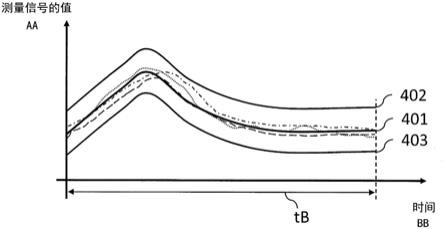
1.本发明涉及一种用于监控用于加工工件的激光加工过程的方法。本发明尤其能够包括一种用于自动调设监控参数和/或用于自动识别过程变化的方法。
背景技术:
2.在用于借助于激光束加工工件的激光加工系统中,从激光源或者激光引导光纤的一端出射的激光束借助射束引导光学器件或者聚焦光学器件聚焦或者集束到待加工的工件上。例如,所述加工能够包括激光切割、激光钎焊或者激光熔焊(schweiβen)。激光加工系统也能够被称为“激光加工设施”或者能够简称为“设施”。激光加工系统能够包括激光加工设备,例如激光加工头,例如激光切割头或者激光熔焊头。尤其是在对工件进行激光熔焊或者激光钎焊时,重要的是,持续地监控熔焊过程或钎焊过程,以便保证加工的质量。这涵盖对加工错误的识别。
3.通常在执行激光加工过程期间实时地进行对激光加工过程的持续监控,因此也被称为在线过程监控(online
‑
prozess
ü
berwachung)或者线上过程监控(in
‑
line
‑
prozess
ü
berwachung)。在监控时,检测并且评判激光加工过程的不同测量参量的测量信号,例如工艺辐射(prozessstrahlung)的或者说工艺放射(prozessemission)的强度。
4.随后进行评判,在所述评判时对测量信号进行如下检查:是否满足一定的错误条件或者错误标准。如果一个或者多个测量信号在能够包括对工件的加工或者对工件的一部分或者一区域的加工的一个加工步骤期间满足事先确定(festgelegt)的错误条件,则输出错误。根据是否出现加工错误,能够将对应的已加工的工件标注为“好”或者“合格件”(即适用于再加工或者出售)或者标注为“差”或者“劣质件”(即废品)。
5.对测量信号的评判通常是复杂的,因为测量参量的变化过程在很大程度上与所使用的材料、调设的激光功率、加工速度、工件的污染程度等等有关。对错误条件的调设和匹配是非常高开销的,并且在激光加工过程发生变化时必须重新进行。此外,通常手工进行对错误条件的调设和匹配。
技术实现要素:
6.因此,本发明的任务在于,说明一种用于监控用于加工工件的激光加工过程的方法,在所述方法中,自动调设监控参数。因此,本发明的任务在于,给出一种用于监控用于加工工件的激光加工过程的方法,在所述方法中,自动识别过程变化,以便重新调设监控参数。因此,本发明的任务在于,给出一种用于监控用于加工工件的激光加工过程的方法,在所述方法中,避免操作人员进行干预。
7.所述任务通过独立权利要求的主题来解决。有利的构型方案和扩展方案是从属权利要求的主题。
8.根据本公开内容的一方面,给出一种用于监控用于加工工件、尤其是金属工件的激光加工过程的方法。该方法包括下述步骤:对于多个加工步骤,在一个加工步骤期间针对
至少一个测量参量检测测量信号。在调设阶段中,基于在调设阶段期间检测的测量信号确定用于至少一个监控参数的极限值。在监控阶段中,基于每个加工步骤的测量信号求取用于该加工步骤的监控参数值,将监控参数的所求取的值与极限值进行比较,用以识别错误(fehlerhaft)的加工步骤,并且基于至少一个加工步骤的测量信号求取是否满足过程变化条件。在此,在预给定的(第一)调设间隔之后或者在预给定的(第一)数量的在调设阶段期间实施的加工步骤之后,从调设阶段更换至监控阶段,并且其中,当满足过程变化条件时,从监控阶段更换回调设阶段。
9.换言之,在调设阶段中,对过程的评估(“好”或者“差”)优选不是主动的(aktiv)。在监控阶段中,求取是否满足过程变化条件。如果满足,则再次更换回到调设阶段中。优选地,系统保持在监控阶段中,直到满足过程变化条件。换言之,在稳定的过程的情况下(不满足过程变化条件),系统优选保持在监控阶段(所谓的“周期性阶段”)中。替代地,在稳定的过程的情况下,在所述过程中不满足过程变化条件,在预给定的(第二)调设间隔之后或者在预给定的(第二)数量的在监控阶段期间实施的加工步骤之后,系统能够更换回到调设阶段中。
10.根据本公开内容的方法,具有多个同类型的或者重复的加工步骤的激光加工过程被划分为两个阶段,即调设阶段和监控阶段,在所述调设阶段中,确定用于监控参数的至少一个极限值,在所述监控阶段中,至少一个加工步骤基于针对该加工步骤求取的监控参数的值来监控。仅在监控阶段期间进行激光加工过程的监控。按照确定的标准,能够往复地在两个阶段之间进行更换。通过所说明的方法,能够自动识别激光加工过程的过程变化,并且能够自动更换回到调设阶段中,以便基于已改变的激光加工过程自动匹配用于监控参数的极限值。
11.激光加工过程能够包括多个重复的和/或同类型的和/或可比较的加工步骤。对工件的加工能够包括一个或者多个加工步骤。换言之,加工步骤能够包括对工件的加工或者对工件的一部分或者一区域的加工。尤其是,加工步骤能够对应于熔焊点或者焊缝。每个测量信号又对应于一个加工步骤。测量信号能够包括测量值,所述测量值是实数。
12.不仅在调设阶段期间、而且在监控阶段期间,都能够在各个加工步骤期间分别检测至少一个测量参量。对测量参量的检测能够包括在一个加工步骤期间,即优选在每个加工步骤期间,或者在每第n个加工步骤期间(例如在每第二个加工步骤或者每第三个加工步骤期间等等),对至少一个测量参量的测量信号或者测量信号变化过程的检测。每个测量信号都能够包括多个测量值,所述测量值分别配属于相应的加工步骤的时刻。
13.至少一个测量参量能够是温度、由工件反射的激光的强度、产生的等离子体辐射的强度、通过激光加工过程产生的在可见光谱范围中的光的强度和/或通过激光加工过程产生的在红外光谱范围中的光的强度。
14.在调设阶段中,确定用于至少一个监控参数的至少一个极限值。所述监控参数能够基于仅一个测量参量或者能够基于多个测量参量。基于在调设阶段中实施的加工步骤期间针对测量参量检测的测量信号,来确定(festlegung或bestimmung)至少一个极限值,所述监控参数基于所述测量参量。例如,基于经检测的测量信号的变化过程并且根据适合的统计学方法、例如箱形图分析来进行确定。所述极限值能够定义值范围。优选地,用于至少一个监控参数的极限值包括上限值和/或下限值和/或具有下限值和上限值的极限值范围。
该极限值能够是正实数。所述确定也能够被称为“学习(einlernen)”或者“教学(teaching)”。
15.例如,在调设阶段中,能够基于在调设阶段期间针对测量参量检测的测量信号确定针对该测量参量的平均值曲线。此外,能够基于该平均值曲线确定针对测量参量的包络曲线(所谓的“参考曲线”或者简称为“参考物”)。包络曲线能够包括上包络曲线和下包络曲线,其中,平均值曲线位于上包络曲线与下包络曲线之间。能够借助统计学方法、例如箱形图分析来确定平均值曲线和/或包络曲线。平均值曲线能够包括在调设阶段期间针对测量参量检测的测量信号的平均值和/或中值。例如,能够将在调设阶段期间针对测量参量检测的测量信号叠置,使得能够将在相同的加工时刻的加工步骤的测量信号相互抵消(verrechnen)。
16.在调设阶段中,能够基于针对测量参量确定的平均值曲线和/或基于针对测量参量确定的包络曲线确定用于至少一个监控参数的相应的极限值。
17.能够尤其如此确定上包络曲线,使得该上包络曲线与平均值曲线具有预给定的第一间距,并且能够如此确定下包络曲线,使得该下包络曲线与平均值曲线具有预给定的第二间距。第一间距和第二间距能够在量值方面相同或者不同。
18.能够如此确定平均值曲线和包络曲线,使得所述平均值曲线和所述包络曲线位于用于相应的测量参量的预给定的可靠性范围内。能够例如由激光加工方法的或者激光加工系统的使用者来预给定测量参量的可靠性范围。测量参量的可靠性范围能够确定用于相应的测量参量的如下范围:测量参量的测量信号在通过激光加工过程加工工件期间不得离开该范围。如果测量信号还是离开该可靠性范围,则可以中断或者结束激光加工过程。
19.在预给定的调设间隔之后或者在预给定数量的经加工的工件之后或者在预给定数量的加工步骤、尤其是同类型的加工步骤之后,能够从调设阶段更换到监控阶段中。
20.在监控阶段中监控加工步骤,以便识别错误的加工步骤。所述监控能够通过以下方式进行:基于每个所实施的加工步骤的测量信号求取用于该加工步骤的监控参数值。优选地,将所求取的监控参数值与对应的确定的极限值进行比较,以便识别所实施的加工步骤是否是错误的。例如,当所求取的监控参数值高于对应的极限值时,加工步骤能够被识别为错误。此外,当加工步骤被识别为错误时,所述方法能够包括将错误输出。
21.至少一个监控参数能够是异常值间距(ausreiβerabstand)、积分、位于包络曲线之外的测量信号与最接近的包络曲线之间的面积、测量信号在时间上的积分、测量信号与平均值曲线的均方差或者异常值频率。可以将所述异常值间距定义为在一个加工步骤期间所检测的测量信号的位于包络曲线之外的测量值与最接近的包络曲线之间(最大)间距。所述积分可以是时间积分或者关于测量信号的测量值的数量的积分。至少一个监控参数还可以是测量信号和参考值所包围的面积。即,至少一个监控参数能够指的是平均值曲线和/或包络曲线。参考值可以是预给定的恒定值,例如零,或者可以对应于平均值曲线。能够分别针对加工步骤求取监控参数的值。
22.此外,在监控阶段中,基于至少一个所实施的加工步骤的测量信号求取是否满足过程变化条件。能够在每个所实施的加工步骤之后或者有规律地在确定数量的所实施的加工步骤之后求取是否满足过程变化条件。如果求取到满足过程变化条件,则从监控阶段更换回到调设阶段中,以便重新确定用于至少一个监控参数的极限值和/或平均值曲线和/或
包络曲线。
23.求取是否满足过程变化条件能够基于在单个所实施的加工步骤期间单个测量参量的测量信号、或者基于在多个所实施的加工步骤期间单个测量参量的经检测的测量信号、或者基于在多个所实施的加工步骤期间多个测量参量的经检测的测量信号来进行。
24.尤其当高于对于异常值频率的预给定的最大值时,能够满足过程变化条件。可以将异常值频率定义为:相对于在一个加工步骤期间检测的测量信号的测量值的总数,在所述加工步骤期间检测的测量信号的位于针对测量信号的包络曲线之外的测量值的数量。例如,当经检测的测量信号的信噪比发生变化时,当待加工的工件不干净时,或者当进行待加工的工件的批次更换(chargenwechsel)时,是这种情况。这些情形能够被称为“过程变化”,并且能够导致一个或者多个测量参量的测量信号或者测量信号变化过程发生变化。例如,测量值的平均值和/或中位数能够发生变化,或者测量值的易变性、即统计离散参数能够发生变化。例如,用于异常值频率的预给定的最大值能够处在10
‑
100%的范围中、优选在50
‑
90%的范围中。
25.在监控阶段中,此外还能够匹配至少一个监控参数的极限值。能够基于针对在前发生的加工步骤检测的测量信号对极限值进行匹配。换言之,根据监控参数的针对在前发生的加工步骤确定的值,能够将极限值选择得更小或者更大,或能够将极限值范围选择得更狭窄或者更宽。通过所述匹配能够对所监控的激光加工过程是稳定地还是不稳定地运行做出反应。
26.例如在预给定数量的加工步骤或者预给定的时间间隔之后,能够周期性地匹配用于至少一个监控参数的极限值。
27.当预给定数量的彼此相继的加工步骤被识别为错误时,或者当高于预给定的错误率时,能够对用于至少一个监控参数的极限值进行匹配。错误率能够被定义为:相对于加工步骤的预给定的总数,如下加工步骤的数量:在所述加工步骤中,超过了至少一个监控参数的极限值。例如,错误率能够以百分比(即相对于100个加工步骤)或者以千分比(即相对于1000个加工步骤)给出。最大错误率能够在0.1%与100%之间。彼此相继的错误的加工步骤的预给定数量可以在3与1000之间、优选在5与10之间。
28.对用于至少一个监控参数的极限值的匹配能够包括缩小极限值或者增大极限值。缩小极限值能够包括减小极限值的量值,并且增大极限值能够包括提高极限值的量值。基于预给定数量的先前的加工步骤的测量信号,能够对用于至少一个监控参数的极限值进行匹配。例如,能够基于测量参量的在最后n个实施的加工步骤期间检测的测量信号来匹配用于至少一个监控参数的极限值,其中,n是自然数。例如,能够基于在最后n个实施的加工步骤期间检测的测量信号计算测量参量的趋势、斜率或者平均值或者中位数。例如,对极限值的匹配能够是对极限值的相对或者绝对匹配。
29.所述匹配能够包括判断该激光加工过程是稳定地运行还是不稳定地运行。此外,所述匹配能够包括基于所述判断对极限值进行匹配。即,在匹配监控参数的极限值时,能够考虑所述激光加工过程是稳定的还是不稳定的。
30.根据本公开内容的另一方面,给出一种用于借助于激光束加工工件的激光加工系统,所述激光加工系统设置用于实施上述方法。
附图说明
31.下面根据附图详细描述本发明。在附图中示出:
32.图1示出根据本公开内容的一种实施方式的用于监控用于加工工件的激光加工过程的方法的流程图;
33.图2示出根据本公开内容的一种实施方式的一种方法的调设阶段的流程图;
34.图3示出根据本公开内容的一种实施方式的一种方法的监控阶段的流程图;
35.图4a示出通过根据本发明的公开内容的一种实施方式的一种方法确定的平均值曲线和包络曲线的示意图;以及
36.图4b示出在一个加工步骤期间针对一个测量参量检测的测量信号和根据本发明的公开内容的一种实施方式的监控参数的示意图。
具体实施方式
37.下面,除非另有说明,相同的附图标记用于相同的和起相同作用的元件。
38.图1示出根据本公开内容的一种实施方式的用于监控激光加工过程的方法的流程图。
39.例如,激光加工过程能够包括激光切割过程和/或激光熔焊过程。在激光加工过程期间实施用于监控的方法。在激光加工过程中,依次实施多个重复的加工步骤。在此,对于每个工件能够实施一个加工步骤,或者对于每个工件能够实施多个加工步骤。
40.如图1所示,所述方法包括调设阶段101和监控阶段102,其中,不仅在调设阶段中、而且在监控阶段中,都连续地执行重复的加工步骤。在预给定的调设间隔之后或者在预给定数量的在调设阶段101期间实施的加工步骤之后,能够从调设阶段101更换到监控阶段102中(箭头103)。如下所述,当满足过程变化条件时(箭头104),能够从监控阶段102更换到调设阶段101中。
41.不仅在调设阶段101中、而且在监控阶段102中,在每个加工步骤期间都检测或者接收至少一个测量参量的信号变化过程或测量信号。在此,在加工工件期间,对测量参量进行持续地检测或测量,以便获得对应的测量信号。随后,对于每个加工步骤,都对测量参量的测量信号进行评判。
42.测量参量可以涉及温度、工艺放射的波长范围、通过加工产生的等离子体辐射的强度、在光的红外光谱范围中的工艺放射(例如热辐射)的强度、在光的可见光谱范围中的工艺放射的强度、或者激光加工射束的经散射回的或者经反射回的部分的强度。测量信号能够包括多个测量点或者测量值,所述测量点或者测量值配属于加工步骤的不同的时刻。换言之,测量信号是在一个加工步骤的持续时间内接收的测量值的集合。一般来说,在每个接收步骤中,针对每个测量参量接收一个测量信号。
43.图2示出根据本公开内容的一种实施方式的一种方法的调设阶段的流程图。
44.在图2中,根据实施方式,调设阶段101包括确定平均值曲线(步骤201)和针对每个测量参量确定包络曲线(步骤202)。平均值曲线的确定基于针对相应的测量参量在调设阶段101期间在多个加工步骤中检测的测量信号,这在下文参考图4a和图4b进行描述。随后,根据平均值曲线确定包络曲线。
45.此外,所述方法在调设阶段101中包括针对每个监控参数确定极限值(步骤203)。
在一个示例中,对于每个实施的加工步骤,能够分别针对一个或者多个测量参量检测一个测量信号。针对这些测量参量中的每个测量参量定义一个或者多个监控参数。基于在调设阶段101期间针对多个加工步骤检测的测量信号,在调设阶段101中针对每个监控参数确定极限值。根据一种实施方式,能够基于平均值曲线和/或基于包络曲线确定相应的极限值。当在监控阶段中高于预给定的监控参数的事先确定的极限值时,对应的加工步骤被评价为错误。在调设阶段中,至少不对极限值进行监控或者甚至不进行过程监控。
46.图3示出根据本公开内容的一种实施方式的一种方法的监控阶段102的流程图。监控阶段的目标是,自动识别熔焊过程的变化(过程变化)并且匹配所述监控。监控阶段中的监控以参数化的方式根据预给定的监控参数进行,所述监控参数分别根据一个或者多个测量参量来定义。
47.监控阶段102包括对于用于在监控阶段102期间实施的加工步骤的每个监控参数求取值(步骤301)。基于至少一个测量参量(该监控参数与所述至少一个测量参量有关)的在该加工步骤期间检测的测量信号,求取监控参数值。随后,将用于该加工步骤的所求取的监控参数值与用于这个监控参数的、在调设阶段101或者监控阶段102中确定的极限值进行比较(步骤302)。所述比较用于识别错误的加工步骤。根据一种实施方式,当所求取的监控参数值高于对应的极限值时,该加工步骤被识别为或者被标注为错误。然后,优选将错误输出。例如,能够向激光加工过程的使用者输出或者显示该错误,或者能够将该错误保存在错误存储器中。此外,在加工步骤中已加工的工件能够被标记为“差”或者“错误”。
48.与步骤301和302并行地,在监控阶段102中,基于在监控阶段期间所实施的至少一个加工步骤的至少一个测量信号来求取是否满足过程变化条件。求取是否满足过程变化条件例如能够基于在多个所实施的加工步骤期间单个测量参量的经检测的测量信号、或基于在单个加工步骤期间多个测量参量的经检测的测量信号、或基于在多个所实施的加工步骤期间多个测量参量的经检测的测量信号来进行。
49.例如,激光加工过程的变化(或者简称为“过程变化”)包括待加工的工件的材料的变化、待加工的工件的污染程度的变化、激光功率的匹配、待加工的工件的批次更换等等。这导致各个测量参量的测量信号的变化。因此,根据本发明,过程变化的识别导致重新执行调设阶段,以便重新求取用于监控参数的包络曲线、平均值曲线和极限值中的至少一个。例如,当异常值频率高于预给定值时,能够满足过程变化条件。在此,异常值被定义为测量信号的位于包络曲线之外的测量值。例如,如果测量信号的超过80%位于包络曲线之外,则从监控阶段更换回到调设阶段中。
50.即使不存在过程变化,激光加工过程也能够不同稳定地运行。优选地,通常能够根据下述内容来调设或者匹配极限值:激光加工过程是遍历稳定的阶段还是遍历不稳定的阶段。在稳定运行的激光加工过程的情况下,错误条件、尤其是用于监控参数的极限值能够调设得更狭窄或者更严格,相反,在不稳定运行的激光加工过程的情况下,错误条件能够调设得更宽或者更宽敞(groβz
ü
gig)或更容忍。用于监控参数的极限值的自动匹配能够基于监控参数的为多个在前发生的加工步骤求取的值来进行。例如,如果最后例如十个加工步骤的监控参数值小于例如极限值的80%,则能够缩小该极限值。在预定给数量的加工步骤的情况下,例如在10个加工步骤之后,能够触发对监控阶段中的极限值的匹配(即在不匹配平均值曲线或者包络曲线的情况下)。这也能够被称为周期性的匹配。除此之外,当高于预给
定数量的连续错误时,即当高于预给定数量的彼此相继的且被评估为错误的加工步骤,或者当高于预给定错误率时,例如当所执行的加工步骤中的超过1%被评估为错误时,能够触发对监控阶段中的极限值的匹配。
51.图4a示出通过根据本发明的公开内容的一种实施方式的一种方法确定的平均值曲线和包络曲线的示意图。
52.如图4a所示,该曲线图包括一个测量参量的多个测量信号(虚线),所述测量信号分别在调设阶段101期间在一个加工步骤中已被检测到。即,针对同类型的、依次在调设阶段中实施的加工步骤检测所述测量信号,并且将所述测量信号叠置在曲线图中。用tb来标注加工步骤的持续时间。根据一种实施方式,基于这些测量信号确定针对所述测量参量的平均值曲线401、上包络曲线402和下包络曲线403。根据一种实施方式,基于平均值计算的统计学方法(例如箱形图分析等等)来进行所述确定。
53.如图4a所示,包络曲线402和403能够具有相同的与平均值曲线401的间距,然而也不限于此。如图4a所示,如此确定包络曲线402的间距,使得所有测量信号都位于通过上包络曲线402和下包络曲线403形成的通道或者窗口内。能够直接基于用于相应的测量参量的测量信号确定包络曲线402和403。替代地,基于平均值曲线401确定包络曲线402和403,例如,能够通过与平均值曲线401的、 20%或
‑
20%的偏差来确定上包络曲线或下包络曲线。
54.图4b示出在监控阶段中在一个加工步骤期间针对一个测量参量已检测的测量信号501,并且示出根据本公开内容的一种实施方式的多个监控参数。此外,图4b示出在调设阶段期间确定的平均值曲线401和包络曲线402和403。
55.例如,监控参数包括异常值间距。在此,根据实施方式,异常值表示位于包络曲线402、403之外的测量值。对应地,异常值间距被定义为测量信号501的位于包络曲线402、403之外的至少一个测量值与最接近的包络曲线402、403之间的间距。如图4b所示,测量信号501具有两个区域502a、502b,在所述两个区域中,测量信号501位于包络曲线402、403之外、即位于通过包络曲线402、403定义的窗口或者走廊之外。根据实施方式,异常值间距能够被定义为测量信号501的位于包络曲线402、403之外的测量值与最接近的包络曲线402、403的最大间距503。
56.此外,监控参数能够包括在包络曲线402、403之外的测量信号501的属于异常值间距的区域502b的面积或者积分。所述积分能够涉及关于测量信号501的位于包络曲线402、403之外且包括异常测量值的区域的积分。所述面积或者所述积分能够涉及多个面积的量值的和或者在测量信号501的位于包络曲线402、403之外的区域502a、502b上的积分。在图4b所示的测量信号501的情况下,测量值位于包络曲线402、403之外的区域502a、502b中。所述区域502a、502b分别配属有根据上述定义的面积或者积分(阴影区域)。所述面积或者所述积分也能够是对应于具有最大异常值间距503的区域502b的面积或者积分。在图4b所示的测量信号501的情况下,这对应于配属于区域502b的面积,因为这个区域包含具有最大异常值间距503的测量值。
57.此外,监控参数能够包括测量信号501在加工步骤的持续时间tb上的积分。例如,测量信号501的积分能够是测量信号501与参考值504的间距505在时间上的积分。如图4a所示,参考值504能够是恒定值,该恒定值也能够等于零,然而不限于此。
58.通过所公开的用于监控用于加工工件的激光加工过程的方法,能够自动重新调设
监控参数或者根据过程稳定性匹配监控参数。尤其是,能够在识别到较大的过程变化之后通过从监控阶段更换回到调设阶段中来自动重新调设监控参数。此外,能够使监控阶段中的监控参数的极限值匹配于较小的过程变化或适配于过程稳定性的变化,即基于激光加工过程的加工步骤是否比在前发生的加工步骤更稳定地或者更不稳定地运行。由此,对监控参数的手动干预和匹配变得多余,并且该激光加工过程能够以多个调设阶段和监控阶段的次序连续进行。
再多了解一些
本文用于企业家、创业者技术爱好者查询,结果仅供参考。