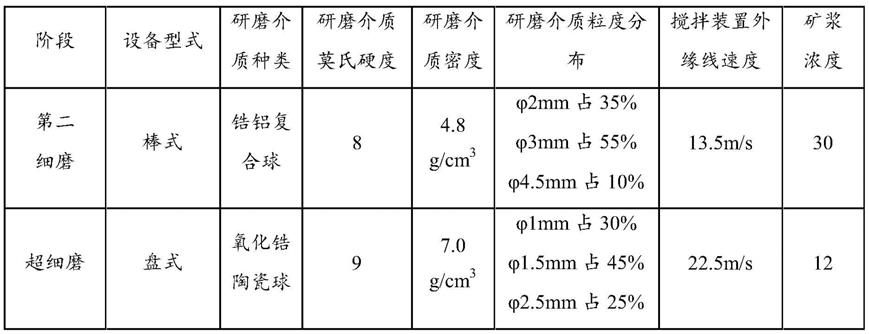
1.本发明涉及研磨技术领域,尤其是涉及一种用于难磨浆料的研磨方法。
背景技术:
2.难磨浆料是一种具有一般胶体性质的有机物质,一般至少由两种以上的有机或无机物质组成。难磨浆料在石油、化工行业中较为普遍,比如石油行业的分子筛浆液、需要细磨的隐晶质石墨、铁氧体磁粉、钛白粉、高岭土等。难磨浆料通常具有以下特征:给矿粒度一般为d90≤58μm;产品粒度要求很细,一般需d90≤3μm;固含量较低,一般不超过35%。
3.细磨和超细磨的主要作用是为了将矿石充分粉磨,在此基础上使矿石中的脉石和有用矿物得以充分解离或达到最终产品的粒度要求,其是矿物处理和领域拓展的关键工艺技术之一,因此在各行各业均占有重要地位。目前,细磨和超细磨技术因存在较多问题,无法在难磨浆料领域进行推广应用,主要体现如下:
4.1)细磨和超细磨主要使用单台卧式或立式搅拌设备,设备的针对性和选择性较差,导致细磨和超细磨的效果较差,同时存在能耗高、效率低、浪费严重等问题;
5.2)细磨和超细磨采用的研磨介质种类、直径、配比等使用不合理,导致碎球率及磨损率较高,研磨介质的消耗量大,研磨介质与难磨浆料的接触比表面积较小,研磨效率低;
6.3)搅拌磨机的选择和配置不合理,研磨速度的设置不合理,使不同阶段的细磨和超细磨效果不一,不仅磨矿时间长,同时研磨效率较低。
7.综上可知,现有细磨和超细磨技术用于难磨浆料领域时的适用性较差,效率较低,能耗较高,而难磨浆料的细磨和超细磨所追求的经济技术指标主要是在较低的能源费用和较高的处理量情况下得到所需的产品粒度。
8.鉴于此,特提出本发明。
技术实现要素:
9.本发明的目的在于提供一种用于难磨浆料的研磨方法,其能够解决难磨物料在研磨过程中的技术问题,实现了提高细磨和超细磨效率、降低能耗和介质消耗等效果。
10.本发明提供一种用于难磨物料的研磨方法,包括如下步骤:
11.s1:对难磨物料进行第一细磨和/或第二细磨,得到细磨物料;
12.s2:对所述细磨物料进行超细磨,得到研磨物料;
13.其中:第一细磨采用的研磨介质的莫氏硬度6-9,优选为6.5-7.5;密度为2.6-4.6g/cm3,优选为3.5-4.5g/cm3,更优选为3.5-4g/cm3;直径为2.5-8mm。第二细磨采用的研磨介质的莫氏硬度7-10,优选为7.5-8.5;密度为3.6-7.6g/cm3,优选为4-5g/cm3,更优选为4.5-5g/cm3;直径为1.5-5.5mm。超细磨采用的研磨介质的的莫氏硬度8-11,优选为8.5-9.5;密度为6.6-8.6g/cm3,优选为6.5-7.5g/cm3,更优选为6.8-7.2g/cm3;直径为0.5-3.5mm。
14.本发明可根据难磨物料的给矿粒度确定具体的细磨方式。具体地,对20μm《d90≤
35%;研磨介质的的莫氏硬度7-10,密度为3.6-7.6g/cm3;直径为1.5-5.5mm;其中:1.5mm-2.5mm的质量占总质量的30-50%,2.5mm-3.5mm的质量占总质量的15-50%,3.5mm-5.5mm的质量占总质量的5-10%。
26.超细磨:在被研磨物料的总质量中,被研磨物料的粒度≤5μm占总质量的90
±
5%,要求产品粒度为≤3μm占总质量的90
±
5%。高速搅拌磨机的搅拌装置型式为盘式、棒式或盘棒混合式等单轴或多搅拌轴的圆形筒体搅拌磨机,搅拌装置的外缘线速度为15-30m/s;难磨浆料的浓度为5-20%;研磨介质的莫氏硬度8-11,密度为6.6-8.6g/cm3;直径为0.5-3.5mm,其中:0.5mm-1mm的质量占总质量的20-40%,1mm-2mm的质量占总质量的30-55%,2mm-3.5mm的质量占总质量的5-25%。
27.上述研磨介质的种类可以是钢球、氧化铝陶瓷球、锆铝复合球、氧化锆陶瓷球等多种类型中的一种;研磨介质的松散体积占搅拌磨机筒体容积的35-85%。
28.难磨浆料最初在一个搅拌槽内混合均匀,配置成所需的矿浆浓度,并利用渣浆泵泵送至第一个搅拌磨机筒体内;搅拌磨机之间的难磨浆料的输送均利用渣浆泵完成;研磨介质的配置需预先完成,按照要求的粒径、重量和数量进行配置并混合,预先添加到搅拌磨机内部;搅拌磨机均为底部给矿,避免短路;搅拌磨机均在上部排料端设置与研磨介质粒度想适应的方孔、不锈钢材质排料筛,用以实现矿浆与研磨介质的分离。
29.本发明的实施,至少具有以下优势:
30.1、本发明的研磨方法分段对难磨浆料进行细磨和超细磨,每段配置不同的搅拌磨机类型、研磨介质类型、尺寸和配比,可以实现针对性、选择性细磨和超细磨矿物,适用性好,能耗低、效率高;
31.2、本发明的研磨方法对研磨介质进行针对性选择,可以有效降低研磨介质的破碎率和磨损率,进而降低介质的消耗;同时,小直径的研磨介质比表面积更大,选择性细磨、超细磨的效率更高;
32.3、本发明的研磨方法对高速搅拌磨机进行针对性选择,可以提高搅拌磨机类型、搅拌装置外缘线速度与研磨介质直径、矿浆粒度的适应性,进而提高针对性细磨和超细磨的效果,提高研磨效率,降低电耗,节约经济成本。
具体实施方式
33.应该指出,以下详细说明都是例示性的,旨在对本技术提供进一步的说明。除非另有指明,本文使用的所有技术和科学术语具有与本技术所属技术领域的普通技术人员通常理解的相同含义。
34.需要注意的是,这里所使用的术语仅是为了描述具体实施方式,而非意图限制根据本技术的示例性实施方式。如在这里所使用的,除非上下文另外明确指出,否则单数形式也包括复数形式,此外,还应当理解的是,当在本说明中使用术语“包含”和/或“包括”时,其指明存在特征、步骤、操作、器件、组件和/或它们的组合。
35.下面将结合实施例对本发明的技术方案进行清楚、完整地描述,显然,所描述的实施例是本发明一部分实施例,而不是全部的实施例。基于本发明中的实施例,本领域普通技术人员在没有做出创造性劳动前提下所获得的所有其他实施例,都属于本发明保护的范围。
36.本发明的用于难磨浆料的研磨方法,主要包括细磨和超细磨,细磨包括第一细磨和/或第二细磨,每段研磨采用不同的研磨介质、高速搅拌磨机以解决现有难磨浆料细磨和超细磨的技术难题,工艺流程如下:
37.1)确定具体细磨流程:
38.根据难磨浆料的具体要求给矿粒度和产品粒度,确定矿物细磨、超细磨所需的段数、搅拌磨机和研磨介质的配置,具体如下:
39.在被研磨物料的总质量中,被研磨物料的粒度≤58μm占总质量的90
±
5%,要求产品粒度为≤10μm占总质量的90
±
5%时选择第一细磨;其中:高速搅拌磨机的搅拌装置型式为双叶轮、多叶轮式多矩形槽式搅拌磨机,搅拌装置的外缘线速度为7-15m/s。难磨浆料的浓度为25-45%。研磨介质的莫氏硬度6-9,密度为2.6-4.6g/cm3;直径为2.58mm,其中2.5mm-5mm的质量占总质量的20-40%,5mm-6.5mm的质量占总质量的40-60%,6.5mm-8mm的质量占总质量的20-40%。
40.在被研磨物料的总质量中,被研磨物料的粒度≤10μm占总质量的90
±
5%,要求产品粒度为≤5μm占总质量的90
±
5%时选择第二细磨;其中:高速搅拌磨机的搅拌装置型式为叶轮式、盘式、棒式等圆形筒体搅拌磨机,搅拌装置的外缘线速度为12-20m/s。难磨浆料的浓度为15-35%。研磨介质的莫氏硬度7-10,密度为3.6-7.6g/cm3;直径为1.5mm-5.5mm,其中1.5mm-2.5mm的质量占总质量的30-50%,2.5mm-3.5mm的质量占总质量的15-50%,3.5mm-5.5mm的质量占总质量的5-10%。
41.在被研磨物料的总质量中,被研磨物料的粒度≤5μm占总质量的90
±
5%,要求产品粒度为≤3μm占总质量的90
±
5%选择超细磨;其中:高速搅拌磨机的搅拌装置型式为盘式、棒式或盘棒混合式等单轴或多搅拌轴的圆形筒体搅拌磨机,搅拌装置的外缘线速度为15-30m/s。难磨浆料的浓度为5-20%。研磨介质的莫氏硬度8-11,密度为6.6-8.6g/cm3;直径为0.5mm-3.5mm,其中0.5mm-1mm的质量占总质量的20-40%,1mm-2mm的质量占总质量的30-55%,2mm-3.5mm的质量占总质量的5-25%。
42.2)配置矿浆:根据细磨和超细磨阶段的要求,利用搅拌槽等装置配置所需浓度的矿浆,一般来说受限于不同阶段,整体矿浆浓度在5-45%。
43.3)配置研磨介质:根据细磨和超细磨阶段的要求,按照配比、密度和直径要求配置所需研磨介质,并预先添加到搅拌磨机的筒体内部。
44.4)给料研磨:启动搅拌磨机到所需转速和线速度,待稳定运转后,将混合均匀的矿浆利用渣浆泵泵入搅拌磨机内部,利用搅拌磨机高速细磨和超细磨;难磨浆料通过搅拌磨机筒体底部进入筒体内,经过搅拌磨机细磨和超细磨后,通过搅拌磨机上部的排料筛排除磨机,并利用渣浆泵泵入下一阶段细磨、超细磨,若达到要求粒度,直接泵入搅拌槽内存储备用。
45.实施例1
46.以石油化工行业的分子筛浆料超细磨为例,要求处理干矿量为1.5t/h,给矿粒度为d90=20μm,要求产品粒度为d90=3.5μm。
47.根据上述工艺流程,选第二细磨和超细磨两段细磨和超细磨工艺流程,第二细磨采用双叶轮式5m3搅拌磨机,超细磨采用500l盘式搅拌磨机,按照第二细磨、超细磨进行研磨介质、磨机线速度、磨机外形、矿浆浓度配置,利用搅拌槽调浆后,利用渣浆泵泵入两种类
型设备进行串联细磨、超细磨,细磨、超细磨完成后,得到最终产品。
48.本实施例各阶段细磨的参数配置和选用设备的具体参数见表1、表2。
49.表1
[0050][0051]
表2
[0052][0053]
经测试,本实施例产品粒度为≤3.5μm占92.3%,达到粒度要求。
[0054]
实施例2
[0055]
以隐晶质石墨超细磨为例,要求处理干矿量为1.2t/h,给矿粒度为d90=58μm,要求产品粒度为d95=3μm。
[0056]
根据上述工艺流程,选第一细磨、第二细磨和超细磨工艺流程,第一细磨采用双叶轮式20m3搅拌磨机,第二细磨采用3500l盘式搅拌磨机、超细磨采用1500l盘、棒混合式搅拌磨机,按照第一细磨、第二细磨、超细磨进行研磨介质、磨机线速度、磨机外形、矿浆浓度配置,利用搅拌槽调浆后,利用渣浆泵泵入三种类型设备进行串联细磨、超细磨,细磨、超细磨完成后,得到最终产品。
[0057]
本实施例各阶段细磨的参数和选用设备的具体参数配置见表3、表4。
[0058]
表3
[0059][0060]
表4
[0061][0062]
经测试,本实施例产品粒度为≤3μm占95.2%,达到粒度要求。
[0063]
对照例1
[0064]
采用原有工艺对实施例1的分子筛浆料进行细磨,原有工艺如下:要求处理干矿量为1.5t/h,给矿粒度为d90=20μm,要求产品粒度为d90=3.5μm。采用双叶轮式20m3搅拌磨机再磨后得到最终产品。参数配置如表5、表6所示。
[0065]
表5
[0066][0067]
表6
[0068]
阶段设备型式设备容积设备装机功率设备实耗功率研磨介质消耗再磨双叶轮式20m3264kw225kw0.648kg/t
[0069]
经测试,本对照例产品粒度为≤3.5μm占91.6%。
[0070]
经过对比本对照例的原有工艺和实施例1的工艺流程,在相同处理量、给排矿粒度
要求的前提下,通过计量一定时间内总研磨介质消耗量、实时地利用钳型表测量电机电流并核算实耗功率,经过计算分析得知,实施例1工艺的研磨介质损耗率较本对照例原有工艺降低15%以上,搅拌磨机能耗降低14%以上。
[0071]
对照例2
[0072]
采用原有工艺对实施例2的隐晶质石墨进行细磨,原有工艺如下:干矿量为1.2t/h,给矿粒度为d90=58μm,要求产品粒度为d95=3μm。采用2台套4000l搅拌磨机再磨后得到最终产品。参数配置如表7、表8所示。
[0073]
表7
[0074][0075][0076]
表8
[0077]
阶段设备型式设备容积设备装机功率设备实耗功率研磨介质消耗细磨盘式4000l1250kw1014kw0.34kg/t超细磨盘式4000l1250kw1077kw0.52kg/t
[0078]
经测试,本对照例产品粒度为≤3μm占95.12%。
[0079]
经过对比本对照例的原有工艺和实施例2的工艺流程,在相同处理量、给排矿粒度要求的前提下,通过计量一定时间内总研磨介质消耗量、实时地利用钳型表测量电机电流并核算实耗功率,经过计算分析得知,实施例2工艺的研磨介质损耗率较本对照例原有工艺降低20%以上,搅拌磨机能耗降低25%以上。
[0080]
对照例3
[0081]
采用原有工艺对实施例2的隐晶质石墨进行细磨,原有工艺如下:干矿量为1.2t/h,给矿粒度为d90=58μm,要求产品粒度为d95=3μm。采用1台套3000l和1台套4000l搅拌磨机再磨后得到最终产品。参数配置如表9、表10所示。
[0082]
表9
[0083]
[0084][0085]
表10
[0086]
阶段设备型式设备容积设备装机功率设备实耗功率研磨介质消耗细磨棒式3000l1000kw912kw0.36kg/t超细磨盘式4000l1250kw1102kw0.54kg/t
[0087]
经测试,本对照例产品粒度为≤3μm占95.09%。
[0088]
经过对比本对照例的原有工艺和实施例2的工艺流程,在相同处理量、给排矿粒度要求的前提下,通过计量一定时间内总研磨介质消耗量、实时地利用钳型表测量电机电流并核算实耗功率,经过计算分析得知,实施例2工艺的研磨介质损耗率较本对照例原有工艺降低25%以上,搅拌磨机能耗降低20%以上。
[0089]
最后应说明的是:以上各实施例仅用以说明本发明的技术方案,而非对其限制;尽管参照前述各实施例对本发明进行了详细的说明,本领域的普通技术人员应当理解:其依然可以对前述各实施例所记载的技术方案进行修改,或者对其中部分或者全部技术特征进行等同替换;而这些修改或者替换,并不使相应技术方案的本质脱离本发明各实施例技术方案的范围。
再多了解一些
本文用于企业家、创业者技术爱好者查询,结果仅供参考。