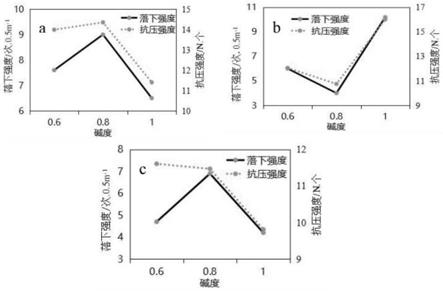
1.本发明涉及球团矿领域,具体为一种生石灰碱性球团及其制备工艺。
背景技术:
2.钢铁是现代社会最重要的原材料之一,其质量和产量往往是一个国家发达程度 和经济实力的重要标志,是国民经济的支柱产业。2019年全球粗钢产量达18.699 亿吨,中国粗钢产量为9.9634亿吨,占比达53%。
3.高炉炼铁是整个钢铁冶炼流程中的一个关键环节,而球团矿是现代高炉冶炼不 可或缺的原料,也是行业内普遍认可的理想高炉炉料结构中的一部分。随着高炉逐 渐向大型化、现代化发展,对高炉炉料结构和质量的要求也越来越高。
4.为保证正常生产,烧结需生产超高碱度烧结矿(r=2.7
±
)。当烧结矿碱度超过 一定值后,粒度细化、强度变差,对烧结矿质量影响很大。为此,降低烧结矿碱度, 生产碱性球团矿,增加球团矿的入炉比例,对改善高炉综合炉料的冶金性能,对增 产节焦降本具有现实和深远的意义。
技术实现要素:
5.本发明为了解决现有技术中存在的缺陷,提供一种抗压强度高、含粉率低、低 温还原粉化性能好、还原性能好、还原膨胀性能好的生石灰碱性球团及其制备工艺。
6.本发明首先提供一种生石灰碱性球团,包括:铁精矿、除尘灰、膨润土、熔剂; 其中铁精矿包含龙蟒精矿、康茂精矿、安宁精矿、太和精矿;铁精矿中龙蟒精矿: 康茂精矿:安宁精矿:太和精矿为1-4:1-6:1-4:1-7;除尘灰配比为总质量的1%-3%; 膨润土配比为总质量的1%-4%;熔剂为生石灰;所述生石灰碱性球团的碱度为 0.5-1.0。
7.本发明还提供如下优化方案:
8.优选的,除尘灰配比为总质量的1.8%。
9.优选的,膨润土配比为总质量的1.5%-2.0%。
10.本发明还公开了一种上述的生石灰碱性球团的制备工艺,包括如下步骤:
11.s1配置生石灰碱性球团配料;
12.s2加水混合造球筛分出合格生球;
13.s3对生球进行干燥;
14.s4将生球进行预热和焙烧;
15.s5将焙烧后的生球均热和冷却得到成品。
16.本发明还提供如下优化方案:
17.优选的,步骤s3中干燥的温度为200-500℃。
18.优选的,步骤s4中预热的温度为900-1000℃。
19.优选的,步骤s4中焙烧的温度为1200-1300℃。
20.优选的,步骤s5中均热温度为1100-1200℃。
21.优选的,步骤s5中冷却时间为40-60分钟。
22.优选的,步骤s5中冷却时间为炉内加炉外的冷却时间。
23.本发明对生石灰为熔剂的碱性球团实验进行了配料、造球、生球性能检测、生 球焙烧等作业,并对成品球团矿的抗压强度、含粉率、低温还原粉化性能、还原性 能和还原膨胀性能进行检测分析,得出如下结论:
24.(1)三种碱度、三种膨润土含量条件下,生球落下强度均达到4.0次/(0.5m
·
p) 以上,抗压强度均达到10n/p以上,爆裂温度在380℃以上;
25.(2)膨润土用量1.5%的生球性能相对较差,膨润土用量2%的生球爆裂温度明 显高于另外两种膨润土用量的;
26.(3)同一膨润土用量,碱度越大时,成品球团矿抗压强度越低(q061、q053除 外);
27.(4)同试样类在不同制度下焙烧,第3制度6个样的抗压强度最高(q043、 q063、q073除外),第3制度的含粉率最低(q083除外),第3制度的rdi 3.15 最大(q063除外);其次为第1制度的,第2制度的最差;
28.(5)膨润土用量一定时,第3制度球团矿的rdi 3.15与碱度基本呈反向关 系;膨润土用量2%、第1或第2制度时,这种反向关系仍然能够保持;但随着膨 润土用量降低,第1或第2制度,碱度0.8却成为rdi 3.15的一个拐点,或为 峰值,或为谷值;
29.(6)第3制度球团矿的还原度指数均达到60%以上,波动较小,且碱度1.0的 球团矿还原度指数最大;
30.(7)三种焙烧制度的球团矿其自由膨胀指数均低于15%;
31.(8)碱度0.8、膨润土用量1.5%、第1焙烧制度为以生石灰为熔剂的碱性球 团生产工艺参数。但第1制度的预热温度、焙烧温度均比第3制度的低,为满足 要求的下限制度,生产中须严格控制好预热温度和焙烧温度。同时碱度0.8的碱性 球团也优化了高炉炉料结构,降低了烧结矿碱度,在生产上更有使用价值和现实意 义。
附图说明
32.图1为碱度对生球强度的影响图;
33.图2为膨润土用量对生球强度的影响图;
34.图3为不同焙烧制度下的各试样低温还原粉化指数rdi 3.15图;
35.图4为第1焙烧制度球团矿rdi 3.15与碱度、膨润土用量之间的关系图;
36.图5为第2焙烧制度球团矿rdi 3.15与碱度、膨润土用量之间的关系图;
37.图6为第3焙烧制度球团矿rdi 3.15与碱度、膨润土用量之间的关系图;
38.图7为第1焙烧制度下球团矿的自由膨胀指数vfs与膨润土含量和碱度的关 系图;
39.图8为第2焙烧制度下球团矿的自由膨胀指数vfs与膨润土含量和碱度的关 系图;
40.图9为第3焙烧制度下球团矿的自由膨胀指数vfs与膨润土含量和碱度的关 系图。
具体实施方式
41.为了使本领域的技术人员更好地理解发明的技术方案,下面结合具体实施方式 对本发明作进一步的详细说明。
42.本发明首先提供一种生石灰碱性球团,包括:铁精矿、除尘灰、膨润土、熔剂; 其中
铁精矿包含龙蟒精矿、康茂精矿、安宁精矿、太和精矿;铁精矿中龙蟒精矿: 康茂精矿:安宁精矿:太和精矿为1-4:1-6:1-4:1-7;除尘灰配比为总质量的1%-3%; 膨润土配比为总质量的1%-4%;熔剂为生石灰;所述生石灰碱性球团的碱度为 0.5-1.0。
43.本发明还提供如下优化方案:
44.优选的,除尘灰配比为总质量的1.8%。
45.优选的,膨润土配比为总质量的1.5%-2.0%。
46.本发明还公开了一种上述的生石灰碱性球团的制备工艺,包括如下步骤:
47.s1配置生石灰碱性球团配料;
48.s2加水混合造球筛分出合格生球;
49.s3对生球进行干燥;
50.s4将生球进行预热和焙烧;
51.s5将焙烧后的生球均热和冷却得到成品。
52.本发明还提供如下优化方案:
53.优选的,步骤s3中干燥的温度为200-500℃。
54.优选的,步骤s4中预热的温度为900-1000℃。
55.优选的,步骤s4中焙烧的温度为1200-1300℃。
56.优选的,步骤s5中均热温度为1100-1200℃。
57.优选的,步骤s5中冷却时间为40-60分钟。
58.优选的,步骤s5中冷却时间为炉内加炉外的冷却时间。
59.上述为本发明的详细阐述,下面为本发明实验方案。
60.配料要求
61.对配合料的要求为:
62.龙蟒、康茂、安宁、太和四种铁精矿配料时各占1/4;
63.除尘灰配比:1.8%;
64.碱度:0.6、0.8、1.0;
65.膨润土配比:1.5%、1.8%、2.0%;
66.熔剂:分别采用生石灰、石灰石。先进行以生石灰为熔剂的碱性球团实验,寻找 出最佳碱度值,再以此最佳碱度值进行以石灰石为熔剂的碱性球团实验。
67.焙烧制度
68.生球在焙烧过程中采用三种不同焙烧制度进行焙烧。考虑成品球s含量(焙烧过 程脱硫率)和feo含量(成品球氧化度)及属于含mgo的钒钛磁铁矿焙烧,在查阅文 献及前期探索实验的基础上采用表1所示的焙烧制度进行焙烧。
[0069][0070]
表1焙烧制度
[0071]
实验方案
[0072]
据配料要求和焙烧制度拟定实验方案如表2所示。其中,试样号为试样类 焙烧制 度号。以生石灰为熔剂的试样类共9个,每个试样类分别在3种焙烧制度下进行焙 烧,得到27个成品球团矿试样。然后根据这27个试样的物理性能和冶金性能的检 测结果,确定最佳碱度值。再据此碱度确定以石灰石为熔剂在配料时需要添加的石灰 石用量和铁精矿用量。以石灰石为熔剂的试样类共3个,每个试样类分别在3种焙 烧制度下进行焙烧,得到9个成品球团矿试样,进行物理性能和冶金性能的检测。
[0073]
[0074][0075]
表2实验方案
[0076]
实验指标及其检测
[0077]
成品球团矿是高炉的顺气丸,它的质量对高炉冶炼过程有重要影响。而质量好的 生球又是获得高产、优质球团矿的先决条件。因此,本项目在碱性球团矿生产过程中 对生球性能和成品球团矿性能均作了检测。生球性能主要包括落下强度、抗压强度和 爆裂温度,成品球团矿性能主要包括抗压强度、含粉率、低温还原粉化性能、还原性 能和还原膨胀性能。
[0078]
生球性能
[0079]
质量好的生球要求具有适宜而均匀的粒度,足够的落下强度和抗压强度及良好的 耐热性,以保证其在转运、筛分、布料、干燥过程中不破裂、变形。
[0080]
生球落下强度
[0081]
生球落下强度是衡量生球在转运过程中能够承受冲击能力大小的重要指标,也是 球团厂设计时允许生球转运次数的依据。随机取10个生球,分别将每个生球自0.5m 高度自由落下至10mm厚的钢板上,记录每个生球产生裂纹或碎裂时的落下次数。取 10个球测定的平均值作为生球的落下强度指标。
[0082]
生球抗压强度
[0083]
生球抗压强度反映生球在转运、堆积过程中承受球层自重和挤压的能力。随机取 20个球,将生球置于电子天平上,用直径为150mm的平盘匀速加压,直到生球发生 破裂,记录此时电子天平所显示的压力值,视为生球的抗压强度。取20个球测定, 测定的平均值作为生球抗压强度指标。
[0084]
生球爆裂温度
[0085]
爆裂温度是评价生球质量的一个重要指标,对球团生产尤其是竖炉球团生产至关 重要(目前球团生产有三种形式:竖炉、带式焙烧机和链箅机-回转窑)。对于带式焙 烧机和链箅机-回转窑工艺,可以根据生球的热敏感性选择合适的干燥工艺。提高生 球的爆裂温度可以减少生球在竖炉干燥床上的爆裂,改善竖炉内球层透气性,减少结 瘤结块事故,可以强化带式焙烧机与链箅机-回转窑的干燥过程。爆裂温度愈高愈有 利于加速干燥过程。
[0086]
如果生球爆裂温度低,干燥时其结构受到破坏,使球层透气性恶化,给预热焙烧 带来困难,最终导致生产率降低,成品球质量不均匀,严重时会导致结圈(链箅机
‑ꢀ
回转窑工艺)等问题。生球爆裂温度与原料性能、粘结剂性能、造球工艺参数、干燥 制度等有关,所以每一次原料变化、造球工艺参数变化、干燥温度和干燥气流速度变 化都需要测定相应生球的爆裂温度,从而调整工艺参数,保证生球在干燥过程中不产 生爆裂,以得到良好质量的球团矿。
[0087]
球团矿抗压强度
[0088]
抗压强度是表示球团矿冷态度的重要指标,指其在受压条件下完全破裂时所对应 的压力大小。
[0089]
①
标准
[0090]
参照《高炉和直接还原用铁矿球团抗压强度的测定》(gb/t 14201-2018)。
[0091]
②
实验设备
[0092]
铁矿球团压力检测机。
[0093]
③
实验过程
[0094]
随机取60个球团矿试样,在烘箱(105
±
5℃)中干燥,并在实验前冷却至室温。 把一个试样(单个球)放在下压板的中心处,整个实验期间以15mm/min的速度向下压 上压板,给试样施加负荷。记下试样在负荷作用下完全破裂时的最大负荷量,用(decanewtons)为单位,结果精确到一位小数。
[0095]
球团矿含粉率
[0096]
目前用球团法处理铁精矿,将其制成球团矿用于高炉冶炼。球团矿在筛分、转运、 进仓过程中经受摩擦、冲击,其含粉率不可避免地再次提高,经检测,目前国内球团 矿在仓内的含粉率一般在20%~35%之间,最高近60%,而一座4350m3的大型高炉每 日所需球团矿量在3000kg
±
,高炉每日将吃进大约1000kg的球团矿粉,加之高炉 所需块矿的含粉率也较高,这些矿粉密实度高、透气性差,影响高炉料柱透气性,对 高炉生产造成一定的负面影响。因此降低球团矿的含粉率无疑成为保证高炉生产稳 定、顺行、高产的一项重要措施。
[0097]
①
标准
[0098]
没有统一标准。
[0099]
②
实验设备
[0100]
转鼓(φ130
×
200)。
[0101]
③
实验过程
[0102]
将焙烧好的球团矿称取500g,放入转鼓中,盖好端盖,以30r/min的转速转动 10分钟。停止后,从转鼓中取出所有试样,用筛孔为5mm和0.5mm的筛子进行筛分, 称取筛上物的重量,计算含粉率。
[0103]
成品碱性球团矿冶金性能
[0104]
球团矿低温还原粉化性能
[0105]
高炉炼铁过程中,当铁矿石进入高炉下降到400~600℃的区间时,在这里它受到 来自高炉下部煤气的还原作用,会发生不同程度的碎裂粉化,严重时则影响高炉上部 料柱的透气性,破坏炉况顺行。铁矿石在低温(400~600℃)还原过程中发生碎裂粉化 的特性通常用低温还原粉化指数(rdi)来表示。
[0106]
实验过程
[0107]
使用瓶装高纯co、co2、n2配制还原气体。试样在105
±
5℃的温度下烘干,烘 干时间超过2h,然后冷却至室温。称取500g试样放入还原管,通入标态流量为 5l/min的n2,并置于还原炉内(炉内温度<200℃)。升温,速度控制在10℃/min以 内,当温度为500℃时,增大n2流量到15l/min,在500℃恒温30min,使温度恒 定在500
±
5℃之间。然后通入15l/min
±
0.5l/min标态流量的还原气体以代替n2, 连续还原1h。还原1h后,改通n2,标态流量为5l/
min,并将还原管提出炉外。 待试样冷却至100℃以下,取出试样,放入转鼓,以30
±
1r/min的转速共转300转, 倒出,再用筛孔为6.30mm、3.15mm和0.5mm的筛子筛分60s,并称量。
[0108]
球团矿还原性能
[0109]
铁矿石还原性能的好坏直接影响着高炉炼铁的产量和焦比等技术经济指标。铁矿 石还原性能表征铁矿石中与铁结合的氧被气体还原剂夺取的难易程度,是铁矿石的一 种重要冶金性能,以180min的还原度作为考核指标,用ri表示。
[0110]
实验过程
[0111]
使用瓶装高纯co、n2配制还原气体。试样在105
±
5℃的温度下烘干,烘干时间 超过2h,然后冷却至室温。称取500g试样放入还原管,通入标态流量为5l/min的 n2,并置于还原炉内(炉内温度<200℃)。升温,速度控制在10℃/min以内,当温 度为900℃时,增大n2流量到15l/min,在900℃恒温30min,使温度恒定在 900
±
5℃之间。然后通入15l/min
±
0.5l/min标态流量的还原气体以代替n2,连续 还原3h。还原3h后,改通n2,标态流量为15l/min,5min后关闭n2,并将还原 管提出炉外,实验结束。
[0112]
球团矿还原膨胀性能
[0113]
还原膨胀性能是指球团矿在还原过程中产生体积膨胀的性能。它是球团矿的一种 重要冶金特性。通常以球团矿在高炉中温区还原前后体积变化的百分率作为还原膨胀 性能的指标。
[0114]
由膨胀指数vfs
[0115]
将粒度为10.0~12.5mm的球团矿取18个置于固定床中,通入15l/min由 30%co和70%n2组成的还原气体,在900℃下还原1h使其自由膨胀,然后冷却至室 温。用还原前后球团矿的体积变化率表征其自由膨胀指数vfs。
[0116]
实验结果
[0117]
生球性能检测结果及分析
[0118]
生球性能的检测结果如表3所示。
[0119]
由表3可知,q03、q05、q09类生球的落下强度仅稍大于4次/(0.5m
·
p),较低。
[0120]
据此,以生石灰为熔剂的碱性球团生产工艺参数不能选择q05、q03、q09类所 对应的参数。
[0121]
[0122]
表3生球性能
[0123]
碱度对生球性能的影响
[0124]
生球强度随碱度的变化如图1所示。由图1可知,膨润土用量为2%和1.5%时, 生球落下强度在碱度0.8时最大,且膨润土含量高,落下强度大;而膨润土用量为 1.8%时,碱度1.0的生球落下强度最高,平均达到10.2次/(0.5m
·
p)。抗压强度呈 现类似的趋势,膨润土为2%、碱度为0.8的生球其抗压强度达到14.35n/p;膨润 土为1.8%、碱度为1.0的生球其抗压强度达到16.02n/p;膨润土为1.5%时,三种 碱度的抗压强度随碱度增大呈现下降的趋势。
[0125]
膨润土用量对生球性能的影响
[0126]
生球强度与膨润土用量的关系如图2所示。由图2可知,碱度0.6时,生球的 强度随膨润土用量的增加呈现增大的趋势;碱度0.8时,膨润土用量为1.8%的生球 强度最差;当碱度达到1.0时,最大强度出现于膨润土用量为1.8%的生球。但不管 何种碱度,何种膨润土用量,落下强度均能达到4.0次/(0.5m
·
p)以上,抗压强度均 能达到10n/p以上。
[0127]
由表3可知,膨润土用量为2%的生球爆裂温度明显高于另外两种膨润土用量的生 球,生球的最低爆裂温度为380℃。
[0128]
膨润土具有高分散度,添加后可改善造球原料的粒度组成,减小球团内毛细管径, 增大毛细力。另外膨润土具有较好的亲水性,吸水后成为胶体状态,填充在铁精矿颗 粒之间,增加了颗粒之间的粘结力,使强度增大。生球爆裂温度的升高主要是由于膨 润土降低生球中水分的蒸发速度,提高了干球强度。
[0129]
成品碱性球团矿物理性能检测结果及分析
[0130]
成品球团矿的抗压强度和含粉率检测结果如表4所示。
[0131][0132]
表4球团矿的物理性能
[0133]
抗压强度检测结果分析
[0134]
由表4可知,三种不同的焙烧制度对球团矿的抗压强度影响较大。三种焙烧制度 中第3制度预热温度970℃、预热时间20min,焙烧温度1260℃,焙烧时间为22min; 第1制度预热温度950℃,预热时间20min,焙烧温度1230℃,焙烧时间25min; 第2制度预热温度930℃、预热时间20min,焙烧温度1200℃,焙烧时间30min。 第3制度焙烧出的球团矿抗压强度最高,均在2000n/p以上,有7个试样的抗压 强度达到2300n/p以上;第1制度焙烧出的球团
矿抗压强度比第3制度焙烧出的略 低,但也只有1个试样的抗压强度低于2000n/p,达到2300n/p以上的试样有5 个,值得一提的是,该制度下的最高抗压强度超过了3000n/p;第2制度焙烧出的 球团矿其抗压强度最差,9个试样中8个试样的强度不能达到1950n/p。这说明在 原料成分一定的情况下,焙烧制度中,预热温度尤其焙烧温度对球团矿抗压强度影响 较大,预热时间、焙烧时间影响相对较小。
[0135]
磁铁精矿球团焙烧固结过程中主要是磁铁矿晶粒氧化后生成赤铁矿微晶,然后发 展为赤铁矿连晶,这种赤铁矿连晶联接紧密,分布均匀,结构力较强,能够保证球团 矿具有较高的强度。当预热温度尤其焙烧温度较低时,球团内部的物理化学变化进行 得不充分,磁铁矿晶粒氧化及其后续结晶发育不够完善,焙烧固结的效果不佳,导致 球团矿强度下降;当预热温度、焙烧温度较高时,磁铁矿晶粒氧化及后续赤铁矿微晶 的生长及长大加快,固结更加充分,并有利于球团内部液相的生成和流动,从而促进 了球团内部颗粒之间的联接,提高了球团矿强度。但当焙烧温度超过一定值后,球团 外层fe2o3快速再结晶,影响气体向球团内部扩散,致使球团中心的fe3o4氧化不完 全,反应不充分,而且fe2o3分解也会影响再结晶过程,从而使球团矿强度降低。此 外,球团矿焙烧时,球团内部的固相扩散和反应均需要足够的高温保持时间(预热时 间 焙烧时间)。只有达到足够长的高温保持时间,固相固结时结晶的发展和完善才可 能充分完成,才能保证球团矿形成比较理想的均质结构。高温保持时间特别是焙烧时 间过短或过长,都会导致球团矿强度下降。值得注意的是,如果预热温度、焙烧温度 不够,即使预热时间与焙烧时间足够长,也不可能达到理想的固结效果,这也是第2 制度球团矿抗压强度差的原因。
[0136]
当膨润土用量较高(1.8%、2%)时,基本遵循碱度越大,强度越低的规律;当膨润 土用量降低到1.5%时,第1焙烧制度、碱度0.8的球团矿抗压强度反而最大。随 着碱度的增大,球团矿中的cao含量增加,导致在焙烧过程中生成了较多液相,冷 却结晶析出强度较低的硅酸盐矿物。
[0137]
含粉率检测结果分析
[0138]
本项目所产球团矿5.0mm以下的粉末较少,均低于5%,绝大部分位于2%以下, 且粒度基本为-0.5mm,含粉率能够符合生产要求。经过与球团矿抗压强度的比较得知, 含粉率的高低与抗压强度基本呈负相关关系,即强度越大,含粉率越低。因此,为满 足运输、倒料、进仓、筛分的要求,应该适当增大球团矿的抗压强度。
[0139]
成品碱性球团矿冶金性能检测结果及分析
[0140]
随着球团矿使用比例的增加,球团矿的综合性能对高炉冶炼的影响越来越重要。 不仅球团矿品位、冷态抗压强度等指标很重要,其高温冶金性能也很重要。高炉冶炼 过程整个炉料应具有足够的稳定性和透气性,尤其在高炉上部,炉料停留时间较长, 所以作为高炉主要炉料之一的球团矿,应具有良好的冶金性能,即低的自由膨胀指数、 高的还原度和还原后强度。球团矿的冶金性能与其化学成分密切相关。900℃还原性 能是基本性能,低温还原粉化、还原膨胀影响高炉中上部料柱的透气性,其冶金性能 的优劣直接影响高炉冶炼技术经济指标。
[0141]
低温还原粉化性能检测结果及分析
[0142]
以生石灰为熔剂的27个碱性球团矿样的低温还原粉化性能检测结果见表5
[0143][0144]
表5第1焙烧制度焙烧出的球团矿低温还原粉化性能检测结果
[0145][0146]
表6第2焙烧制度焙烧出的球团矿低温还原粉化性能检测结果
[0147][0148]
表7第3焙烧制度焙烧出的球团矿低温还原粉化性能检测结果
[0149]
低温还原粉化指数是铁矿石冶金性能的一项重要指标,rdi的大小直接影响铁矿 石的质量,以及高炉的操作和产量。球团矿通常具有规则的形状、均匀的粒度、较高 的抗压抗磨强度,能进一步改善高炉料柱的透气性和炉内煤气的分布,而碱性球团矿 较酸性球团矿又具有还原膨胀率降低、软熔性和还原性改善等优点,使高炉生产过程 中配加碱性球团矿成为一种发展趋势。
[0150]
由图3和表5-7,第1制度和第3制度焙烧的球团矿的低温还原粉化指标 rdi 3.15较高,位于96%~100%之间,完全能够满足高炉生产的要求,而第2制度 的rdi 3.15较低,位于68%~94%之间,9个样中只有2个样达到了90%。比较第1制 度和第3制度下的rdi 3.15,只有q061的低温还原粉化指标rdi 3.15高于q063 的,其余试样第3制度下的rdi 3.15均优于第1制度的。
[0151]
还原性能检测结果及分析
[0152]
铁矿石作为高炉炼铁的主要原料,其还原性的好坏直接影响高炉冶炼的技术经济 指标。高炉生产时,易还原的铁矿石中的氧大部分在高炉中上部被高炉煤气所夺取(间 接还原),此时焦炭消耗较少;难还原的铁矿石中相当多的氧的失去要到高炉下部依 靠碳的直接还原来完成,此时焦炭消耗较高。为了降低焦比,要求入炉铁矿石有良好 的还原性,尽可能以间接还原的方式夺取铁矿石中的氧。
[0153]
通常球团矿中feo含量低,微孔发达,有较好的还原性,更有利于高炉内还原 反应的进行。
[0154][0155]
表8球团矿还原性能检测结果(第1焙烧制度)
[0156][0157]
表9球团矿还原性能检测结果(第2焙烧制度)
[0158][0159]
表10球团矿还原性能检测结果(第3焙烧制度)
[0160]
由表8-10可见,第1焙烧制度和第3焙烧制度下,配入1.8%和2%膨润土用量 时,碱度1.0的球团矿还原度指数最大;第2制度下,配入1.5%和1.8%膨润土用 量时,碱度0.6的球团矿还原度指数最大。根据前人对矿相的研究分析表明,碱度 提高后,钛赤铁矿含量增加,钛磁铁矿含量减少,球团矿孔隙度增加,导致还原度指 数上升。
[0161]
但预热温度和焙烧温度偏低(如第2制度),各种物理化学反应进行缓慢,导致 难以达到理想的固结效果,不利于还原性能的改善。
[0162]
当膨润土用量为1.5%时,第1制度和第2制度下的碱度1.0的球团矿还原度 指数最差,而第3制度下碱度1.0的最大,说明当膨润土用量较低时,焙烧温度对 还原性能的影响更明显。
[0163]
综上分析,在预热温度尤其焙烧温度足够(如第1、第3制度)的情况下,膨润 土用量较高(1.8%和2%)时,可以选择生产碱度1.0的球团矿;当膨润土用量较低 (1.5%)时,可以选择生产碱度0.8的球团矿。
[0164]
由图4-6可见,第1和第2制度焙烧,膨润土用量2%时,碱度越高,rdi 3.15 越小。第1制度焙烧,当膨润土用量1.8%时,球团矿rdi 3.15随碱度增加(0.6、 0.8、1.0)而对应变为98.94%、98.05%、98.54%;而膨润土用量1.5%时,rdi 3.15 随碱度增加(0.6、0.8、1.0)而对应变为98.56%、99.56%、96.43%;很明显,碱度0.8 是rdi 3.15变化的一个拐点,或为谷值,或为峰值。第2制度焙烧,膨润土用量1.8% 时,球团矿rdi 3.15随碱度增加(0.6、0.8、1.0)而对应变为93.82%、84.37%、85.29%; 而膨润土用量1.5%时,rdi 3.15随碱度增加(0.6、0.8、1.0)而对应变为90.01%、 68.87%、80.49%;又很明显,碱度0.8还是rdi 3.15变化的一个拐点,但为谷值。 所以第1和第2制度下需要对该范围内的碱度和膨润土用量特别关注。第3制度 焙烧,膨润土用量较低时(1.5%和1.8%),碱度越高,rdi 3.15越小;但这种变化趋势 随膨润土用量由1.5%增至1.8%而越来越平缓;当膨润土用量增至2%时,该趋势有 所变化,但是变化值很小;三种碱度的rdi 3.15均达到了99%以上。
[0165]
由图7-9可见,当膨润土用量不同时,碱度与自由膨胀指数的关系没有明显的规 律,但值得注意的是碱度0.8的情况,或为峰值,或为谷值。当膨润土用量1.8% 或2.0%、碱
度0.8时,第1制度下球团矿的膨胀情况最小,说明在这种情况下, 预热温度尤其焙烧温度的升高或降低均会增大球团矿的体积膨胀。当膨润土用量 1.5%、碱度0.8或1.0时,第1制度下球团矿的膨胀情况最大,这也说明在这种 情况下,预热温度尤其焙烧温度的升高或降低均会减小球团矿的体积膨胀。
[0166]
以上仅是本发明的优选实施方式,应当指出的是,上述优选实施方式不应视为 对本发明的限制,本发明的保护范围应当以权利要求所限定的范围为准。对于本技 术领域的普通技术人员来说,在不脱离本发明的精神和范围内,还可以做出若干改 进和润饰,这些改进和润饰也应视为本发明的保护范围。
再多了解一些
本文用于企业家、创业者技术爱好者查询,结果仅供参考。