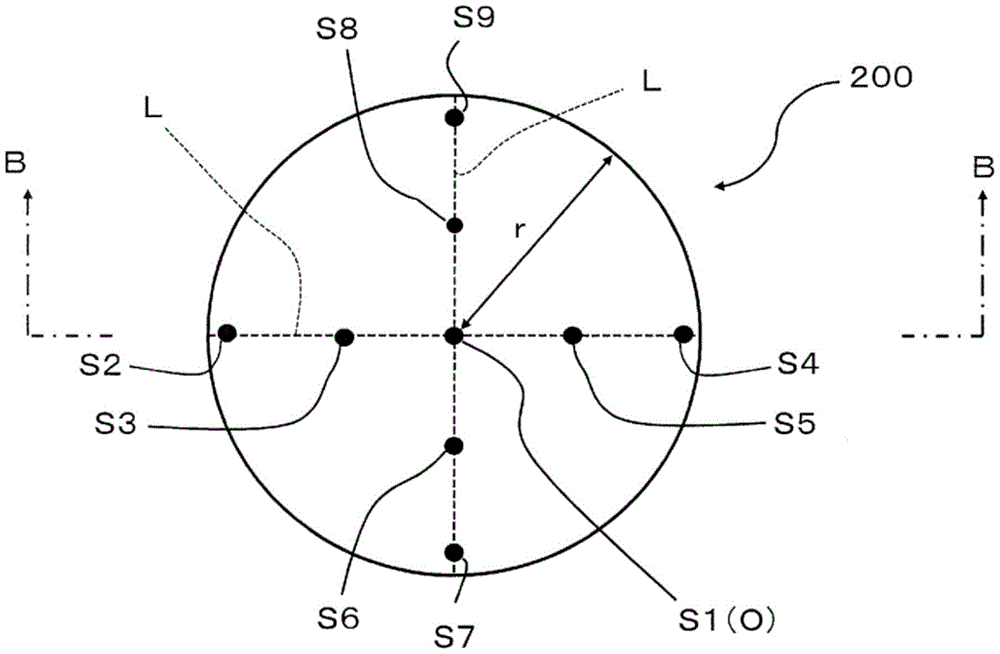
本发明涉及一种于压电元件中用以形成压电响应性良好的金属膜或氮化膜的合适的溅镀靶材。
背景技术:
预测当今及今后社会,随着少子高龄化发展,劳动人口会减少,因此,于制造业中也致力于利用物联网(IoT:InternetOfThings)的自动化。另外,于汽车产业中也不断向制造AI(ArtificialIntelligence,人工智能)等成为主体而不由人操作便能自动驾驶的汽车的社会转变。在自动化、自动驾驶中重要的技术是基于无线的超高速通信,对于基于无线的超高速通信来说,高频滤波器不可或缺。另外,为了使无线通信高速化,预计会从以往的第4代移动通信(4G)中使用的3.4GHz频带向第5代移动通信(5G)中使用的3.7GHz、4.5GHz、28GHz频带即高频侧转变。如果进行此转变,那么高频滤波器在以往的表面声波(SAW:SurfaceAcousticWave)滤波器中技术上较为困难。因此,技术不断从表面声波滤波器向主体声波(BAW:BulkAcousticWave)滤波器转变。作为BAW滤波器或压电元件感测器的压电膜,主要使用氮化铝膜。氮化铝因被称为Q值(Qualityfactor,品质因数)的振幅放大系数较高而为人所知,因此被用作压电膜。但是,因为在高温下无法使用,所以为了谋求压电元件的高温化、高Q值化,包含铝元素及稀土类元素的氮化膜较有希望。作为用以形成包含铝元素及稀土类元素的氮化膜的溅镀靶材,揭示有如下溅镀靶材,包含Al与Sc的合金,含有25原子%~50原子%的Sc,且氧含量为2000质量ppm以下,维氏硬度(Hv)的变动为20%以下(例如参照专利文献1)。记述了该溅镀靶材是经过熔解步骤,进而实施锻造步骤等塑性加工而制作(例如参照专利文献1)。另外,在专利文献1中,记载了溅镀靶材的TOP(靶材上表面)与BTM(靶材下表面)的Sc的含量变动为±2原子%的范围内(说明书段落0040~0041)。另外,在包含铝与稀土类元素的合金的溅镀靶材的制造方法中,有如下技术:准备铝与稀土类元素的元素比处于满足所获得的合金靶材仅由两种金属间化合物所构成的范围内的原料,利用雾化法由该原料制作铝与稀土类元素的合金粉末,通过热压法或放电等离子体烧结法,在真空氛围下由所获得的合金粉末制作成为合金靶材的烧结体(例如参照专利文献2)。另外,已知在ScxAl1-xN合金中,压电常数d33因Sc浓度的组成偏差而极端地变化(例如参照非专利文献1、图3)。
背景技术:
文献专利文献专利文献1:WO2017/213185号公报专利文献2:日本专利特开2015-96647号公报非专利文献非专利文献1:加纳一彦等人,DensotechnicalreviewVol.17,2012,p202~207技术实现要素:[发明要解决的问题]在铝合金的制造中,铝的熔点低至660℃,与此相对,添加到铝的元素的熔点温度非常高,钪的情况下为1541℃,钇的情况下为1522℃,钛的情况下为1668℃,锆的情况下为1855℃,铪的情况下为2233℃,因为铝与所添加的元素的熔点差成为800℃以上,所以几乎不存在铝与所添加的元素完全固溶的范围。因此,如果如专利文献1,相对于铝,增加钪的添加量,那么也存在熔点成为1400℃以上的组成,因熔解后的凝固时的温度不均而导致金属间化合物的生长产生差异,因此难以制作在溅镀靶材的面内方向及厚度方向上具有均匀组成的溅镀靶材。另外,如果如专利文献1,使用熔解法且仅由金属间化合物构成,那么成为非常硬且脆的溅镀靶材,即使通过熔解而形成锭,进行锻造等塑性加工时溅镀靶材也容易发生破裂等。另外,如果如专利文献1,利用熔解法进行制作,那么析出相生长较大,在溅镀靶材的面内方向及厚度方向上产生组成不均,因此,即使溅镀而形成薄膜,所获得的合金薄膜的组成分布也变得不稳定。在专利文献1中,记载了溅镀靶材的TOP与BTM的Sc的含量变动为±2原子%的范围内,但为了获得所形成的膜的均质性,不仅需要抑制厚度方向的不均,也需要抑制面内方向的不均。尤其是如非专利文献1的图3中所指出,也存在因组成偏差而观察到特性极端变化的情况,因此,重要的是在面内方向及厚度方向上保持均匀的组成。为了解决利用熔解法制作时的问题,想到如专利文献2,通过以下等方式减少塑性加工等:在粉末的时间点消除铝与稀土类的组成偏差;或者于烧结时,以与制品的最终形状接近的形状进行最后加工。但是,如果过度地混入氟、氯、氧等杂质,那么溅镀靶材中的氟、氯、氧因成膜时的加热而被释出,容易发生异常放电,使所获得的膜的配向性变差,或者产生颗粒而使膜的良率下降。因此,本发明的目的在于提供一种溅镀靶材,在溅镀靶材中作为杂质的氟元素的混入得到抑制,且使用该溅镀靶材形成薄膜时能够抑制因氟所导致的异常放电的发生,而形成配向性良好的薄膜。[解决问题的技术手段]本发明者等人为了解决所述课题而进行了锐意研究,结果发现,通过将溅镀靶材中作为杂质的氟元素的浓度设为指定值以下,能够抑制氟元素混入的问题,从而完成本发明。也就是说,本发明的溅镀靶材的特征在于:包含铝且还包含稀土类元素及钛族元素中任一种或两种,且氟的含量为100ppm以下。使用溅镀靶材形成薄膜时能够抑制因氟所导致的异常放电的发生,而形成配向性更良好的薄膜。另外,通过抑制因氟所导致的异常放电的发生,能够抑制颗粒的产生,并且良率良好地形成薄膜。在本发明的溅镀靶材中,优选氯的含量为100ppm以下。使用溅镀靶材形成薄膜时能够抑制因氯所导致的异常放电的发生,而形成配向性更良好的薄膜。另外,通过抑制因氯所导致的异常放电的发生,能够抑制颗粒的产生,并且良率良好地形成薄膜。在本发明的溅镀靶材中,优选氧的含量为500ppm以下。使用所述溅镀靶材形成薄膜时能够抑制因氧所导致的异常放电的发生,而形成配向性更良好的薄膜。另外,通过抑制因氧所导致的异常放电的发生,能够抑制颗粒的产生,并且良率良好地形成薄膜。在本发明的溅镀靶材中,优选在所述溅镀靶材中存在包含选自铝、稀土类元素及钛族元素中的至少2种元素的金属间化合物。通过减少单质的铝、单质的稀土类元素、单质的钛族元素的部位,能够抑制组成的不均。如果在靶材中存在金属间化合物,那么金属元素间的溅镀速率的差异得到缓和,所获得的膜的组成不均变小。在本发明的溅镀靶材中,也可在所述溅镀靶材中存在1种、2种、3种或4种所述金属间化合物。通过减少单质的铝、单质的稀土类元素、单质的钛族元素的部位,能够抑制组成的不均。通过使金属间化合物存在1种或多种,金属元素间的溅镀速率的差异进一步得到缓和,所获得的膜的组成不均变得更小。在本发明的溅镀靶材中,也可在所述溅镀靶材中存在1种以上的选自铝、稀土类元素及钛族元素中的至少1种元素的氮化物。形成压电元件的氮化膜时,能够应对压电元件的高温化,并且高Q值化。在本发明的溅镀靶材中,优选所述稀土类元素是钪及钇中至少任一种。形成压电元件的氮化膜时,能够应对压电元件的高温化,并且高Q值化。在本发明的溅镀靶材中,优选所述钛族元素是钛、锆及铪中至少任一种。形成压电元件的氮化膜时,能够应对压电元件的高温化,并且高Q值化。本发明的溅镀靶材优选具有:在铝母相中存在以下材料中至少任一种的组织,即,包含铝及稀土类元素的材料、包含铝及钛族元素的材料、以及包含铝、稀土类元素及钛族元素的材料;或者由复合相构成的组织,该复合相是在铝母相中至少包含以下相中任一种或两种,即,仅包含稀土类元素及不可避免的杂质作为金属种的相、以及仅包含钛族元素及不可避免的杂质作为金属种的相。能够提供一种导电性得到提高,例如在使用DC(directcurrent,直流)溅镀装置成膜时使生产性提高的溅镀靶材。[发明的效果]关于本发明的溅镀靶材,在溅镀靶材中作为杂质的氟元素的混入得到抑制,且使用该溅镀靶材形成薄膜时能够抑制因氟所导致的异常放电的发生,而形成配向性良好的薄膜。另外,通过抑制因氟所导致的异常放电的发生,能够抑制颗粒的产生,并且良率良好地形成薄膜。附图说明图1是表示圆板状靶材的溅镀面内方向上的组成分析的测定部位的概略图。图2是表示B-B截面处所示的圆板状靶材的靶材厚度方向上的组成分析的测定部位的概略图。图3是表示正方形板状靶材的溅镀面内方向上的组成分析的测定部位的概略图。图4是表示C-C截面处所示的正方形板状靶材的靶材厚度方向上的组成分析的测定部位的概略图。图5是用以说明圆筒形状靶材的组成分析的测定部位的概念图。图6是用以说明铝母相的概念的说明图。图7是利用电子显微镜观察实施例1中的Al-Sc靶材的表面时的图像。图8是利用电子显微镜观察比较例4中的Al-Sc靶材的表面时的图像。图9是利用显微镜观察实施例4中的Al-ScN靶材的表面时的图像。具体实施方式以下,示出实施方式对本发明详细地进行说明,但并不限定于这些记载来解释本发明。只要发挥本发明的效果,那么实施方式也可进行各种变化。本实施方式的溅镀靶材包含铝且还包含稀土类元素及钛族元素中任一种或两种,且氟含量为100ppm以下,优选50ppm以下,更优选30ppm以下。如果氟含量超过100ppm,那么溅镀靶材中的氟因成膜时的加热而被释出,由此施加于溅镀靶材的电压不稳定而引起异常放电,导致产生颗粒、使所形成的薄膜的良率降低、形成配向性较差的薄膜,因此,需要将溅镀靶材中的氟含量设为100ppm以下。在本实施方式的溅镀靶材中,氯含量优选100ppm以下,更优选50ppm以下,进而优选30ppm以下。如果氯含量超过100ppm,那么溅镀靶材中的氯因成膜时的加热而被释出,由此施加于溅镀靶材的电压不稳定而引起异常放电,会导致产生颗粒、使所形成的薄膜的良率降低、形成配向性较差的薄膜,因此,优选将溅镀靶材中的氯含量调整到100ppm以下。在本实施方式的溅镀靶材中,氧含量优选500ppm以下,更优选300ppm以下,进而优选100ppm以下。如果氧含量超过500ppm,那么溅镀靶材中的氧因成膜时的加热而被释出,由此施加于溅镀靶材的电压不稳定而引起异常放电,会导致产生颗粒、使所形成的薄膜的良率降低、形成配向性较差的薄膜,因此,优选将溅镀靶材中的氧含量调整到500ppm以下。在本实施方式的溅镀靶材中,碳含量优选200ppm以下,更优选100ppm以下,进而优选50ppm以下。如果碳含量超过200ppm,那么溅镀时碳被引入到膜中,形成结晶性变差的薄膜。另外,如果在靶材表面形成坚固的化合物,那么有损导电性,因异常放电而产生颗粒,会导致膜的良率降低,因此,优选将溅镀靶材中的碳含量调整到200ppm以下。在本实施方式的溅镀靶材中,硅含量优选200ppm以下,更优选100ppm以下,进而优选50ppm以下。如果硅含量超过200ppm,那么溅镀时会形成硅的氧化物或氮化物,以此为起点引起异常放电而产生颗粒,会导致所形成的薄膜的良率降低,因此,优选将溅镀靶材中的硅含量调整到200ppm以下。在本实施方式的溅镀靶材中,(条件1)或(条件2)中的所述溅镀靶材的溅镀面内方向及靶材厚度方向的组成与成为基准的组成的差均为±3%以内,优选±2%以下,更优选±1%以下。此处,成为基准的组成为按照(条件1)或(条件2)所测得的总计18处的组成的平均值。如果与成为基准的组成的差超过±3%,那么存在溅镀靶材成膜时溅镀速率有所不同的情况,而在形成压电元件的压电膜等时,每个衬底中压电膜的压电特性不同,另外,即使是同一衬底,也存在因组成根据压电膜的部位而不同,从而导致压电特性不同的情况。因此,为了抑制压电元件的良率变差,优选将溅镀靶材的溅镀面内方向及靶材厚度方向的组成与成为基准的组成的差控制在±3%以内。如果在面内方向及厚度方向上具有均匀的组成,那么形成用于压电元件等的薄膜时,能够抑制因压电响应性等特性变化所导致的良率降低,所述压电响应性等特性的变化是因组成偏差所导致。(条件1)溅镀面内方向:所述溅镀靶材是中心为O、半径为r的圆板状靶材,且使组成分析的测定部位处于以中心O为交点而正交的假想十字线上,设为中心O为1处,与中心O距离0.45r合计4处,及与中心O距离0.9r合计4处的总计9处。靶材厚度方向:形成穿过假想十字线中任一条线的截面,该截面是纵向为t(也就是靶材的厚度为t)、横向为2r的长方形,且关于组成分析的测定部位,设以下总计9处作为测定地点:穿过中心O的垂直横截线上的中心X及在上下与中心X距离0.45t合计3处(称为a地点、X地点、b地点),在所述截面上从a地点朝向左右的侧边离开0.9r合计2处,从X地点朝向左右的侧边离开0.9r合计2处,以及从b地点朝向左右的侧边离开0.9r合计2处。(条件2)溅镀面内方向:所述溅镀靶材是纵向长度为L1,横向长度为L2的长方形(其中,包括L1与L2相等的正方形;或者长方形包括将长度J、周长K的圆筒形侧面展开而得的长方形,在此形态中,L2与长度J对应,L1与周长K对应,长度J与周长K是J>K、J=K或J<K的关系成立),且使组成分析的测定部位处于以重心O为交点而正交的假想十字线上,且假想十字线与长方形的边正交时,设为如下总计9处:重心O为1处,在假想十字线上纵向上与重心O相隔0.25L1的距离合计2处,横向上与重心O相隔0.25L2的距离合计2处,纵向上与重心O相隔0.45L1的距离合计2处,以及横向上与重心O相隔0.45L2的距离合计2处。靶材厚度方向:形成穿过假想十字线中与纵向L1及横向L2的任一边平行的线的截面,在一边为横向L2的情况下,该截面是纵向为t(也就是所述靶材的厚度为t)、横向为L2的长方形,且关于组成分析的测定部位,设以下总计9处作为测定地点:穿过重心O的垂直横截线上的中心X及在上下与中心X距离0.45t合计3处(称为a地点、X地点、b地点),在所述截面上从a地点朝向左右的侧边离开0.45L2合计2处,从X地点朝向左右的侧边离开0.45L2合计2处,以及从b地点朝向左右的侧边离开0.45L2合计2处。图1是表示圆板状靶材的溅镀面内方向上的组成分析的测定部位(以后,也简称为测定部位)的概略图,参照图1对(条件1)的溅镀靶材的溅镀面内方向上的测定部位进行说明。在圆板状靶材的情况下,半径优选25~225mm,更优选50~200mm。靶材的厚度优选1~30mm,更优选3~26mm。在本实施方式中,预计对大型靶材更有效。在图1中,溅镀靶材200是中心为O、半径为r的圆板状靶材。测定部位处于以中心O为交点而正交的假想十字线(L)上,设为中心O为1处(S1),与中心O距离0.45r合计4处(S3、S5、S6及S8),及与中心O距离0.9r合计4处(S2、S4、S7及S9)的总计9处。图2是表示图1的B-B截面处所示的圆板状靶材的靶材厚度方向上的组成分析的测定部位的概略图,参照图2对(条件1)的溅镀靶材的靶材厚度方向上的测定部位进行说明。在图2中,图1的B-B截面是纵向为t(也就是靶材的厚度为t)、横向为2r的长方形。而且,关于测定部位,设以下9处作为测定地点:穿过中心O的垂直横截线上的中心X(C1)及在上下与中心X距离0.45t合计3处(称为a地点(C4)、X地点(C1)、b地点(C5)),在所述截面上从a地点朝向左右的侧边离开0.9r合计2处(C6、C7),从X地点朝向左右的侧边离开0.9r合计2处(C2、C3),以及从b地点朝向左右的侧边离开0.9r合计2处(C8、C9)。图3是表示正方形板状靶材的溅镀面内方向上的组成分析的测定部位的概略图,参照图3对(条件2)的溅镀靶材的溅镀面内方向上的测定部位进行说明。在长方形或正方形靶材的情况下,纵向长度及横向长度优选50~450mm,更优选100~400mm。靶材的厚度优选1~30mm,更优选3~26mm。在本实施方式中,预计对大型靶材更有效。溅镀靶材300是纵向长度为L1、横向长度为L2的长方形(其中,包括L1与L2相等的正方形)靶材,在图3中,示出溅镀靶材300为L1=L2的形态。测定部位处于以重心O为交点而正交的假想十字线(Q)上,且假想十字线与长方形(或正方形)的边正交时,设为如下总计9处:重心O为1处(P1),在假想十字线上纵向上与重心O相隔0.25L1的距离合计2处(P6、P8),横向上与重心O相隔0.25L2的距离合计2处(P3、P5),纵向上与重心O相隔0.45L1的距离合计2处(P7、P9),以及横向上与重心O相隔0.45L2的距离合计2处(P2、P4)。此外,在溅镀靶材为长方形的情况下,无关边的长度,可适当选择L1、L2。图4是表示图3的C-C截面处所示的正方形板状靶材的靶材厚度方向上的组成分析的测定部位的概略图,参照图4对(条件2)的溅镀靶材的靶材厚度方向上的测定部位进行说明。在图4中,图3的C-C截面形成穿过与横边平行的线的截面,该截面是纵向为t(也就是所述靶材的厚度为t)、横向为L2的长方形,且关于测定部位,设以下总计9处作为测定地点:穿过重心O的垂直横截线上的中心X及在上下与中心X距离0.45t合计3处(称为a地点(D4)、X地点(D1)、b地点(D5)),在所述截面上从a地点朝向左右的侧边离开0.45L2合计2处(D6、D7),从X地点朝向左右的侧边离开0.45L2合计2处(D2、D3),以及从b地点朝向左右的侧边离开0.45L2合计2处(D8、D9)。(圆筒形状的溅镀靶材)图5是用以说明圆筒形状靶材的测定部位的概念图。在溅镀靶材为圆筒形状的情况下,圆筒的侧面为溅镀面,展开图成为长方形或正方形,因此,关于(条件2)可与图3及图4的情形同样地进行考虑。在图5中,在溅镀靶材400是高度(长度)为J、主体的周长为K的圆筒形状的情况下,考虑E-E截面、及该截面成为两端的D-D展开面。首先,靶材厚度方向的组成分析的测定部位在E-E截面中与图4同样地进行考虑。也就是说,认为圆筒材的高度J与图4的L2对应,圆筒材的厚度与图4的厚度t对应,而作为测定部位。另外,溅镀面内方向的测定部位在D-D展开面中与图3同样地进行考虑。也就是说,认为圆筒材的高度J与图3的L2对应,圆筒材的主体的周长K与图3的L1对应,而作为测定部位。长度J与周长K是J>K、J=K或J<K的关系成立。在圆筒形状靶材的情况下,圆筒的主体周的长度优选100~350mm,更优选150~300mm。圆筒的长度优选300~3000mm,更优选500~2000mm。靶材的厚度优选1~30mm,更优选3~26mm。在本实施方式中,预计对大型靶材更有效。本实施方式的溅镀靶材优选具有:在铝母相中存在以下材料中至少任一种的组织,即,包含铝及稀土类元素的材料、包含铝及钛族元素的材料、以及包含铝、稀土类元素及钛族元素的材料;或者由复合相构成的组织,该复合相是在铝母相中至少包含以下相中任一种,即,仅包含稀土类元素及不可避免的杂质作为金属种的相、仅包含钛族元素及不可避免的杂质作为金属种的相、以及仅包含稀土类元素、钛族元素及不可避免的杂质作为金属种的相。提供一种导电性得到提高,例如在使用DC溅镀装置成膜时使生产性提高的溅镀靶材。接下来,针对本实施方式,对溅镀靶材的具体的微细组织进行说明。溅镀靶材的具体的微细组织例如分类为第一组织~第五组织及它们的变化例。此处,具有铝母相的形态是第二组织、第五组织及它们的变化例,尤其是第二组织及作为其变化例的第二组织-2、以及第五组织及作为其变化例的第五组织-2。[第一组织]本实施方式的溅镀靶材具有由以下材料中至少任一种构成的第一组织,即,包含铝及稀土类元素(以后,也记为RE)的材料、包含铝及钛族元素(以后,也记为TI)的材料、以及包含铝、稀土类元素及钛族元素的材料。也就是说,在第一组织中有以下7组的材料的组合:存在包含Al及RE的材料A、包含Al及TI的材料B或包含Al、RE及TI的材料C的形态;以及材料A与材料B共存、材料A与材料C共存、材料B与材料C共存、或材料A、材料B及材料C共存的形态。在本实施方式中,用语“材料”是指构成溅镀靶材的材质,例如包含合金或氮化物。进而合金中例如包含固溶体、共晶、金属间化合物。此外,如果氮化物为类金属,那么也可包含于合金中。[第二组织]本实施方式的溅镀靶材具有在铝母相中存在以下材料中至少任一种的第二组织,即,包含铝及稀土类元素的材料、包含铝及钛族元素的材料、以及包含铝、稀土类元素及钛族元素的材料。也就是说,在第二组织中,在铝母相中存在第一组织中所列举的7组的材料的组合。也就是说,在第二组织中有以下形态的组合,即,在铝母相中存在材料A、材料B或材料C的形态;及在铝母相中发现材料A与材料B共存、材料A与材料C共存、材料B与材料C共存、或材料A、材料B及材料C共存的形态。在本实施方式中,用语“铝母相”也可称为铝基体。在图6中,以第二组织为例对铝母相的概念进行说明。在溅镀靶材100中,其微细构造是在铝母相中存在包含铝及稀土类元素的材料,具体来说,存在Al-RE合金。也就是说,Al母相3将多个Al-RE合金粒子1相接合。Al-RE合金粒子1是Al-RE合金的晶粒2的集合体。Al-RE合金的晶粒2a与相邻的Al-RE合金的晶粒2b的交界为晶界。Al母相3是铝晶粒4的集合体。铝晶粒4a与相邻的铝晶粒4b的交界为晶界。这样一来,在本实施方式中,用语“母相”是指将多个金属粒子或合金粒子或氮化物粒子相接合的相,是接合的相本身也是晶粒的集合体的概念。一般来说,金属间化合物或氮化物具有缺乏作为金属的特性的导电性或塑性加工性(展延性)的特征。在溅镀靶材的Al-RE合金仅由金属间化合物构成,或仅由氮化物构成,或由金属间化合物及氮化物构成的情况下,有溅镀靶材的导电性下降的倾向。但是,通过存在铝(母)相,能够防止溅镀靶材整体的导电性下降。另外,在溅镀靶材的Al-RE合金仅由金属间化合物构成,或仅由氮化物构成,或由金属间化合物及氮化物构成的情况下,有溅镀靶材变得非常脆的倾向。但是,通过存在铝(母)相,能够缓和靶材的脆性。[第三组织]本实施方式的溅镀靶材具有由复合相构成的第三组织,该复合相包含以下相中任一种或两种,即,仅包含铝及不可避免的杂质作为金属种的相、仅包含稀土类元素及不可避免的杂质作为金属种的相、以及仅包含钛族元素及不可避免的杂质作为金属种的相。也就是说,在第三组织中有以下形态的3组的组合,即,由以下复合相构成的形态,该复合相包括包含铝作为金属种的相及包含稀土类元素作为金属种的相;由以下复合相构成的形态,该复合相包括包含铝作为金属种的相及包含钛族元素作为金属种的相;或由以下复合相构成的形态,该复合相包括包含铝作为金属种的相、包含稀土类元素作为金属种的相及包含钛族元素作为金属种的相。作为不可避免的杂质,例如有Fe、Ni等,不可避免的杂质的原子%浓度例如优选200ppm以下,更优选100ppm以下。在本实施方式中,用语“相”为固相,是每同一组成聚在一起的集合体,例如同一组成的粒子的集合体的概念。在本实施方式中,用语“复合相”是存在2种以上的“相”的概念。这些相在每个种类中组成互不相同。[第四组织]本实施方式的溅镀靶材具有由复合相构成的第四组织,该复合相包括包含铝且还包含稀土类元素及钛族元素中任一种或两种的相;及以下相中至少任一种相,即,仅包含铝及不可避免的杂质作为金属种的相、仅包含稀土类元素及不可避免的杂质作为金属种的相、以及仅包含钛族元素及不可避免的杂质作为金属种的相。也就是说,在第四组织中存在以下21组的相的组合。此处,将包含铝及稀土类元素的相设为相D,将包含铝及钛族元素的相设为相E,将包含铝、稀土类元素及钛族元素的相设为相F。另外,将仅包含铝及不可避免的杂质作为金属种的相设为相G,将仅包含稀土类元素及不可避免的杂质作为金属种的相设为相H,将仅包含钛族元素及不可避免的杂质作为金属种的相设为相I。第四组织由以下复合相构成,即,相D及相G;相D及相H;相D及相I;相D、相G及相H;相D、相G及相I;相D、相H及相I;相D、相G、相H及相I;相E及相G;相E及相H;相E及相I;相E、相G及相H;相E、相G及相I;相E、相H及相I;相E、相G、相H及相I;相F及相G;相F及相H;相F及相I;相F、相G及相H;相F、相G及相I;相F、相H及相I;或相F、相G、相H及相I。[第五组织]本实施方式的溅镀靶材具有由复合相构成的第五组织,该复合相是在铝母相中至少包含以下相中任一种或两种,即,仅包含稀土类元素及不可避免的杂质作为金属种的相、以及仅包含钛族元素及不可避免的杂质作为金属种的相。第五组织由在铝母相中存在以下3组的相的复合相构成。也就是说,第五组织由在铝母相中存在相H的复合相、在铝母相中存在相I的复合相、或在铝母相中存在相H及相I的复合相构成。在本实施方式中,用语“铝母相”也可称为铝基体。在第五组织中,在溅镀靶材中,其微细构造是在铝母相中存在相H、相I、或相H与相I两者而构成复合相。铝母相是铝晶粒的集合体,铝晶粒与相邻的铝晶粒的交界为晶界。相H例如为同一组成的粒子的集合体的概念。相I也相同。在存在相H与相I两者的情况下,在铝母相中存在2个组成不同的相。[第五组织的变化例]本实施方式的溅镀靶材在第五组织中包括如下形态,即,所述复合相还包括仅包含铝及不可避免的杂质作为金属种的相。第五组织由在铝母相中存在以下3组的相的复合相构成。也就是说,该复合相是在铝母相中存在相H及相G的复合相、在铝母相中存在相I及相G的复合相、或在铝母相中存在相H、相I及相G的复合相。第一组织~第五组织及第五组织的变化例还包括以下形态。[第一组织-2]本实施方式的溅镀靶材例示以下形态:具有第一组织且所述材料为合金;具有第一组织且所述材料为氮化物;或者具有第一组织且所述材料为合金与氮化物的组合。此处,材料有以下7组的材料的组合:存在包含Al及RE的材料A、包含Al及TI的材料B或包含Al、RE及TI的材料C的形态;以及材料A与材料B共存、材料A与材料C共存、材料B与材料C共存、或材料A、材料B及材料C共存的形态。[第二组织-2]本实施方式的溅镀靶材例示以下形态:具有第二组织且所述材料为合金;具有第二组织且所述材料为氮化物;或者具有第二组织且所述材料为合金与氮化物的组合。此处,材料为[第一组织]中所列举的7组的材料的组合。[第三组织-2]本实施方式的溅镀靶材例示以下形态:具有第三组织且所述复合相为金属相的复合;具有第三组织且所述复合相为氮化物相的复合;或者具有第三组织且所述复合相为金属相与氮化物相的复合。此处,所谓“复合相为金属相的复合”,是指包含Al相及RE相的复合相;包含Al相及TI相的复合相;或包含Al相、RE相及TI相的复合相。所谓“复合相为氮化物相的复合”,是指包含AlN相及REN相的复合相;包含AlN相及TIN相的复合相;或包含AlN相、REN相及TIN相的复合相。另外,所谓“复合相为金属相与氮化物相的复合”,是指例如包含Al相及REN相的复合相;包含AlN相及RE相的复合相;包含Al相、AlN相及RE相的复合相;包含Al相、AlN相及REN相的复合相;包含Al相、RE相及REN相的复合相;包含AlN相、RE相及REN相的复合相;包含Al相、AlN相、RE相及REN相的复合相;包含Al相及TIN相的复合相;包含AlN相及TI相的复合相;包含Al相、AlN相及TI相的复合相;包含Al相、AlN相及TIN相的复合相;包含Al相、TI相及TIN相的复合相;包含AlN相、TI相及TIN相的复合相;包含Al相、AlN相、TI相及TIN相的复合相;包含Al相、AlN相、RE相及TI相的复合相;包含Al相、AlN相、REN相及TI相的复合相;包含Al相、AlN相、RE相及TIN相的复合相;包含Al相、AlN相、REN相及TIN相的复合相;包含Al相、RE相、REN相及TI相的复合相;包含AlN相、RE相、REN相及TI相的复合相;包含Al相、RE相、REN相及TIN相的复合相;包含AlN相、RE相、REN相及TIN相的复合相;包含Al相、RE相、TI相及TIN相的复合相;包含AlN相、RE相、TI相及TIN相的复合相;包含Al相、REN相、TI相及TIN相的复合相;包含AlN相、REN相、TI相及TIN相的复合相;包含Al相、AlN相、RE相、REN相及TI相的复合相;包含Al相、AlN相、RE相、REN相及TIN相的复合相;包含Al相、AlN相、RE相、TI相及TIN相的复合相;包含Al相、AlN相、REN相、TI相及TIN相的复合相;包含Al相、RE相、REN相、TI相及TIN相的复合相;包含AlN相、RE相、REN相、TI相及TIN相的复合相;或包含Al相、AlN相、RE相、REN相、TI相及TIN相的复合相。此外,省略价数的记载。在本实施方式中,用语“金属相”为包含单一金属元素的相的概念。在本实施方式中,用语“氮化物相”为包含氮化物的相的概念。[第四组织-2]本实施方式的溅镀靶材例示以下形态:具有第四组织且所述复合相为合金相与金属相的复合;具有第四组织且所述复合相为合金相与氮化物相的复合;具有第四组织且所述复合相为氮化物相与金属相的复合;具有第四组织且所述复合相为氮化物相与另一氮化物相的复合;或具有第四组织且所述复合相为合金相、金属相及氮化物相的复合。此处,金属相是相G、相H及相I分别为未被氮化或氧化而呈金属状态的相的情形,合金相是相D、相E及相F分别为未被氮化或氧化而呈合金状态的相的情形,氮化物相是相G、相H、相I、相D、相E及相F分别为被氮化的相的情形。另外,有金属相、合金相及氮化物相各自在靶材中存在1种的情况、及存在2种以上的情况,进而有金属相、合金相及氮化物相多种组合而存在的情况。作为这些形态的例,例如有以下形态,即,于相D的合金相或相D的氮化物相中至少1种相中包含相G的金属相、相G的氮化物相、相H的金属相、相H的氮化物相、相I的金属相、相I的氮化物相中至少1种;于相E的合金相或相E的氮化物相中至少1种相中包含相G的金属相、相G的氮化物相、相H的金属相、相H的氮化物相、相I的金属相、相I的氮化物相中至少1种;于相F的合金相或相F的氮化物相中至少1种相中包含相G的金属相、相G的氮化物相、相H的金属相、相H的氮化物相、相I的金属相、相I的氮化物相中至少1种。在本实施方式中,用语“合金相”是包含合金的相的概念。[第五组织-2]本实施方式的溅镀靶材可例示以下形态:具有第五组织且所述复合相为铝母相与至少1种金属相的复合;具有第五组织且所述复合相为铝母相与氮化铝相、稀土类元素的氮化物相及钛族元素的氮化物相中至少1种氮化物相的复合;或者具有第五组织且所述复合相为金属相与氮化物相的复合。此处,所谓“至少1种金属相”,是指仅为相H、仅为相I、或相H及相I两种。所谓“复合相为铝母相与氮化铝相、稀土类元素的氮化物相及钛族元素的氮化物相中至少1种氮化物相的复合”,是指例如包含Al母相及REN相的复合相;包含Al母相及TIN相的复合相;包含Al母相、AlN相及REN相的复合相;包含Al母相、AlN相及TIN相的复合相;包含Al母相、REN相及TIN相的复合相;或包含Al母相、AlN相、REN相及TIN相的复合相。所谓“复合相为金属相与氮化物相的复合”,是指例如包含Al母相、RE相及TIN相的复合相;包含Al母相、REN相及TI相的复合相;包含Al母相、AlN相、RE相及TI相的复合相;包含Al母相、AlN相、REN相及TI相的复合相;包含Al母相、AlN相、RE相及TIN相的复合相;包含Al母相、RE相、REN相及TI相的复合相;包含Al母相、RE相、REN相及TIN相的复合相;包含Al母相、RE相、TI相及TIN相的复合相;包含Al母相、REN相、TI相及TIN相的复合相;包含Al母相、AlN相、RE相、REN相及TI相的复合相;包含Al母相、AlN相、RE相、REN相及TIN相的复合相;包含Al母相、AlN相、RE相、TI相及TIN相的复合相;包含Al母相、AlN相、REN相、TI相及TIN相的复合相;包含Al母相、RE相、REN相、TI相及TIN相的复合相;或包含Al母相、AlN相、RE相、REN相、TI相及TIN相的复合相。此外,N是指氮元素,例如“AlN相”是指氮化铝相。另外,对氮化物省略价数的记载。在第五组织-2中包括如下形态,即,所述复合相为还包含氮化铝相的氮化物相的复合。也就是说,第五组织-2中的复合相是在第五组织中所列举的形态例的每一个中还追加了AlN相的复合相。具体来说,第五组织-2中,作为本实施方式,尤其包括以下情况,即,(1)“复合相为铝母相与氮化铝相、稀土类元素的氮化物相及钛族元素的氮化物相中至少1种氮化物相的复合”为包含Al母相、AlN相及REN相的复合相;包含Al母相、AlN相及TIN相的复合相;或包含Al母相、AlN相、REN相及TIN相的复合相;以及(2)“复合相为金属相与氮化物相的复合”为包含Al母相、AlN相、RE相及TI相的复合相;包含Al母相、AlN相、REN相及TI相的复合相;包含Al母相、AlN相、RE相及TIN相的复合相;包含Al母相、AlN相、RE相、REN相及TI相的复合相;包含Al母相、AlN相、RE相、REN相及TIN相的复合相;包含Al母相、AlN相、RE相、TI相及TIN相的复合相;包含Al母相、AlN相、REN相、TI相及TIN相的复合相;或包含Al母相、AlN相、RE相、REN相、TI相及TIN相的复合相。在本实施方式的溅镀靶材中,优选在溅镀靶材中存在金属间化合物,该金属间化合物包含选自铝、稀土类元素及钛族元素中的至少2种元素。例如在第一组织或第二组织中,在溅镀靶材中存在这种金属间化合物。另外,在第四组织中存在合金相的情况下,在合金相中存在金属间化合物。通过减少单质的铝、单质的稀土类元素、单质的钛族元素的部位,能够抑制组成的不均。另外,在靶材包含金属单质的组合的情况下,溅镀时应用每种单质的溅镀速率,会出现明显差异,因此难以获得均质的膜,如果在靶材中存在金属间化合物,那么金属元素间的溅镀速率的差异得到缓和,所获得的膜的组成不均变小。在本实施方式的溅镀靶材中,也可在所述溅镀靶材中存在1种、2种、3种或4种所述金属间化合物。例如在第一组织、第二组织或第四组织中存在合金相的情况下,在溅镀靶材中根据金属种的种类数量存在1种、2种、3种或4种金属间化合物。在靶材包含金属单质的组合的情况下,溅镀时应用每种单质的溅镀速率,会出现明显差异,因此难以获得均质的膜,通过存在1种或多种金属间化合物,金属元素间的溅镀速率的差异进一步得到缓和,所获得的膜的组成不均变得更小。在本实施方式的溅镀靶材中,也可在所述溅镀靶材中存在1种以上的选自铝、稀土类元素及钛族元素中的至少1种元素的氮化物。形成压电元件的氮化膜时,能够应对压电元件的高温化,并且高Q值化。例如在第一组织~第五组织中,均因导入氮元素而存在氮化物。氮化物的种类根据金属种的种类数量存在1种、2种、3种或4种或其以上的数量。在本实施方式的溅镀靶材中,优选所述稀土类元素是钪及钇中至少任一种。形成压电元件的氮化膜时,能够应对压电元件的高温化,并且高Q值化。作为稀土类元素,存在仅为钪,仅为钇或钪与钇两者的组合。在包含钪与钇两者作为稀土类元素时,例如有存在Al-Sc-Y材料或Al-Sc-Y相的形态,除此以外,还有同时存在Al-Sc材料、Al-Y材料及Al-Sc-Y材料的至少2种材料的形态、或同时存在Al-Sc相、Al-Y相及Al-Sc-Y相的至少2种相的形态。在本实施方式的溅镀靶材中,优选所述钛族元素是钛、锆及铪中至少任一种。形成压电元件的氮化膜时,能够应对压电元件的高温化,并且高Q值化。作为钛族元素,存在如下情况,即,仅为钛;仅为锆;仅为铪;钛及锆;钛及铪;锆及铪;或钛、锆及铪。例如在包含钛与锆两者作为钛族元素时,例如有存在Al-Ti-Zr材料或Al-Ti-Zr相的形态,除此以外,还有同时存在Al-Ti材料、Al-Zr材料及Al-Ti-Zr材料的至少2种材料的形态、或同时存在Al-Ti相、Al-Zr相及Al-Ti-Zr相的至少2种相的形态。另外,在包含钛与铪两者时,例如有存在Al-Ti-Hf材料或Al-Ti-Hf相的形态,除此以外,还有同时存在Al-Ti材料、Al-Hf材料及Al-Ti-Hf材料的至少2种材料的形态、或同时存在Al-Ti相、Al-Hf相及Al-Ti-Hf相的至少2种相的形态。另外,在包含锆与铪两者时,例如有存在Al-Zr-Hf材料或Al-Zr-Hf相的形态,除此以外,还有同时存在Al-Zr材料、Al-Hf材料及Al-Zr-Hf材料的至少2种材料的形态、或同时存在Al-Zr相、Al-Hf相及Al-Zr-Hf相的至少2种相的形态。包含钛、锆及铪时,例如有存在Al-Ti-Zr-Hf材料或Al-Ti-Zr-Hf相的形态,除此以外,还有同时存在Al-Ti材料、Al-Zr材料、Al-Hf材料、Al-Ti-Zr材料、Al-Ti-Hf材料、Al-Zr-Hf材料及Al-Ti-Zr-Hf材料的至少2种材料的形态、或同时存在Al-Ti相、Al-Zr相、Al-Hf相、Al-Ti-Zr相、Al-Ti-Hf相、Al-Zr-Hf相及Al-Ti-Zr-Hf相的至少2种相的形态,进而在所述形态中,有除Al以外还加入包含Ti、Zr及Hf中的2种的材料或相的形态、除Al以外还加入包含Ti、Zr及Hf中的1种的材料或相的形态。本实施方式的溅镀靶材中,作为铝中所含有的稀土类元素,可列举钪、钇等,作为铝中所含有的钛族元素,可列举钛、锆、铪等。靶材中的钪的含量优选5~75原子%。更优选10~50原子%。靶材中的钇的含量优选5~75原子%。更优选10~50原子%。靶材中的钛的含量优选5~75原子%。更优选10~50原子%。靶材中的锆的含量优选5~75原子%。更优选10~50原子%。靶材中的铪的含量优选5~75原子%。更优选10~50原子%。至少1种以上的所述各元素以满足所述含量的方式与铝一同包含于本实施方式的溅镀靶材中。在形成铝中含有稀土类元素、钛族元素的合金的情况下,首先在所述组成范围内形成铝-钪合金、铝-钇合金等铝-稀土类元素合金。接下来,在所述组成范围内形成铝-钛合金、铝-锆合金、铝-铪合金等铝-钛族元素的合金。之后,通过调整所述铝-稀土类元素的合金及所述铝-钛族元素的合金各自的含量并且将它们加以混合,而形成铝-稀土类元素-钛族元素的合金。另外,也可不如上所述将二元合金加以混合来形成三元合金,而是直接形成铝-稀土类元素-钛族元素的合金。通过在溅镀靶材中形成金属间化合物或在溅镀时形成氮化膜,即使在高温下,也能形成可获得高Q值的压电膜。对本实施方式的溅镀靶材的制造方法进行说明。本实施方式的溅镀靶材的制造方法包括:第1步骤,制造(1)包含铝及稀土类元素的原料、(2)包含铝及钛族元素的原料、或(3)包含铝、稀土类元素及钛族元素的原料;第2步骤,由所述第1步骤中制造的原料来制造(1)铝与稀土类元素的合金粉末(铝-稀土类元素)、(2)铝与钛族元素的合金粉末(铝-钛族元素)、或(3)铝、稀土类元素及钛族元素的合金粉末(铝-稀土类元素-钛族元素);以及第3步骤,由所述第2步骤中所得的粉末获得(1)铝-稀土类元素的烧结体、(2)铝-钛族元素的烧结体、(3)铝-稀土类元素-钛族元素的烧结体。另外,在制造包含铝母相的溅镀靶材的情况下,溅镀靶材的制造方法包括:第1步骤,制造预计主要成为母相的铝原料、及作为预计主要成为存在于母相中的材料或相的原料的(1)包含铝及稀土类元素的原料、(2)包含铝及钛族元素的原料、或(3)包含铝、稀土类元素及钛族元素的原料;第2步骤,由所述第1步骤中制造的原料制造预计主要成为母相的铝粉末、及作为预计主要成为存在于母相中的材料或相的合金粉末的(1)铝与稀土类元素的合金粉末(铝-稀土类元素)、(2)铝与钛族元素的合金粉末(铝-钛族元素)、或(3)铝、稀土类元素及钛族元素的合金粉末(铝-稀土类元素-钛族元素);以及第3步骤,由所述第2步骤中所得的粉末获得(1)铝与铝-稀土类元素的烧结体、(2)铝与铝-钛族元素的烧结体、或(3)铝与铝-稀土类元素-钛族元素的烧结体。[第1步骤]该步骤是制作第2步骤中制造铝-稀土类元素的合金粉末、铝-钛族元素的合金粉末或铝-稀土类元素-钛族元素的合金粉末时所使用的原料的步骤。在第1步骤中制作的用以制造粉末的原料(以后,也简称为“原料”)可例示以下形态:(1A)分别准备合金靶材的构成元素的单金属作为起始原材料,将其混合而作为原料;(2A)准备组成与合金靶材相同的合金作为起始原材料,并将其作为原料;或(3A)准备构成元素与合金靶材相同或欠缺一部分且组成比与所需组成比有偏差的合金、及为了调整到所需组成而调配的单金属作为起始原材料,并将它们混合而作为原料。将作为起始原材料的铝与稀土类元素、铝与钛族元素、或铝、稀土类元素及钛族元素中任一种投入到熔解装置中来进行熔解,制作铝-稀土类元素的合金原料、铝-钛族元素的合金原料、或铝-稀土类元素-钛族元素的合金原料。优选用于熔解装置的装置或容器的材质也使用杂质较少的材质以使得熔解后,杂质不会大量地混入到铝-稀土类元素的合金原料、铝-钛族元素的合金原料、或铝-稀土类元素-钛族元素的合金原料中。作为熔解法,选择能应对以下熔解温度的方法。作为熔解温度,以1300~1800℃对铝-稀土类元素的合金进行加热,以1300~1800℃对铝-钛族元素的合金进行加热,或以1300~1800℃对铝-稀土类元素-钛族元素的合金进行加热。作为熔解装置内的氛围,设为真空度为1×10-2Pa以下的真空氛围、含有4vol%以下的氢气的氮气氛围、或含有4vol%以下的氢气的惰性气体氛围等。在使铝母相包含于靶材中的情况下等,当制造铝原料时,以700~900℃对铝进行加热,投入到熔解装置中并以与其它原料相同的方式进行制造。合金粉末原料的形态除了所述(1A)(2A)(3A)中记载的3种原料形态以外,还可为合金粒或合金块,或者也可为粉末、粒、块的组合。粉末、粒、块虽表现出粒径的差异,但无论哪一种,只要能在第2步骤的粉末制造装置中使用,那么粒径并无特别限制。具体来说,为了在第2步骤的粉末制造装置内使原料熔解,只要是可供给到粉末制造装置的原料大小,那么并无特别限制。[第2步骤]该步骤是制造铝-稀土类元素的合金粉末、铝-钛族元素的合金粉末、或铝-稀土类元素-钛族元素的合金粉末的步骤。将第1步骤中制造的铝-稀土类元素的合金原料、铝-钛族元素的合金原料、或铝-稀土类元素-钛族元素的合金原料中至少一种原料投入到粉末制造装置中,使其熔解而制成熔液之后,对熔液吹送气体或水等,使熔液飞散,进行急冷凝固而制作粉末。优选用于粉末制造装置的装置或容器的材质也使用杂质较少的材质以使得熔解后,杂质不会大量地混入到铝-稀土类元素的合金粉末、铝-钛族元素的合金粉末、或铝-稀土类元素-钛族元素的合金粉末中。作为熔解法,选择能应对以下熔解温度的方法。作为熔解温度,以1300~1800℃对铝-稀土类元素的合金原料进行加热,以1300~1800℃对铝-钛族元素的合金原料进行加热,或以1300~1800℃对铝-稀土类元素-钛族元素的合金原料进行加热。作为粉末制造装置内的氛围,在真空度为1×10-2Pa以下的真空氛围、含有4vol%以下的氢气的氮气氛围或含有4vol%以下的氢气的惰性气体氛围等下进行。作为进行吹送时的熔液的温度,优选在“铝-稀土类元素的合金、铝-钛族元素的合金、或铝-稀土类元素-钛族元素的合金各自的熔点 100℃以上”进行,更优选在“铝-稀土类元素的合金、铝-钛族元素的合金、或铝-稀土类元素-钛族元素的合金各自的熔点 150~250℃”进行。其原因在于:如果温度过高,那么造粒中的冷却进行不充分,难以成为粉末,生产效率欠佳。另外,如果温度过低,那么容易产生喷射时易发生喷嘴堵塞的问题。进行吹送时的气体可使用氮气、氩气等,但并不限定于此。在合金粉末的情况下,存在如下情况,即,通过进行急冷凝固,合金粉末的金属间化合物的析出与熔解法时相比得到抑制,相当于海岛结构的岛的析出粒径变小,在合金粉体的阶段中已获得此状态,即使在烧结后或形成靶材时,也会维持此状态。经急冷后的粉末成为第1步骤中准备的铝与稀土类元素、铝与钛族元素、或铝、稀土类元素及钛族元素的元素比。在使铝母相包含于靶材中的情况下等,当制造铝粉末时,以700~900℃对铝进行加热,投入到熔解装置中并以与其它粉末相同的方式进行制造。[第3步骤]该步骤是由第2步骤中所得的粉末获得成为靶材的烧结体的步骤。作为烧结法,通过热压法(以下,也称为HP)、放电等离子体烧结法(以下,也称为SPS)、或热均压烧结法(以下,也称为HIP)进行烧结。使用第2步骤中所得的铝-稀土类元素的合金粉末、铝-钛族元素的合金粉末、或铝-稀土类元素-钛族元素的合金粉末进行烧结。烧结时所使用的粉末为以下实例。(1B)在铝-稀土类元素的合金的情况下,使用铝-稀土类元素的合金粉末。(2B)在铝-钛族元素的合金的情况下,使用铝-钛族元素的合金粉末。(3B)在铝-稀土类元素-钛族元素的合金的情况下,例如使用铝-稀土类元素-钛族元素的合金粉末,或使用将铝-稀土类元素的合金粉末与铝-钛族元素的合金粉末2种混合而成的混合粉末。优选将所述(1B)~(3B)中所示的任一粉末填满模具,通过10~30MPa的预加压,利用模具及冲头等将粉末密闭后进行烧结。此时,优选将烧结温度设为700~1300℃,加压力优选设为40~196MPa。作为烧结装置内的氛围,在真空度为1×10-2Pa以下的真空氛围、含有4vol%以下的氢气的氮气氛围或含有4vol%以下的氢气的惰性气体氛围等下进行。氢气优选含有0.1vol%以上。保持时间(烧结温度的最高温度的保持时间)优选2小时以下,更优选1小时以下,进而优选无保持时间。在使铝母相包含于靶材中的情况下等,当使铝粉末混合于所述(1B)、(2B)或(3B)的合金粉末中时,优选将烧结温度设为500~600℃,除此以外,在相同条件下进行烧结。通过至少经过第1步骤至第3步骤,能够抑制溅镀靶材的面内方向及厚度方向的组成偏差,而制作在薄膜形成时会造成影响的杂质的含量较少的溅镀靶材。进而,能够制作氟的含量较少的溅镀靶材。在本实施方式的溅镀靶材的制造方法中,也包括如下变化例。也就是说,在第1步骤中,也可制造预计主要成为母相的铝原料、及作为预计主要成为存在于母相中的材料或相的原料的(1)稀土类元素原料、(2)钛族元素原料、或(3)包含稀土类元素及钛族元素的原料。在第2步骤中,也可将所述第1步骤中制造的原料分别制成雾化粉末。在第3步骤中,由第1步骤中所得的原料或第2步骤中所得的粉末获得(1)铝与稀土类元素的烧结体、(2)铝与钛族元素的烧结体、或(3)铝与稀土类元素-钛族元素的烧结体。在本实施方式中,(条件1)及(条件2)中的组成分析的方法有能量分散型X射线光谱法(EDS)、高频感应耦合等离子体发射光谱分析法(ICP)、萤光X射线分析法(XRF)等,优选利用EDS进行组成分析。实施例以下,示出实施例并且对本发明更详细地进行说明,但本发明并不限定于实施例来解释。(实施例1)将纯度4N的Al原料及纯度3N的Sc原料投入到粉末制造装置中,接下来,将粉末制造装置内调整为5×10-3Pa以下的真空氛围,以熔解温度1700℃使Al原料及Sc原料熔解而成为熔液,接下来,对熔液吹送氩气,使熔液飞散,进行急冷凝固,而制作粒径为150μm以下的Al-40原子%Sc粉末(此情况下,Al为60原子%Al,但省略了Al的原子百分率的记载;以后也相同)。之后,将Al-40原子%Sc粉末填充到放电等离子体烧结(以后,也称为SPS烧结)用的碳模具中。接下来,通过10MPa的预加压,利用模具及冲头等将混合粉末密闭,将填充有混合粉末的模具设置在SPS装置(型号:SPS-825、SPSSINTEX公司制造)中。而且,作为烧结条件,设为烧结温度为550℃、加压力为30MPa、烧结装置内的氛围为8×10-3Pa以下的真空氛围、烧结温度的最高温度的保持时间为0小时,在该条件下实施烧结。使用研削加工机、车床等对Al-40原子%Sc烧结体进行加工,制作实施例1的φ50.8mm×5mmt的Al-40原子%Sc靶材。接下来,使用电子显微镜以500倍的倍率观察Al-40原子%Sc靶材的截面。将观察到的电子显微镜的图像示于图7。图7的图像的横边长度为250μm。图7的结果为,确认到对比度上浓淡较小,金属间化合物较为微细,并且分散得均匀。另外,图7的电子显微镜的图像的结果为,靶材包含Al2Sc及AlSc两种金属间化合物,具有第一组织。接下来,使用质量分析装置(型号:ElementGD、ThermoFisherScientific公司制造),对实施例1的Al-40原子%Sc靶材测定氟的含量。氟的含量为5.5ppm。接下来,利用溅镀装置(型号MPS-6000-C4、ULVAC公司制造),使用实施例1的Al-40原子%Sc靶材,在φ76.2mm×5mmt的单晶Si衬底上成膜。成膜条件为将溅镀装置内抽真空,成膜前极限真空度达到5×10-5Pa以下之后,使用氩气将溅镀装置内的压力调整为0.13Pa。之后,一边将单晶Si衬底加热到300℃,一边将Al-40原子%Sc靶材的溅镀电力调整为150W,在单晶Si衬底上以厚度1μm形成Al-40原子%Sc膜。此时,观察Al-40原子%Sc靶材的溅镀状况,电压稳定,未确认到异常放电等,实现了成膜。(实施例2)在实施例1中,制造粒径为150μm以下的Al-30原子%Sc粉末来代替Al-40原子%Sc粉末,制造φ50.8mm×5mmt的Al-30原子%Sc靶材来代替实施例1的Al-40原子%Sc靶材,除此以外,以相同方式获得实施例2的Al-30原子%Sc靶材。接下来,以与实施例1相同的方式对实施例2的Al-30原子%Sc靶材测定氟的含量。氟的含量为22ppm。靶材包含Al2Sc及AlSc两种金属间化合物,具有第一组织。接下来,使用实施例2的Al-30原子%Sc靶材来代替实施例1的Al-40原子%Sc靶材,除此以外,以与实施例1相同的方式在单晶Si衬底上以厚度1μm形成Al-30原子%Sc膜。此时,观察Al-30原子%Sc靶材的溅镀状况,电压稳定,未确认到异常放电等,实现了成膜。(实施例3)在实施例1中,使用纯度4N的Al原料及纯度3N的Ti原料来代替使用纯度4N的Al原料及纯度3N的Sc原料,除此以外,以相同方式制作粒径为150μm以下的Al-40原子%Ti粉末。接下来,制造φ50.8mm×5mmt的Al-40原子%Ti靶材来代替实施例1的Al-40原子%Sc靶材,除此以外,以与实施例1相同的方式获得实施例3的Al-40原子%Ti靶材。接下来,以与实施例1相同的方式对实施例3的Al-40原子%Ti靶材测定氟的含量。氟的含量为14ppm。靶材包含Al2Ti及AlTi两种金属间化合物,具有第一组织。接下来,使用实施例3的Al-40原子%Ti靶材来代替实施例1的Al-40原子%Sc靶材,除此以外,以与实施例1相同的方式在单晶Si衬底上以厚度1μm形成Al-40原子%Ti膜。此时,观察Al-40原子%Ti靶材的溅镀状况,电压稳定,未确认到异常放电等,实现了成膜。(比较例1)使用粒径为150μm以下、纯度3N的纯Al粉末及粒径为150μm以下、纯度2N的Sc粉末,以成为Al-40原子%Sc的方式调整各粉末的量后,进行混合。之后,将Al-40原子%Sc混合粉末填充到SPS烧结用的碳模具。接下来,通过10MPa的预加压,利用模具及冲头等将混合粉末密闭,将填充有混合粉末的模具设置在SPS装置(型号:SPS-825、SPSSINTEX公司制造)中。而且,作为烧结条件,设为烧结温度为550℃、加压力为30MPa、烧结装置内的氛围为8×10-3Pa以下的真空氛围、烧结温度的最高温度的保持时间为0小时,在该条件下实施烧结。使用研削加工机、车床等对烧结后的Al-40原子%Sc烧结体进行加工,制作比较例1的φ50.8mm×5mmt的Al-40原子%Sc靶材。接下来,以与实施例1相同的方式对比较例1的Al-40原子%Sc靶材测定氟的含量。氟的含量为130ppm。靶材包含Al2Sc及AlSc两种金属间化合物,具有第一组织。接下来,使用比较例1的Al-40原子%Sc靶材来代替实施例1的Al-40原子%Sc靶材,除此以外,以与实施例1相同的方式在单晶Si衬底上以厚度1μm形成Al-40原子%Sc膜。此时,观察比较例1的Al-40原子%Sc靶材的溅镀状况,电压不稳定,确认到异常放电。作为与实施例1相比较发生异常放电的原因,认为是溅镀靶材中的氟因成膜时的加热而被释出。(比较例2)在比较例1中,以成为Al-30原子%Sc来代替Al-40原子%Sc的方式调整各粉末的量,除此以外,以相同方式制作比较例2的φ50.8mm×5mmt的Al-30原子%Sc靶材来代替比较例1的Al-40原子%Sc靶材。接下来,以与实施例1相同的方式对比较例2的Al-30原子%Sc靶材测定氟的含量。氟的含量为180ppm。靶材包含Al2Sc及AlSc两种金属间化合物,具有第一组织。接下来,使用比较例2的Al-30原子%Sc靶材,来代替实施例1的Al-40原子%Sc靶材,除此以外,以与实施例1相同的方式在单晶Si衬底上以厚度1μm形成Al-30原子%Sc膜。此时,观察比较例2的Al-30原子%Sc靶材的溅镀状况,电压不稳定,确认到异常放电。作为与实施例2相比较发生异常放电的原因,认为是溅镀靶材中的氟因成膜时的加热而被释出。(比较例3)在比较例1中,使用粒径为150μm以下、纯度3N的纯Al粉末及粒径为150μm以下、纯度2N的Ti粉末以成为Al-40原子%Ti的方式调整各粉末的量,来代替使用粒径为150μm以下、纯度3N的纯Al粉末及粒径为150μm以下、纯度2N的Sc粉末以成为Al-40原子%Sc的方式调整各粉末的量,除此以外,以相同方式制作比较例3的φ50.8mm×5mmt的Al-40原子%Ti靶材。接下来,以与实施例1相同的方式对比较例3的Al-40原子%Ti靶材测定氟的含量。氟的含量为190ppm。靶材包含Al2Ti及AlTi两种金属间化合物,具有第一组织。接下来,使用比较例3的Al-40原子%Ti靶材来代替实施例1的Al-40原子%Sc靶材,除此以外,以与实施例1相同的方式于单晶Si衬底上以厚度1μm形成Al-40原子%Ti膜。此时,观察比较例3的Al-40原子%Ti靶材的溅镀状况,电压不稳定,确认到异常放电。作为与实施例3相比较发生异常放电的原因,认为是溅镀靶材中的氟因成膜时的加热而被释出。(比较例4)将纯度4N的Al原料及纯度3N的Sc原料以成为Al-40原子%Sc的方式称量,利用电弧熔解装置(ULVAC公司制造AME-300型)进行熔解,获得60mm见方×6mm左右的熔解后的板。接下来,尝试对该板进行机械加工而制作φ50.8mm×5mmt的溅镀靶材,但在研削加工中,在板的外周产生缺口,在利用线放电加工的切断加工中,板产生龟裂,而无法制作溅镀靶材。为了确认产生龟裂的原因,使用电子显微镜以500倍的倍率观察Al-40原子%Sc靶材的截面。将观察到的电子显微镜的图像示于图8。图8的图像的横边长度为250μm。图8的结果为,上端的不连续的表面为靶材加工面,但在金属间化合物的内部确认到破裂。因此,认为容易以粗大化的金属间化合物的粒子为起点而出现龟裂,加工性变差。表1中,针对实施例1~3及比较例1~3,示出对Al添加的元素的种类、添加元素的添加量及氟的含量。通过分别比较实施例1与比较例1、实施例2与比较例2、实施例3与比较例3,可知如上所述,即使对Al添加的元素的种类及添加量相同,只要氟的含量并非指定值(100ppm以下),那么成膜时也会发生异常放电。在比较例4中,因为仅利用熔解法来制作板,所以所获得的板具有金属间化合物粗大化的组织。因此认为金属间化合物变脆,以该较脆的金属间化合物为起点会产生加工中途的缺口或龟裂。与此相对,在实施例1中,通过利用熔解、急冷凝固进行造粒,而抑制成为金属间化合物粗大化的组织,之后,经过烧结的制程来制作溅镀靶材,因此,微细的组织得到维持,缺口或龟裂得到遏制,加工性提高。在实施例1的溅镀靶材中,通过维持微细的组织,因靶材内的位置不同所造成的组成偏差较小。为了确认组成偏差,对(条件1)中的溅镀靶材的溅镀面内方向及靶材厚度方向的组成进行了确认。组成是使用EDS(energydispersivespectrometer,能谱仪)(日本电子制造)进行测定。结果,与成为基准的组成的差均为±1%以内,确认到组成偏差较小。与此相对,可知在比较例4中,根据测定部位不同而存在与成为基准的组成的差未落入±3%以内的部位,与实施例1相比较,组成偏差较大。[表1]添加元素添加量(原子%)氟的含量(ppm)实施例1Sc405.5实施例2Sc3022实施例3Ti4014比较例1Sc40130比较例2Sc30180比较例3Ti40190在实施例1中,使用质量分析装置(型号:ElementGD、ThermoFisherScientific公司制造)测定氯的含量。氯的含量为5.6ppm。另外,在比较例1中,同样地测定氯的含量。氯的含量为146ppm。在实施例1中,使用质量分析装置(型号:ON836、LECO公司制造)测定氧的含量。氧的含量为424ppm。另外,在比较例1中,同样地测定氧的含量。氧的含量为2993ppm。(实施例4)使用粒径为150μm以下、纯度4N的纯Al粉末及粒径为150μm以下、纯度3N的ScN粉末以成为Al-10mol%ScN的方式调整各粉末的量后,进行混合。之后,将Al-10mol%ScN混合粉末填充到放电等离子体烧结(以后,也称为SPS烧结)用的碳模具。接下来,通过10MPa的预加压,利用模具及冲头等将混合粉末密闭,将填充有混合粉末的模具设置在SPS装置(型号:SPS-825、SPSSINTEX公司制造)中。而且,作为烧结条件,设为烧结温度为550℃、加压力为30MPa、烧结装置内的氛围为8×10-3Pa以下的真空氛围、烧结温度的最高温度的保持时间为0小时,在该条件下实施烧结。使用研削加工机、车床等对烧结后的Al-10mol%ScN烧结体进行加工,制作φ50mm×6mmt的Al-10mol%ScN靶材。制作靶材时,加工性良好,能够成型为靶材形状。利用显微镜观察所制作的靶材的表面。将观察到的图像示于图9。图9的图像的横边长度为650μm。从图9确认到相对于ScN,Al占大部分,且认为因存在相连的Al而存在铝母相。结果,认为获得了靶材制作时的加工性。此时,靶材包含Al与ScN两种相,具有第五组织-2。接下来,使用质量分析装置(型号:ElementGD、ThermoFisherScientific公司制造)对实施例4的Al-10mol%ScN靶材测定氟的含量。氟的含量为4.1ppm。接下来,利用溅镀装置(型号MPS-6000-C4、ULVAC公司制造),使用实施例4的Al-10mol%ScN靶材,在φ76.2mm×5mmt的单晶Si衬底上成膜。成膜条件为将溅镀装置内抽真空,成膜前极限真空度达到5×10-5Pa以下之后,使用氩气将溅镀装置内的压力调整为0.13Pa。之后,一边将单晶Si衬底加热到300℃,一边将Al-10mol%ScN靶材的溅镀电力调整为150W,在单晶Si衬底上以厚度1μm形成Al-10mol%ScN膜。此时,观察Al-10mol%ScN靶材的溅镀状况,电压稳定,未确认到异常放电等,实现了成膜。[符号的说明]100,200,300,400溅镀靶材O中心L,Q假想十字线S1~S9溅镀面的测定部位C1~C9截面的测定部位P1~P9溅镀面的测定部位D1~D9截面的测定部位1Al-RE合金粒子3Al母相2,2a,2bAl-RE合金的晶粒4,4a,4b铝晶粒。当前第1页12
再多了解一些
本文用于企业家、创业者技术爱好者查询,结果仅供参考。