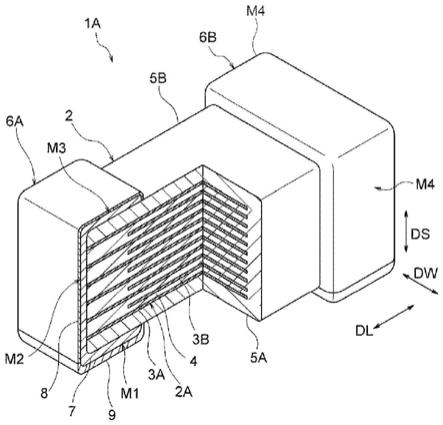
1.本发明涉及一种电子部件、电路板装置以及制造该电子部件的方 法。
背景技术:
2.在存在缩小电子设备尺寸的需求的情况下,为了减小电子部件的 安装面积,通常在其内设置内部电极的元件本体上形成外部电极。外 部电极通过焊接连接到电路板,使得电子部件安装到电路板上。
3.外部电极不仅可以形成在元件本体的安装面上,还可以形成在元 件本体的侧面和上表面上。在这种构造中,湿焊料可能会沿外部电极 的侧面向上移动并导致安装面积增大。
4.为了防止湿焊料沿着端子电极的侧面向上移动,jp
‑
2014
‑
53599a 公开了一种构造,其中,形成在电子部件的侧面上的第一和第二端子 电极的侧面部分被氧化膜覆盖。
技术实现要素:
5.然而,如果端子电极的侧面部分被氧化膜覆盖,并且向氧化膜施 加机械应力,那么氧化膜可能沿端子电极和氧化膜之间的界面剥离。 氧化膜可能突然从端子电极的大面积剥离。
6.本发明的一个目的是提供一种电子部件,其中形成在外部电极上 的氧化层难以从外部电极剥离。本发明的另一目的是提供一种制造这 种电子部件的方法。本发明的另一目的是提供一种电路板装置,其中 在安装在电路板上的电子部件的外部电极上形成的氧化层难以从外部 电极剥离。
7.根据本发明的第一方面,提供一种电子部件,其包括元件本体和 至少一个外部电极。元件本体具有电介质和内部电极。每一个外部电 极包括连接到内部电极的基底层。基底层形成在元件本体的多个面上, 并包含金属和与金属混合的第一共材。每一个外部电极还包括形成在 基底层的至少一个面上的镀层。每一个外部电极还包括氧化层,氧化 层形成在基底层的除形成有镀层的面之外的一个或多个面上。氧化层 具有由基底层的金属的氧化膜和第二共材形成的表面层。
8.在基底层中所包含的第一共材和在氧化层中所包含的第二共材可 以具有相同的组成。
9.电介质的主要成分可以是氧化物陶瓷。
10.在基底层中所包含的第一共材和在氧化层中所包含的第二共材可 以具有与电介质的主要成分相同的组成。
11.从基底层到氧化层,第一共材可以延续到第二共材,并且,第一 共材和第二共材可以具有连续的晶体结构或非晶结构。
12.基底层的金属可以以晶体或非晶颗粒的形式存在,并且,第一共 材也可以以晶体或非晶颗粒的形式存在,使得基底层的金属的颗粒与 第一共材的颗粒混合存在。
13.电介质的主要成分可以是钛酸钡。
14.氧化层可以形成在基底层的侧面的至少一部分上以及与其上形成 有镀层的面相对的面上。
15.第二共材在氧化层的表面的比率可以在20at%至75at%的范围内。
16.基底层的金属可以是包含选自cu、fe、zn、al、ni、pt、pd、ag、 au及sn中的至少一种的金属或合金。
17.第一共材可以选自钛酸钡、钛酸锶、钛酸钙、钛酸镁、钛酸锶钡、 钛酸钙钡、锆酸钙、锆酸钡、锆酸钛酸钙和钛氧化物中的至少一种。
18.从氧化层的表面看,氧化层可以包括氧化镍和钛酸钡。
19.从氧化层的表面看,氧化层还可以包含含有镍、镁和氧的化合物。
20.元件本体可以具有层叠体,其中至少一个第一内部电极层和至少 一个第二内部电极层隔着电介质而交替层叠。上述的至少一个外部电 极可以包括第一外部电极和第二外部电极,第一外部电极和第二外部 电极设置在层叠体的相对的侧面上,使得第一外部电极与第二外部电 极隔开。第一内部电极层可以连接到第一外部电极,并且,第二内部 电极层可以连接到第二外部电极。
21.镀层可以形成在基底层的面的其中之一上,所述面垂直于第一内 部电极层、第二内部电极层和电介质的层叠方向延伸。
22.根据本发明的第二方面,提供一种电路板装置,其中,上述的电 子部件安装在电路板上,并且电子部件经由附着在电子部件的镀层上 的焊料层连接到电路板。
23.根据本发明的第三方面,提供一种制造电子部件的方法。该方法 包括形成包括电介质和内部电极的元件本体。该方法还包括将通过将 共材与含有金属的电极材料混合而获得的混合材料施加到元件本体的 两个相对的侧面和元件本体的邻近侧面的边缘表面。该方法还包括烧 结混合材料,并在元件本体的相对的侧面和元件本体的所述边缘表面 上形成金属和共材混合存在的基底层。该方法还包括氧化基底层的金 属,并在基底层的多个面上形成金属的氧化膜。该方法还包括从基底 层的多个面中的至少一个面去除氧化膜,同时将氧化膜留在元件本体 的所述边缘表面的至少一部分上。该方法还包括在基底层的多个面中 已去除了氧化膜的至少一个面上形成镀层。
24.从基底层的多个面中的至少一个面去除氧化膜的步骤可以包括: 从基底层的多个面中的至少一个面对氧化膜进行喷砂,以抛光基底层 的面。
25.形成元件本体的步骤可以包括:形成包含电介质陶瓷作为主要成 分的片材;和将含有基底层的金属的导电膏施加在片材上。元件本体 可以在烧结混合材料的步骤中进行烧结。
26.根据本发明的一个方面,在每个外部电极上形成的氧化层很难从 外部电极剥离。
附图说明
27.图1是示出根据本发明第一实施例的多层陶瓷电容器的构造的立 体图。
28.图2是通过纵向切割图1的多层陶瓷电容器而获得的横截面图。
29.图3a是图2中外部电极的ea部分的放大横截面图。
30.图3b是图2中外部电极的eb部分的放大横截面图。
31.图4是示出图2所示的外部电极的氧化层的表面的示例性组成的 示意图。
32.图5是示出根据本发明第二实施例的制造多层陶瓷电容器的方法 的流程图。
33.图6a是用于描述根据第二实施例的制造多层陶瓷电容器的方法 的横截面图。
34.图6b是用于描述根据第二实施例的制造多层陶瓷电容器的方法 的另一横截面图。
35.图6c是用于描述根据第二实施例的制造多层陶瓷电容器的方法 的另一横截面图。
36.图6d是用于描述根据第二实施例的制造多层陶瓷电容器的方法 的又一横截面图。
37.图6e是用于描述根据第二实施例的制造多层陶瓷电容器的方法的 另一横截面图。
38.图6f是用于描述根据第二实施例的制造多层陶瓷电容器的方法的 另一横截面图。
39.图6g是用于描述根据第二实施例的制造多层陶瓷电容器的方法 的另一横截面图。
40.图6h是用于描述根据第二实施例的制造多层陶瓷电容器的方法 的另一横截面图。
41.图6i是用于描述根据第二实施例的制造多层陶瓷电容器的方法的 另一横截面图。
42.图6j是用于描述根据第二实施例的制造多层陶瓷电容器的方法的 另一横截面图。
43.图7a是示出图6i的示例性过程的平面图。
44.图7b是通过纵向切割图7a的结构而获得的横截面图。
45.图8是示出根据第三实施例的在电路板上安装多层陶瓷电容器的 电路板装置的构造的横截面图。
46.图9是示出根据第四实施例的多层陶瓷电容器的构造的横截面图。
47.图10是示出根据第五实施例的电子部件的构造的立体图。
48.图11是示出根据第六实施例的电子部件的构造的立体图。
具体实施方式
49.下面将参考附图描述本发明的实施例。以下实施例并不旨在限制 本发明。在每个实施例中描述的所有特征的组合对于本发明并不总是 必需的。可以根据应用本发明的设备和装置的设计、规范和各种条件 (使用条件、使用环境等)来修改和/或改变每个实施例的构造。本发 明的技术范围由所附的权利要求限定,不受以下实施例的限制。此外, 出于更容易地理解零件、组件和元件的目的,在用于结合以下描述的 附图中所示的零件、组件和元件可以在结构、比例和形状上与实际的 零件、组件和元件不同。
50.第一实施例
51.图1是示出根据本发明第一实施例的多层陶瓷电容器1a的构造的 立体图。图2是在图1的多层陶瓷电容器1a的纵向取得的图1的多层 陶瓷电容器1a的横截面图。
52.在图1和图2中,多层陶瓷电容器1a包括元件本体(元件组件) 2、外部电极(外侧电极)6a和另一外部电极(外侧电极)6b。元件 本体2具有层叠体(或叠层)2a、下覆盖层5a和上覆盖层5b。层叠 体2a具有多个内部电极层3a、多个另一内部电极层3b和多个电介质 层4。
53.层叠体2a的最下层被下覆盖层5a覆盖,层叠体2a的最上层被 上覆盖层5b覆盖。多个内部电极层3a和3b隔着多个电介质层4交 替层叠。元件本体2的形状可以是基本上矩形的平行六面体形状,层 叠体2a的形状也可以是基本上矩形的平行六面体形状。元件本体2可 以沿着元件本体2的各个棱(边缘)形成倒角。在下面的描述中,元 件本体2的两个侧面彼此面对的方向可以被称为纵向dl,元件本体2 的前表面和后表面彼此面对的方向可以被称为宽度方向dw,元件本 体2的顶面和底面彼此面对的方向可以被称为堆叠方向ds。
54.外部电极6a和6b分别位于元件本体2的相对侧。外部电极6a 和6b彼此隔开间隔(分离)。外部电极6a和6b中的每个从元件本体 2的侧面连续地延伸到前表面和后表面以及顶面和底面。
55.在纵向dl上,内部电极层3a和3b交替地布置在层叠体2a中 的不同位置。内部电极层3a可以相对于内部电极层3b布置在元件本 体2的一个侧面的一侧,并且内部电极层3b可以相对于内部电极层 3a布置在元件本体2的相对的侧面。内部电极层3a的端部在元件本 体2的纵向dl上的一个侧面(右侧面)处被引出到相应电介质层4 的左端,并被连接到外部电极6a。内部电极层3b的端部在元件本体 2的纵向dl上的另一侧面处被引出到电介质层4的右端,并被连接到 外部电极6b。
56.另一方面,在与元件本体2的侧面彼此相对的方向(长度方向dl) 垂直的方向(宽度方向dw)上,内部电极层3a和3b的端部被电介 质层4覆盖。在宽度方向dw上,内部电极层3a的端部的位置可以 与内部电极层3b的端部的位置对齐。
57.多层陶瓷电容器1a的外部尺寸例如具有以下值。长度为1.0mm, 宽度为0.5mm,高度为0.5mm。内部电极层3a、内部电极层3b和电 介质层4中的每一个在堆叠方向ds上的厚度可以分别在0.05μm到 5μm的范围内,例如,0.3μm。
58.内部电极层3a、3b的材料可以选自例如cu(铜)、ni(镍)、ti (钛)、ag(银)、au(金)、pt(铂)、pd(钯)、ta(钽)和w(钨) 的金属,并且可以是包含这些金属的合金。
59.电介质层4的材料的主要成分例如是具有钙钛矿结构的陶瓷材料。 主要成分的含量可为50at%或更多。电介质层4的陶瓷材料可选自例如 钛酸钡、钛酸锶、钛酸钙、钛酸镁、钛酸锶钡、钛酸钙钡、锆酸钙、 锆酸钡、锆酸钛酸钙和钛氧化物。
60.下覆盖层5a和上覆盖层5b的材料的主要成分可以是例如陶瓷材 料。下覆盖层5a和上覆盖层5b的陶瓷材料的主要成分可以与电介质 层4的陶瓷材料的主要成分相同。
61.如图1和图2所示,外部电极6a和6b在长度方向dl上彼此间 隔,并且形成在元件本体2的多个面上。外部电极6a和6b中的每个 具有在堆叠方向ds上彼此面对的安装面m1和上表面m3、侧面m2、 在宽度方向dw上彼此面对的前表面m4和后表面m4。外部电极6a 和6b中的每个包括安装面m1上的基底层(底层)7和镀层9。外部 电极6a的侧面m2在长度方向dl上朝向外部电极6b的侧面m2。安 装面m1是面向其上安装有多层陶瓷电容器1a的电路板的面。安装面m1设置在元件本体2的下表面上。安装面m1上的外部电极6a和6b 中的每个的在堆叠方向ds上的厚度例如在10μm到40μm的范围内。
62.基底层7形成在每个外部电极6a和6b的除安装面m1之外的那 些面(即,侧面m2、上
表面m3、前表面m4和后表面m4)上,并且 氧化层8形成在基底层7的表面上。基底层7连续地形成在元件本体2 上,使得基底层7存在于侧面m2上并从侧面m2延伸到安装面m1上。 基底层7还从侧面m2延伸到上表面m3、前表面m4和后表面m4上。
63.基底层7包括作为导电材料的金属。例如,基底层7的金属包含 选自cu、fe(铁)、zn(锌)、al(铝)、ni、pt、pd、ag、au和sn (锡)组成的组中的至少一种金属或其合金作为其主要成分。基底层7 还包括共材(co
‑
material)的颗粒。共材减小了元件本体2和基底层7 之间的热膨胀系数差,并减轻了施加在基底层7上的应力。共材例如 是作为电介质层4的主要成分的陶瓷成分。基底层7可包含玻璃成分。 玻璃成分用于基底层7的致密化等。玻璃成分例如是ba(钡)、sr(锶)、 ca(钙)、zn、al、si(硅)或b(硼)的氧化物。基底层7电连接到 被引出到元件本体的侧面的多个内部电极层。
64.氧化层8的材料包括用作基底层7的导电材料的金属的氧化膜和 用于基底层7的共材的材料。基底层7的共材可具有与电介质层4相 同的组成,例如钛酸钡。用作基底层7的导电材料的金属例如为镍。 用作基底层7的导电材料的金属的氧化膜例如为氧化镍,并且其厚度 例如在0.05μm到3μm的范围内。
65.基底层7和氧化层8中的每一个可以具有包含在元件本体2中的 金属成分。包含在元件本体2中的金属成分可以包括mg、ni、cr、sr、 al、na和fe中的至少一种。例如,元件本体2中包含的金属成分是 mg。如果金属成分是mg,那么基底层7和氧化层8中的每一个可以 包括用作基底层7的导电材料的金属、包含在元件本体2中的金属和 氧的化合物。例如,包括在基底层7和氧化层8中的每一个中的化合 物包含ni、mg和o。
66.镀层9的材料的主要成分例如是金属,例如cu、ni、al、zn和 sn,或者是含有cu、ni、al、zn和sn中至少两种的合金。镀层9可 以是单个金属成分的镀层,或者可以包括不同金属成分的多个镀层。 例如,如图2所示,镀层9可以具有三层结构,即,镀层9可以包括 形成在基底层7上的cu镀层9a、形成在cu镀层9a上的ni镀层9b 和形成在ni镀层9b上的sn镀层9c。cu镀层9a可以提高镀层9与 基底层7的附着力。ni镀层9b可提高焊接时外部电极6a、6b的耐热 性。sn镀层9c可以改善镀层9的焊料的润湿性。镀层9形成在基底 层7的一部分上,使得镀层9导电连接到内部电极层。例如,镀层9 可以形成在基底层7的沿垂直于堆叠方向ds的方向延伸的一个面上。 此外,镀层9通过焊料导电连接到电路板的端子。顺便提一下,当基 底层7的金属成分是cu时,可以不形成cu镀层9a。如果没有形成 cu镀层9a,则镀层9可以具有两层结构,即镀层9可以包括ni镀层 9b和形成在ni镀层9b上的sn镀层9c。
67.图3a是示出图2所示的外部电极6b的ea部分的放大构造的横 截面图,图3b是示出图2所示的外部电极6b的eb部分的放大构造 的横截面图。外部电极6a与外部电极6b具有相同的构造。
68.如图3a和图3b所示,导体12和共材11以混合方式存在于基底 层7中。导体12的主要成分是包括cu、fe、zn、al、ni、pt、pd、 ag、au和sn中的至少一种的金属或其合金。共材11例如是作为电介 质层4的主要成分的氧化物陶瓷。
69.如图3a所示,在每一外部电极6a和6b的侧面m2、上表面m3、 前表面m4和后表面m4上的基底层7的导体12的表面上涂覆有氧化 膜8a。氧化膜8a是导体12中使用的金属或合金的氧化膜。氧化膜 8a由存在于直到基底层7表面处的共材颗粒11分割。氧化层8可以 构造为包括氧化膜8a以及由共材颗粒11限定的表面层。
70.另一方面,图3b示出了安装面m1上的基底层7,该基底层7由 下面将描述的制造方法制成。如图3b所示,在外部电极6a、6b的安 装面m1上,在从基底层7暴露的导体12的表面上并未形成氧化膜8a。 而是在基底层7上形成镀层9。由此,导体12和镀层9彼此连接,确 保了外部电极6a、6b的安装面m1的导电性。
71.在图3a中,氧化镍的氧化膜8a在导体12上形成。在基底层7 的深度方向上,共材颗粒11和导体12以镶嵌形状混合。共材颗粒11 以在导体12中的不规则岛的形式分布。共材11从氧化层8到基底层7 连续存在,并可以具有连续的晶体结构或非晶结构。类似地,导体12 从氧化层8到基底层7连续存在,并可以具有连续的晶体结构或非晶 结构。
72.图4示意性地示出图2的氧化层8的表面的示例性组成。图4示 出了用于基底层7的导体12的金属为ni,用于共材11的氧化物陶瓷 为钛酸钡(batio3),氧化膜8a为氧化镍的示例。
73.在图4中,共材11和氧化膜8a混合存在于氧化层8的表面上。 共材11和氧化膜8a以晶态或非晶颗粒的形式混合存在,使得共材11 的颗粒分散在氧化膜8a的颗粒中。共材颗粒11以岛的形式分布在氧 化层8的整个表面上。在长轴上,颗粒共材11的一个颗粒的尺寸(长 度)在0.1μm到8μm的范围内。mg、ni和o的化合物13在氧化层8 的表面上以颗粒形式分离。当如图4所示,从表面观察氧化层8时, 共材与整体组成的比率在20at%到75at%的范围内。这可以通过例如通 过edx(能量色散x射线光谱)对足够大的区域进行面分析来证实。 足够大的面积足够大以表示氧化层8的表面组成。
74.共材11从氧化层8的表面经由基底层7向元件本体2延伸。共材 11由聚集为约1μm到40μm尺寸的多个颗粒制成,并可以沿深度方向 分布。因此,即使对氧化层8施加机械应力,暴露在氧化层8的表面 上的共材11也几乎不发生剥离。当机械应力施加于氧化层8时,共材 11可用作穿刺进入氧化层8的支柱,并将氧化层8支撑在基底层7上。
75.共材11暴露在氧化层8的表面上,并且分裂由氧化镍制成的氧化 膜8a。因此,即使当机械应力被施加到氧化层8并且由氧化镍制成的 氧化膜8a从导体12剥离时,在暴露在氧化层8的表面上的共材11的 位置处也防止氧化膜8a的剥离过程。
76.因此,即使在对氧化层8施加机械应力的情况下,也能够降低整 个氧化层8立即破裂的可能性,并且降低氧化膜8a(氧化层8)从外 部电极6a、6b剥离的可能性。
77.由于氧化层8包括mg、ni和o的颗粒化合物13,因此能够提高 氧化层8和基底层7之间的附着强度。因此,能够进一步降低氧化层8 从外部电极6a、6b剥离的可能性。
78.根据上述第一实施例,氧化层8包括用作基底层7的导电材料的 金属的氧化膜和基底层7的共材。因此,能够抑制氧化层8从每个外 部电极6a和6b剥离。由于多层陶瓷电容器1a在每个外部电极6a和 6b的侧面m2、上表面m3、前表面m4和后表面m4的表面上具有几 乎不剥落的氧化层8,湿焊料不会向上移动到外部电极6a、6b的除了 安装面m1之外的面上,并且通过焊接的电容器1a(电子部件)的安 装能够以稳定的方式进行。
79.第二实施例
80.图5是示出制造多层陶瓷电容器的方法的流程图。制造多层陶瓷 电容器的方法将作为本发明的第二实施例描述。图6a至图6j是示出 根据第二实施例的制造多层陶瓷电容器的示例性方法的一系列横截面 图。顺便提一下,为了说明目的,图6c至图6j仅示出两个内部电极 层3a和两个内部电极层3b隔着电介质层4交替层叠。
81.在图5的步骤s1中,将作为分散剂和成型助剂的有机粘合剂和有 机溶剂添加到电介质材料粉末中,并将其粉碎并混合以产生泥浆料。 电介质材料粉末包括例如陶瓷粉末。电介质材料粉末可包括一种添加 剂或多种添加剂。添加剂可以是,例如mg、mn、v、cr、y、sm、 eu、gd、tb、dy、ho、er、tm、yb、co、ni、li、b、na、k或si 氧化物或玻璃。有机粘合剂例如是聚乙烯醇缩丁醛树脂或聚乙烯醇缩 乙醛树脂。有机溶剂例如是乙醇或甲苯。
82.接着,如图5的步骤s2所示和如图6a所示,制造生片24。具体 地,将含有陶瓷粉末的浆料以片状形式施加于载体膜上并干燥以制造 生片24。载体膜例如是pet(聚对苯二甲酸乙二醇酯)膜。浆料的施 加例如通过刮墨刀法、模具涂布机法或凹版涂布机法进行。反复进行 步骤s2以制备多个生片24。
83.然后,如图5的步骤s3所示和如图6b所示,将成为内部电极的 导电膏以预定的图案施加到在步骤s1中制备的生片24的每一个上, 该导电膏将形成图1所示的内部电极层3a和3b,以在生片24上形成 多个内部电极图案23。在步骤s3中,可以在单个生片24上形成多个 内部电极图案23,使得内部电极图案23在生片24的纵向上彼此分离。 用于内部电极的导电膏包括用作内部电极层3a、3b的材料的金属粉 末。例如,如果用作内部电极层3a、3b的材料的金属为ni,则用于 内部电极的导电膏包括ni粉末。此外,用于内部电极的导电膏包括粘 合剂、溶剂以及(如有必要的)辅助剂。用于内部电极的导电膏可包 括作为电介质层4的主要成分的陶瓷材料作为共材。用于内部电极的 导电膏的施加可通过丝网印刷方法、喷墨印刷方法或凹版印刷方法来 实施。因此,步骤s3可以被称为印刷步骤。以这种方式,制备其上具 有内部电极图案23的多个生片24。
84.接着,如图5的步骤s4所示和如图6c所示,以预定的顺序层叠 其上形成有内部电极图案23的生片24和其上未形成内部电极图案23 的生片24a,以形成生片24的块25。其上未形成内部电极图案23的 生片24a用作外层。在步骤s4中,将其上具有内部电极图案23的生 片24分为两组,即,其上具有内部电极图案23a的生片24和其上具 有内部电极图案23b的生片24。然后,其上具有内部电极图案23a的 生片24和其上具有内部电极图案23b的生片24沿层叠方向交替地堆 叠,使得生片24上的内部电极图案23a和下一个或相邻的生片24上 的内部电极图案23b沿生片材24的纵向交替地转换。此外,在生片块 25中定义了三种类型的部分。具体地,在生片块25中定义了:在堆叠 方向上仅堆叠内部电极图案23a的部分、在堆叠方向上交替堆叠内部 电极图案23a和23b的部分以及在堆叠方向上仅堆叠内部电极图案 23b的部分。
85.接着,如图5的步骤s5所示和图6d所示,压制在图5的步骤s4 的形成过程中获得的层叠块25,使得生片24被压接。压制层叠块25 可通过例如将层叠块25夹在树脂膜之间并对层叠块25进行流体静压 来实施。
86.然后,如图5的步骤s6所示和图6e所示,切割被压制的层叠块 25,使得块25被分离成多个元件本体,每个元件本体具有矩形平行六 面体形状。每个元件本体有六个面。如多条竖直虚线27所示,在堆叠 方向上仅存在内部电极图案23a的部分和堆叠方向上仅存在内部电极 图案23b的部分处执行层叠块25的切割。层叠块25的切割例如通过 刀片切割或类似方法来执行。得到的元件本体2如图6f所示。
87.如图6f所示,在各元件本体2的每一个中,内部电极层3a和3b 隔着电介质层4交替层叠。内部电极层3a暴露在每个元件本体2的一 个侧面上,内部电极层3b暴露在每个元件
本体2的另一个侧面上。
88.接着,如图5的步骤s7所示,去除在图5的步骤s6中获得的每 个元件本体2中包含的粘合剂。例如,通过在大约350℃的n2气氛中 加热元件本体2来去除粘合剂。
89.接着,如图5的步骤s8所示,将用于基底层(底层)7的导电膏 施加到在图5的步骤s7中每个元件本体2的去除了粘合剂的两个侧面 以及元件本体2的与这两个侧面邻接的其余四个面的那些边缘。然后, 干燥导电膏。用于基底层7的导电膏包括用作基底层7的导电材料的 金属粉末或填料。例如,当用作基底层7的导电材料的金属是ni时, 用于基底层的导电膏包括ni的粉末或填料。此外,用于基底层的导电 膏包括例如作为电介质层4的主要成分的陶瓷成分作为共材。例如, 以钛酸钡为主要成分的氧化物陶瓷颗粒(d50粒径为0.8μm到4μm) 作为共材在10wt%到40wt%的范围内混合在用于基底层的导电膏中。 此外,用于基底层的导电膏包括粘合剂和溶剂。
90.接下来,如图5的步骤s9所示和如图6g中所示,对在其上于图 5的步骤s8中施加了用于基底层的导电膏的元件本体2进行烧结过程, 使得在每个元件本体2中,内部电极层3a和3b与电介质层4集成, 并且基底层7被形成并与元件本体2集成。元件本体2的烧结例如在 1000℃至1350℃温度范围的烧成炉(firing furnace)中进行10分钟至 2小时。如果使用诸如ni或cu之类的基底金属作为内部电极层3a、 3b的材料,那么烧结过程可以在烧成炉中进行,同时烧成炉的内部保 持在还原性气氛中,以防止内部电极层3a和3b的氧化。
91.接着,如图5的步骤s10所示和如图6h所示,暴露在每个基底层 7的表面上的金属被氧化以在基底层7的表面上形成氧化层8,其包括 该金属的氧化膜和基底层7的共材。在暴露在每个基底层7的表面上 的金属的氧化中,例如可以在n2气氛中在600℃到1000℃下执行再氧 化处理。顺便提一下,为了确保暴露在每个基底层7的表面上的金属 的氧化膜形成足够的厚度,可以向再氧化过程的氛围气体中添加氧气。
92.接着,如图5的步骤s11所示,用抗蚀树脂涂覆除了每个基底层7 的安装面m1以外的四个面(即,侧面m2、上表面m3、前表面m4 和后表面m4)。抗蚀树脂的涂覆例如通过转移辊施加抗蚀树脂并热固 化抗蚀树脂来进行。
93.接着,如图5的步骤s12所示和如图6j所示,通过喷砂(喷砂抛 光)从每个基底层7的安装面m1去除氧化膜,以露出包含在基底层7 的安装面m1中的金属。在喷砂过程中,将元件本体2放置在喷砂装 置中,使得安装面m1朝向上,然后将喷砂介质从元件本体2的正上 方施加到安装面m1上。从元件本体2正上方施加的喷砂介质包绕在 元件本体2的侧面上,但两个基底层7中的每一个的侧面m2、上表面 m3、前表面m4和后表面m4被抗蚀树脂覆盖。因此,氧化膜可以保 持在每个基底层7的侧面m2、上表面m3、前表面m4和后表面m4 上。喷砂后,用溶剂等除去抗蚀树脂。
94.接着,如图5的步骤s13所示和如图6j所示,在每个基底层7的 安装面m1上形成镀层9。在形成镀层9的过程中,例如,可以依次进 行镀cu、镀ni和镀sn。在该过程中,在每个基底层7的安装面m1 上的氧化膜被去除的元件本体2与镀液一起放置在桶中,并且在旋转 桶的同时向桶供应电力,从而形成镀层9。在此过程中,氧化膜存在于 每个基底层7的侧面m2、上表面m3、前表面m4和后表面m4上, 因此在这些面上不形成镀层。
95.图7a是示出图6i的示例性过程的平面图,图7b是通过在长度方 向dl上切割图7a而获得的横截面图。
96.在图7a和图7b中,将多个元件本体2放置在基板31上,每个 元件本体2包括形成在每个基底层7的表面上的氧化膜8。当将元件本 体2放置在基板31上时,每个元件本体2的上表面m3通过固定带32 附着在基板31上,使得每个元件本体2的安装面m1朝上。然后,喷 砂介质34从安装在元件本体2上方的喷嘴33施加(喷砂)到元件本 体2。喷砂介质34例如是由锆石或氧化铝制成的颗粒。
97.喷砂条件主要设置喷砂速度、喷砂量和喷砂面积。喷砂速度由喷 砂介质34的压力和路径调整。喷砂量根据介质循环和喷砂时间进行调 整。喷砂面积通过喷嘴33的形状以及元件本体2和喷嘴33之间的距 离来调整。
98.在喷砂过程中,每个基底层7的侧面m2、上表面m3、前表面m4和后表面m4涂有抗蚀树脂。因此,即使当从喷嘴33喷射的喷砂 介质34包绕到每个元件本体2的侧面上时,在每个基底层7的侧面 m2和上表面m3上保留氧化膜,而从每个基底层7的安装面m1上去 除氧化膜。顺便提一下,从基底层7的安装面m1去除(喷砂)氧化 膜的量可以设置为能够在基底层7的安装面m1上形成镀层9的值或 范围。
99.根据上述第二实施例,作为电介质层4的主要成分的陶瓷成分混 合在用于基底层的导电膏中。因此,可以在每个基底层7上形成包括 用作基底层7的导电材料的金属的氧化膜以及包含用作基底层7的共 材的金属的氧化物的氧化层8。因此,可以制造多层陶瓷电容器1a, 该多层陶瓷电容器1a能够减少或消除氧化层8从外部电极6a和6b 剥离的可能性,同时抑制制造步骤的数量的增加。
100.应当注意,尽管在上述实施例中已经描述了利用喷砂去除外部电 极6a和6b的安装面m1上的氧化层8的方法,但是也可以使用诸如 等离子体蚀刻之类的各向同性干法蚀刻来代替喷砂,也可采用化学抛 光(如湿法蚀刻)代替喷砂。
101.第三实施例
102.图8是示出根据本发明第三实施例的电路板装置的横截面图。电 路板装置包括电路板41和安装在电路板41上的多层陶瓷电容器1a。
103.在图8中,接地电极42a和42b形成在电路板41上。多层陶瓷 电容器1a经由分别附接到外部电极6a和6b的锡镀层9c、9c的焊 料层43a和43b连接到接地电极42a和42b。通过氧化层8防止焊料 层43a润湿(向上移动到)外部电极6a的侧面m2、上表面m3、前 表面m4和后表面m4。类似地,通过氧化层8防止焊料层43b润湿外 部电极6b的侧面m2、上表面m3、前表面m4和后表面m4。因此, 能够防止由于焊料层43a和43b润湿外部电极6a和6b的侧面m2而 导致电子部件之间的间隔减小。由此,能够增加电路板41上的电子部 件的安装密度。
104.即使在回流炉中的还原气氛中执行在电路板41上的焊料安装,并 且暴露在每个氧化层8的表面上的金属的氧化物被还原为金属,每个 基底层7的共材仍保持其在氧化层8的表面上的状态。因此,能够防 止湿焊料层43a向上移动到外部电极6a的侧面m2和上表面m3,并 防止湿焊料层43b向上移动到外部电极6b的侧面m2和上表面m3。
105.由于氧化层8包含基底层7的共材,因此氧化层8能够提高其耐 热性。此外,由于从基底层7到氧化层8的表面存在基底层7的共材, 因此能够提高对热历史(thermal history)的抵抗能力。
106.根据上述第三实施例,氧化层8设置在每个外部电极6a和6b的 侧面m2、上表面m3、前表面m4和后表面m4上。因此,能够提高 安装在电路板41上的多层陶瓷电容器1a的可靠
性,同时增加电路板 41上的电子部件的安装密度。
107.第四实施例
108.图9是示出根据本发明第四实施例的多层陶瓷电容器1b的结构的 横截面图。在图9中,多层陶瓷电容器1b包括元件主体2和两个外部 电极56a和56b。
109.外部电极56a和56b位于元件主体2的相对的侧面上并且彼此分 离(隔开)。外部电极56a和56b中的每一个从元件主体2的侧面延 伸到元件主体2的前表面、后表面、上表面和下表面。
110.外部电极56a和56b中的每一个包括基底层7和三个镀层59a、 59b和59c。外部电极56a和56b中的每一个具有安装面m1、侧面 m2、上表面m3、前表面m4和后表面m4。安装面m1是面向安装有 多层陶瓷电容器1b的电路板(41)的面。上表面m3是与安装面m1 相对的面。尽管在图9中未示出,但如图8所示的构造,多层陶瓷电 容器1b安装在电路板41上的接地电极42a和42b上。
111.外部电极56a和56b中的每一个的安装面m1、侧面m2、前表面 m4和后表面m4以外的面(即上表面m3)涂覆有氧化层58。氧化层 58的材料与图1所示的氧化层8的材料相同。在每个外部电极56a和 56b的基底层7的安装面m1、侧面m2、前表面m4和后表面m4上 依次形成cu镀层59a、ni镀层59b和sn镀层59c。
112.根据上述第四实施例,外部电极56a和56b中的每一个的上面 m3被氧化层58涂覆。此外,镀层59a、59b和59c形成在每个外部 电极56a和56b的安装面m1、侧面m2、前表面m4和后表面m4上。 因此,当在图8的电路板41上安装多层陶瓷电容器1b时,能够允许 湿焊料沿着每个外部电极56a和56b的侧面m2向上移动(延伸),同 时防止湿焊料向上移动到每个外部电极56a和56b的上表面m3上。 因此,即使在接地电极42a和42b上过度施加焊料时,也能够抑制或 防止焊料从接地电极42a和42b向外(横向)延伸,同时防止电路板 41和安装在电路板41上的多层陶瓷电容器1b的总高度超过设计值。 因此,能够缩小安装在电路板41上的电子部件之间的距离,同时降低 安装在电路板41上的电子部件之间短路的可能性。这使得能够以高密 度安装电子部件。
113.第五实施例
114.图10是示出根据本发明第五实施例的电子部件的构造的立体图。 图10示出了作为电子部件的示例的片式电感器61。
115.在图10中,片式电感器61包括元件主体62和两个外部电极66a 和66b。元件主体62具有线圈图案63、内部电极层63a和63b以及 磁性材料64。元件主体62的形状可以是基本上矩形的平行六面体形状。 外部电极66a和66b位于元件主体62的相对的侧面上并且彼此分离。 外部电极66a和66b中的每一个从元件主体62的相关侧面向元件主 体的前表面、后表面、上表面和下表面延伸。
116.线圈图案63和内部电极层63a和63b被磁性材料64覆盖。然而, 内部电极层63a的端部在元件主体62的一个侧面上从磁性材料64露 出并连接到外部电极66a。内部电极层63b的端部从元件主体62的另 一个侧面上的磁性材料64露出并连接到外部电极66b。
117.线圈图案63、内部电极层63a和内部电极层63b的材料可以是例 如cu、ni、ti、ag、au、pt、pd、ta和w等金属或含有这些金属的 合金。磁性材料64例如是铁氧体。
118.外部电极66a和66b中的每一个包括基底层67和镀层69。外部 电极66a和66b中的
每一个具有安装面m1、侧面m2、顶面m3、前 表面m4和后表面m4。安装面m1是面向安装有片式电感器61的电 路板的面。上表面m3是与安装面m1相对的面。
119.基底层67的导电材料的主要成分可以是,例如,包括cu、fe、 zn、al、ni、pt、pd、ag、au和sn中的至少一种的金属或其合金。 基底层67包括共材。共材是例如作为磁性材料64的主要成分的陶瓷 成分。基底层67可包含玻璃成分。例如,玻璃成分是ba、sr、ca、 zn、al、si或b的氧化物。
120.除每个外部电极66a和66b的安装面m1之外的面(即,侧面 m2、上表面m3、前表面m4和后表面m4)涂覆有氧化层68。氧化层 68包括用作基底层67的导电材料的金属的氧化膜和包含用作基底层 67的共材的金属的氧化物。镀层69形成在每个外部电极66a和66b 的基底层67的安装面m1上。基底层67、氧化层68和镀层69可以分 别以与图1的基底层7、氧化层8和镀层9类似的方式构造。
121.根据上述第五实施例,氧化层68包括用作基底层67的导电材料 的金属的氧化膜和含有用作基底层67的共材的金属的氧化物,因此, 能够防止湿焊料向上移动到外部电极66a、66b的其上形成有氧化层 68的那些面。此外,能够抑制或防止氧化层68从外部电极66a和66b 剥离。
122.第六实施例
123.图11是示出根据本发明第六实施例的电子部件的构造的立体图。 图11示出了作为电子部件的示例的片式电阻器71。
124.在图11中,片式电阻器71包括元件主体72、两个外部电极76a 和76b以及保护膜75。元件主体72具有电阻器73、内部电极层73b 和基板74。元件本体72可以具有基本上矩形的平行六面体形状。外部 电极76a和76b布置在元件主体72的相对的侧面上并且彼此分离。 外部电极76a和76b中的每一个从元件主体72的相关侧面延伸到元 件主体72的上表面和下表面。
125.电阻器73和内部电极层73b设置在基板74上并被保护膜75覆盖。 电阻器73的一端连接到基板74上的内部电极层73b。内部电极层73b 伸长到元件主体72的一个侧面并连接到外部电极76b。连接到电阻器 73的另一端的另一内部电极层(未示出)延伸到元件主体72的另一侧 面并连接到外部电极76a。
126.电阻器73的材料可以选自金属,例如ag和pd,或者可以是包含 这些金属的合金。或者,电阻器73的材料可以是金属氧化物,例如氧 化钌。内部电极层73b的材料可以是选自诸如cu、ni、ti、ag、au、 pt、pd、ta和w的金属,或者可以是包含这些金属的合金。基板74 的材料例如是氧化铝等氧化物陶瓷。保护膜75的材料例如是玻璃或树 脂。
127.外部电极76a和76b中的每一个包括基底层77和镀层79。外部 电极76a和76b中的每一个具有安装面m1、侧面m2和上表面m3。 安装面m1是朝向安装有片式电阻器71的电路板的面。上表面m3是 与安装面m1相对的面。
128.基底层77的导电材料的主要成分可以是,例如,包括cu、fe、 zn、al、ni、pt、pd、ag、au和sn中的至少一种的金属或包含cu、 fe、zn、al、ni、pt、pd、ag、au和sn中的至少一种的合金。基底 层77包括共材。共材例如是陶瓷成分,其是基板74的主要成分。基 底层77可包含玻璃成分。例如,玻璃成分是ba、sr、ca、zn、al、 si或b的氧化物。
129.除外部电极76a和76b中的每一个的安装面m1之外的面(侧面 m2和上表面m3)涂覆
有氧化层78。氧化层78包括用作基底层77的 导电材料的金属的氧化膜和包含用作基底层77的共材的金属的氧化物。 镀层79形成在每个外部电极76a和76b的基底层77的安装面m1上。 基底层77、氧化层78和镀层79可以分别类似于图1所示的基底层7、 氧化层8和镀层9来构造。
130.根据上述第六实施例,氧化层78包括用作基底层77的导电材料 的金属的氧化膜和含有用作基底层77的共材的金属的氧化物。因此, 能够防止湿焊料向上移动到外部电极76a和76b的其上形成有氧化层 78的那些面,并且减少氧化层78从外部电极76a和76b剥离的可能 性。
131.应当注意,尽管在上述每个实施例中描述的电子部件具有两个端 子,但是电子部件可以具有三个或更多个端子,例如晶体管或变压器。
132.本技术以日本专利申请no.2020
‑
95332(2020年6月1日提交) 为基础并要求其优先权,其全部内容通过引用并入本文。
再多了解一些
本文用于企业家、创业者技术爱好者查询,结果仅供参考。