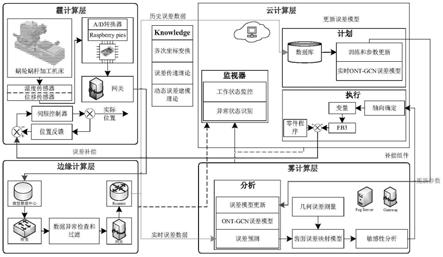
基于ont-gcn时空模型的热误差预测模型及建模方法和霾-边-雾-云误差补偿系统
技术领域
1.本发明属于机械误差分析技术领域,具体的为一种基于ont-gcn时空模型的热误差预测模型及霾-边-雾-云误差补偿系统。
背景技术:
2.机械传动是装备制造业的基础,蜗轮是机械传动中最常见和最基本的零件之一。蜗轮的几何精度受加工系统多源误差的影响。几何误差和热误差是两个最重要的误差。对于蜗轮加工机床来说,影响热误差的热源很多,包括电机、轴承、滚动导轨、滚珠丝杠等。主轴是对热误差影响显着的关键部件。减少热误差的方法主要有以下三种:(1)温度控制方法;(2)热误差预防方法;(3)热误差补偿方法。温度控制方法通过控制热误差来减少热误差,但实施成本高,技术实施难度也高;温度传递的滞后导致温度控制的滞后,所以它不是减少热误差的最佳选择。热误差预防方法在设计和制造阶段选择合理的材料和机床结构设计,从而降低对热流的误差敏感性,提高热稳定性,然而,该方法的成本随着控制精度的提高呈指数增长,因此,它不是常用的措施。热误差补偿方法是探索热误差与其他变量之间的关系,因此,热误差补偿方法是实际应用中最实用的措施,因其简单、高效、低成本的独特特点而被广泛使用。
3.为了表征了热误差的变化过程,提出了多种数学模型,主要有数值模拟模型和经验模型,传统的经验模型基于统计方法,无法挖掘潜在关系,缺乏数据特征的提取能力。近来的一些经验模型使用了机器学习技术,与传统的经验模型不同,考虑了误差产生机理,说明了热误差是运行时间的函数。采用具有强记忆能力的长短期记忆网络(lstmn)进行建模。结果表明,lstmn是一个出色的模型,这一结论也反映在机床热误差建模中。但误差数据的时间序列分析导致传感器的空间信息被忽略,从而热误差数据不受传感器网络的限制。
4.经验误差模型的训练非常耗时。云计算具有强大的计算能力,被广泛用于解决耗时问题,但由于工业互联网高延迟和有限带宽等问题,云计算不能直接应用于误差控制,必须有雾计算或边缘计算等分布式计算来缓解工业互联网的带宽压力,然而,边缘-雾-云架构中忽略了终端设备的设计和配置。
技术实现要素:
5.有鉴于此,本发明的目的在于提供一种基于ont-gcn时空模型的热误差预测模型及霾-边-雾-云误差补偿系统,能够有序地传递热误差的时间和空间特征,从而提高热误差的预测精度。
6.为达到上述目的,本发明提供如下技术方案:
7.本发明首先提出了一种基于ont-gcn时空模型的热误差预测模型,所述ont-gcn神经网络的表达式为:
8.f
t
=δ(wf[h
t-1
,f(a,x
t
)] bf)
[0009]it
=δ(wi[h
t-1
,f(a,x
t
)] bi)
[0010][0011]ot
=δ(wo[h
t-1
,f(a,x
t
)] bo)
[0012][0013][0014]
cumax(
·
)=cumsum(softmax(
·
))
[0015][0016][0017][0018][0019][0020]
其中,f
t
表示遗忘门;i
t
表示输入门;o
t
表示输出门;表示主遗忘门;表示主输入门;h
t-1
表示前一个单元的输出值,与f(a,x
t
)结合增加三个门的权重,x
t
表示特征序列,a表示邻接矩阵,f(a,x
t
)表示x
t
经过图卷积之后的序列;表示
t
时刻临时单元的内存状态;c
t-1
表示t-1时刻临时单元的内存状态;c
t
表示内存在
t
时刻的单元状态;wf、wi、wc和wo表示权重矩阵;bf、bi、bc和bo表示偏置向量;σ表示激活函数;h
t
表示t时刻的隐藏状态;
[0021]
和分别表示和的权重矩阵;和分别表示和的偏置向量;comsum表示求和的函数;w
t1
、w
t2
和w
t3
分别表示高等级、中等级和低等级,其中,w
t1
*c
t-1
存储低等级信息,受当前输入信息的影响;存储高等级信息,受历史信息影响;存储中等级信息,受当前输入信息和历史信息影响;
[0022]
f(a,x
t
)表示x
t
经过图卷积之后的序列,并作为on-lstmn模型的输入向量,且:
[0023][0024]
其中,i表示单位矩阵;a表示邻接矩阵;x表示特征序列;w0表示第一层的权重参数;σ表示激活函数;
[0025]
热误差预测模型需要时空特性,因此,热误差的时空预测可以表示为传感器网络g与特征序列x
t
之间映射关系f的学习,下一时刻t的热误差序列可以表示为:
[0026]
[x
t 1
,
…
,x
t t
]=f(g;(x
t-n
,
…
,x
t-1
,x
t
))
[0027]
其中,n表示历史时间序列的长度。
[0028]
本发明还提出了一种基于ont-gcn时空模型的热误差预测模型的建模方法,包括如下步骤:
[0029]
11)构建传感器网络:在机床上布置温度传感器和位移传感器,并将各个传感器分别标记在机床的三维模型上;
[0030]
12)生成时空图数据集:需要两个条件来预测当前节点的热误差信号,分别为:
①
位移测量点的历史热误差信号;
②
相邻传感器的位置和历史信号;
[0031]
传感器网络的空间特征由邻接矩阵表征,邻接矩阵为:
[0032][0033]
其中,w
i,j
表示边权重,与节点i和节点j的位置有关;δ表示控制w
i,j
分布的阈值;d
i,j
为节点i和节点j之间的距离,是机床三维模型上测量得到的;
[0034]
13)构建如上所述基于ont-gcn时空模型的热误差预测模型;
[0035]
14)以邻接矩阵和传感器的时间数据作为热误差预测模型的输入,预测热误差。
[0036]
本发明还提出了一种霾-边-雾-云误差补偿系统,其特征在于:包括霾计算层、边缘计算层、雾计算层和云计算层;
[0037]
所述霾计算层包括:
[0038]
温度传感器:用于测量温度;
[0039]
位移传感器:用于测量位移;
[0040]
采集卡:用于采集所述温度传感器和位移传感器测量得到的温度信号和位移信号;
[0041]
树莓派:所述树莓派上连接有用于将温度信号和位移信号转换为数字信息的a/d转换器;
[0042]
网关:用于经a/d转换器转换得到的数据传输至所述边缘计算层;
[0043]
所述边缘计算层包括用于存储经所述霾计算层传入的数据的微型数据中心、用于过滤数据的交换机和用于将过滤后的数据传输至雾计算层和云计算层的网关和路由器,其中,历史数据传输至云计算层,实时误差数据传输至雾计算层;
[0044]
所述雾计算层内设有分析模块,所述分析模块内设有如上所述基于ont-gcn时空模型的热误差预测模型,将以温度传感器、位移传感器的位置信息生成的邻接矩阵和以各个传感器采集的数据作为特征序列作为热误差预测模型的输入预测热误差,再结合误差映射模型得到误差补偿值,并将误差补偿值传输至云计算层;
[0045]
所述云计算层包括误差补偿执行模块和热误差模型更新模块,所述误差补偿执行模块根据所述雾计算层输入的误差补偿值确定需要补偿的变量,并将补偿指令发送至霾计算层进行误差补偿;所述热误差模型更新模块根据边缘计算层输入的历史数据更新热误差预测模型,并将更新后的热误差预测模型传输至雾计算层。
[0046]
本发明的有益效果在于:
[0047]
本发明基于ont-gcn时空模型的热误差预测模型,利用lstmn神经网络捕捉传感器收集的数据的时间依赖性,利用gcn神经网络捕捉拓扑结构的空间特征,从而可以将捕获的空间特征和时序特征保留在ont-gcn单元中;ont-gcn单元的独特排序特性允许保留重要的热误差信息,因此,ont-gcn单元可以有序地传递热误差的时间和空间特征,从而提高热误差的预测精度。
[0048]
本发明的霾-边-雾-云误差补偿系统,云计算具有强大的计算能力,用于解决耗时问题,但由于工业互联网高延迟和有限带宽等问题,云计算不能直接应用于误差控制;通过设置雾计算层和边缘层等分布式计算层,可缓解工业互联网的带宽压力,但雾计算层和边缘层忽略了终端设备的设计和配置,因此设置了霾计算层以加快信息获取过程,霾计算层可以被认为是一个极端的边缘层,从而以保证系统执行效率和机床的加工精度。
附图说明
[0049]
为了使本发明的目的、技术方案和有益效果更加清楚,本发明提供如下附图进行说明:
[0050]
图1为本发明霾-边-雾-云误差补偿系统实施例的框架图;
[0051]
图2为简化的一维主轴的结构示意图;
[0052]
图3为lstm神经网络的结构图;
[0053]
图4为on-lstmn的结构图;
[0054]
图5为ont-gcn的时空预测过程;
[0055]
图6为ont-gcn单元的示意图;
[0056]
图7为机床坐标系传动链的示意图;(a)为机床坐标系;(b)为坐标系传动链;
[0057]
图8为涡轮蜗杆的加工示意图;
[0058]
图9为x轴热误差示意图;
[0059]
图10为z轴热误差示意图;
[0060]
图11为圆柱滚刀的渐开线侧面示意图;
[0061]
图12为敏感性分析的流程图;
[0062]
图13为齿面误差分量敏感度指标的曲线图;
[0063]
图14为热误差时空预测原理图;
[0064]
图15为温度传感器现场布置;
[0065]
图16为蜗轮加工机床传感器网络;(a)为蜗轮蜗杆机床三维模型图;(b)为反映距离示意图;
[0066]
图17为传感器邻接矩阵;
[0067]
图18为800mm/min以下的温度场和热伸长率;(a)测量温度;(b)热误差;
[0068]
图19为1500mm/min下的温度场和热伸长率;(a)测量温度;(b)热误差;
[0069]
图20为预测性能对比的曲线图;
[0070]
图21为蜗轮蜗杆加工实验图;
[0071]
图22为齿面误差的示意图;
[0072]
图23为齿面误差曲线图;(a)不执行霾-边-雾-云系统;(b)使用霾-边-雾-云系系统进行几何误差控制;(c)使用霾-边-雾-云系系统进行几何-热误差控制。
具体实施方式
[0073]
下面结合附图和具体实施例对本发明作进一步说明,以使本领域的技术人员可以更好的理解本发明并能予以实施,但所举实施例不作为对本发明的限定。
[0074]
如图1所示,为本发明霾-边-雾-云误差补偿系统实施例的框架图。本实施例的霾-边-雾-云误差补偿系统,包括霾计算层、边缘计算层、雾计算层和云计算层。本实施例以蜗轮蜗杆机床为例,对霾-边-雾-云误差补偿系统的具体实施方式进行详细说明。
[0075]
所述霾计算层包括:温度传感器:用于测量温度;位移传感器:用于测量位移;采集卡:用于采集所述温度传感器和位移传感器测量得到的温度信号和位移信号;树莓派:所述树莓派上连接有用于将温度信号和位移信号转换为数字信息的a/d转换器;网关:用于经a/d转换器转换得到的数据传输至所述边缘计算层。具体的,霾计算层是终端,主要负责硬件
放置、数据采集和数据预处理。温度humirel ni1000sot和位移传感器micro-epsilon eddydt3010-a布置在霾计算层。温度和位移传感器的放置非常重要,因为合理的温度传感器网络可以反映蜗轮加工机床的热状态,正确放置的位移传感器可以准确测量热误差。被测信号由树莓派4采集,再传输到a/d转换器pcf8591模块进行数据转换,具体的,a/d转换器安装在树莓派4上,是典型的终端设备。数据通过树莓派4到达网关,然后发送到边缘层,所有的计算层都由esp8266wi-fi编程的linux传输。
[0076]
所述边缘计算层包括用于存储经所述霾计算层传入的数据的微型数据中心、用于过滤数据的交换机和用于将过滤后的数据传输至雾计算层和云计算层的网关和路由器,其中,历史数据传输至云计算层,实时误差数据传输至雾计算层。从雾层传输到边缘层的数据存储在微数据中心,数据通过交换机,其型号为西门子scalance x-200,检测出异常值,如果数据很大,它将被滤波并到达网关和路由器。其中,历史数据直接发送到云计算层数据库进行存储,实时错误数据发送到雾计算层进行错误建模和分析。
[0077]
所述雾计算层内设有分析模块,所述分析模块内设有如上所述基于ont-gcn时空模型的热误差预测模型,将以温度传感器、位移传感器的位置信息生成的邻接矩阵和以各个传感器采集的数据作为特征序列作为热误差预测模型的输入预测热误差,再结合误差映射模型得到误差补偿值,并将误差补偿值传输至云计算层。ont-gcn的建模过程在雾计算层完成。此外,ont-gcn模型的鲁棒性可能会在霾-边-雾-云系统运行一段时间后下降。因此需要云计算层将重新训练的模型传输到雾计算层。ont-gcn的输入有两个关键因素,即:(1)温度和位移传感器的位置信息用于生成邻接矩阵;(2)传感器采集的数据作为特征序列。数据从边缘计算层传输到雾计算层,根据蜗轮蜗杆机床的传递参数建立齿面误差映射模型,再结合齿面误差映射模型进行的灵敏度分析,确定关键误差项。如此就可以得到补偿值,传送到云计算层生成补偿指令。上述任务的执行平台为第11代intel core i5-1135g7,由cuda编程。
[0078]
所述云计算层包括误差补偿执行模块和热误差模型更新模块,所述误差补偿执行模块根据所述雾计算层输入的误差补偿值确定需要补偿的变量,并将补偿指令发送至霾计算层进行误差补偿;所述热误差模型更新模块根据边缘计算层输入的历史数据更新热误差预测模型,并将更新后的热误差预测模型传输至雾计算层。云计算层根据雾计算层提供的补偿值,确定需要补偿的变量,通过fb3输入补偿指令给西门子840d的霾计算层终端进行补偿。霾计算层接收来自云计算层的控制指令,通过伺服控制来控制各轴的实际位置,最后通过位置反馈调整实现重新控制。历史误差数据传输到配置有hadoop的云服务器,再由云服务器用于重新训练ont-gcn模型,ont-gcn模型更新后的参数传递到雾层。另外,云计算层还提供监控任务,通过云服务器识别异常情况,实现各层的工作状态的监控,。
[0079]
几何-热误差建模控制系统架构的合理布局,有利于提高补偿效率,缓解工业互联网的带宽压力。补偿建模架构如图1所示,用于构建霾-边-雾-云系统的功能划分见表1。
[0080]
表1构建雾边雾云系统的功能划分
[0081][0082]
1、基于ont-gcn时空模型的热误差预测模型及其建模方法的具体实施过程如下:
[0083]
1.1、时空行为
[0084]
将机床主轴简化为一维细长轴,如图2所示。主轴左端是自由的,由恒定的热流加热,右端固定。一维主轴的热微分方程为:
[0085][0086]
其中其中c表示比热容,ρ表示密度,k表示热导率;和是拉普拉斯算子;l表示轴的长度;t表示时间;
x
表示距离;
[0087]
热微分方程的初始条件如下:
[0088]
t(x,0)=t
t
[0089]
其中,t表示环境温度。为方便起见,坐标原点设置在自由端,因此边界条件为:
[0090][0091]
其中,h是一个正常数;温度t被离散化为:
[0092]
t(x,t)=x(x)t
ime
(t)
[0093]
得到:
[0094][0095]
只有当上式等于一个常数时,才是合理的,即:
[0096][0097][0098][0099]
根据热微分方程的初始条件,t
ime
=t
t
e-wt
;根据x的特征方程,可以选择解为
根据边界条件a=0,并得到为了避免平凡的解决方案,有一个方程
[0100]
如果则该方程有无数个解,满足(k-1/2)π<vk<kπ。那么就可以得到得到一个特殊的解为:
[0101][0102]
其中,bk是常数。因此,热变形为:
[0103][0104]
表明热误差数据的时空行为对于指导经验模型的选择具有重要意义。为了进一步了解热误差的时间和空间特性,将热传导模型离散为n个节点,热传导的表达式如下:
[0105][0106]
其中t=[t1,t2,t3,
…
tn]
t
;l=d-a,其中a表示邻接矩阵,d表示度矩阵;l表示拉普拉斯矩阵。gcn使用拉普拉斯矩阵来提取空间特征,gcn在提取特征过程中使用的laplacian矩阵与热传导过程中使用的laplacian矩阵是一致的,热扩散定律与gcn中的扩散定律是一致的。gcn可以描述空间热传导的特征,用于提取热误差的空间特征,再加上on-lstmn可以挖掘数据的时间特征,因此,所提出的ont-gcn可以捕获热误差的时间和空间特征。
[0107]
1.2、on-lstmn神经网络
[0108]
lstmn模型的结构如图3所示,遗忘门f
t
、输入门i
t
、输出门o
t
如下图所示:
[0109]ft
=σ(wf[h
t-1
,x
t
] bf)
[0110][0111][0112]
其中,x
t
表示输入向量;h
t-1
表示前一个单元的输出值,与x
t
结合增加三个门的权重;表示
t
时刻临时单元的内存状态;c
t-1
表示t-1时刻临时小区的小区状态;c
t
表示内存在t时刻的单元状态;wf,wi,wc和wo表示权重矩阵;bf,bi,bc和bo表示偏置向量;σ表示激活函数,是sigmoid;h
t
表示t时刻的隐藏状态。on-lstmn在lstmn的基础上设计了主遗忘门和主输入门
[0113]ft
=δ(wf[h
t-1
,x
t
] bf)
[0114]it
=δ(wi[h
t-1
,x
t
] bi)
[0115][0116]ot
=δ(wo[h
t-1
,x
t
] bo)
[0117][0118][0119]
cumax(
·
)=cumsum(softmax(
·
))
[0120][0121][0122][0123][0124]ht
=o
t
*tanh(c
t
)
[0125]
其中,和分别是和的权重矩阵,和表示它们的偏置向量;w
t1
、w
t2
和w
t3
分别表示高等级、中等级和低等级,其中,w
t1
*c
t-1
存储低等级信息,受当前输入信息的影响;存储高等级信息,受历史信息影响;存储中等级信息,受当前输入信息和历史信息影响;comsum是一个求和的函数。on-lstmn的结构如图4所示。
[0126]
on-lstmn对神经元进行排序后,信息水平由位置的前后表示。w
t1
*c
t-1
存储低等级信息,受当前输入信息的影响。存储高等级信息,受历史信息影响。存储的是中等级信息,受当前输入信息和历史信息影响。信息分级非常有利于热误差的预测。热误差数据包含长期趋势信息和短期瞬态信息。趋势信息是由于机器运行过程中温度持续升高引起的,瞬态信息是由环境干扰引起的,与当前时刻的输入密切相关。因此,需要合理保留热误差的长期和短期信息。on-lstmn可以将高等级信息保留相当远的距离,将热误差的趋势信息作为高等级信息。低等级信息可以在输入信息的每一步更新,热误差的瞬态信息作为低等级信息。重叠部分由处理。on-lstmn捕获了热误差的趋势特征和电流输入特征,显着提高了基于on-lstmn的热误差预测精度。
[0127]
1.3、ont-gcn神经网络
[0128]
为表征热误差的时间和空间行为,热误差的空间特征可以通过传感器网络的图g=(v,e)来反映,其中v是传感器的集合,e是传感器通道的集合。gcn的方程为:
[0129][0130]
其中,i表示单位矩阵;a表示邻接矩阵;x表示特征序列;w0表示第一层的权重参数;σ表示激活函数;
[0131]
热误差时空预测模型需要时空特性,即(1)空间特性由传感器网络g反映;(2)位移传感器信号序列反映时间特性。因此,热误差的时空预测问题可以表示为传感器网络g与特征序列x
t
之间映射关系f的学习,下一时刻t的热误差序列可以表示为:
[0132]
[x
t 1
,
…
,x
t t
]=f(g;(x
t-n
,
…
,x
t-1
,x
t
))
[0133]
其中,n表示历史时间序列的长度。
[0134]
为了捕捉传感器网络的时间和空间依赖性,提出了基于on-lstmn和gcn的ont-gcn模型。ont-gcn的时空预测过程如图5所示。邻接矩阵和传感器的时间数据作为ont-gcn的输入,gcn用于提取传感器的空间特征,on-lstmn模型用于提取序列的时间特征,如此即可实现数据预测了。
[0135]
传输过程如图6所示,图6左边是热误差的时空预测,右边是ont-gcn信元。gc是图卷积过程。h
t-1
和h
t
分别是t-1时刻和
t
时刻的输出。w和b分别是权重和偏差。将on-lstmn中的x
t
更新为f(x,a),则f
t
,i
t
,o
t
,和的六个门被改写为:
[0136]ft
=δ(wf[h
t-1
,f(a,x
t
)] bf)
[0137]it
=δ(wi[h
t-1
,f(a,x
t
)] bi)
[0138][0139]ot
=δ(wo[h
t-1
,f(a,x
t
)] bo)
[0140][0141][0142]
如此,所提出的ont-gcn单元可以通过f(a,x
t
)捕获传感器网络的空间依赖性,然后使用f
t
,i
t
,o
t
,和的六个独特门来有序地挖掘热误差的时间和空间依赖性,从而有效地完成了热误差的时空预测任务。
[0143]
1.4、基于ont-gcn时空模型的热误差预测模型及其建模方法
[0144]
热误差时空预测框架如图14所示,本实施例基于ont-gcn时空模型的热误差预测模型的建模方法,包括如下步骤:
[0145]
11)构建传感器网络:在机床上布置温度传感器和位移传感器,并将各个传感器分别标记在机床的三维模型上。在蜗轮蜗杆机床上合理布置温度和位移传感器,采用9个测温点和1个位移测点,如图15所示。以上9个测温点可以完整反映整个机床的温度场分布并挖掘它们对位移传感器的依赖性。时空预测可以胜任挖掘相关性的任务,将传感器节点标记在蜗轮机床三维模型上,传感器网络如图16(a)所示,s代表位移传感器。由于x和y方向的位移传感器相对较近,因此将它们视为同一节点。可以看出,s接近于t7、t8和t9,所以热误差主要受它们影响。
[0146]
12)生成时空图数据集:根据时空图的假设,需要两个条件来预测当前节点的热误差信号,分别为:
①
位移测量点的历史热误差信号;
②
相邻传感器的位置和历史信号。图16(b)是反映距离的示意图,传感器网络的空间特征由邻接矩阵表征,导热通道在材料方向,不同部位的导热系数不同,因此,邻接矩阵应根据热导率进行加权。为简化模型,本实施例仅考虑材料方向的直线距离,计算邻接矩阵为:
[0147][0148]
其中,w
i,j
表示边权重,与节点i和节点j的位置有关;δ表示控制w
i,j
分布的阈值;d
i,j
为节点i和节点j之间的距离,是机床三维模型上测量得到的,如表5所示。
[0149]
表5每两个节点之间的距离
[0150][0151]
从而得到邻接矩阵,如图17所示。可以看出,t8和t9比其他传感器对热误差的影响更大,因为它们更靠近位移传感器。以上9个测温点t8、t9温升明显,说明t8、t9是引起热误差的主要热源。
[0152]
图18为转速800r/min,运行时间100分钟左右得到的图;图19是在1500r/min的速度和大约45分钟的运行时间下得到的。这两个实验的结果用于获得热特性的时序特性。图18用作训练集,图19用作测试集。速度和运行时间的不同导致温度场和热变形的不同趋势。但是,蜗轮蜗杆机床的热误差产生机制没有改变,即热误差的时空依赖性不会改变。时空预测模型用于学习这种依赖性,变化的条件可以测试所提出的ont-gcn模型的鲁棒性。
[0153]
13)构建如上所述基于ont-gcn时空模型的热误差预测模型。收敛时间与硬件和软件平台有关,详情如下:使用windows 10操作系统,cpu为第11代intel core i5,ram为16.0gb。该程序由python编程语言开发,开发环境为pycharm community edition 2020.2.5,管理使用anaconda。为了便于机器学习建模,使用pytorch机器学习库进行编程。
[0154]
为了测试所提出的ont-gcn模型的有效性,使用mlr、标准lstmn和on-lstmn与ont-gcn进行比较。超参数是影响ont-gcn模型预测性能和鲁棒性的重要因素,通过贝叶斯优化算法进行优化。由于传感器节点的信号电平不同,在训练模型之前需要对特征序列进行归一化,然后对预测结果进行反向归一化。为了比较,lstmn、on-lstmn和ont-gcn被设置为具有表6中列出的相同超参数。
[0155]
表6模型超参数
[0156][0157]
此外,mlr作为传统的热误差建模方法也用于与ont-gcn进行比较。通过模糊聚类选择了三个温度变量t5、t8和t9,调用matlab中的regress toolbox,确定x方向热误差的回归系数为b0=0.9974,b1=84.677,b2=-36.593and b3=28.687;b0=-0.3514,b1=133.667,b2=-35.048,and b3=-64.987为y方向。那么,建立的mlr模型为:
[0158][0159]
结果表明,mlr只将温度作为输入,并没有考虑两个重要的关键点,即(1)热误差序列的时间特性,以及(2)传感器节点的空间特性。因此,mlr无法表征错误的时间和空间特
征。
[0160]
14)以邻接矩阵和传感器的时间数据作为热误差预测模型的输入,预测热误差。
[0161]
x-和y-方向的预测结果如图20所示。mlr模型只能捕捉到热误差的趋势,而不能捕捉到热误差的瞬态特征。mlr受温度影响很大,未经过滤的温度波会在热误差的预测结果中产生噪声。时间序列预测模型可以更好地捕捉热误差数据的非线性特征,而且,具有空间特征提取能力的时间序列模型比其他误差预测模型具有更优异的预测性能。
[0162]
然后计算评价指标,如表7至8所示。ont-gcn的rmse小于on-lstmn模型的rmse,因为ont-gcn模型基于热误差产生机制考虑了温度传感器的空间特性。ont-gcn模型比on-lstmn模型消耗更多的时间,因为卷积操作增加了计算量。on-lstmn模型的rmse小于lstmn模型,因为on-lstmn模型保留了基于有序神经元的热误差的长期趋势和短期瞬态特性。on-lstmn模型比lstmn模型花费更多的时间,因为额外的和增加了计算量。lstmn模型的rmse小于mlr模型,因为lstmn模型可以反映热误差的时间特征。lstmn模型比mlr需要更多的时间,因为lstmn需要根据输入不断改变门的状态,而mlr模型是固定参数的模型。因此,热误差的时间特性是首要考虑的问题。引入温度传感器的空间特性可以进一步探索温度场之间的关系,提高热误差的预测精度。
[0163]
表7x方向热误差预测性能评价
[0164][0165]
表8y方向热误差预测性能评价
[0166][0167]
2、误差映射模型
[0168]
本实施例的误差映射模型为根据蜗轮蜗杆机床的传递参数建立的齿面误差与几何-热误差的映射模型。
[0169]
蜗轮蜗杆机床的结构和传动顺序分别如图7(a)和图7(b)所示,传动链0-3-4-5-6-7-8从床身传送到滚刀端,传动链0-1-2从床身传送到工件端。蜗轮蜗杆机床有六个主要的运动轴,功能见表2。x、y、z、a、b、c轴的误差是影响机床加工精度的主要误差源,因此,有必要重点分析这些误差。
[0170]
表2机床运动轴功能特性
[0171]
[0172]
齿轮加工时,滚刀与工件的位置关系如图8所示,根据齿轮啮合原理,滚刀(b轴)的旋转角度b和工件(c轴)的旋转角度有固定的比例关系。蜗轮和滚刀的模数为mn,螺旋角为β和λ,齿数分别为z1和z2,工件和滚刀在p点具有相同的切向速度v0,即:
[0173][0174]
其中,ωg和ωh分别表示工件和滚刀的角速度。那么工件转角与滚刀转角b的比例关系表示为:
[0175][0176]
具体的,齿面误差与几何-热误差的映射模型的创建方法为:
[0177]
21)根据蜗轮蜗杆机床的坐标系传动链,得到理想状态下滚刀坐标系h相对于工件坐标系g的齐次变换矩阵
[0178]
在理想状态下,蜗轮蜗杆机床各运动副均无运动误差,每两个相邻运动对之间的齐次坐标变换矩阵(齐次坐标变换矩阵)表示为:
[0179][0180][0181]
理想状态下滚刀坐标系h相对于工件g坐标系的齐次坐标变换矩阵为:
[0182][0183]
其中,和分别表示理想状态下c轴相对于工件坐标系的齐次坐标变换矩阵和滚刀坐标系相对于b轴的齐次坐标变换矩阵,且和滚刀坐标系相对于b轴的齐次坐标变换矩阵,且表示表示理想状态下床身r相对于c轴坐标系的齐次坐标变换矩阵,身r相对于c轴坐标系的齐次坐标变换矩阵,表示表示理想状态下c轴相对于床身r坐标系的矩阵;表示表示理想状态下x轴相对于床身r坐标系的距离为x的矩阵;表示表示理想状态下z轴相对于x轴的距离为z的矩阵;表示表示理想状态下a轴相对于z轴的矩阵;表示表示理想状态下y轴相对于a轴的矩阵;表示表示理想状态下b轴相对于y轴的矩阵;
[0184]
22)在实际状态下,结合理想状态下滚刀坐标系相对于工件坐标系的齐次变换矩阵考虑各运动副的误差,得到滚刀坐标系h相对于工件坐标系g的齐次变换矩阵
[0185]
在实际加工过程中,制造、装配、调试、运动等过程中都会产生各种误差,实际状态下的齐次坐标变换矩阵与理想状态下的齐次坐标变换矩阵存在差异。实际状态下的齐次坐标变换矩阵为:
[0186]
[0187]
其中,和分别表示p坐标系到q坐标系的运动误差矩阵、几何误差矩阵和热误差矩阵。
[0188]
对于x轴相对于床身的齐次坐标变换矩阵,几何误差矩阵为运动误差矩阵表示为:
[0189][0190]
其中,ε
xx
、ε
yx
和ε
zx
分别表示x轴沿x方向的定位误差,x轴沿y方向的直线度误差,x轴沿z方向的直线度误差;ε
xx
、ω
yx
和ε
zx
分别表示x轴绕x方向的角度误差,x轴绕y方向的角度误差和x轴沿z方向的角度误差。
[0191]
而且,x轴是机床的最大部件,需要考虑其热误差。床身与工作台刚性连接,因此x轴和c轴一起分析。床身的加热主要来自两个方面:一是加工过程中冷却液与金属屑形成的高温混合物所产生的热量,二是立柱在x轴方向移动时因摩擦产生的热量。床身向上弯曲变形引起x轴上的两个位置误差,分别是x方向的位置误差和z方向的位置误差如图9所示。
[0192][0193][0194]
其中,l表示床身上表面长度;h表示立柱内侧面长度;β表示床身热变形引起x轴在y方向的角度误差;δl表示床身上表面在x轴方向总的受热膨胀量。
[0195]
那么热误差矩阵为:
[0196][0197]
则x轴相对于床身坐标系的齐次坐标变换矩阵为:
[0198][0199]
对于z轴相对于x轴的齐次坐标变换矩阵,几何误差矩阵和运动误差矩阵表示为:
[0200][0201]
其中,s
xz
表示z轴沿x方向的垂直度误差;δ
xz
表示z轴沿x方向的直线度误差;δ
yz
表
示z轴沿y方向的直线度误差;δ
zz
表示z轴沿z方向的定位误差;ε
xz
表示z轴绕x方向的角度误差;ε
yz
表示z轴绕y方向的角度误差;ε
zz
表示z轴绕z方向的角度误差。
[0202]
此外,z轴受热误差影响很大,因为立柱是蜗轮机床的第二大部件。立柱向外弯曲变形,导致z轴产生两个位置误差,分别是x方向的位置误差和z方向的位置误差如图10所示。
[0203][0204][0205]
其中,h'表示立柱上表面长度;w表示立柱外侧面长度;α表示立柱热变形引起z轴在y方向的角度误差;δh'表示表示立柱在z轴方向总的受热膨胀量。
[0206]
热误差矩阵为:
[0207][0208]
可以得到z轴相对于x轴的齐次坐标变换矩阵
[0209][0210]
对于a轴相对于z轴的齐次坐标变换矩阵,几何误差矩阵和运动误差矩阵表示为:
[0211][0212]
其中,δ'
ya
表示a轴沿y方向的位置误差;δ'
za
表示a轴沿z方向的位置误差;ε'
ya
表示a轴在xz平面内的平行度误差;ε'
za
表示a轴在xy平面内的平行度误差;δ
xa
表示a轴沿x方向的直线度误差;δ
ya
表示a轴沿y方向的直线度误差;δ
za
表示a轴沿z方向的直线度误差;ε
xa
表示a轴绕x方向的角度误差;ε
ya
表示a轴绕y方向的角度误差;ε
za
表示a轴绕z方向的角度误差;γ表示a轴绕x方向旋转的角度。
[0213]
则a轴相对于z轴的齐次坐标变换矩阵为:
[0214][0215]
对于y轴相对于a轴的齐次坐标变换矩阵,几何误差矩阵和运动误差矩阵表示为:
[0216][0217]
其中,s
xy
表示y轴沿x方向的垂直度误差;s
zy
表示y轴沿z方向的垂直度误差;δ
xy
表示y轴沿x方向的直线度误差;δ
yy
表示y轴沿y方向的定位误差;δ
zy
表示y轴沿z方向的直线度误差;ε
xy
表示y轴绕x方向的角度误差;ε
yy
表示y轴绕y方向的角度误差;ε
zy
表示y轴绕y方向的角度误差。
[0218]
则y轴相对于a轴的齐次坐标变换矩阵为:
[0219][0220]
对于b轴相对于y轴的齐次坐标变换矩阵,几何误差矩阵和运动误差矩阵表示为:
[0221][0222]
其中,δ
xb
表示b轴沿x方向的直线度误差;δ
yb
表示b轴沿y方向的直线度误差;δ
zb
表示b轴沿z方向的直线度误差;ε
xb
表示b轴绕x方向的角度误差;ε
yb
表示b轴绕y方向的角度误差;ε
zb
表示b轴绕z方向的角度误差;δ'
xb
表示b轴沿x方向的位置误差;δ'
zb
表示b轴沿z方向的位置误差;ε'
xb
表示b轴在yz平面内的平行度误差;ε'
zb
表示b轴在xy平面内的平行度误差。
[0223]
则b轴到y轴的齐次坐标变换矩阵为:
[0224][0225]
对于床身c轴相对于r坐标系的齐次坐标变换矩阵,几何误差矩阵和运动误差矩阵表示为:
[0226][0227]
其中,δ'
xc
表示c轴沿x方向的位置误差;δ'
yc
表示表示c轴沿y方向的位置误差;ε'
xc
表示c轴在yz平面内的平行度误差;ε'
yc
表示c轴在xz平面内的平行度误差;δ
xc
表示c轴沿x方向的直线度误差;δ
yc
表示c轴沿y方向的直线度误差;δ
zc
表示c轴沿z方向的直线度误差;ε
xc
表示c轴绕x方向的角度误差;ε
yc
表示c轴绕y方向的角度误差;ε
zc
表示c轴绕z方向的角度
误差。
[0228]
则c轴到床身的齐次坐标变换矩阵为:
[0229][0230]
在实际状态下,考虑各运动副的误差,滚刀坐标系h相对于工件坐标系g的齐次坐标变换矩阵为:
[0231][0232]
其中,和分别表示实际状态下c轴相对于工件坐标系的齐次坐标变换矩阵和滚刀坐标系相对于b轴的齐次坐标变换矩阵,且和滚刀坐标系相对于b轴的齐次坐标变换矩阵,且表示实际状态下x轴相对于床身坐标系的齐次坐标变换矩阵;表示实际状态下z轴相对于x轴的齐次坐标变换矩阵;表示实际状态下a轴相对于z轴的齐次坐标变换矩阵;表示实际状态下y轴相对于a轴的齐次坐标变换矩阵;表示实际状态下b轴相对于y轴的齐次坐标变换矩阵;表示实际状态下c轴相对于床身r坐标系的齐次坐标变换矩阵,且
[0233]
将热误差和几何误差映射到工具的空间误差为:
[0234][0235]
其中,[a,b,c,1]
t
和[i,j,k,0]
t
分别表示滚刀中心位置和轴姿态的齐次坐标;δ和
ε
分别表示位置误差和姿态误差,δ
x
、δy和δz分别表示x、y、z方向的位置误差分量;ε
x
、εy和εz分别表示x、y、z方向的姿态误差分量。
[0236]
23)创建齿面误差与几何-热误差的映射模型
[0237]
渐开线齿轮滚刀端面齿廓为标准渐开线,如图11所示。齿廓基圆半径r
bh
对称,σ0为基齿槽半角,u为渐开线展开角。那么坐标系o
p
x
pyp
中渐开线a0b0的参数方程为:
[0238][0239]
其中,表示滚刀的转角。
[0240]
顺时针旋转时,得到角度θ,得到渐开线齿面a1b1,参数方程为:
[0241]
[0242][0243]
其中,ph表示滚刀的螺旋参数,ph=mnz/[2
·
sin(π/2-λ)];mn和z分别表示齿轮滚刀的法向模数和头数。齿面的法向量为:
[0244][0245]
在理想状态下,理想齿面在工件坐标系中的坐标向量和单位法向量表示为:
[0246][0247][0248]
其中,表示理想状态下工件坐标系g相对于滚刀坐标系h的齐次变换矩阵,且表示理想状态下工件坐标系g相对于滚刀坐标系h的齐次变换矩阵,且表示理想齿面在工件坐标系中的坐标向量;rh表示滚刀齿面的渐开线参数方程;表示理想齿面在工件坐标系中的单位法向量;nh表示滚刀齿面的单位法向量;
[0249]
则在考虑了热误差和几何误差的实际状态下,工件坐标系中的坐标向量和单位法向量表示为:
[0250][0251][0252]
其中,表示实际状态下工件坐标系g相对于滚刀坐标系h的齐次变换矩阵,且表示实际状态下工件坐标系g相对于滚刀坐标系h的齐次变换矩阵,且表示实际齿面在工件坐标系中的坐标向量;表示实际齿面在工件坐标系中的单位法向量;
[0253]
从而得到齿面误差与几何-热误差的映射模型为:
[0254][0255]
其中,n表示离散值;齿面误差定义为e=[δ;ε]=[δ
x
,δy,δz,ε
x
,εy,εz]
t
,其中δ
x
,δy和δz分别表示x、y、z方向的齿面位置误差分量;ε
x
,εy,εz分别表示齿面单位法向量在x、y、z方向的分量。
[0256]
进一步,基于所述齿面误差与几何-热误差的映射模型,采用morris方法识别出齿面误差的关键误差项,所述雾计算层中,结合所述齿面误差与几何-热误差的映射模型得到所述关键误差项的误差补偿值,并将关键误差项的误差补偿值传输至云计算层。
[0257]
具体的,对蜗轮蜗杆加工误差敏感性分析的方法如下。
[0258]
敏感性分析方法常用于统计学或经济学领域,该方法的目标是识别和分析对目标结果有重要影响的敏感因素。基于齿面误差与几何-热误差的映射模型,采用morris方法识别出齿面误差的关键误差项和敏感部位,为后续研究提供理论支持。敏感性分析流程如图12所示。
[0259]
循环次数n极大地影响morris方法的运行效率。经过多次测试,选择n=50来平衡实验效率和求解精度。选取直线轴和旋转轴的几何误差和热误差g=[x1,x2,...,xm]
t
作为
模型输入参数,以6个齿面误差e=[δ
x
,δy,δz,ε
x
,εy,εz]
t
作为分析目标。输出是每个几何误差和热误差的均值μi和标准差σi。具体的,以δ
x
为分析对象,将morris方法应用于机床的几何误差。齿面误差映射模型的具体过程如下:
[0260]
(1)求解齐次变换矩阵、渐开线滚刀模型、几何和热误差g=[x1,x2,...,x
55
]
t
。
[0261]
(2)利用机床的齐次坐标变换矩阵将渐开线滚刀方程转换为工件坐标系,计算渐开线扩展角u的取值范围,并根据扩展角取值范围将转换后的方程离散化,获得一定数量的离散点坐标方程并计算法向量方程ng。
[0262]
(3)测量每个运动轴的热和几何误差分布。测量结果表明,热误差、几何位移误差和几何角度误差分别在[0,100μm]、[0,20μm]和[0,29mdeg]范围内均匀分布。热误差、几何位移误差、几何角度误差的误差采样区间分别生成为{0,δ1,2δ1,...,100},{0,δ1,2δ1,...,20}和{0,δ3,2δ3,...,29}。其中δ1=1/(q-1)
×
100,δ2=1/(q-1)
×
20和δ3=1/(q-1)
×
29,生成几何误差基向量向量元素的值在采样间隔内随机采样。
[0263]
(4)误差个数为m=55,构造并生成随机化矩阵和随机化采样矩阵然后将的每一行元素作为齿面误差与几何-热误差,并且任何相邻的两行都只有某个误差元素与δ不同。
[0264]
(5)将步骤(4)中得到的随机抽样矩阵的第i
th
行代入接触条件作为输入参数,求解二元非线性方程组。得到滚刀加工面与待加工蜗轮齿面的接触点组。在输入误差参数的条件下,这些接触点形成的轨迹被用作加工的齿面方程。
[0265]
(6)计算每个误差项的基本效果,重复步骤(4)至(5)。独立计算每个误差的n个基本效应,得到其均值μi和标准差σi。
[0266]
本实施例的滚刀和蜗轮蜗杆加工参数设置见表3。
[0267]
表3滚刀、蜗轮加工参数设置
[0268][0269][0270]
误差敏感性分析结果如图13所示。横坐标为由51个几何误差和4个热误差项组成的误差序列,纵坐标为均值μi和标准偏差σi。比较误差序列中每个误差项的灵敏度指标μi和σi的大小,根据具体的齿面成分识别出关键误差项。也可以通过对运动轴的整体评价来判断某一运动轴误差项的敏感性,以齿面误差δ
x
为例进行分析。根据图13,关键误差项通过比较均值μi确定,分别为δ
xx
,ε
yx
,δ
xy
,ε
yy
,δ
xz
,ε
yz
,δ
xa
,ε
ya
,ε
ya
',ε
yb
,δ
xc
,ε
yc
,ε
yc
',δ
xc
',δ
txx
,andδ
tzx
,,通过比较标准差σi确定耦合误差,分别为ε
yx
,ε
zx
,ε
zy
,s
xy
,ε
yz
,ε
za
,,ε
ya
',ε
zb
,ε
zb
',ε
yc
,ε
zc
,ε
yc
',δ
tzz
,δ
txz
,δ
txx
,andδ
tzx
。
[0271]
综合评价表明,敏感元件的顺序为x》c》a》z。因此,应综合考虑上述误差项,调整c轴和x轴的精度,以减小齿面误差。可以得到每个齿面误差的关键误差和敏感部位,如表4所示。因此,找出关键误差并根据计算出的补偿值进行补偿,可以提高蜗轮蜗杆加工机床的加
工精度。
[0272]
表4关键错误和敏感部分
[0273][0274]
3、系统构架验证
[0275]
为了测试所提出架构的有效性,表9列出了以ont-gcn模型作为错误预测模型的不同系统架构的执行时间。霾-云、霾-边缘-云、霾-雾-云和本实施例提出的霾-边-雾-云架构系统的总执行时间分别为184s、179s、164s和153s。霾-边-雾-云系统架构为四层架构。综合发挥霾计算层、雾计算层和边缘计算层服务器的优势。对于霾-边-雾-云系统,在边缘层进行数据异常检查。将训练有素的ont-gcn模型嵌入到雾层中以实现热误差预测。雾层中嵌入了齿面误差与几何热误差的映射模型和灵敏度分析模型。云层用于实现ont-gcn误差模型的再训练。ont-gcn误差模型更新后的参数传递到雾层,实现训练好的ont-gcn模型的参数更新。霾-云系统架构只有两层。为保证比较的公平性,将数据异常检查和模型预测再训练放在云层,导致云层计算量增加;此外,由于缺少边缘层和雾层,云层的数据传输时间和时间消耗显着增加,导致霾-云架构最耗时。霾-边-云架构分为三层,边缘层分担霾-边-雾-云系统架构中雾层的工作,承担数据异常检查任务,导致边缘层花费的时间增加,云层花费的时间比霾-云架构的云层花费的时间减少;边缘层的边缘服务器具有强大的计算能力和数据传输能力,导致霾-边-云架构的执行时间比霾-云架构短。霾-雾-云架构也有三层,雾层分担边缘层的任务,承担数据异常检查任务;雾服务器的计算能力和数据传输能力强于边缘服务器,因此,雾层可以承担数据异常检查和错误预测等任务,所以霾-雾-云架构的效率要高于雾-边-云架构。对于所提出的霾-边-雾-云系统架构,与霾-雾-云架构相比,数据传输时间减少,并且所提出的系统架构在所有架构中效率最高。
[0276]
表9ont-gcn不同框架的时间消耗
[0277][0278][0279]
3.1、加工实验验证
[0280]
随着提出的霾-边-雾-云系统的实施,进行了蜗轮的加工实验,如图21所示。求解了网格点坐标和单位法向量。蜗轮机参数如下:加工的蜗轮为右手蜗轮,蜗杆头数z1为1,蜗轮齿数z2为90,齿廓角a为20
°
,模数m为5,分度圆的直径d1为320mm,修正系数x2为0.042,齿顶高度系数h为1,头部间隙系数为0.2。
[0281]
如图22所示,可以清楚地获得整个齿面的误差分布,得到蜗轮齿面误差测量的最
终结果。根据网格平面图,齿面有5列9行网格点,每条网格有45个网格点,如图22所示。红色实线代表实际齿面点数据,蓝色交错虚线表示理论齿面点数据,上下两侧为齿面齿根,中间部分为齿面齿顶。两个网格用于表示整个牙齿的左侧和右侧的误差。每个测量点的误差值用该点垂直黑色实线的长度表示。箭头符号表示左右两侧齿面误差的方向。
[0282]
给定相同的实验条件,多次测量同一被测齿面,并通过多次测量计算平均误差值。
[0283][0284]
其中,xi表示第i次测量得到的误差;n为误差测量的次数。
[0285]
每个测量网格点的单个数据的标准不确定度由贝塞尔方程计算。
[0286][0287]
标准不确定度为:
[0288][0289]
由测量重复性引起的标准不确定度u
x
的计算属于a类不确定度,即自由度为v=n-1。
[0290]
计算正态误差,如表10中所列。
[0291]
表10齿面法向误差
[0292]
[0293][0294]
如图23所示,得到齿面误差。不实施霾-边-雾-云系统时,齿面第一、二、三、四、五行几何误差在范围内分别为[5.75μm,23μm]、[5.75μm,21.85μm]、[0,23μm]、[-0.23μm,17.25μm]和[5.75μm,19.55μm]。采用霾-边-雾-云系统进行几何误差控制时,齿面第一、二、三、四、五行几何误差在[2.95μm,13.47μm]范围内,[5.26μm,13.31μm],[0.12,14.13μm],[-0.28μm,11.27μm],和[4.60μm,12.81μm]。采用霾-边-雾-云系统进行几何-热误差控制时,齿面第一、二、三、四、五行几何误差在[3.27μm,12.87μm],[2.35μm,11.70μm],[0.23,13.28μm],[-0.20μm,8.90μm]和[2.23μm,10.35μm]范围内。结论是,霾-边-雾-云系统的实施减少了齿面几何误差,因此,所提出的系统架构的效率得到验证。此外,嵌入模型,包括ont-gcn模型、渐开线滚刀模型以及齿面误差与几何热误差之间的映射模型,都得到了验证。更重要的是,采用雾边-雾云系统进行几何误差控制的齿面几何误差大于采用雾边-雾云系统进行几何-热误差控制的齿面几何误差。控制。因此,证明了几何热误差控制的必要性。
[0295]
4、结论
[0296]
霾-边-雾-云计算系统基于ont-gcn时空模型进行几何和热误差补偿与预测。基于ont-gcn时空模型提出深度学习热误差模型。此外,提出了齿面误差与几何-热误差的映射模型和灵敏度分析模型,并将其嵌入到霾-边-雾-云计算系统的雾层中。证明了热补偿和几何误差补偿的必要性。最后,通过执行所提出的霾-边-雾-云计算系统,实现了同时的几何-热误差控制。主要结论如下:
[0297]
(1)在误差控制方面,设计了霾-边-雾-云计算系统来补偿几何误差和热误差。霾-云系统、雾-边-云系统、霾-雾-云系统和霾-边-雾-云系统的总执行时间分别为184s、179s、164s和153s。霾-边-雾-云计算系统实现了合理的任务分配,所提出的霾-边-雾-云系统的执行效率高于霾-云系统、霾-边-云系统和霾-雾-云系统。
[0298]
(2)求解一维热传导的偏微分方程,揭示误差机制。结果表明,热变形是运行时间和空间的函数。应建立一个能够捕捉时空特征的模型。错误机制为ont-gcn模型提供了理论依据。为提高热误差的预测精度,构建了蜗轮蜗杆机床传感器网络,反映热误差与温度的空
间位置关系,并提出了用于时空预测的ont-gcn模型。一个传感器网络可以充分反映蜗轮蜗杆机床的热状态,网络拓扑作为ont-gcn的输入之一。提议的ont-gcn模型可以保留和捕获ont-gcn单元中的空间和时序特征。ont-gcn单元的独特排序特性允许保留重要的热误差信息。因此,ont-gcn单元可以有序地传递热误差的时间和空间特征,从而比其他机器学习模型更高的预测精度。mlr、lstmn、on-lstmn和ont-gcnn模型的预测准确率分别为93.18%、94.56%、95.36%和97.35%。mlr、lstmn、on-lstmn和ont-gcn的rmse分别为0.7642、0.6931、0.4822和0.4167。
[0299]
(3)考虑热误差产生的机理,考虑x轴和z轴的剧烈热变形,根据几何关系反映热误差的变化。然后获得几何误差和热误差的转换矩阵。齿面误差与几何热误差的映射模型及灵敏度分析模型。使用morris方法识别关键误差项,然后通过映射模型对关键误差项进行补偿。当采用霾-边-雾-云系统进行几何误差控制时,齿面第一、二、三、四、五排的几何误差减小到[2.95μm,13.47μm],[5.26μm,13.31μm],[0.12,14.13μm],[-0.28μm,11.27μm]和[4.60μm,12.81μm]范围内。当采用霾-边-雾-云系统进行几何-热误差控制时,齿面第一、二、三、四、五排的几何误差减小到[3.27μm,12.87μm]、[2.35μm,11.70μm]、[0.23,13.28μm]、[-0.20μm,8.90μm]和[2.23μm,10.35μm]范围内。
[0300]
以上所述实施例仅是为充分说明本发明而所举的较佳的实施例,本发明的保护范围不限于此。本技术领域的技术人员在本发明基础上所作的等同替代或变换,均在本发明的保护范围之内。本发明的保护范围以权利要求书为准。
再多了解一些
本文用于企业家、创业者技术爱好者查询,结果仅供参考。