6.1的接口x连通,第二电磁换向阀7.2的接口a与第二两通插装阀6.2的接口x连通,第一液控换向阀4.1的接口b与第二平衡阀5.2的压力控制口连通,第二液控换向阀4.2的接口b与第一平衡阀5.1的压力控制口连通。
11.所提出的闭式泵控快速起竖液压系统使用伺服电机3驱动液压泵1,液压缸10的换向由液压泵1切换斜盘的正负倾角来完成,伺服电机3的转速和液压泵1的排量共同决定输出流量的大小,以此来控制液压缸10上升和下降的速度。齿轮泵2在系统中起到补油作用。所有阀类元件均可集成一体化到一个液压阀块内,不需要繁杂的管路连接。集成后的阀块直接与液压缸10和液压泵1相连,由伺服电机3提供动力,大大缩小了整个液压系统的体积。系统设计充分考虑了液压缸10两腔的面积差,使用对称油路应对非对称液压缸10排油的流量变化,在过重心时优先考虑使用伺服电机3吸收负载势能,负载下降时使用平衡阀5.1将多余的流量导入油箱,从而保证液压缸10在上升和下降时液压泵1都有合适的吸油和压油流量。齿轮泵2在液压回路中起到补油的作用。对于负载的锁止,使用第一两通插装阀6.1、第二两通插装阀6.2组成的开关回路进行控制,避免了传统起竖系统中使用平衡阀锁止负载带来的节流损失,使负载的上升和下降同时具有较高的液压效率。
12.结合附图1,液压系统工作过程说明如下,负载上升时,液压泵1调整为正摆角,第一电磁换向阀7.1的第一开关s1和第二电磁换向阀7.2的第二开关s2同时得电,解除液压缸
10锁止状态,调整伺服电机3转速,液压缸10无杆腔进油,负载上升。无杆腔压力高于第一液控换向阀4.1设定压力p1时,第二平衡阀5.2先导压力建立后开启,第二平衡阀5.2导通后的流动压损是预设压力p2,此时液压泵1连接液压缸10的无杆腔侧处于吸油和经油箱补油阶段,p2的压损会使油液进入液压泵10的进油口,而不会经第二平衡阀5.2外泄。负载上升至过重心位置时,在负载的作用下,液压缸10产生负推力,负载有牵引液压缸10的工况时,会导致液压泵1进油侧压力上升,压油侧压力下降,待压油侧压力降至p1以下时,第二平衡阀5.2关闭,防止负推力下液压缸10有杆腔的油液经第二平衡阀5.2外泄,使液压缸10不受控,此时对负推力下产生的负功率由伺服电机3吸收。负载上升至顶端后,对第一开关s1、第二开关s2断电,同时将伺服电机3的转速调整至0rpm,液压泵1的斜盘倾角回至零位,液压缸10被第一两通插装阀6.1、第二两通插装阀6.2组成的开关回路锁止。在任意位置停止时,与此过程相同。负载下降时,液压泵1调节为负摆角,第一开关s1和第二开关s2同时得电,解除液压缸10锁止状态,调整伺服电机3转速,液压缸10有杆腔进油,负载下降,由于液压缸10两腔面积差的存在,此时无杆腔的排油流量大于有杆腔的进油流量,液压泵1能够接受无杆腔的排油而不用从油箱补油。液压缸10下降过程两腔存在流量差,如果第一平衡阀5.1不导通,液压缸10的无杆腔侧多余流量将导致有杆腔侧的压力上升,有杆腔侧的压力高于第二液控换向阀4.2的设定压力p3时,第一平衡阀5.1建立先导压力后导通,多余的流量从第一平衡阀5.1泄流至油箱。如果在负载下降过程中液压缸10失控, 液压缸10有杆腔的压力势必下降甚至出现负压,在有杆腔侧压力低于p3时,第一平衡阀5.1关闭,同时伺服电机3将被液压泵1反拖超速而形成的制动效应,从而阻止液压缸10的失控下降。负载下降至底端后,对第一开关s1、第二开关s2断电,同时将伺服电机3的转速调整至0rpm,液压泵1的斜盘摆角回至零位,液压缸10被第一两通插装阀6.1、第二两通插装阀6.2组成的开关回路锁止。在下降的任意位置停止时,与此过程相同。
13.结合附图1,系统安全性说明如下,在闭式回路中,液压泵充足的补油和补油的及时性,是保证液压泵的安全工作的前提。此回路中,液压泵1的吸油不仅接受系统回油,也能够直接从油箱内吸油,如果吸油侧有正压力,说明液压泵1已经具有可靠吸油的条件,无簧单向阀能够隔断油箱和液压泵1的吸油口,防止吸油侧的压力油进入油箱内,一旦吸油出现负压,油箱内的油液会通过无簧单向阀及时的补充到液压泵1的吸油侧,同时串联的齿轮泵2作为补油泵,保证液压泵1吸油的及时性和可靠性。液压缸10下降时,负载势能主要由伺服电机3吸收,第一平衡阀5.1只用于下降时液压缸10无杆腔的排油,第二平衡阀5.2工作时不节流,不会带来额外的节流损失,因此在负载快速起竖的情况下可以大大减少能源的浪费。负载下降时的减速和停止依靠伺服电机3的制动特性,减速和制动平稳。第一两通插装阀6.1、第二两通插装阀6.2组成的开关回路在负载静止和液压泵1斜盘摆角回零时锁止负载,防止液压泵1斜盘零位时的微小泄漏导致负载下滑。液压缸10两腔分别连接第一溢流阀9.1、第二溢流阀9.2,有效防止第一两通插装阀6.1、第二两通插装阀6.2开启失效时液压缸10两腔憋压,提高回路安全性。
14.结合图1,系统可靠性说明如下,过起竖重心后,此时液压缸10受拉,产生的负功率由伺服电机3吸收,伺服电机3反拖工作时通过制动电阻耗散能量,伺服电机3工作在发电机模式,响应快。依靠调节伺服电机3转速和液压泵1排量两种方式实现流量控制。过重心时,伺服电机3具有抱闸功能,若伺服电机3减速失效,对第一开关s1、第二开关s2断电,锁止液
压缸10,保证安全可控。系统故障或断电后,全开第二节流阀8.2,再开启第一节流阀8.1,通过调整第一节流阀8.1的开度,能够控制负载下放的速度。
再多了解一些
本文用于企业家、创业者技术爱好者查询,结果仅供参考。