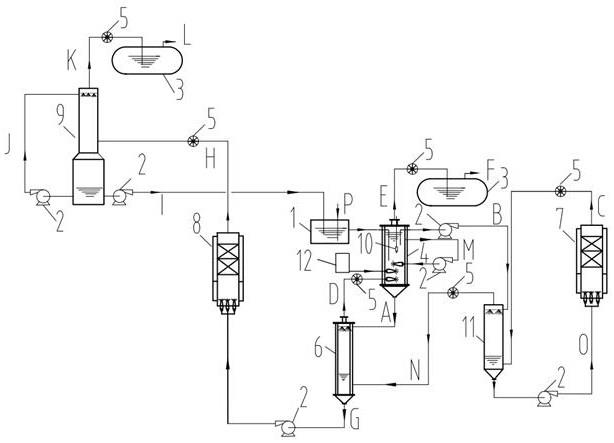
1.本发明涉及碘循环制氢技术,属于热化学循环制备氢气相关技术领域,具体涉及一种热化学硫碘循环制氢全流程方法和装置。
背景技术:
2.氢能是最清洁的能源之一,不仅氢本身无毒无害,而且在利用过程中的产物只有水,没有二氧化碳等污染物的排放。氢能的能量密度大,转化效率高。除了作为能源使用外,氢气还是重要的化工原料。每年全球有一半以上的氢气用于合成氨、石油裂化等重要化工过程。氢是二次能源,需要通过一次能源制备。水通过热解离可以制氢,但是反应需要4000℃以上的高温,硫碘循环制氢法是将水的分解反应分成几步,这样既可以降低反应温度,又可以避免氢-氧分离问题,并且循环中所用的二氧化硫和碘都可以循环使用。硫碘(si)循环是由美国原子能(general atomics)公司在1970年代首先提出的。由于具有非常多的优点,包括全流相过程易于连续运行、较高的能量利用效率、完全闭式循环、可与核能或者太阳能匹配等。硫碘循环具备大规模、低成本制氢的潜力,被提出作为未来氢能经济的一种主要的供氢方式,始终是制氢领域的研究热点。热化学硫碘循环(si 循环)主要由三步反应组成 :so
2 2h2o i
2 = h2so
4 2hi (333-393k);2h2so
4 = 2so
2 2h2o o
2 (1123k);2hi = h
2 i
2 (773k)。
3.硫碘循环系统包含三个子系统,bunsen反应子系统,h2so4分解子系统,hi分解子系统。首先,二氧化硫和碘与过量的水发生bunsen反应生成硫酸和氢碘酸的混合溶液。在碘过量的条件下,溶液能够自发地出现液液分层现象。上层轻相溶液为硫酸相,主要是硫酸溶液,由于液液分层的局限性,不可避免地会包含有hi和碘杂质。下层重相为氢碘酸相(hix),主要是hi-i
2-h2o三元混合溶液,也会包含少量的硫酸杂质。鉴于分离后的hix溶液和h2so4溶液都含有杂质,并且所含的杂质均会对后续流程产生较大的影响,所以需要对两种酸溶液进行纯化处理,即利用bunsen反应的逆反应将少量的hi和h2so4重新转化为i2、so2以及h2o。杂质的存在在一定条件下可以引发下列副反应:副产物s生成:h2so4 6hi=s 3i2 4h2o;副产物h2s生成:h2so4 8hi=h2s 4i2 4h2o。
[0004] hix相溶液经过纯化后,需要进行浓缩,以提高其中hi的浓度至超恒沸状态。然后通过常规精馏塔进行精馏分离,塔底釜液为含i2浓度较高的hix溶液,而塔顶精馏物为高浓度的hi,接着进入hi分解反应器在450℃左右分解成氢气和碘单质。h2so4相与hix相操作相似,需要多级闪蒸以提高h2so4的浓度,然后进入h2so4反应器分解成so2、o2和h2o,由此构成一个完整的闭合回路。整个系统只需不断补充水和热量,其他物质循环使用,就可得到高纯度的氢气和氧气。
[0005] 为保证后续氢碘酸相(hix)和硫酸相的分离,bunsen反应罐中加入了过量的i2。固体碘为紫黑色有光泽的片状晶体,易升华,易凝华。为防止碘的析出,ga公司建议提供120
℃, 4.3bar的环境。但是在实际操作中,由于hi 和h2so4为强腐蚀性物质,高压条件下有极大的安全风险。同时,hi水溶液的沸点为127℃,在120℃条件下,大量hi会以气体状态存在,极大增加了后续氢碘酸相(hix)和硫酸相的分离难度。因此,在实际操作中,bunsen反应罐的温度设定为85℃,压力为常压。低温常压的环境中,i2极易附着在搅拌釜的叶片上,导致各反应物之间的混合不够充分。同时,随着i2附着量的增加,最终将会导致搅拌釜停止工作,后期需要投入大量时间和人力进行设备的检修和清理。在利用bunsen逆反应进行hix相的纯化中,实验室通常采用氮气作吹扫气,但是其后续还需增加与氢气的分离工作,不适合大规模工业化应用。850℃下,h2so4分解产生高温o2、so2和h2o混合气,需要先冷凝降温以后再返回至bunsen反应罐中,此过程造成大量的能量浪费。
[0006]
目前公开的技术和文献资料中对于硫碘循环中碘化氢制氢的工艺的研究,其中专利cn103213945b发明了一种促进热化学硫碘循环制氢中bunsen反应的方法,使原来的气液固三相反应转变为气液反应,但是并未解决bunsen罐中i2的低温析出附着问题。专利cn107904617b公开了一种在硫碘循环制氢中以电化学分解hi制氢的方法及装置,但是电化学方法消耗电能,与热化学的初衷背道而驰;同时对电极材料的耐腐蚀性要求极高,造价昂贵;电解池受体积限制,很难实现大规模的工业应用。专利cn107944217a提供了一种碘硫循环制氢中hi浓缩精馏塔的建模方法,解决了碘硫循环制氢中hi浓缩分离的精馏问题,并未提到实际的工艺设备,并且对物料做了简化处理,忽略了hix气相中的少量的so2夹带。专利cn112142001a发明公开了一种基于高效光能利用的碘硫循环制氢方法及系统,采用太阳光照对hi溶液进行光催化分解获得氢气,该过程集成了太阳能和光催化,将其应用于碘硫循环hi分解过程,只停留在试验阶段,无法大规模工业化应用。专利cn113233415a,发明了一种热集成复合塔的新型管壳式结构,强化了传质和传热过程,虽然将整个工艺的hix汽提段、hix反应精馏段、hix水洗段耦合在一起,但是只关注了hi系统,没有对整个硫碘制氢系统进行研究和优化。
[0007]
碘硫循环制氢工艺产氢效率高、无co2排放,有利于碳中和,因此碘硫循环有望成为清洁、经济、可持续的大规模制氢方法。但是,传统碘硫循环的设备体系非常复杂庞大,包含了bunsen反应塔、液液分离塔、hi和h2so4纯化塔、冷凝塔、数个hi和h2so4精馏塔、hi和h2so4分解塔以及缓冲罐、多个加热器等。并且,hix相纯化过程中生成的s不仅会堵塞管道而且可能造成后续hi分解塔中催化剂中毒,严重影响催化剂的使用寿命。同时系统中过量水的存在需要蒸馏进行hi溶液和h2so4溶液的浓缩,消耗了大量能量。而从h2so4分解塔中产生的高温so2,o2混合气必须先经过冷却才能进入bunsen反应塔中,此过程造成了能量的浪费。
技术实现要素:
[0008]
本发明的目的是提供一种热化学硫碘循环制氢全流程方法和装置,用以解决i2析出,在同一个反应塔内实现bunsen反应发生以及hix相和h2so4相分离,避免hix相纯化生成s,减少hi和h2so4精馏塔数量,简化整个循环系统,同时利用自身产生的高温气体作为加热热源,提高系统的热效率。
[0009]
本发明的技术方案如下:本发明一方面提供了一种热化学硫碘循环制氢全流程方法,其包括如下步骤:含碘液体与补充水从bunsen预混罐送入bunsen反应分离塔内使塔内具有液位,反
应进料混合气从塔底部气相入口中被喷入塔内与含碘液体进行反应,反应后待hix相与h2so4相分离,分离后的hix相送至hix纯化浓缩塔,h2so4相送至h2so4浓缩塔;h2so4相液体从h2so4浓缩塔顶部喷淋,来自h2so4分解塔中的so2和o2高温混合气从h2so4浓缩塔底部喷入,h2so4相液体下降过程中与高温混合气体相遇,水被高温混合气体迅速汽化带走并进入hix纯化浓缩塔;hix相液体从hix纯化浓缩塔顶部喷淋,来自h2so4浓缩塔中的so2、o2和h2o高温混合气从hix纯化浓缩塔底部喷入;使下降的hix相中的水迅速汽化,实现hi溶液浓缩;hix相中的h2so4杂质在富氧环境中转为so2带离,实现hi溶液纯化;hix纯化浓缩塔顶出气作为反应进料混合气进入bunsen反应分离塔进入下一个循环;hix纯化浓缩塔底部的hi浓缩溶液进入hi分解塔中进行分解;来自hi分解塔的气体从底部进入冷凝塔,在上升过程中与下降的含碘液体相遇,气体中混有的h2o、hi以及i2被洗涤除去,制得氢气;冷凝塔底部的含碘液体一部分重新被加压输送到冷凝塔顶进行喷淋,一部分离开冷凝塔进入bunsen预混罐。
[0010]
作为本发明的优选方案,hix纯化浓缩塔利用高温下so
2 和o2的混合气,除去了hix相中的杂质h2so4。发生bunsen逆反应:h2so
4 8hi = h2s 4i
2 4h2o;h2so
4 6hi = s 3i
2 4h2o。
[0011]
副产物h2s和s在富氧环境下发生反应:s o2=so2;2h2s 3o
2 = 2so
2 2h2o。
[0012]
混合气与hix相夹杂的s、h2s发生反应,达到纯化hix的目的。进入hix纯化浓缩塔内的混合气中,o2和so2的摩尔流量之比为1:2,离开hix纯化浓缩塔后混合气中,o2和so2的摩尔流量小于1:2。
[0013]
作为本发明的优选方案,所述bunsen反应分离塔、hix纯化浓缩塔、h2so4浓缩塔、冷凝塔、hi分解塔、h2so4分解塔的塔压控制在1bar,bunsen反应分离塔温度85℃;hix纯化浓缩塔气相进口温度为450-500℃,气相出口温度150-200℃,液相出口温度为85-90℃;h2so4浓缩塔气相进口温度为800-850℃,气相出口温度450-500℃,液相出口温度为85-90℃;hi分解塔温度为450℃;h2so4分解塔温度为850-900℃。
[0014]
本发明另一方面提供了一种实施上述方法的热化学硫碘循环制氢全流程装置,其包括:bunsen预混罐、so2储罐、bunsen反应分离塔、hix纯化浓缩塔、h2so4浓缩塔、冷凝塔、hi分解塔、h2so4分解塔、naoh洗涤罐;所述bunsen反应分离塔至少具有三个液相出口、两个液相进口,一个气相出口和两个气相进口,且bunsen反应分离塔配置有自循环管路,自循环管路上设置有加压泵;三个液相出口分别连接hix纯化浓缩塔的顶部喷淋入口、h2so4浓缩塔的顶部喷淋入口和加压泵入口,一个液相进口连接bunsen预混罐获取冷凝塔输出的含碘液体,一个液相进口连接加压泵出口输入循环的反应混合物;气相出口与naoh洗涤罐相连接输出产品氧气;一个气相进口与hix纯化浓缩塔的顶部气体出口相连,一个气相进口与so2储罐相连补充so2;bunsen反应分离塔内设置有密度计;hix纯化浓缩塔的底部出口连接hi分解塔,底部气体进口连接h2so4浓缩塔的顶部气体出口。hi分解塔的顶部气体出口与冷凝塔的底部气体入口连接。冷
凝塔的底部液体出口与bunsen预混罐相连。h2so4浓缩塔的底部液体出口连接h2so4分解塔的入口。h2so4分解塔的顶部气体出口与h2so4浓缩塔的底部气体入口相连。所述bunsen反应分离塔和冷凝塔均设置有顶部气体出口,所述顶部气体出口连接naoh洗涤罐输出产品氧气与氢气。
[0015]
与现有技术相比,本发明的有益效果包括:与传统的碘化氢制备氢气工艺与装置相比,本发明通过将混合气体反应物喷入bunsen反应分离塔,并不断进行循环的方式使气液充分混合,提高了转化率,预防了i2析出。bunsen反应段与hix和h2so4两相分离段耦合在一起,将hix纯化段和浓缩段耦合在一起,大大简化了整个系统。将h2so4分解产生的高温气体的热量集成到hix纯化段、浓缩段以及h2so4浓缩段,实现了工艺和系统的能量梯级利用。本发明将硫酸分解单元的高温混合气直接先通入到h2so4浓缩塔中,在没有外界热源的条件下,h2so4溶液中大量的水迅速汽化,达到浓缩h2so4溶液的目的。随后,高温混合气继续进入下游hix纯化浓缩塔中,hix物系中大量的水被汽化带离,达到浓缩hi溶液的目的。hix物系中夹杂的h2so4在富氧环境中转化为so2被带离,部分单质碘以碘蒸气方式被带离,达到纯化hi溶液的目的,被带离的混合气体重新返回bunsen反应分离塔进入下一个循环。冷凝塔中氢气被分离后剩余的含碘液体重新返回bunsen预混罐中被重复利用,相对于传统碘化氢制备氢气投资和能耗均可降低40%以上。
附图说明
[0016]
图1是本发明硫碘循环制氢的工艺流程示意图;其中:1-bunsen预混罐,2-加压泵,3-naoh洗涤罐,4-bunsen反应分离塔,5-风机,6-hix纯化浓缩塔,7-h2so4分解塔,8-hi分解塔,9-冷凝塔,10-密度计,11-h2so4浓缩塔,12-so2储罐。a-hix相液体,b-h2so4相液体,c-so2、o2、h2o高温混合气,d
‑ꢀ
so2、o2、h2o和i2混合气,e-氧气,f-除酸后氧气,g-hi浓缩溶液,h-h2、hi、h2o和i2混合气,i-含碘液体,j-含碘液体,k-氢气,l-除酸后氢气,m-bunsen反应混合物,n-so2、o2和h2o高温混合气,o-h2so4浓缩溶液,p-补充水。
具体实施方式
[0017]
下面结合附图和具体实施例对本发明技术方案进行详细说明,此处所描述的具体实施例仅用以解释本发明,但是本发明的保护范围不局限于所述实施例。
[0018]
如图1所示,本实施例提供的热化学硫碘循环制氢全流装置主要包括bunsen预混罐、so2储罐、加压泵、naoh洗涤罐、bunsen反应分离塔、风机、hix纯化浓缩塔、h2so4浓缩塔、h2so4分解塔、hi分解塔、冷凝塔。
[0019]
bunsen反应分离塔4中的液相混合物来自于bunsen预混罐1,气相混合物来自于hix纯化浓缩塔6和so2储罐12。bunsen反应分离塔内未反应完全的混合物在塔侧面经加压泵2抽出后又重新喷入塔中,加快反应进程。两相分离后的h2so4相经塔侧面出料口进入h2so4浓缩塔11中,hix相从塔底部流入hix纯化浓缩塔6。氧气经塔顶部进入naoh洗涤罐。bunsen反应分离塔4运行环境为常压85℃,反应为自发进行的放热反应。
[0020]
h2so4浓缩塔11中的h2so4相混合物来自bunsen反应分离塔4,从塔顶部喷淋,与来自h2so4分解塔7的高温混合气相遇后从塔底部离开进入h2so4分解塔7。高温混合气从塔顶
部离开进入hi纯化浓缩塔6。h2so4浓缩塔11的液相温度为85-90℃,气相进口温度为800-850℃,气相出口温度为450-500℃。
[0021]
h2so4分解塔7中的h2so4溶液来自h2so4浓缩塔11,从塔底部进入喷淋发生分解反应,运行环境为常压850-900℃。产生的高温混合气体从塔顶部离开进入h2so4浓缩塔11中。
[0022]
hix纯化浓缩塔6中的hix相混合物来自bunsen反应分离塔4,从塔顶部喷淋,下降过程中与来自h2so4浓缩塔11的高温气体相遇,经浓缩后从塔底部离开进入hi分解塔8中。h2so4浓缩塔11中的高温气体从侧面进入hix纯化浓缩塔6后,从顶部离开返回bunsen反应分离塔4。hix纯化浓缩塔6液相温度为85-90℃,气相进口温度为450-500℃,气相出口温度为150-200℃。hix纯化浓缩塔6内发生bunsen副反应,此反应为吸热反应。
[0023]
hi分解塔8中的hi溶液来自hix纯化浓缩塔6,从塔底部喷淋进入。塔内运行环境为常压450℃,在催化剂的作用下发生hi分解反应。分解后的高温气体混合物从塔顶部离开进入冷凝塔9中。
[0024]
冷凝塔9中含碘液体从顶部喷淋,与来自hi分解塔8中的高温气体相遇,在塔底一部分重新循环到塔顶部喷淋,其余部分进入bunsen反应预混罐1中。氢气从塔顶部离开进入naoh洗涤罐3中。
[0025]
整套装置中,bunsen预混罐1暂存返回的含碘液体以及定时补充的水。
[0026]
在需要提供输送动力的气体管路上设置风机5,在需要提供输送动力的液体管路上设置加压泵2。风机5为气体输送提供动力。加压泵2为液体输送提供动力。
[0027]
naoh洗涤罐用于去除产品气体中的酸性杂质和水。
[0028]
采用上述装置在碘硫循环中制氢气的工艺步骤如下:bunsen预混罐1和bunsen反应分离塔4构成bunsen反应以及液液两相分离工艺段,反应物进入bunsen反应分离塔4在85℃下发生自发反应产生hi和h2so4。反应结束静置后,上层h2so4相液体通过泵送入h2so4浓缩塔11中,下层hix相液体送入到hix纯化浓缩塔6中。
[0029]
出bunsen塔的h2so4相液体在h2so4浓缩塔11里从顶部喷淋,下降过程中与来自h2so4分解塔7中的高温气体混合物(so2、o2、h2o)相遇,水被迅速汽化从塔顶部离开进入到hix纯化浓缩塔6中。浓缩后的h2so4溶液聚集到塔底部后,经泵喷淋进入到h2so4分解塔7在850-900℃催化剂的作用下发生分解反应,生成so2、o2和h2o,从塔顶部离开后经风机作用,进入到h2so4浓缩塔11中。
[0030]
富含so2和o2的混合高温气体从hix纯化浓缩塔6底部喷入,在上升过程中与下降的hix相液体相遇,其中的水被迅速汽化带离,杂质h2so4发生反应最终以so2的方式带离。
[0031]
so2、o2和h2o的混合气体从hix纯化浓缩塔6顶部离开重新返回bunsen系统中,最后在风机5的作用下,氧气经naoh洗涤罐3作为商品气输出。塔底部被浓缩后的hi溶液经泵从hi分解塔8底部喷入,在450℃,催化剂的作用下发生hi分解反应制取氢气。
[0032]
氢气、i2和未分解的hi气体以及水蒸气进入冷凝塔9,在上升过程中与喷淋的含碘液体相遇,水汽冷凝析出,i2和hi溶解于水中。最后在风机的作用下,分离出的h2从塔顶部离开经naoh洗涤以后作为商品气输出。吸收hi气体的含碘液体一部分被重新送入塔顶喷淋,剩余部分返回bunsen预混罐1中。
[0033]
本发明通过将混合气体喷入bunsen反应分离塔,并不断进行循环的方式使气液固充分混合,提高了转化率,预防了i2析出。bunsen反应段与hix和h2so4两相分离段耦合在一
起,将hix纯化段和浓缩段耦合在一起,大大简化了整个系统。将h2so4分解产生的高温气体的热量集成到hix纯化浓缩段以及h2so4浓缩段,实现了工艺和系统的能量梯级利用。
[0034]
实施例1bunsen反应分离塔内初始温度85℃常压,塔内投料为10 mol h2so4,20 mol hi,10mol so2,20mol i2,120mol水。反应1.5h后so2转化率达95%。两相静置20min分离,分别进入h2so4系统和hix系统。h2so4相和hix相出口温度为85℃。
[0035]
h2so4相组成为h2so
4 4.7 mol/kg,hi 0.34 mol/kg,i
2 0.115 mol/kg,h2o 25.9 mol/kg。液相混合物从h2so4浓缩塔顶部喷淋,下降过程中与来自h2so4分解塔的so2和o2的高温蒸汽相遇,液体水被迅速汽化带离。高温混合气体(450-500℃)从h2so4浓缩塔塔顶经风机作用进入hix纯化浓缩塔。h2so4浓缩塔底部h2so4浓度达到9.6 mol/kg,塔底部出口温度85-90℃。浓硫酸进入h2so4分解塔,在850-900℃催化剂的作用下发生分解反应,分解率达96%以上。分解产生的so2、o2和h2o的摩尔比约为2:2:1,混合气体从塔顶部离开,出口温度为800-850℃。高温混合气体返回至h2so4浓缩塔中循环。
[0036]
hix相组成为h2so
4 0.14 mol/kg,hi 1.34 mol/kg,i
2 2.7 mol/kg,h2o 2.6 mol/kg。液相混合物从hix纯化浓缩塔顶部喷淋,下降过程中与来自h2so4浓缩塔的so2和o2的高温蒸汽(450-500℃)相遇,液体水被迅速汽化带离。杂质h2so4与hi在富氧条件下发生反应转化为so2被带离。发生反应如下:副产物s生成:h2so
4 6hi = s 3i
2 4h2o;副产物h2s生成:h2so
4 8hi = h2s 4i
2 4h2o;副产物与混合气发生反应:s o
2 = so2,2h2s 3o
2 = 2so
2 2h2o,s和h2s在富氧环境中转化率为100%,有效的达到纯化hix的目的。
[0037]
hix纯化浓缩塔顶出口温度为150-200℃,富氧混合气体从塔顶重新返回bunsen反应分离塔。氧气从bunsen反应分离塔顶部离开,经naoh溶液去酸洗涤作为纯度100%商品气输出。hix纯化浓缩塔底部hi浓度达到1.9 mol/kg,塔底部出口温度85-90℃。浓hi溶液进入hi分解塔,在450℃催化剂的作用下发生分解反应,分解率为22%。分解产生的h2、i2未反应的hi气体以及水蒸气从塔顶部离开,出口温度为450℃。高温混合气体经风机作用送入冷凝塔中,上升过程中与塔顶喷淋的含碘液体相遇,水蒸气冷凝析出,hi、i2气体溶解于水中,氢气从塔顶离开经naoh溶液去酸洗涤作为纯度100%商品气输出。冷凝塔底部的含碘液体部分重新从塔顶喷淋循环,剩余部分重新返回至bunsen预混罐。
[0038]
对系统热量衡算可知,总余热回收效率91%,实现了高能量利用效率。
[0039]
实施例2bunsen反应分离塔内初始温度85℃常压,塔内投料为10 mol so2,34 mol i2,105 mol水。反应1.5h后so2转化率达95%。两相静置20 min分离,分别进入h2so4系统和hix系统。h2so4相和hix相出口温度为85℃。
[0040]
h2so4相组成为h2so
4 4.6 mol/kg,hi 0.3mol/kg,i
2 0.07 mol/kg,h2o 27.4 mol/kg。液相混合物从h2so4浓缩塔顶部喷淋,下降过程中与来自h2so4分解塔的so2和o2的高温蒸汽相遇,液体水被迅速汽化带离。高温混合气体(450-500℃)从h2so4浓缩塔塔顶经风机作用进入hix纯化浓缩塔。h2so4浓缩塔底部h2so4浓度达到9.6 mol/kg,塔底部出口温度85-90℃。浓硫酸进入h2so4分解塔,在850-900℃催化剂的作用下发生分解反应,分解率达96%以
上。分解产生的so2、o2和h2o的摩尔比约为2:2:1,混合气体从塔顶部离开,出口温度为850-900℃。高温混合气体返回至h2so4浓缩塔中循环。
[0041]
hix相组成为h2so
4 0.04 mol/kg,hi 1.17 mol/kg,i
2 3.2 mol/kg,h2o 1.9 mol/kg。液相混合物从hix纯化浓缩塔顶部喷淋,下降过程中与来自h2so4浓缩塔的so2和o2的高温蒸汽(450-500℃)相遇,液体水被迅速汽化带离。杂质h2so4与hi在富氧条件下发生反应转化为so2被带离。发生反应如下:副产物s生成:h2so
4 6hi = s 3i
2 4h2o;副产物h2s生成:h2so
4 8hi = h2s 4i
2 4h2o;副产物与混合气发生反应:s o
2 = so2,2h2s 3o
2 = 2so
2 2h2o,s和h2s在富氧环境中转化率为100%,有效的达到纯化hix的目的。
[0042]
hix纯化浓缩塔顶出口温度为150-200℃,富氧混合气体从塔顶重新返回bunsen反应分离塔。氧气从bunsen反应分离塔顶部离开,经naoh溶液去酸洗涤作为纯度100%商品气输出。hix纯化浓缩塔底部hi浓度达到2.2 mol/kg,塔底部出口温度85-90℃。浓hi溶液进入hi分解塔,在450℃催化剂的作用下发生分解反应,分解率为22%。分解产生的h2、i2、未反应的hi气体以及水蒸气从塔顶部离开,出口温度为450℃。高温混合气体经风机作用送入至冷凝塔中,上升过程中与冷凝塔塔顶喷淋的含碘液体相遇,水蒸气冷凝,hi、i2气体溶解于水中,氢气从冷凝塔塔顶离开经naoh溶液去酸洗涤作为纯度100%商品气输出。冷凝塔底部的含碘液体部分作为塔顶喷淋液被加压泵送至塔顶喷淋循环,剩余部分重新返回至bunsen预混罐。
[0043]
对系统热量衡算可知,总余热回收效率91%,实现了高能量利用效率。
[0044]
以上所述实施例仅表达了本发明的几种实施方式,其描述较为具体和详细,但并不能因此而理解为对本发明专利范围的限制。应当指出的是,对于本领域的普通技术人员来说,在不脱离本发明构思的前提下,还可以做出若干变形和改进,这些都属于本发明的保护范围。因此,本发明的保护范围应以所附权利要求为准。
再多了解一些
本文用于企业家、创业者技术爱好者查询,结果仅供参考。