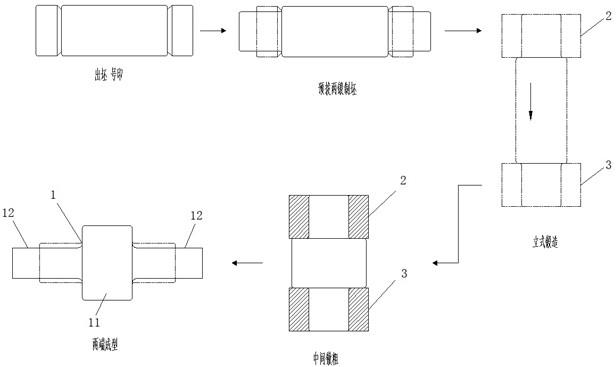
1.本发明涉及轴类锻件的锻造技术领域,尤其涉及一种高质量轴类锻件立式锻造工艺。
背景技术:
2.在自由锻行业,锻造大型轴类锻件很常见,尤其是中间直径较粗,两端直径较细的台阶轴,参见图1,台阶轴一般使用在齿轮行业上的传动齿轴、机械设备上的托轮轴等。此类轴锻件中间段直径较粗,两端直径较细,直径差较大,按常规轴类锻件锻造方法,做完锻造比后,出坯成圆柱,再两端号印分料,拔出两端直径小的台阶,参见图2;但此常规工艺成型方法有号印长度的局限性:号印端坯料的长度l1最小不能小于出坯直径d的1/3,如产品的材质锻造可塑性较差,则号印时出坯长度l1不小于出坯直径d的1/2,如满足不了这个条件,号印后拔长小台阶时,会在小台阶的两端中心在拔长过程中形成中心缩孔,造成产品尺寸不合格而报废,参见图3;且主轴材质为17-4ph,属沉淀硬化马氏体型时效不锈钢,塑性较差,锻造过程中锻件表面易开裂。
技术实现要素:
3.本发明的目的在于克服上述不足,提供一种高质量轴类锻件立式锻造工艺,节省原料,提高产品质量。
4.本发明的目的是这样实现的:一种高质量轴类锻件立式锻造工艺,用于生产台阶轴,台阶轴包括中间段以及两端的小台阶,它包括以下内容:步骤一、出坯:出坯时坯料直径小于锻件成型中间段的直径,大于锻件成型中间段直径的一半;步骤二、镦粗、拔长;步骤三、号印两端小台阶;步骤四、预拔两端小台阶,保留最后一火次的变形量,;步骤五、将预制坯锻件竖立,两端小台阶放进模具内,上部的小台阶放入上模中,下部的小台阶放入下模中;步骤六:将预制坯锻件竖向镦粗,使中间段变粗,直径达到锻件的成型尺寸;步骤七:脱模;步骤八:将两端小台阶再次按锻件的成型尺寸拔长到位。
5.进一步地,所述步骤四中预留锻造比大于1.5。
6.进一步地,所述步骤五中上模和下模的结构相同,均为圆环形模具。
7.进一步地,所述步骤七中脱模后滚圆。
8.与现有技术相比,本发明的有益效果是:(1)本发明出坯时不必按照产品尺寸的中间段直径出坯,出坯直径变小,避免了号
印分料的局限性,两端小台阶拔长时无需再加料,因此本发明可节省原材料,同一产品,使用本发明的锻造工艺技术,可节省30%的材料重量。
9.(2)本发明在最后一个火次锻造时,镦粗中间段,拔长两端小台阶,产品各部位都有变形量,组织更均匀,常规工艺最后只拔长两端小台阶,中间段再有变形,易产生粗晶,各部位组织差异大。
10.(3)本发明在镦粗中间段时将上下两个小台阶装入工装模具,易于控制两端小台阶与大直径中间段的同轴度,可校正各段台阶的同轴度,常规工艺无法校正同轴度。
11.(4)因本产品材料为不锈钢,材质塑性差,易开裂,常规工艺在号印拔两端小台阶时,因台阶落差大,极易在台阶根部产生裂纹;而本发明的各次变形量小,可避免裂纹的产生,提高产品质量。
附图说明
12.图1为台阶轴的结构示意图。
13.图2为对比例1的变形过程示意图。
14.图3为对比例1的次品示意图。
15.图4为本发明的实施例1的工艺过程示意图。
16.图5为本发明的实施例2的变形过程示意图。
17.图6为本发明的实施例3的变形过程示意图。
18.图7为本发明的实施例4的锻件示意图。
19.其中:台阶轴1、中间段11、小台阶12、上模2、下模3。
具体实施方式
20.为更好地理解本发明的技术方案,以下将结合相关图示作详细说明。应理解,以下具体实施例并非用以限制本发明的技术方案的具体实施态样,其仅为本发明技术方案可采用的实施态样。需先说明,本文关于各组件位置关系的表述,如a部件位于b部件上方,其系基于图示中各组件相对位置的表述,并非用以限制各组件的实际位置关系。
21.实施例1:参见图4,图4绘制了一种高质量轴类锻件立式锻造工艺的工艺过程示意图。如图所示,本实施例1的一种高质量轴类锻件立式锻造工艺,生产产品为台阶轴1,台阶轴1包括中间段11以及两端的小台阶12,中间段11的长度为570mm、直径为845mm,小台阶12的长度为800mm、直径为350mm,其工艺流程包括以下内容:步骤一、出坯:出坯时坯料直径做到φ580mm,由此号印出坯时的最小长度可以变小,不必再增加额外辅料;步骤二、号印两端小台阶12;步骤三、预拔两端小台阶12,保留最后一火次的变形量,预留锻造比大于1.5;步骤四、将预制坯锻件竖立,两端小台阶12放进模具内,上部的小台阶12放入上模2中,下部的小台阶12放入下模3中;上模2和下模3结构相同,均为圆环形模具,圆环的中心孔的直径略大于预制坯锻件的小台阶12的直径;
步骤五:用压机将预制坯锻件竖向镦粗,使中间段11变粗,直径达到锻件的设计尺寸;步骤六、脱模;步骤七、脱模后将两端小台阶12再次按锻件的设计尺寸拔长成型到位。
22.本实施例1的锻件的下料重量为4.5t。
23.实施例2:参见图5,图5绘制了一种高质量轴类锻件立式锻造工艺的工艺过程示意图。如图所示,本实施例2生产主轴,产品成型尺寸为:中间段的长度为510mm、直径为805mm,小台阶的长度为567.5mm、直径为290mm,其工艺流程包括以下内容:第一火次在 1170℃的始锻温度下,锯除钢锭水口,在 900℃ 的终锻温度以上锭身周面轻压约20-30mm,倒八方,小变形镦粗后回炉;第二火次再将锻件加热到 1180℃的始锻温度,将锻件回炉加热出炉转至镦粗漏盘镦粗,在 900℃ 的终锻温度以上镦粗至800mm高,拔长到670mm八方;第三火次再将锻件回炉加热到 1180℃的始锻温度,出炉转至镦粗漏盘镦粗,在 900℃ 的终锻温度以上镦粗至800mm高,拔长到620mm八方;号印,拔两端小台阶;第四火次再将锻件回炉加热到 1180℃的始锻温度,将锻件竖立,将两端小台阶分别放入上模和下模中,在 900℃ 的终锻温度以上用压机竖向镦粗,使中间段变粗,直径达到锻件的设计尺寸;脱模后滚圆;最后拔长两端小台阶,达到锻件的设计成型尺寸。
24.实施例3:参见图6,图6绘制了一种高质量轴类锻件立式锻造工艺的工艺过程示意图。如图所示,本实施例3生产主轴,产品成型尺寸为:中间段的长度为480mm、直径为670mm,小台阶的长度为407.5mm、直径为265mm,其工艺流程包括以下内容:第一火次电渣钢锭热送,在 1170℃的始锻温度下,锻件锭身周面轻压约20-30mm,在 900℃ 的终锻温度以上,小端凹坑局部镦压镦平,小变形镦平后回炉;第二火次再将锻件回炉加热到 1180℃的始锻温度,出炉转至镦粗漏盘镦粗,在 900℃ 的终锻温度以上镦粗至850mm高,拔长到630mm八方;第三火次再将锻件回炉加热到 1180℃的始锻温度,出炉转至镦粗漏盘镦粗,在 900℃ 的终锻温度以上镦粗至800mm高,拔长到φ620mm;第四火次
再将锻件回炉加热到 1180℃的始锻温度,出炉后号印,号印时压下深度约40-50mm,在 900℃ 的终锻温度以上拔两端小台阶;第五火次再将锻件回炉加热到 1180℃的始锻温度,将锻件竖立,将两端小台阶分别放入上模和下模中,在 900℃ 的终锻温度以上用压机竖向镦粗,使中间段变粗,直径达到锻件的设计尺寸;脱模后滚圆;最后拔长两端小台阶,达到锻件的设计成型尺寸。
25.实施例4:参见图7,图7绘制了一种高质量轴类锻件立式锻造工艺的工艺过程示意图。如图所示,本实施例4生产齿轴,产品成型尺寸为:中间段的长度为510mm、直径为1044mm,一端的小台阶的长度为1100mm、直径为351mm,另一端的小台阶的长度为673mm、直径为444mm,其工艺流程包括以下内容:第一火次在 1200℃的始锻温度下,将钢锭锻件压把、倒棱、剁冒口,然后在 850℃ 的终锻温度以上镦粗至900mm高,拔长800mm八方;第二火次将锻件回炉加热至1200℃的始锻温度后出炉转至镦粗漏盘镦粗,然后在 850℃ 的终锻温度以上镦粗至900mm高,拔圆至直径为φ800mm,两端出坯拔直径φ500mm,长度为850mm;第三火次将锻件回炉加热至1200℃的始锻温度后出炉,将锻件竖立,将两端小台阶分别放入上模和下模中,然后在 850℃ 的终锻温度以上用压机竖向镦粗,使中间段变粗,直径达到锻件的设计尺寸;脱模后滚圆;最后拔长两端小台阶,达到锻件的设计成型尺寸。
26.对比例1:参见图2和图3,图2绘制了对比例1的变形过程示意图。如图所示,对比例1的工艺方法包括以下内容:步骤一、做锻造比:计算拔长两端小台阶,号印长度不到200mm,远远小于直径的1/2,故按常规锻造方法,需把出坯长度延长到坯料直径的1/2,因此两端小台阶需额外增加辅料锻造;步骤二、出坯:按实施例1的产品尺寸出坯,坯料直径为φ845mm;步骤三、两端号印分料;步骤四、拔出两端直径小的台阶;按本对比例1的方法生产,锻件下料重量需要6.5t,实施例1所需锻件下料重量比对比例1少2t。
27.以上仅是本发明的具体应用范例,对本发明的保护范围不构成任何限制。凡采用等同变换或者等效替换而形成的技术方案,均落在本发明权利保护范围之内。
再多了解一些
本文用于企业家、创业者技术爱好者查询,结果仅供参考。