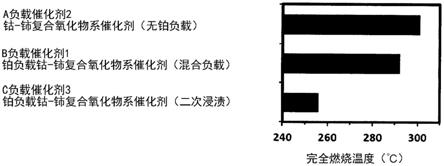
voc处理用催化剂的制造方法
技术领域
1.本发明涉及一种挥发性有机化合物(voc)处理用催化剂的制造方法。
背景技术:
2.需要一种简单地处理挥发性有机化合物(volatile organic compounds:以下表述为“voc”)的技术,所述挥发性有机化合物会导致来自涂装工厂、印刷工厂、化学工厂等的排气所引起的恶臭或大气污染的问题,所述挥发性有机化合物从家庭/办公室中使用的建筑材料/电子设备等中散发并成为损害健康的要因。作为处理方法,提出了直接燃烧法、蓄热燃烧法、催化剂燃烧法、吸附处理法、等离子体法等各种方法,其中,催化剂燃烧法因能够在相对低温条件下燃烧处理从而被广泛应用。
3.但是,由于基于催化剂燃烧法的处理通常需要300~350℃左右的温度,因此存在需要花费用于加热的电费、燃料费的问题。另外,在将该方法应用于面向家庭/办公室的处理装置的情况下电费也会升高,并且会产生确保安全性、实现小型化等课题,从而限定了应用范围。为了扩大应用范围也需要在更低温的条件下示出高活性的催化剂。
4.催化剂处理性能大多因voc的种类而产生差异,例如,在使用市售的铂负载氧化铝(pt/al2o3)催化剂在一般条件下处理的情况下,甲苯等芳香族烃能够在200~250℃左右的相对低温的条件下处理,但不含苯环的乙酸乙酯等的处理需要300~350℃左右的相对高温。另一方面,在使用已经提出的钴-铈系复合氧化物(co3o
4-ceo2)催化剂(专利文献1、2)的情况下,反而是不含苯环的乙酸乙酯等voc能够在200~250℃左右的相对低温的条件下处理,但芳香族烃的处理需要300℃左右的相对高温。因此,虽然适合单独处理含苯环的voc和不含苯环的voc的情况,但产生了开发用于在低于300℃的温度区域同时处理这两种voc的新催化剂的课题。
5.为解决上述课题而进行了潜心研究的发明人,发现通过使规定量的铂直接负载于钴-铈系复合氧化物催化剂,进一步优选通过以胶体溶液为原料的方法来使规定量的铂负载于钴-铈系复合氧化物催化剂的新组合,来进一步提高钴-铈系复合氧化物催化剂的低温活性,并提出了无论是否含芳香环,在低温条件下都能持续高活性的voc处理用催化剂的发明(专利文献3)。由专利文献3可知,在使用作为以往广泛使用的典型原料的氯铂酸在钴-铈系复合氧化物催化剂上负载铂的情况下,铂未均匀地分散而是凝集,从而未提高性能。通过将由分散剂保护的铂胶体作为原料,成功将铂直接负载于钴-铈系复合氧化物催化剂。
6.现有技术文献
7.专利文献
8.专利文献1:日本再表2014/157721号公报;
9.专利文献2:日本特开2018-126738号公报;
10.专利文献3:日本特开2019-13871号公报。
技术实现要素:
11.发明要解决的课题
12.但是,专利文献3是基于使用粉末催化剂的研究结果而提出的,在工业上应用本技术时,必须将铂负载钴-铈系复合氧化物负载在球或蜂窝等载体上。
13.本发明是鉴于以上情况而完成的,其课题是提供一种使铂直接负载于钴-铈系复合氧化物,并且在负载于球或蜂窝等载体时提高催化剂性能的技术方案。
14.解决课题的技术方案
15.本发明人潜心研究的结果,发现在负载液中的铂量相同的情况下,预先在陶瓷制的蜂窝载体上负载钴-铈系复合氧化物后,使用其他负载液负载铂(后附加)时,性能更好。能够以作为市售的现有催化剂的铂负载氧化铝的一半以下(1.1质量%以下)的铂量,在低50℃以上的温度条件下使甲苯和乙酸乙酯的混合成分完全燃烧。此外,即使在使用涂装室中的稀释剂喷射分支排气的催化剂性能评价中,通过使用负载于陶瓷制的蜂窝载体上的铂负载钴-铈系复合氧化物,成功在250℃条件下使具有含苯环的voc(芳香族烃)和不含苯环的voc这两者的成分完全燃烧。本发明是基于这样的见解而完成的。
16.即,本发明的voc处理用催化剂的制造方法的特征在于包含以下工序(a)~(c):
17.(a)制备以铂为原料的负载液的工序;
18.(b)将负载有钴-铈系复合氧化物的载体浸渍于所述负载液中的工序;以及
19.(c)对所述浸渍后的载体进行烧成的工序。
20.发明效果
21.根据本发明,能够制造铂直接负载钴-铈系复合氧化物催化剂(不是在氧化铝等典型的载体上负载钴-铈系复合氧化物和铂,而能够在钴-铈系复合氧化物上直接负载铂)。根据该效果,与市售的铂氧化铝催化剂或钴-铈系复合氧化物催化剂相比,能够在更低的温度条件下确保高性能。由此,通过降低工厂等中的处理温度,能削减电费、燃料费或将面向家庭/办公室的小型催化剂处理装置实用化。此外,通过将用途扩大至现有催化剂难以应对的低温规格的催化剂的处理技术领域,能够对改善大气污染、室内环境做出贡献。
附图说明
22.图1是示出甲苯单一成分燃烧时的co2生成率(燃烧率)的温度依赖性在混合负载、二次浸渍时的差异的图。
23.图2是示出乙酸乙酯单一成分燃烧时的co2生成率(燃烧率)的温度依赖性在混合负载、二次浸渍时的差异的图。
24.图3是示出甲苯和乙酸乙酯混合成分燃烧时的co2生成率(燃烧率)的温度依赖性在混合负载、二次浸渍时的差异的图。
25.图4是将甲苯和乙酸乙酯混合成分燃烧时的完全燃烧温度在混合负载、二次浸渍时的差异进行汇总的图。
26.图5是示出甲苯单一成分燃烧时的co2生成率(燃烧率)的温度依赖性在改变铂负载量时的差异的图。
27.图6是示出乙酸乙酯单一成分燃烧时的co2生成率(燃烧率)的温度依赖性在改变铂负载量时的差异的图。
28.图7是示出甲苯和乙酸乙酯混合成分燃烧时的co2生成率(燃烧率)的温度依赖性在改变铂负载量时的差异的图。
29.图8是将在甲苯和乙酸乙酯混合成分燃烧时的完全燃烧温度在改变铂负载量时的差异进行汇总的图。
30.图9是示出使用涂装室中的稀释剂喷射分支排气的催化剂性能评价体系的图。
31.图10是示出稀释剂喷射分支排气中的voc成分燃烧时co2生成率(燃烧率)的温度依赖性的图。(a)市售现有催化剂铂负载氧化铝催化剂、(b)钴-铈系复合氧化物催化剂(无铂负载)、(c)铂负载钴-铈系复合氧化物催化剂。
具体实施方式
32.以下,详细说明本发明。
33.本发明中,所述工序(a)没有特别限制于以铂为原料的负载液,但优选以由分散剂保护的铂胶体溶液为原料。在以铂胶体溶液为原料的情况下,能够提高所负载的铂粒子的分散性。作为铂胶体的保护剂,优选聚乙烯吡咯烷酮,但除此以外,例如,使用聚乙烯吡咯烷酮以外的高分子、配体、胶束等也无妨。
34.在本发明中,所述工序(b)没有特别限制于钴-铈系复合氧化物,参照专利文献1、2。如果示出其一个例子,则能够通过:将平均粒径0.8~2.0μm的钴氧化物粒子与能生成钴离子的盐或化合物、能生成铈离子的盐或化合物以及水进行混合来制备催化剂浸渍液的工序;用获得的催化剂浸渍液对载体进行浸渍处理的工序;以及对浸渍处理后的载体进行烧成的工序来制造。由此,催化剂粒子负载于载体物质。催化剂粒子中,平均粒径0.8~2.0μm的钴氧化物粒子的周围被以钴离子为前驱体的钴氧化物和以铈离子为前驱体的铈氧化物覆盖。在此,平均粒径是指通过激光衍射法求出的粒度分布中累计值为50%时的粒径(d0.5)。另外,“钴氧化物粒子的周围被钴氧化物和铈氧化物覆盖”是指在钴氧化物粒子的表面形成有钴氧化物和铈氧化物。因此,催化剂粒子是具有平均粒径0.8~2.0μm的钴氧化物粒子、以钴离子为前驱体的钴氧化物和以铈离子为前驱体的铈氧化物而构成的,所述钴氧化物和所述铈氧化物形成在所述钴氧化物粒子的表面。催化剂粒子中,钴氧化物粒子的周围除了钴氧化物和铈氧化物之外,还可以被以铜离子为前驱体的铜氧化物覆盖。即,催化剂粒子还可以具有以铜离子为前驱体的铜氧化物而构成,所述钴氧化物、所述铈氧化物和所述铜氧化物可以形成在所述钴氧化物粒子的表面。为了提高催化剂粒子的分散性,负载催化剂可以具有以复合硅酸盐为主体的粘土矿物,也可以是催化剂粒子彼此分散的结构。
35.钴氧化物粒子可以是各种钴化合物例如碳酸盐、硝酸盐、硫酸盐、氯化物等无机酸盐或醇化物、羧酸盐、络合盐等有机化合物或有机盐等的烧成物、干固物。其中,优选通过将以碳酸盐为前驱体的化合物在空气中于250~400℃进行低温烧成而制作的物质。另外,钴氧化物粒子优选粉碎处理至平均粒径在0.8~2.0μm的范围内。粉碎处理可以为干式粉碎处理或湿式粉碎处理,不限制其处理方法。例如,可以使用干式喷射磨机进行粉碎处理,也可以通过干式珠磨法或湿式旋转球磨法等进行粉碎处理。在钴氧化物粒子的平均粒径小于0.8μm的情况下,由于钴的氧化物粒子之间变得易凝集,在加热下会导致其比表面积降低且活性易降低,因此不优选。另外,在超过2.0μm的情况下,由于与载体的附着面积小且易剥离,因此不优选。从该观点出发,为了获得活性不易降低、耐久性良好而且剥离性良好、耐久
性与剥离性的平衡良好的负载催化剂,优选钴氧化物粒子的平均粒径为0.8~2.0μm的范围。
36.另外,本发明中的所述钴离子、铈离子,是钴和铈以水溶性的盐或化合物的形式形成的。例如,硝酸盐、硫酸盐等。这样的钴离子、铈离子中还可以共存有铜离子。在使铜离子共存下制造的负载催化剂,是钴氧化物粒子的周围除了钴氧化物和铈氧化物之外还被以铜离子为前驱体的铜氧化物覆盖的负载催化剂。铜离子更优选以催化剂粒子的氧化物质量比计为0.1~30质量%的范围的方式与钴离子和铈离子共存。由此,能够获得催化剂性能更良好的负载催化剂。
37.另外,本发明中使用的载体可以是以现有公知的载体为代表的各种载体。例如,作为优选的载体,可举出将不锈钢、钢铁、铜合金、铝合金和陶瓷材料中的任一者成型成所期望的形状而得到的载体。具体而言,可举出球或蜂窝等。另外,载体能够采用表面具有直径5μm~50μm左右的气孔的多孔质结构体,作为本发明的负载催化剂,能够是催化剂粒子保持于该载体的结构。
38.由以上成分(要素)构成的负载催化剂,可以采用各种方法制造,但优选能够通过以下工艺制造。
39.即,首先,将平均粒径0.8~2.0μm的钴氧化物粒子与能生成钴离子的盐或化合物、能生成铈离子的盐或化合物以及水一同混合来制备催化剂浸渍液。根据需要,也可以混合能生成铜离子的盐或化合物、以高岭土、活性白土等复合硅酸盐为主体的粘土矿物来制备催化剂浸渍液。接着,用其对载体进行浸渍处理,并在脱水后进行烧成。通过该烧成,钴离子、铈离子分别被转化为氧化物。在催化剂浸渍液中包含铜离子的情况下,通过该烧成,铜离子也被转化为氧化物。
40.在本发明的负载催化剂中,关于(i)平均粒径0.8~2.0μm的钴氧化物粒子、(ii)以钴离子为前驱体的钴氧化物、(iii)以铈离子为前驱体的铈氧化物的质量比,没有特别限定,可以考虑为(i):20~50质量%、(ii):6~12质量%、(iii):39~66质量%。另外,烧成温度没有特别限定,可以考虑为200~600℃。另外,能够考虑作为催化剂的使用对象的voc的种类、处理条件等来适当确定对载体的负载量,但通常作为质量比,优选考虑相对于载体为10~30质量%的范围。
41.在所述工序(b)中,作为所述铂,优选的是,使用由分散剂保护的铂胶体溶液的原料,在钴-铈系复合氧化物上直接负载铂,铂的含量a(单位:质量%)为0<a≤1.1。在该范围内,适合提高催化剂性能等。
42.在所述工序(c)中,将负载有钴-铈系复合氧化物的载体浸渍于以铂为原料的负载液中后,对浸渍后的载体进行烧成。烧成温度没有特别限定,考虑为200~600℃。
43.根据本发明,通过预先在载体上负载钴-铈系复合氧化物后,使用其他负载液负载铂(后附加),从而能够提高催化剂性能。例如,与市售的铂氧化铝催化剂或钴-铈系复合氧化物催化剂相比,能够在更低的温度条件下确保高性能。由此,通过降低工厂等中的处理温度,能削减电费、燃料费,将面向家庭/办公室的小型催化剂处理装置实用化。此外,通过将用途扩大至现有催化剂难以应对的低温规格的催化剂的处理技术领域,能够对改善大气污染、室内环境做出贡献
44.实施例
45.以下,通过实施例进一步详细说明本发明,但本发明不限定于这些实施例。
46.1.基于小型固定床流通层型装置的催化剂性能评价
47.如下,基于小型固定床流通层型装置进行催化剂性能评价。
48.向设置在管状电炉内的催化剂填充管(内径3mm)内填充粉碎至粒径约1mm的负载催化剂,并向该填充层连续流通包含甲苯、乙酸乙酯中的任一者或两者的蒸气的干燥空气。将甲苯、乙酸乙酯(蒸气)的体积相对于干燥空气的体积的比例调节至约260~270ppm的范围。空间速度约为10000h-1
,流速为100ml
·
min-1
。
49.如下控制管状电炉内的催化剂填充层的温度。在干燥空气流通下将填充了负载催化剂的填充管升温至400℃后,使包含甲苯、乙酸乙酯中的任一者或两者的蒸气的干燥空气流通并保持该温度1小时,此后以1分钟降1℃的速度降温至30℃。降温时使用附带导热系数检测器的气相色谱(安捷伦科技有限公司(agilent technologies inc.)制,agilent 3000micro gc)测定气体中的co2浓度和甲苯、乙酸乙酯浓度。将甲苯、乙酸乙酯完全燃烧时气体中的co2浓度记作c1,将通过催化剂填充层后生成的气体中的co2浓度记作c2时,co2生成率(燃烧率)a(%)由a=c2/c1
×
100的式子求出。
50.关于铂的负载方法,评价并比较以下两种方法:将钴-铈系复合氧化物原料和铂原料混合在同一负载液中,负载于陶瓷制的蜂窝载体上的方法(称作混合负载);以及在将钴-铈系复合氧化物负载于陶瓷制的蜂窝载体上之后,使用其他负载液负载铂的方法(称作二次浸渍)。
51.将硝酸铈六水合物186g、硝酸钴六水合物42g、四氧化三钴47g、硝酸铜三水合物1.2g、纯水200ml混合并搅拌,获得负载液1。
52.在将负载液1与1.7g铂胶体溶液(由分散剂聚乙烯吡咯烷酮保护的铂胶体溶液,溶液中的铂含量:4质量%,田中贵金属工业株式会社制)混合并搅拌而得到的溶液中,浸渍陶瓷制的蜂窝载体约15秒钟后,使其干燥,并在空气中于380℃烧成3小时,由此,获得负载催化剂1(在混合负载的条件下负载的催化剂)。
53.通过将陶瓷制的蜂窝载体在负载液1中浸渍约15秒钟后干燥,并在空气中于380℃烧成3小时,从而获得负载催化剂2(钴-铈系复合氧化物(无铂负载))。
54.图1示出对于甲苯单一成分的催化剂活性(co2生成率(燃烧率)的温度依赖性),图2示出对于乙酸乙酯单一成分的催化剂活性,图3示出对于甲苯和乙酸乙酯的混合成分的催化剂活性。图1、图2、图3中,在混合负载的条件b下,甲苯、乙酸乙酯的完全燃烧温度(达到a=100%的温度)与未负载铂的情况a相比,没有发现具有显著差异。
55.在将铂胶体溶液1.7g与纯水200ml混合并搅拌而得到的溶液中,将负载催化剂2浸渍约15秒钟后干燥,并在空气中于380℃烧成3小时,由此获得负载催化剂3(二次浸渍的条件下负载的催化剂)。由能量色散型荧光x射线分析(株式会社堀场制作所制,x射线分析显微镜xgt-7200v)求出负载催化剂表面上的铂量。
56.图1中在二次浸渍的条件c下,与未负载铂的情况a相比,甲苯单一成分的完全燃烧温度低30℃左右。图2中在二次浸渍的条件c下,与未负载铂的情况a相比,乙酸乙酯单一成分的完全燃烧温度几乎未发现区别。图3中在二次浸渍的条件c下,与未负载铂的情况a相比,甲苯和乙酸乙酯的混合成分的完全燃烧温度低40℃以上。甲苯和乙酸乙酯的混合成分的完全燃烧温度汇总于图4。
57.通过荧光x射线分析求出负载催化剂1(混合负载的条件下负载的催化剂)表面上的铂量为0.01质量%(以原子组成百分率计,小于0.01原子%),负载催化剂3(二次浸渍的条件下负载的催化剂)表面上的铂量为0.05质量%(0.01原子%)。由于在二次浸渍的条件下负载的铂集中在外表面,因此,在负载液中的铂量相同的情况下,二次浸渍比混合负载的低温活性更优异。在仅处理乙酸乙酯的情况下,可以不负载铂,但在处理甲苯单一成分、甲苯和乙酸乙酯的混合成分的情况下,通过二次浸渍来负载铂更占优势。
58.评价并比较在改变铂量来制备负载液时的负载催化剂表面上的铂量、催化剂性能。
59.在将铂胶体溶液1.7g与纯水200ml混合并搅拌而得到的溶液中,将负载催化剂2浸渍约1分钟后干燥,并在空气中于380℃烧成3小时,由此获得负载催化剂4。
60.通过荧光x射线分析求出负载催化剂4表面上的铂量为0.06质量%(0.01原子%)。图5示出对于甲苯单一成分的催化剂活性(co2生成率(燃烧率)的温度依赖性),图6示出对于乙酸乙酯单一成分的催化剂活性,图7示出对于甲苯和乙酸乙酯的混合成分的催化剂活性。图5、图6、图7中,铂量为0.05质量%的条件b为前述结果。图5中,铂量0.06质量%的条件c比条件b的完全燃烧温度低30℃左右,但在图6、图7中条件b与条件c的完全燃烧温度几乎没有差别。条件c与未负载铂的情况a相比,乙酸乙酯单一成分中完全燃烧温度几乎未发现区别(图6),但对甲苯单一成分而言,完全燃烧温度因负载铂而降低60℃左右(图5),对甲苯和乙酸乙酯的混合成分而言,降低50℃左右(图7)。甲苯和乙酸乙酯的混合成分的完全燃烧温度汇总于图8。
61.在将铂胶体溶液17g与纯水200ml混合并搅拌而得到的溶液中,将负载催化剂2浸渍约1分钟后干燥,并在空气中于380℃烧成3小时,由此获得负载催化剂5。
62.通过荧光x射线分析求出负载催化剂5表面上的铂量为0.76质量%(0.09原子%)。图5、图6、图7中,铂量0.76质量%的条件d与未负载铂的情况a相比,乙酸乙酯单一成分的完全燃烧温度几乎未发现区别(图6),但对甲苯单一成分而言,完全燃烧温度因负载铂而降低90℃左右(图5),对甲苯和乙酸乙酯的混合成分而言,降低60℃左右(图7)。在仅处理乙酸乙酯的情况下,可以不负载铂,但在处理甲苯单一成分、甲苯和乙酸乙酯的混合成分的情况下,增加铂量更占优势。
63.评价并比较市售现有催化剂铂负载氧化铝(日挥universal株式会社(nikki-universal co.,ltd.)制)表面上的铂量、催化剂性能。
64.通过荧光x射线分析求出市售现有催化剂铂负载氧化铝表面上的铂量为2.2质量%(0.32原子%)。图5、图7中,铂量0.76质量%的条件d与铂负载氧化铝使用时e相比,对甲苯单一成分而言,铂负载氧化铝的情况下的完全燃烧温度低10℃左右(图5),但对甲苯和乙酸乙酯的混合成分而言,铂负载钴-铈系复合氧化物(条件d)的情况下的完全燃烧温度低50℃以上(图7)。在处理甲苯和乙酸乙酯的混合成分的情况下,使用铂负载钴-铈系复合氧化物更占优势。负载催化剂5表面上的铂量是铂负载氧化铝表面上的铂量的一半以下的量,但能够在低50℃以上的温度条件下使甲苯和乙酸乙酯的混合成分完全燃烧。
65.2.使用涂装室中的稀释剂喷射分支排气的催化剂性能评价
66.如下,使用涂装室中的稀释剂喷射分支排气进行催化剂性能评价。将催化剂性能评价体系示于图9。使用喷枪在涂装室内进行稀释剂喷射,喷射后气化的成分通过排气管
道。由热线式风量计实测的通过管道的排气的空塔速度(线速度)为8600m/h,风量为3400m
3n
/h。
67.向催化剂填充层内填充负载催化剂(载体:15
×
15
×
50mm的陶瓷制蜂窝),并向该填充层连续流通管道分支排气。将带式加热器卷绕于预热层和催化剂填充层并加热。空间速度约为29000h-1
。分别使用voc总浓度分析仪(附带氢火焰离子化型检测器(fid),东亚dkk株式会社(dkk-toa corporation)制,ght-200型)和co2浓度计(理研计器株式会社制,红外线式co2监测器ri-215d)测量催化剂处理前后气体中的voc总浓度和催化剂处理后气体中的co2浓度。将催化剂处理前的管道分支排气中的voc总浓度(单位:ppmc)记作c3,将通过催化剂填充层后生成的气体中的co2浓度(单位:ppm)记作c4时,co2生成率(燃烧率)b(%)由b=c4/c3
×
100的式子求出。在将催化剂填充层的温度从300℃减少至150℃时,每隔50℃求出co2生成率(燃烧率)。本试验中的c3的值被调节至700~900ppmc的范围。
68.通过气相色谱/质量分析仪(安捷伦科技有限公司制,agilent 7890a gc5975c gc/msd)分析催化剂处理前的管道分支排气中的voc成分(用于喷射的稀释剂被气化的成分)。将气相色谱图中检测的成分的峰面积比示于表1。排气组成中混合存在含苯环的voc(芳香族烃)即甲苯、以及不含苯环的voc即乙酸乙酯、乙酸丁酯等。
69.表1通过气相色谱/质量分析检测的催化剂处理前的管道分支排气中的voc成分
[0070][0071]
向催化剂填充层内填充作为市售现有催化剂的铂负载氧化铝(日挥universal株式会社制),求出填充层温度150℃、200℃、250℃、300℃条件下的co2生成率(燃烧率)。
[0072]
如图10(a)所示,在作为市售现有催化剂的铂负载氧化铝的情况下,填充层温度为300℃时,管道分支排气中的表1所示的成分几乎完全燃烧(达到b=100%),但在250℃以下时,co2生成率降低至小于70%。
[0073]
向催化剂填充层内填充负载催化剂2(钴-铈系复合氧化物(无铂负载)),求出填充层温度150℃、200℃、250℃、300℃条件下的co2生成率(燃烧率)。
[0074]
如图10(b)所示,在负载催化剂2(钴-铈系复合氧化物(无铂负载))的情况下,填充层温度为300℃时,管道分支排气中的表1所示的成分完全燃烧,但在250℃以下时co2生成率大致降低至80%以下。
[0075]
向催化剂填充层内填充负载催化剂5(铂负载钴-铈系复合氧化物),求出填充层温度150℃、200℃、250℃、300℃条件下的co2生成率(燃烧率)。
[0076]
如图10(c)所示,在负载催化剂5(铂负载钴-铈系复合氧化物)的情况下,在填充层温度为250℃、300℃的条件下,能够使管道分支排气中的表1所示的成分完全燃烧。在150℃、200℃条件下,co2生成率高于其他催化剂(铂负载氧化铝和钴-铈系复合氧化物)的情况。在含苯环的voc(芳香族烃)和不含苯环的voc混合的体系中,使用铂负载钴-铈系复合氧
化物更占优势。如上所述,负载催化剂5表面上的铂量为0.76质量%(0.09原子%),该值是小于铂负载氧化铝表面上的铂量2.2质量%(0.32原子%)的值。通过使用铂负载钴-铈系复合氧化物,能够以更少的铂量使管道分支排气中的表1所示的成分在250℃条件下完全燃烧。
再多了解一些
本文用于企业家、创业者技术爱好者查询,结果仅供参考。