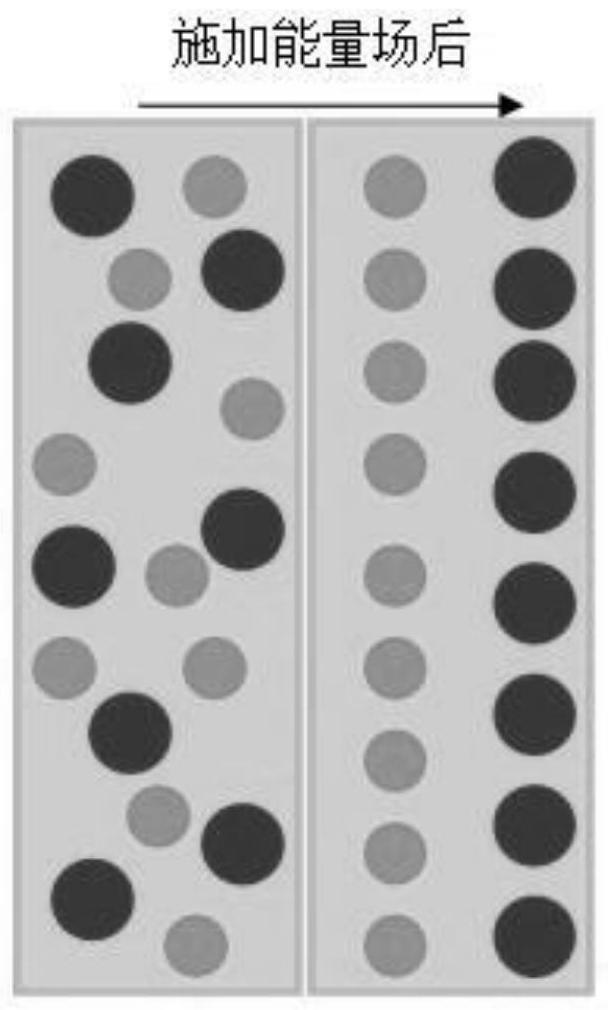
1.本发明属于电子薄膜材料,具体涉及一种铜合金薄膜以及基于该铜合金薄膜在铜线路板表面、铜基板焊盘表面形成的保护层和方法。
背景技术:
2.随着科技的发展,人们对便携式电子产品的需求日益增加,轻薄,短小的电子产品更能得到市场,这使得印制电路板要变得更加微小并且高密度集成。同时,电子元器件服役时的工作条件愈加恶劣,经常在高温,高湿,高电压情况下长时间工作。近些年,在印制电路板的引线之间发现了腐蚀失效。由于高密度集成印制电路板上引线间距很小,当印制电路板通电后,相邻的引线之间存在着压差,相邻引线之间构成一个类似电容器的结构,在高温高湿情况下,会发生电化学迁移,金属离子从一侧的引线向另一侧移动,最终形成一条电化学迁移路径使引线之间短路,最终导致电子仪器的失效。
3.为了提高印制电路板的可靠性,会对印制电路板采取一些表面处理,例如浸银(imag)、浸金(enig)等方法。其中浸银(imag)技术广泛应用,特别是作连接器的接触材料,因为它具有优异的耐腐蚀性、低电阻率、低成本的优点。但是浸银技术的工艺特点使得浸银的印制电路板上镀银层很薄,有许多微小的孔洞,并且银镀层不能完整的覆盖在基板金属上。因此,尽管对印制电路板采取了浸银处理,但在一定的湿度和温度条件下银镀层会与基板金属铜发生电化学反应,使铜发生电化学迁移现象,导致电子设备失效。
技术实现要素:
4.发明目的:本发明的目的在于提供一种用于防止电子设备失效的具有正混合熵的铜合金薄膜;本发明的第二目的在于提供一种基于具有正混合熵的铜合金薄膜在服役中形成的保护层;本发明的第三目的在于提供上述保护层的制备方法。
5.技术方案:本发明的一种铜合金薄膜,所述铜合金薄膜为二元合金,包括铜元素以及与铜在常温、稳态条件下形成正混合熵的添加元素;其中,铜元素的质量百分含量为95~99wt%。
6.进一步的,所述添加元素选自mo、ni、co和cr中的任一种。
7.进一步的,所述常温为25℃,所述稳态条件具体是指使用薄膜达到热力学平衡的条件。
8.本发明还保护一种服役后的保护层,该保护层包括基底,和设于基底上的铜合金薄膜,铜合金薄膜位于基底表面。
9.本发明还进一步保护上述的保护层的制备方法,在基底上形成具有正混合焓的铜合金薄膜;对铜合金薄膜施加能量场,使其中的添加元素析出并在铜薄膜表面形成保护层。
10.进一步的,所述能量场包括电场、温度场或应力场;能量场维持时间为4~24h。
11.进一步的,所述电场是在铜合金薄膜上施加3~9v的电压形成;所述温度场的温度为25~60℃,湿度为30%~90%rh。
12.进一步的,采用物理和/或化学沉积方式在基底上形成铜合金薄膜。
13.进一步的,所述物理和/或化学沉积方式包括电镀、磁控溅射、气相沉积中的任意一种或多种方式的组合。
14.进一步的,所述基底包括金属基底或树脂基底。具体包括铜线路板、铜基板焊盘、印制电路板等。
15.本发明保护层的成型原理为:本发明中的铜合金薄膜为二元合金体系,具体包括cu-mo、cu-ni、cu-co、cu-cr合金系列,由于cu与金属co、cr、mo、ni的混合焓在常温25℃、稳态条件下为正值,因此所形成的二元合金在室温、稳态条件下很难形成固溶体或金属间化合物。参见图1,无论是电镀、磁控溅射、还是气相沉积形成的一定配比的cu与金属co、cr、fe、mo、ni的混合薄膜层,必然处于一个热力学的不稳定状态,该不稳定的二元合金镀层,会在外加能量场(比如电场、温度场,甚至是应力场)的作用下趋于稳定,形成双层薄膜,此时添加元素会在铜表面析出形成一层金属层,进而在铜薄膜的表面形成保护层。
16.本发明通过混合焓为正的合金来抑制电化学迁移现象,具有正混合焓的合金互不相溶,其金属离子在压差的驱动下会向相反方向运动,最终导致分层;通过一次镀膜方式,在后续服役过程中,由于电子风力或温度梯度的驱动下,原子趋于重新排列,达到能量最低,形成双层镀膜,自然形成镀层的分离,在铜表面形成金属防护层,该层金属由于焊料较低,对纯铜本身的热导率、电导率影响可以忽略不计。
17.有益效果:与现有技术相比,本发明的具有如下显著优点:本发明采取在铜线路板上沉积具有正的混合焓的铜合金薄膜,通过压差的作用导致合金中的添加元素向表面运动,最终使添加元素覆盖在铜上,抑制了金属铜的电化学迁移,通过在铜的表面形成保护层,可以进一步提高铜线路板对电化学迁移的抵抗能力,更好的防止了铜线路板被腐蚀,大幅提高了此类电子仪器的使用寿命;本发明的制备方法可以一次形成双元素镀层,简化了工艺,提高了镀层的可靠性。
附图说明
18.图1是本发明的保护层成型原理示意图;
19.图2是本发明的基板样品制作流程示意图;
20.图3是实施例1制备的铜钼合金镀层表面形貌图;
21.图4是实施例1制备的铜钼合金镀层能谱测试图;
22.图5是实施例1制备的铜钼合金镀层在能量场作用后的截面扫描图;
23.图6是实施例1制备的铜钼合金镀层在能量场作用后的eds线扫描图谱;
24.图7是实施例2制备的铜铬合金xrd图;
25.图8是实施例4制备的cu-ni二元固溶体相图;
26.图9是实施例5制备的铜镍合金镀层通电后测试图;
27.图10是对比例1制备的铜薄膜截面微观扫描图;
28.图11是对比例1制备的铜薄膜表面形貌图;
29.图12是对比例1制备的铜薄膜在能量场作用后的截面扫描图;
30.图13是对比例1制备的铜薄膜在能量场作用后的eds线扫描图谱;
31.图14是对比例2制备的铜钼合金镀层在能量场作用后的截面扫描图。
具体实施方式
32.下面结合附图和实施例对本发明的技术方案做进一步详细说明。
33.参见图2的基板样品流程,以树脂基底、电镀铜为例,具体包括三个步骤,第一步:切割出目标尺寸的树脂板;如果是电镀镀层,需要制备目标电流密度条件下的涂层数值板;电流密度根据电镀所用电压除以阴极拟镀件浸入镀液的面积来计算;第二步:制备带有目标铜镀层的树脂基板;第三步:将镀层基板制备成可以通电场的正负极基板,进行电压条件下的镀层物质迁移观察。
34.实施例1
35.在印制电路板上电沉积铜钼合金,然后该合金镀层在服役过程中,分层形成具有保护金属铜的被腐蚀、迁移损伤等缺陷,提高线路可靠性,具体步骤包括:
36.1)制备电镀液:将87g/l柠檬酸(c6h8o7)、40g/l硫酸铜(cuso4)、160g/l钼酸钠(na2moo4·
h2o)以及0.2g/l十二烷基硫酸钠(c
12h25
so4na)加入到去离子水中搅拌均匀后制得所述电镀液;
37.2)电镀前处理:用1500、2000目的金相砂纸将铜板表面打磨平滑,并用去离子水和无水乙醇清洗,然后干燥得到待镀基体;
38.3)电沉积:将步骤2)中制得的待镀基体作为阴极,碳板为阳极,将阳极和阴极放入装有步骤1)中制备的电镀液的电镀槽中,电流密度为0.1a/cm2,镀液温度为室温,磁力搅拌速率小一些,电镀4h即可制得所述的铜钼合金镀层;
39.参见图3是铜钼合金镀层的表面形貌,由图可知表面具有等轴晶、柱状晶双层薄膜形貌,说明了薄膜沉积过程的两个阶段;参见图4的能谱测试,说明了铜钼合金镀层中仅存在cu和mo两种金属元素,同时进一步测得铜钼镀层的表面原子、质量百分比,具体结果参见表1。
40.表1铜钼镀层的表面原子、质量百分比
[0041][0042]
4)电压作用下镀层的有效保护:参见图2的过程制备成可以通电场的正负极基板,在温度60℃、湿度90%rh、电压9v条件下,通电压48h后,从而使钼元素析出并在铜膜表面形成保护层。
[0043]
参见图5和图6,在极板表面的铜元素中夹杂着钼元素,说明了这是电镀的铜钼合金而不是电化学迁移产生的铜;因此可以得出铜钼镀层样品几乎没有发生电化学迁移现象,铜钼镀层对印制电路板的电化学迁移行为能起到一定抑制作用。
[0044]
实施例2
[0045]
在线路板上通过磁控溅射的方法形成的铜铬合金,具体步骤包括:
[0046]
磁控溅射过程中,cu靶材的纯度为99.99%,cr靶材的纯度为99.9%;基础真空度为10-7
torr,溅射过程中保持氩气保护,保持氩气压强为10-3
torr;得到质量百分比含量为
4.2%的cu-4.2cr薄膜。
[0047]
参见图7的xrd结果显示基本为铜的峰,但峰的宽度增加,这应该是cr在溅射过程中在物理上和cu实现混合。
[0048]
由于该结构在热力学上不稳定,进一步给该薄膜施加温度场,即在60℃的温度下热时效处理12h后,此时cr就会在cu表面析出,形成一薄层连续的cr层,起到保护cu层的作用。
[0049]
实施例3
[0050]
由于冷快速凝固在很大程度上使co在cu相中的固溶度从平衡条件下的7.46%扩展到20%不同成分的cu-co都为正的混合焓,相图中存在亚稳定的溶解度间隙,这使得cu-co合金在过饱和条件下的固溶度有了极大的空间。
[0051]
在铜板上电沉积铜钴合金镀层,包括以下步骤:
[0052]
1)制备电镀液:取0.01mol的硫酸铜、0.7mol的硫酸钴和0.2mol的乙酸钠加入到去离子水中搅拌均匀后制得所述电镀液;
[0053]
2)电镀前处理:用1500、2000目的金相砂纸将铜板表面打磨平滑,并用去离子水和无水乙醇清洗,然后干燥得到待镀基体;
[0054]
3)电沉积:将步骤2)中制得的待镀基体作为阴极,碳板为阳极,将阳极和阴极放入装有步骤1)中制备的电镀液的电镀槽中,用双氧水调节ph值为4.8,温度为40℃,电流密度保持在0.05a/cm2条件下,进行沉积4h;得到铜铬合金镀层。
[0055]
对制备好的铜铬合金镀层施加9v偏压后,发现镀层出现分离,实现了co与cu之间的分层。
[0056]
实施例4
[0057]
通过磁控溅射的方法形成的铜镍合金镀层薄膜,具体步骤包括:
[0058]
磁控溅射过程中cu-ni薄膜溅射参数为:cu靶材的纯度为99.99%,ni靶材的纯度为99.9%;基底温度100℃,靶基距50mm,溅射功率90w,工作气压0.5pa,得到ni含量质量百分比为0.1wt%的cu-ni薄膜。
[0059]
参见图8的cu-ni二元固溶体相图,由图可知cu、ni会在液态完全互溶,而在固态由于正的混合焓,会在外加能量场下,促进分离。
[0060]
将cu-ni薄膜外部施加能量场,具体为室温25℃、湿度45%rh、3v偏压作用,在上述的能量场下可以驱动元素ni至薄膜表面,形成防护层。
[0061]
实施例5
[0062]
通过电沉积的方式制备铜镍合金镀层,并观察铜镍合金镀层在电压场、一定湿度条件下铜在阴阳极之间的物质迁移、迁移损伤等缺陷,具体步骤包括:
[0063]
1)镀液配制:电镀溶液由10g/l的硫酸铜(cuso4·
5h2o)、280g/l的硫酸镍(niso4·
6h2o)、55g/l的柠檬酸钠(c6h5na3o7·
2h2o)、40g/l额氯化镍(nicl2·
6h2o)、0.3g十二烷基硫酸钠(sds)、60g/l的糖精钠(c7h4no3sna
·
2h2o)、0.5g的edta组成;
[0064]
2)用1500、2000目的金相砂纸将铜板表面打磨平滑,并用去离子水和无水乙醇清洗,然后干燥得到待镀基体;
[0065]
3)电沉积:将步骤2)中制得的待镀基体作为阴极,碳板为阳极,将阳极和阴极放入装有步骤1)中制备的电镀液的电镀槽中,电流密度为0.02a/cm2,镀液温度为40℃室温,磁
力搅拌速率小一些,电镀2h即可制得所述的铜镍合金镀层。
[0066]
对制备好的铜镍合金镀层施加9v偏压后,参见图9和表2,发现镀层出现分离,ni与cu之间实现了分层。
[0067]
表2铜镍镀层的截面不同位置元素分布质量百分比(通电后)
[0068][0069]
对比例1
[0070]
在印制电路板上采用电镀的方式镀出铜镀层,观察在电压场、一定湿度条件下铜在阴阳极之间的物质迁移、迁移损伤等缺陷,具体步骤包括:
[0071]
1)制备电镀液:将80g/l无水硫酸铜,200g/l硫酸,60mg/l的cl
-
离子加入到去离子水中,搅拌均匀后制得所述电镀液;
[0072]
2)电镀前处理:用1500、2000目的金相砂纸将铜板表面打磨平滑,并用去离子水和无水乙醇清洗,然后干燥得到待镀基体;
[0073]
3)电沉积:将步骤2)中制得的待镀基体作为阴极,铜板为阳极,将阳极和阴极放入装有步骤1)中制备的电镀液的电镀槽中,电流密度为0.1a/cm2,镀液温度为室温20℃,电流密度0.04a/cm2,转速600rpm条件下电镀1h即可制得所述的铜镀层。
[0074]
参见图10,可以看到电镀铜薄膜的微观组织由两个区域组成,底部的细晶区与上部的柱状晶区。薄膜总体厚度平均值为32.6μm,其中,柱状晶区厚度约为28.6μm、细晶区约为4.0μm,薄膜厚度的88%为柱状晶。在柱状晶区,柱状晶直径范围为0.4-1.5μm;参见图11,其表面表现为等轴晶形貌。
[0075]
将该铜薄膜做成如图2的样品,并在9v偏压条件下、60℃、湿度90%rh,通电24h观察其阴极,如图12所示,发现纯铜镀层会产生阴极与阳极之间的物质传输;在阴极板表面覆盖的厚厚一层电化学迁移产物中含有铜元素,且从图13中可以估算出电化学迁移产物的厚度约为30μm,这会使得线路之间在电压作用下,发生短路、失效的可能性增大。因此采用纯铜镀层是不能防止电化学迁移现象。
[0076]
对比例2
[0077]
具体制备过程同实施例1,不同之处在于电镀液中钼酸钠的含量由4.08变为8.4,得到的镀层成分见表3。
[0078]
表3铜钼镀层的表面原子、质量百分比
[0079][0080]
[0081]
将该铜钼镀层在电压9v、温度60℃、湿度90%rh条件下通电48h,参见图14,虽然未发现了铜元素的电化学迁移现象,但由于mo元素含量增大,电阻率较高,热效应增大,会增大迁移效应,对整个薄膜电路电路来说,电阻率过高,达到32.45-6
ω
·
cm,为纯铜同类薄膜的10倍;因此,mo含量不适过高,需要控制铜合金薄膜中添加元素的质量百分含量不高于5wt%。
再多了解一些
本文用于企业家、创业者技术爱好者查询,结果仅供参考。