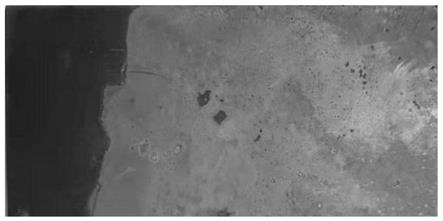
1.本发明属于高温化学气相沉积(htcvd)金属表面改性技术领域,涉及一种高温防渗金属涂料,具体涉及一种水性防渗铝涂料及基于化学气相沉积的部分渗铝改性方法。
背景技术:
2.在舰船、发电燃气涡轮轮机,航空发动机等一些精密零部件是耐高温镍(钴)基合金材料,需要采用高温化学气相沉积(htcvd)工艺进行金属表面渗铝改性处理。这部分零件一般在高温、高速的严酷苛刻工况下运行,进行渗铝改性后提高零件表面的抗氧化性和耐蚀性、延长零件的使用寿命。有些零件局部不需要渗铝改性,否则影响零件局部性能,而高温化学气相沉积一般都是无差别的沉积,因此需要提前对不需要渗铝改性的零件部位进行遮蔽,遮蔽涂层要求能够适应高温化学气相沉积(htcvd)渗铝工艺温度范围700~1100℃,还要不对零件本身造成损害,特别是高温化学气相沉积结束后,要能方便快捷的去掉遮蔽涂层,以便零件正常使用。
3.目前市面上出现的防渗铝涂料主要适用于包埋法、气体法渗铝工艺,而且现有防渗铝涂料含有碳、磷、硫等元素,防渗铝涂料涂层较厚,会对零件表面产生不利影响,因此需要开发一种针对高温化学气相沉积法的防渗铝涂料。
4.高温化学气相沉积(htcvd)渗铝工艺温度范围700~1100℃,前驱体媒介包含载气、还原气体、促进气体、以及活性渗铝剂等组成,针对高温化学气相沉积渗铝工艺设计了防渗铝水性涂料,应具有无毒环保,不含有碳、磷、硫等对零件表面不利元素的特点,选用渗铝工艺过程中不易发生分解的无机材料,在高温条件下不起皱、不流挂、粘结性好易剥落,不影响渗铝组态气氛,涂层较薄易于清理。
技术实现要素:
5.本发明针对高温化学气相沉积(htcvd)工艺,提供一种具有环保性的水性防渗铝涂料,涂料中不含对零件表面性能不利的碳、磷、硫元素,该水性防渗铝涂料对零件表面的附着力好、易自干或烘干,涂覆在零件表面时能够在高温条件下不起皱、不流挂、粘结性好,在渗铝过程中不易分解,不影响渗铝气氛,易于喷水或喷砂清理。
6.为了解决上述技术问题,本发明采用的技术手段如下:
7.一种用于高温化学气相沉积工艺的水性防渗铝涂料,其特征在于:由石英粉、刚玉粉、钛白粉、屏蔽剂粉、液体硅酸钠盐和水混合组成。
8.优选的,所述水性防渗铝涂料中各组分按照质量分数如下:
9.石英粉10.0~15.0%,刚玉粉6.0~12.0%,钛白粉10.0~20.0%,屏蔽剂粉10.0~30.0%,液体硅酸钠盐20.0~40.0%,其余量为去离子水。
10.优选的,所述石英粉、刚玉粉、钛白粉和屏蔽剂粉的粒度参数如下:石英粉400~600目,刚玉粉400~600目,钛白粉400~600目,屏蔽剂粉400~600目。
11.优选的,所述液体硅酸钠盐的模数为2.2~2.6。
12.优选的,所述屏蔽剂粉为铬镍合金粉。
13.优选的,所述铬镍合金粉中金属铬含40.0~60.0%。
14.优选的,所述铬镍合金粉中金属铬含量为50.0%。
15.优选的,水性防渗铝涂料的各组分混合搅拌均匀后涂料粘度为35s~60s,该粘度可以良好的挂膜。
16.一种利用上述水性防渗铝涂料的部分渗铝改性方法,其特征在于,包括以下步骤:
17.步骤1、根据水性防渗铝涂料的组成,将各组分充分混合,并搅拌均匀待用;
18.步骤2、清理待改性零件的表面;
19.步骤3、在零件不需要渗铝改性的区域涂覆步骤1中制备的水性防渗铝涂料;
20.步骤4、将步骤3中涂覆水性防渗铝涂料的零件在烘箱中烘干,形成防渗铝涂层;
21.步骤5、将烘干后的零件按照高温化学气相沉积工艺进行渗铝改性;渗铝工艺温度可在700~1100℃间连续调控。
22.步骤6、渗铝改性完成后,利用软质材料敲击防渗铝涂层,使其剥落;
23.步骤7、采用喷水或喷砂工艺去掉残余防渗铝涂层,完成零件部分渗铝改性加工。
24.优选的,步骤1中,搅拌均匀约20~30分钟,捡测涂料粘度在35s~60s之间。
25.优选的,步骤2中,所述清理包括脱脂和去氧化皮处理。
26.优选的,步骤3中,水性防渗铝涂料的涂刷厚度为0.3~0.6mm,涂刷方式为涂刷或喷涂。
27.优选的,步骤4中,烘干温度为110~130℃。
28.优选的,步骤6中,采用橡胶棒轻击即可剥落防渗铝涂层。
29.优选的,步骤7中,喷水压力0.4~0.6mpa(如果采用喷砂处理,则喷砂压力0.2~0.3mpa,刚玉砂120~180目),喷口距表面8~12cm,入射方向与表面夹角15~30
°
。
30.本发明有益效果如下:
31.本发明水性防渗铝涂料不含碳、磷、硫等会对零件表面产生不利影响的元素,涂层能够耐受高温化学气相沉积工艺的高温,并且后续剥落容易,不损失零件表面。本发明部分渗铝改性方法能对零件进行局部选择性渗铝改性,大大降低了渗铝改性对零件性能的影响,提高了渗铝改性的应用范围。
附图说明
32.图1为本发明实施例中试片(100
×
50)右侧部分涂刷水性防渗铝涂料,进行高温化学气相沉积工艺渗铝处理,清洗水性防渗铝涂料后外观状态。
33.图2为本发明实施例中零件试样没有涂刷水性防渗铝涂料,进行高温化学气相沉积工艺渗铝处理后观察显微金相组织,左边为试样内部金相组织,中间窄带为有渗铝层,右边为镶嵌试样的镶嵌料。
34.图3本发明实施例中为零件试样涂刷了水性防渗铝涂料,进行高温化学气相沉积工艺渗铝处理后观察显微金相组织,左边为试样内部金相组织,右边为进行镶嵌试样的镶嵌料,界限分明,没有渗铝层。
具体实施方式
35.依据下述实施例,操作技术人员可以更好地理解本发明,实施例所描述的内容进一步详细说明本发明。
36.实施例1
37.本发明用于高温化学气相沉积工艺的水性防渗铝涂料,由如下质量数成分比配制而成:石英粉12.0%、600目,刚玉粉10.0%、600目,钛白粉20.0%、600目,屏蔽剂粉(铬镍合金粉)20.0%、500目,液体硅酸钠盐30.0%、模数2.6,其余量为去离子水(8%)。
38.利用水性防渗铝涂料的部分渗铝改性方法,包括如下步骤:
39.步骤1、根据水性防渗铝涂料的组成,将各组分充分混合,并搅拌均匀待用;搅拌均匀约25分钟,捡测涂料粘度为40s~50s。
40.步骤2、清理待改性零件的表面;所述清理包括脱脂和去氧化皮处理。
41.步骤3、在零件不需要渗铝改性的区域涂覆步骤1中制备的水性防渗铝涂料;水性防渗铝涂料的涂刷厚度为0.3~0.6mm,涂刷方式为涂刷。
42.步骤4、将步骤3中涂覆水性防渗铝涂料的零件在烘箱中烘干,形成防渗铝涂层;
43.步骤5、将烘干后的零件按照高温化学气相沉积工艺进行渗铝改性;渗铝工艺温度可在700~1100℃间连续调控。
44.步骤6、渗铝改性完成后,利用橡胶棒轻击防渗铝涂层,使其剥落;
45.步骤7、采用喷水或喷砂工艺去掉残余防渗铝涂层,完成零件部分渗铝改性加工,喷水压力0.4~0.6mpa,喷口距表面8~12cm,入射方向与表面夹角15~30
°
。
46.实施例2
47.本发明用于高温化学气相沉积工艺的水性防渗铝涂料,由如下质量数的成分配制而成:石英粉10.0%、400目,刚玉粉8.0%、400目,钛白粉15.0%、400目,屏蔽剂粉(铬镍合金粉)25.0%、400目,液体硅酸钠盐36.0%、模数2.3,其余量为去离子水(6%)。捡测涂料粘度为50s~60s。
48.部分渗铝改性方法与实施例1相同。
49.实施例3
50.本发明用于高温化学气相沉积工艺的水性防渗铝涂料,由如下质量数的成分配制而成:石英粉15.0%、400目,刚玉粉10.0%、400目,钛白粉10.0%、400目,屏蔽剂粉(铬镍合金粉)15.0%、400目,液体硅酸钠盐40.0%、模数2.3,其余量为去离子水(10%)。捡测涂料粘度为35s~45s。
51.部分渗铝改性方法与实施例1相同。
52.将实施例中水性防渗铝涂料按照部分渗铝改性方法中的步骤涂覆在试片(100
×
50)上部分区域,并进行高温化学气相沉积(htcvd)渗铝处理,清理水性防渗铝涂料后外观状态,如图1所示,可知对原零件表面呈现本体色泽,保持原貌。
53.将试样没有涂覆水性防渗铝涂料,进行高温化学气相沉积(htcvd)渗铝处理后观察显微金相组织,如图2所示,左边为试样内部金相组织,中间窄带为有渗铝层,右边为镶嵌试样的镶嵌料。
54.将试样涂覆水性防渗铝涂料,进行高温化学气相沉积(htcvd)渗铝处理后观察显微金相组织,如图3所示,左边为试样内部金相组织,右边为镶嵌试样的镶嵌料,界限分明,
没有渗铝层。
55.以上实施方式仅用于说明本发明,而非对本发明的限制。尽管参照实施例对本发明进行了详细说明,本领域的普通技术人员应当理解,对本发明的技术方案进行各种组合、修改或者等同替换,都不脱离本发明技术方案的精神和范围,均应涵盖在本发明的权利要求范围当中。
再多了解一些
本文用于企业家、创业者技术爱好者查询,结果仅供参考。