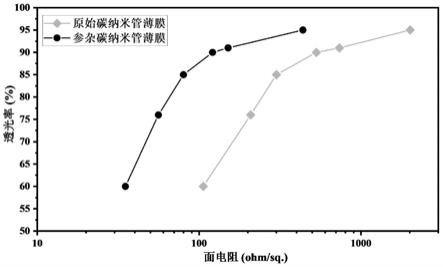
1.本发明属于透明导电薄膜技术领域,具体涉及一种具有长管束碳纳米管且均匀透明的导电薄膜及其制备方法。
背景技术:
2.碳纳米管透明导电薄膜在现代电子学领域有非常广泛的应用,包括在光伏、触摸屏、液晶显示器、有机发光二极管等领域。碳纳米管透明导电薄膜是有望替代传统的氧化铟锡薄膜的潜力。当今制备碳纳米管透明导电薄膜的方法主要分为干法和湿法制备。其中,湿法制备碳纳米管薄膜通常是将碳纳米管分散在表面活性剂中,然后经超声、离心、抽滤等步骤制成薄膜(h.-z.geng,k.k.kim,k.p.so,y.s.h.lee,y.chang and y.s.h.lee,j.am.chem.soc.,2007,129,7758
–
7759)。但是,湿法制备的过程中由于溶剂和超声等影响,导致碳纳米管被切割或引入杂质,最终导致碳纳米管的导电性能不能完全发挥。另一方面,干法制备薄膜由于不需要经过溶液或超声等后续处理,制备的碳纳米管保持了本征的物理化学性质,从而能够获得导电性优异的碳纳米管薄膜。浮动催化化学气相沉积法就是一种具有代表性的干法制备碳纳米管薄膜的方法(a.kaskela,a.g.nasibulin,m.y.timmermans,b.aitchison,a.papadimitratos,y.tian,z.zhu,h.jiang,d.p.brown,a.zakhidov and e.i.kauppinen,nano lett.,2010,10,4349
–
4355.)。这种方法不仅可以得到导电性优异的薄膜,而且可以将碳纳米管薄膜转移至任意基底,且更该方法是一个可以持续生产的过程。
3.目前,使用浮动催化化学气相沉积法制备碳纳米管薄膜的面电阻远高于理论值,主要原因是生产的碳纳米管长度不够,导致碳管与碳管之间的接触结变多,最终使得薄膜的电阻变高。另外,由于气相中生长的碳纳米管具有随气流任意流动的特性,导致制备的碳纳米管薄膜不够均匀。因此,获得高导电性且均匀的碳纳米管薄膜是一项重大的挑战。
技术实现要素:
4.鉴于此,本发明的目的是提供一种具有长管束碳纳米管且均匀透明的导电薄膜及其制备方法。解决了通常情况下制备的碳纳米管长度过短且不够均匀的问题,以获得高导电性的碳纳米管薄膜。
5.本发明的技术方案如下:
6.一种具有长管束碳纳米管且均匀透明的导电薄膜的制备方法,采用浮动催化化学气相沉积法,以乙醇、甲苯、乙腈等作为碳源,以含硫的化合物(包括噻吩、硫脲、硫醇)作为助生长剂,二茂铁、二茂镍、二茂钴等为催化剂,将碳源、助生长剂和催化剂的混合溶液在惰性气体和氢气的携带作用下以一定速率注入高温管式炉,通过调节氢气的流速,从而调节催化剂的尺寸和活性,调节碳纳米管的生长条件,最终获得超长的高纯度的碳纳米管,将高温管式炉内气相中生长的碳纳米管收集至不同尺寸的滤膜上,获得不同尺寸的具有长管束
碳纳米管且均匀透明的导电薄膜。
7.进一步地,所述的制备方法中使用的设备主要由进样系统、载气系统、高温管式炉、1/8英寸加1/4英寸组合不锈钢气路管、滤膜收集器和真空泵组成,进样系统、高温管式炉、1/8英寸加1/4英寸组合不锈钢气路管、滤膜收集器和真空泵依次连接,载气系统的载气(惰性气体和氢气)由进样系统和高温管式炉之间进入高温管式炉。
8.进一步地,所述的高温管式炉为卧式高温管式炉,长度为100~150cm,有效加热区为70~90cm,高温管式炉内石英管的内直径为2.5~3.5cm。
9.进一步地,所述的进样系统中设置有装催化剂、助生长剂和碳源的前驱体溶液的容器,前驱体溶液通过微量注射泵输送。
10.进一步地,所述的制备方法包括如下步骤:
11.(1)在200-400sccm(cm3/min)惰性气体保护下,将高温管式炉逐渐升温至950-1050℃,通过微量注射泵将进样系统中的前驱体溶液以5~20μl/min注入高温管式炉内;催化剂的质量浓度为0.2~0.4%,助生长剂的质量浓度为0.03~0.06%;
12.(2)将惰性气体的流速调节为200-500sccm,氢气流速调节为50~400sccm,碳源和催化剂在管式炉高温区裂解为原子碳和催化剂纳米颗粒,在助生长剂和高温的作用下,碳纳米管在高温管式炉内的高温区生长;
13.(3)生长后的碳纳米管随载气带出高温管式炉,并经过1/8英寸加1/4英寸组合不锈钢气路管后均匀沉积在滤膜收集器中的滤膜上,通过控制沉积时间得到不同厚度的碳纳米管导电薄膜。
14.进一步地,步骤(1)中高温管式炉的升温速率为5~10℃/min。
15.进一步地,步骤(3)中通过真空泵抽滤的方式辅助碳纳米管均匀沉积在滤膜上。
16.进一步地,为了获得大尺寸的碳纳米管薄膜,步骤(3)中所述的滤膜的直径为4-10cm。
17.进一步地,步骤(3)中碳纳米管的管束的直径为1.5~60nm,管束的长度为10~80μm。
18.本发明另一方面提供有上述制备方法制得的具有长管束碳纳米管且均匀透明的导电薄膜。
19.进一步地,所述的导电薄膜的拉曼光谱ig/id的比值为80~100。
20.进一步地,所述的导电薄膜可通过按压法直接转移到玻璃或塑料基底上。
21.本发明相对于现有技术具有的有益效果如下:
22.1.本发明获得的碳纳米管长度较长,有效降低了薄膜中接触结的数量,从而显著提高碳纳米管薄膜的导电性。
23.2.本发明使用较低的进样速率和较小的氢气载气,降低了成本。
24.3.本发明采用1/8英寸加1/4英寸组合不锈钢气路管收集样品,使薄膜更加均匀。
25.4.本发明提供了一种可持续生长高导电性碳纳米管薄膜的方法,为实际生产带来帮助,具有广阔的应用前景。
附图说明
26.为了更清楚地说明本发明实施例,下面将对实施例涉及的附图进行简单地介绍。
27.图1.本发明制备具有长管束且均匀的碳纳米管透明导电薄膜的制备系统图。
28.图2.实施例1制备的不同尺寸和不同厚度的碳纳米管导电薄膜(a)以及碳纳米管导电薄膜可转移到柔性透明基底(b)。
29.图3.实施例1制备的碳纳米管的扫描电镜图(a)、碳纳米管长度分布图(b)、透射电镜图(c)和碳纳米管导电薄膜拉曼光谱图(d)。
30.图4.实施例1制备的碳纳米管导电薄膜的透光率与面电阻图。
31.图5.对比例2中单独使用1/4英寸气体管收集的碳纳米管薄膜样品图。
具体实施方式
32.下面结合实施例对本发明进行详细的说明,但本发明的实施方式不限于此,显而易见地,下面描述中的实施例仅是本发明的部分实施例,对于本领域技术人员来讲,在不付出创造性劳动性的前提下,获得其他的类似的实施例均落入本发明的保护范围。
33.如图1所示,本发明的制备具有长管束碳纳米管且均匀透明的导电薄膜的设备主要由进样系统、载气系统、高温管式炉、1/8英寸加1/4英寸组合不锈钢气路管、滤膜收集器和真空泵组成,进样系统、高温管式炉、1/8英寸加1/4英寸组合不锈钢气路管、滤膜收集器和真空泵依次连接,载气系统的载气由进样系统和高温管式炉之间进入,进样系统中装有催化剂、助生长剂和碳源的前驱体溶液,在惰性气体和氢气的作用下,载入高温管式炉中反应并生长碳纳米管,碳纳米管随着载气沉积到尾部的滤膜收集器中,最终得到碳纳米管薄膜。
34.在具体实施过程中,本发明选用卧式高温管式炉,利用浮动催化化学气相沉积法制备大尺寸且均匀的碳纳米管透明导电薄膜。以二茂铁、二茂镍、二茂钴等金属有机物为催化剂,以含硫的物质为助生长剂,以乙醇、甲苯、丙酮等液体有机物为碳源,以惰性气体(氩气或氮气)加入一定量的氢气为载气,在1000℃条件下生长碳纳米管,并通过1/8英寸加1/4英寸组合不锈钢气路管将载气中的碳纳米管沉积到滤膜收集器中,得到均匀的薄膜;具体步骤如下:
35.(1)在200-400sccm氮气保护下,将管式炉逐渐升温至1000℃,再将微量注射泵中的前驱体以5~20μl/min注入管式炉内;
36.(2)将载气氮气的流速调节为500sccm,氢气流速调节为50~300sccm(现有技术一般需要2-8l/min)。碳纳米管在高温区生长;
37.(3)生长后的碳纳米管随载气带出管式炉,并采用1/8英寸加1/4英寸组合不锈钢气路管将碳纳米管沉积在滤膜上,通过控制不同沉积时间可得到不同厚度的碳纳米管薄膜,采用不同的尺寸的滤膜即可得到不同尺寸的碳纳米管薄膜。
38.(4)制备结束后,将管式炉降至室温,结束样品制备。
39.下面,通过实施例和附图相结合的方式对本发明的具有长管束碳纳米管且均匀透明的导电薄膜的制备方法进行详细说明。
40.实施例1
41.本实施例中,在200sccm氮气保护下,将管式炉逐渐升温至1000℃,再将微量注射泵中的前驱体,包括100ml乙醇,二茂铁(质量浓度为0.3%)和噻吩(质量浓度为0.03%),以5μl/min注入管式炉内,然后将载气氮气的流速调节为500sccm,氢气流速调节为150sccm,
在高温区生长碳纳米管,生长后的碳纳米管随载气带出管式炉,并采用1/8英寸加1/4英寸组合不锈钢气路管将碳纳米管沉积在滤膜上,通过控制不同沉积时间可得到不同厚度的碳纳米管薄膜,采用不同的尺寸的滤膜即可得到不同尺寸的碳纳米管薄膜,见图2(a),且滤膜上的碳纳米管薄膜可转移到柔性透明基底,如聚对苯二甲酸乙二醇酯(pet),见图2(b)。
42.如图3(a)所示,通过扫描电镜可知,所制备的碳纳米管均匀且致密,且无其他杂质,碳纳米管呈无序交叉排布;如图3(b)所示,所制备的碳纳米管管束的长度分布范围为5~45μm,平均长度为18.39μm;如图3(c)的透射电镜结果所示,所制备的碳纳米管干净少杂质,管束的直径大约为10nm;如图3(d)可知,制备的碳纳米管薄膜的ig/id值为96.4,表明制备的碳纳米管具有很高的结晶度。
43.如图4所示,将不同厚度的碳纳米管薄膜通过干法转移到石英基底上,测试其透光率和面电阻,得到透光率为95%,91%,90%,85%,76%,60%,其对应的面电阻分别为2015,736,530,300,208,106ω/sq.(采用了四探针测试碳纳米管薄膜的面电阻),氯化金掺杂可进一步降低面电阻,采用预先配制好的氯化金的乙腈溶液,氯化金浓度为16mmol/l,取氯化金溶液100μl,将其滴涂于碳纳米管薄膜上,静置3min后用纯乙腈溶液冲洗,干燥后即完成掺杂,然后进一步测试掺杂后的碳纳米管面电阻,掺杂之后的碳纳米管薄膜面电阻分别为438,151,121,80,56,35ω/sq.。
44.实施例2
45.本实施例中,在400sccm氮气保护下,将管式炉逐渐升温至1000℃,再将微量注射泵中的前驱体,包括100ml乙醇,二茂铁(质量分数为0.4%)和噻吩(质量分数为0.04%),以10μl/min注入管式炉内,然后将载气氮气的流速调节为500sccm,氢气流速调节为300sccm,在高温区生长碳纳米管,生长后的碳纳米管随载气带出管式炉,并采用1/8英寸加1/4英寸组合不锈钢气路管将碳纳米管沉积在滤膜上,通过控制不同沉积时间可得到不同厚度的碳纳米管薄膜,采用不同的尺寸的滤膜即可得到不同尺寸的碳纳米管薄膜。
46.通过扫描电镜可知,所制备的碳纳米管均匀且致密,且无其他杂质,碳纳米管呈无序交叉排布。所制备的碳纳米管管束的长度分布范围为8~76μm,平均长度为26.4μm。通过透射电镜结果可知,所制备的碳纳米管干净少杂质,管束的直径大约为18.4nm。通过拉曼光谱结果可知,制备的碳纳米管薄膜的ig/id值为101.5,表明制备的碳纳米管具有很高的结晶度。
47.将不同厚度的碳纳米管薄膜通过干法转移到石英基底上,测试其透光率和面电阻,得到透光率为94%,92%,90%,83%,77%,64%,其对应的面电阻分别为1421,644,481,299,179,99ω/sq.,氯化金掺杂之后的碳纳米管薄膜(氯化金浓度16mmol/l,掺杂量为100μl)面电阻分别为401,112,101,72,49,29ω/sq.。
48.对比例1
49.本实施例中,在400sccm氮气保护下,将管式炉逐渐升温至1000℃,再将微量注射泵中的前驱体,包括100ml乙醇,二茂铁(质量分数为0.6%)和噻吩(质量分数为0.06%),以30μl/min注入管式炉内,然后将载气氮气的流速调节为500sccm,氢气流速调节为50sccm,在高温区生长碳纳米管,生长后的碳纳米管随载气带出管式炉,并采用1/8英寸加1/4英寸组合不锈钢气路管将碳纳米管沉积在滤膜上,通过控制不同沉积时间可得到不同厚度的碳纳米管薄膜,采用不同的尺寸的滤膜即可得到不同尺寸的碳纳米管薄膜。
50.通过扫描电镜可知,所制备的碳纳米管均匀且致密,碳纳米管呈无序交叉排布。所制备的碳纳米管管束的长度分布范围为4~35μm,平均长度9.2μm。通过透射电镜结果可知,所制备的碳纳米管有较多无定形碳,管束的直径大约为40.6nm。通过拉曼光谱结果可知,制备的碳纳米管薄膜的ig/id值为45.2。
51.将不同厚度的碳纳米管薄膜通过干法转移到石英基底上,测试其透光率和面电阻,得到透光率为96%,92%,90%,85%,74%,67%,其对应的面电阻分别为3061,1145,984,877,692,501ω/sq.,氯化金掺杂之后的碳纳米管薄膜(氯化金浓度16mmol/l,掺杂量为100μl)面电阻分别为1083,501,392,301,252,169ω/sq.。
52.对比例2
53.本实施例中,在200sccm氮气保护下,将管式炉逐渐升温至1000℃,再将微量注射泵中的前驱体,包括100ml乙醇,二茂铁(质量浓度为0.3%)和噻吩(质量浓度为0.03%),以5μl/min注入管式炉内,然后将载气氮气的流速调节为500sccm,氢气流速调节为150sccm,在高温区生长碳纳米管,生长后的碳纳米管随载气带出管式炉,只采用1/4英寸不锈钢气路管将碳纳米管沉积在滤膜上,所制备的碳纳米管薄膜均匀性较差,如图5所示。
54.由对比例1-2和实施例1-2结果表明,本发明的具有长管束碳纳米管均匀透明导电薄膜的制备方法制得的导电薄膜具有较长的管束和优异的导电性,所制备的薄膜在90%透光率下,面电阻为481ω/sq.,氯化金掺杂之后为101ω/sq.。本发明实现了大尺寸且均匀的透明导电薄膜的制备,解决了目前薄膜不均匀,导电性差等问题。
55.最后应说明的是:以上各实施例仅用以说明本发明的技术方案,而非对其限制;尽管参照前述各实施例对本发明进行了详细的说明,本领域的普通技术人员应当理解:其依然可以对前述各实施例所记载的技术方案进行修改,或者对其中部分或者全部技术特征进行等同替换;而这些修改或者替换,并不使相应技术方案的本质脱离本发明各实施例技术方案的范围。
再多了解一些
本文用于企业家、创业者技术爱好者查询,结果仅供参考。