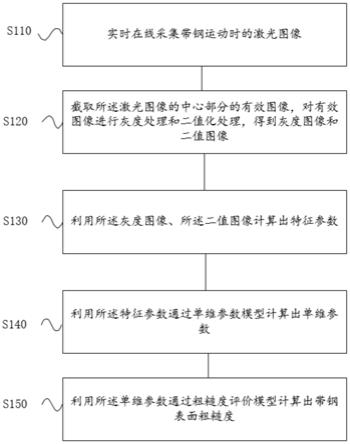
1.本发明涉及带钢表面检测技术领域,特别是指一种带钢表面粗糙度在线检测装置及方法。
背景技术:
2.冷轧钢板在近年来的应用越发广泛,成为制造业中的主要工业原料。需求的不断扩大造成了对其质量与精度的高要求。到目前为止,我国用于制造业中冷轧带钢的表面质量还有待提高,并不能满足实际的要求。高档冷轧产品表面质量缺陷大都是由钢板表面微观形貌引起的,钢板表面质量除了与轧制工艺有关,与轧辊表面微观形貌也有密不可分的关系。在所有表面形貌的表征参数中,粗糙度作为体现冷轧带钢表面质量的重要特性之一,不仅影响到带钢冲压时的变形行为和涂镀后的外观面貌,而且可以改变材料的耐蚀性。
3.目前,对于冷轧生产的带钢表面形貌的检测大都集中于取样后的显微镜检测,传统测量表面粗糙度的方式也都需要离线而且有时间差,并不能实时监测粗糙度异常的带钢,对于现场带钢的实时监测,效率低下,影响冷轧连续作业。
技术实现要素:
4.本发明提供了一种带钢表面粗糙度在线检测装置及方法,现有的带钢检测具有以下问题,检测带钢表面粗糙度为离线检测,有时间差,不能实时监测粗糙度异常的带钢,效率低。
5.为解决上述技术问题,本发明的实施例提供如下方案:
6.本发明实施例提供一种带钢表面粗糙度在线检测方法,所述方法包括:
7.实时在线采集带钢运动时的激光图像;
8.截取所述激光图像的中心部分的有效图像,对有效图像进行灰度处理和二值化处理,得到灰度图像和二值图像;
9.利用所述灰度图像、所述二值图像计算出特征参数;
10.利用所述特征参数通过单维参数模型计算出单维参数;
11.利用所述单维参数通过粗糙度评价模型计算出带钢表面粗糙度。
12.优选地,所述粗糙度评价模型的公式为:
13.sa=f(z)
14.f(z)=17560.77-1222.66z 37.61z
2-0.43z
3-93961.65/z
15.其中,sa为带钢表面粗糙度,单维μm;z为单维参数。
16.优选地,所述特征参数包括灰度图像中的平均亮暗像素之比、空隙率、四阶方差统计量、灰度图像中的平均光强值、纹理特征中的粗糙度、统计量对比度、统计量惯性、逆矩差、二值图像中的亮像素所占比例、灰度图像中的总亮暗像素之比。
17.优选地,对有效图像进行灰度处理和二值化处理包括:
18.截取有效图像并获取每个像素点三原色数值与透明度信息;
19.计算每个像素点的灰度值,将所述有效图像转化为灰度图像;
20.计算所述灰度图像的灰度阈值;
21.利用所述灰度阈值对所述灰度图进行二值化处理,获得所述二值图像。
22.优选地,所述单维参数模型的公式为:
23.z=(0.16x1 0.02x2 0.01x3 20.79x4 1.71x5 0.07x6 999.78x7 0.22x8 0.42x9 0.01x
10
)/100000
24.其中,z为单维参数,x1为灰度图像中的平均亮暗像素之比,x2为空隙率,x3为四阶方差统计量,x4为灰度图像中的平均光强值,x5为纹理特征中的粗糙度,x6为统计量对比度,x7为统计量惯性,x8为二值图像中的亮像素所占比例,x9为灰度图像中的总亮暗像素之比,x
10
为逆矩差。
25.优选地,利用所述灰度图像、所述二值图像计算出特征参数包括:
26.计算所述灰度图像中的平均亮暗像素之比;
27.计算特征参数空隙率;
28.计算高斯-马尔科夫随机场纹理特征中的四阶方差统计量;
29.计算灰度图像中平均光强值;
30.计算tamura纹理特征中的粗糙度;
31.利用灰度共生矩阵法计算统计量对比度;
32.利用灰度梯度共生矩阵法计算统计量惯性以和逆矩差;
33.计算二值图像中亮像素所占比例;
34.计算灰度图像中总亮暗像素之比。
35.优选地,计算所述灰度图像的灰度阈值包括:
36.利用otsu算法获取图像灰度阈值。
37.本发明实施例提供一种带钢表面粗糙度在线检测装置,所述带钢表面粗糙度在线检测装置得以应用在所述的带钢表面粗糙度在线检测方法中;
38.所述检测装置包括支撑及传动辊道,所述支撑及传动辊道带动带钢运动,在所述带钢的上方设置有激光发生器和组合透镜,所述激光发生器发射的激光光束通过所述组合透镜后照射在所述带钢表面,所述激光光束与所述带钢的法线方向呈角度,在所述带钢的法线方向依次设置有远心镜头和高速工业面阵相机,所述高速工业面阵相机实时在线采集带钢运动时的激光图像并传输至服务器。
39.优选地,所述激光光束与所述带钢的法线方向之间的角度范围为30
°
~60
°
。
40.本发明的上述方案至少包括以下有益效果:
41.上述方案中,带钢表面粗糙度在线检测方法将计算激光图像中的特征参数作为输入量,通过单维参数模型计算出单维参数,再将单维参数作为输入量过建立粗糙度评价模型计算出带钢表面粗糙度,实现带钢表面粗糙度实时在线检测,没有时间差,可以实时监测粗糙度异常的带钢,效率高,为带钢产品表面质量的提升奠定了基础;
42.带钢表面粗糙度在线检测装置可以实现带钢表面粗糙度实时在线检测,没有时间差,可以实时监测粗糙度异常的带钢,效率高,为带钢产品表面质量的提升奠定了基础。
附图说明
43.图1为本发明的带钢表面粗糙度在线检测方法的流程图一;
44.图2为本发明的带钢表面粗糙度在线检测方法的流程图二;
45.图3为本发明的带钢表面粗糙度在线检测方法的流程图三;
46.图4为利用本发明的带钢表面粗糙度在线检测方法的处理一张激光图像的灰度图和二值图;
47.图5为利用本发明的带钢表面粗糙度在线检测方法的处理另一张激光图像的灰度图和二值图;
48.图6为本发明的带钢表面粗糙度在线检测装置的示意图。
49.附图标记:
50.1、支撑及传动辊道;2、带钢;3、激光发生器;4、组合透镜;5、远心镜头;6、高速工业面阵相机;7、服务器。
具体实施方式
51.下面将参照附图更详细地描述本公开的示例性实施例。虽然附图中显示了本公开的示例性实施例,然而应当理解,可以以各种形式实现本公开而不应被这里阐述的实施例所限制。相反,提供这些实施例是为了能够更透彻地理解本公开,并且能够将本公开的范围完整的传达给本领域的技术人员。
52.实施例一
53.如图1所示的,本实施例一种带钢表面粗糙度在线检测方法,方法包括:
54.s110、实时在线采集带钢运动时的激光图像;
55.s120、截取激光图像的中心部分的有效图像,对有效图像进行灰度处理和二值化处理,得到灰度图像和二值图像;
56.s130、利用灰度图像、二值图像计算出特征参数;
57.s140、利用特征参数通过单维参数模型计算出单维参数;
58.s150、利用单维参数通过粗糙度评价模型计算出带钢表面粗糙度。
59.本实施例的带钢表面粗糙度在线检测方法将计算激光图像中的特征参数作为输入量,通过单维参数模型计算出单维参数,再将单维参数作为输入量过建立粗糙度评价模型计算出带钢表面粗糙度,实现带钢表面粗糙度实时在线检测,没有时间差,可以实时监测粗糙度异常的带钢,效率高,为带钢产品表面质量的提升奠定了基础。
60.具体地,如图2所示的,在步骤s120,对有效图像进行灰度处理和二值化处理包括:
61.s121、截取有效图像并获取每个像素点三原色数值与透明度信息;
62.s122、计算每个像素点的灰度值,将有效图像转化为灰度图像;
63.s123、计算灰度图像的灰度阈值;
64.s124、利用灰度阈值对灰度图进行二值化处理,获得二值图像。
65.具体地,在步骤s123中,计算灰度图像的灰度阈值包括:利用otsu算法获取图像灰度阈值。
66.具体地,在步骤s130中,特征参数包括灰度图像中的平均亮暗像素之比、空隙率、四阶方差统计量、灰度图像中的平均光强值、纹理特征中的粗糙度、统计量对比度、统计量
惯性、逆矩差、二值图像中的亮像素所占比例、灰度图像中的总亮暗像素之比。
67.具体地,如图3所示的,在步骤s130中,利用灰度图像、二值图像计算出特征参数包括:
68.s131、计算灰度图像中的平均亮暗像素之比;
69.s132、计算特征参数空隙率;
70.s133、计算高斯-马尔科夫随机场纹理特征中的四阶方差统计量;
71.s134、计算灰度图像中平均光强值;
72.s135、计算tamura纹理特征中的粗糙度;
73.s136、利用灰度共生矩阵法计算统计量对比度;
74.s137、利用灰度梯度共生矩阵法计算统计量惯性以和逆矩差;
75.s138、计算二值图像中亮像素所占比例;
76.s139、计算灰度图像中总亮暗像素之比。
77.具体地,在步骤s140中,单维参数模型的公式为:
78.z=(0.16x1 0.02x2 0.01x3 20.79x4 1.71x5 0.07x6 999.78x7 0.22x8 0.42x9 0.01x
10
)/100000
79.其中,z为单维参数,x1为灰度图像中的平均亮暗像素之比,x2为空隙率,x3为四阶方差统计量,x4为灰度图像中的平均光强值,x5为纹理特征中的粗糙度,x6为统计量对比度,x7为统计量惯性,x8为二值图像中的亮像素所占比例,x9为灰度图像中的总亮暗像素之比,x
10
为逆矩差。
80.具体地,在步骤s150中,粗糙度评价模型的公式为;
81.优选地,粗糙度评价模型的公式为:
82.sa=f(z)
83.f(z)=17560.77-1222.66z 37.61z
2-0.43z
3-93961.65/z
84.其中,sa为带钢表面粗糙度,单维μm;z为单维参数。
85.实施例二
86.如图1~图3所示的,本实施例一种带钢表面粗糙度在线检测方法,方法包括:
87.s110:实时在线采集带钢运动时的激光图像;
88.s120:截取中心部分有效图像并对图像进行平均值法灰度处理以及二值化处理;包括:
89.s121、截取有效图像并获取每个像素点三原色数值与透明度信息,截取后图像大小为1024*1024;
90.s122、获取每个像素点的灰度值:将每个像素点三原色的色值取平均值即为该像素点的灰度值,将彩色图像转换为灰度图像,计算公式如下:
91.gray(i,j)=(r(i,j) g(i,j) b(i,j))/3
92.其中,gray(i,j)是用平均法求得的灰度值,r(i,j)表示图像中红色分量亮度,g(i,j)表示图像中绿色分量亮度,b(i,j)表示图像中蓝色分量亮度;
93.s123、otsu算法获取灰度阈值:选定某一灰度值为界将整个图像分为两部分,分别计算总灰度均值与各部分的灰度均值以及各部分像素数占总像素的比例,则使得类间方差达到最大值的灰度值就是otsu算法自动获取的灰度阈值,计算公式如下:
94.g=ω0ω1(μ
0-μ)295.其中,g表示类间方差;
[0096][0097][0098]
n0 n1=1024*1024
[0099]
μ=ω0*μ0 ω1*μ1[0100]
g=ω0(μ
0-μ)2 ω1(μ
1-μ)2[0101]
其中,假设初始阈值为t,图像中像素的灰度值小于阈值t的像素个数记作n0,像素灰度大于阈值t的像素个数记作n1,ω0:背景像素点占整幅图像的比例,μ0:背景像素点的平均灰度,ω1:前景像素点占整幅图像的比例,μ1:前景像素点的平均灰度,μ:整幅图像的平均灰度;
[0102]
s124、灰度图二值化处理:将每个点的像素值与计算得到的灰度阈值t进行较:当像素值小于阈值时,将该像素点的三原色值均设为0;当像素值大于等于阈值时,将该像素点的三原色值均设为255,计算公式如下:
[0103][0104]
其中,t为大津算法得出的阈值,f(x)为图像上像素点的灰度值;
[0105]
在本实施例中,经上述处理后的2幅激光图像如图4图5所示;
[0106]
s130、计算处理后图像中的特征参数;具体步骤为:
[0107]
s131、计算灰度图像中平均亮暗像素之比bdaverage,计算公式如下:
[0108][0109]
其中,baverage(单位为pixel)和daverage(单位为pixel)分别为二值化处理后图像亮像素和暗像素连通区域的平均面积,通过亮像素数和暗像素数分别除以相应的连通区域的个数进行计算;
[0110]
s132、计算特征参数空隙率λ,计算公式如下:
[0111][0112]
其中,n(m,r)定义为大小为r,质量为m的盒子数量,q(m,r)为概率密度函数,通过将n(m,r)除以盒子总数得到;
[0113]
s233、计算高斯-马尔科夫随机场纹理特征中的四阶方差统计量v,计算公式如下:
[0114][0115]
其中,θi是高斯-马尔科夫随机线性模型中特征向量参数,共有十个分量,m是各分
量的平均值;
[0116]
s134、计算灰度图像中平均光强值intensity,计算过程如下:计算激光图像中像素的平均灰度值即为平均光强值intensity;
[0117]
s135、计算tamura纹理特征中的粗糙度f
cn
,计算如下:
[0118]
计算图像中大小为4*4个像素点的活动窗口中像素的平均强度值a(x,y);
[0119][0120]
其中,g(i,j)是位于(i,j)处的像素的灰度值,对于每一个像素点分别计算水平和垂直方向上互不重叠的窗口之间的平均强度差eh(x,y)和ev(x,y);
[0121]eh
(x,y)=|a(x 2,y)-a(x-2,y)|
[0122]ev
(x,y)=|a(x,y 2)-a(x,y-2)|
[0123]
式中,eh(x,y)代表该像素点水平方向的差值,ev(x,y)代表该像素点垂直方向差值。根据每个像素点,找到能使eh(x,y)或ev(x,y)达到最大的最佳尺寸s
best
,通过计算整幅图像中s
best
的平均值得到特征参数粗糙度f
cn
[0124][0125]
s136、利用灰度共生矩阵法计算统计量对比度con,计算过程如下:
[0126]
灰度共生矩阵的一个元素代表了一种灰度组合沿竖直方向出现的次数,用p(a,b)(a,b=0,1,2...,l-1)表示,其中l表示图像的灰度级,a,b分别表示像素的灰度。如元素p(1,0)代表了图像上位置关系为竖直方向的两个像素灰度分别为1和0的情况出现的次数。其中l表示图像的灰度级,a,b分别表示像素的灰度。
[0127][0128]
统计量对比度的计算公式如下:其中,是将各个元素p(a,b)除以各元素之和得到的;
[0129]
s137、:利用灰度梯度共生矩阵法计算统计量惯性t1以及逆矩差t2,计算如下:
[0130]
设定一幅图像为f(x,y),定义归一化的灰度图像为:
[0131][0132]
式中:f(x,y)为原图像在(x,y)处的灰度值;f(x,y)为变换后的图像在(x,y)处的
变化值;int为取整变换,nf为变换后最大灰度值;f
max
为变换前的f(x,y)的最大灰度值;
[0133]
归一化的梯度图像为:
[0134]
式中:g(x,y)为原图像在(x,y)处的灰度值;g(x,y)为变换后的图像在(x,y)处的梯度值;ng为变换后最大灰度值;g
max
为变换前的g(x,y)的最大灰度值;g(x,y)=j,f(x,y)=i,i=1,2...,nf,j=1,2...,ng,满足上式的像素点对数,该个数为共生矩阵h(i,j)的值;p(i,j)为灰度值为i,梯度值为j的共生矩阵的h(i,j)概率,统计量惯性的计算公式如下:
[0135][0136]
统计量逆矩差的计算公式如下:
[0137][0138]
s138、计算二值图像中亮像素所占比例as,计算公式如下:
[0139][0140]
其中,at(单位为个)是二值图像中像素点显示为1的个数;
[0141]
s139、:计算灰度图像中总亮暗像素之比bd,计算公式如下:
[0142]
bd=bar/dar
[0143]
其中,bar(单位为pixel)是亮相素数除以总面积,总面积定义为二值图像的像素数之和,dar(单位为pixel)是暗相素数除以总面积,总面积定义为二值图像的像素数之和。
[0144]
在本实施例中,在步骤s130中,对应图像的计算结果如表1所示:
[0145]
表1特征参数计算结果
[0146][0147]
s140、根据图像特征参数,计算单维参数z的方法如下:
[0148]
z=(0.16x1 0.02x2 0.01x3 20.79x4 1.71x5 0.07x6 999.78x7 0.22x8 0.42x9 0.01x
10
)/100000
[0149]
其中,z是单维参数,x1到x
10
是步骤3中计算出的特征参数的值,x1是bdaverage,x2是lac,x3是v,x4是intensity,x5是f
cn
,x6是con,x7是t1,x8是as,x9是bd,x
10
是t2。
[0150]
在步骤s140中,对应图像的计算结果如表2所示:
[0151]
表2单维参数z计算结果
[0152]
图4图5z22.7025.56
[0153]
s150、根据特征参数z,通过粗糙度评价模型f(z)计算带钢表面粗糙度的方法如下:
[0154]
sa=f(z)=17560.77-1222.66z 37.612
2-0.43z
3-93961.65/z
[0155]
其中,sa是带钢表面粗糙度,单位是μm,z是根据激光图像特征参数计算出的单维参数。
[0156]
在本实施案例中,对应图像计算结果如下:图4中z=22.70,对应的sa=6.13μm;图5中z=25.56,对应的sa=8.04μm,实施例中的带钢表面经过激光共聚焦离线检测其表面粗糙度为sa=6.30μm和sa=7.80μm,本发明提出的检测方法误差分别为2.77%和3.08%,检测精度高,效率高。
[0157]
实施例三
[0158]
如图4所示的,本实施例提供了一种带钢表面粗糙度在线检测装置,带钢表面粗糙
度在线检测装置得以应用带钢表面粗糙度在线检测方法中;
[0159]
检测装置包括支撑及传动辊道1,支撑及传动辊道1带动带钢2运动,在带钢2的上方设置有激光发生器3和组合透镜4,激光发生器3发射的激光光束通过组合透镜4后照射在带钢2表面,激光光束与带钢2的法线方向呈角度,在带钢2的法线方向依次设置有远心镜头5和高速工业面阵相机6,高速工业面阵相机6实时在线采集带钢2运动时的激光图像并传输至服务器7。
[0160]
具体地,激光光束与带钢2的法线方向之间的角度范围为30
°
~60
°
。组合透镜4调整激光光束的直径与强度。激光图像经千兆网线传输至服务器7。
[0161]
本实施例的带钢表面粗糙度在线检测装置可以实现带钢2表面粗糙度实时在线检测,没有时间差,可以实时监测粗糙度异常的带钢2,效率高,为带钢2产品表面质量的提升奠定了基础。
[0162]
以上所述是本发明的优选实施方式,应当指出,对于本技术领域的普通技术人员来说,在不脱离本发明所述原理的前提下,还可以作出若干改进和润饰,这些改进和润饰也应视为本发明的保护范围。
再多了解一些
本文用于企业家、创业者技术爱好者查询,结果仅供参考。