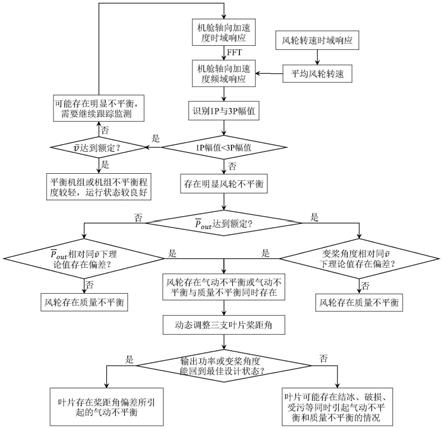
1.本发明属于风力发电技术领域,具体涉及一种风电机组风轮气动不平衡和质量不平衡识别方法。
背景技术:
2.作为风电机组一种典型机械故障,风轮不平衡会影响机组的发电性能、振动稳定性、部件载荷,缩短机组使用寿命,甚至造成损坏。因此,风轮不平衡的准确识别对提升机组发电性能,维持机组安全稳定运行具有重要意义。
3.风轮不平衡主要包括风轮气动不平衡和风轮质量不平衡两种,其中气动不平衡主要由叶片气动性能偏差引起,质量不平衡则由转子质量分布不均匀引起。单纯的气动不平衡主要由叶片安装角零位偏差、变桨控制系统故障等引起;单纯的质量不平衡主要由叶片制造质量分布不一致、轮毂内部质量分布不均匀等引起;叶片结冰、破损、受污等则会同时引起风轮气动不平衡和质量不平衡。
4.本领域技术人员主要通过两种方法来进行风轮不平衡识别。一种是基于大数据分析、人工神经网络算法来进行不平衡识别,但这种方法需要大量风电机组运行数据,且无法识别具体的故障类型。另一种方法是对机组的振动信号或电信号进行频谱分析,通过判定频谱图中与风轮一倍旋转频率1p对应的频率幅值大小来识别不平衡,但已有识别方法几乎都忽视了风速对1p幅值的影响,以及机组不同的控制区间下不平衡对机组运行参数的影响。
5.对于不平衡类型的识别,专利“风电机组动态不平衡在线检测和故障辨识方法及系统”(cn105569932a)中提出了判定不平衡为气动不平衡还是质量矩不平衡的方法。但事实上,叶片结冰、破损、受污等会同时引起风轮气动不平衡和质量不平衡,此方法可能会增加不平衡原因识别的误判风险。
技术实现要素:
6.本发明的目的在于针对现有技术的上述不足和缺陷,提供一种风电机组风轮气动不平衡和质量不平衡识别方法,其优势在于考虑了风速、机组不同运行区间以及不同的不平衡类型对风电机组振动和多项运行参数的影响,降低了机组风轮不平衡误判、漏判风险,提高了风轮不平衡识别精度。
7.为了实现以上目的,本发明所采用的技术方案为,
8.一种风电机组风轮气动不平衡和质量不平衡识别方法,包括以下步骤:
9.1)提取风电机组机舱轴向加速度、风轮转速、风速、输出功率、变桨角度时域响应,并对风轮转速、风速、输出功率、变桨角度取均值;
10.2)对机舱轴向加速度时域响应进行快速傅里叶变换,得到机舱轴向加速度频域响应,通过平均风轮转速识别频域响应中风轮一倍旋转频率1p与风轮三倍旋转频率3p的幅值;
11.具体识别识别风轮一倍旋转频率1p与风轮三倍旋转频率3p的幅值时,需给定平均风轮转速对应的频率识别区间,在频率识别区间范围内寻找峰值最大值作为风轮一倍旋转频率1p与风轮三倍旋转频率3p的幅值,以避免机组处于最佳风能捕获区时风轮转速变化所带来的风轮一倍旋转频率1p频率识别偏差;具体风轮一倍旋转频率1p幅值和风轮三倍旋转频率3p幅值采用下式求得:
[0012][0013][0014]
3)判断风轮一倍旋转频率1p幅值与风轮三倍旋转频率3p幅值的相对大小,若风轮一倍旋转频率1p幅值小于风轮三倍旋转频率3p幅值则进入步骤4,否则判定机组存在明显风轮不平衡并进入步骤5);
[0015]
4)判断平均风速是否达到额定风速,若达到额定则认为该风电机组为平衡机组或机组不平衡程度较轻,运行状态良好;否则判定机组可能存在明显不平衡,需要继续跟踪监测,并回到步骤1);
[0016]
5)判断机组平均输出功率是否达到额定输出功率,若达到额定则进入步骤6),若未达到额定则进入步骤7);
[0017]
6)比较机组当前变桨角度相对于同风速下理论值是否存在偏差,若不存在偏差,则判定风轮存在质量不平衡,若变桨角度存在偏差则进入步骤8);
[0018]
7)比较机组当前平均输出功率相对于同风速下理论值是否存在偏差,若不存在偏差,则判定风轮存在质量不平衡,若输出功率存在偏差则进入步骤8);
[0019]
8)判定所检测风电机组风轮存在气动不平衡或气动不平衡与质量不平衡同时存在,此时通过动态调整机组三只叶片桨距角查看风电机组输出功率或变桨角度能否回到最佳设计状态;若能回到最佳状态,则判定机组不平衡是由三只叶片存在桨距角偏差所引起,若不能回到最佳状态,则判定叶片可能存在结冰、破损、受污等能够同时引起气动不平衡和质量不平衡的情况。
[0020]
与现有风轮不平衡识别方法相比,本发明提出了一种风电机组风轮气动不平衡和质量不平衡识别方法,其中,以机舱轴向加速度频谱中风轮一倍旋转频率1p幅值与风轮三倍旋转频率3p幅值相对大小来进行风轮不平衡识别,充分考虑了风速对风轮一倍旋转频率1p幅值和风轮三倍旋转频率3p幅值的影响,进一步提高了风轮不平衡识别精度。基于风轮质量不平衡和气动不平衡在风电机组不同控制区间对输出功率、变桨角度的不同影响规律,以及纯粹的气动不平衡与气动不平衡和质量不平衡同时存在时控制系统通过调整叶片桨距角能否回到最佳设计状态,提出了风轮不平衡类型的识别方法,为确定风轮不平衡产生原因和后续检修维护提供了方向。
附图说明
[0021]
图1为本发明的方法流程图。
具体实施方式
[0022]
下面结合说明书附图对本发明作进一步详细的描述。
[0023]
如图1所示,本发明一种风电机组风轮气动不平衡和质量不平衡识别方法,具体包括以下步骤:
[0024]
1)提取风电机组机舱轴向加速度、风轮转速、风速、输出功率、变桨角度时域响应,并对风轮转速、风速、输出功率、变桨角度取均值;
[0025]
2)对机舱轴向加速度时域响应进行快速傅里叶变换,得到机舱轴向加速度频域响应,通过平均风轮转速识别频域响应中风轮一倍旋转频率1p与风轮三倍旋转频率3p的幅值;
[0026]
具体识别风轮一倍旋转频率1p与风轮三倍旋转频率3p的幅值时,需给定平均风轮转速对应的频率识别区间,在频率识别区间范围内寻找峰值最大值作为风轮一倍旋转频率1p与风轮三倍旋转频率3p的幅值,以避免机组处于最佳风能捕获区时风轮转速变化所带来的风轮一倍旋转频率1p频率识别偏差;具体风轮一倍旋转频率1p幅值和风轮三倍旋转频率3p幅值采用下式求得:
[0027][0028][0029]
3)判断风轮一倍旋转频率1p幅值与风轮三倍旋转频率3p幅值的相对大小,若风轮一倍旋转频率1p幅值小于风轮三倍旋转频率3p幅值则进入步骤4),否则判定机组存在明显风轮不平衡并进入步骤5);
[0030]
风电机组三只叶片旋转一圈风轮推力以风轮三倍旋转频率3p规律变化,而当机组一支叶片相对于另两只叶片的质量分布或气动载荷存在偏差时,推力会出现与一倍风轮旋转频率1p相同变化周期的波动,相应地机舱轴向加速度频谱中也会在风轮一倍旋转频率1p处出现峰值;当不平衡程度越大,频谱图中风轮一倍旋转频率1p幅值越大,当不平衡程度较为明显时,风轮一倍旋转频率1p幅值会超过风轮三倍旋转频率3p幅值成为主频;
[0031]
此外,风轮一倍旋转频率1p幅值与风轮三倍旋转频率3p幅值的相对大小与风速相关;风速增大,不平衡机组机舱轴向加速度频谱图中风轮一倍旋转频率1p幅值会显著增大,而风轮三倍旋转频率3p幅值随风速变化相对较小,但是在机组刚切入的低风速区,不平衡机组的风轮一倍旋转频率1p幅值也小于风轮三倍旋转频率3p幅值;因此若检测得到某工况下某台风电机组风轮一倍旋转频率1p幅值小于风轮三倍旋转频率3p幅值,不能直接断定该风电机组不存在明显的不平衡,还需判定其对应的风速,若风速较小则该风电机组也有存在明显不平衡的可能,还需通过步骤4)继续跟踪监测;
[0032]
4)判断平均风速是否达到额定风速,若达到额定则认为该风电机组为平衡机组或机组不平衡程度较轻,运行状态良好。否则判定机组可能存在明显不平衡,需要继续跟踪监测,并回到步骤1);
[0033]
5)判断机组平均输出功率是否达到额定输出功率,若达到额定则进入步骤6),若未达到额定则进入步骤7);
[0034]
风电机组三只叶片仅质量分布存在差异时,不平衡质量会引起叶片重量矩呈现与
风轮转速频率一致的周期性变化,这会增大风电机组风轮转速、发电机转矩、输出功率、叶片变桨角度等参数的波动幅度,但对其均值影响很小;而当风电机组存在气动不平衡时,气动性能偏差会降低叶片所产生的气动转矩,导致风电机组远离最佳运行状态,也进一步影响风轮转速、发电机转矩、输出功率、叶片变桨角度等参数的大小。因此,可以通过比较这些参数的平均值相对于相同风速下的理论值是否存在偏差来区分气动不平衡与质量不平衡。
[0035]
具体为,在不同的控制区间,控制策略的不同会影响气动不平衡对各项参数的影响效果。在风电机组达到额定输出功率之前,气动不平衡降低了风轮气动转矩,使得相同风速下风电机组输出功率产生明显损失,而当输出功率相同时,气动不平衡机组所对应的风速更高。在风电机组达到额定输出功率之后,控制系统通过改变桨距角维持输出功率和风轮转速恒定。此时,质量不平衡和气动不平衡都会增大风轮转速、发电机转矩、输出功率的波动幅度,但对其均值影响很小。但是,由于气动不平衡降低了风轮气动转矩,使得机组在更高风速下达到额定功率。气动不平衡机组为了维持输出功率恒定,机组桨距角相对于相同风速下桨距角理论值会存在差别。
[0036]
因此可以根据机组达到额定输出功率之前相对于相同风速下输出功率是否存在偏差,以及机组达到额定输出功率之后相对于相同风速下桨距角是否存在偏差来区分气动不平衡与质量不平衡两种类型,具体参见步骤6)7)8)。
[0037]
6)比较机组当前变桨角度相对于同风速下理论值是否存在偏差,若不存在偏差,则判定风轮存在质量不平衡,若变桨角度存在偏差则进入步骤8);
[0038]
7)比较机组当前平均输出功率相对于同风速下理论值是否存在偏差,若不存在偏差,则判定风轮存在质量不平衡,若输出功率存在偏差则进入步骤8);
[0039]
8)判定所检测风电机组风轮存在气动不平衡或气动不平衡与质量不平衡同时存在,此时通过动态调整机组三只叶片桨距角查看风电机组输出功率或变桨角度能否回到最佳设计状态。若能回到最佳状态,则判定机组不平衡是由三只叶片存在桨距角偏差所引起,若不能回到最佳状态,则判定叶片可能存在结冰、破损、受污等能够同时引起气动不平衡和质量不平衡的情况。
再多了解一些
本文用于企业家、创业者技术爱好者查询,结果仅供参考。