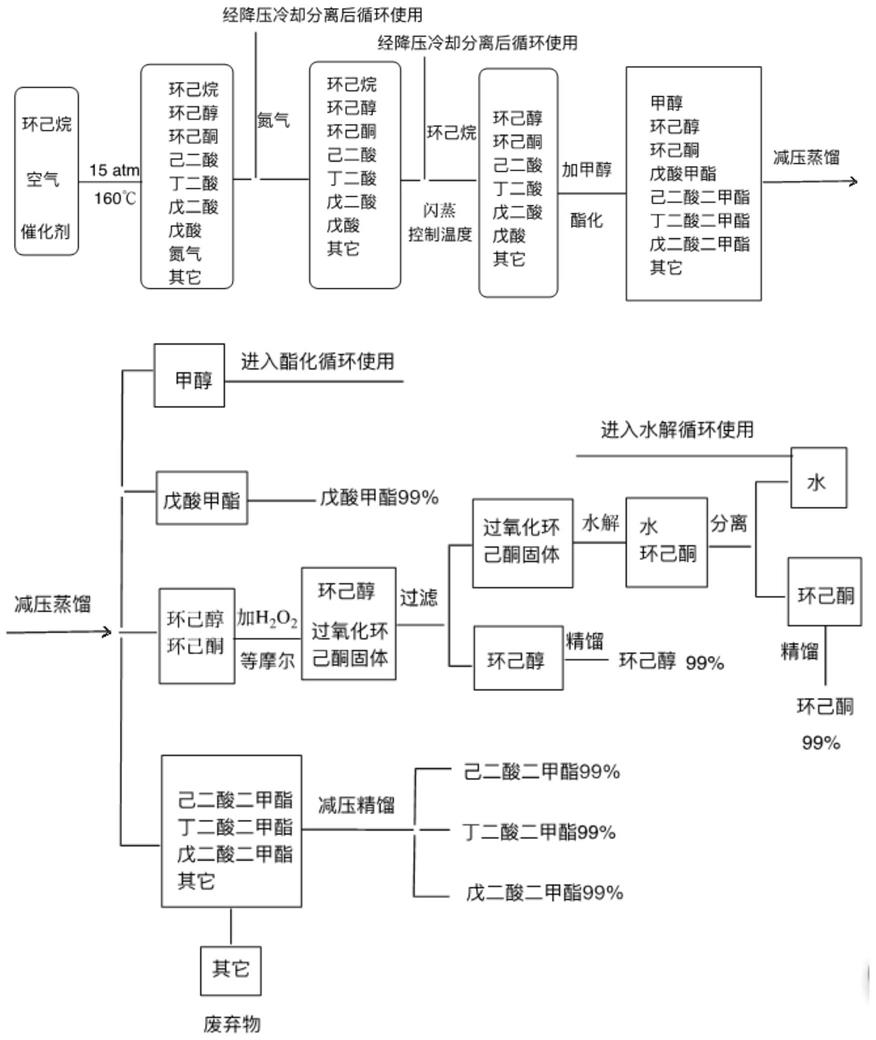
1.本发明涉及一种环己烷氧化方法,特别涉及一种环己烷空气催化氧化以及氧化生成的醇酮酸复杂氧化产物高效分离的方法,属于环己烷氧化技术领域。
背景技术:
2.环己烷的空气氧化是用于生产环己醇、环己酮、己二酸、戊二酸、丁二酸和戊酸的重要工艺。其中,环己酮和己二酸是分别用于制备尼龙6和尼龙66的主要原料,环己醇和戊二酸、丁二酸和戊酸也是重要的基本化工产品。但是,环己醇和环己酮物化性质非常相近,己二酸、戊二酸、丁二酸和戊酸的物化性质也非常相近,传统的化工分离过程很难用于环己醇和环己酮的分离或者己二酸、戊二酸、丁二酸和戊酸的混合羧酸体系的分离,而对于环己烷的空气氧化产物环己醇、环己酮、己二酸、戊二酸、丁二酸和戊酸的复杂产物系统,则更难应用传统化工分离过程进行分离。为了避免环己烷的空气氧化出现难于分离的复杂产物系统,美国专利us3530185a、us3957867a等专利技术公开了通过控制环己烷的空气氧化的较低转化率(小于4%),使氧化产物中不含羧酸产物而只含有环己醇和环己酮的混合物,再通过对环己醇和环己酮混合物进行催化脱氢处理,使环己醇转变为环己酮。但是这种方法并不能获得环己醇产物。虽然通过高精度精馏方法可以实现从环己醇和环己酮混合物分离出单一的环己醇和环己酮,但是能耗特别高,不适合大型工业上的实际应用。环己醇和环己酮混合物进一步氧化可以变为己二酸为主要产物的羧酸混合产物,而水相体系的混合羧酸则可以通过多步重结晶方法将溶解度区别较大且含量较高的己二酸从混合羧酸中分离出来。工业上利用这一现象发展了比较成熟的生产己二酸的工艺:以过量50%~60%的硝酸在两级串联的反应器中,于60~80℃和0.1~0.4mpa下氧化ka油,催化剂为铜-钒系(铜0.1%~0.5%,钒0.1%~0.2%),收率为理论值的92%~96%,反应物蒸出硝酸后,经两次结晶精制可得高纯度己二酸,该方法虽然通过环己醇和环己酮混合物的氧化获得己二酸的收率较高,但是从环己烷氧化获得环己醇和环己酮的收率和选择性均较低,由此,从环己烷原料经历了两步氧化反应到己二酸的过程中,对环己烷原料及中间产物的利用率低。近年,也有直接将环己烷空气催化氧化来获得ka油和己二酸的相关报道,如中国专利(cn1850756a)公开了环己烷原料中加入1~100ppm金属卟啉为催化剂,以及通入1~20atm的空气或者氧气或者富氧空气或者贫氧空气,在温度120~160℃条件下,反应45~120分钟,可以获得含量大于90%的环己醇、环己酮和己二酸混合物。实际上,在使用这些技术生产己二酸时,除己二酸之外,还有少量丁二酸、戊酸、戊二酸等产物存在,氧化产物为复杂的混合羧酸体系。这是一种处于非水系统的复杂混合产物体系,并且这些物质的溶解度、酸度等物化性质差别又比较小,分离比较困难。该专利没有公开从环己烷空气氧化的复杂产物体系中分离出环己醇、环己酮和己二酸的过程和方法。中国专利(cn121892c)公开了1-20atm、50~200℃使用1~100ppm单金属卟啉或μ-氧双金属卟啉或它们与过渡金属盐或氧化物构成的混合催化剂催化环己烷、环己醇、环己酮、环己烯单一原料或者环己醇与环己酮混合物生产己二酸的技
术,该技术提出了从环己烷或者环己烷氧化产物环己醇与环己酮氧化生产己二酸的方案。中国专利(cn101337879a)公开了环己烷在1~50ppm单金属卟啉或μ-氧双金属卟啉或它们与过渡金属盐或氧化物构成的混合催化剂作用下,通入5~12atm的空气或富氧、贫氧空气,控制反应温度为140~160℃,将环己烷氧化45~120分钟;氧化反应混合物进入闪蒸分离器,在温度78~155℃,压力0.1~1.0atm条件下闪蒸,使低沸点产物环己烷、环己醇和环己酮变为气体,与含量超过80%的己二酸分离;再将低沸点产物连续循环氧化,将高沸点氧化产物的分离纯化,得到精己二酸产品。该方法通过环己烷的循环使用和环己醇和环己酮的二次氧化,环己烷的转化率可以达到95%,但由于环己醇和环己酮二次氧化中存在深度氧化现象,己二酸的收率只有70%,有接近25%的其它环己烷氧化产物丁二酸、戊二酸、戊酸等,该专利技术中也没有提供纯化分离混合酸的方法,其中只分离到了高含量的己二酸产物。
3.技术内容
4.针对现有环己烷氧化产物分离技术存在的缺陷,本发明的目的是在于提供一种实现环己烷高效空气催化氧化并可以将醇、酮、酸等复杂氧化产物实现彻底分离获得附加值较高的环己醇、环己酮和多种酯类化合物的方法,该方法对环己烷的转化率较高,且实现了各种原料及中间产物闭路循环,减少废液和废气排放量,同时获得多种附加值较高的目标产品,特别适合工业化大生产。
5.为了实现上述技术目的,本发明提供了一种环己烷空气催化氧化生成的醇酮酸复杂氧化产物分离的方法,该方法包括以下步骤:
6.1)环己烷在催化作用下进行空气氧化反应,得到含环己醇、环己酮和混合酸的环己烷溶液;所述混合酸包括戊酸、己二酸、丁二酸和戊二酸;
7.2)所述含环己醇、环己酮和混合酸的环己烷溶液通过闪蒸回收环己烷返回空气氧化反应过程,得到含环己醇、环己酮和混合酸的混合物;
8.3)含环己醇、环己酮和混合酸的混合物与甲醇进行酯化反应,酯化反应产物经过减压蒸馏分离,先蒸馏回收甲醇返回酯化反应过程,再分段蒸馏分离得到戊酸甲酯,环己醇与环己酮的混合物以及己二酸二甲酯、丁二酸二甲酯和戊二酸二甲酯的混合酯;
9.4)将环己醇与环己酮混合物与过氧化氢溶液进行氧化反应生成环己酮沉淀,固液分离,得到过氧化环己酮晶体和环己醇,过氧化环己酮经过水解得到环己酮和水混合液,静置分层,收集上层环己酮;或者,将环己醇和环己酮混合物进行催化脱氢得到环己酮;或者,将环己醇和环己酮混合物进行催化氧化得到混合酸,返回酯化反应过程;
10.5)将混合酯通过减压精馏,分别得到己二酸二甲酯、丁二酸二甲酯和戊二酸二甲酯产品。
11.作为一个优选的方案,环己烷在催化作用下进行空气氧化反应的条件为:温度为150~170℃,时间为1.5~2.5小时,空气压力为14~16atm,采用金属卟啉作为催化剂,或采用金属卟啉与过渡金属氧化物组合作为催化剂,催化剂在环己烷中的浓度为1~50ppm。在优选的反应条件下可以获得较高的环己烷转化率,可以控制环己烷转化率在20~40%。
12.作为一个进一步优选的方案,所述金属卟啉类化合物为四苯基卟啉铁、四对氯苯基卟啉铁、四苯基卟啉钴、四苯基卟啉铜、四苯基卟啉锰、四苯基卟啉铁μ-二聚体、四对氯苯基卟啉钴、四对氯苯基卟啉铜、四对氯苯基卟啉锰、四对氯苯基卟啉铁μ-二聚体中至少一
种;所述过渡金属盐为钴和/或锰的醋酸盐或者环烷酸盐中至少一种。这些催化剂都是现有技术中常见的可以用于环己烷空气催化氧化的催化剂,最优选为金属卟啉类化合物,而一般的过渡金属盐单独使用效果较差,需要搭配适当比例的金属卟啉类化合物催化剂使用,如金属卟啉催化剂的比例不低于10%,最好是不低于30%。
13.作为一个优选的方案,含环己醇、环己酮和混合酸的环己烷溶液通过闪蒸回收环己烷的条件为:温度为70~90℃,压强为0.5~1atm。在优选的条件下可以控制环己烷的选择性回收。
14.作为一个优选的方案,含环己醇、环己酮和混合酸的混合物与甲醇进行酯化反应的条件为:甲醇与混合酸摩尔比为1~2:1,在浓硫酸催化剂存在条件下,在70~90℃温度下,反应6~7小时,其中混合酸以其包含的羧基摩尔量计量。在优选的反应条件下可以获得较高的酯化反应效率,混合酸的酯化转化率可以达到95~98%。
15.作为一个优选的方案,酯化反应产物经过减压蒸馏分离的条件为:先在压力为80~90kpa,温度为45~55℃条件下蒸馏回收甲醇,再在压力为30~40kpa,温度为60~70℃蒸馏回收戊酸甲酯,再在压力为10~20kpa,温度为70~90℃蒸馏回收环己醇和环己酮混合物,最后在压力为1.7~5kpa,温度为90~115℃蒸馏回收己二酸二甲酯、丁二酸二甲酯和戊二酸二甲酯的混合酯。通过严格控制减压蒸馏条件,可以实现酯化反应产物的初步分离,可以获得高纯的甲醇和戊酸甲酯产品,而己二酸二甲酯、丁二酸二甲酯和戊二酸二甲酯等以混合酯形式回收,环己醇和环己酮也以混合物形式回收。
16.作为一个优选的方案,将过氧化氢溶液滴加至环己醇与环己酮混合物中在15~40℃温度下搅拌反应,析出过氧化环己酮沉淀,直到反应进行到无沉淀析出时,停止反应。通过过氧化氢氧化法可以实现环己酮的选择性氧化定量生成过氧化环己酮,而过氧化环己酮在环己醇中溶解度低,从而通过简单过滤分离即可实现两者的分离。
17.作为一个优选的方案,所述水解反应过程为:将过氧化环己酮置于水中加热到60~80℃进行水解反应。过氧化环己酮在大量水中经过加热可以再生成环己酮,而环己酮水溶性较低,且密度小于水,从而可以油水分离。
18.作为一个优选的方案,混合酯通过减压精馏的条件为:塔板数大于20,精馏过程为:压力为1.5~2kpa,釜底温度大于115℃,从精馏釜顶部、中部和底部分别收集得到丁二酸二甲酯、戊二酸二甲酯和己二酸二甲酯。塔板数优选为25~35。釜底温度优选为120~135℃。丁二酸二甲酯、戊二酸二甲酯和己二酸二甲酯物化性质较为相近,通过优选条件下进行加压精馏,可以分别获得均纯度大于99%的丁二酸二甲酯、戊二酸二甲酯和己二酸二甲酯产品。
19.作为一个优选的方案,环己醇和环己酮混合物在钯碳催化剂作用下,于200~210℃及0.01~0.1mpa进行催化脱氢得到环己酮产物;环己醇的脱氢反应在现有技术中比较常规,在优选的反应条件下,可以控制环己醇的高效选择性脱氢氧化,转化率达到98%以上。钯碳催化剂的用量为催化量,这是行业内熟知的。
20.作为一个优选的方案,环己醇和环己酮混合物在金属卟啉催化下,在空气压力为8~15atm,温度为140~160℃条件下,反应60~120分钟,得到混合酸。在优选的反应条件下可以实现环己醇和环己酮的同时高效氧化,获得以己二酸为主的混合酸产品,己二酸比例高达70%以上,还包含戊酸、丁二酸和戊二酸等产品。
21.所述金属卟啉催化剂为四苯基卟啉铁、四对氯苯基卟啉铁、四苯基卟啉钴、四苯基卟啉铜、四苯基卟啉锰、四苯基卟啉铁μ-二聚体、四对氯苯基卟啉钴、四对氯苯基卟啉铜、四对氯苯基卟啉锰、四对氯苯基卟啉铁μ-二聚体中至少一种。
22.相对现有技术,本发明技术方案带来的有益技术效果:
23.1)本发明技术方案实现了环己烷的高效催化氧化,环己烷的转化率最高可以达到40%。
24.2)本发明技术方案实现了环己烷、甲醇等原料以及环己醇、环己酮、混合酸等中间产物的内部循环,提高对原料或中间产物的利用率,同时减少废料排放。
25.3)本发明技术方案实现了环己烷复杂氧化产物的高效彻底分离,并可以同时获得高纯的环己醇、环己酮以及各种酯类化合物,克服了现有技术对环己烷氧化产物分离困难,且获得产物种类较少的技术问题。
26.4)本发明技术方案通过对氧化产物采用了先酯化再进行蒸馏、精馏等技术手段,大大简化了环己烷氧化产物分离过程,特别对于混合羧酸的分离,在现有技术中一般利用羧酸溶解度差别通过重结晶方法进行分离,或者利用羧酸酸性差别通过调节酸度的方法进行分离,这些工艺处理都难以适应工业上年产10万吨以上的混合羧酸分离过程,混合酸溶解度差别很小,酸度差别也很小,而通过酯化后,容易通过蒸馏和精馏等技术手段分离。
附图说明
27.图1为本发明实施例1的工艺流程图。
具体实施方式
28.以下实施例旨在进一步说明本
技术实现要素:
,而不是限制本发明权利要求的保护范围。
29.实施例1
30.本实施例提供的一种环己烷空气催化氧化生成的醇酮酸复杂氧化产物分离的方法,包括以下步骤:
31.1)环己烷原料加入反应釜内,添加20ppm四苯基卟啉钴,在温度为155℃,时间为2.5小时,空气压力为14atm,进行催化氧化反应,得到环己醇、环己酮、戊酸、己二酸、丁二酸和戊二酸及环己烷混合溶液,排出气体成分主要为氮气,经过冷却回收循环使用,环己烷转化率在30%;
32.2)将混合溶液在温度为75℃、压强为0.5atm的条件下进行闪蒸,所得环己烷经过冷却回收返回氧化过程循环使用,剩余即为含环己醇、环己酮和混合酸的混合物;
33.3)混合物与甲醇进行酯化反应,甲醇与混合物中混合酸的摩尔比为1.2:1(以混合酸中羧基摩尔量计量),在浓硫酸催化剂(添加量为催化量)存在条件下,在75℃温度下,反应7小时,混合酸的酯化转化率为98%,酯化反应产物先在压力为82kpa,温度为45℃条件下蒸馏回收过量甲醇,甲醇返回酯化反应过程,再在压力为32kpa,温度为60℃蒸馏回收戊酸甲酯,再在压力为12kpa,温度为75℃蒸馏回收环己醇和环己酮混合物,最后在压力为2kpa,温度为95℃蒸馏回收己二酸二甲酯、丁二酸二甲酯和戊二酸二甲酯的混合酯;
34.4)将过氧化氢溶液(浓度为45%)滴加至环己醇与环己酮混合物中在25℃温度下
搅拌反应,析出过氧化环己酮沉淀,直到反应进行到无沉淀析出时,停止滴加过氧化氢溶液,固液分离,得到过氧化环己酮晶体和环己醇,环己醇经过简单精馏得到99%环己醇,将过氧化环己酮晶体置于水中加热到65℃进行水解反应得到环己酮和水混合液,静置分层,收集上层环己酮;环己酮进一步简单精馏得到99%环己酮。
35.5)将混合酯进行减压精馏,塔板数为25,精馏过程为:压力为1.5kpa,釜底温度为125℃,从精馏釜顶部、中部和底部分别收集得到99%丁二酸二甲酯、99%戊二酸二甲酯和99%己二酸二甲酯。
36.实施例2
37.本实施例提供的一种环己烷空气催化氧化生成的醇酮酸复杂氧化产物分离的方法,包括以下步骤:
38.1)环己烷原料加入反应釜内,添加15ppm四苯基卟啉钴和15ppm醋酸钴,在温度为165℃,时间为2.0小时,空气压力为15atm,进行催化氧化反应,得到环己醇、环己酮、戊酸、己二酸、丁二酸和戊二酸及环己烷混合溶液,排出气体成分主要为氮气,经过冷却回收循环使用,环己烷转化率在25%;
39.2)将混合溶液在温度为85℃、压强为0.8atm的条件下进行闪蒸,所得环己烷经过冷却回收返回氧化过程循环使用,剩余即为含环己醇、环己酮和混合酸的混合物;
40.3)混合物与甲醇进行酯化反应,甲醇与混合物中混合酸的摩尔比为1.8:1(以混合酸中羧基摩尔量计量),在浓硫酸催化剂(添加量为催化量)存在条件下,在85℃温度下,反应6.5小时,混合酸的酯化转化率为97%,酯化反应产物先在压力为90kpa,温度为50℃条件下蒸馏回收过量甲醇,甲醇返回酯化反应过程,再在压力为38kpa,温度为65℃蒸馏回收戊酸甲酯,再在压力为18kpa,温度为85℃蒸馏回收环己醇和环己酮混合物,最后在压力为4kpa,温度为110℃蒸馏回收己二酸二甲酯、丁二酸二甲酯和戊二酸二甲酯的混合酯;
41.4)将过氧化氢溶液(工业级)滴加至环己醇与环己酮混合物中在30℃温度下搅拌反应,析出过氧化环己酮沉淀,直到反应进行到无沉淀析出时,停止滴加过氧化氢溶液,固液分离,得到过氧化环己酮晶体和环己醇,环己醇经过简单精馏得到99%环己醇,将过氧化环己酮晶体置于水中加热到75℃进行水解反应得到环己酮和水混合液,静置分层,收集上层环己酮;环己酮进一步简单精馏得到99%环己酮。
42.5)将混合酯进行减压精馏,塔板数为30,精馏过程为:压力为1.5kpa,釜底温度为130℃,从精馏釜顶部、中部和底部分别收集得到99%丁二酸二甲酯、99%戊二酸二甲酯和99%己二酸二甲酯。
43.实施例3
44.本实施例提供的一种环己烷空气催化氧化生成的醇酮酸复杂氧化产物分离的方法,包括以下步骤:
45.1)环己烷原料加入反应釜内,添加40ppm四对氯苯基卟啉锰,在温度为160℃,时间为1.8小时,空气压力为14atm,进行催化氧化反应,得到环己醇、环己酮、戊酸、己二酸、丁二酸和戊二酸及环己烷混合溶液,排出气体成分主要为氮气,经过冷却回收循环使用,环己烷转化率在35%;
46.2)将混合溶液在温度为80℃、压强为0.6atm的条件下进行闪蒸,所得环己烷经过冷却回收返回氧化过程循环使用,剩余即为含环己醇、环己酮和混合酸的混合物;
47.3)混合物与甲醇进行酯化反应,甲醇与混合物中混合酸的摩尔比为2:1(以混合酸中羧基摩尔量计量),在浓硫酸催化剂(添加量为催化量)存在条件下,在80℃温度下,反应6.0小时,混合酸的酯化转化率为96%,酯化反应产物先在压力为90kpa,温度为48℃条件下蒸馏回收过量甲醇,甲醇返回酯化反应过程,再在压力为30kpa,温度为70℃蒸馏回收戊酸甲酯,再在压力为15kpa,温度为82℃蒸馏回收环己醇和环己酮混合物,最后在压力为3.5kpa,温度为105℃蒸馏回收己二酸二甲酯、丁二酸二甲酯和戊二酸二甲酯的混合酯;
48.4)将环己醇和环己酮混合物在钯碳催化剂(催化量)作用下,于205℃及0.05mpa进行催化脱氢得到环己酮产物,环己醇转化率为98%,得到环己酮经过简单蒸馏得到99%环己酮。
49.5)将混合酯进行减压精馏,塔板数为25,精馏过程为:压力为1.8kpa,釜底温度为135℃,从精馏釜顶部、中部和底部分别收集得到99%丁二酸二甲酯、99%戊二酸二甲酯和99%己二酸二甲酯。
50.实施例4
51.本实施例提供的一种环己烷空气催化氧化生成的醇酮酸复杂氧化产物分离的方法,包括以下步骤:
52.1)环己烷原料加入反应釜内,添加20ppm四对氯苯基卟啉锰和20ppm四苯基卟啉铜,在温度为165℃,时间为2小时,空气压力为14atm,进行催化氧化反应,得到环己醇、环己酮、戊酸、己二酸、丁二酸和戊二酸及环己烷混合溶液,排出气体成分主要为氮气,经过冷却回收循环使用,环己烷转化率在40%;
53.2)将混合溶液在温度为80℃、压强为0.8atm的条件下进行闪蒸,所得环己烷经过冷却回收返回氧化过程循环使用,剩余即为含环己醇、环己酮和混合酸的混合物;
54.3)混合物与甲醇进行酯化反应,甲醇与混合物中混合酸的摩尔比为1.8:1(以混合酸中羧基摩尔量计量),在浓硫酸催化剂(添加量为催化量)存在条件下,在80℃温度下,反应7.0小时,混合酸的酯化转化率为98%,酯化反应产物先在压力为80kpa,温度为45℃条件下蒸馏回收过量甲醇,甲醇返回酯化反应过程,再在压力为40kpa,温度为65℃蒸馏回收戊酸甲酯,再在压力为15kpa,温度为80℃蒸馏回收环己醇和环己酮混合物,最后在压力为4kpa,温度为105℃蒸馏回收己二酸二甲酯、丁二酸二甲酯和戊二酸二甲酯的混合酯;
55.4)将环己醇和环己酮混合物在钯碳催化剂(催化量)作用下,于210℃及0.08mpa进行催化脱氢得到环己酮产物,环己醇转化率为99%,得到环己酮经过简单蒸馏得到99%环己酮。
56.5)将混合酯进行减压精馏,塔板数为25,精馏过程为:压力为1.8kpa,釜底温度为135℃,从精馏釜顶部、中部和底部分别收集得到99%丁二酸二甲酯、99%戊二酸二甲酯和99%己二酸二甲酯。
57.实施例5
58.本实施例提供的一种环己烷空气催化氧化生成的醇酮酸复杂氧化产物分离的方法,包括以下步骤:
59.1)环己烷原料加入反应釜内,添加30ppm四苯基卟啉铁,在温度为165℃,时间为2小时,空气压力为15atm,进行催化氧化反应,得到环己醇、环己酮、戊酸、己二酸、丁二酸和戊二酸及环己烷混合溶液,排出气体成分主要为氮气,经过冷却回收循环使用,环己烷转化
率在25%;
60.2)将混合溶液在温度为80℃、压强为0.9atm的条件下进行闪蒸,所得环己烷经过冷却回收返回氧化过程循环使用,剩余即为含环己醇、环己酮和混合酸的混合物;
61.3)混合物与甲醇进行酯化反应,甲醇与混合物中混合酸的摩尔比为1.5:1(以混合酸中羧基摩尔量计量),在浓硫酸催化剂(添加量为催化量)存在条件下,在85℃温度下,反应7.0小时,混合酸的酯化转化率为98%,酯化反应产物先在压力为85kpa,温度为50℃条件下蒸馏回收过量甲醇,甲醇返回酯化反应过程,再在压力为35kpa,温度为65℃蒸馏回收戊酸甲酯,再在压力为15kpa,温度为80℃蒸馏回收环己醇和环己酮混合物,最后在压力为4kpa,温度为105℃蒸馏回收己二酸二甲酯、丁二酸二甲酯和戊二酸二甲酯的混合酯;
62.4)将环己醇和环己酮混合物在四苯基卟啉钴(40ppm)催化下,在空气压力为15atm,温度为155℃条件下,反应80分钟,得到戊酸、己二酸、丁二酸和戊二酸混合酸,环己醇和环己酮转化率为98%,其中己二酸比例为75%,混合酸返回酯化反应过程。
63.5)将混合酯进行减压精馏,塔板数为25,精馏过程为:压力为1.8kpa,釜底温度为135℃,从精馏釜顶部、中部和底部分别收集得到99%丁二酸二甲酯、99%戊二酸二甲酯和99%己二酸二甲酯。
64.实施例6
65.本实施例提供的一种环己烷空气催化氧化生成的醇酮酸复杂氧化产物分离的方法,包括以下步骤:
66.1)环己烷原料加入反应釜内,添加5ppm四苯基卟啉钴和10ppm四苯基卟啉铁μ-二聚体,在温度为165℃,时间为2.5小时,空气压力为15atm,进行催化氧化反应,得到环己醇、环己酮、戊酸、己二酸、丁二酸和戊二酸及环己烷混合溶液,排出气体成分主要为氮气,经过冷却回收循环使用,环己烷转化率在40%;
67.2)将混合溶液在温度为80℃、压强为1atm的条件下进行闪蒸,所得环己烷经过冷却回收返回氧化过程循环使用,剩余即为含环己醇、环己酮和混合酸的混合物;
68.3)混合物与甲醇进行酯化反应,甲醇与混合物中混合酸的摩尔比为1.4:1(以混合酸中羧基摩尔量计量),在浓硫酸催化剂(添加量为催化量)存在条件下,在80℃温度下,反应6.5小时,混合酸的酯化转化率可以达到97%,酯化反应产物先在压力为85kpa,温度为50℃条件下蒸馏回收过量甲醇,甲醇返回酯化反应过程,再在压力为35kpa,温度为65℃蒸馏回收戊酸甲酯,再在压力为15kpa,温度为80℃蒸馏回收环己醇和环己酮混合物,最后在压力为4kpa,温度为105℃蒸馏回收己二酸二甲酯、丁二酸二甲酯和戊二酸二甲酯的混合酯;
69.4)将环己醇和环己酮混合物在10ppm四苯基卟啉钴和20ppm四对氯苯基卟啉钴催化下,在空气压力为18atm,温度为160℃条件下,反应70分钟,得到戊酸、己二酸、丁二酸和戊二酸混合酸,环己醇和环己酮转化率为99%,其中己二酸比例为79%,混合酸返回酯化反应过程。
70.5)将混合酯进行减压精馏,塔板数为25,精馏过程为:压力为1.8kpa,釜底温度为135℃,从精馏釜顶部、中部和底部分别收集得到99%丁二酸二甲酯、99%戊二酸二甲酯和99%己二酸二甲酯。
再多了解一些
本文用于企业家、创业者技术爱好者查询,结果仅供参考。