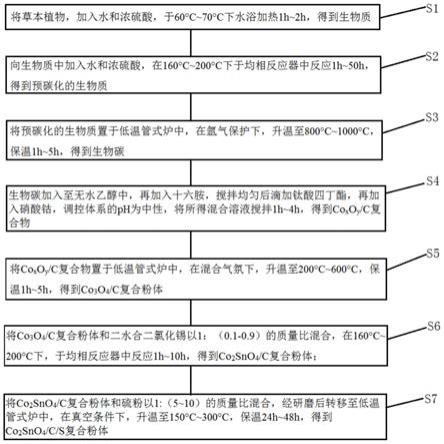
co2sno4/c/s复合材料及其二氧化钛诱导生长方法、应用
技术领域
1.本发明属于锂-硫电池电极制备技术领域,涉及co2sno4/c/s复合材料及其二氧化钛诱导生长方法、应用。
背景技术:
2.化石燃料的大量燃烧导致生态环境急剧恶化,可充电电池的出现和发展让我们逐步走向更加绿色环保的新世纪。到目前为止,锂离子电池已经可以广泛应用在便携式电子设备和电动汽车中。随着大型电子设备的大量渗入,对于锂离子电池的尺寸需求也从中型发展为大型,从而保证能量在电网系统的大量存储。但是,锂电的制备技术中仍然存在高成本、安全隐患、能量密度低等问题,为了这些问题,研究者们正在加紧对于新型能量存储系统(例如:钠离子电池、锂空气电池、锂-硫电池等)的研究。
3.其中,锂硫电池得到了广泛的关注主要由于硫元素的含量丰富并且具有环境兼容性。除此以外,在电化学反应过程中,硫与锂离子发生了两步电子氧化还原反应,产生了1675mah
·
g-1
的高比容量和2600wh
·
kg-1
的能量密度,具有良好的研究和应用前景。
4.但是,锂硫电池在推广使用中仍然存在大量的问题,主要表现在三个方面:(1)s8和li2s的电化学绝缘性。在电化学反应过程中,s8和li2s的降低了硫的利用率,锂硫中间产物在电解液中的溶解,导致电池库伦效率低、容易发生自放电现象。(2)电解液不适配。传统的碳基电解液与硫电极并不匹配,聚硫化物中间产物容易溶解在电解液中,导致首圈较高的容量在第二圈快速降到接近于0。后来采用醚基电解液取代该电解液来解决该化学反应不稳定问题,但该类电解液系统具有较高的蒸气压,燃点较低,在真空条件下容易造成安全隐患。(3)较大的体积膨胀。锂金属具有较高的比容量但是循环稳定性较差。不同于石墨等惰性电极,循环过程中体积膨胀仅有20%。锂离子在放电过程中锂金属表面脱出,在充电过程中不断补充回表面造成体积膨胀。在反应产物中在锂金属和电解液表面产生sei膜,较大的体积变化在每一次循环过程中形成的sei膜表面产生裂纹,大量的电解液和聚硫化物被消耗,造成容量的损失[fang r,zhao s,hou p,et al.3d interconnected electrode materials with ultrahigh areal sulfur loading for li-s batteries[j].advanced materials,2016,28(17):3374-3382.,zhang z,li q,jiang s,et al.sulfur encapsulated in a tio
2-anchored hollow carbon nanofiber hybrid nanostructure for lithium
–
sulfur batteries[j].chemistry,2015,21(3):1343-1349.,chen l,shaw l l.recent advances in lithium
–
sulfur batteries[j].journal of power sources,2014,267(3):770-783,wang j g,xie k,wei b.advanced engineering of nanostructured carbons for lithium-sulfur batteries[j].nano energy,2015,15:413-444.]。
[0005]
锡具有导电性能好、锂离子扩散率高、氧化还原电位低的优点[葛荣云.石墨烯基锗酸盐、锡酸盐材料的合成及其作为锂电池负极材料的性能研究[d].华南理工大学,2016.]。大量研究表明,锡酸盐(m2sno4)材料具有较高的理论容量和较强的催化活性,将有
利于实现较高的锂-硫电池容量。cao[cao yiqi,zhang lei,tao duolei et.al.facile synthesis of cosno3/graphene nanohybrid with superior lithium storage capability[j].electrochimica acta,2014,18(05):34-68.]等人用石墨烯包裹锡酸钴形成纳米复合物,当电流密度为200ma
·
g-1
时,第一圈充电比容量达到830mah
·
g-1
并且在循环50圈后仍具有87%的容量保持率。然而,金属锡酸盐在锂-硫电池中的研究较少,其对聚硫化物的转化机理并不明确。此外,锡酸盐的制备方法比较复杂,一般为沉淀法或溶胶-凝胶法。由于其表面极性较强,不利于和极性弱的碳材料复合,这限制了金属锡酸盐在锂-硫电池中的发展。
技术实现要素:
[0006]
为了达到上述目的,本发明提供co2sno4/c/s复合材料及其二氧化钛诱导生长方法、应用,所制得的co2sno4/c/s复合材料作为锂-硫电池电池正极时,具有良好的导电性和较强的催化能力,在循环过程中正极材料结构不易破坏,可以更加稳定地捕获聚硫化物,有利于提升li-s电池的循环稳定性,解决了现有技术中存在的正极材料具有的各组成结合程度不强、中间产物易溶解、大体积膨胀,以及制备方法复杂的问题。
[0007]
本发明所采用的技术方案是,co2sno4/c/s复合材料的二氧化钛诱导生长方法,包括以下步骤:
[0008]
步骤1:将2g~4g草本植物,加入45ml水和5ml~15ml浓硫酸,置于水热反应釜中,于60℃~70℃下水浴加热1h~2h,所得产物经清洗、干燥,得到生物质;
[0009]
步骤2:向步骤1得到的生物质中,加入25ml~45ml的水和5ml~25ml的浓硫酸,置于水热反应釜中,在160℃~200℃的温度条件下,于均相反应器中反应1h~50h,得到预碳化的生物质;
[0010]
步骤3:将步骤2得到的预碳化的生物质置于低温管式炉中,在氩气保护下,升温至800℃~1000℃,保温1h~5h,所得产物经清洗、干燥,得到生物碳;
[0011]
步骤4:取0.1g~0.5g的所述生物碳加入至无水乙醇中,再加入十六胺,所述十六胺与生物碳的质量比为1:1,搅拌均匀后滴加1滴~100滴的钛酸四丁酯,搅拌均匀后再加入硝酸钴,所述硝酸钴与钛酸四丁酯的摩尔比为0.05:1;搅拌均匀后调控体系的ph为中性,得到混合溶液,将混合溶液搅拌1h~4h,所得产物经离心、干燥,得到co
x
oy/c复合材料,x=1~3,y=1~4;
[0012]
步骤5:将步骤4得到的co
x
oy/c复合材料置于低温管式炉中,在氩气和氢气的混合气氛下,升温至200℃~600℃,保温1h~5h,所得产物经清洗、干燥,得到co3o4/c复合材料;
[0013]
步骤6:将步骤5得到的co3o4/c复合材料和二水合二氯化锡以1:(0.1-0.9)的质量比混合,加入50ml水,转移至水热反应釜中,在160℃~200℃的温度条件下,于均相反应器中反应1h~10h,得到co2sno4/c复合材料;
[0014]
步骤7:将步骤6得到的co2sno4/c复合材料和硫粉以1:(5~10)的质量比混合,经研磨后转移至低温管式炉中,在真空条件下,升温至150℃~300℃,保温24h~48h,得到所述co2sno4/c/s复合材料。
[0015]
进一步地,步骤1中,草本植物包括:蒲草、金鱼草、醉鱼草、油点草中的任一种。
[0016]
进一步地,步骤2中,水和浓硫酸的体积之和为50ml。
[0017]
进一步地,步骤3中,升温的速率为:10℃/min~20℃/min。
[0018]
进一步地,步骤4中,将混合溶液搅拌1h~4h具体为:将混合溶液以500r/min~1000r/min的速率搅拌1h~4h。
[0019]
进一步地,步骤5中,氩气和氢气的混合气氛中,氩气与氢气的体积比为9:1。
[0020]
进一步地,步骤5中,升温的速率为10℃/min~20℃/min。
[0021]
进一步地,步骤7中,升温的速率为10℃/min~20℃/min。
[0022]
本发明的另一发明目的,在于提供一种co2sno4/c/s复合材料,如上述二氧化钛诱导生长co2sno4/c/s复合材料的方法制备而得。
[0023]
本发明的再一发明目的,在于提供一种上述co2sno4/c/s复合材料在锂硫电池正极材料领域的应用。
[0024]
本发明的有益效果是:
[0025]
(1)本发明实施例在生物碳表面合成结晶性较弱的无定型二氧化钛来促进co2sno4在生物碳表面的生长;无定型二氧化钛辅助生长在生物碳表面产生更多且均一的活性位点,这更有利于co2sno4在生物碳表面的均匀负载,相比于传统的沉淀法,在实现高负载量的同时,降低颗粒在生物碳表面的团聚几率,产生高的比表面积;并且无定型二氧化钛在生物碳表面的包覆增强了生物碳的表面极性,为co3o4的生长奠定了基础;钴夺取无定型二氧化钛和生物碳表面的氧原子,得到结晶性强的co3o4。
[0026]
(2)本发明实施例通过水热反应,实现sno2原位负载,得到co2sno4/c复合材料,再通过硫负载得到co2sno4/c/s复合材料用于锂-硫电池正极;co2sno4/c/s复合材料具有具有更强的结合能,co2sno4在生物碳表面的负载更加均匀,在充放电过程中更稳定地捕获聚硫化物,复合电极具有较好的循环稳定性。
附图说明
[0027]
为了更清楚地说明本发明实施例或现有技术中的技术方案,下面将对实施例或现有技术描述中所需要使用的附图作简单地介绍,显而易见地,下面描述中的附图仅仅是本发明的一些实施例,对于本领域普通技术人员来讲,在不付出创造性劳动的前提下,还可以根据这些附图获得其他的附图。
[0028]
图1是本发明实施例co2sno4/c/s复合材料的制备工艺流程图。
[0029]
图2是本发明实施例制得的co2sno4/c复合材料的xrd图。
[0030]
图3是本发明实施例制得的co2sno4/c复合材料的sem图。
[0031]
图4是本发明实施例制得的co2sno4/c复合材料的细节放大图。
[0032]
图5是本发明实施例制得的co2sno4/c/s复合材料的xrd图。
[0033]
图6是本发明实施例制得的co2sno4/c/s复合材料的ti 2p峰图。
[0034]
图7是本发明实施例制得的co2sno4/c/s复合材料的sem图。
[0035]
图8是本发明实施例制得的co2sno4/c/s复合材料在高倍条件下的sem图。
[0036]
图9是本发明实施例制得的co2sno4/c/s复合材料作为锂硫电池正极的循环性能图。
具体实施方式
[0037]
下面将结合本发明实施例中的附图,对本发明实施例中的技术方案进行清楚、完整地描述,显然,所描述的实施例仅仅是本发明一部分实施例,而不是全部的实施例。基于本发明中的实施例,本领域普通技术人员在没有做出创造性劳动前提下所获得的所有其他实施例,都属于本发明保护的范围。
[0038]
本发明采用的浓硫酸为质量分数大于或等于70%的硫酸水溶液。
[0039]
co2sno4/c/s复合材料的二氧化钛诱导生长方法,如图1所示,包括以下步骤:
[0040]
步骤1:取2.0g~4.0g草本植物,加入45ml水和5ml~15ml浓硫酸,置于水热反应釜中,在60℃~70℃的温度条件下于水浴锅内加热1h~2h,所得产物经100ml水清洗,并在冷冻干燥机中干燥(-10℃~-60℃,2h~20h),得到生物质。
[0041]
草本植物包括:蒲草、金鱼草、醉鱼草、油点草中的任一种。
[0042]
本步骤采用蒲草、金鱼草、醉鱼草或油点草的草本植物制备生物碳的原料,草本类植物具有较薄的厚度,易于热处理且孔隙率较高,有利于以其为原料制成的生物碳表面具有更大的孔隙率、比表面积以及活性位点,有利于后续金属锡酸盐和硫单质的负载。
[0043]
本步骤的目的是:分解草本植物表面难分解的物质(如:纤维素等大分子物质),产生更多的孔结构,增加产物的微孔结构和活性位点,提高产物的比表面积。
[0044]
步骤2:向生物质中,加入25ml~45ml的水和5ml~25ml的浓硫酸,水和浓硫酸的体积之和为50ml,置于水热反应釜中,在160℃~200℃的温度条件下,于均相反应器中反应1h~50h,得到预碳化的生物质。
[0045]
本步骤将生物质在酸性环境下,经水热处理的目的是:通过温和调控的水热处理手段,在保持生物质本身结构的完整的前提下,调控产物的微孔分布均匀性、以及数量和孔径大小,提高产物的比表面积,调控产物表面含氧基团的数量和分布均匀性,提高产物的表面极性和活性,并增加产物中碳的石墨化程度,为后续步骤锡酸钴和硫的均匀负载提供有利的结构基础。
[0046]
本步骤的实现原理是:生物质在酸性条件下,经水热反应,其本身结构完整,但其表面发生分解反应,暴露出更多分布均匀的微孔,且微孔孔径也受控增大,且在水热过程中形成众多分布均匀的含氧官能团(如羟基、羧基、酚羟基等),使得水热产物既增加了比表面积又增加了表面极性,产物的活性位点也更多以及分布均匀,这种改变为后续物质在生物碳上的负载提供了良好的基础。
[0047]
同时,生物质经水热处理后,所得产物中碳的碳化程度提高,具有一定的石墨化程度,这种改变使得下一步骤预碳化的生物质在热处理的过程中,热能用来对碳源进行石墨化程度的调控与优化。若没有本步骤,生物质直接经下一步骤低温管式炉中碳化,就不能直接调控产物中碳的石墨化程度和孔径大小,且在热处理快速升温过程中,生物质的纤维素可能直接断裂,造成生物质本身结构的破坏,这样不利于锡酸钴和硫的均匀、稳定负载。
[0048]
步骤3:将预碳化的生物质置于低温管式炉中,在氩气保护下,从室温以10℃/min~20℃/min的升温速率升温至800℃~1000℃,保温1h~5h,所得产物经20ml的hcl(浓度为1mol/l~5mol/l)和100ml水清洗、抽滤机抽滤、以及在冷冻干燥机中干燥(-10℃~-60℃,2h~20h),得到生物碳。
[0049]
本步骤制得的生物碳为管状、块状或片状结构,其具有高的表面极性、大的比表面
积和丰富的孔隙率,有利于金属锡酸盐和硫单质的稳定负载,在电池循环过程中由于硫单质不容易从生物碳表面脱落,可以充分缓解硫的体积效应。
[0050]
若采用葡萄糖/蔗糖作为碳源,制得的碳材料一般为球状结构,而球状结构碳不利于金属锡酸盐和硫单质的稳定负载,在电池循环过程中硫的体积效应不能充分缓解,导致硫颗粒从球状结构表面脱落。
[0051]
若采用市售碳粉和石墨烯为碳源,由于其一般具有高的导电性和弱的表面极性,不利于与极性强的锡酸盐结合,致使两者的结合力不强。此外,石墨烯在负载过程中容易发生卷曲和堆叠,结构不可控。
[0052]
步骤4:取0.1g~0.5g生物碳加入到盛有20ml无水乙醇的烧杯中,再加入与生物碳质量比为1:1的十六胺,搅拌10min~20min后,用胶头滴管滴加钛酸四丁酯,钛酸四丁酯的滴加量为1滴~100滴,继续搅拌10min~20min后,加入硝酸钴(晶体形态),硝酸钴与钛酸四丁酯的摩尔比为0.05:1,又继续搅拌10min~20min,加入氨水用于调控体系的ph,直到溶液的ph为中性,得到混合溶液,将混合溶液以500r/min~1000r/min的搅拌速率搅拌1h~4h后离心,所得产物用水洗三次后继续离心,所得产物在冷冻干燥机中干燥(-10℃~-60℃,2h~20h),得到co
x
oy/c复合材料,x=1~3,y=1~4。
[0053]
本步骤的实现原理是:生物碳、钛酸四丁酯、硝酸钴均匀混合,在钛酸四丁酯经溶胶凝胶法制备无定型二氧化钛的过程中,生成的无定型二氧化钛均匀原位包覆在生物碳表面,由于无定型二氧化钛的结晶性弱,且二氧化钛中的氧来自于生物碳表面的含氧官能团,因此,无定型二氧化钛与生物碳的结合程度良好。同时由于无定型二氧化钛的极性良好,大幅提升了生物碳的表面极性,有利于生物碳与极性物质的负载。并且,钴元素在参与原位反应的过程中,夺取无定型二氧化钛中的氧原子,形成钴的氧化物co
x
oy,这种结合方式相比直接将钴盐与生物碳结合,大幅增强了钴的氧化物与生物碳的结合程度,为后续锡酸钴的合成奠定基础。
[0054]
若没有钛元素的添加,直接将生物碳浸渍在硝酸钴溶液中,由于生物碳的表面极性较弱,与钴的极性差别较大,二者结合力较差。
[0055]
步骤5:将co
x
oy/c复合材料置于低温管式炉中,在氩气/氢气的混合气氛保护下,从室温以10℃/min~20℃/min的升温速率升温至200℃~600℃,保温1h~5h,所得产物经100ml水中清洗、抽滤机抽滤、以及在冷冻干燥机中干燥(-10℃~-60℃,2h~20h),得到co3o4/c复合材料,co3o4/c复合材料中钛元素仍然以无定型二氧化钛形态存在。
[0056]
本步骤的起始原料co
x
oy/c复合材料中co
x
oy与生物碳的结合程度良好,因此其经热处理后,所得产物co3o4/c复合材料中co3o4与生物碳的结合程度也很好,co3o4不容易从生物碳表面脱落,不会造成复合结构的破坏。并且co
x
oy在转变为co3o4的过程中,其氧元素是夺取无定型二氧化钛中的氧原子和生物碳表面的氧原子实现的,进一步提升了co3o4与生物碳的结合程度。
[0057]
本步骤所得钴类产物是co3o4,由于反应过程中氩氢混合气氛的还原作用,不产生其他副产物。混合气氛中氩气与氢气的体积比为9:1,氢气在体系中所起的作用是提供还原气氛,防止钴的氧化物被碳还原。
[0058]
(6)将co3o4/c复合材料和二水合二氯化锡以1:(0.1-0.9)的质量比混合,加入50ml水,转移至水热反应釜中,在160℃~200℃的温度条件下,于均相反应器中反应1h~10h,得
到co2sno4/c复合材料。
[0059]
(7)将co2sno4/c复合材料和硫粉以1:(5-10)的质量比混合,并在研钵中研磨30min~90min,将所得混合物转移至低温管式炉中,在真空条件下,从室温以10℃/min~20℃/min的升温速率升温至150℃~300℃,保温24h~48h,得到co2sno4/c/s复合材料。
[0060]
本步骤所采用的硫粉为升华硫,纯度99.99%,粉末状。
[0061]
本步骤升温至150℃~300℃的原因是保证硫处于熔融的状态,防止死硫(负载在表面结合力不强的硫)在表面聚集。
[0062]
本发明制备的co2sno4/c/s复合材料,其引入极性强的无定形二氧化钛诱导co2sno4生长在生物碳表面,co2sno4与生物碳的结合程度更强,且经过本发明各步骤的实施,使得co2sno4与生物碳的负载更加均匀、更加稳定。
[0063]
上述优势使得本发明制得的co2sno4/c/s复合材料作为锂-硫电池电池正极时,具有良好的催化活性,有利于聚硫化物的快速转化:生物碳具有高比表面积和高导电性,正极材料具有较快的电子传输能力;正极材料的表面极性有利于聚硫化物的快速吸附,形成较高的容量;在循环过程中正极材料结构不易破坏,可以更加稳定地捕获聚硫化物,有利于提升li-s电池的循环稳定性。
[0064]
实施例1
[0065]
(1)取2.0g蒲草置于水热反应釜中,加入45ml水,5ml浓硫酸,在60℃水浴锅内加热1h,随后用100ml水清洗并在冷冻干燥机中干燥(-10℃,20h),得到生物质。
[0066]
(2)将生物质置于水热反应釜中,加入45ml水,5ml浓硫酸,在均相反应器中反应,反应温度为160℃,反应时间为50h,得到预碳化的生物质。
[0067]
(3)将预碳化的生物质置于低温管式炉中,在氩气保护下,从室温以10℃/min的升温速率升温至800℃,并保温1h。将产物在20ml的hcl(浓度为1mol/l)和100ml水中清洗,用抽滤机抽滤并在冷冻干燥机中干燥(-10℃,20h),得到生物碳。
[0068]
(4)取0.1g生物碳加入到盛有20ml无水乙醇的烧杯中,再加入与生物碳质量比为1:1的十六胺,搅拌10min后,用胶头滴管滴加钛酸四丁酯,钛酸四丁酯的滴加量为1滴,继续搅拌10min后,加入硝酸钴,硝酸钴和钛酸四丁酯的摩尔比为0.05:1,又继续搅拌10min后,加入氨水,直到溶液的ph为中性,得到混合溶液;将混合溶液以500r/min的搅拌速率继续搅拌1h后离心,所得产物用水洗三次后继续离心,将反应所得沉淀在冷冻干燥机中干燥(-10℃,20h),得到co
x
oy/c复合材料。
[0069]
(5)将co
x
oy/c复合材料置于低温管式炉中,在氩气/氢气混合气体保护下加热,氩气与氢气的体积比为9:1,从室温以10℃/min的升温速率升温至200℃,并保温1h。将产物在100ml水中清洗,用抽滤机抽滤并在冷冻干燥机中干燥(-10℃,20h),得到co3o4/c复合材料。
[0070]
(6)将co3o4/c复合材料和二水合二氯化锡以质量比1:0.1的比例混合后,加入50ml水后转移至水热反应釜中,在均相反应器中反应,反应温度为160℃,反应时间为10h,得到co2sno4/c复合材料。
[0071]
(7)将co2sno4/c复合材料和硫粉以质量比1:5的比例混合,并在研钵中研磨30min。将所得混合物转移至低温管式炉中,在真空条件下加热,从室温以10℃/min的升温速率升温至150℃,并保温24h,得到co2sno4/c/s复合材料。
[0072]
实施例2
[0073]
(1)取4.0g金鱼草置于水热反应釜中,加入45ml水,15ml浓硫酸,在70℃水浴锅内加热2h,随后用100ml水清洗并在冷冻干燥机中干燥(-60℃,2h),得到生物质。
[0074]
(2)将生物质置于水热反应釜中,加入25ml水,25ml浓硫酸,在均相反应器中反应,反应温度为200℃,反应时间为1h,得到预碳化的生物质。
[0075]
(3)将预碳化的生物质置于低温管式炉中,在氩气保护下加热,从室温以20℃/min的升温速率升温至1000℃,并保温5h。将产物在20ml hcl(浓度为5mol/l)和100ml水中清洗,用抽滤机抽滤并在冷冻干燥机中干燥(-60℃,2h),得到生物碳。
[0076]
(4)取0.5g生物碳加入到盛有20ml无水乙醇的烧杯中,再加入与生物碳质量比为1:1的十六胺,搅拌20min后,用胶头滴管滴加钛酸四丁酯,钛酸四丁酯的滴加量为100滴,继续搅拌20min后,加入硝酸钴,硝酸钴和钛酸四丁酯的摩尔比为0.05:1,又继续搅拌20min后,加入氨水,直到溶液的ph为中性,得到混合溶液;将混合溶液以1000r/min的搅拌速率继续搅拌4h后离心,所得产物用水洗三次后继续离心,将反应所得沉淀在冷冻干燥机中干燥(-60℃,2h),得到co
x
oy/c复合材料。
[0077]
(5)将co
x
oy/c复合材料置于低温管式炉中,在氩气/氢气混合气体保护下加热,氩气与氢气的体积比为9:1,从室温以20℃/min的升温速率升温至600℃,并保温5h。将产物在100ml水中清洗,用抽滤机抽滤并在冷冻干燥机中干燥(-60℃,2h),得到co3o4/c复合材料。
[0078]
(6)将co3o4/c复合材料和二水合二氯化锡以质量比1:0.9的比例混合后,加入50ml水后转移至水热反应釜中,在均相反应器中反应,反应温度为200℃,反应时间为1h,得到co2sno4/c复合材料。
[0079]
(7)将co2sno4/c复合材料和硫粉以质量比1:10的比例混合,并在研钵中研磨90min。将所得混合物转移至低温管式炉中,在真空条件下加热,从室温以20℃/min的升温速率升温至300℃,并保温48h,得到co2sno4/c/s复合材料。
[0080]
实施例3
[0081]
(1)取3.0g醉鱼草置于水热反应釜中,加入45ml水,10ml浓硫酸,在65℃水浴锅内加热1h,随后用100ml水清洗并在冷冻干燥机中干燥(-40℃ 12h),得到生物质。
[0082]
(2)将生物质置于水热反应釜中,加入40ml水,10ml浓硫酸,在均相反应器中反应,反应温度为180℃,反应时间为24h,得到预碳化的生物质。
[0083]
(3)将预碳化的生物质置于低温管式炉中,在氩气保护下加热,从室温以15℃/min的升温速率升温至1000℃,并保温2h。将产物在20ml hcl(浓度为3mol/l)和100ml水中清洗,用抽滤机抽滤并在冷冻干燥机中干燥(-40℃,12h),得到生物碳。
[0084]
(4)取0.3g生物碳加入到盛有20ml无水乙醇的烧杯中,再加入与生物碳质量比为1:1的十六胺,搅拌16min后,用胶头滴管滴加钛酸四丁酯,钛酸四丁酯的滴加量为50滴,继续搅拌13min后,加入硝酸钴,硝酸钴和钛酸四丁酯的摩尔比为0.05:1,又继续搅拌15min后,加入氨水,直到溶液的ph为中性,得到混合溶液;将混合溶液以750r/min的搅拌速率继续搅拌2h后离心,所得产物用水洗三次后继续离心,将反应所得沉淀在冷冻干燥机中干燥(-40℃,20h),得到co
x
oy/c复合材料。
[0085]
(5)将co
x
oy/c复合材料置于低温管式炉中,在氩气/氢气混合气体保护下加热,氩气与氢气的体积比为9:1,从室温以15℃/min的升温速率升温至400℃,并保温3h。将产物在100ml水中清洗,用抽滤机抽滤并在冷冻干燥机中干燥(-40℃,12h),得到co3o4/c复合材料。
[0086]
(6)将co3o4/c复合材料和二水合二氯化锡以质量比1:0.5的比例混合后,加入50ml水后转移至水热反应釜中,在均相反应器中反应,反应温度为180℃,反应时间为7h,得到co2sno4/c复合材料。
[0087]
(7)将co2sno4/c复合材料和硫粉以质量比1:7的比例混合,并在研钵中研磨60min,将所得混合物转移至低温管式炉中,在真空条件下加热,从室温以16℃/min的升温速率升温至200℃,并保温36h,得到co2sno4/c/s复合材料。
[0088]
本实施例步骤(6)所得的co2sno4/c复合材料的xrd测试结果如图2所示,可以看出,co2sno4/c复合材料中存在co2sno4主特征峰,说明co2sno4/c复合材料中成功制备得到了co2sno4,co2sno4/c复合材料的结晶程度不高,这可能与co
x
oy生长前无定型的二氧化锡的存在有关。
[0089]
结合图3所示的co2sno4/c复合材料的sem图,可以看到co2sno4/c复合材料整体呈现管状结构,且管状结构表面均匀且大量地负载了co2sno4,且从图4所示的co2sno4/c复合材料的细节放大sem图可以看出,管状结构表面负载的co2sno4的粒度大量小于50nm,且在图4中也可以看出管状结构上存在孔洞,有助于增加其比表面积和提供足够多的活性位点,有利于快速捕获聚硫化物和缓解硫的氧化还原反应所带来的体积膨胀。
[0090]
本实施例步骤(7)所得的co2sno4/c/s复合材料的xrd测试结果如图5所示,可以看出产物中明显存在s的主特征峰,证明步骤(7)成功将s引入产物体系。
[0091]
由图6可知,本实施例制得的co2sno4/c/s复合材料存在ti 2p峰,可知在产物中钛元素仍以无定型二氧化钛形式存在。
[0092]
本实施例步骤(7)所得的co2sno4/c/s复合材料的sem图如图7所示,可以看出产物的尺寸明显增大,且产物表面的粗糙程度明显增加,表面的负载量明显增强,各种物质的结合程度显著增加,这有助于维持反应过程中复合结构的稳定性。
[0093]
通过图8所示的co2sno4/c/s复合材料在高倍条件下测试的sem图可以明显看出,产物的表面的负载物与生物碳的结合程度非常好,且负载的量大、分布均匀性好,均有利于提高电极的循环稳定性和倍率性能。
[0094]
本实施例制得的co2sno4/c/s复合材料作为锂硫电池正极的循环性能图,如图9所示,在1c的电流密度下循环500圈后的可逆容量仍然保持在~300mah
·
g-1
,其电化学性能已经可以单独作为锂-硫电池正极使用,其循环稳定性已基本能够满足要求。
[0095]
实施例4
[0096]
(1)取3.5g蒲草置于水热反应釜中,加入45ml水,7.5ml浓硫酸,在62℃水浴锅内加热1.5h,随后用100ml水清洗并在冷冻干燥机中干燥(-50℃,4h),得到生物质。
[0097]
(2)将生物质置于水热反应釜中,加入35ml水,15ml浓硫酸,在均相反应器中反应,反应温度为170℃,反应时间为36h,得到预碳化的生物质。
[0098]
(3)将预碳化的生物质置于低温管式炉中,在氩气保护下加热,从室温以12℃/min的升温速率升温至850℃,并保温4h。将产物在20ml hcl(浓度为2mol/l)和100ml水中清洗,用抽滤机抽滤并在冷冻干燥机中干燥(-30℃,6h),得到生物碳。
[0099]
(4)取0.45g生物碳加入到盛有20ml无水乙醇的烧杯中,再加入与生物碳质量比为1:1的十六胺,搅拌18min后,用胶头滴管滴加钛酸四丁酯,钛酸四丁酯的滴加量为40滴,继续搅拌18min后,加入硝酸钴,硝酸钴和钛酸四丁酯的摩尔比为0.05:1,又继续搅拌18min
后,加入氨水,直到溶液的ph为中性,得到混合溶液;将混合溶液以650r/min的搅拌速率继续搅拌2.5h后离心,所得产物用水洗三次后继续离心,将反应所得沉淀在冷冻干燥机中干燥(-30℃,18h),得到co
x
oy/c复合材料。
[0100]
(5)将co
x
oy/c复合材料置于低温管式炉中,在氩气/氢气混合气体保护下加热,氩气与氢气的体积比为9:1,从室温以12℃/min的升温速率升温至300℃,并保温2h。将产物在100ml水中清洗,用抽滤机抽滤并在冷冻干燥机中干燥(-30℃,18h),得到co3o4/c复合材料。
[0101]
(6)将co3o4/c复合材料和二水合二氯化锡以质量比1:0.7的比例混合后,加入50ml水后转移至水热反应釜中,在均相反应器中反应,反应温度为170℃,反应时间为7h,得到co2sno4/c复合材料。
[0102]
(7)将co2sno4/c复合材料和硫粉以质量比1:6的比例混合,并在研钵中研磨70min,将所得混合物转移至低温管式炉中,在真空条件下加热,从室温以12℃/min的升温速率升温至250℃,并保温30h,得到co2sno4/c/s复合材料。
[0103]
实施例5
[0104]
(1)取2.0g油点草置于水热反应釜中,加入45ml水,12.5ml浓硫酸,在68℃水浴锅内加热2h,随后用100ml水清洗并在冷冻干燥机中干燥(-30℃,15h),得到生物质。
[0105]
(2)将生物质置于水热反应釜中,加入30ml水,20ml浓硫酸,在均相反应器中反应,反应温度为190℃,反应时间为12h,得到预碳化的生物质。
[0106]
(3)将预碳化的生物质置于低温管式炉中,在氩气保护下加热,从室温以18℃/min的升温速率升温至900℃,并保温3h。将产物在20ml hcl(浓度为4mol/l)和100ml水中清洗,用抽滤机抽滤并在冷冻干燥机中干燥(-50℃,16h),得到生物碳。
[0107]
(4)取0.4g生物碳加入到盛有20ml无水乙醇的烧杯中,再加入与生物碳质量比为1:1的十六胺,搅拌12min后,用胶头滴管滴加钛酸四丁酯,钛酸四丁酯的滴加量为60滴,继续搅拌12min后,加入硝酸钴,硝酸钴和钛酸四丁酯的摩尔比为0.05:1,又继续搅拌12min后,加入氨水,直到溶液的ph为中性,得到混合溶液;将混合溶液以850r/min的搅拌速率继续搅拌3.5h后离心,所得产物用水洗三次后继续离心,将反应所得沉淀在冷冻干燥机中干燥(-50℃,16h),得到co
x
oy/c复合材料。
[0108]
(5)将co
x
oy/c复合材料置于低温管式炉中,在氩气/氢气混合气体保护下加热,氩气与氢气的体积比为9:1,从室温以18℃/min的升温速率升温至500℃,并保温4h。将产物在100ml水中清洗,用抽滤机抽滤并在冷冻干燥机中干燥(-50℃,8h),得到co3o4/c复合材料。
[0109]
(6)将co3o4/c复合材料和二水合二氯化锡以质量比1:0.3的比例混合后,加入50ml水后转移至水热反应釜中,在均相反应器中反应,反应温度为190℃,反应时间为3h,得到co2sno4/c复合材料。
[0110]
(7)将co2sno4/c复合材料和硫粉以质量比1:8的比例混合,并在研钵中研磨80min,将所得混合物转移至低温管式炉中,在真空条件下加热,从室温以18℃/min的升温速率升温至155℃,并保温24h,得到co2sno4/c/s复合材料。
[0111]
实施例6
[0112]
(1)取3.6g金鱼草置于水热反应釜中,加入45ml水,9ml浓硫酸,在65℃水浴锅内加热1.2h,随后用100ml水清洗并在冷冻干燥机中干燥(-40℃,10h),得到生物质。
[0113]
(2)将生物质置于水热反应釜中,加入38ml水,12ml浓硫酸,在均相反应器中反应,
反应温度为185℃,反应时间为22h,得到预碳化的生物质。
[0114]
(3)将预碳化的生物质置于低温管式炉中,在氩气保护下加热,从室温以16℃/min的升温速率升温至950℃,并保温2.5h。将产物在20ml hcl(浓度为2.5mol/l)和100ml水中清洗,用抽滤机抽滤并在冷冻干燥机中干燥(-40℃,14h),得到生物碳。
[0115]
(4)取0.35g生物碳加入到盛有20ml无水乙醇的烧杯中,再加入与生物碳质量比为1:1的十六胺,搅拌13min后,用胶头滴管滴加钛酸四丁酯,钛酸四丁酯的滴加量为80滴,继续搅拌14min后,加入硝酸钴,硝酸钴和钛酸四丁酯的摩尔比为0.05:1,又继续搅拌13min后,加入氨水,直到溶液的ph为中性,得到混合溶液;将混合溶液以925r/min的搅拌速率继续搅拌3h后离心,所得产物用水洗三次后继续离心,将反应所得沉淀在冷冻干燥机中干燥(-40℃,18h),得到co
x
oy/c复合材料。
[0116]
(5)将co
x
oy/c复合材料置于低温管式炉中,在氩气/氢气混合气体保护下加热,氩气与氢气的体积比为9:1,从室温以17℃/min的升温速率升温至450℃,并保温1.5h。将产物在100ml水中清洗,用抽滤机抽滤并在冷冻干燥机中干燥(-40℃,16h),得到co3o4/c复合材料。
[0117]
(6)将co3o4/c复合材料和二水合二氯化锡以质量比1:0.6的比例混合后,加入50ml水后转移至水热反应釜中,在均相反应器中反应,反应温度为180℃,反应时间为6h,得到co2sno4/c复合材料。
[0118]
(7)将co2sno4/c复合材料和硫粉以质量比1:9的比例混合,并在研钵中研磨75min。将所得混合物转移至低温管式炉中,在真空条件下加热,从室温以13℃/min的升温速率升温至270℃,并保温24h,得到co2sno4/c/s复合材料。
[0119]
对比例1
[0120]
除步骤(3)中,升温至750℃,其余均与实施例3相同。
[0121]
对比例2
[0122]
除步骤(4)中不添加钛酸四丁酯,其余均与实施例3相同。
[0123]
对比例3
[0124]
除步骤(5)中升温至700℃,其余均与实施例3相同。
[0125]
对比例4
[0126]
除步骤(7)中升温至400℃,其余均与实施例3相同。
[0127]
实验例
[0128]
将实施例1~6制得的co2sno4/c/s复合材料作为电池正极,对其进行电池循环性能测试,在1c的电流密度下循环500圈后,其各自的可逆容量结果如表1所示。
[0129]
表1各实施例制得的co2sno4/c/s复合材料的电池循环性能测试结果
[0130]
项目1c的电流密度下循环500圈后的可逆容量实施例1100mah
·
g-1
实施例270mah
·
g-1
实施例3300mah
·
g-1
实施例4250mah
·
g-1
实施例5190mah
·
g-1
实施例6350mah
·
g-1
对比例1180mah
·
g-1
对比例2160mah
·
g-1
对比例3150mah
·
g-1
对比例450mah
·
g-1
[0131]
由表1可知,对比实施例3和对比例2,无定型二氧化钛的加入,显著提高了co2sno4和生物碳的结合能力,更有利于co2sno4在生物碳表面的负载,co2sno4和生物碳的紧密结合使得产物在电池长循环过程中复合结构不容易被破坏,实现优异的电化学性能。
[0132]
对比实施例1~3,钛酸四丁酯的添加量对复合结构的性能有重要影响,钛酸四丁酯的添加量过多或过少均不利于co2sno4和生物碳的复合,过多会减少生物碳表面的负载位点,过少会导致co2sno4和生物碳的结合能力不强,选取适当含量的钛酸四丁酯有利于实现结构稳定的co2sno4/c/s复合材料,提升li-s电池的电化学性能。
[0133]
对比实施例3~5,均相反应的温度对co2sno4的结晶程度有重要影响,进而影响复合结构的循环稳定性,180℃反应温度为co2sno4的最佳合成温度。
[0134]
对比实施例3和实施例6,硫的负载温度显著影响复合结构的循环稳定性,在较高的负载温度下得到的复合结构表面不存在“死硫”,所有的硫均可以可逆地参与氧化还原反应,实现较高的循环稳定性。
[0135]
对比实施例3和对比例1可知,生物碳的较高热解温度有利于提升复合结构的导电性,导电性的提升可以促进电子的快速传输,实现良好的循环稳定性。
[0136]
对比实施例3和对比例3,co
x
oy/c复合材料的热解温度调控对复合产物的物相有重要影响。当反应温度过高时,c会将co
x
oy还原为co单质,产物的物相发生变化,不利于形成co2sno4/c/s复合材料和实现优异的电化学性能。
[0137]
对比实施例3和对比例4,当硫的负载温度过高时,硫会以硫蒸气的方式存在,对复合材料进行硫化,这不利于co2sno4/c复合材料的硫负载,造成硫的负载率过低,从而循环稳定性下降。
[0138]
本说明书中的各个实施例均采用相关的方式描述,各个实施例之间相同相似的部分互相参见即可,每个实施例重点说明的都是与其他实施例的不同之处。
[0139]
以上所述仅为本发明的较佳实施例而已,并非用于限定本发明的保护范围。凡在本发明的精神和原则之内所作的任何修改、等同替换、改进等,均包含在本发明的保护范围内。
再多了解一些
本文用于企业家、创业者技术爱好者查询,结果仅供参考。