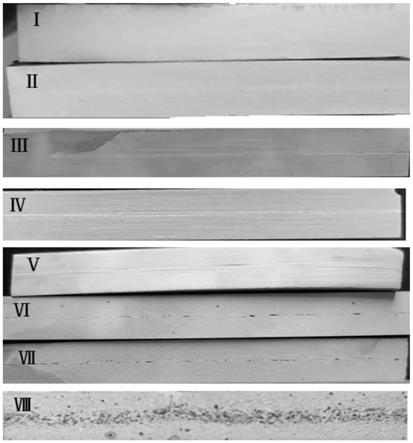
1.本发明属于钢铁冶金技术领域,特别涉及螺旋埋弧焊钢管焊缝是否出现气孔缺陷的判断方法。
背景技术:
2.在实际生产中,除人为操作失误导致的管线钢焊缝产生气孔缺陷的特例外,焊缝产生气孔缺陷主要是由钢材中元素组成导致,如当钢水或轧钢容器内水分含量过多,并且钢水中硫元素含量过多时,易导致轧制的钢材中心处含有大量的硫化锰夹杂物,而这些硫化锰夹杂物在轧制过程中易在轧材中心聚集,当进行螺旋埋弧焊焊接时,在高温作用下,水分解产生较多氢原子,氢原子易在焊缝硫化锰夹杂物处聚集,因此焊缝处产生气孔。
3.目前判断螺旋埋弧焊焊缝是否出现气孔缺陷的常用手段为使用x射线探伤进行检测,当焊缝处观察到气孔,判定探伤的钢材不合格,如说明书附图8所示,黑色位置处为焊缝,白色斑点为气泡。x射线探伤虽然能精确检测焊缝是否产生了气孔缺陷,但是必须将轧材进行螺旋埋弧焊焊接之后才能进行检测,因此操作复杂,容易造成轧材浪费,不适用于大批量轧材焊缝气孔缺陷的快速判断。
技术实现要素:
4.本发明为了解决以上x射线探伤轧材焊缝气孔缺陷存在的操作复杂、容易造成轧材浪费及无法应对大批量轧材在出厂前同时进行高效准确的检测的技术问题,提供一种无需经过轧材焊接即可实现轧材焊缝是否产生气孔缺陷的判断方法。
5.为了实现上述目的,本发明采用以下技术方案:
6.本发明提供一种螺旋埋弧焊钢管焊缝是否出现气孔缺陷的判断方法,其特征在于,包括:当轧材生产过程中钢水的氢含量≤5ppm时,若轧材芯部纵截面内的硫化锰夹杂物总长度小于130μm,轧材经螺旋埋弧焊焊接之后,焊缝不出现气孔缺陷,若轧材芯部纵截面内的硫化锰夹杂物总长度≥130μm,轧材经螺旋埋弧焊焊接之后,焊缝出现气孔缺陷;所述硫化锰夹杂物总长度为轧材芯部纵截面内的所有硫化锰夹杂物的长度之和;所述夹杂物的长度为硫化锰夹杂物沿取向方向的长度;定义轧材的轧制面为水平面,定义轧材的轧制方向为左右方向,所述轧材沿水平方向的上表面为上轧制面,定义所述轧材的左、右侧面沿竖直方向的中心线所在面为垂直纵截面,所述垂直纵截面沿左右方向的中心线向上、下方各延伸100μm,并沿左右方向延伸100mm的区域为芯部纵截面,所述芯部纵截面在轧材中的位置如说明书附图3所示。
7.所述硫化锰夹杂物聚集在轧材芯部纵截面内,夹杂物取向方向为轧材轧制方向。
8.优选的,所述轧材包括l245、l245m、l290、l290、l320、l320m、l360、l360m、l390、l390m、l415、l415m。
9.优选的,所述轧材芯部纵截面内的硫化锰夹杂物总长度的判断方法包括以下步骤:将轧材芯部纵截面所在平面打磨、抛光后得到抛光面,用浓盐酸对抛光面进行酸蚀得到
酸蚀面,通过金相显微镜或扫描电镜观察并计算酸蚀面的轧材芯部纵截面内硫化锰夹杂物的总长度。
10.优选的,所述轧材芯部纵截面内的硫化锰夹杂物总长度是否小于130μm的判断方法为:用芯部纵截面内的硫化锰夹杂物总长度为130μm的标准轧材制备标准金相试样,用待测轧材制备待测金相试样,将标准金相试样的酸蚀面与待测金相试样的酸蚀面进行比较,若标准金相试样的酸蚀面粗糙度大于待测金相试样的酸蚀面粗糙度,则待测轧材芯部纵截面内的硫化锰夹杂物总长度小于130μm,所述酸蚀面为浓盐酸侵蚀之后的金相试样表面,所述轧材芯部纵截面位于所述酸蚀面内,如说明书附图3所示。
11.优选的,所述酸蚀面的制备方法为:用质量分数为38%的浓盐酸对金相试样的表面进行侵蚀,浓盐酸液面需没过表面12mm以上,侵蚀时间大于10min,然后对侵蚀之后的表面进行清洗和烘干,得到酸蚀面。
12.优选的,所述标准金相试样的制备方法包括以下步骤:
13.(1)在标准轧材中取n个纵向长度为100mm、宽度10mm、厚度为轧材厚度的金相试样,对金相试样中包含轧材芯部纵截面的表面依次进行打磨、抛光、浓盐酸酸蚀,得到n个酸蚀面;
14.(2)用金相显微镜或扫描电镜观察步骤(1)中n个酸蚀面,计算得到n个酸蚀面的芯部纵截面内硫化锰夹杂物总长度;
15.(3)n个酸蚀面的芯部纵截面内硫化锰夹杂物总长度为130μm的金相试样作为标准金相试样。
16.优选的,所述n≥6。
17.优选的,所述待测金相试样的制备方法为:
18.以待测轧材芯部纵截面所在平面为金相试样的其中一面,在待测轧材中取1个纵向长度为100mm、宽度10mm、厚度为轧材厚度的金相试样,对金相试样中包含轧材芯部纵截面的表面依次进行打磨、抛光、浓盐酸酸蚀,得到包含酸蚀面的待测金相试样;进一步优选的,所述待测轧材金相试样在待测轧材中的取样位置与标准金相试样在标准轧材中的取样位置一致。
19.优选的,所述标准轧材的制备方法包括以下步骤:
20.1)控制原材料、辅料及炼钢容器内的水分含量小于1%,采用kr法进行铁水脱硫,铁水中硫含量为0.001-0.002%,铁水温度为1300-1310℃,脱硫完毕扒净铁水表面的脱硫渣,铁水包表面渣层厚度为3-5mm;
21.2)铁水脱硫后进行转炉冶炼,控制转炉冶炼所用的石灰中硫含量为0.01-0.02%,转炉冶炼的终渣碱度r为3.1-3.2,转炉冶炼终点的碳含量为0.07-0.09%,转炉出钢温度为1635-1640℃,挡渣出钢,转炉渣下渣量为5-7kg/吨钢;根据钢水目标成份向钢包内添加合金,控制钢包内加入合金的水份含量小于0.1%;
22.3)转炉冶炼之后进行lf精炼深脱硫操作,精炼时间为46-48min,软吹时间为12-14min,钢水硫含量小于0.001%,软吹要求包内钢液微动,钢水不得裸露;
23.lf精炼炉所用炼钢辅料的水份含量均小于1%,lf精炼后添加的钢水保温覆盖剂中的水份含量小于0.5%;
24.4)lf精炼后进行连铸操作,控制中间包钢水过热度为16-18℃,中间包覆盖剂、结
晶器保护渣中的水份含量小于0.5%;控制新砌筑中间包水分含量小于1%;连铸机二冷制度为强冷模型,二冷配水量为1.0m3/吨钢;
25.5)将连铸之后的板坯依次经加热炉、粗轧、半连续精轧、层流冷却及卷取,得标准轧材。
26.优选的,所述标准轧材的芯部纵截面内硫化锰夹杂物的总长度为125-135μm。
27.优选的,所述标准轧材的钢种包括l245、l415。
28.优选的,所述标准金相试样的酸蚀面粗糙度通过粗糙度仪测得。
29.优选的,所述待测金相试样的酸蚀面粗糙度通过粗糙度仪测得,或者将待测金相试样的酸蚀面与标准金相试样的酸蚀面进行对比,目测得出待测金相试样的酸蚀面粗糙度相对于标准金相试样的酸蚀面粗糙度的大小关系。
30.本发明实施例提供的一个或多个技术方案,至少具有以下技术效果:
31.1、本技术提供了一种螺旋埋弧焊钢管焊缝是否出现气孔缺陷的判断方法,即当钢水中的氢含量小于5ppm时,通过轧材芯部纵截面内的硫化锰夹杂物总长度是否大于130μm判断焊缝是否易出现气孔缺陷,无需经过焊接及x射线探伤即可做出判断,方法准确、高效。
32.2、本发明还提供一种用待测金相试样酸蚀面的粗糙度判断待测轧材芯部纵截面内mns夹杂物总长度的方法,用此方法判断轧材芯部纵截面内mns夹杂物总长度是否小于130μm的准确率为90.4%,用轧材芯部纵截面内mns夹杂物总长度的平均值小于130μm判断焊缝不出现气孔缺陷的准确率为100%,该方法与使用金相显微镜或扫描电镜观察相比,更高效快捷,适用于大批量轧材的快速检验,为轧材的质量检测提供标准。
附图说明
33.图1为本发明实施例1轧材1芯部纵截面金相组织照片*200倍;
34.图2为本发明实施例1轧材1经螺旋焊制成钢管的焊缝位置处x射线探伤照片;
35.图3为本发明的芯部纵截面在轧材中的位置图,(a)为轧材主视图,(b)为轧材右视图,(c)为轧材俯视图;
36.图4为本发明的标准金相试样酸蚀面的表观图;
37.图5为本发明的标准轧材芯部纵截面的金相组织图;
38.图6为本发明实施例2中试样
ⅰ‑ⅷ
的酸蚀面表观图;
39.图7为本发明实施例3中轧材a至轧材f的金相试样酸蚀面表观图;
40.图8为本发明实施例3中轧材f焊缝x射线探伤出现的气孔缺陷示意图;
41.图9为本发明实施例3中轧材f的芯部纵截面内的金相组织*500倍;
42.其中,(1)为焊缝,(2)为气孔,(3)为芯部纵截面,(4)为轧材,a为1/2轧材宽度,b为1/2轧材厚度,h为100μm,l为100mm。
具体实施方式
43.下面结合具体实施例对本发明做进一步说明,但不限于此。
44.应当说明的是,下述实施例中所述实验方法,如无特殊说明,均为常规方法;所述试剂、材料和设备,如无特殊说明,均可从商业途径获得。
45.实施例1
46.一种螺旋埋弧焊钢管焊缝是否出现气孔缺陷的判断方法,通过金相显微镜观察轧材芯部纵截面内的mns夹杂物总长度,若总长度大于或等于130μm,焊缝出现气孔缺陷,若总长度小于130μm,焊缝不出现气孔缺陷,主要包括:
47.本实施例共选取6种不同生产工艺制备的管线钢用轧材(轧材1-轧材6)作为实验对象,轧材1至轧材6的牌号分别为l245、l245、l290、l360、l415、l245,硫含量分别为0.001%、0.002%、0.001%、0.002%、0.005%、0.010%。
48.用金相显微镜对轧材1的芯部纵截面进行金相组织检测,金相组织照片如图1所示,芯部纵截面内mns夹杂物的总长度见表1;轧材被运入螺旋焊管厂经埋弧焊后制成钢管,对焊缝处进行x射线探伤,探伤照片如图2所示,未在探伤位置处发现气孔缺陷。
49.对轧材2-轧材6进行金相组织检测,得到轧材芯部纵截面内的硫化锰夹杂物的总长度,如表1所示,并将轧材2-轧材6螺旋埋弧焊焊接制管,对焊缝进行x射线探伤,x射线探伤所得气孔缺陷情况见表1。
50.表1.实施例1中轧材1-轧材6芯部纵截面内mns夹杂物总长度及气孔缺陷情况
[0051][0052][0053]
由表1可得,通过金相显微镜所得轧材芯部纵截面内的mns夹杂物总长度判断气孔缺陷的结果与x射线探伤所得气孔缺陷的结果一致,表明本发明方法具有可靠性。
[0054]
实施例2
[0055]
一种用标准金相试样的酸蚀面粗糙度与待测轧材金相试样的酸蚀面粗糙度进行对比,得出待测轧材芯部纵截面内硫化锰总长度是否小于130μm,进而得出待测轧材螺旋埋弧焊焊缝是否产生气孔缺陷的方法,包括以下操作内容:
[0056]
第一部分:标准金相试样的制备
[0057]
(1)制备标准轧材
[0058]
1)控制原材料、辅料及炼钢容器内的水分含量小于1%,采用kr法进行铁水脱硫,铁水中硫含量为0.002%,铁水温度为1310℃,脱硫完毕扒净铁水表面的脱硫渣,铁水包表面渣层厚度为4mm;
[0059]
2)铁水脱硫后进行转炉冶炼,控制转炉冶炼所用的石灰中硫含量为0.01%,转炉冶炼的终渣碱度r为3.2,转炉冶炼终点的碳含量为0.08%,转炉出钢温度为1638℃,挡渣出钢,转炉渣下渣量为6kg/吨钢;根据钢水目标成份向钢包内添加合金,控制钢包内加入合金的水份含量为0.1%;
[0060]
3)转炉冶炼之后进行lf精炼深脱硫操作,精炼时间为47min,软吹时间为13min,钢水硫含量小于0.001%,软吹要求包内钢液微动,钢水不得裸露;
[0061]
lf精炼炉所用炼钢辅料的水份含量均小于1%,lf精炼后添加的钢水保温覆盖剂中的水份含量小于0.5%;
[0062]
4)lf精炼后进行连铸操作,控制中间包钢水过热度为17℃,中间包覆盖剂、结晶器保护渣中的水份含量小于0.5%;控制新砌筑中间包水分含量小于1%;连铸机二冷制度为强冷模型,二冷配水量为1.0m3/吨钢;
[0063]
5)将连铸之后的板坯依次经加热炉、粗轧、半连续精轧、层流冷却及卷取,得标准轧材,标准轧材的牌号为l245;
[0064]
用金相显微镜得标准轧材芯部纵截面内mns夹杂物总长度平均值为132μm。
[0065]
(2)制备标准金相试样
[0066]
1)在标准轧材中取10个纵向长度为100mm、宽度10mm、厚度为轧材厚度的金相试样,金相试样在标准轧材中的取材位置如图3所示,对金相试样中包含轧材芯部纵截面的表面依次进行打磨、抛光、浓盐酸酸蚀,得到10个酸蚀面,其中浓盐酸的质量分数为38%,对金相试样的表面进行侵蚀时浓盐酸需没过金相试样表面15mm,侵蚀时间为12min,然后对侵蚀之后的表面进行清洗和烘干;
[0067]
2)用金相显微镜或扫描电镜观察步骤(1)中10个酸蚀面,计算得到10个酸蚀面的芯部纵截面内硫化锰夹杂物总长度分别为133μm、135μm、131μm、131μm、133μm、132μm、133μm、131μm、130μm、131μm;
[0068]
3)将10个酸蚀面的芯部纵截面内硫化锰夹杂物总长度为130μm的金相试样作为标准金相试样,所述标准金相试样酸蚀面的表观图如图4所示,金相组织图如图5所示。
[0069]
(3)标准金相试样酸蚀面的粗糙度
[0070]
用粗糙度仪对标准金相试样酸蚀面进行粗糙度检测,得粗糙度ra为12.5。
[0071]
第二部分:待测金相试样的制备
[0072]
在一批待测轧材(轧材
ⅰ‑
轧材
ⅷ
)中各取1个纵向长度为100mm、宽度10mm、厚度为轧材厚度的金相试样,对金相试样中包含轧材芯部纵截面的表面依次进行打磨、抛光、浓盐酸酸蚀,其中浓盐酸的质量分数为38%,对金相试样的表面进行侵蚀时浓盐酸需没过金相试样表面15mm,侵蚀时间为12min,得到包含酸蚀面的待测金相试样(试样
ⅰ‑
试样
ⅷ
),所述待测金相试样酸蚀面表观图如图6所示。
[0073]
第三部分:待测金相试样酸蚀面的粗糙度
[0074]
通过粗糙度仪对待测金相试样酸蚀面进行粗糙度检测,所得数值见表2;或者,将待测金相试样的酸蚀面与标准金相试样的酸蚀面进行比对,目测观察,若待测金相试样酸蚀面比标准金相试样酸蚀面更粗糙,则待测金相试样酸蚀面粗糙度大于12.5,粗糙度结果见表2。
[0075]
第四部分:待测金相试样芯部纵截面内硫化锰夹杂物总长度的测算
[0076]
通过金相显微镜观察并计算待测金相试样酸蚀面的芯部纵截面内mns夹杂物总长度,结果见表2;或者,将待测金相试样酸蚀面的粗糙度与标准金相试样酸蚀面粗糙度进行比较,得到待测金相试样酸蚀面的粗糙度值是否大于12.5(目测得到待测金相试样酸蚀面是否比标准金属试样酸蚀面更粗糙),结果见表2;根据待测金相试样酸蚀面的粗糙度与
12.5的相对大小,得出待测金相试样芯部纵截面内的硫化锰总长度与130μm的相对大小,结果见表2;根据待测金相试样芯部纵截面内硫化锰夹杂物总长度判断焊缝是否产生气孔缺陷的结果如表2所示。
[0077]
表2.待测金相试样的钢种、酸蚀面表观图、粗糙度、mns夹杂物总长度及气孔缺陷情况
[0078]
[0079][0080]
实施例3
[0081]
为了验证用待测金相试样酸蚀面粗糙度判断轧材芯部纵截面内mns夹杂物总长度的准确性,以及进一步用轧材芯部纵截面内mns夹杂物的总长度判断焊缝是否产生气孔缺陷的准确性,同时使用金相显微镜和待测金相试样酸蚀面粗糙度对待测管线钢轧材(轧材a-轧材f硫含量不同,钢种牌号分别为:l245、l245、l290、l360、l415、l245,轧材生产体系中含氢量均在5ppm以内)进行mns夹杂物含量判断;轧材a-轧材f的酸蚀面分别如图7中所示,与标准金相试样酸蚀面进行粗糙程度的对比,目测观察得出轧材a-轧材f的芯部纵截面内mns夹杂物总长度与130μm的关系见表3;用金相显微镜所得轧材芯部纵截面内mns夹杂物总长度平均值见表3;对轧材a-轧材f进行螺旋埋弧焊焊接;用x射线对焊缝进行探伤,气孔缺
陷检测结果见表3,发现轧材f焊缝(1)处存在气孔缺陷(2),气孔缺陷(2)的形貌如图8所示,对轧材f芯部纵截面进行金相检测后发现,在芯部纵截面存在大量mns夹杂物,mns夹杂物形貌如图9所示。从表3中可得,通过待测金相试样粗糙度判断轧材芯部纵截面内的mns夹杂物总长度是否小于130μm的准确率为90.4%,通过轧材芯部纵截面内的mns夹杂物总长度平均值是否大于130μm的方法判断螺旋埋弧焊钢管焊缝出现气孔缺陷的准确率达100%。
[0082]
表3.实施例3中轧材a-轧材f芯部纵截面内mns夹杂物总长度及气孔缺陷情况
[0083][0084]
再多了解一些
本文用于企业家、创业者技术爱好者查询,结果仅供参考。