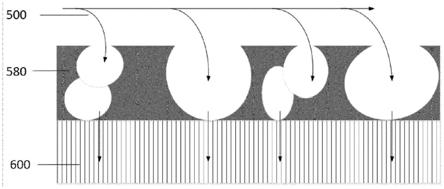
具有多孔涂层的催化剂基材
1.说明书
2.本发明涉及用于涂覆催化剂基材的涂料悬浮液,用于涂覆催化剂基材的方法,和根据本发明涂覆的催化剂基材。具体地,将可使用其制备多孔层的涂料悬浮液用于制备经涂覆的催化剂基材。
3.机动车辆中的内燃机的废气通常含有有害气体一氧化碳(co)和烃类(hc)、氮氧化物(nox)和可能的硫氧化物(sox)以及颗粒,所述颗粒主要由纳米级烟尘颗粒、可能粘附的有机附聚物以及灰分残留物组成。这些被称为主要排放物。co、hc和颗粒是发动机的燃烧室内部的燃料不完全燃烧的产物。当燃烧温度局部超过1400℃时,进气中的氮和氧在气缸中形成氮氧化物。硫氧化物是有机硫化合物燃烧引起的,有机硫化合物中的少量始终存在于非合成燃料中。为了去除机动车辆废气中这些对健康和环境有害的排放物,已经开发了多种用于净化废气的催化技术,其基本原理通常基于引导需要净化的废气通过其上施加有催化活性涂层的流通式或壁流式蜂窝主体或整料。
4.涂层中的催化剂促进各种废气组分的化学反应,同时形成非有害产物,诸如二氧化碳和水,其中当废气流经过滤器的多孔壁时,壁流式过滤器另外从废气中去除有害烟尘和灰分颗粒。具体地,在经涂覆的流通式基材的情况下,而且在通道壁上具有涂层的壁流式过滤器基材的情况下,催化涂层必须具有一定孔隙率,其具有可流动通过的开孔,并且因此具有良好的气体渗透率。一方面,多孔层的孔隙率和因此较高的自由表面积使得废气能够更好地触及层中的催化活性成分,并且另一方面,其仅允许气体自由进入和通过多孔过滤器壁。在多孔过滤器壁上的大部分封闭的、不可渗透的涂层的情况下,废气背压将增加到不可接受地大的程度,并且因此导致减小的发动机扭矩,并且可导致增加的燃料消耗。因此,具体地对于过滤器应用而言,期望催化涂层具有多孔结构,该多孔结构具有良好的气体渗透率并且基本上不增加废气背压。
5.由金属或陶瓷制成的温度稳定的蜂窝主体组成的经涂覆的催化剂基材通过使基材与涂料悬浮液(基面修补涂料)接触来制备。涂料悬浮液由无机涂层材料(例如氧化铝、氧化钛)、催化活性贵金属(诸如铂、钯或铑),以及可能的其他成分(诸如储氧材料)或其他催化活性物质(诸如沸石)的浆料组成。为了调节悬浮液的粘度和另外的流变特性,它们还可含有增稠剂、润湿剂、消泡剂或沉降抑制剂。在基材已涂覆有液体修补基面涂料之后,将其干燥并在500℃至700℃的温度下煅烧,从而形成紧密粘附的氧化物层,其中包埋催化活性元素。
6.过去经常努力增加过滤器或流通式基材上的这些催化活性涂层的孔隙率。孔隙率通常被理解为意指孔的空隙体积与物质或主体的总体积的比率。为了增加自由表面的可及性和涂层的气体渗透率,可流动通过并彼此连接并通向环境的开孔是特别重要的。由闭合孔确定的孔隙率的分数与气体渗透率和对催化活性中心的可及性不相关。
7.wo2009049795公开了一种涂料悬浮液和用该涂料悬浮液涂覆催化剂基材的方法,该涂料悬浮液含有无机载体材料和聚合物造孔剂,该聚合物造孔剂由直径为0.5μm至2μm的附聚的聚合物初级颗粒组成并且以至多8重量%存在于该涂料悬浮液中。聚合物造孔剂在
此选自合成聚合物,诸如聚乙烯、聚丙烯、聚氨酯、聚丙烯腈、聚丙烯酸酯、聚甲基丙烯酸酯、聚乙酸乙烯酯或聚苯乙烯。在涂料悬浮液已施加并在120℃下干燥之后,层中的有机聚合物造孔剂通过550℃下的温度处理来烧尽以形成孔。专利说明书不提供关于通过添加造孔剂增加涂层的孔隙率达到的程度的任何信息。
8.在wo2017209083 a1中描述了使用在较高温度下烧尽的有机造孔剂在催化涂层中产生孔的相同原理。本技术要求保护用于纯化废气的过滤器壁上的多孔催化活性层。多孔层具有限定的孔隙率和孔径分布,并且使用含有催化活性载体材料和有机造孔剂的涂料悬浮液制备。粒径为2μm至20μm的物质,诸如淀粉、碳或活性炭粉末和有机聚合物,诸如聚乙烯、聚丙烯、三聚氰胺或聚甲基丙烯酸甲酯树脂,被提出作为可能的造孔剂。造孔剂的体积与载体材料的体积的比率在3至1,至多15至1的范围内。通过在500℃下将有机造孔剂烧尽来产生层的孔结构。wo08153828 a2还公开了一种用于由无机颗粒制备多孔层的方法。在该文献中,将可热分解粉末(诸如蛋白质、淀粉或聚合物颗粒)用作无机膜的造孔剂。
9.所有这些解决方案均共享以下共性:相对于悬浮液中的固体含量,含有相当大体积分数的由有机颗粒制成的造孔剂,以便产生足够高的层的孔隙率。为了制备孔隙率为大约50体积%(与过滤器基材的通道壁的孔隙率相当)的层,并且仅使用示例性计算,由氧化铝(3.95g/cm3)和作为有机造孔剂的聚乙烯树脂(0.9g/cm3)的纯密度得出大约20重量%的造孔剂含量。涂料悬浮液中的这种高比例的有机物导致在层煅烧期间产生相当大量的有机分解产物。取决于所使用的聚合物,所述有机分解产物可导致处于煅烧炉爆炸风险中的气氛,并且也可能对健康有害。然后必须通过昂贵且复杂的热后燃烧将它们从废气中去除。另外,存在以下风险:由于高含量的有机添加剂且不完全的热分解,大量不可取的残基保留在层中,并且由此降低了催化效果。
10.因此,仍然需要一种用于使用造孔剂在催化剂基材上制备多孔催化活性涂层,但在煅烧期间不产生相当大量的有机分解产物的所述问题的解决方案。因此,本发明基于提供涂料悬浮液和用于在催化剂基材上制备多孔催化活性涂层的方法的目的,所述涂层具有高孔隙率和自由表面积,并且在制备期间仅发生低有机排放。此外,本发明的目的是提供包含具有多孔涂层的催化剂基材的催化剂。
11.该目的通过用于涂覆载体基材的涂料悬浮液来实现,所述涂料悬浮液具有至少一种无机涂层材料和至少一种聚合物有机造孔剂,其中该聚合物造孔剂由水不溶性溶胀颗粒构成,所述水不溶性溶胀颗粒具有40重量%至99.5重量%的水含量。完全意料不到地,在干燥过程期间,在所施加的催化涂料悬浮液中的高水含量情况下,这些溶胀的聚合物造孔剂仅略收缩。它们在干燥期间基本上保持其形状和尺寸,并且因此防止粉状涂层材料形成封闭的不可渗透层。仅在最终煅烧期间,它们才由于热分解而消失,但是这样做时自然会留下对应的孔。由于溶胀的聚合物造孔剂具有40
–
99.5%,优选地70
–
98%,非常优选地80-95%的高水含量,因此与常用的有机造孔剂相比,来自形成它们的聚合物的有机分解产物的量非常小。造孔剂诸如碳(石墨、活性炭、石油焦和炭黑)、淀粉(诸如玉米、大麦、豆类、土豆、大米、木薯、豌豆、西米棕榈、小麦、美人蕉)、大米和胡桃壳粉以及聚合物(诸如聚丁烯、聚甲基戊烯、聚乙烯、聚丙烯、聚苯乙烯、聚酰胺、环氧树脂、abs、丙烯酸酯和聚酯)已属于现有技术。
12.优选的是使用被称为是水凝胶的物质作为水不溶性溶胀颗粒。水凝胶通常被理解
为意指含水但水不溶性的聚合物,其分子例如通过共价键或离子键化学连接,或例如通过使聚合物链缠结物理连接,以形成三维网络。由于掺入的亲水性聚合物组分,它们在水中溶胀,其中体积显著增加,但不损失其材料内聚力("hydrogel"entry in:wikipedia,the free encyclopedia;版本有效日期:2018年11月18日,03:24utc;url:https://de.wikipedia.org/w/index.php?title=hydrogel&oldid=182851302;enas m.ahmed,hydrogel:preparation,characterization,and applications:a review,journal of advanced research(2015)6,105
–
121)。优选地,形成水凝胶的聚合物包含选自天然聚合物和合成聚合物的聚合物,所述天然聚合物为藻酸盐、角叉菜胶、黄原酸、葡聚糖、果胶、明胶、透明质酸、脱乙酰壳多糖,所述合成聚合物为聚丙烯酸酯、聚乙烯醇、聚甲基丙烯酸酯、聚乙烯吡咯烷酮、聚乙二醇丙烯酸酯/甲基丙烯酸酯(pega/pegma)、和聚苯乙烯、或这些聚合物的混合物。基于藻酸盐、角叉菜胶、明胶和聚丙烯酸酯的溶胀水凝胶特别适合作为造孔剂。聚合物造孔剂优选地由平均直径d50为1μm至100μm,优选地10μm至50μm,非常优选地10μm至30μm的球形水凝胶颗粒组成(使用根据申请日期有效的最新版本iso 13320-1的激光衍射方法测量)。
13.水凝胶颗粒的形状也可以是不规则的或圆柱形的以及纤维状的。在纤维状或圆柱形水凝胶颗粒的情况下,通过激光衍射测得的平均直径d50也为1μm至100μm,优选地5μm至50μm,其中颗粒可优选具有50比1至2比1,优选地20比1至5比1的长度与直径的纵横比。当然,水凝胶颗粒的不规则形状和其他几何形状也可以在本发明的范围内使用。
14.在涂料悬浮液中,由溶胀颗粒制成的聚合物造孔剂相对于涂料悬浮液的固体含量的重量比为1:40至1:0.7。在优选的实施方案中,这为1:20至1:2且非常特别优选地1:10至1:3。如果悬浮液中的水凝胶与固体的重量比小于0.025,则在层中产生的附加孔隙率太小而不具有积极效果。虽然高于1:0.7的比率的较大量水凝胶颗粒确实进一步增加孔隙率,然而,它们可最终导致催化剂基材的总体过低负载和涂层的过低耐粘附性和耐磨性。本领域技术人员将能够针对下面涂层问题找到正确值。
15.除了造孔剂之外,根据本发明的涂料悬浮液还具有至少一种无机涂层材料。这可以由本领域技术人员根据适用于本发明目的的材料来设计。通常,这些是由金属的氧化物、混合氧化物和/或沸石制成的材料,所述金属来自下列的组:铝、硅、钛、锆、铪、铈、镧、钇、钕、镨以及它们的混合物。材料特别优选包括铝、铈、锆或铈-锆的氧化物。这些可以以少量(1-10重量%)与来自钡、镧、钇、镨、钕的组的稳定剂一起提供。通常,这些是高表面积化合物(超过10m2/g至400m2/gbet表面积,根据申请日期的最新版本din 66132进行测量),其承受对应的高热负载。
16.刚刚提及的涂层材料通常具有在废气纯化方面的催化活性的金属。因此,涂层材料可另外含有催化活性金属和/或呈盐、氧化物的形式或呈金属形式的它们的混合物,所述催化活性金属来自下列的组:铁、铜、铂、钯、铑、钴、镍、钌、铱、金和银。
17.在本发明上下文中,特别优选的是铁或铜离子交换沸石,具体地cha、aei或eri类型的那些沸石。还优选的是基于铝、铈和锆的混合物或混合氧化物,其具有钯和/或铑。还可优选使用基于铝的催化活性涂层材料,其具有铂和/或钯。本领域技术人员也可在以下文献中找到合适的催化活性涂层:wo2011151711 a1。
18.根据本发明的涂料悬浮液的固体含量可由本领域技术人员来确定。无机涂层材料
(例如,氧化物、沸石、含有贵金属的氧化物等)也根据该涂料悬浮液以另外的固体添加剂(例如,储氧材料、混合氧化物、稳定剂等)的形式变化,并且相对于该悬浮液通常介于20重量%与55重量%之间,优选地25重量%-50重量%,并且非常优选地30重量%-45重量%。
19.待涂覆有根据本发明的涂料悬浮液的载体基材是流通式基材或壁流式过滤器基材。载体基材通常也称为催化剂基材、催化剂载体、蜂窝主体、基材或整料。流通式整料是现有技术中的常规催化剂基底,其可由金属(波纹载体,例如wo17153239a1、wo16057285a1、wo15121910a1以及其中引用的文献)或陶瓷材料组成。优选地使用耐火陶瓷,诸如堇青石、碳化硅或钛酸铝等。单位面积的通道数量是通过孔密度来表征的,孔密度的范围通常介于每平方英寸300至900个孔之间(cpsi)。陶瓷中通道壁的壁厚介于0.5mm至0.05mm之间。
20.现有技术中常用的所有陶瓷材料均可用作壁流式整料或壁流式过滤器。优选使用由堇青石、碳化硅或钛酸铝制成的多孔壁流式过滤器基底。这些壁流式过滤器基底具有流入通道和流出通道,其中流入通道的相应的下游端和流出通道的相应的上游端由气密“塞”交替地封闭。在这种情况下,迫使要净化的并流经过滤器基底的废气通过流入通道和流出通道之间的多孔壁,这会带来极佳的微粒过滤效果。微粒的过滤性能可借助于孔隙率、孔隙/半径分布和壁厚来设计。可以根据本发明的涂料悬浮液的形式将催化剂材料施加到入口通道和出口通道的多孔壁上。壁流式过滤器的孔隙率通常大于40%,通常为40%至75%,特别是45%至70%[根据提交日期的最新版本din 66133测量]。平均孔径(直径)为至少7μm,例如7μm至34μm,优选地大于10μm,具体地10μm至20μm或21μm至33μm[根据申请日期的最新版本din 66134进行测量]。
[0021]
在足够小粒径的水凝胶颗粒和涂料悬浮液的剩余固体组分的情况下(在平均孔径为大约15μm至20μm,通常《5μm的标准过滤器的情况下),被称为壁内涂层的物质(其中多孔涂层则在通道壁中的孔表面上形成)也可由根据本发明的涂料悬浮液来制备。这对于壁流式过滤器而言是特别要关注的,因为在这种情况下,通常存在尽可能高的量的位于壁中的催化活性材料。因此,可在不影响催化活性的情况下,另外积极地影响废气背压。
[0022]
还可使用根据本发明的悬浮液来涂覆流通式基材。通道壁上涂层的多孔结构增加了可触及的自由表面积,并且废气的湍流导致更好的交换,并且因此导致催化反应的改善。图2中示出了由水凝胶颗粒作为造孔剂制备的流通式基材的壁上涂层。
[0023]
除了在根据本发明的涂料悬浮液中使用的溶胀的造孔剂之外,相对于涂料悬浮液的量,另外的填料还可以1重量%至10重量%,优选地2重量%-8重量%,非常优选地4重量%-6重量%的量存在。例如,可使用另外的造孔剂,具体地被设计为纤维状的那些造孔剂。这种混合物可导致单独的纤维与涂料悬浮液的不同的溶胀造孔剂接触,并且因此在烧尽之后,在固体涂料悬浮液中由该溶胀的造孔剂产生的单独的孔通过通道彼此交联(图4)。因此,通过多孔涂层的气体通道可甚至进一步最小化,因为废气穿过其中的限定通道的可能性增加。此类造孔剂可由本领域技术人员随意地选择。它们通常具有50比1至2比1,优选地20比1至5比1的长度与宽度比。
[0024]
涂料悬浮液中的用于孔成形的水不溶性的溶胀造孔剂,例如水凝胶颗粒可仅由水和有机凝胶形成聚合物组成,或者它们还可含有另外的填料或被化学修饰。例如,溶胀的水凝胶颗粒可在该凝胶颗粒中另外含有纤维状填料或具有高表面积的填料,其保留在干燥并烧尽水凝胶颗粒之后形成的孔中,并且因此例如增加颗粒过滤效率。
[0025]
非常优选地,聚合物造孔剂可以例如呈水凝胶、催化活性金属或催化活性金属的前体的形式含有。例如,由水凝胶颗粒制得的造孔剂可同样含有例如不含贵金属的氧化物或含有贵金属的氧化物作为填料,如上文已经提及的,其在烧尽优选使用的水凝胶颗粒之后部分地填充所得的孔,并且改善催化活性,例如成品涂层的烟尘烧尽或氧化效应。溶胀颗粒,优选地水凝胶中填料的比例被选择成使得水凝胶分解后产生孔的松散、透气填充。具有对氧气、氮氧化物或有机化合物的储存功能的物质(诸如铈、锆或钡的氧化物或混合氧化物或离子交换沸石)也被设想为溶胀水凝胶颗粒中的填料。原则上,本文可使用本领域技术人员已知的用于废气纯化的所有活性物质。有利地,在优选使用的水凝胶分解之后,废气中的活性组分因此特别位于优选发生流动、物质转移或扩散的位置处。因此,它们与最大材料流密切接触。通常,相对于涂料悬浮液的量,这种另外的填料以1重量%至10重量%,优选地2重量%-8重量%,特别优选地4重量%-6重量%的量存在。
[0026]
图3概述了具有松散填充的孔的过滤器壁的壁上涂层。另选地,例如,还可通过随后在其制备之后使贵金属吸收到或吸收进溶胀的水不溶性水凝胶颗粒来实现造孔剂的化学改性(参见实施例1至3)(journal of molecular liquids,第276卷,2019年2月15日,第927-935页)。通过仅化学改性接近表面的区域,具有壳形构造的水凝胶颗粒也是可能的。例如,通过仅在颗粒的靠近表面的区域,简单地将水凝胶颗粒引入贵金属溶液中,可以吸收贵金属,所述贵金属保留在优选的水凝胶热分解之后所形成的孔壁上。非常优选地,水凝胶可在刚刚提及的范围内具有上述可能的催化活化涂层材料作为填料。
[0027]
优选地以被称为涂覆工艺的方式将涂料悬浮液施加到催化剂载体上。从这个意义上来讲,许多此类工艺在过去由机动车废气催化剂制造商公布(ep1064094b1、ep2521618b1、wo10015573a2、ep1136462b1、us6478874、us4609563、wo9947260a1、jp5378659b2、ep2415522a1、jp2014205108a2)。
[0028]
us6478874陈述了使用真空向上抽吸修补基面涂料悬浮液穿过基材整料的通道。us4609563描述了针对基材的催化涂覆使用计量加入系统的方法。该系统包括使用真空用精确控制的预定量的修补基面涂料悬浮液来涂覆陶瓷整体式基材的方法(下文中称为“计量加入”)。将整体式基材浸入定量确定量的修补基面涂料悬浮液中。然后通过真空将修补基面涂料悬浮液吸入基材整料中。然而,在这种情况下,很难以使得整体式基材中的通道的涂覆轮廓是均匀的方式涂覆整体式基材。
[0029]
相比之下,还提出了一种方法,通过该方法将特定量的修补基面涂料悬浮液(计量加入)施加到直立基材整料的顶侧,该量使得修补基面涂料悬浮液实际上完全保留在所提供的整料内(us6599570)。通过作用于整料的端部中的一个上的真空/压力装置,修补基面涂料悬浮液被完全吸入/压入整料中,而不会有过量的悬浮液在整料的下端逸出(wo9947260a1)。在该上下文中,还可参见科特拉公司(cataler company)的jp5378659b2、ep2415522a1和jp2014205108a2。
[0030]
非常特别优选地,用于使用根据本发明的悬浮液的催化剂基材是壁流式过滤器。所述壁流式过滤器具有30g/l至200g/l、优选地50g/l至160g/l、并且最特别优选地60g/l至145g/l的干涂料悬浮液载量。气体渗透率,并且因此催化剂层的孔隙率对于功能能力并且对于实现经涂覆的壁流式过滤器的尽可能低的废气背压而言是至关重要的。
[0031]
用根据本发明的涂料悬浮液涂覆催化剂载体后,将其干燥。该层可在室温下进行
干燥或在间歇式或连续式炉中在温度升高至80℃至180℃下进行干燥。在这种情况下,水首先从层中蒸发,并且还从水凝胶颗粒中蒸发至一定程度,然而,后者在很大程度上保持其尺寸。然后将催化剂载体加热至500℃至700℃的温度并煅烧,其中在涂层中含有的造孔剂的有机部分从水不溶性溶胀颗粒中烧尽。烧尽之后的孔径取决于水凝胶颗粒的起始直径,并且可通过选择水凝胶颗粒的合适粒度分布来设置。以这种方式涂覆壁流式过滤器使得其可确保足够高的气体渗透率,这防止了废气背压过度增加。这导致基材表面上的多孔催化活性层,其具有数量增加的孔,所述孔具有数量级为1μm至100μm、优选地10μm至50μm、非常特别优选地10μm-30μm的直径(通过层的多个切口(例如,10个)的sem或显微镜图像中孔径的光学长度分析并计算平均值来确定)。
[0032]
图5中的扫描电子显微照片(sem)中示出了多孔陶瓷基材上涂层的典型设计和结构。在此可以看到与在不具有造孔剂的情况下制备的层相比,与含有水不溶性溶胀颗粒作为造孔剂的悬浮液相比,根据本发明的涂层的孔隙率显著增加。在孔壁上具有涂层的过滤器的情况下,这导致允许废气以尽可能低的压力损失流动通过涂层的目的。这通过分解的水凝胶留下的腔更好地实现(图1)。
[0033]
在本发明的优选实施方案中,取决于起始材料,通过添加溶胀聚合物,孔隙率增加至少30%,更优选地40%,并且非常优选地50%(相对孔隙率增加)。在此,上限通过随着孔隙率增加,催化活性材料的量减少或层的粘附力可能受损的事实产生。取决于应用,通过使用水凝胶颗粒作为造孔剂产生的涂层的孔隙率应增加至介于5%和75%之间的值(绝对孔隙率)。施加的涂层的孔隙率可例如通过煅烧层的一个或多个横截面切口的sem图像的图像分析来确定(如上文已经示出的)。
[0034]
通过使用具有例如水凝胶颗粒作为造孔剂的根据本发明的涂料悬浮液,可在过滤器基材(壁流式)的通道壁上和/或中以及在流通式基材上制备具有良好气体渗透率的多孔涂层。具有此类涂层的过滤器具有比使用不具有造孔剂的常规涂料悬浮液所制备的过滤器更低的废气背压。图1示意性地示出了气体流动通过由层中的水凝胶颗粒分解产生的腔。
[0035]
本发明还涉及一种用于通过提供涂料悬浮液来制备载体基材上的多孔涂层的方法,所述涂料悬浮液具有至少一种无机涂层材料和至少一种聚合物有机造孔剂,其特征在于该聚合物造孔剂由水不溶性溶胀颗粒构成,所述水不溶性溶胀颗粒具有相对于水凝胶颗粒的40重量%至99.5重量%的水含量,用该涂料悬浮液涂覆载体基材,并且干燥并煅烧经涂覆的载体基材。涂料悬浮液的优选实施方案经必要修改也适用于本文提到的方法。
[0036]
相应制备的载体基材可成功地用于对来自汽车发动机的废气进行后处理。原则上,可原样使用适合本领域技术人员针对此目的的所有废气后处理。如所提及的,沸石尤其存在于twc(三元催化剂)、doc(柴油氧化催化剂)、pna(被动nox吸收剂)lnt(氮氧化物储存材料催化剂)中,并且具体地存在于scr催化转化器中。使用根据本发明的方法制备的催化剂适用于所有这些应用。这些催化转化器用于处理稀燃汽车发动机的废气的用途是优选的。
附图说明:
[0037]
图1:壁流式过滤器的根据本发明的涂层的示意图。
[0038]
图2:流通式基材的根据本发明的涂层的示意图。
[0039]
图3:壁流式过滤器的根据本发明的涂层的示意图,其中孔中具有填料。
[0040]
图4:壁流式过滤器的根据本发明的涂层的示意图,其中孔通过附加的造孔剂通道样连接。
[0041]
图5:具有(下部)和不具有(上部)造孔剂的涂层的孔隙率的比较结果。
[0042]
图6:藻酸盐水凝胶颗粒的光显微照片
[0043]
图7:藻酸盐水凝胶颗粒的粒径分布(d50:30μm;d90:53μm);根据iso 13320-1粒度分析-激光衍射方法,根据激光衍射方法测量
[0044]
附图的文字说明
[0045]
500废气
[0046]
570基材的孔壁
[0047]
580修补基面涂料
[0048]
590通道形连接孔
[0049]
600过滤器基材的孔壁
[0050]
610由分解的水凝胶制得的填料或富集功能性材料
实施例
[0051]
因此,含有水的溶胀聚合物造孔剂(水凝胶颗粒)不可商购获得,而是按照实施例中所述单独地制备,然后掺入涂料悬浮液中。
[0052]
a.藻酸盐水凝胶颗粒的制备
[0053]
基于藻酸盐的水凝胶颗粒的制备早已在文献中进行描述(参见,例如,wan-ping voo,european polymer journal 75(2016)343
–
353;aurelie schoubben,chemical engineering journal 160(2010)363
–
369)。从可用文献中,本领域技术人员可容易地识别最佳工艺参数以便制备粒径为5μm至100μm的水不溶性溶胀藻酸盐水凝胶颗粒。
[0054]
以举例的方式,在一个实验中,在搅拌下将2%藻酸钠溶液经由喷嘴喷入5%氯化钙溶液中。钙离子在冲击液体表面时导致藻酸盐液滴的自发胶凝。将所得藻酸钙小珠在溶液中搅拌另外两小时以完成溶胀过程,并且然后通过离心或过滤从溶液中分离。颗粒表现出主要为球形的形状,其中平均粒径d50为29μm(q3分布的中值,根据申请日期有效的最新版本iso 13320-1进行测量)并且水含量为95%。图6示出了藻酸盐水凝胶颗粒的光显微照片;图7示出了粒度分布。
[0055]
也可以使用其他水溶性钙盐代替氯化钙。根据本文所述的一般方法,还可制备具有形成水不溶性溶胀水凝胶颗粒的其他多价阳离子的由藻酸盐水凝胶颗粒制得的造孔剂。例如,藻酸盐水凝胶颗粒可通过沉淀以及钠与第二和第三主族(例如,锶、钡、铝等)的多价阳离子、过渡金属(镍、铜、铂、钯、铑等)的多价阳离子或稀土金属(诸如铈或镧)的阳离子进行交换来制备。以此方式,除了成孔功能之外,还可经由水凝胶颗粒将催化活性元素引入修补基面涂料层中,并且在水凝胶已经被烧尽之后保留在由其形成的孔中。
[0056]
b.交联的明胶水凝胶颗粒的制备
[0057]
将20g明胶(imagelgelita)悬浮在180g水中,并使其在室温下溶胀一小时。通过加热至40℃来制备澄清溶液。在第二容器中,通过将50g聚乙烯醇(例如,4-98,cas号9002-89-5,sigma-aldrich)溶解在450g水中,并在90℃下搅拌来制备澄清的
10%pva溶液。
[0058]
将175g水和175g明胶溶液(两者均加热至40℃)添加到350g pva溶液中并在40℃下搅拌,在40℃下搅拌15分钟,然后在搅拌下冷却至室温。
[0059]
为了交联明胶,将350μl 50%戊二醛水溶液(cas号:111-30-8,sigma-aldrich)添加到该溶液中并搅拌过夜。将由交联明胶制得的沉淀的水凝胶颗粒从剩余溶液中离心出来。水凝胶颗粒主要是平均粒径d50为9μm的球形并且水含量为91.3重量%。
[0060]
c.聚丙烯酸酯水凝胶颗粒的制备
[0061]
可商购获得的聚丙烯酸钠用于制备聚丙烯酸酯水凝胶颗粒(例如,sigma aldrich,cas号:9003-04-7)。这种物质在本领域中也称为超吸收剂,因为其能够在极性液体(例如水)中吸收其自身重量的多倍,并由此形成水凝胶。为了制备由聚丙烯酸酯制得的溶胀水凝胶颗粒,在搅拌下将5g聚丙烯酸钠添加到一升水中。在几分钟后结束的溶胀过程之后,将悬浮液用立式混合器预粉碎,然后在球磨机中用氧化铝球体(1mm)研磨至平均粒径d50为50μm。
[0062]
根据本发明的涂料悬浮液的制备
[0063]
为了展示出根据本发明的造孔剂的效果,将含有沸石并且具有scr官能团的修补基面涂料与基于藻酸盐和明胶的水凝胶颗粒(实验a和b)以表1中指示的比率混合。添加水凝胶颗粒之前的修补基面涂料悬浮液的固体含量为49.8重量%。最初将修补基面涂料装入搅拌容器中,并且在搅拌下添加对应量的溶胀水凝胶颗粒。随后将所得涂料悬浮液铺展到多孔陶瓷板上,干燥并在550℃下煅烧。煅烧层的层厚度介于80μm和150μm之间。为了确定孔隙率,将经涂覆的陶瓷板嵌入合成树脂中,并且在扫描电子显微镜中分析其区段。然后在图像分析程序(zeiss axio软件)中以电子方式检查sem图像。为此,将定义的rgb值分配给黑白色sem图像,并且对分析窗口中rgb值的面积比进行分析,以便计算确定孔隙率。
[0064]
表1涂料悬浮液的组成和表征
[0065][0066]
修补基面涂料(涂层材料)的固体含量
ꢀꢀꢀꢀꢀꢀꢀꢀꢀꢀꢀꢀ
49.8重量%
[0067]
藻酸盐水凝胶颗粒的水含量
ꢀꢀꢀꢀꢀꢀꢀꢀꢀꢀꢀꢀꢀꢀꢀꢀꢀꢀꢀꢀ
94.4重量%
[0068]
明胶水凝胶颗粒的水含量
ꢀꢀꢀꢀꢀꢀꢀꢀꢀꢀꢀꢀꢀꢀꢀꢀꢀꢀꢀꢀꢀꢀ
91.3重量%
[0069]
从表1可以看出,与不具有水凝胶颗粒的悬浮液相比,通过使用根据本发明的悬浮液,该层的孔隙率(经由如上所述的图像分析方法测定)是干燥层中平均值的双倍,根据本发明的悬浮液具有造孔剂,所述造孔剂由具有为5重量%的非常低的有机物比例的溶胀水
凝胶颗粒制成。
再多了解一些
本文用于企业家、创业者技术爱好者查询,结果仅供参考。