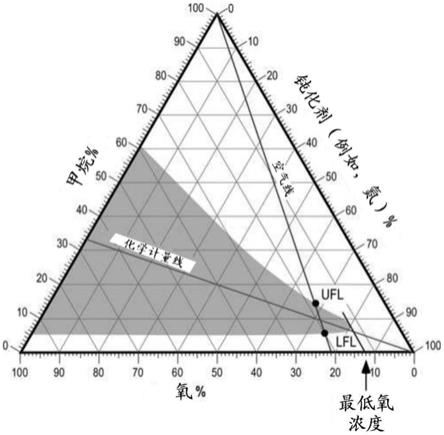
优化发酵过程的方法
1.本发明的技术领域
2.本发明涉及一种发酵反应器和发酵方法。具体而言,本发明涉及包含气体传感器的发酵反应器,和用于甲烷营养型微生物或甲基营养型微生物的优化发酵方法。
3.发明背景
4.在传统发酵能够代谢甲烷的微生物的过程中,添加甲烷气体和氧气对于促进微生物的生长是非常重要的。将气体注入发酵培养基并进行各种混合步骤,以便在发酵培养基中溶解尽可能多的气体,从而使其可用于待培养微生物的繁殖和生长。由于不可能溶解引入发酵罐的所有气体,以及由于液体和气体之间存在的相平衡,导致一定量的甲烷气体和氧气成为未溶解的气体,将从发酵反应器中排出。
5.未溶解的氧的存在可能导致若干缺点,因此需要非常严格地控制,且最好避免,在发酵过程中未溶解的氧的过程和水平。
6.包含氧气和甲烷的未溶解气体的一个挑战是在出口处或甚至在发酵反应器内部存在发生着火和爆炸的风险。
7.因此,在错误的情况下,氧气和甲烷气体的混合物会导致爆炸危险,如图1中灰色区域所示。
8.由于燃料、氧化剂和点火源的存在,会引发着火。空气中的氧通常用作氧化剂。因此,在存在一定浓度的燃料和氧化剂的情况下,会开始着火。图1是氧气和甲烷的可燃混合物的典型三角形图(爆炸三角),其中还包括氮气,但是氮气充当惰性气体(钝化剂)。这意味着,当氮浓度增加时,可燃性范围减小,观察到超过84%不发生点火(见图1)。氮气也可以被交换成二氧化碳(co2),当co2含量超过73%时,在这里没有观察到燃点。
9.爆炸上限(uel)和爆炸下限(lel)是可燃气体的最重要的性质。大多数可燃材料表现出可燃性区域(图1中的灰色阴影区域),即在其内的区域,混合物(图1中,甲烷和氧气的混合物)在所有浓度下都是可燃的。u形回路技术的当前操作方案包括用空气/氧气过量进料或吹扫以停留在“低于”爆炸下限的区域中。在目前的方法中,向废气中提供约2.5%甲烷的反应器中添加氧气,以确保不在可燃区/爆炸区。这种策略导致氧气的过高的消耗和损失,以及排放到大气中并损失的废气中的低浓度甲烷。
10.如下式(1)和(2)所示的标准化学计量法说明了为什么使用相对于甲烷浓度的高浓度的氧气。从标准化学计量的角度来看,为了提供所需的生物质产品,氧气的需求量高于甲烷的需求量,其中甲烷在氮源下与氧气发生反应。
11.所述标准化学计量学方程1以基于硝酸盐化学计量学为基础,在标准化学计量学方程2中,氨用作氮源。
12.所述化学计量比如下所示:
13.ch4 1.22 o2 0.104 nano
3-》0.52生物质 0.48 co2 1.532 h2o
ꢀꢀꢀ
(1)
14.和
15.ch4 1.45 o2 0.104 nh
3-》0.52生物质 0.48 co2 1.69 h2o
ꢀꢀꢀ
(2)
16.根据标准化学计量方程式1和2,在该方法中,使用1mol甲烷,使用更多mol氧气(当
硝酸盐作为氮源时使用1.22mol氧气,当氨作为氮源时使用1.45mol氧气)。
17.因此,基于该理论化学计量,当前描述的发酵方法使用比实际需要更多的氧气,并且这使得发酵方法由于可燃性问题成为更危险的方法,并且它还提供了一种不太环保且成本更高的方法。
18.因此,为了限制传统发酵反应器的着火和/或爆炸的风险,向发酵培养基中添加含量远高于甲烷气体的氧气,并且控制该过程,以避免废气中存在超过5%的未溶解的甲烷,从而降低着火和爆炸的风险。因此,发酵反应器中的氧气含量(溶解和未溶解的)显著高于甲烷含量(溶解和未溶解的)。
19.在发酵反应器中,氧气相对于甲烷含量(溶解和未溶解的)过剩的另一个缺点是它可能对发酵过程的稳定性和功能性方面造成挑战。如果没有正确处理该挑战,则发酵培养基发生亚硝酸盐中毒的风险显著增加,亚硝酸盐可能是氨(在标准化学计量方程式2所示的发酵过程中作为氮源而添加)在硝化过程中被氧化时形成的,这是硝化的限速步骤。在硝化过程中,微生物处于极端应激下,并且可能形成亚硝酸盐。由于亚硝酸盐不能完全转化为硝酸盐并且将停留在发酵罐中,因此发酵过程必须被终止,丢弃发酵培养基,并且必须开始新批次。这一过程被称为发酵的“死亡路径”,并且为所有单细胞蛋白质生产所担忧。
20.氨是最便宜的氮源之一,已经成为发酵过程中使用的标准或首选的氮源。然而,氨在任何应激条件下都会形成亚硝酸盐,细菌在一定的亚硝酸盐水平下无法生长。亚硝酸盐会形成抑制生长的细菌,这是一种无法挽救的状况,导致所谓的“死亡路径”。
21.因此,改进的发酵方法和改进的发酵反应器将是有利的,尤其是提供更安全、更环保、更经济高效、更简单、更有效、更可靠、降低失败风险、不向行业成本挑战妥协的发酵反应器和发酵工艺将是有利的。
22.发明概述
23.因此,本发明的目的涉及用于培养一种或多种甲烷营养型或一种或多种甲基营养型的微生物的改良的发酵反应器和改良的发酵方法。
24.具体而言,本发明的目的是提供发酵反应器和发酵工艺,该发酵反应器和发酵方法用来解决现有技术中存在的关于安全、成本、简易、危害环境、低效、不可靠、失败风险(例如由于“死亡路径”)的上述问题。
25.因此,本发明的一个方面涉及培养一种或多种能够代谢甲烷的微生物的方法,该方法包括以下步骤:
26.(i)向发酵反应器中添加发酵培养基;
27.(ii)将所述一种或多种微生物添加到发酵反应器中,提供接种的发酵培养基,其中所述一种或多种微生物不包括重组微生物;
28.(iii)在所述一种或多种微生物发酵期间,向发酵反应器和/或接种的发酵培养基中添加c1-c5碳源,例如甲烷;和
29.(iv)任选地,在所述一种或多种微生物发酵期间向发酵反应器和/或接种的发酵培养基添加氧气,
30.其中,将氧气添加到发酵反应器和/或接种的发酵培养基中,以提供发酵反应器中最多为10%(vol/vol)的未溶解的氧气含量和/或废气中气态氧的含量。
31.本发明的另一方面涉及培养一种或多种能够代谢甲烷的微生物的方法,该方法包
括以下步骤:
32.(i)向发酵反应器中添加发酵培养基;
33.(ii)将所述一种或多种微生物添加到发酵反应器中,提供接种的发酵培养基,其中所述一种或多种微生物不包括重组微生物;
34.(iii)在所述一种或多种微生物发酵期间,向发酵反应器和/或接种的发酵培养基中添加c1-c5碳源,例如甲烷;和
35.(iv)任选地,在所述一种或多种微生物发酵期间向发酵反应器和/或接种的发酵培养基添加氧气,
36.其中,所述方法为半需氧发酵方法或厌氧发酵方法,其中发酵反应器中未溶解的氧含量或废气中气态氧的含量最多可为5%(vol/vol)。
37.本发明的另一个方面涉及用于发酵一种或多种微生物的发酵反应器,所述发酵反应器包括至少一个入口,用于将c1-c5碳源,例如甲烷,引入发酵反应器,以及一个或多个传感器,所述一个或多个传感器是用于确定发酵反应器中未溶解和/或释放的气体的浓度的一个或多个传感器,其中所述未溶解和/或释放的气体为氧气。
38.本发明的又一方面涉及用于发酵一种或多种微生物的发酵反应器,所述发酵反应器包括用于将c1-c5碳源引入所述发酵反应器的至少一个入口和一个或多个传感器,其中所述一个或多个传感器是用于确定所述发酵反应器中未溶解和/或释放的气体的浓度的一个或多个传感器。
39.本发明的另一方面涉及用于发酵一种或多种微生物的发酵反应器,该发酵反应器包括用于将甲烷气体引入发酵反应器的至少一个进气口;以及用于从发酵反应器排放未溶解和/或释放的气体的排气口,以及一个或多个传感器,其中所述一个或多个传感器是用于确定发酵反应器中未溶解和/或释放的气体浓度的一个或多个传感器。
40.本发明的又一个方面涉及通过根据本发明的方法获得的生物质材料,优选地,所述生物质材料包含具有降低至少25%(w/w)转录水平的至少25个基因。
41.本发明的另一方面涉及包含根据本发明所述生物质材料的动物饲料产品、或鱼饲料产品、或人类食品。
42.本发明的又一方面涉及用于在培养一种或多种能够代谢甲烷的微生物时减少发酵过程的环境影响和/或能量消耗的系统,该系统包括根据本发明的发酵反应器,和与用于从发酵反应器排出未溶解和/或释放的气体的排气管连接的废气管,所述发酵反应器具有发电机,用于产生电力;加热装置,用于产生热量;和/或用于将甲烷再循环到发酵反应器的清洁单元。
附图说明
43.图1显示了爆炸三角。爆炸三角的边表示每种物质占总气体组合物的百分比。灰色区域是其中气体组合物变得可燃且爆炸风险高的比率,
44.图2显示了在厌氧条件下连续发酵92小时的甲烷营养菌(荚膜甲基球菌(m.capsulatus))的生长情况。发酵68小时后,停止氧气供应,生物质的连续生长伴随着酸水平(用三角形表示)的降低;no
2-水平(用正方形表示)和no
3-水平(用圆圈表示),在24小时内(从连续发酵开始的68小时到92小时)均显著下降。因此,甲烷营养菌的厌氧发酵,例如荚
膜甲基球菌(m.capsulatus),可在不提供气态氧的情况下进行。
45.下面将更详细地描述本发明。
46.发明详述
47.因此,本发明涉及用于培养能够代谢如甲烷的c1-c5化合物的微生物的发酵反应器和发酵方法,例如甲烷营养菌或甲基营养菌,例如选自甲基球菌科(methylococcaceae)或甲基包囊菌科(methylocystaceae)的微生物,其可以在降低的氧气水平下;降低的氧气/甲烷比率,或优选在厌氧条件下发酵,与发酵能够代谢如甲烷的c1-c5化合物的微生物的传统方法相比,该方法表现得更可靠,具有更低的失败风险,更有效,对环境更少的危害,同时更具经济效益。
48.因此,本发明的一个优选实施方案涉及培养一种或多种能够代谢甲烷的微生物的方法,所述方法包括以下步骤:
49.(i)向发酵反应器中添加发酵培养基;
50.(ii)将所述一种或多种微生物添加到发酵反应器中,提供接种的发酵培养基;
51.(iii)在所述一种或多种微生物发酵期间,向发酵反应器和/或接种的发酵培养基中添加c1-c5碳源,例如甲烷;和
52.(iv)任选地,在所述一种或多种微生物发酵期间向发酵反应器和/或接种的发酵培养基添加氧气,
53.其中,所述方法为半需氧发酵方法或厌氧发酵方法。
54.优选地,所述一种或多种微生物可以是一种或多种需氧微生物。
55.所述一种或多种需氧微生物可以优选地选自一种或多种甲烷营养型需氧微生物和/或一种或多种甲基营养型需氧微生物。
56.所述一种或多种甲烷营养型需氧微生物或一种或多种甲基营养型需氧微生物可以是一种或多种甲烷营养型需氧细菌和/或一种或多种甲基营养型需氧细菌。
57.在本发明的一个实施例中,所述一个或多个甲烷营养型需氧细菌可选自甲基球菌属(methylococcus),优选是荚膜甲基球菌(m.capsulatus)。
58.在本发明的另一个实施例中,所述一个或多个甲烷营养型需氧细菌可包括荚膜甲基球菌(优选是ncimb 11132);a.acidovorans(优选是ncimb 13287);b.firmus(优选是ncimb 13289);和a.danicus(优选是ncimb 13288)的组合。
59.在本发明的一个优选实施方案中,所述一种或多种微生物不包括重组微生物。
60.在本发明的上下文中,术语“重组微生物”涉及使用质粒,现有基因的删除;或其他基因工程技术改变其遗传物质的转基因生物体(gmo)。重组微生物可被视为与在微生物中自然发生的基因改变相反,例如通过交配和/或自然突变。
61.优选地,所述一种或多种微生物可以是一种或多种天然微生物。
62.在本发明的上下文中,术语“天然微生物”涉及尚未使用基因工程技术改变其遗传物质的微生物。微生物遗传物质的自然修饰或改变可视为被术语“天然微生物”所涵盖。
63.在本发明的一个实施例中,半需氧发酵方法可以是这样的发酵方法,其中发酵反应器中未溶解的氧的含量或废气中气态氧的含量最多可为10%(vol/vol),诸如最多8%(vol/vol),例如最多6%(vol/vol),诸如最多4%(vol/vol),例如最多2%(vol/vol),诸如最多1%(vol/vol),例如最多0.5%(vol/vol),诸如0%(vol/vol)。
64.在本发明的上下文中,术语“半需氧发酵”涉及的发酵方法,其中氧气被添加到发酵过程和/或发酵反应器中,然而,添加到发酵过程和/或发酵反应器中的氧气的含量小于所添加的c1-c5碳源例如甲烷的含量。
65.本发明的另一个优选实施方案涉及培养一种或多种能够代谢甲烷的微生物的方法,所述方法包括以下步骤:
66.(i)向发酵反应器中添加发酵培养基;
67.(ii)将所述一种或多种微生物添加到发酵反应器中,提供接种的发酵培养基;
68.(iii)在所述一种或多种微生物发酵期间,向发酵反应器和/或接种的发酵培养基中添加c1-c5碳源,例如甲烷;和
69.(iv)任选地,在所述一种或多种微生物发酵期间向发酵反应器和/或接种的发酵培养基添加氧气,
70.其中,将氧气添加到发酵反应器和/或接种的发酵培养基中,以提供发酵反应器中最多为10%(vol/vol)的未溶解的氧气的含量和/或废气中气态氧的含量。
71.在本上下文中,所述c1-c5碳源可被添加到发酵反应器中。所述c1-c5碳源可以是c1-c3碳源。优选地,c1-c5碳源可包含烷烃或醛。烷烃可优选为c1化合物和/或c1烷烃和/或c1醛或其衍生物。
72.优选地,所述c1化合物和/或所述c1烷烃可以是甲烷、甲醇、天然气、沼气、合成气或其任何组合。优选地,所述c1醛可以是甲醛或其衍生物。更优选地,所述c1化合物和/或c1烷烃可以是甲烷。
73.在步骤(iii)中添加的所述c1-c5碳源可以是液体形式或气体形式。在本发明的实施例中,所述c1-c5碳源,例如被添加到根据本发明的方法的步骤(iii)的甲烷可优选为气态甲烷。
74.在本发明的另一个实施方案中,被添加到根据本发明的方法的步骤(iv)中的氧可以是气态氧或液态氧。优选地,所述氧可以大气气体、纯氧或富氧空气的形式来提供。
75.在半需氧发酵过程中,未溶解的气体(和废气)可以包括除甲烷气体和氧气之外的气体。即使可能存在其他气体,c1-c5碳源,例如甲烷,与氧气之间的比率也可能很重要。
76.因此,在本发明的一个实施例中,c1-c5碳源,例如甲烷,与未溶解和/或在废气中的氧之间的比率,可以至少为5:1(vol c1-c5碳源/vol氧),诸如至少6:1(vol c1-c5碳源/vol氧),例如至少7:1(vol c1-c5碳源/vol氧),诸如至少8:1(vol c1-c5碳源/vol氧),例如至少9:1(vol c1-c5碳源/vol氧),诸如至少10:1(vol c1-c5碳源/vol氧),例如至少15:1(vol c1-c5碳源/vol氧),诸如至少20:1(vol c1-c5碳源/vol氧),例如至少25:1(vol c1-c5碳源/vol氧),诸如至少30:1(vol c1-c5碳源/vol氧气),例如至少35:1(vol c1-c5碳源/vol氧气)。
77.在发酵期间,区分溶解的气体和未溶解的气体可能是重要的,因为只有溶解的气体可被微生物消耗。未溶解的气体,如未溶解的c1-c5碳源,如甲烷,和/或未溶解的氧气,将在废气中分离,可能被浪费,并可能增加如前所述的爆炸风险。
78.在本发明的上下文中,术语“溶解的”涉及被发酵培养基吸收的气体,在本发明的上下文中,是指已经被发酵培养基吸收并可供待培养的微生物消耗的气体。与溶解气体相比,存在未溶解气体。在上下文中,术语“未溶解的”涉及未被发酵培养基吸收并且不会被待
培养的微生物消耗的气体。
79.在本发明的另一个实施例中,发酵过程可以是半需氧发酵过程,其含有相对于发酵培养基0%(vol/vol)的未溶解的氧和超过1%(vol/vol)的溶解的氧,诸如超过3%(vol/vol)的溶解的氧,例如超过5%(vol/vol)的溶解的氧;诸如超过3%(vol/vol)的溶解的氧;例如超过10%(体积/体积)的溶解的氧;诸如超过15%(vol/vol)的溶解的氧;例如超过20%(vol/vol)的溶解的氧;诸如超过25%(vol/vol)的溶解的氧,例如在1-50%(vol/vol)范围内的溶解的氧;诸如在5-25%(vol/vol)范围内的溶解的氧。
80.发酵反应器可以包括一个用于将co2引入发酵培养基的入口。在本发明的一个实施例中,可将co2添加到发酵反应器和/或发酵培养基中。co2可被连续注入发酵培养基中。优选地,注入发酵培养基的co2量至少为0.001l/min/l的发酵培养基,诸如至少为0.005l/min/l的发酵培养基,例如至少为0.01l/min/l的发酵培养基,诸如至少为0.05l/min/l的发酵培养基,例如至少为0.1l/min/l的发酵培养基,诸如至少为0.13l/min/l的发酵培养基,例如至少为0.15l/min/l的发酵培养基,诸如至少为0.2l/min/l的发酵培养基,例如至少为0.25l/min/l的发酵培养基,诸如至少为0.3l/min/l的发酵培养基,例如至少为0.4l/min/l的发酵培养基,诸如至少为0.5l/min/l的发酵培养基,例如至少为0.60l/min/l的发酵培养基,诸如至少为0.7l/min/l的发酵培养基,例如至少为0.75l/min/l的发酵培养基。
81.在本发明的一个实施例中,发酵反应器中未溶解的co2的含量或废气中存在的气态co2的含量为高于2.5%(vol/vol),诸如至少4%(vol/vol),例如至少5%(vol/vol),诸如至少7.5%(vol/vol),例如至少10%(vol/vol),诸如至少12.5%(vol/vol),例如至少15%(vol/vol),诸如至少20%(vol/vol),例如至少30%(vol/vol),诸如至少40%(vol/vol),和/或未溶解的co2的含量小于75%(vol/vol),诸如小于70%(vol/vol),例如小于60%(vol/vol),诸如小于50%(vol/vol),例如小于40%(vol/vol),诸如小于30%(vol/vol),例如小于20%(体积/体积),诸如小于10%(体积/体积),例如小于5%(体积/体积)。
82.在本发明的又一实施例中,c1-c5碳源,例如甲烷,与溶解在发酵培养基中的co2之间的摩尔比约为1:1摩尔比,诸如约为0.525:0.475摩尔比。
83.在本发明的另一个实施例中,未溶解的气体可以为气相。
84.当未溶解的气体包括甲烷或甲烷和氧气时,在某一点上存在非最佳发酵条件,例如,发酵培养基中溶解的气体的量不足,可能会影响微生物的生长,微生物可能生长缓慢或停止生长;或者,发酵反应器中可能添加过多的气体,可能会影响发酵过程的成本和生产率,并且根据爆炸三角可能会产生安全风险,其中某些浓度的甲烷和氧气是高度易燃的,并因此构成爆炸风险。
85.因此,可能需要持续调整工艺,以优化发酵条件,同时降低可燃性/爆炸风险。
86.未溶解相和溶解相的气体之间存在平衡。可以通过增加发酵培养基中溶解的气体的量的方式来操控该平衡,也可以通过另一种方式来操控该平衡,即增加未溶解的气体从而允许未消耗的甲烷和/或未消耗的氧气,和/或微生物生长产生的co2,和/或添加的co2,从发酵反应器中释放。因此,也许不可能仅添加刚好足够的甲烷和/或氧气以获得最优的发酵条件,并避免在未溶解相中存在甲烷和/或氧气。
87.甲烷和/或氧气显示出有利于未溶解相的趋势,并且,为了提高在接种的发酵培养基中的溶解的氧气和甲烷的含量,在发酵反应器中可以提供持续混合。
88.为了避免具有包含可燃量(比例)的甲烷和氧气的未溶解气相,并因此具有爆炸风险,传统地是向发酵反应器和/或发酵培养基中添加过量的氧气,以确保气体不处于可燃量(比率)。因此,传统的培养能够代谢甲烷的微生物的发酵方法是通过调节未溶解氧的量/浓度来控制的。
89.本发明的发明人惊奇地发现,代替基于废气中过量的氧含量来控制和调节发酵过程,该方法可以优选地通过在废气中提供过量的甲烷来控制,其中甲烷可以任选的被回收或在例如下游工艺中用作能源,并且与发酵能够代谢甲烷的微生物的传统方法相比,这种方式提供更可靠、失败风险更低、更有效、对环境危害更小、同时更有经济效益的方法。在将甲烷再循环到反应器之前或在将其用作能源之前,可以通过例如从废气中剥离co2和/或o2(如果存在)来清洁废气,以提供纯净或基本纯净的甲烷气体。
90.在本发明的一个实施例中,废气中存在的甲烷和/或废气中存在的氧气可再循环至发酵罐。优选地,废气中存在的co2和/或硫化物可在重新注入或再循环至发酵罐之前部分或完全的从甲烷和/或氧气中去除。
91.基于过量的c1-c5碳源,例如甲烷,来控制和调节发酵过程的其他优点是通过使用较高含量的c1-c5碳源,例如甲烷,达到较低的氧气爆炸(lel)水平,从而减少工艺的可燃性和爆炸性问题。此外,根据本发明,通过添加更多的c1-c5碳源,例如甲烷,还降低了亚硝酸盐形成的可能性,这是存在过量氧的情况下的问题,并且这可能导致由于培养的死亡路径而造成发酵过程的失败。
92.因此,在本发明的一个实施例中,在步骤(iii)和/或步骤(iv)中添加的c1-c5碳源,例如甲烷,和/或氧的量可由废气中未溶解的和/或释放的c1-c5碳源,例如甲烷,和/或氧的含量来控制。
93.从废气中获得的甲烷可再循环至发酵反应器,或用于能源消耗,例如为一个或多个下游工艺发电和/或加热,诸如干燥器,例如闪蒸干燥器;分离器,例如离心机;和/或收获产品的其他下游工艺的装置。
94.在本发明的一个实施例中,添加c1-c5碳源,例如甲烷,(步骤iii)包括向发酵反应器和/或接种的发酵培养基中连续添加c1-c5碳源,例如甲烷。
95.在本发明的另一个实施例中,添加氧气(步骤iv)包括向发酵反应器和/或接种的发酵培养基连续添加氧气。
96.连续添加的氧和/或c1-c5碳源,例如甲烷,可通过未溶解和/或释放的c1-c5碳源,例如甲烷,和/或在废气中的氧气的含量来控制,或者通过未溶解和/或释放的c1-c5碳源,例如甲烷,和/或在接种的发酵培养基中氧气的含量进行控制。
97.在本发明的优选实施例中,发酵方法可以是半需氧发酵方法或半厌氧发酵方法。
98.优选地,“半需氧发酵方法”或“半厌氧发酵方法”可以互换使用,并且可以涉及如下发酵方法,其中在发酵反应器中未溶解的氧的含量和/或存在于废气中未溶解的(气态)氧的含量与c1-c5碳源例如甲烷的含量相比,是相等的或者更低的,或者降低到相等或者更低。
99.在本发明的另一个实施例中,“半需氧发酵方法”或“半厌氧发酵方法”可以互换使用,并且可以涉及如下发酵过程,其中溶解在发酵反应器中的发酵培养基中的氧的含量,等于或小于c1-c5碳源例如甲烷的含量。
100.在本发明的一个实施例中,“半需氧发酵方法”或“半厌氧发酵方法”可以互换使用,并且可以涉及如下发酵过程,其中添加到发酵反应器中的氧的含量等于或小于添加到发酵反应器中的c1-c5碳源例如甲烷的含量。
101.在本发明的另一个实施例中,“半需氧发酵方法”或“半厌氧发酵方法”可以互换使用,并且可以涉及:
[0102]-发酵方法,其中,在发酵反应器中未溶解的氧的含量和/或存在于废气中未溶解的(气态)氧的含量与c1-c5碳源例如甲烷的含量相比,是相等的或者更低的,或者降低到相等或者更低的;和/或
[0103]-发酵过程,其中溶解在发酵反应器中的发酵培养基中的氧的含量,等于或小于c1-c5碳源例如甲烷的含量;和/或
[0104]-发酵过程,其中添加到发酵反应器中的氧的含量等于或小于添加到发酵反应器中的c1-c5碳源例如甲烷的含量。
[0105]
在本发明的一个实施例中,半需氧发酵方法可以是发酵过程,其中发酵反应器中未溶解的氧的含量或废气中存在的气态氧的含量最多可为10%(vol/vol),诸如最多8%(vol/vol),例如最多6%(vol/vol),诸如最多4%(vol/vol),例如最多2%(vol/vol),诸如最多1%(vol/vol),例如最多0.5%(vol/vol),诸如0%(vol/vol)。
[0106]
优选地,发酵反应器中未溶解的氧的含量或废气中存在的气态氧的含量最多可为10%(vol/vol),诸如最多8%(vol/vol),例如最多6%(vol/vol),诸如最多4%(vol/vol),例如最多2%(vol/vol),诸如最多1%(vol/vol),例如最多0.5%(vol/vol),诸如0%(vol/vol)。
[0107]
在本发明的另一个实施方案中,发酵过程可以是厌氧发酵过程。
[0108]
在本发明的上下文中,术语“厌氧发酵方法”涉及如下发酵方法,其中氧气,优选气态氧或液态氧,未被添加到发酵反应器中。
[0109]
根据本发明的发酵方法可以始于厌氧发酵方法;或始于需氧或半需氧的发酵方法,随后是厌氧发酵方法,其中停止氧、气态氧或液态氧的供应。
[0110]
在本发明的一个实施例中,发酵方法最初可以是半需氧发酵方法,随后是厌氧发酵方法。
[0111]
根据本发明的发酵过程可以是需氧或半需氧的发酵方法,随后是厌氧发酵方法,其中可以停止氧优选气态氧的供应。优选地,为了厌氧发酵方法,氧优选气态氧的供应,可停止至少2小时的时间,诸如至少5小时,例如至少10小时,诸如至少20小时,例如至少24小时,诸如至少30小时,例如至少35小时,诸如至少40小时,例如至少50小时,诸如至少60小时,例如至少70小时。
[0112]
在本发明的又一个实施方案中,本发明的方法不涉及向发酵培养基中添加气态氧。
[0113]
在本发明的又一个实施方案中,本发明的方法不涉及向发酵培养基中添加液态氧。
[0114]
在本发明的又一个实施方案中,本发明的方法不涉及向发酵培养基中添加气态氧和液态氧。
[0115]
在本发明的一个实施例中,在半需氧发酵方法或厌氧发酵方法中,存在于发酵培
养基中的氧可以选自结合氧,诸如甲醇;甲酸;甲醛或其衍生物。
[0116]
在半需氧发酵方法或厌氧发酵方法中,存在于发酵培养基中的结合氧可以是,诸如甲醇;甲酸;甲醛或其衍生物,其可通过添加到发酵反应器中的组分而形成,或者结合氧,诸如甲醇;甲酸;甲醛或其衍生物,可被添加到发酵反应器中。
[0117]
对于甲烷,实验性获得生物质x(分子式ch
1.8o0.5n0,2
和分子量24.6g每c原子)的碳产率y
ch4,x
是0.52/1=0.52mol碳每mol来自甲烷的碳或0.8kg生物质/kg甲烷=1.75m3甲烷(1atm,0℃)每kg生产的生物质。
[0118]
使用在需氧条件下能够代谢甲烷的微生物的传统生物质生产可以按以下净化学计量比进行收集:
[0119]
ch4 1.45 o2 0.104 nh3→
0.52 ch
1.8o0.5n0.2
0.48 co2 1.69 h2o
[0120]
氧气需求量是1.75
·
1.45=2.54m
3 o2(1atm,0℃)每kg生物质。
[0121]
对于ch4上的o2,大的产率系数y
ch4
,o2=1.45可能是通过需氧方法的生物质生产的经济负担。人们更愿意使用大气空气(21%o2),但现今o2向液相(发酵培养基)的传质容易受到限制,资本成本急剧增加。折衷方案是在进料气中使用技术上纯的o2(》90%)。现在基本上可以避免传质阻力,但o2可以变为经济上占主导地位的底物。
[0122]
因此,本发明提供了显著的优点,因为在提供生物质例如单细胞蛋白(scp)的发酵方法中,减少或甚至避免了氧气的添加,从而相对于传统方法实现了显著的成本节约。
[0123]
此外,反应热也成为技术以及经济问题。作为经验规则,任何需氧化学计量中的反应热等于460
×ycxx,o2 kj,其中cxx是每c-mol碳的碳源公式。在上述净化学计量比中,y
cxx,o2
=y
ch4,o2
=1.45,并且热量释放是460
×
1.45
×
(1000/(24.6
×
0.52))=52159kj每1kg生产的生物质。如此多的热量无法通过在釜内冷却的方法从即使一个小的50至100m3的搅拌釜式反应器中去除。要么必须安装大型外部制冷设备,要么生物反应器必须长且纤细,这种设计使得环流反应器几乎成为唯一的合理选择。
[0124]
对于生物质诸如单细胞蛋白(scp)的生产者而言,在使用荚膜甲基球菌的生物质发酵中,y
cxx,o2
的高值是令人不快的意外。
[0125]
因此,本发明的发明人建议减少在发酵方法中的氧,甚至减少氧直至提供半需氧发酵方法或甚至厌氧发酵方法,以允许用甲烷为底物的scp生产,其化学计量比远好于上述净化学计量比:
[0126]
0.525 ch4 0.475 co2 0.2 nh3→
ch
1.8o0.5n0.2
0.45h2o
[0127]
本发明的发明人从该反应中,发现ch4可与co2反应,以形成甲醛及其衍生物,其适用于在半需氧发酵和厌氧发酵方法中生产scp。
[0128]
在本发明的一个实施例中,发酵反应器中未溶解的c1-c5碳源的含量,例如甲烷,或废气中存在的气态c1-c5碳源的含量,例如甲烷,可高于5%(vol/vol),诸如至少7.5%(vol/vol),例如至少10%(vol/vol),诸如至少15%(vol/vol),例如至少20%(vol/vol),诸如至少25%(vol/vol),例如至少40%(vol/vol),诸如至少60%(vol/vol),例如至少75%(vol/vol),诸如至少85%(vol/vol),例如至少90%(vol/vol),诸如至少95%(vol/vol),例如至少98%(vol/vol)。
[0129]
发酵方法可进一步包括向发酵反应器和/或接种的发酵培养基添加氮源的步骤。氮源的添加可以是发酵源的连续添加。
[0130]
在本文的上下文中,术语“连续添加”涉及根据需要和/或基于从发酵反应器的一个或多个传感器接收到的信息,在整个发酵过程中,不间断地添加例如c1-c5碳源,例如甲烷、氧、co2和/或氮。
[0131]
在本发明的一个实施例中,氮源可选自氨、硝酸盐、分子氮及其组合。优选地,氮源包含氨。
[0132]
优选地,发酵培养基中c1-c5碳源,例如甲烷,与氨之间的比率可以至少为2:1(vol/vol),诸如至少为3:1(vol/vol),例如至少为5:1(vol/vol),诸如至少为10:1(vol/vol),例如至少为12:1(vol/vol),诸如至少为14:1(vol/vol),例如至少为16:1(vol/vol),诸如至少为18:1(vol/vol),例如至少20:1(vol/vol),诸如至少25:1(vol/vol),例如至少30:1(vol/vol)。
[0133]
在本发明的一个实施例中,c1-c5碳源,例如甲烷,与溶解在发酵培养基中的氨之间的摩尔比约为100:1,例如约为50:1;诸如10:1,例如约3:1,诸如约2:1,例如约1:1。
[0134]
在根据本发明的培养方法的进一步的步骤中,可收获生物质。
[0135]
因此,根据本发明的培养方法可以继续进行,直到达到至少1.0g/l的生物质浓度,诸如至少1.25g/l的生物质浓度,例如至少1.5g/l的生物质浓度,诸如至少1.75g/l的生物质浓度,例如至少2.0g/l的生物质浓度,诸如至少2.25g/l的生物质浓度,例如至少2.5g/l的生物质浓度,诸如至少2.75g/l的生物质浓度,例如至少3.0g/l的生物质浓度,诸如至少3.25g/l的生物质浓度,例如,至少3.5g/l的生物质浓度,诸如至少3.75g/l的生物质浓度,例如至少4.0g/l的生物质浓度。
[0136]
本发明的发明人发现,根据在半需氧发酵条件或厌氧发酵条件下生产的生物质在一些基因的转录水平上,与在有氧发酵条件下生产的生物质的转录水平相比,显示出显著差异,
[0137]
在本发明的一个实施例中,生物质材料包含至少25个基因,诸如至少50个基因,例如至少75个基因,诸如至少100个基因,例如至少125个基因,诸如至少150个基因,例如至少175个基因,诸如至少200个基因,例如至少210个基因,诸如至少219个基因,具有降低至少25%(w/w)的转录水平,诸如至少50%(w/w),例如至少60%(w/w)。
[0138]
根据本发明的生物质材料可以以液体或固体的形式提供,例如以粉末、糊剂、浆液、胶囊或小袋的形式提供。
[0139]
在本发明的一个实施例中,发酵方法可以是分批发酵、分批补料或连续发酵方法。优选地,发酵过程可以是连续发酵过程。
[0140]
在本发明的另一实施例中,连续发酵过程可作为恒化器、恒ph器、恒产品器或其它连续发酵过程模式来进行。
[0141]
在本发明的一个实施方案中,未溶解的气体(诸如氧气和/或c1-c5碳源,例如为甲烷和/或co2)包括在发酵培养基中、顶部罐中和发酵反应器中的气袋中的未溶解的氧气和/或未溶解的c1-c5碳源,例如甲烷和/或未溶解的co2。
[0142]
根据本发明的发酵方法可以导致改进的所述生物质的生产和/或所述微生物的增加的生长速率。
[0143]
在本发明的实施例中,本发明的方法提供在发酵过程中微生物的生长速率至少为0.04h-1
,例如至少为0.05h-1
,诸如至少为0.06h-1
,例如至少为0.08h-1
,诸如至少为0.10h-1
,
例如至少为0.12h-1
,诸如至少为0.14h-1
,例如至少为0.15h-1
,诸如至少为0.16h-1
,例如至少为0.17h-1
,诸如至少为0.18h-1
,例如至少0.19h-1
,诸如至少0.20h-1
1,例如至少0.22h-1
,诸如至少0.25h-1
,例如至少0.27h-1
,诸如至少0.30h-1
,例如至少0.32h-1
,诸如至少0.35h-1
,例如至少0.37h-1
。
[0144]
在本发明的另一个实施例中,可提供干物质基础上至少2.5g/l的生物质产量,诸如可提供干物质基础上至少3.0g/l的生物质产量,例如可提供干物质基础上至少3.5g/l的生物质产量,诸如可提供干物质基础上至少4.0g/l的生物质产量,例如可提供干物质基础上至少7.5g/l的生物质产量,诸如可提供干物质基础上至少10.0g/l的生物质产量,例如可提供干物质基础上至少20.0g/l的生物质产量,诸如可提供干物质基础上至少30.0g/l的生物质产量。
[0145]
所述微生物可以选自下组:细菌、真菌、藻类和动物。优选地,微生物可以是细菌。
[0146]
优选地,所述一种或多种微生物可以是一种或多种需氧微生物。
[0147]
在本发明的一个实施方案中,所述一种或多种微生物可以是甲烷营养型微生物或甲基营养型微生物。
[0148]
在本发明的又一实施例中,甲烷营养型微生物可以是甲烷营养型细菌,优选地选自甲基球菌属菌株。
[0149]
在本发明的进一步实施例中,所述甲基球菌属菌株可以是荚膜甲基球菌。
[0150]
在本发明的另一个实施例中,所述一种或多种微生物可包括荚膜甲基球菌与一种或多种的a.acidovorans(优选是ncimb 13287);b.firmus(优选是ncimb 13289);和/或a.danicus(优选是ncimb 13288)的组合。
[0151]
在本发明的另一个实施例中,所述发酵方法仅包括能够代谢甲烷的细菌细胞,特别是仅包括能够代谢甲烷的微生物。
[0152]
在本发明的一个实施例中,所述发酵方法仅包括能够在半需氧条件或厌氧条件下代谢甲烷的微生物。
[0153]
在本发明的另一个实施例中,所述发酵方法不包括含有不能代谢甲烷的生物体的共培养物,例如蓝藻。具体而言,半需氧条件或厌氧发酵过程可以不包括含有不能代谢甲烷的生物体的共培养物,例如蓝藻。
[0154]
所述发酵过程,尤其是厌氧发酵过程,可包括能够代谢甲烷的单一菌株。
[0155]
当向发酵培养基中添加气体时,例如甲烷、co2和/或氧气,气体将不溶解。未溶解气体将自然传质至发酵培养基,并成为溶解气体。溶解的气体能够在发酵期间支持微生物的生长。
[0156]
根据本发明的方法可优选地在如本文所述的发酵反应器中进行。
[0157]
本发明的一个优选的实施例涉及用于发酵一种或多种微生物的发酵反应器,该发酵反应器包括用于将c1-c5碳源引入发酵反应器的至少一个入口和一个或多个传感器,其中,所述一个或多个传感器是用于确定发酵反应器中未溶解和/或释放的气体的浓度的一个或多个传感器。
[0158]
在本发明的一个实施例中,所述发酵反应器可包含c1-c5碳源,其为c1碳源或其衍生物。所述c1碳源可以是甲烷;甲醇、甲酸、甲醛或其衍生物。
[0159]
在本发明的又一实施例中,用于将c1-c5碳源引入发酵反应器的所述至少一个入
口是至少一个气体入口,优选地,所述至少一个气体入口是甲烷气体入口。
[0160]
在本发明的另一个实施例中,所述发酵反应器不包括用于从该发酵反应器排放未溶解和/或释放的气体的排气口。
[0161]
在本发明的另一个实施例中,所述发酵反应器包括用于从该发酵反应器排放未溶解和/或释放的气体的排气口。
[0162]
优选地,所述发酵反应器可以是气升式反应器、环流反应器、u形反应器或搅拌槽反应器,优选地,所述发酵反应器是环流反应器或u形反应器。
[0163]
在本发明的一个实施例中,所述发酵反应器是气升式反应器、环流反应器、u形反应器或搅拌槽反应器(优选是环流反应器或u形反应器),其中所述发酵器(优选顶部罐)包括至少一个目视检查装置。
[0164]
在本发明的一个实施例中,所述目视检查装置可以如此安置,使之具有水平或基本水平的检查视图。
[0165]
在本发明的另一个实施例中,可将目视检查装置安置在顶部罐的侧面,以获得发酵液表面上方和发酵液表面下方的组合视图。
[0166]
优选地,所述目视检查装置可安置在顶部罐的末端。
[0167]
更优选地,所述目视检查装置可安置在顶部罐的末端,从而提供从第一入口(或上流部分)到第一出口(或下流部分)的视图。
[0168]
在本发明的一个实施例中,所述目视检查装置可以是检查孔、照相机或检查孔和照相机的组合。
[0169]
优选地,所述检查孔可以是视镜。
[0170]
所述照相机可以是内联照相机(inline camera)。
[0171]
在本发明的一个实施例中,所述顶部罐可以设置有光源,以改善顶部罐内部的目视检查。光源可以提供为允许周围光线进入顶部罐的窗口和/或提供为并入顶部槽中的人造光源。
[0172]
在发酵反应器(尤其是环流反应器或u形反应器的顶部罐)中引入目视检查装置,可获得关于顶部罐中的发泡特性的直接和/或实时的信息。所述顶部罐中的发泡特性(如顶部储罐中出现的泡沫密度、泡沫高度和湍流水平)可能指示适当的c1-c5碳源与氧的比率和/或用于评估爆炸风险。因此,本发明的发明人发现传统上使用的泡沫传感器不足以监控发酵过程。
[0173]
本发明的一个优选实施例涉及用于发酵一种或多种微生物的发酵反应器,该发酵反应器包括用于将甲烷气体引入发酵反应器的至少一个进气口;以及用于从发酵反应器排放未溶解和/或释放的气体的排气口,以及一个或多个传感器,其中所述一个或多个传感器是用于确定发酵反应器中未溶解和/或释放的气体的浓度的一个或多个传感器。
[0174]
本发明还可涉及用于发酵一种或多种微生物的发酵反应器,该发酵反应器包括至少一个用于将c1-c5碳源,例如甲烷,引入发酵反应器的入口和一个或多个传感器,其中,所述一个或多个传感器是用于确定发酵反应器中未溶解和/或释放的气体的浓度的一个或多个传感器,其中所述未溶解和/或释放的气体为氧气。
[0175]
在本发明的一个优选实施例中,所述发酵反应器还包括用于从发酵反应器排出未溶解和/或释放的气体的排气口。
[0176]
在本发明的另一个实施例中,所述发酵反应器不包括用于从发酵反应器排出未溶解和/或释放的气体的排气口。
[0177]
所述发酵反应器可以优选地是气升式反应器、环流反应器、u形反应器或搅拌罐反应器。更优选地,所述发酵反应器可以是环流反应器或u形反应器。提供发酵反应器的基本构造(包括传感器、混合器、加压区和泵)的实例可以如wo 2010/069313和/或wo 2000/70014中所述,其通过引用并入本文。
[0178]
在本发明的一个实施例中,所述发酵反应器可包括一个或多个静态混合器。
[0179]
在本发明的另一个实施例中,所述发酵反应器包括一个或多个动态混合器。
[0180]
根据本发明的发酵反应器可包括至少一个静态混合器和至少一个动态混合器。
[0181]
所述发酵反应器还可包括循环泵。
[0182]
根据本发明的发酵反应器可进一步包括至少一个用于将氧气引入发酵反应器的进气口。
[0183]
根据本发明的发酵反应器可进一步包括至少一个用于将co2引入发酵反应器的入口。
[0184]
根据本发明的发酵反应器甚至可进一步包括至少一个用于将氮源引入发酵反应器的入口。
[0185]
在本发明的一个实施例中,所述一个或多个传感器是用于确定发酵反应器中未溶解和/或释放的氧气浓度的一个或多个传感器。所述一个或多个传感器可以是用于确定发酵反应器中未溶解和/或释放的甲烷浓度的一个或多个传感器。
[0186]
如果将发酵反应器用于厌氧发酵方法,则微生物体不需要氧气的存在。因此,在本发明的一个实施例中,所述发酵反应器不包括用于将氧气引入发酵反应器的进气口。
[0187]
根据本发明的发酵反应器还可包括co2传感器。
[0188]
在本发明的一个实施例中,所述发酵反应器可进一步包括氮传感器。
[0189]
在本发明的一个实施例中,所述至少一个传感器可以放置在发酵反应器的充满发酵培养基的区域中。
[0190]
在本发明的另一个实施例中,所述至少一个传感器可放置在排气口旁边。所述至少一个传感器可放置在顶部罐中。
[0191]
用于将氧气引入发酵反应器的至少一个进气口可由计算机控制。
[0192]
用于将甲烷气体引入发酵反应器的至少一个进气口可由计算机控制。
[0193]
所述一个或多个传感器可由计算机控制。
[0194]
在本发明的一个实施例中,用于将氧气引入发酵反应器的至少一个进气口和/或用于将甲烷气体引入发酵反应器的至少一个进气口可通过从一个或多个传感器获得的响应来控制。优选地,该控制由计算机实施。
[0195]
本发明的一个方面涉及包含本发明生物质材料的动物饲料产品或用于动物饲料产品的成分;或包含根据本发明的生物质材料的鱼饲料产品或用于鱼饲料产品的成分;或包含根据本发明的生物质材料的人类食品或用于人类食品的成分。
[0196]
在本发明的一个实施例中,所述动物饲料产品或用于动物饲料产品的成分;或鱼类饲料产品或用于鱼类饲料产品的成分;或者,人类食品或用于人类食品的成分可以是干燥形式或液体形式。
[0197]
应当注意,在本发明的一个方面的上下文中描述的实施例和特征也适用于本发明的其他方面。
[0198]
本发明引用的所有专利和非专利的参考文献通过引用其整体并入本文。
实施例
[0199]
实施例1-甲烷营养型细菌的厌氧发酵
[0200]
在试验工场中连续发酵荚膜甲基球菌,并且在连续相中以10g/l运行,其中累积大量硝酸盐/亚硝酸盐,并且在连续发酵后停止供氧,且未停止引入氧气。开始向u形回路反应器中供应co2,以便在u形反应器中提供厌氧阶段。
[0201]
图2显示了试验工场中,甲烷营养菌(荚膜甲基球菌)在厌氧条件下连续发酵92小时的生长情况。发酵68小时后,停止供氧,生物质持续增长后,伴随着酸水平下降(用三角形表示);no
2-水平(用正方形表示)和no
3-水平(用圆圈表示),在24小时内(从连续发酵开始的68小时到92小时)都会显著下降。因此,可以在不提供气态氧的情况下进行甲烷营养菌例如荚膜甲基球菌的厌氧发酵。
[0202]
在24小时内,通过消耗发酵培养基中存在的酸、硝酸盐(1400ppm至100ppm)和亚硝酸盐(150ppm至10ppm),生物质显示连续缓慢生长至11.5g/l。
[0203]
这清楚地表明,在24小时内,生物质能够在厌氧发酵条件下生长,该发酵反应器中没有任何未溶解的氧气和/或废气中的气态氧含量。
[0204]
如linde et al(1999)所述,分析获得的生物质,结果表明,与在需氧发酵条件下产生的生物质的转录水平相比,该生物质显示降低了至少75个基因的转录水平,这是由于厌氧发酵过程引起的。
[0205]
参考文献
[0206]
wo 2010/069313
[0207]
wo 2000/70014
[0208]
linde et al(1999);“genome-wide transcriptional analysis of aerobic and anaerobic chemostat cultures of saccharomyces cerevisiae”;j.bacteriology,dec 1999,vol.181,no.24,p:7409-7413
再多了解一些
本文用于企业家、创业者技术爱好者查询,结果仅供参考。