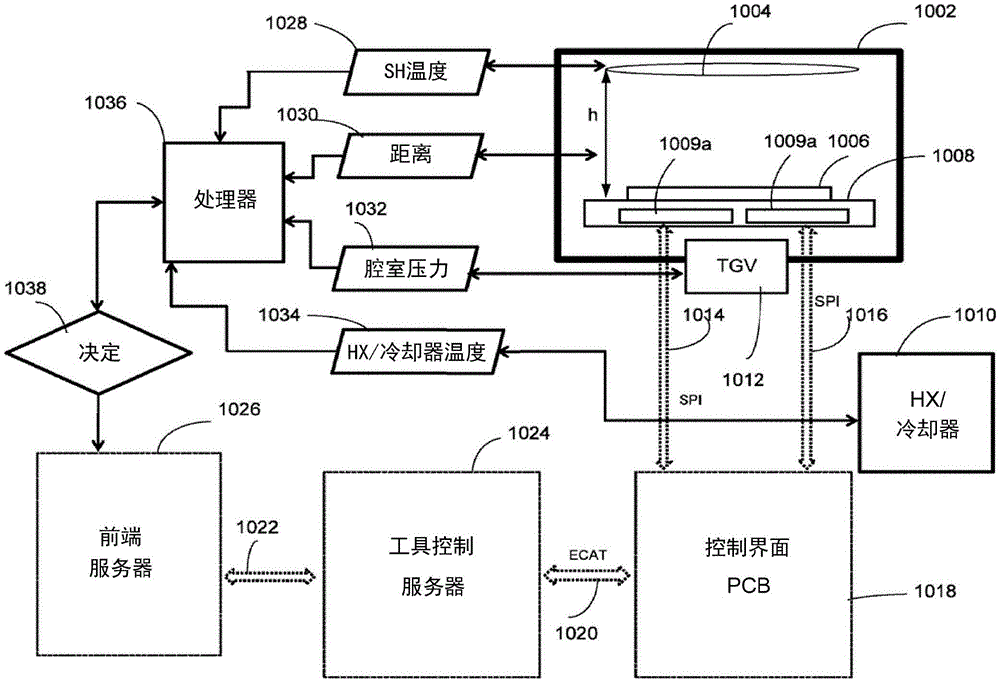
本文描述的实施方式总体上涉及半导体制造,并且更特定来说涉及用于温度控制的基板支撑组件的基于模型的控制架构及其在工艺控制中的使用。
背景技术
随着集成电路的装置图案的特征尺寸变小,所述特征的临界尺寸(CD)规格成为稳定和可重复的装置性能的更重要标准。由于腔室的不对称性(诸如喷头和基板温度、流导和RF场(视情况而定)),难以实现在整个处理腔室内处理的基板(在整篇说明书中还称为“晶片”)上的可允许的CD变化。
由于在基板下方的基板支撑组件的非均匀构造,跨基板表面的温度控制的均匀性可能是有挑战性的。例如,基板支撑件的一些区域具有气孔,而其他区域具有从气孔横向偏移的升降杆孔。其他区域可具有加热器电极。由于基板支撑件的结构可能会区域地变化,因此支撑组件与基板之间的热传递均匀性非常复杂,且很难获得所述热传递均匀性,从而导致跨基板支撑面的局部的热点和冷点,从而导致沿基板表面的处理结果的不均匀性。
基板支撑组件与基板之间的热传递的区域均匀性由于常规的基板支撑组件中所通常使用的热传递方法而变得更加复杂。例如,常规的基板支撑件通常仅具有边缘到中心的温度控制。当利用常规的基板支撑件的传热特征时,不能补偿基板支撑件内的局部的热点和冷点。
技术实现要素:
本文描述的实施方式提供了用于在处理放置在基板支撑组件上的晶片的腔室中,独立地控制基板支撑组件中的多个加热区的方法和系统。将来自多个温度检测器的温度反馈提供为工艺控制算法的第一输入。工艺控制算法的第二输入是使用模型所计算的一个或多个加热区的加热器温度的目标值。计算为一个或多个加热区实现加热器温度的目标值所需的加热器功率的目标值。控制腔室硬件以匹配加热器温度的目标值,所述目标值与对应于一个或多个工艺参数的当前最佳值的晶片特性相关。
在本公开内容的一个方面中,公开了一种方法,所述方法包括以下操作:收集来自多个温度检测器的温度反馈,所述多个温度检测器中的每一者经放置在支撑晶片的基板支撑组件的多个加热区中的相应加热区中;提供代表所述温度反馈的数据作为工艺控制算法的第一输入;提供如使用模型所计算的所述多个加热区中的一个或多个加热区的加热器温度的目标值来作为所述工艺控制算法的第二输入;计算加热器功率的目标值以用于实现针对所述一个或多个加热区的所述加热器温度的目标值,其中由运行所述工艺控制算法的处理器基于所述第一输入和所述第二输入来执行所述计算;以及控制包括所述基板支撑组件的处理腔室的腔室硬件,以匹配所述一个或多个加热区的所述加热器温度的目标值。
工艺控制算法可以是闭环算法,在所述闭环算法中重复以下操作:收集温度反馈、提供代表所述温度反馈的数据、提供加热器温度的目标值、计算加热器功率的目标值、和控制腔室硬件。
在本公开内容的另一方面中公开了一种系统,其包括:多个温度检测器,所述多个温度检测器中的每一者经放置在经配置为支撑晶片的基板支撑组件的多个加热区中的相应加热区中;处理器,所述处理器执行工艺控制算法。处理器从所述多个温度检测器接收温度反馈数据;提供所述温度反馈数据作为所述工艺控制算法的第一输入;使用服务器中存储的模型来计算所述多个加热区中的一个或多个加热区的加热器温度的目标值;提供通过所述模型所计算的所述一个或多个加热区的所述加热器温度的目标值来作为所述工艺控制算法的第二输入;基于所述第一输入和所述第二输入来计算加热器功率的目标值以用于实现针对所述一个或多个加热区的所述加热器温度的目标值;以及计算用于调节包括所述基板支撑组件的处理腔室的腔室硬件的量,以匹配所述一个或多个加热区的所述加热器温度的目标值。
附图说明
可通过参考实施方式来详细理解在上文简要概述且在下文更详细描述的本发明的上述特征,所述实施方式中的一些实施方式在附图中示出。然而,应注意附图仅示出了本公开内容的一些实施例,且因此不应视为对本发明范围的限制。
图1是具有基板支撑组件的处理腔室的一个实施例的示意性横截面侧视图,所述基板支撑组件具有多区加热器;
图2是具有多区加热器的加热器组件的另一实施例的透视图;
图3示出了根据本公开内容的实施例的包含两个并排布置的多区加热器的设施板的顶视图;
图4是根据本公开内容的实施例的多区加热器的顶视图;
图5是根据本公开内容的实施例的多区加热器的温度回读方案的表格描绘;
图6示出根据本公开内容的实施例的生成用于计算晶片蚀刻量的数学模型;
图7示出根据本公开内容的实施例的生成用于计算晶片温度的数学模型;
图8示出了根据本公开内容的实施例的生成用于从加热器功率和热交换器温度计算加热器温度的数学模型;
图9示出了根据本公开内容的实施例的生成用于从加热器功率计算加热器温度的数学模型;
图10示出了根据本公开内容的实施例的用于独立控制多区加热器中的一个或多个的系统的控制架构和功能;
图11示出了根据本公开内容的实施例的用于独立控制多区加热器中的每个多区加热器的系统的基于模型的控制架构;
图12示出了根据本公开内容的不同实施例的闭环加热器温度控制如何用于不同目的;
图13是用于闭环温度控制的方法的一个实施例的流程图;以及
图14示出了本公开内容的一些实施例可在其中运行的示例性计算机系统的框图;
可预期,在一个实施方式中公开的元件可在没有特定叙述的情况下有益地用于其他实施方式中。
具体实施方式
本公开内容的各方面针对一种基板支撑组件,其使得能够对基板支撑组件本身的温度进行局部调整,这又使得能够对放置在处理腔室内的基板支撑组件上的晶片的温度分布进行局部调整。闭环工艺控制算法利用来自基板支撑组件的温度反馈,并使用基于模型的方法来控制加热器功率,以最终控制与晶片特性相关的工艺参数。可独立控制每个加热区,从而提高整个晶片上温度调整的精细度。
在加热器具有多个加热区的情况下,常规工艺调整不具效率,这是因为常规工艺调整没有考虑区域间温度的影响,并且在实现任何合理性能之前通常需要进行多次调整迭代。本公开内容使用由机器学习算法所导出的基于模型的温度控制器。如此的控制器使用来自位于基板支撑组件中的电阻式加热元件附近的空间传感器的实时温度反馈,以及可用的腔室状态信息及其对温度传感器的影响的数学模型,来改进闭环控制性能。
在实施例中,基板支撑组件包括多个加热区。每个加热区可由位于所述加热区中的加热元件加热。每个加热区还可具有温度检测器,所述温度检测器向将在下文进一步详细描述的闭环工艺控制算法提供实时温度反馈。基板支撑组件可包括从两个加热区到数百个加热区的任何位置(例如,在一个实施例中的176个具有两个区域(“侧面”)的加热区,每个区域具有88个独立可控的加热区)。每个加热区包括单独的温度传感器,所述单独的温度传感器可为电阻式温度检测器(RTD),或在一些实施例中,所述单独的温度传感器可为热电偶。多个加热元件可共享一个或多个共用接地,且温度传感器可共享一个或多个其他共用接地。通过为每个加热元件具有单独的温度传感器,温度控制器可确定加热元件中的任一者何时发生故障。另外,若校准温度传感器,则所述温度传感器可确定特定加热区的温度且可用于与所述加热区相关联的加热元件的反馈控制。
尽管下文在蚀刻处理腔室中描述了基板支撑组件,但基板支撑组件可用于其他类型的处理腔室(诸如物理气相沉积腔室、化学气相沉积腔室及离子注入腔室等等)及期望横向温度分布的方位角调整的其他系统。还可预期,空间可调(还称为“可独立控制”)的加热器还可用于控制其他表面的温度,所述其他表面包括那些没有用于半导体处理的表面。
在一个或多个实施例中,基板支撑组件允许基于调整基板温度来校正真空处理(诸如蚀刻、沉积、注入等)期间基板边缘处的临界尺寸(CD)变化,以补偿腔室的不均匀性,诸如温度、流导、电场及等离子体密度等。
图1是具有基板支撑组件126的示例性蚀刻处理腔室100的纵向截面示意图。如上所述,基板支撑组件126可用于其他处理腔室,诸如等离子体处理腔室、退火腔室、物理气相沉积腔室、化学气相沉积腔室及离子注入腔室等。另外,基板支撑组件126可用于其他系统,所述其他系统中控制表面或工件(诸如基板)的温度分布的能力是有益的。对整个表面上许多离散区域的温度进行独立和局部的控制,可有利地实现温度分布的方位角调整、温度分布的中心到边缘的调整以及减少局部温度不均匀度(诸如热点和冷点)。
在一个实施例中,处理腔室100包括接地的腔室主体102。腔室主体102包括包围内部容积124的壁104、底部106和盖108。基板支撑组件126经设置在内部容积124中且在处理期间支撑基板134。
处理腔室100的壁104可包括开口(未示出),经由所述开口可将基板134自动地移入和移出内部容积124。泵送端口110形成在壁104中的一者中或形成在腔室主体102的底部106中,且泵送端口110流体地连接至泵送系统(未示出)。泵送系统可在处理腔室100的内部容积124内维持真空环境,并且可从处理腔室去除处理副产物。
气体面板112可经由一个或多个形成在腔室主体102的盖108和/或壁104中的入口114向处理腔室100的内部容积124提供工艺气体和/或其他气体。在一个实施例中,盖可包括喷头(未单独示出)。由气体面板112提供的工艺气体可在内部容积124内被激发以形成等离子体122,等离子体122被用于处理经设置在基板支撑组件126上的基板134。可由感应耦接到工艺气体的RF功率来激发工艺气体,所述工艺气体来自位于腔室主体102外部的等离子体施加器120。在图1所示的实施例中,等离子体施加器120是经由匹配电路118耦接到RF功率源116的一对同轴线圈。注意,本公开内容的范围比用于RF应用的基板支撑组件更宽。
控制器148经耦接到处理腔室100以控制处理腔室100的操作和基板134的处理。控制器148可以是通用数据处理系统,其可在工业环境中用于控制各种子处理器和子控制器。一般而言,控制器148包括与存储器174和输入/输出(I/O)电路176通信的中央处理单元(CPU)172、及其他常见部件。由控制器148的CPU执行的软件命令可使处理腔室例如将蚀刻剂气体混合物(即,工艺气体)引入至内部容积124中、通过施加来自等离子体施加器120的RF功率从工艺气体中形成等离子体122、以及在基板134上蚀刻材料层。
基板支撑组件126通常至少包括基板支撑件132。基板支撑件132可以是真空吸盘、静电吸盘(ESC)或其他工件支撑表面。尽管在一些示例中,ESC被明确地提及为基板支撑件132的类型,但本公开内容的范围不限于ESC。基板支撑组件126可另外包括加热器组件170,加热器组件170包括主电阻式加热元件154(也被称为主电阻式加热器)和多个另外的电阻式加热元件(在本文中称为空间可调加热元件140,也被称为可独立控制的加热器)。
基板支撑组件126还可包括冷却基座130,冷却基座130通过耦接至冷却基座的冷却器/热交换器144加热/冷却。冷却基座130可以可替代地与基板支撑组件126分离。基板支撑组件126可以可移除地耦接至支撑基座125。可包括台座基座128和设施板180的支撑基座125安装至腔室主体102。可周期性地从支撑基座125移除基板支撑组件126以允许翻新基板支撑组件126的一个或多个部件。
设施板180经配置成容纳一个或多个驱动机构,所述一个或多个驱动机构经配置成升高和降低多个升降杆。另外,设施板180经配置成容纳来自基板支撑件132和冷却基座130的流体连接。设施板180还经配置为容纳来自基板支撑件132和加热器组件170的电连接。大量连接可在基板支撑组件126的外部或内部延伸,且设施板180可提供用于连接到各个终端的接口。
基板支撑件132具有安装表面131和与安装表面131相对的工件表面133。展示于图1的示例中的基于ESC的基板支撑件130通常包括经嵌入在介电主体150中的吸盘电极136。吸盘电极136可经配置为单极或双极电极或其他合适布置。吸盘电极136可经由无线射频(RF)滤波器182耦接到夹持功率源138,夹持功率源138提供RF或直流(DC)功率以将基板134静电地固定到介电主体150的上表面。对于非基于ESC的基板支撑件132而言,可用其他类型的机制(诸如机械夹紧及基于真空的夹紧等)以将基板134固定到基板支撑件132。RF滤波器182防止用于形成处理腔室100内的等离子体122的RF功率会损坏电子设备或在处理腔室外部造成电危险。再次说明,本发明并不受限于基于ESC的基板支撑件和/或用于RF应用的基板支撑件。
基板支撑件132的工件表面133可包括气体通道(未示出),所述气体通道用于将背侧传热气体提供给在基板134和基板支撑件132的工件表面133之间限定的间隙空间。基板支撑件132还可包括用于容纳升降杆的升降杆孔(均未示出),以将基板134升高到基板支撑件132的工件表面133上方,以促进机器人移入和移出处理腔室100。
经温控的冷却基座130经耦接至作为传热流体源的冷却器/热交换器(HX)144。冷却器/热交换器144提供诸如液体、气体或上述组合之类的传热流体,所述传热流体经由设置在冷却基座130中的一个或多个导管160循环。可将流过相邻导管160的流体隔离成能够局部控制基板支撑件132与冷却基座130的不同区域之间的传热,这有助于控制基板134的横向温度分布。
流体分配器(未示出)可流体地耦接在冷却器/热交换器144的出口与温度受控的冷却基座130之间。操作流体分配器以控制提供给导管160的传热流体的量。流体分配器可设置在处理腔室100的外部、基板支撑组件126内部、台座基座128内部或其他合适的位置处。
加热器组件170可包括一个或多个主电阻式加热器154和/或经嵌入在主体152中的多个空间可调加热器140。在一些实施例中,主电阻式加热器和空间可调加热器可以是相同的元件。主体152可另外包括多个温度传感器(图1中未示出)。多个温度传感器中的每者可用于测量加热器组件的区域和/或与加热器组件的区域相关联的基板支撑件的区域的温度。在一个实施例中,加热器组件170被包括在基板支撑件132中。
可提供主电阻式加热器154以将基板支撑组件126的温度升高到进行腔室处理的温度。空间可调加热器140与主电阻式加热器154互补,且经配置为在由主电阻式加热器154限定的多个横向分离的加热区中的一者或多者内的多个离散位置中调整基板支撑件132的局部温度。空间可调加热器140对经放置在基板支撑组件126上的基板134的温度分布提供局部调整。主电阻式加热器154在全局宏观尺度上运行,而空间可调加热器140在局部微观尺度上运行。
主电阻式加热器154可经由RF滤波器184耦接到主加热器功率源156。主加热器功率源156可向主电阻式加热器154提供900瓦或更多的功率。控制器148可控制主加热器功率源156的操作,主加热器功率源156的操作通常经设置成将基板134加热到大约预定温度。在一个实施例中,主电阻式加热器154包括侧向分离的加热区,其中控制器148使主电阻式加热器154的一个区域相对于位于一个或多个其他区域中的主电阻式加热器154优先被加热。例如,可将主电阻式加热器154同心地布置在多个分开的加热区中。
在一个实施例中,主电阻式加热器154和/或空间可调加热器140可形成在基板支撑件132中。在此类实施例中,基板支撑组件126可在没有加热器组件170的情况下形成,其中基板支撑件132直接设置在冷却基座130上。调整加热器控制器202(其可为控制器148的一部分)可与冷却基座相邻设置,并有选择地控制各个空间可调加热器140。
基板支撑件132和/或加热器组件170可包括用于提供温度反馈信息的多个温度传感器。可将温度反馈信息发送到控制器148以控制由主加热器功率源156施加到主电阻式加热器154的功率从而控制冷却基座130的操作,和/或控制由调整加热器功率源142施加至空间可调加热器140的功率。可替代地或另外地,可将温度反馈信息提供给加热器控制器202,以确定空间可调加热器140的可操作性和/或控制施加到空间可调加热器140的功率。每个温度传感器可位于空间可调加热器中的一者附近且可用于确定附近的空间可调加热器的可操作性。在一个实施例中,每个温度传感器是电阻式温度检测器(RTD)。
处理腔室100中的基板134的表面温度可能受到泵、狭缝阀和/或其他因素对工艺气体的抽空的影响。冷却基座130、一个或多个主电阻式加热器154以及空间可调加热器140均有助于控制基板134的表面温度。
随着独立可控加热区的数量增加,在整个基板上产生定制的热分布的能力也增强。使整个基板上的临界尺寸的变化最小化的优势促使减小了基板表面的经确定的工艺温度中可接受的变化。空间可调加热器140通过减小温度分布的变化来改进由主电阻加热器154所产生的基板134的表面的温度分布。通过使用空间可调加热器140,可使温度分布在基板134的各个区域上变得均匀或以预定方式精确地变化。
可预期,可用不同的配置和方向来布置空间可调加热器140、主电阻式加热器154和温度传感器。例如,基板支撑组件126可具有多个用于加热基板134的空间可调加热器140、基板支撑组件126可不具有主电阻式加热器154,且基板支撑组件126可包括温度传感器以监视空间可调加热器140。替代地,基板支撑组件126可具有主电阻式加热器154和温度传感器,但基板支撑组件126可缺少空间可调加热器140。此类实施例中,温度传感器将设置在与包括主电阻式加热器154的平面邻近的平面中。在一个实施例中,空间可调加热器140和主电阻式加热器154在基板支撑组件126内彼此直接位于下方。空间可调加热器140可对由基板支撑件126支撑的基板134的温度分布提供微调控制,且温度传感器可提供空间可调加热器140操作的详细信息。
与空间可调加热器140相似,温度传感器可在加热器组件170的主体152上或内部形成或设置。可替代地,温度传感器可在静电卡盘132上或内部形成或设置。在一个实施例中,温度传感器是RTD。RTD的电阻系数可以是温度的函数。因此,RTD的电阻可基于温度的变化而变化。可测量每个RTD处的电阻以确定特定的空间可调加热器140是否正在工作和/或空间可调加热器140的温度。可替代地,温度传感器可为热电偶。
在一个实施例中,空间可调加热器140和温度传感器在形成加热器组件170的同时设置在加热器组件170内。在另一实施例中,空间可调加热器140和/或温度传感器直接设置在基板支撑件132的安装表面131上。在一些实施例中,主电阻式加热器154类似于空间可调加热器140来制造。在其中主电阻式加热器154类似于空间可调加热器140来制造的实施例中,可以可选地在没有额外的空间可调加热器140的好处的情况下利用主电阻式加热器。换句话说,基板支撑组件126的主电阻式加热器154本身可以是空间可调的,即,主电阻式加热器154被分成多个离散的电阻式加热元件。在此类实施例中,可在每个主电阻加热器154附近设置分离的温度传感器。以小电阻加热器的形式分割主电阻式加热器154允许了局部控制基板134的表面上的热点和冷点。取决于要实施的温度控制的水平,空间可调加热器140的额外层是可选的。
图2示出了基板支撑组件126的替代配置。此基板支撑组件200在顶部具有加热器组件203,在底部具有轴204。电连接206将加热器组件203中的加热元件耦接到外部温度控制器(诸如控制接口印刷电路板(PCB),如图10中更详细地描述)。
图3示出了根据本公开内容实施例的包含并排设置的两个多区加热器的设施板的顶视图。尽管在此示例中,设施板380内有两个主要加热区,每个加热区具有其自身的多区加热器303a和303b,但设施板380内可有任意数量的加热区。可彼此独立地控制每个加热区。
图4是穿过加热器组件170的主体152的截面图,其从顶部示出了空间可调加热器140。加热器组件170可包括多个空间可调加热器140,其实现了加热器组件170和基板支撑件132之间的热传递。每个空间可调加热器140可横向布置在整个加热器组件170上,并在加热器组件170内限定区450,以向与所述区450对准的加热器组件170的区域(和主电阻式加热器154的一部分)局部提供额外的热。在给定的基板支撑组件126经配置成与整个基板(例如300mm基板)一起使用的实施例中,可设想有数百个空间可调加热器140。
加热器组件170可进一步包括多个温度传感器。每个温度传感器可横向布置在整个加热器组件170上,使得每个温度传感器都在加热器组件170中的由空间可调加热器140限定的区450内。每个温度传感器可测量其所设置于其中的区450的温度和/或确定在所述区450中的空间可调加热器140的可操作性。另外,在由主电阻式加热器154限定的区域中的一个或多个温度传感器可用于测量区的温度和/或确定主电阻式加热器154的可操作性。通过单独和独立地控制提供给每个空间可调加热器140的功率,从而控制穿过区450的热传递,可实现逐像素方法的温度控制,从而能实现基板134的特定点待加热或待冷却,使得能实现真正寻址的横向温度分布的调整和基板134的表面的控制。
调整加热器控制器148可在相对于其他区450的每个区450处调节加热器组件170中的空间可调加热器140的温度。替代地,调整加热器控制器148相对于另一组区450跨过一组区450来调节加热器组件170中的一组空间可调加热器140的温度。调整加热器控制器202可切换各个空间可调加热器140的开/关状态和/或控制工作周期。替代地,调整加热器控制器148可控制传递到各个空间可调加热器140的功率量。
在一个实施例中,加热器控制器148从多个温度传感器接收温度测量值。在一个实施例中,加热器控制器148可接收每个温度测量值作为电阻测量值。加热器控制器148接着可基于电阻温度转换模型将电阻测量值转换为温度测量值。每个温度传感器可使用单独的电阻温度转换模型。替代地,可将相同的电阻温度转换模型用于多个温度传感器。可通过执行对温度传感器的校准来产生电阻温度转换模型。
加热器控制器148可将每个温度传感器的所接收的温度测量值与所述温度传感器的所预期的温度测量值进行比较。温度传感器的所预期的温度测量值可基于与温度传感器所位于的区相关联的空间可调加热器140的电流设置和/或主电阻式加热器154的电流设置。若温度传感器的所预期温度测量值与所接收的温度测量值之间的差值超过阈值,则加热器控制器148可调整与温度传感器相关联的特定空间可调加热器140的工作周期和/或功率。替代地或另外地,加热器控制器148可调节与温度传感器相关联的主电阻式加热器的工作周期和/或功率。
在一个实施例中,每个区450可例如使用热扼流圈416与相邻区450热隔离,热扼流圈416使得能够进行更精确的温度控制。在另一个实施例中,每个区450可热结合到相邻区,从而沿着加热器组件170的上表面产生类似的(即,平滑的或混合的)温度分布。
使用独立可控的空间可调加热器140可将整个基板上的局部温度均匀性控制到非常小的公差,且在处理基板134时可进行精确的工艺和CD控制。此外,空间可调加热器140尺寸小且密度高,使得能够在基板支撑组件126上的特定位置处进行温度控制,而基本上不影响相邻区域的温度。这允许了补偿局部的热点和热点,而不会引起偏斜或其他温度不对称性。具有多个空间可调加热器140的基板支撑组件126具有控制在基板支撑组件126上处理的基板134的温度均匀性的能力。
每个空间可调加热器140皆拥有电阻404,电阻404终止于端子406、408。当电流进入一个端子(诸如标为406的端子)并存在另一个端子(诸如标为408的端子)时,电流流经电阻404的导线并产生热。空间可调加热器140可具有设计功率密度,以沿基板支撑组件126的外表面426提供适当的温度升高。电阻器404释放的热量与流经所述电阻器的电流的平方成正比。
空间可调加热器140可经配置成图案490,以有效地沿着基板支撑组件126的表面产生热分布。图案490可围绕中点对称,同时在孔422内和周围提供间隙以进行升降杆或其他机械、流体或电连接。每个空间可调加热器140可由调整加热器控制器148控制。调整加热器控制器148可开启限定了加热器440的单个空间可调加热器140,或调整加热器控制器148可开启多个空间可调加热器140,多个空间可调加热器140经分组以限定内部楔形件462、周边组464、饼形区域460或其他包括非连续配置的几何配置。以此方式,可在沿着基板支撑组件126的表面的独立位置处精确地控制温度,此种独立位置并不限于如本领域中已知的同心环。尽管所示的图案包括较小单元,但所述图案可替代地具有较大和/或较小的单元、延伸到边缘或具有其他形式。
图4中也示出的是RTD 405,RTD 405为一种类型的温度传感器。RTD 405经定位在空间可调加热器140的上方或下方。如图所示,RTD 405在大多数情况下将比空间可调加热器140小。RTD405可以是基于温度改变电阻的特定类型的电阻器。在一个实施例中,RTD 405是铂丝。替代地,RTD 405可以是本文所讨论的任何其他材料。RTD 405终止于端子407和端子409。可经由端子将电流发送穿过RTD 405,且可测量RTD 405的电阻以确定空间可调加热器140的温度。可选择RTD 405的材料、导线长度和导线厚度以控制RTD 405敏感的温度范围。
可用网格形式来布置空间可调加热器140,所述网格形式限定温度控制区450的阵列,所述温度控制区域的阵列还以xy网格图案、多边形图案(例如,六方最密堆积)、极性阵列图案布置在同心通道图案中。应当理解,如上所述,可成组或单个启动空间可调加热器140。
空间可调加热器140的数量和密度有助于将整个基板上的温度均匀性控制到非常小的公差的能力,这使得在处理基板134时能够进行精确的处理和CD控制。另外,相对于另一个空间可调加热器140对空间可调加热器140的单独控制使得能够在基板支撑组件126中的特定位置处进行温度控制,而基本上不影响相邻区域的温度,使得能够在不引入偏斜或其他温度不对称的情况下补偿局部的热点和热点。在一实施例中,基板支撑组件126中的多个空间可调加热器140与主电阻式加热器154结合具有将在其上处理的基板134的温度均匀性控制为小于约±0.3摄氏度的能力。空间可调加热器140允许在基板支撑组件126上所处理的基板134的横向温度分布的横向和方位角调整两者。
相对于多路控制,接线方案提供了对空间可调加热器140的单独控制。单独控制使任何一个空间可调加热器140或对空间可调加热器140的选择与任何其他空间可调加热器140或对空间可调加热器140的选择一样而为同时有效的。接线方案允许相对于多个空间可调加热器中的另一者来独立控制多个空间可调加热器中的一者的输出,并允许在空间可调加热器140处实现定制的温度分布的快速的响应时间。
控制器148可同时控制施加到相对于另一者的一个或多个选定的空间可调加热器140的工作周期、电压、电流或功率持续时间中的至少一者或多者。
图5示出了如何经由电连接将RTD的实时模拟温度读数传送到数字解码器装置,所述数字解码器装置以数字数据形式提供RTD行/列温度的回读。图5中所示的特定示例示出了从90个RTD读回的温度,所述温度分布在9列及11行上。
从RTD收集的温度回读数据用于建立数学模型,所述数学模型用于设计多区加热器中加热区之基于模型的独立控制。
图6至图7示出了两个模型,当加热器温度数据作为输入被馈送到模型时,所述两个模型分别预测晶片蚀刻量和晶片温度。请注意,实时RTD数据可用于训练模型以提高预测结果的准确性,但代表加热器温度的历史可信赖数据还可用于构建模型。模型的其他输入包括各种工艺参数。在图6和图7所示的示例中,所使用的工艺参数是喷头温度、腔室压力及到喷头的距离(也称为喷头与基板支撑组件中的加热器之间的距离)。请注意,还可使用其他工艺参数,例如,腔室主体温度、热交换器温度、升降杆高度和工艺气体等。
特定来说,在图6所示的示例中,通过模型来基于加热器温度、喷头温度、腔室压力及喷头与基板支撑组件之间的距离的变化来预测晶片蚀刻量。在图7所示的示例中,晶片温度由模型基于加热器温度、喷头温度、腔室压力及喷头与基板支撑组件之间的距离的变化来预测。注意到,可使用单独的模型来预测每个晶片特性,或可使用单个模型来预测多个晶片特性,诸如晶片蚀刻量和晶片温度。
注意,可能存在能够基于不同的工艺参数(例如,热交换器温度或加热器功率)来预测加热器温度的另一模型(或一组模型)。特定来说,在图8所示的示例中,模型基于热交换器温度的变化来预测加热器温度。由于加热器温度是传递给加热器的功率及热交换器提供的冷却剂流量的函数,因此当要传递给加热器的目标功率作为除热交换器温度外的输入时,图8中的模型可以更准确地预测加热器温度。图9示出了仅基于加热器功率变化的加热器温度模型。可使用以下方法的组合来生成图6至图9中的每个模型,所述方法包括用于导出定义模型结构的微分方程的第一原理分析及机器学习算法,所述机器学习算法基于可得数据来训练此类模型,所述可得数据从不同的腔室配置(即,不同的喷头温度、腔室压力、到喷头的距离、热交换器功率和加热器功率)的腔室收集。可导出机器学习算法以对每个数学模型执行离线递归训练,以允许此类模型表示基板的热行为和蚀刻动态行为,并表示基板支撑件内每个加热区的热行为。
图10示出了框图,所述框图表示加热器温度的基于模型的闭环控制中的系统部件的控制架构和功能,所述控制架构和功能继而实现了工艺参数的基于模型的控制。从腔室1002收集的示例性工艺参数是喷头1004的温度1028、喷头与基板支撑组件1008之间的距离1030(显示为“h”)及由节流阀(TGV)1012供应的腔室压力1032。由经整合到基板支撑组件1009的多区加热器1009a和1009b来加热晶片1006。经由串行外设接口(SPI)通信链路1014和1016或其他类型的通信链接来将RTD温度数据传递至控制界面模块1018。控制界面模块功能可由模块1018内的印刷电路板(PCB)实行。模块1018直接或经由工具控制服务器(TCS)1024与前端服务器(FES)1026通信耦接。在实施例中,前端服务器1026和工具控制服务器1024及模块1018可经由用于控制自动化技术的以太网络(ECAT)通信链路1020和1022或其他类型的通信链路来耦接。
处理器1036基于模型(例如,图6至图9中所示的模型)和从腔室1002收集的实时输入来执行闭环控制算法。可从腔室之外的其他硬件收集额外输入,所述其他硬件为诸如热交换器(HX)/冷却器1010。HX/冷却器1010可向处理器提供温度1034。在一个实施例中,用于一个或多个训练过的机器学习模型的输入数据可包括向量,所述向量包括喷头温度1028、距离1030、腔室压力1032、热交换器的温度1034和/或一个或多个与加热区相关的温度传感器的温度。一个或多个模型可处理输入数据以生成输出。输出可以是自动计算喷头温度、喷头与基板支撑组件之间的距离、腔室压力及热交换器温度的服务。处理器1036做出关于哪个腔室硬件需要被控制的决定1038,将决定1038传送至FES 1026。在一些实施例中,处理器1036是FES 1026的一部分。
服务器(可以是工具控制服务器1024)从前端服务器1026接收计算出的加热器功率的目标值,并计算控制或调节腔室硬件以为一个或多个加热区匹配加热器温度的目标值的量。控制腔室硬件可包括控制加热器电子设备,以将加热器功率的目标量传送到一个或多个独立于其他加热区的加热区。控制腔室硬件还可包括控制HX/冷却器温度,这是因为加热器温度是加热器功率和冷却剂流量两者的函数。例如,若某个区域变得太热,则需要供应较冷的流体以将温度降低到目标值,并且需向所述区域中的加热器传递较少的功率。另一方面,若区域变得太冷,则需要供应较热的流体以将温度降低到目标值,且需向所述区域中的加热器传递较多的功率。
图11示出了由图10中所示的系统所实施的基于模型的控制架构1100的更多细节,控制架构1100系用于独立地控制多区加热器的每个区。如图11所示,将晶片1102放置在具有一个或多个多区加热器的基板支撑组件1104上。加热器电子设备1118向加热器提供功率,且热交换器1106提供流体以控制基板温度。将来自RTD的实时温度数据1108提供给闭环加热器温度控制算法1114。算法接收由模型1112基于目标晶片温度和/或蚀刻量1111计算出的目标加热器温度值1110。模型1112可以是图6和图7中所示模型的逆模型,所述逆模型中基于加热器温度来计算晶片蚀刻量和/或晶片温度。闭环加热器温度控制算法1114基于目标加热器温度110和加热器温度反馈1108来输出目标加热器功率1116,将目标加热器功率1116传送至加热器电子设备1118,以实现对加热区的独立控制。可如本公开内容中前文所述使用机器学习算法来完成模型的生成。图11中的逆模型表示是如何使用模型的功能表示。由于每个区域的温度可能会彼此有所不同(这归因于区的表面积大小不同且每个区周围的相邻区的不同集),因而无法将针对一个区域获得的相同模型应用于所有区域。此外,由于相邻区域之间的交互作用,每个区域都不可能有独立的模型。在此实施例中考虑的温度控制模型包括单个大型模型,所述单个大型模型同时监视来自可用RTD传感器的所有区的温度反馈,且基于每个区的温度和相应的相邻温度的行为,同时为基板支撑件的所有区域生成功率。目标加热器温度1110包括针对基板支撑件的每个区域的单独的目标温度。这允许闭环加热器温度控制器1114在基板1102上实现期望的温度模式。类似地,反向的晶片温度和反向的晶片蚀刻量模型可为基板支撑件的每个区域提供单独的目标加热器温度1110,以允许基板1102达到目标晶片温度和蚀刻量1111(空间分布)。
另一模型1128(另一模型1128可以是图8中所示的模型的逆模型)使用目标加热器温度1110作为输入并输出目标热交换器温度1120,将目标热交换器温度1120传送到热交换器1106。
图12示出了闭环加热器温度控制架构1200(闭环加热器温度控制架构1200类似于图11中描述的1114)如何为图10中所示的系统服务于不同的目的。架构1200的核心是控制算法1202,算法1202从RTD接收加热器温度反馈1216。图11中所展示的逆模型计算并提供目标加热器温度1212(类似于图11中的1110)作为闭环加热器温度控制算法的输入。闭环加热器温度控制算法使用加热器功率-温度模型1204来输出目标加热器功率1214,将目标加热器功率1214供应给加热器电子设备,如图11所示。
另外,算法可用于使用功率和温度反馈信息的晶片错位检测(1206)。可选地,可产生晶片错位警告信号1218。可使用有关基板支撑件边缘周围的温度和功率使用的信息来检测晶片的错位。通过利用图4中所示的区布局的优势来实现此功能:可在基板支撑件的圆形边缘处进行独立温度测量允许了检测是否由于因基板错位而使任何此类区部分或全部暴露出来。
此外,此算法可促进检测硬件状态(1208),且可选地使用FES的图形用户界面(GUI)来显示硬件状态1220。
此外,此算法可用于决定多个腔室上不同设备之间的不匹配(1210),并通过调整目标加热器温度进行补偿。特定来说,可使用关于参考腔室的信息及相应的可接受的变化极限来设计补偿器1210。在不同的腔室上安装新的台座加热器后,可实时地或离线地将有关基板支撑件所有区的温度反馈测量和功率使用的可用信息与设计阶段期间提供的参考信息进行比较。这允许检测并警告任何硬件故障或超出预定义的可接受限制的不匹配。此外,每当根据不匹配的类型而允许时,关于不匹配的定量信息可用于偏置目标加热器温度1110,以使基板性能符合目标规格1111。
图13是用于闭环温度控制的方法1300的一个实施例的流程图。方法1300可由处理逻辑来执行,所述处理逻辑可包括硬件(例如,处理装置、电路、专用逻辑、可编程逻辑、微代码、硬件装置及集成电路等)、软件(例如,在处理装置上运行或执行的指令)或上述组合。方法1300可由图10的系统的部件来执行。为了实现闭环控制,可重复框1320至1360中的操作。
方法1300从框1310开始,如上所述地将RTD放置在与基板支撑组件整合在一起的多区加热器的不同加热区处。
在框1320处,从RTD收集温度反馈。可实时收集温度反馈,即,在测量当前温度数据和通过改变腔室硬件来调节温度之间没有明显的延迟。
在框1330处,提供实时温度反馈数据来作为闭环工艺控制算法的输入。已参考图10至图12讨论了工艺控制算法的示例。
在框1340处,将每个加热区的加热器温度的目标值设置成闭环工艺控制算法的另一输入。加热器温度的目标值由诸如晶片温度-加热器温度模型之类的模型计算。晶片温度是工艺参数的函数,所述工艺参数是诸如喷头温度、腔室压力、加热器与喷头的距离等(如图6、图7和图10中所示)。
在框1350处,算法输出加热器功率的目标值。注意,此算法可计算要被输送到多区加热器的仅一个区的功率,或可计算要被输送到多区加热器的多个区的功率的相应值。注意,在一些实施例中,采用多个多区加热器。此算法具有以与多区加热器的空间配置相称的适当精细度来计算功率的能力。
在框1360处,控制腔室硬件以匹配与工艺参数的最佳值相关的加热器温度的目标值。推荐参数的最佳值可以是对应于已知最佳方法(BKM)的历史参数。例如,可控制加热器的功率(可选地,可控制热交换器的温度)以在多区加热器的特定区达到特定温度,从而得到的晶片温度表明工艺参数为最佳。使用工艺参数的BKM值作为参考,可对当前工艺进行调整,以提出一种改进的配方,所述改进的配方更适合于特定的腔室配置以使产量最大化。
本领域技术人员将理解,尽管图13中的流程图示出了特定的序列或顺序,但除非另有说明,否则可修改工艺的顺序。因此,示出的实施例应当仅被理解为示例,且可用不同顺序执行示出的工艺,且可平行地执行一些工艺。另外,在各种实施例中可省略一个或多个工艺。因此,并非在每个实施例中都需要所有工艺。其他工艺流程也为可能的。
图14示出了计算机系统1400的示例机器,计算机系统1400的示例机器中可执行用于使机器执行本文所讨论的方法中的任何一者或多者的一组指令。一些实施例中,计算机系统1400可用于执行控制器的操作(例如,以执行算法以独立地控制多区加热器中的温度)。在替代实施例中,机器可连接(例如联网)到LAN、内部网络、外部网络和/或因特网中的其他机器。机器可在客户端-服务器网络环境中以服务器或客户端机器的身份运行,可作为对等(或分布式)网络环境中的对等机器运行,或可作为云端计算架构或环境的服务器或客户端机器运行。
机器可以是个人计算机(PC)、平板PC、机顶盒(STB)、个人数字助理(PDA)、蜂窝式电话、网络(Web)设施、服务器、网络路由器、交换器或桥接器,或任何能够执行一组指定所述机器要执行的操作的指令(顺序指令或其他指令)的机器。此外,虽然示出单个机器,但是术语“机器”还应被理解为包括机器的任何集合,所述机器的任何集合单独地或共同地执行一组(或多组)指令以执行本文讨论的任何一个或多个方法。
示例性计算机系统1400包括处理装置1402、主存储器1404(例如,只读存储器(ROM)、闪存、诸如同步DRAM(SDRAM)之类的动态随机存取存储器(DRAM)等)、静态存储器1406(例如,闪存及静态随机存取存储器(SRAM)等)和数据存储系统1418,它们经由总线1430而彼此通信。
处理装置1402代表一个或多个通用处理装置,诸如微处理器及中央处理单元等。特定来说,处理装置可以是复杂指令集计算(CISC)微处理器、精简指令集计算(RISC)微处理器、超长指令字(VLIW)微处理器、或实施其他指令集的处理器,或是实施指令集组合的处理器。处理装置1402还可为一个或多个专用处理装置,诸如专用集成电路(ASIC)、现场可编程门阵列(FPGA)、数字信号处理器(DSP)及网络处理器等。处理装置1402经配置为执行指令1426以执行本文所讨论的操作和步骤。计算机系统1400可进一步包括网络接口装置1408,以经由网络1420进行通信。
数据存储装置1418可包括机器可读介质1424(也称为计算机可读介质),其上存储有体现本文所述方法或功能中的任何一者或多者的一组或多组指令1426或软件(例如,用于闭环工艺控制算法1114的指令)。在计算机系统1400执行指令1426的期间,指令1426还可全部或至少部分地驻留在主存储器1404内和/或处理装置1402内,主存储器1404和处理装置1402还构成机器可读存储介质。
在一个实施例中,指令1426包括用于运行算法以控制工艺参数的指令。尽管在示例实施例中将机器可读存储介质1424图示成单个介质,但术语“机器可读存储介质”应被认为包括存储一个或多个指令集的单个介质或多个介质。术语“机器可读存储介质”还应被认为包括能够存储或编码一组指令以供机器执行且使机器执行本发明的任何一个或多个方法的任何介质。术语“机器可读存储介质”因此应被认为包括但不限于固态存储器、光学介质和磁性介质。
已根据对计算机存储器内的数据位元的操作的算法和符号表示来呈现前述详细描述的某些部分。所述算法描述和表示是数据处理领域技术人员用来最有效地向所述领域中其他技术人员传达其工作实质的方式。在本文中,算法通常被认为是引起期望结果的自我一致的操作序列。操作是需要对物理量进行物理操纵的操作。一般而言,尽管不是必须的,所述量采取能被存储、组合、比较和以其他方式操纵的电信号或磁信号的形式。主要出于通用的原因,已证明有时将所述信号称为位、值、元素、符号、字符、项、数字等是方便的。
然而,应所述牢记,所有这些和类似术语均应与适当的物理量相关联,且仅仅是应用于这些量的方便标签。本公开内容可参考计算机系统或类似的电子计算装置的动作和处理,所述动作和处理将表示为计算机系统的寄存器和存储器内的实体(电子)量的数据操纵和转换为类似地表示为计算机系统存储器或其他此类信息存储系统内的实体量的其他数据。
本公开内容还涉及用于执行本文中的操作的设备。此设备可被特别建构成用于预期目的,或此设备可包括由存储在计算机中的计算机程序选择性地启动或重新配置的通用目的计算机。如此的计算机程序可存储在计算机可读存储介质中,所述计算机可读存储介质为诸如(但不限于)任何类型的磁盘,所述任何类型的磁盘包括软盘、光盘、CD-ROM和磁光盘、只读存储器(ROM)、随机存取存储器(RAM)、EPROM、EEPROM、磁卡或光卡或任何类型的适用于存储电子指令的介质,每者都耦接到计算机系统总线。
本文所呈现的算法和显示与任何特定的计算机或其他设备并非固有地相关。各种通用系统可与根据本文的教示的程序一起使用,或可证明建构更专用的设备来执行方法是方便的。各种所述系统的结构将在以下说明中列出。另外,没有参考任何特定的程序语言来描述本公开内容。将应当理解,可使用各种程序语言来实施如本文所述的本公开内容的教示。
可将本公开内容设置为计算机程序产品或软件,其可包括其上存储有指令的机器可读介质,所述指令可用于对计算机系统(或其他电子装置)进行编程以执行根据本公开内容的工艺。机器可读介质包括用于以机器(例如,计算机)可读的形式存储信息的任何机制。在一些实施例中,机器可读(例如,计算机可读)介质包括机器(例如,计算机)可读存储介质,诸如只读存储器(“ROM”)、随机存取存储器(“RAM”)、磁性磁盘存储介质、光学存储介质及闪存部件等。
在前述说明书中,已参考本公开内容的特定示例来描述本公开内容的实施例。显而易见的是,在不背离如权利要求中阐述的本公开内容的实施例的更广泛的精神和范围的情况下,可对本公开内容的实施例进行各种修改。说明书和附图因此应被认为是说明性的而不是限制性的。
本文用于企业家、创业者技术爱好者查询,结果仅供参考。