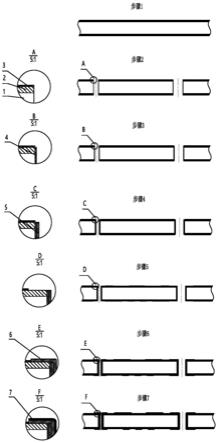
1.本发明属于电路制作技术领域,涉及激光加工技术,尤其是一种选择性电镀孔,激光制抗镀图案,图形电镀蚀刻的制造电路板方法。
背景技术:
2.本发明利用激光加工技术,用同一表面疏化学镀活性种子的高聚物薄膜作为掩敝层,通过激光分步光蚀去除加工,分别制只电镀孔壁,以及同时电镀孔壁和线路的抗电镀图案,分别控制孔壁铜厚和线路铜厚制电路板,能更好地满足对电子产品对电路板的电气要求,特别适合制造厚铜导电图案,也适合各种电路板大批量,小批量、多品种以及样品生产。
3.其制造流程是:在双面覆铜箔板,或完成内层制作叠加外层的多层电路板表面上覆高聚物薄膜
→
钻孔
→
孔导电化
→
电镀铜加厚孔壁
→
激光去除高聚物膜露出焊盘和线路铜
→
电镀铜加厚
→
电镀抗蚀性金属
→
激光去膜露出非线路区域铜
→
蚀刻
→
通断检查
→
去除金属抗蚀剂
→
贴阻焊膜
→
组装现场用激光制阻焊图案并对焊接区进行可焊性处理
→
漏印焊膏,进行元件安装,焊接。
4.当今世界,电子产品无所不在。电子产品最重要的部件之一就是电路板,它是各个元器件的间的电气连接通道,决定着各自的电气参数和电气逻辑关系;同时,它又是各个元器件的安装和固定载体,是产品的骨架。其中,电气连接通道由导电图案和金属化孔实现,元件安装固定的质量与阻焊图案质量及焊接区的可焊性密切相关,电路板的主要生产过程也是围绕导电图案、金属化孔、阻焊图案及焊接区的可焊性展开。然而,传统制电路板方法,制造导电图形、阻焊图案均靠图形转移完成,制造金属化孔需要用基材铜箔陪镀,本质上都是间接技术,不能满足电子技术对图形精密度和孔质量的要求。
5.空间上,可以把电路板上的电气连接分成两组:水平方向上的连接,即通常称之为导电图案的部分,处于各层平面之上,用于实现x、y方向上的连接;垂直方向上的连接,由金属化孔实现,z向上穿过绝缘层和导电层,用于实现导电图案层层间的电气互连。传统的电路板制造技术,制造水平方向上的导电图案,以减成法为主,即:去掉覆铜箔板上多余的铜箔,用留下的铜箔作为导电图形,作为包括导线、焊盘等有电气连接功能的部分;制造垂直方向上的层层间的电气互连,以加成法为主,即:向孔内的孔壁上添加导电材料,用导电的孔壁穿过水平方向的金属层实现电气互连。
6.作为电气连接链路上的重要环节,在制造电路板过程中,理应能够分别控制x、y方向上导电图形和z方向上孔壁导电层的厚度,使整个电气通道达到产品的电气要求,特别是要能独立控制孔壁上的导电层厚度,不让其成为连接链路上的薄弱环节。但是,通用的电路板技术中,孔壁铜厚控制与线路铜厚控制相互干涉,不得不在两者之间进行取舍,这是影响电路板电气性能和可靠性的难题之一。
7.孔金属化,一般采用化学方法。先用化学镀,或其它手段在绝缘的孔壁上沉积薄导电材料层;在此起始导电层上,再用电镀方法镀覆导电金属到需要的厚度,使穿过金属层的
孔具备可靠的层间电气互连指标。基于不同的孔金属化技术,衍生出了不同的工艺路线,包括掩孔法,图形电镀蚀刻法等。两种工艺路线各有优缺点,其技术方案和关键技术简述如下:
8.图形电镀蚀刻法,通称反镀法,是制作印制板的经典工艺路线。开料后的制程从钻孔、孔金属化开始,用化学镀或直接电镀方法在孔壁上形成起始导电层,用电镀方法继续在孔壁和板面上沉积金属铜至一定厚度后,进行图形转移,通过贴光敏膜、曝光、显影,把非线路部分的铜箔先用一层有机材料薄层,称为抗镀剂,掩蔽起来,而把线路部分,包括导线、焊盘、孔壁等表面裸露出来。这样,需要去除部分的金属铜表面被掩蔽,在电镀过程中不与药液接触,不再继续沉积金属;需要保留的部分,包括导线、焊盘、孔壁表面暴露在外,在电镀时与药液接触,或先继续电镀铜,或直接电镀耐蚀刻金属,比如锡、锡铅合金、镍和金等。随后,去除有机材料掩蔽层,把非线路部分的铜箔裸露出来,使之在蚀刻过程中与蚀刻剂反应,被氧化后溶入药液从板面上消失,而导线、焊盘、孔壁等线路部分的表面有金属抗蚀剂遮蔽,不与蚀刻剂接触,被保留在板材上,形成需要的导电图形。最后,要在电路板的非焊接区制造阻焊图案,在焊接区域上涂覆可焊性材料。
9.反镀法制作电路板,成熟稳定但工序步骤多、操作复杂,能对线路部分和非线路部分区别进行电镀处理。其中,孔金属化形成起始导电层后,用电镀方法一次性往孔壁上沉积铜直到要求的最终厚度,同时,也在板面上其余部分增加铜导电层厚度的方法称为全板电镀蚀刻法;而在孔金属化后,在孔壁和板面上先电镀一薄层铜,铜厚控制到刚刚能耐受后续工序即止,在图形转移后,再进行电镀铜至要求的最终厚度,即仅使导电图案部分镀较厚的铜,在非导电图案部分镀较薄的铜的方法称为图形电镀蚀刻法。
10.掩孔法,是另外一种常用的制作电路板工艺路线。开料后的制程从钻孔、孔金属化开始,用化学镀或直接电镀方法在孔壁上形成起始导电层,用电镀方法继续在孔壁和板面上沉积金属铜至最终需要的厚度。然后,进行图形转移,通过贴光敏膜、曝光、显影,用一层有机材料薄层,称为抗蚀剂,把线路部分,包括导线、焊盘、孔掩蔽起来,把非线路部分的铜箔裸露出来。在接下来的蚀刻过程中,铜箔表面裸露的非线路部分接触蚀刻剂,发生氧化反应,溶入药液从板面上消失,而导线、焊盘、孔壁等线路部分的表面因为有抗蚀剂遮蔽,未与蚀刻剂接触,结果被保留在板材上,形成需要的导电图形。与反镀法一样,掩孔法最后也要在电路板的非焊接区制造阻焊图案,在焊接区域上涂覆可焊性材料。掩孔工艺,特点是在全板电镀加厚铜,相对简单,但在制作导电图形时,因为需要蚀刻较厚的铜箔,更加不利于精细电路结构生产。
11.在上述现在常用的两种工艺路线中,通过孔金属化制造z向连接的过程可以分成两个阶段:在绝缘的孔壁上制作初始导电层阶段和对孔壁上的导电层电镀加厚阶段。
12.制作初始导电层技术可分为化学镀铜和直接电镀两种方法。化学镀铜,也称化学沉铜,过程相对复杂,但更为成熟、稳定、应用面广,利用一种自身催化性氧化还原反应,在孔壁上把化学镀铜溶液中的铜(cu
2
)离子还原成cu,而这些被还原的金属铜晶核本身又成为溶液中其它铜离子的催化剂,使铜的还原反应继续在这些新的铜晶核表面上进行,最终在绝缘的孔壁上形成薄薄的一层金属铜层。相比于化学镀铜技术,直接电镀技术过程简单、环境友好,有碳膜法、钯膜法和高聚物膜三种方法流行,直接在孔壁上涂覆或制作导电的碳、钯或高分子材料,形成连续的薄层后,为后续电镀沉积提供基础导电膜。
13.从技术实现上、经济上和电气性能上看,直接电镀和化学沉铜技术形成导电层速度慢、物理性质差,不足以满足电子产品对于z向链路段导电性能和机械性能的要求,所以,加工进程到达薄层导电物呈连续状态且厚度和强度可耐受后续加工后,电路板生产就转用电镀技术,借助外部电源的动力,在孔壁上继续添加性能较好的金属铜。如前所述,有全板电镀和图形电镀两种技术路线可选,虽然两种技术的区别是电镀铜加厚的范围不同,但本质上,两种技术的重要目的,都是为了在孔壁上电镀铜,而为了在孔壁上电镀铜,都不得不用基材上原有的铜箔作为孔壁上镀铜的电源线,从这个角度看,x、y平面上的导电图案,在电镀孔壁过程中起的仅仅是陪镀作用。
14.分析现行的用x、y导电图案为z向链路陪镀的结果,可以看到,现行的技术会限制z向链路机、电性能的提高,还会导致后续导电图案制作流程的困难,影响整个电路板的精密度和制造成本。
15.首先,对比x、y平面与z向导电层,可以看到,无论是全板电镀还是图形电镀都没有真正解决电路板连接链路z向导电层厚度与x、y向导电层厚度一致的问题,在电镀加厚起始导电层过程中,还会扩大构成z向链路的孔壁导电层与构成x、y链路的板面导电层的厚度差。因为,在x、y平面上,导电层基于基板上固有的导电铜箔,上述的电镀铜加厚孔壁导电层过程,还在板面固有铜箔基础上,与孔壁同步增加导电层厚度,而且,由于电力线分步的因素,还由于电镀过程的深度能力和均镀能力限制,板面沉积层的厚度会大于孔壁沉积层。这与当前和未来的电子产品,对于电路板电气连接性能不断增加的要求,特别是对于z向链路的越来越高的性能要求背道而驰。因此,有必要开发一种能选择性电镀加厚孔的技术。
16.其次,分析图形电镀、全板电镀后的在制板板面铜箔和原始绝缘基板板面铜箔,不难知道,铜箔的厚度增加了,质量变差了。ipc标准ipc
‑
6012中,对金属化孔壁厚有明确的要求,至少为20μm。现在的电路板制程,深镀能力有限,当孔壁铜厚达到20μm时,板面增加的铜厚度超出孔壁铜厚,与材料原有铜箔厚度18um相加后,总铜厚超过40μm。这样,电路板电镀铜工序产生的导电层,成了未来导电图形导电层的顶层,在趋肤效应的作用下,是频率较高的电信号传输的主要介质。然而,必须看到,电路板生产中用电镀技术沉积出铜层的质量,比材料原有的用电铸或压延技术制造出的铜箔的纯度略低,晶体略粗糙,电气和机械性能质量略差,在这个意义上,导电层厚度的增加反而不利于信号传输。因此,有必要开发一种技术,不用x、y面上的导电图案作电源线,能独立地电镀增加孔壁导电层。
17.更进一步,现行的电路板生产技术,不论是图形电镀,还是全板电镀,都会在材料原始铜箔基础上,增加厚度达25μm的电镀铜层。毫无疑问,如此孔金属化技术的结果大幅度增加了制造导电图案过程的难度。传统技术,用化学蚀刻技术制造导电图案,加工过程中,蚀刻液与铜箔接触进行蚀刻,蚀刻除了垂直向铜箔深度进行,由于蚀刻液与导线两侧面接触,使得蚀刻同时也在导线的两个侧向进行。被蚀刻的铜层越厚,时间越长,侧向蚀刻现象越严重,侧向蚀刻不仅减小了导线宽度,严重时还会产生断线,可见,铜箔厚度及其导致的侧向蚀刻是一种制约导电图案精细度的因素。如此看来,为了制造更精密的导电图案,也有必要开发一种技术,不用在x、y面上增加铜箔厚度,降低蚀刻制造导电图案的难度。
18.此外,整体上看,传统电路板制造技术,无论是制造x、y平面上的导电图案,还是制造阻焊图案,都面临着精密度和制造难度大的问题,都属于转移制造技术/transfer process,要靠掩膜底版
‑
模具和中间材料间接加工/indirect processing实现设计目标。
现行的技术,制造抗蚀图案、抗电镀图案、阻焊图案都需要光绘制作掩膜底版,作为模具并串联使用,单个模具、单个工序的误差、缺陷会在后续的制程中被放大,造成了现有的电路板技术,难以制造出精细产品。在现在的技术体系中,用于图形转移制程的干膜、金属抗蚀剂、热风整平用助焊剂等等,并非电路板的机械、电气性能所需要的材料,最终并不存在于产品上,而是为实现加工目标而采用的工艺材料,起到中间过渡的功能后,还需要被去除掉,使用和去除这些材料,需要光绘、贴膜、曝光、显影、蚀刻、去膜等等设备,使得传统电路板技术,制造过程复杂,不仅占用资金、场地,还浪费材料、设备等资源,还增加了制造难度。另外,在现有的技术中,导电图案、阻焊图案,都产生于由中间材料、模具形成的抗蚀图案、抗镀图案的转移过程,大部分需要在水中或者化学药液中进行,会产生废渣、废液,废气,环境压力大。因此,有必要开发一种以常用材料代替专用材料,不用或少用中间材料,不用或者少用中间设备,以直接加工为主的技术,取代现有的间接加工技术,这是本发明的另一个目标。
技术实现要素:
19.针对现有技术不能分别电镀加厚孔和线路的不足,本发明开发了一种新型制造方法,能有区别地电镀孔壁和线路,用表面疏化学镀活性种子的高聚物薄膜掩蔽板面,钻孔后只电镀孔壁至厚度满足要求后,再用激光直接去除材料,制作电镀孔壁和线路的图案,图形电镀蚀刻法制造导电图案,最后,用激光直接去除材料制造阻焊图案。
20.具体的加工步骤如下:
21.(1)往内部没有或含有一层及以上导电图形的双面覆有铜箔的工件表面上贴表面疏化学镀活性种子并且抗电镀、抗蚀刻的高聚物薄膜;
22.(2)按设计要求钻孔;
23.(3)孔导电化;
24.(4)电镀,在孔壁上沉积铜加厚孔壁;
25.(5)激光去除焊盘和线路上的高聚物薄膜掩蔽层;
26.(6)电镀,往焊盘、线路和孔壁上沉积铜加厚;
27.(7)电镀,往焊盘、线路和孔壁上沉积抗蚀性金属保护层;
28.(8)激光去除非线路区域高聚物薄膜掩蔽层;
29.(9)蚀刻去除非线路区域上的未被抗蚀性金属保护层覆盖区域的铜箔层;
30.(10)对在制电路板进行电气通断检查;
31.(11)去除焊盘、线路和孔壁上的抗蚀性金属保护层;
32.(12)全板涂覆并一次性固化阻焊材料;
33.(13)在组装现场用激光去除焊接区表面阻焊材料层,制造阻焊图案,并对焊接区表面进行清洁及可焊性处理;
34.(14)向连接盘上添加焊料,进行元件贴装、插装,进行重熔焊接及或波峰焊接。
35.其中,步骤(1),在双面覆铜板或已经完成内层线路制作的多层覆铜箔板上覆高聚物薄膜。
36.现有技术一般采用光致干膜作为抗电镀掩膜,光致干膜为三层结构,光敏胶涂层在载膜和保护膜之间,由胶粘剂和光聚合单体等组成,形成图案过程较复杂,要经过光绘制
版、贴膜、曝光、显影工序;而且,价格贵,强度不高且厚度较大,一般在20μm以上,分辨率受限,掩蔽效果较差。
37.本发明的掩蔽膜不需要具备光敏感性能,但其表面需具有疏化学镀活性种子状态,并且具有抗电镀、抗蚀刻性质;包括由单一组分、多组分、复合的热固、光固、可热压合附着的,非光敏和光敏的材料制造的干性pet、pi、rpp、bopet、bopp、pa、ppe、派瑞林等高聚物薄膜,以及单体的、预聚合的、或已完成聚合的液态、膏状或其它形态的材料;材料的涂覆方法包括滚压、热压、印刷、镀覆、喷涂、帘涂等方法或方法相结合的加工;材料的厚度厚度大于线路上增厚的总金属厚度,范围在2μm
‑
3000μm,优选20μm
‑
1000μm。
38.事实上,一般的预涂覆压敏涂层膜、热敏涂层的高聚物薄膜,经过疏化学镀活性种子处理后即可满足要求。例如,热压贴厚度为200μm热敏pet、bopet膜作为抗电镀掩膜。
39.其中,步骤(2),按照设计要求钻孔。被钻孔材料是导电铜箔和绝缘材料交替叠层而成的复合材料,与传统技术不同,本发明所钻材料增加了贴在板面上的高聚物掩蔽膜。钻孔工具既可以是机械钻头,也可以是聚焦激光光束。
40.如果采用机械钻头钻孔,在孔壁上可能出现环氧钻污,在进行孔导电化前,应该用不伤害上述高聚物薄膜的药液或过程将环氧钻污去除掉,以保证孔金属化质量。
41.其中,步骤(3),孔导电化。本步骤的目的是在孔壁上沉积起始导电层,为下一步电镀孔壁打底。
42.传统的化学沉铜工艺,是先在孔壁上先沉积具有活性的贵金属粒子,然后再沉积铜孔金属实现孔壁表面导电的,因此孔导电化即是现行电路板制造技术中的孔金属化过程;而对于直接电镀工艺,特别是其中的碳膜法、高分子膜法,实现孔壁导电的物质不是金属,因此用孔金属化描述形成起始导电层的过程并不准确。本发明中,涉及现行技术时仍用孔金属化进行描述,涉及本发明的过程时用孔导电化描述,孔导电化既包括用金属实现的孔导电过程,也包括用非金属材料实现孔导电的过程。
43.实现本步骤的目标有两种方法,一种是直接电镀方法,例如,用碳膜法对孔进行黑孔化,经过“前处理
→
黑孔”步骤后形成起始导电层;另一种是传统化学沉铜工艺,经过“镀前处理
→
活化处理
→
化学镀铜”后形成起始导电层。其中,化学镀铜的厚度达到保证过程可靠的下限即可,比如1μm。
44.本步骤中,因为板面覆有高聚物薄膜,且该薄膜表面外表面具有疏化学镀活性种子性能,掩蔽了板面,所有在直接电镀方法的黑孔步骤后,或在化学沉铜方法的活化处理后,板面不会有导电的炭黑、石墨等物质,也不会附着具有催化作用的金属钯活性粒子以及化学沉积的铜等物质。这样,就能维持板面与覆铜箔导电层处于电气绝缘状态,在后续电镀时,就不会有金属铜在板面上沉积,从而达到只在孔壁上电镀铜导电层的目的。
45.其中,步骤(4),电镀铜,在孔壁上沉积铜加厚孔壁。
46.为了解决电镀孔壁时,总面积过小,电力线分步不均,电流密度不容易控制等问题,可以在工件上制造有助于改善质量的电镀平衡块。方法为:在进行步骤(1)之后,在进行步骤(2)、(3)之前或之后,在进行步骤(4)之前,用激光去除非线路且与线路间隔大于30μm以上,优选间隔大于50μm的无电气功能的死铜区域,或其导电层需要去除且不对后续去除过程产生负面影响的区域,或铜厚不影响其功能的区域,或增加铜厚对功能有正面影响的区域上的抗电镀薄膜掩蔽层,露出其下的铜箔面,形成有利于电镀孔壁时电镀电流平衡分
布的分散图案。
47.制造电镀平衡块,仅需去除对应部位铜箔表面的有机材料。此时,所用聚焦激光光斑光功率密度须大于去除有机材料所需的最低功率密度,并且低于或接近于去除其下所覆盖的金属层所需最低光功率密度。优选大于去有机材料所需最低光功率密度的1.2倍。
48.步骤(4)的控制点是电镀时间。此时,板面上除孔壁和电镀平衡块以外,全部区域上都有掩膜覆盖,掩膜是绝缘材料,虽然与电镀药液接触,但表面上沉积不上铜,因此,只有孔壁和平衡块在电镀过程中能沉积铜,电镀时间足够,就能在孔壁上获得足够厚度的铜沉积层,达到了选择性控制孔壁铜厚的目的。
49.其中,步骤(5),激光去除焊盘和线路上的高聚物薄膜掩蔽层。
50.加工目的是露出焊盘和线路的铜表面,以便在焊盘、线路和孔壁上再电镀金属铜加厚,以及在铜表面再电镀镍、金或锡等金属作为抗蚀刻的保护层。
51.不同的电路板,不同的线路,需要去除的区域宽窄不一。如果去除区域宽度与光束直径或其倍数不相符合,会降低去除速度,还会产生搭接,搭接时罗叠区域被激光加工两遍,造成与非罗叠区域加工效果不一致。本发明根据去除的区域形状和尺寸改变聚焦激光光束直径,使聚焦光束直径或其倍数恰等于需要去除区域的宽度,以降低或去除激光加工区域的搭接,提高加工效率。
52.本步骤与制造电镀平衡块过程一样,仅需去除对应部位铜箔表面的有机材料。此时,所用聚焦激光光斑光功率密度须大于去除有机材料所需的最低功率密度,且低于或接近于去除其下所覆盖的金属层所需最低光功率密度。优选大于去有机材料所需最低光功率密度的1.2倍。
53.其中,步骤(6),电镀,往焊盘、线路和孔壁上沉积铜加厚。目的是得到足够厚度的导电层,以满足电路板设计的电气要求。
54.本步骤的控制点是电镀时间。电镀时间足够,就能在孔壁、焊盘和线路上获得足够厚度的铜沉积层,能达到选择性控制电路板导电图案的导电层厚度的目的。
55.现在的电路板制造技术,一般采用光致干膜作为抗电镀掩膜,材料多为紫外光固型,其所形成的掩蔽图案厚度在一定的范围内,既不能太薄,也不能过厚。因为材料是在热压贴膜、紫外曝光后才交联聚合,成为掩膜,后续还要能比较容易地被去膜化学药液分解,如此的后续技术要求造成的掩膜在某种程度上只能是一种不完美的亚固体。太厚,分辨率低,需要的曝光量大,会出现一方面靠近光源的薄层过曝光,另一方面远离光源的薄层欠曝光现象;如果太薄,本来就脆弱的亚固体材料,就更达不到掩蔽需要的机械强度,可能导致渗镀。
56.本发明用激光直接去除制造抗镀掩蔽图形,使用的是非光敏材料,材料本身是聚合完全的固体,无论薄厚,都有足够的掩蔽能力,即使电镀时间较长,也不会脱落、溶解。对于要求线路铜厚度大的电路板,可以在步骤(1)选择较厚的材料,例如,选择厚度为300μm的掩膜,用激光去除需要线路表面上的掩膜材料后,控制电镀时间,直到金属层厚度接近或达到300μm为止。
57.其中,步骤(7),电镀,往焊盘、线路和孔壁上沉积抗蚀性金属。
58.同步骤(6),本发明使用非光敏抗镀材料,掩蔽能力好,可以经受更长的电镀时间,也可以耐受更严苛的镀液及操作条件,因此,可选具备抗蚀性金属的品种更多。
59.其中,步骤(8),激光去除非线路区域高聚物薄膜掩蔽层。目的是露出非线路区域铜箔表面,以便下一步骤蚀刻去除。
60.和步骤(5)一样,此步骤,需要去除对应部位铜箔表面的有机材料层。此时,所用聚焦激光光斑光功率密度须大于去除有机材料所需的最低功率密度,且低于或接近于去除其下所覆盖的金属层所需最低光功率密度。优选大于去有机材料所需最低光功率密度的1.2倍。
61.去除铜箔表面的高分子聚合物,可以选择以co2激光器为光源的设备加工。co2激光器发出的激光,波长为10μm左右,处于远红外波段。铜对这个波段的激光吸收系数低,但这个波段的激光与大多数高聚物耦合性好。因此,去除掉高聚物又不伤铜的激光参数范围宽。选择co2激光,可以使用大直径光斑,去除效率高,成本低,性价比高,而且不伤铜。除了co2激光外,波长在1μm左右的脉冲光纤激光,性能稳定,使用方便且成本低,也适合去除高聚物材料,制造抗蚀图案。
62.其中,步骤(9),蚀刻去除非线路区域上的未被抗蚀性金属保护层覆盖区域的铜箔层。
63.因为需要去掉的铜箔层,被高聚物薄膜掩蔽,在电镀线路过程中,没有铜金属沉积,依然为原料覆铜箔,与传统技术相比,没有厚度增加,更容易蚀刻去除。本步骤,采用传统化学蚀刻技术,但因为需要去除的铜箔层较传统技术薄,需要时间较短,侧腐蚀现象得以减轻,制出的导电图案侧壁质量较好。
64.其中,步骤(10),对在制电路板进行电气通断检查。
65.电路板的最重要功能就是提供电气连接。通过电气通断检查,判断各个网络是否符合设计要求,是现代电路板生产中的重要环节之一。传统电路板技术,通断检查一般是在形成阻焊图案,并且完成焊接区和插装孔可焊性涂覆后,例如在化学镀镍、金,热风整平或浸锡后进行。在阻焊图案和可焊性涂覆后进行通断检查,优点是测试点的焊盘表面有可焊性金属保护,适合进行检查的时间段长,便于组织管理;缺点是如果电路板有通断问题,则问题大都发生在制造过程中间,因为问题发现晚,修复问题或将电路板作废成本较高。在制造阻焊之前进行电气通断检查,缺点是适合进行检查的时间段短,组织管理的窗口小;优点是能及时发现制程问题,修复或作废问题板成本低。本发明中,电气通断检查要么安排在步骤(12)之前,(9)或步骤(11)之后,要么安排在电路板元器件组装现场。
66.其中,步骤(11),去除焊盘、线路和孔壁上的抗蚀性金属保护层。如果电镀质量、镀层品种满足设计要求,可跳过本步骤,直接进入步骤(12)。如果没有在步骤(9)之后,进行电气通断检查,可在步骤(11)之后,进行步骤(12)之前,检查在制电路板各组连接网络内和网络之间的电气通断功能是否正确。
67.其中,步骤(12),全板涂覆并一次性固化阻焊材料。
68.现有技术一般采用液体光敏油墨作为阻焊剂,阻焊剂中含有胶粘剂和光聚合单体,形成图案过程非常复杂,除了要光绘底版外,还要经过涂覆、预烘、曝光、显影、固化等多道工序;而且,价格贵,分辨率不高,在细节距连接盘之间常有漏涂阻焊或阻焊溢流上焊盘现象,涂覆质量很难保证。
69.本发明的阻焊剂不需要具备光敏感性能,一般的预涂覆压敏涂层膜、热敏涂层膜即可满足要求,价格便宜,分辨率高,可以制作精细的图案结构。此外,本发明采用热压涂
覆,不需要额外的固化过程,阻焊图案留待元件组装前现场用激光制作,流程简单。例如,热压贴厚度为5μm
‑
300μm,或者更进一步,30μm
‑
100μm热敏pi、pvc、pc、pet、pp、rpp、bopet、bopp、pa、ppe、派瑞林膜作为阻焊剂。
70.对于导电图案厚度较大,超出高聚物薄膜包覆能力的电路板,应该选择液体阻焊涂料,尽量在吸真空条件下涂覆,以使阻焊剂除了覆盖导电图案的顶面,也能覆盖导电图案的侧壁。因为本发明用激光直接去除,制造阻焊图案,液体阻焊涂料,也不需要具备光敏性能,应该满板涂覆,一次性固化。
71.其中,步骤(13),在组装现场用激光去除焊接区表面高聚物薄膜层,制造阻焊图案,并对焊接区表面进行清洁及可焊性处理。
72.本步骤的要点是在组装现场制造阻焊图案,指一旦阻焊图案制作完毕,裸露出新鲜的铜箔,应立即进行往焊盘表面涂覆焊料,贴片,焊接过程,或插件、焊接过程。
73.本步骤中的激光加工既有选择性去除阻焊材料,制阻焊图案作用;又有清洁焊接区,对焊接表面进行可焊性处理的作用。
74.用激光制造阻焊图案的技术要点在于:图案尺寸准确、光滑,无毛刺;去除干净,阻焊剂无残留、无碳化;保持焊接区金属性能,不伤金属、无重熔、变色;不影响焊盘与基材的附着力,无过热,焊盘不起翘,附着力不降低。阻焊剂一般是高分子聚合物,物理上、化学上与金属差异大,用激光加工去除,找到符合技术要求的窗口比较容易,可以用一种波长激光在同一设备一步完成,也可以在不同设备上分两步进行。
75.纳秒紫外激光,皮秒、飞秒激光,既能被高聚物吸收,起去除作用;也能被铜金属较好地吸收,起到清洁其表面的作用。特别是皮秒、飞秒激光,单脉冲能量较小,但光的强度,即单位面积上的激光功率大,能够仅仅去除微量物质,但改变材料表面性能,是对裸铜表面进行可焊性处理的较好选择。本步骤,可以选择这样的激光加工系统,用同一设备,一步或分步完成制阻焊图案并对焊接区进行可焊性处理加工。
76.co2激光、光纤激光与高聚物作用,吸收率高,而与铜作用,吸收率低。一般而言,这类激光,不能兼顾去除铜箔上的高聚物制阻焊图案与对焊接区进行清洁和可焊性处理功能。因此,本步骤的另外一种选择,是用两类激光光源分两步进行:选择大光斑co2激光,高效去除高聚物制出图案;再用纳秒uv脉冲激光,或皮秒、飞秒激光再去除阻焊剂残余物。
77.第一步:制作阻焊图案,生成焊接区:用波长较长的co2激光器发出的大直径激光光斑,选择性光蚀去除掉焊接区上的阻焊剂涂覆层,去除可能进入孔内的阻焊剂,制作出阻焊图案,生成焊接区。
78.第二步,对焊接区表面进行清洁及可焊性处理,用波长较短的uv波段,或者光强度较大的皮秒、飞秒脉冲激光,去除焊接区表面的阻焊剂残存物,并轻微光蚀焊接区金属表面层,去除金属氧化物,露出新鲜的金属表面,产生容易被熔融的焊料浸润的可焊性。
79.其中,步骤(14),向连接盘上添加焊料,进行元件贴装、插装,进行重熔焊接及或波峰焊接。
80.本发明的方法,因为用激光处理过的新鲜铜表面替代焊接区的可焊性涂覆层,因此,结束步骤(13)之后,应该在尽可能短的时间内进行步骤(14),以避免连接盘表面氧化,在激光处理后可焊性优良的状况下,完成元器件装联,包括,进行元器件插装,并直接向激光处理过的焊接区施加焊料,完成元器件焊接;或直接在向激光处理过的焊接区漏印焊锡
膏,然后进行元器件贴装和回流焊接;或依照其它技术进行元器件组装。
81.在本发明中,激光加工既用于钻孔,还用于去除铜箔层上的高聚物薄膜。所用激光加工设备由一套或者多套数据获取与处理系统、设备操作系统、激光光源、光束整形及传输系统、激光聚焦系统、工件夹持及自动和手动上料与下料系统,工件定位及与光束间的运动与控制系统,视觉检测以及激光功率监测及补偿系统,清洁、恒温系统,激光及设备安全使用系统等组成;激光去除高聚物薄膜或激光去除非线路区域上的铜箔时,能根据被加工区域的形状和尺寸,以单位面积上能量和功率为恒量,以与材料相互作用的光斑直径为变量,以加工速度快、加工路径搭接时无罗叠或有一定量的罗叠、脉冲间有一定罗叠量或间距量之一或其组合为优先,生成激光参数和加工数据;在加工中能针对被加工图形的结构,按预定的激光参数、加工路径要求,在线变换光斑直径。
82.本发明的优点和效果是:
83.1、本发明可以只电镀加厚孔壁,容易控制镀层厚度,能解决孔壁镀层厚度偏薄问题。
84.2、本发明使用非光敏材料作为抗电镀材料,降低成本,而且耐电镀性能好,可以制造具有孔壁和线路金属铜层更厚的导电图案。
85.3、本发明使用激光直接去除方法制造抗电镀图案、阻焊图案,不用图形转移,减少步骤和相关材料、设备,降低成本,可以制造精细的导电图案和阻焊图案。
86.4、本发明技术方案只电镀孔和线路,不增加非线路部分导电层厚度,使蚀刻更容易,有利于制造更精细的导电图案。
87.5、本发明的激光制造图案过程中,根据去除的区域形状和尺寸改变聚焦激光光束直径,使聚焦光束直径或其倍数恰等于需要去除区域的宽度,能降低或去除激光加工区域的搭接,提高加工效率。
88.6、本发明一次性固化阻焊材料,在组装现场制造阻焊图案,不需要可焊性涂覆步骤、材料、设备,大幅度降低成本,降低制造难度。
89.7、本发明用非光敏材料作为阻焊剂,分别用不同波长、脉冲宽度、功率密度的激光制造阻焊图案和进行焊接区清洁以及可焊性处理,效率更高,处理的效果更好。
附图说明
90.图1a为本发明的工艺流程图(步骤1
‑
7);
91.图1b为本发明的工艺流程图(步骤8
‑
14);
92.图中:1、绝缘基板;2、覆铜板铜层;3、抗电镀抗蚀刻的高聚物薄膜层;4、起始导电层;5、电镀铜层;6、沉积铜层;7、抗蚀性金属保护层;8、阻焊材料层;9、可焊性处理表面;10、焊料;11、元件。
具体实施方式
93.以下将结合实施实例,对本发明做进一步的说明。下述的实施实例是说明性的,不是限定性的,不能以下述实施实例来限定本发明的保护范围。
94.电子工业中常用覆铜板为基础材料制作电路板,覆铜板包括绝缘基板1和覆铜板铜层2。
95.实施例1
96.一种选择性电镀孔,激光制抗镀图案,图形电镀蚀刻的制造电路板方法、材料和设备,方法为:
97.(1)往内部无图形的fr4覆铜板上双面热压表面涂敷有机硅树脂的pet膜,形成抗电镀抗蚀刻的高聚物薄膜层3.
98.使用德中dct
‑
br300型号刷板机对1.5h/h覆铜板进行双面刷板(进板速度1.2mm/min;摆动频率70次/min),压缩空气吹净板面水分,微热烘干或自然干燥。
99.进行叠片/叠层,把覆铜板正反两面分别和尺寸相同的表面涂敷有机硅树脂的pet膜贴合并用橡胶辊轮轻微滚压,因为覆铜板表面经过刷板后表面清洁无灰尘,表面涂敷有机硅树脂的pet膜表面也非常干净,因此可以较紧密贴合,可以保证在后续操作过程中不产生相对滑动,橡胶辊轮滚压是为了排出贴合面之间的空气,本实例所用表面涂敷有机硅树脂的pet膜厚度为10um。
100.使用德中dct
‑
la400热压合设备对双面覆pet膜双面板进行压合(12千克力,105℃
‑
115℃,走板速度200mm/min)。
101.(2)按照设计要求钻孔
102.使用德中dct
‑
dm350设备按照设计要求钻孔。将设计好的数据导入德中circuitcam软件,经此软件处理之后,生成设备可用的打孔数据,并导入dm350设备,将压合之后的板子至于设备平台,ccd定位,进行全自动打孔加工,根据孔径不同,具体钻孔参数也有所不同,其主要参数范围如下:钻头转速45000转/min
‑
100000转/min,进刀速度15mm/s
‑
30mm/s,退刀速度25mm/s
‑
40mm/s。
103.(3)活化及化学沉铜,形成起始导电层4.
104.使用碱性除油剂进行除油(50
‑
60℃,5
‑
8min);稀盐酸溶液预浸(室温,1
‑
2min);钯盐溶液活化(25
‑
30℃,3
‑
5min);解胶溶液处理(45
‑
50℃,5
‑
8min);碱性沉铜溶液进行沉铜(40
‑
45℃,60
‑
80min)。
105.本步骤中,只有孔壁部分能与药液接触,其余部分全部被表面涂敷有机硅树脂的pet膜所覆盖。此pet膜表面的有机硅树脂具有疏化学活化的特性,因此最终表面不能形成化学沉铜层,而孔壁的表面会形成一层较薄的化学沉铜层。
106.(4)电镀,在孔壁上形成电镀铜层5。
107.使用德中dct
‑
tp300孔化设备进行孔壁铜层的加厚电镀。采用小电流、长时间(0.1安培
‑
0.15安培,20min
‑
30min)的方式增加孔壁镀层的均匀性。为了进一步提高均镀、深镀能力,dct
‑
tp300孔化设备还配备了药液射流循环结构、脉冲直流电镀功能及反脉冲电镀功能。
108.本步骤中,因为涂敷有机硅树脂的pet膜表面并无导电能力,因此电镀只是针对孔壁进行。
109.(5)激光去除焊盘和线路上的pet膜
110.将数据导入德中circuitcam软件,经过软件处理、计算,生成激光去除焊盘表面和线路表面pet膜的路径;将路径数据导入德中dct
‑
u5设备的dreamcreator设备操作软件中,板子至于设备平台,ccd自动对位后,激光自动去除线路表面和焊盘表面的pet膜。
111.本步骤中,circuitcam软件计算激光加工路径时,会根据具体图形的尺寸,匹配合
适的光斑直径并生成相应的加工路径;在dreamcreator软件执行激光加工的过程中,会根据数据自动实时改变光斑直径并调整功率,以高效率、高质量完成激光去除。本过程中,涉及的关键激光加工参数如下:
[0112][0113]
(6)往焊盘、线路和孔壁上电镀铜加厚,形成沉积铜层6.
[0114]
使用德中dct
‑
tp300孔化设备,对焊盘、线路、孔壁铜层进行加厚电镀,电镀参数:025安培,30min。
[0115]
(7)焊盘、线路和孔壁上电镀锡铅作为抗蚀层,形成抗蚀性金属保护层7.
[0116]
使用锡铅比为6:4的氟硼酸盐镀液,电流密度为2.5a/dm2,电镀25min,后续进行板面清洁处理,使用压缩空气进行风干。
[0117]
(8)激光去除板面上剩余的pet膜(除焊盘、线路之外板面上的pet膜)
[0118]
操作步骤同步骤(5),涉及的关键激光加工参数如下:
[0119][0120]
(9)化学蚀刻去除非线路区域的铜层
[0121]
德中dct
‑
eu400自动化蚀刻设备,集蚀刻、清洗、干燥功能于一体,走板速度2.0m/min。
[0122]
(10)对在制板进行通断检查
[0123]
使用万用表,人工对在制板上的线路进行通断检查。
[0124]
(11)去除焊盘、线路和孔壁上的锡铅保护层.
[0125]
首先,采用加热及热风剥离去除大部分锡铅的方法进行物理去除;然后将板子浸入退镀液,按照工艺要求,控制温度和时间,化学方法去除焊盘、线路和孔壁上剩余的少量锡铅镀层。
[0126]
(12)全板印刷阻焊油墨并一次性全固化,形成阻焊材料层8.
[0127]
使用丝网印刷设备,双面印刷太阳psr
‑
400系列g23khp型阻焊油墨,于烘箱中120℃烘烤60min,进行完全固化处理。
[0128]
(13)组装时,激光去除阻焊膜制造阻焊图形,对焊接区进行清洁和可焊性处理,可焊性处理表面9.
[0129]
使用ciucumcam软件计算去除阻焊路径、焊接区铜面清洁及可焊性处理路径数据,使用dct
‑
u5(20w)皮秒紫外设备,进行阻焊去除、焊接区铜面清洁及可焊性处理,其主要参数如下:
[0130][0131]
(14)向连接盘上添加焊料10,进行元件11贴装、插装,进行重熔焊接及波峰焊接。
[0132]
向焊盘表面添加焊料,进行表面贴装、插装,进行重熔焊接。
[0133]
实施例2
[0134]
一种选择性电镀孔、焊盘,激光制抗蚀图案,化学蚀刻制导电图案的制造电路板方法、材料和设备,方法为:
[0135]
(1)往内部已完成2层图形制做、表面已层压铜箔但未进行线路制作的板子层压pi膜
[0136]
使用德中dct
‑
br300型号刷板机进行双面刷板(进板速度1.2mm/min;摆动频率70次/min),压缩空气吹净板面水分,微热烘干或自然干燥。
[0137]
使用德中dct
‑
mp300层压机对完成叠片的双面板及pi膜进行层压,层压时为缓冲压力及平衡热量在板面平面上的分布,使用了硅橡胶垫作为热压合衬垫。依据材料特性,热压合分五步进行:step1中温低压(15min;80℃;24n/cm2);step2中温中压(25min;140℃;94n/cm2);step3中温高压(25min;180℃;188n/cm2);step4高温高压(60min;220℃;188n/cm2);step5保压并冷却(45min;
‑‑‑‑
;188n/cm2)。
[0138]
本实例采用的初始板材,即内部包含两层导电图形,外部压合了两层铜箔的四层板,为后续表述清晰,将四层导电层按剖面结构从上到下依次称顶层、次顶层、次底层和底层,中间三层介质层亦按照此种方式称为介一层、介二层和介三层。
[0139]
本实例中使用的干膜为25um杜邦kapton hn膜。
[0140]
(2)激光钻孔
[0141]
使用德中dct
‑
d6(飞秒紫外)激光设备按照设计要求打孔。将设计好的数据导入德中circuitcam软件,经此软件处理之后,生成设备可用的打孔数据,并导入d6设备操作软件dreamcreator,将压合之后的板子至于设备平台,ccd定位,进行全自动打孔加工。
[0142]
激光钻孔关键参数:
[0143]
波长脉宽光斑直径平均功率脉冲频率加工速度加工次数355nm600fs20um12.5w1200khz800mm/s12次
[0144]
(3)黑孔
[0145]
用碱性除油剂进行除油(45
‑
50℃,10
‑
15min,加摆动);含微纳级碳颗粒的悬浮液(黑孔液)进行黑孔(10
‑
15min,加摆动);用压缩空气去除板面附着的微量黑孔液;自然风干或低热烘干(25℃
‑
40摄氏度),以蒸发黑孔液溶剂,使之在孔内壁表面上形成一层连续的碳介质膜,用作电镀铜时的导电前驱物。
[0146]
(4)电流平衡区/陪镀区制作
[0147]
按照线路的设计要求,去除板子上符合电流平衡区/陪镀区定义区域表面的pi膜,露出其下层铜箔,以做电镀孔壁时平衡电流之用。
[0148]
具体方法,将数据导入德中circuitcam软件,经过软件处理、计算,生成激光去除电流平衡区/陪镀区表面pi膜的路径;将路径数据导入德中dct
‑
u5设备的dreamcreator设备操作软件中,板子至于设备平台,ccd自动对位后,激光自动去除电流平衡区/陪镀区表面pi膜。
[0149]
(5)针对孔壁镀铜
[0150]
使用德中dct
‑
tp300孔化设备进行孔壁铜层的加厚电镀(1.25安培,20min
‑
30min,此为考虑了电流平衡区/陪镀区的影响,经优化后的电镀参数)。
[0151]
(6)激光去除焊盘和线路上的pi膜
[0152]
将数据导入德中circuitcam软件,经过软件处理、计算,生成激光去除焊盘表面和线路表面pi膜的路径;将路径数据导入德中dct
‑
u5(20w,纳秒紫外光源)设备的dreamcreator设备操作软件中,板子至于设备平台,ccd自动对位后,激光自动去除焊盘表面和线路表面的pi膜。
[0153]
(7)对焊盘、线路和孔壁上进行电镀,加厚铜层
[0154]
使用德中dct
‑
tp300孔化设备进行焊盘、线路和孔壁铜层的加厚电镀,2安培,20min。
[0155]
(8)电镀锡铅
[0156]
使用锡铅比为6∶4的氟硼酸盐镀液,电流密度为2.0a/dm2,时间45min,往焊盘、线路和孔壁上电镀锡铅抗蚀层,之后进行板面清洁处理,使用压缩空气进行风干。
[0157]
(9)激光去除非线路区域的pi膜
[0158]
将数据导入德中circuitcam软件,经过软件处理、计算,生成激光去除非线路上pi膜的路径;将路径数据导入dreamcreator设备操作软件中,板子置于设备平台,ccd自动对位后,激光自动加工,本过程中,涉及的关键激光加工参数如下:
[0159]
波长脉宽光斑直径焦点偏移平均功率脉冲频率加工速度加工次数10600nm
‑‑
250um0mm2020khz1200mm/s2次
[0160]
(10)化学蚀刻去除非线路区域的铜层
[0161]
德中dct
‑
eu400自动化蚀刻设备,集蚀刻、清洗、干燥功能于一体,走板速度2.0m/min。
[0162]
(11)进行电气通断检查
[0163]
根据设计原理图,对在制的裸板进行电气通断检查。
[0164]
(12)去除锡铅抗蚀层
[0165]
使用热油浸泡的物理方法以及退锡铅液浸泡的化学方法相结合,去除焊盘、线路和孔壁表面的锡铅抗蚀层。
[0166]
(13)往工件表面上贴合rpp薄膜作为阻焊膜
[0167]
通过热压贴合方式将rpp薄膜贴合在已经制作完成导电图案的多层覆铜箔板上,贴膜机贴合参数:压力20kg/cm2,温度120℃,速度0.5m/min。
[0168]
(14)用激光去除焊接区表面rpp薄膜层,制造阻焊图案;
[0169]
具体地,本实施例采用20w紫外纳秒激光机进行阻焊图案的制作,将电路板置于激光设备吸附台上,导入激光加工的工程资料数据,将电路板与加工数据精准对位,激光光蚀rpp薄膜成型阻焊图案。顶面加工完成后,翻转电路板,同样的方法完成底面阻焊图案的制作。加工参数如下:
[0170]
功率频率脉宽加工速度加工次数5w100khz20ns600mm/s2
[0171]
(15)添加焊料,装联元器件
[0172]
向焊盘等焊接区添加导电膏,进行元器件装联,过回流焊进行终固化。
[0173]
以上所述的仅是本发明的优选实施方式,应当指出,对于本领域的普通技术人员来说,在不脱离发明构思的前提下,还可以做出若干变形和改进,这些都属于本发明的保护范围。
再多了解一些
本文用于企业家、创业者技术爱好者查询,结果仅供参考。