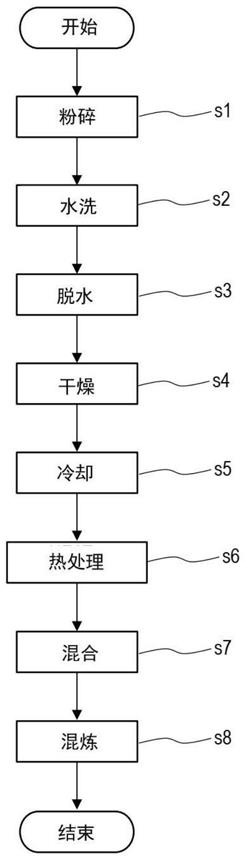
1.本发明涉及一种铸造用砂再生方法,更具体而言,涉及一种用于使表面粘附有无机粘结剂的已使用铸造用砂再生的铸造用砂再生方法。
背景技术:
2.在实践中,从已用于铸造的砂模(sand mold)中回收铸造用砂,并在执行再生过程以去除粘附到铸造用砂表面的粘结剂后,将铸造用砂作为再生铸造用砂重新进行铸造。用于形成砂模的粘结剂可大致分为酚醛树脂和呋喃树脂之类的有机粘结剂和硅酸钠(水玻璃)之类的无机粘结剂。
3.一般而言,无机粘结剂比有机粘结剂更难从铸造用砂的表面上去除。例如,粘附到铸造用砂表面上的有机粘结剂可通过焙烧去除,但无机粘结剂即使通过焙烧也无法去除。此外,通过对铸造用砂加热后进行研磨,可以在一定程度上去除粘附到表面上的无机粘结剂,但在这种情况下,砂表面可能会变得不平整或砂本身可能会粉碎。因此,当使用无机粘结剂时,铸造用砂的可回收性比使用有机粘结剂时要差。此外,无机粘结剂很难通过使用化学品以化学方法去除。
4.因此,当使用无机粘结剂作为形成砂模的粘结剂时,比使用有机粘结剂时更难使铸造用砂再生。因此,本技术的申请人在专利文件1中提出了一种再生方法,该方法能够使表面粘附有无机粘结剂的铸造用砂适当地再生。专利文件1公开的再生方法包括以下步骤(1)至(4)。
5.(1)粉碎步骤,将回收的铸造用砂模粉碎成小块,并将其制成粉碎铸造用砂。
6.(2)混合步骤,在5℃至70℃的水中混合和搅拌获得的粉碎铸造用砂,以使粘附到表面上的无机粘结剂与铸造用砂分离。
7.(3)回收、搅拌、加热以及干燥步骤,回收已与无机粘结剂分离的铸造用砂,并对铸造用砂进行搅拌、加热以及干燥。
8.(4)去除步骤,从加热和干燥后的铸造用砂中去除细粒。
9.引文列表
10.专利文献
11.[专利文件1]6188502号日本专利
技术实现要素:
[0012]
技术问题
[0013]
然而,发明人进行了详细的研究,发现如果使用专利文件1的再生方法使铸造用砂反复再生,粘附到铸造产物表面上的砂量会增加,因此铸造产物表面上可能会残留一些砂。此外,如果是精细复杂的形状,例如,气缸盖的水套,则会出现一个问题,即砂可能会堵塞流动路径,并且无法通过落砂机(knockout machine)或超声波水洗机等将砂去除。
[0014]
本发明是鉴于上述问题而提出的,其目的在于提供一种铸造用砂再生方法,其中,
即使使表面粘附有无机粘结剂的铸造用砂反复再生,粘附到铸造产物上的砂量也不太可能增加。
[0015]
问题解决方案
[0016]
根据本发明的实施例,提供了如下所述的铸造用砂再生方法。
[0017]
[第1项]
[0018]
一种用于使表面粘附有无机粘结剂的已使用铸造用砂再生的铸造用砂再生方法,包括以下步骤:
[0019]
粉碎步骤,通过粉碎用于铸造的砂模来回收铸造用砂;
[0020]
水洗步骤,在所述粉碎步骤后,在不低于5℃且不高于100℃的水中搅拌清洗所述铸造用砂;以及
[0021]
热处理步骤,在所述水洗步骤后,将所述铸造用砂加热至不低于550℃且不高于900℃的温度。
[0022]
因为根据本发明实施例的铸造用砂再生方法包括,在水洗步骤后,将所述铸造用砂加热至不低于550℃且不高于900℃的温度的热处理步骤,此热处理步骤可消除(即,脱水)存在于所述铸造用砂和残留在其表面上的无机粘结剂之间的水分以及所述无机粘结剂中所含的结晶水。因此,当使用由根据本发明实施例的铸造用砂再生方法再生的铸造用砂形成的砂模进行铸造时,可以防止铸造用砂因受潮而粘到铸造产物上。
[0023]
[第2项]
[0024]
根据第1项所述的铸造用砂再生方法,其中,在移动所述铸造用砂的同时执行所述热处理步骤。
[0025]
当在移动所述铸造用砂的同时执行所述热处理步骤时,由于无机粘结剂软化,可以防止相邻的砂颗粒相互粘结。
[0026]
[第3项]
[0027]
根据第1项或第2项所述的铸造用砂再生方法,其中,所述水洗步骤中的水温不低于20℃且不高于100℃。
[0028]
当所述水洗步骤中的水温为20℃或更高温度时,所述无机粘结剂的溶解度可以足够高。此外,可以缩短后续步骤中的预热时间。
[0029]
[第4项]
[0030]
根据第1项或第2项所述的铸造用砂再生方法,其中,所述水洗步骤中的水温不低于80℃且不高于100℃。
[0031]
当所述水洗步骤中的水温为80℃或更高温度时,可进一步缩短后续步骤中的预热时间。
[0032]
[第5项]
[0033]
根据第1项至第4项中任一项所述的铸造用砂再生方法,还包括在所述水洗步骤和所述热处理步骤之间的干燥步骤,所述干燥步骤通过将所述铸造用砂搅拌加热至不低于100℃且不高于300℃的温度来对所述铸造用砂进行干燥。
[0034]
在所述水洗步骤和所述热处理步骤之间,可执行通过将所述铸造用砂搅拌加热至不低于100℃且不高于300℃的温度来对所述铸造用砂进行干燥的干燥步骤。通过执行所述干燥步骤,可以很容易地获得具有平滑表面的干砂,并且在砂表面上形成残留粘结剂的涂
层。
[0035]
[第6项]
[0036]
根据第5项所述的铸造用砂再生方法,还包括在所述水洗步骤和所述干燥步骤之间的脱水步骤,所述脱水步骤从所述铸造用砂中分离并去除所述水洗步骤中使用的大部分水。
[0037]
通过在所述水洗步骤和所述干燥步骤之间执行脱水步骤,可以降低所述干燥步骤所需的能量。
[0038]
[第7项]
[0039]
根据第6项所述的铸造用砂再生方法,其中,所述水洗步骤、所述脱水步骤以及所述干燥步骤在同一设施中进行。
[0040]
当在同一设施中执行所述水洗步骤、所述脱水步骤以及所述干燥步骤时,可缩小铸造用砂再生所需的整个设施的占地面积。
[0041]
[第8项]
[0042]
根据第6项所述的铸造用砂再生方法,其中,所述水洗步骤、所述脱水步骤以及所述干燥步骤在不同的设施中进行。
[0043]
当所述水洗步骤、所述脱水步骤以及所述干燥步骤在不同的设施中执行时,可以增加单位时间内的再生量。
[0044]
[第9项]
[0045]
根据第5项至第8项中任一项所述的铸造用砂再生方法,还包括在所述干燥步骤和所述热处理步骤之间通过通风对所述铸造用砂进行冷却的冷却步骤。
[0046]
当在所述干燥步骤和所述热处理步骤之间执行通过通风来冷却所述铸造用砂的冷却步骤时,可以防止所述铸造用砂上的结露(condensation)。
[0047]
[第10项]
[0048]
根据第1项至第9项中任一项所述的铸造用砂再生方法,其中,所述无机粘结剂包括硅酸钠。
[0049]
可适当使用含有硅酸钠(水玻璃)的无机粘结剂。
[0050]
[第11项]
[0051]
根据第10项所述的铸造用砂再生方法,其中,所述硅酸钠由通式na2o
·
nsio2表示(其中n不小于0.5且不大于4.0)。
[0052]
可适当使用由通式na2o
·
nsio2表示的硅酸钠(其中n不小于0.5且不大于4.0)。
[0053]
[第12项]
[0054]
根据权利要求1至9中任一项所述的铸造用砂再生方法,其中,
[0055]
所述无机粘结剂由通式xsio2·
ym2o
·
zh2o表示的碱硅酸盐水溶液组成(其中m为li
、k
或na
);
[0056]
将含钠材料作为吸潮剂添加到所述无机粘结剂中,使得所述含钠材料与所述碱硅酸盐水溶液之间的质量比在1:4至1:6的范围内;以及
[0057]
将沸点为250℃或更高的乳液形式的硅油作为表面活性剂进一步添加到所述无机粘结剂中,使得所述乳液中的硅油含量不低于所述无机粘结剂质量的8%且不高于其10%。
[0058]
所述无机粘结剂可以是水玻璃基粘结剂,由通式xsio2·
ym2o
·
zh2o表示的碱硅酸
盐水溶液组成(其中m为li
、k
或na
)。在这种情况下,优选向所述无机粘结剂中添加吸湿剂。具体而言,含钠材料可用作吸湿剂。所述含钠材料与所述所述碱硅酸盐水溶液的质量比优选在1:4至1:6的范围内。当所述含钠材料与碱硅酸盐水溶液的质量比在1:4至1:6的范围内时,例如,当所述碱硅酸盐水溶液中na2o和sio2的质量比(na2o/sio2)不小于2.5且不大于3.5(固体含量不低于20%且不高于40%)时,可防止所述无机粘结剂过早硬化。此外,优选将表面活性剂添加到此无机粘结剂中以适当地控制吸湿性。具体而言,优选添加沸点为250℃或更高的乳液形式的硅油作为表面活性剂,并且更优选的是乳液中的硅油含量不低于粘结剂质量的8%且不高于其10%。
[0059]
发明的有利效果
[0060]
根据本发明的实施例,提供了一种铸造用砂再生方法,其中,即使使表面粘附有无机粘结剂的铸造用砂反复再生,粘附到铸造产物上的砂量也不太可能增加。
附图说明
[0061]
[图1]示出根据本发明实施例的铸造用砂再生方法的一个实施例的流程图。
[0062]
[图2]示出热处理步骤s6中使用的窑炉10的图示。
[0063]
[图3]示出根据本发明实施例的铸造用砂再生方法的另一实施例的流程图。
[0064]
[图4]示出根据实施例、对照实施例以及参考实施例的粘附到铸造产物表面上的砂量的图表。
具体实施例
[0065]
对砂粘附到铸造产物表面上的机理进行详细研究后,发明人发现砂的粘附是由粘附到铸造用砂表面上的无机粘结剂(残留粘结剂)和砂之间存在的水分以及残留粘结剂中所含的结晶水引起的。本发明是基于上述发现而提出的。下文描述砂粘附机理和根据本发明实施例的铸造用砂再生方法。
[0066]
[砂粘附到铸造产物表面上的机理]
[0067]
当使用专利文件1的再生方法使铸造用砂反复再生20次以上时,会出现砂粘附到铝合金铸造产物表面上的现象。
[0068]
观察粘附到铸造产物表面上的砂以及砂与铸造产物表面之间的界面,发现有一种白色物质粘附到砂表面上。经x射线衍射技术鉴定,此白色物质的主要成分为一水合碳酸钠。
[0069]
用sem(扫描电子显微镜)观察砂和铸造产物表面之间的界面,由此发现存在类似粘结剂的膜。通过eds(能量色散x射线分析)对膜进行定性分析,并检测到硅(si)和氧(o),表明膜的成分与无机粘结剂的成分相似。
[0070]
当仅将再生砂放置在不锈钢杯中并加热至740℃时,观察到再生砂颗粒在杯中相互粘结的现象。对加热后的再生砂的观察表明,再生砂表层上的残留粘结剂层在约600℃下软化,产生气泡,进一步加热到740℃导致平滑。此外,气体分析确定从气泡中排出的气体为水、氢、一氧化碳以及二氧化碳。
[0071]
从这些事实可以推断,砂粘附是由以下机理引起的。首先,在与熔体接触的砂模表面上,通过将粘结剂成分加热至600℃或更高温度使其软化,并且砂和残留粘结剂之间的剩
余水分以及残留粘结剂中所含的结晶水与软化的粘结剂成分反应形成水玻璃。然后,粘结剂转化的水玻璃吸收砂和残留粘结剂之间产生的二氧化碳,以及砂模中的二氧化碳,形成凝胶(此时产生碳酸钠)。此后,粘结剂在粘附到铝合金的同时硬化,从而使砂粘附到铸造产物的表面上。
[0072]
因此,推测砂粘附是由于粘附到铸造用砂表面上的无机粘结剂(残留粘结剂)与砂之间存在的水分以及残留粘结剂中所含的结晶水引起的。
[0073]
[铸造用砂再生方法]
[0074]
将参照图1描述根据本发明实施例的铸造用砂再生方法。图1是示出根据本发明实施例的铸造用砂再生方法的一个实施例的流程图。根据本发明实施例的铸造用砂再生方法是一种用于使表面粘附有无机粘结剂的已使用铸造用砂再生的方法。
[0075]
《铸造用砂》
[0076]
可以使用各种已知的耐火粒状材料作为铸造用砂而没有任何特别限制。例如,可以使用硅砂、铬铁矿砂、锆英砂、橄榄石砂、合成莫来石砂、以及氧化铝基集料颗粒。这些粒状材料可以单独使用,也可以组合其中两种或两种以上。在此例示的粒状材料中,从成型模具的填充性和铸造后砂模的塌陷性的角度来看,优选氧化铝基集料颗粒。
[0077]
铸造用砂可以是新砂、再生一次或多次的再生砂,也可以是新砂和再生砂的混合物。当使用混合物时,相对于再生砂的质量,新砂的质量例如不小于0.01倍且不大于10倍,优选不小于0.1倍且不大于10倍,更优选不小于1倍且不大于10倍。
[0078]
《无机粘结剂》
[0079]
例如,硅酸钠(水玻璃)、粘土、硅溶胶、硫酸盐、磷酸盐以及硝酸盐可用作砂模形成的无机粘结剂。无机粘结剂,诸如,在此例示的那些,可以单独使用,也可以组合其中两种或两种以上。
[0080]
在图示的无机粘结剂中,优选硅酸钠,更优选由通式na2o
·
nsio2(其中n不小于0.5且不大于4.0)表示的那些硅酸钠。此类硅酸钠基于氧化钠和二氧化硅之间的摩尔比(即,上述通式中的n的值)分类。具体而言,可以使用原硅酸钠[na4sio4(na2o
·
0.5sio2:n=0.5)]、偏硅酸钠[na2sio3(na2o
·
sio2:n=1)]等。硅酸钠的其他实施例包括jis no.1硅酸钠[na2si2o5(na2o
·
2sio2:n=2)]、jis no.2硅酸钠[na4si5o
12
(na2o
·
2.5sio2:n=2.5)]、jis no.3硅酸钠[na2si3o7(na2o
·
3sio2:n=3)]以及jis no.4硅酸钠[na2si4o9(na2o
·
4sio2:n=4)]。
[0081]
无机粘结剂可以是由通式xsio2·
ym2o
·
zh2o(其中m为li 、k 或na )表示的碱金属硅酸盐水溶液组成的水玻璃基粘结剂。在这种情况下,优选的是将吸湿剂(或湿性赋予剂)添加到无机粘结剂中。具体而言,可以使用含钠材料作为吸湿剂。含钠材料与碱金属硅酸盐水溶液的质量比优选在1:4至1:6的范围内。当含钠材料与碱金属硅酸盐水溶液的质量比在1:4至1:6的范围内时,例如,当碱金属硅酸盐水溶液中的na2o和sio2的质量比(na2o/sio2)不小于2.5且不大于3.5(固体含量不小于20%且不大于40%)时,可以防止无机粘结剂过早硬化。此外,为了适当地控制吸湿性(湿性赋予性),优选在无机粘结剂中添加表面活性剂。具体而言,优选添加沸点为250℃或更高的乳液形式的硅油作为表面活性剂,且更优选的是乳液中的硅油含量不低于粘结剂质量的8%且不超过其10%。
[0082]
当形成砂模时,添加到铸造用砂中的无机粘结剂的量优选不小于质量分数0.2%
且不大于质量分数10%,且更优选的是不小于质量分数0.5%且不大于质量分数5%。
[0083]
《粉碎步骤》
[0084]
首先,用于铸造的砂模被粉碎以回收铸造用砂(粉碎步骤s1)。对砂模的粉碎方法没有特别限制,可以使用已知的各种粉碎方法。例如,可以通过粉碎机进行粉碎。如果砂模是芯体,则在用落砂机等将砂去除后,使用清砂器(sand-fresher)等将其制成细粒。
[0085]
《水洗步骤》
[0086]
接下来,在不低于5℃且不高于100℃的水中搅拌清洗铸造用砂(水洗步骤s2)。这使得粘附到铸造用砂表面上的无机粘结剂溶解在水中并在一定程度上被去除。对水的用量没有特别限制,只要能在一定程度上去除粘附到铸造用砂上的无机粘结剂即可。例如,相对于铸造用砂的质量,该量不小于其0.5倍且不大于100倍,优选不小于0.5倍且不大于50倍,更优选不小于1倍且不大于30倍。
[0087]
对搅拌方法没有特别限制,可以使用任何已知的搅拌方法,只要能够在一定程度上去除粘附到铸造用砂上的无机粘结剂即可。例如,可以通过使用搅拌器(混合器)适当地进行搅拌。从充分去除粘附到铸造用砂上的无机粘结剂和防止铸造用砂的粒度因搅拌而变得不均匀的角度来看,搅拌器的转数为,例如,不小于30rpm且不大于300rpm,优选不小于40rpm且不大于250rpm,更优选不小于50rpm且不大于200rpm。搅拌时间为,例如,不低于5分钟且不超过60分钟,优选不低于10分钟且不超过50分钟,更优选不低于15分钟且不超过40分钟。用搅拌器搅拌时的转数和搅拌时间可以根据搅拌器的规格以及铸造用砂和无机粘结剂的类型在上述范围内适当设定。
[0088]
《脱水步骤》
[0089]
然后,从铸造用砂中分离并去除在水洗步骤s2中使用的大部分水(脱水步骤s3)。对脱水方法没有特别限制,可以使用任何已知的脱水方法,只要能够从铸造用砂中分离并去除大部分水即可。
[0090]
例如,准备一个容器,容器具有排水口和进气孔,排水口装有铁丝网或类似物以防止砂流出,进气孔用于引入压缩空气,容器可以气密密封,除了排水口和进气孔外。将水洗后的含水砂置于此容器中,在砂静止的状态下通过进气孔向容器内引入压缩空气(例如,0.2mpa或0.2mpa以下),以使残留在砂粒间的水分排出,便于脱水。
[0091]
《干燥步骤》
[0092]
接下来,将铸造用砂搅拌加热至不低于100℃且不高于300℃的温度进行干燥(干燥步骤s4)。脱水后的砂可以通过在搅拌的同时向砂施用例如,热空气、微波或过热蒸汽来干燥。这可以产生具有球形平滑表面的干砂,同时在砂表面上形成具有残留粘结剂成分的涂层。
[0093]
《冷却步骤》
[0094]
然后,在通风的同时将铸造用砂冷却到预定温度(例如,60℃)(冷却步骤s5)。例如,可以通过向铸造用砂施用冷空气来进行冷却。
[0095]
《热处理步骤》
[0096]
之后,将铸造用砂加热至不低于550℃且不高于900℃的温度(热处理步骤s6)。对热处理没有特别限制,只要可以将铸造用砂加热至不低于550℃且不高于900℃的温度即可。例如,如果使用窑炉作为进行热处理的装置,则可以在移动铸造用砂的同时将铸造用砂
加热至不低于550℃且不高于900℃的温度。热处理时间可适当设定。例如,可以在电子显微镜下检查热处理后的砂的表面,且可以设定热处理时间,使表面处于适当的状态。或者,也可以将热处理后的砂放入水中,且设定热处理时间,使溶解的钠离子浓度适当。
[0097]
图2示出了热处理步骤s6中使用的窑炉的实施例。图2所示的窑炉(回转炉)10装有主体(窑炉的主体)11、主体11内部的螺旋叶片(给料器)12、以及对主体11内部进行加热的燃烧器13。主体11的一端有一个入口11a,用于将经过处理的物质1(在此例中是铸造用砂)引入主体11,而在另一端,有一个出口11b,用于将经过处理的物质1排出主体11。窑炉10是在使螺旋叶片12旋转的同时对从入口11a引入的经过处理的物质1进行热处理,然后传送所得的经过热处理的物质以使其从出口排出的装置。使用这种窑炉10允许在移动铸造用砂的同时进行热处理。虽然图2示出了其中经过处理的物质1直接暴露于燃烧器13的火焰的构造,但窑炉10不限于这种构造。
[0098]
《混合步骤》
[0099]
接下来,将预定量的新砂(例如,质量分数为5%)添加到热处理后的铸造用砂中并进行混合(混合步骤s7)。执行混合步骤s7的目的是调整粒度并补充已经损失的部分。
[0100]
《混炼步骤》
[0101]
之后,进一步添加粘结剂(无机粘结剂)并进行混炼,从而提供混炼砂(混炼步骤s8)。以这种方式,可以使表面粘附有无机粘结剂的已使用铸造用砂再生。
[0102]
如上所述,根据本发明实施例的铸造用砂再生方法包括热处理步骤s6,其在水洗步骤s2之后将铸造用砂加热至不低于550℃且不高于900℃的温度,使得热处理步骤s6可以消除(即,脱水;也就是说,最大程度减少)存在于铸造用砂与残留在其表面上的无机粘结剂之间的水分以及无机粘结剂中所含的结晶水。因此,当使用由根据本发明实施例的铸造用砂再生方法再生的铸造用砂形成的砂模进行铸造时,可以防止铸造用砂由于受潮而粘到铸造产物上。
[0103]
当在移动铸造用砂的同时进行热处理步骤时(例如,通过搅拌或振动它),由于无机粘结剂软化,可以防止相邻的砂粒彼此粘结。优选继续移动铸造用砂直到其温度低于550℃为止。
[0104]
水洗步骤中的水温优选不低于20℃且不高于100℃。当水温为20℃或更高温度时,无机粘结剂的溶解度可以足够高。此外,可以缩短后续步骤中的预热时间。
[0105]
水洗步骤中的水温更优选不低于80℃且不高于100℃。当水洗步骤中的水温为80℃或更高温度时,可进一步缩短后续步骤中的预热时间。
[0106]
如图所示,通过在水洗步骤s2和热处理步骤s6之间进行将铸造用砂搅拌加热至不低于100℃且不高于300℃的温度进行干燥的干燥步骤s4,可以很容易地获得具有平滑表面的干砂,并且在砂表面上形成残留粘结剂的涂层。
[0107]
只要在热处理步骤s6中能够在砂表面上适当地形成残留粘结剂的涂层,干燥步骤s4(和冷却步骤s5)就可以省略,如图3所示,其中热处理步骤s6基本上兼作干燥步骤s4。例如,通过使用上述窑炉10等,可以在热处理步骤s6中在搅拌铸造用砂的同时进行热处理,由此热处理步骤s6基本上可以兼作干燥步骤s4。
[0108]
此外,通过在水洗步骤s2和干燥步骤s4之间进行脱水步骤s3,能够降低干燥步骤s4所需的能量。
[0109]
水洗步骤s2、脱水步骤s3以及干燥步骤s4可以在同一设施中进行,也可以在不同的设施中进行。当水洗步骤s2、脱水步骤s3以及干燥步骤s4在同一设施中进行时,能够缩小铸造用砂再生所需的整个设施的占地面积。当水洗步骤s2、脱水步骤s3以及干燥步骤s4在不同的设施中进行时,能够增加单位时间的再生量。
[0110]
如果在干燥步骤s4之后立即将热砂直接放入料斗中并冷却至室温,则料斗内和砂粒之间的热空气可能会冷却并引起结露。如果这种结露产生的水分与砂表面上残留的粘结剂发生反应,就会发生阻塞。通过在干燥步骤s4和热处理步骤s6之间进行对铸造用砂进行通风以使其冷却的冷却步骤s5,能够防止铸造用砂上的结露。因此,能够防止上述阻塞。
[0111]
[防止砂粘附效果的研究结果]
[0112]
将描述通过使用根据本发明实施例的铸造用砂再生方法使铸造用砂实际再生并研究防止砂粘附的效果的结果。
[0113]
《实施例》
[0114]
根据实施例的再生铸造用砂如下获得。
[0115]
·
粉碎步骤
[0116]
将在除砂步骤后回收的砂模(芯体)的部分(fraction)(粗粒)放入装有2-4mm筛网的清砂器中,并进行振动,使粗粒相互摩擦,形成细颗粒。通过网口为850μm的钢丝网来回收铸造用砂。
[0117]
·
水洗步骤
[0118]
将250kg铸造用砂和250kg水放入远州铁工所(enshu iron works)制造的混合器中,且使叶轮以61rpm旋转20分钟进行水洗。
[0119]
·
脱水步骤
[0120]
上述混合器底部安装有配置有防止砂流出的铁丝网过滤器的排水口,且除引入压缩空气的进气孔和排水口外的所有阀门均关闭,准备好进行气密密封。水洗后,停止叶轮,然后关闭除进气孔以外的阀门,打开排水口阀门,且通过进气孔将0.2mpa的压缩空气引入混合器。通过引入压缩空气20分钟,进行脱水直至水分含量为5%-10%为止。
[0121]
·
干燥步骤
[0122]
在上述混合器中,打开排气口和热风孔的阀门,且在混合器叶轮以81rpm旋转的同时,从热风孔吹入300℃的热空气,并从排气口排出,以获得具有平滑球面的干砂。
[0123]
·
冷却步骤
[0124]
在上述混合器中,在干燥步骤之后,关闭热空气发生器的加热器并切换到鼓风机运行,使叶轮的旋转降低至27rpm,并继续搅拌直至达到约60℃为止。然后排入料斗。
[0125]
·
热处理步骤
[0126]
将干燥步骤后的铸造用砂放入远州铁工所制造的回转炉中,在750℃下加热10分钟,并冷却至500℃,之后回收铸造用砂。
[0127]
《对照实施例》
[0128]
提供了通过专利文件1的再生方法再生的铸造用砂。具体而言,除了不进行热处理步骤之外,铸造用砂再生方式与实施例类似。
[0129]
《参考实施例》
[0130]
提供新砂作为参考实施例。
[0131]
《粘附砂量》
[0132]
使用如上所述提供的实施例、对照实施例以及参考实施例制成砂模(芯体),并使用它们提供铝合金的铸造产物。然后,研究了粘附到铸造产物表面上的砂量。
[0133]
·
芯体制造
[0134]
将质量分数为0.2%的烧碱、质量分数为1.0%的硅酸钠以及质量分数为0.6%的纳米二氧化硅悬浮液添加到实施例、对照实施例以及参考实施例的铸造用砂中并进行混炼后,将其倒入成型模具中,脱水和硬化后取出,以获得芯体。
[0135]
·
铸造
[0136]
通过采用芯体,利用重力铸造来铸造气缸盖。使用铝合金ac4b作为气缸盖的材料。
[0137]
·
除砂
[0138]
将所得气缸盖安装在由yomar co.,ltd.制造的落砂机上并经受敲击和摇晃30秒。
[0139]
对于实施例、对照实施例以及参考实施例,粘附到铸造产物表面上的砂量的测量结果示于表1和图4中。
[0140]
[表1]
[0141] 粘附砂量参考实施例(新砂)0.86g对照实施例8.01g实施例0.95g
[0142]
从表1和图4可知,对照实施例的粘附砂量远多于参考实施例(新砂)。另一方面,实施例中的粘附砂量与参考实施例中的几乎相同。在实施例中,砂模(芯体)还具有良好的塌陷性,类似于参考实施例。因此,经证实,根据本发明的实施例,粘附到铸造产物上的砂量与新砂相当。
[0143]
如上所述,根据本发明实施例的铸造用砂再生方法是一种用于使表面粘附有无机粘结剂的已使用铸造用砂1再生的铸造用砂再生方法,包括以下步骤:粉碎步骤s1,通过粉碎用于铸造的砂模来回收铸造用砂1;水洗步骤s2,在粉碎步骤s1之后,在不低于5℃且不高于100℃的水中搅拌清洗铸造用砂1;以及热处理步骤s6,在水洗步骤s2之后,将铸造用砂1加热至不低于550℃且不高于900℃的温度。
[0144]
根据本发明的实施例的铸造用砂再生方法包括热处理步骤s6,其中在水洗步骤s2之后将铸造用砂1加热至不低于550℃且不高于900℃的温度,使得热处理步骤s6可以消除(即脱水)存在于铸造用砂1与残留在其表面上的无机粘结剂之间的水分以及无机粘结剂中所含的结晶水。因此,当使用由根据本发明实施例的铸造用砂再生方法再生的铸造用砂1形成的砂模进行铸造时,可以防止铸造用砂1由于受潮而粘到铸造产物上。
[0145]
在一个实施例中,在移动铸造用砂1的同时执行热处理步骤s6。
[0146]
当在移动铸造用砂1的同时执行热处理步骤s6时,由于无机粘结剂软化,能够防止相邻的砂颗粒相互粘结。
[0147]
在一个实施例中,水洗步骤s2中的水温不低于20℃且不高于100℃。
[0148]
当水洗步骤s2中的水温为20℃或更高温度时,可以使无机粘结剂的溶解度足够高。此外,可以缩短后续步骤中的预热时间。
[0149]
在一个实施例中,水洗步骤s2中的水温不低于80℃且不高于100℃。
[0150]
当水洗步骤s2中的水温为80℃或更高温度时,能够进一步缩短后续步骤中的预热时间。
[0151]
在一个实施例中,铸造用砂再生方法还包括,在水洗步骤s2和热处理步骤s6之间,通过将铸造用砂1搅拌加热至不低于100℃且不高于300℃的温度来对铸造用砂1进行干燥的干燥步骤s4。
[0152]
在水洗步骤s2和热处理步骤s6之间,可执行将铸造用砂1搅拌加热至不低于100℃且不高于300℃的温度来对铸造用砂1进行干燥的干燥步骤s4。通过执行干燥步骤s4,可以很容易地获得具有平滑表面的干砂,并且在砂表面上形成残留粘结剂的涂层。
[0153]
在一个实施例中,铸造用砂再生方法还包括在水洗步骤s2和干燥步骤s4之间的脱水步骤s3,以从铸造用砂1中分离并去除水洗步骤s2中使用的大部分水。
[0154]
通过在水洗步骤s2和干燥步骤s4之间执行脱水步骤s3,能够降低干燥步骤s4所需的能量。
[0155]
在一个实施例中,水洗步骤s2、脱水步骤s3以及干燥步骤s4在同一设施中进行。
[0156]
当水洗步骤s2、脱水步骤s3以及干燥步骤s4在同一设施中进行时,可以缩小铸造用砂1再生所需的整个设施的占地面积。
[0157]
在一个实施例中,水洗步骤s2、脱水步骤s3以及干燥步骤s4在不同的设施中进行。
[0158]
当水洗步骤s2、脱水步骤s3以及干燥步骤s4在不同的设施中进行时,可以增加单位时间的再生量。
[0159]
在一个实施例中,铸造用砂再生方法还包括在干燥步骤s4和热处理步骤s6之间通过通风来对铸造用砂1进行冷却的冷却步骤s5。
[0160]
通过在干燥步骤s4和热处理步骤s6之间进行对铸造用砂1进行通风以使其冷却的冷却步骤s5,能够防止铸造用砂1上的结露。
[0161]
在一个实施例中,无机粘结剂包含硅酸钠。
[0162]
可以适当地使用含有硅酸钠(水玻璃)的无机粘结剂。
[0163]
在一个实施例中,硅酸钠由通式na2o
·
nsio2表示(其中n不小于0.5且不大于4.0)。
[0164]
可适当使用由通式na2o
·
nsio2表示的硅酸钠(其中n不小于0.5且不大于4.0)。
[0165]
在一个实施例中,无机粘结剂由通式xsio2·
ym2o
·
zh2o表示的碱硅酸盐水溶液组成(其中m为li
、k
或na
);将含钠材料作为吸潮剂添加到无机粘结剂中,使得含钠材料与碱硅酸盐水溶液之间的质量比在1:4至1:6的范围内;以及将沸点为250℃或更高的乳液形式的硅油作为表面活性剂进一步添加到无机粘结剂中,使得乳液中的硅油含量不低于无机粘结剂质量的8%且不高于其10%。
[0166]
无机粘结剂可以是水玻璃基粘结剂,由通式xsio2·
ym2o
·
zh2o表示的碱硅酸盐水溶液组成(其中m为li
、k
或na
)。在这种情况下,优选向无机粘结剂中添加吸湿剂。具体而言,可将含钠材料用作吸湿剂。含钠材料与碱硅酸盐水溶液的质量比优选在1:4至1:6的范围内。当含钠材料与碱硅酸盐水溶液的质量比在1:4至1:6的范围内时,例如,当碱硅酸盐水溶液中na2o和sio2的质量比(na2o/sio2)不小于2.5且不大于3.5(固体含量不低于20%且不高于40%)时,可防止无机粘结剂过早硬化。此外,优选将表面活性剂添加到此无机粘结剂中以适当地控制吸湿性。具体而言,优选添加沸点为250℃或更高的乳液形式的硅油作为表面活性剂,并且更优选的是乳液中的硅油含量不低于粘结剂质量的8%且不高于其10%。
[0167]
工业适用性
[0168]
根据本发明的实施例,提供了一种铸造用砂再生方法,其中,即使使表面粘附有无机粘结剂的铸造用砂反复再生,粘附到铸造产物上的砂量也不太可能增加。
[0169]
附图标记列表
[0170]1ꢀꢀꢀ
经过处理的物质(铸造用砂)
[0171]
10
ꢀꢀ
窑炉
[0172]
11
ꢀꢀ
旋转体
[0173]
11a 入口
[0174]
11b 出口
[0175]
12
ꢀꢀ
燃烧器
再多了解一些
本文用于企业家、创业者技术爱好者查询,结果仅供参考。