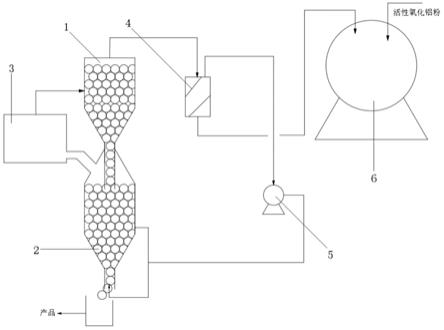
1.本发明涉及氧化铝制备技术领域,尤其涉及一种氧化铝焙烧节能系统及方法。
背景技术:
2.由于氧化铝具有合适比表面积、孔结构可控、热稳定性好、吸附能力强等特点,被广泛用作催化剂载体与吸附剂。为更好发挥性能,除要求更优或更合适的载体物化指标(通常指比表面、孔容、孔径分布、抗压碎强度等)外,工程化应用(传质、传热、磨损等)对催化剂形状也有要求,常用形状有:球形、环形、片状、条状(圆柱、三叶草、四叶草)、带齿、带孔等。与柱状相比,球形催化剂载体具有独特的优势:球形催化剂表面光滑,可自行滚动,装卸容易,装填后床层均匀;在粒度相同情况下,催化剂压降可降低约30%;球形催化剂颗粒规整,床层气流分布均匀,同平面温差小,不易产生沟流;球形催化剂表面光滑,耐磨性好,不易粉化。目前石油炼制与石油化工的反应器中,球形催化剂几乎可取代其他所有形状催化剂,并显示更优异的催化性能,但由于生产制备技术中的成本因素,球形氧化铝载体没有得到大规模应用。
3.现有的球形氧化铝生产时的焙烧过程中会长生大量热风,但现有技术中心对这些热风的利用率较低,这样就造成了大量能源的浪费。
技术实现要素:
4.本发明提出了一种氧化铝焙烧节能系统及方法。
5.为了实现上述目的,本发明采用了如下技术方案:
6.一种氧化铝焙烧节能系统,包括成球盘和焙烧炉,所述成球盘用于将原料制粒,所述焙烧炉用于将制粒后的原料进行焙烧,所述焙烧炉上部与气液分离器相连接,所述焙烧炉下部与用于产品降温的预热器相连接,所述气液分离器的出水端将滤出的液体送入成球盘,所述气液分离器的出气端通过引风机将过滤后的气体送入预热器,所述预热器与加热炉相连接,所述加热炉还与焙烧炉相连接。
7.进一步地,所述加热炉的进气端与预热器相连通,所述加热炉的出气端与焙烧炉相连通。
8.进一步地,所述加热炉为空气电加热炉。
9.进一步地,所述气液分离器为除湿气液分离器。
10.进一步地,所述引风机通过管路与预热器的底部和中部相连通。
11.进一步地,所述预热器的出料口与包装系统相连接。
12.一种氧化铝焙烧节能方法,将焙烧炉中的热空气引出,热空气经过气液分离器后,从气液分离器引出的管路将分离出来的水送入成球盘中使用,然后将制得的氧化铝球状颗粒送入焙烧炉中焙烧,焙烧炉焙烧的同时,空气电加热炉为焙烧炉提供热风,焙烧结束后,经过焙烧后的氧化铝球状颗粒进入预热器中进行降温,通过引风机将气液分离器中的热风引入预热器中,通过该热风对氧化铝球状颗粒进行降温,该热风对氧化铝球状颗粒降温后
通过管路进入电加热炉中进行二次加热后再进入焙烧炉中使用。
13.本发明具有以下有益之处:本发明通过将焙烧炉中的热空气引出,热空气经过气液分离器后,分离出的液体进入成球盘中使用,分离出的气体经过引风机送入预热器中对成品降温,并且将降温后的热空气再次回收加热用于焙烧炉中,实现了整个生产系统中的热量循环利用,与现有技术相比,降低了整个系统的20
‑
30%的能耗。
附图说明
14.图1为本发明的整体示意图。
15.图中,1焙烧炉,2预热器,3加热炉,4气液分离器,5引风机,6成球盘。
具体实施方式
16.下面对本发明实施例中的技术方案进行清楚、完整地描述,显然,所描述的实施例仅仅是本发明一部分实施例,而不是全部的实施例。
17.在本发明的描述中,需要理解的是,术语“上”、“下”、“前”、“后”、“左”、“右”、“顶”、“底”、“内”、“外”等指示的方位或位置关系为基于附图所示的方位或位置关系,仅是为了便于描述本发明和简化描述,而不是指示或暗示所指的装置或元件必须具有特定的方位、以特定的方位构造和操作,因此不能理解为对本发明的限制。
18.实施例1:
19.参照图1,一种氧化铝焙烧节能系统,包括成球盘6和焙烧炉1,所述成球盘6用于将原料制粒,所述焙烧炉1用于将制粒后的原料进行焙烧,所述焙烧炉1上部与气液分离器4相连接,所述焙烧炉1下部与用于产品降温的预热器2相连接,所述气液分离器4的出水端将滤出的液体送入成球盘6,所述气液分离器4的出气端通过引风机5将过滤后的气体送入预热器2。所述预热器2与加热炉3相连接。所述加热炉3还与焙烧炉1相连接。所述焙烧炉1包括主体为空心圆柱体的炉体、分别设于炉顶和炉底的入料口和出料口、插入炉内的热风管,在所述的热风管外设有与其同轴的套管。沿炉内壁轴向和圆周周长方向均匀间隔设有由金属材料制作形状为长条平板的炉壁溜板,炉壁溜板的一端与炉体内壁固定连接,另一端向下倾斜悬空,其与炉体内壁的倾斜夹角为120度。沿所述的热风管外壁轴向和圆周周长方向均匀间隔设有由金属材料制作形状为长条平板的管壁溜板,管壁溜板的一端与管外壁固定连接,另一端向下倾斜悬空,其与管外壁的倾斜夹角为120度。所述的炉壁溜板与炉体内壁的连接端、管壁溜板与管外壁的连接端在轴向上的位置相错开。其顶端位于炉体的上端之上150mm处,其目的是对热风管进行保温,减少热能通过热风管壁向炉内释放能量,热风通过热风管的出口吹向炉内,其热能由下向上均匀传递,使得处于同一层的活性氧化铝湿球受热均匀,活化性能一致。
20.所述加热炉3为空气电加热炉3。所述空气电加热炉3包括全炉体,所述炉体内部安装有过滤器,所述过滤器的前方设有安装于炉体内部的电加热器,所述炉体的内部后端安装有循环风机,炉体的后端侧壁上设有与循环风机连接的出风口,所述炉体的前端侧壁上设有进风口,所述进风口处整体连接插入式风机,所述炉体的前端侧壁上设有补新风口,所述电加热器包括若干根矩阵排列的碳晶电热管。
21.所述气液分离器4为除湿气液分离器4。所述引风机5通过管路与预热器2的底部和
中部相连通。
22.本技术实施例工作时,首先将原料放入成球盘6中,成球盘6滚动造粒将原料制成氧化铝球状颗粒,并且通过从气液分离器4引出的管路将分离出来的水送入成球盘6中,气液分离器4将焙烧炉1中的气体中带有的水分分离后送入成球盘6,以便成球盘使用,然后将制得的氧化铝球状颗粒送入焙烧炉1中焙烧,焙烧炉1焙烧的同时,空气电加热炉3为焙烧炉1提供热风,焙烧温度为500~1300℃,焙烧时间为2~6小时;焙烧结束后,经过焙烧后的氧化铝球状颗粒进入预热器2中进行降温,通过引风机5将气液分离器4中的热风引入预热器2中,该热风的温度低于从焙烧炉1中进入预热器2中的氧化铝球状颗粒的温度,通过该热风对氧化铝球状颗粒进行降温,该热风对氧化铝球状颗粒降温后通过管路进入电加热炉3中进行二次加热后再进入焙烧炉1中使用。通过这一循环回路,实现了对焙烧炉1中排出的热空气的循环利用,与现有技术相比,降低了整个系统的20
‑
30%的能耗。
23.表1本技术的实施例1与现有技术的对比
[0024] 焙烧炉工作温度/℃每吨产品的天然气用量/m3实施例1300
‑
50051现有技术300
‑
50060
[0025]
本技术实施例的焙烧炉工作温度与现有技术中焙烧炉的工作温度无异,但本技术实施例由于对焙烧炉的热空气进行了回收再利用,大大减少了产品生产过程中天然气的消耗量。
[0026]
实施例2:
[0027]
一种氧化铝焙烧节能方法,将焙烧炉1中的热空气引出,热空气经过气液分离器4后,从气液分离器4引出的管路将分离出来的水送入成球盘6中使用,然后将制得的氧化铝球状颗粒送入焙烧炉1中焙烧,焙烧炉1焙烧的同时,空气电加热炉3为焙烧炉1提供热风,焙烧结束后,经过焙烧后的氧化铝球状颗粒进入预热器2中进行降温,通过引风机5将气液分离器4中的热风引入预热器2中,通过该热风对氧化铝球状颗粒进行降温,该热风对氧化铝球状颗粒降温后通过管路进入电加热炉3中进行二次加热后再进入焙烧炉1中使用。
[0028]
本技术实施例通过将焙烧炉1中的热空气引出,热空气经过气液分离器4后,分离出的液体进入成球盘6中使用,分离出的气体经过引风机5送入预热器2中对成品降温,并且将降温后的热空气再次回收加热用于焙烧炉1中,实现了整个生产系统中的热量循环利用,与现有技术相比,降低了整个系统的20
‑
30%的能耗。
[0029]
以上所述,仅为本发明较佳的具体实施方式,但本发明的保护范围并不局限于此,任何熟悉本技术领域的技术人员在本发明揭露的技术范围内,根据本发明的技术方案及其发明构思加以等同替换或改变,都应涵盖在本发明的保护范围之内。
再多了解一些
本文用于企业家、创业者技术爱好者查询,结果仅供参考。