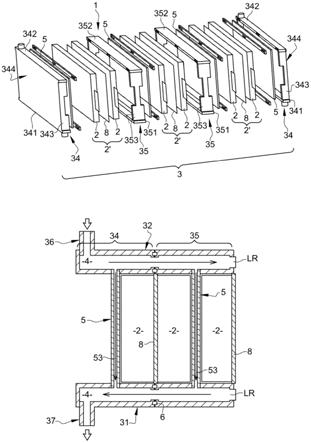
1.本发明涉及自动电能源领域,特别涉及关于机动车辆的车载自动电能源,并且涉及电池组和配备有至少一个这种电池组的电动或混合动力机动车辆。
背景技术:
2.电动或混合动力机动车辆配备有允许储存其运行所需的电能的电池。目前的挑战要求优化电池的设计,以便在寿命和续航里程方面获得最佳性能。充电时间也是在这些电池的日常使用中的重要因素。为此,越来越多地使用高存储密度的电池。它们通常由串联或并联的多个电池单元形成,这些电池单元能够以块或模块的形式物理地组合在一起。
3.理想情况下,这些高存储密度电池需要在包括在20℃至40℃之间的温度下运行。温度过高会严重影响这些电池的寿命。因此,有必要有效地移除由电池单元产生的热。
4.在车载应用的背景下,有风冷电池解决方案,但热交换仍然相当有限。目前的趋势是使用冷却剂来改善热交换和提高冷却效率。
5.使用冷却剂的现有解决方案之一在图1a和图1b中表示,并且基于以下原理:使冷却剂lr循环通过基部支承件s,并且塑料壳体b搁置在基部支承件s上,该塑料壳体b容纳以由泡沫隔板ps分开的若干单元c的块的形式组合在一起的电池单元c,借助于铝传导板pc确保电池单元c与基部支承件s之间的热传递。具体地,每个传导板pc具有l形,l的分支部中的一个分分支部设置在单元的两个相邻的块之间,而l的另一个分支部与基部支承件s接触。然而,这种已知的解决方案具有夸张地延伸热传递回路的缺点,这限制了冷却的效率。此外,制造和组装这种电池结构的成本相对较高。
6.因此,本发明旨在提出该现有解决方案的替代解决方案,并且该替代解决方案不具有上述缺点。
技术实现要素:
7.为此,本发明涉及一种电池组,特别是用于电动或混合动力机动车辆的电池组,其包括:
8.‑
多个电池单元,可选地以两个或更多个电池单元的模块形式物理地组合在一起,
9.‑
壳体,该壳体容纳并包围所述多个电池单元,所述壳体包括下壁、上壁和连接该下壁和该上壁的侧壁,电池单元搁置在该下壁上,该上壁布置在电池单元的上方,
10.其特征在于,壳体的下壁和上壁中的每一者被至少一个冷却通道横穿,冷却剂能够沿着该至少一个冷却通道流动,所述冷却通道构造成分别覆盖下壁的整个表面和上壁的整个表面,并且,壳体的下壁和上壁通过多个冷却板连接,每个冷却板设置在两个相邻的电池单元、或者相邻的电池单元的模块之间,或者每个冷却板与至少一个电池单元接触,并且构造成将由电池单元产生的热传递至冷却剂。
11.本发明的电池组还可以包括以下特征中的一个或更多个:
12.‑
每个冷却板由塑料材料形成,并且包括多个内部通道,多个内部通道从通向上壁
的冷却通道的上端部延伸至通向下壁的冷却通道的下端部,从而允许冷却剂通过所述内部通道从上壁循环到下壁。
13.‑
冷却板由具有高热导率的材料形成。
14.‑
冷却板的构成材料的热导率大于或等于20w.m
‑1.k
‑1,并且优选地大于或等于100w.m
‑1.k
‑1。
15.‑
冷却板由导热的塑料材料形成。
16.‑
冷却板由铝形成。
17.‑
冷却板是大致平坦的。
18.‑
冷却板与壳体包覆模制。
19.‑
冷却板是u形的。
20.‑
冷却板胶合在壳体上。
21.‑
壳体设置有至少一个入口孔口和至少一个出口孔口,所述入口孔口和出口孔口分别与冷却通道连通,以分别允许冷却剂进入到壳体内部以及排出至壳体外部。
22.‑
壳体由通过连接装置固定在一起的若干壳体面板的组件形成,所述壳体面板包括设置在壳体的端部中的每个端部处的至少两个端板和插在所述端板之间的多个中间板。
23.‑
连接装置是与形成在壳体面板内的对应螺纹配合的螺钉。
24.‑
端板中的至少一个端板配备有入口孔口和/或出口孔口,所述入口孔口和/或出口孔口分别与冷却通道连通,以便分别允许冷却剂进入到壳体内部以及排出至壳体外部。
25.‑
每个壳体面板均紧固至单个冷却板。
26.本发明还涉及一种配备有至少一个如上所述的电池组的机动车辆,特别是电动或混合动力机动车辆。
附图说明
27.通过阅读以示例的方式且参照附图给出的以下描述,本发明的其他方面和优点将变得明显,在附图中:
28.[图1a]是根据现有技术的电池组的分解立体图;
[0029]
[图1b]是图1a的电池组的横截面图;
[0030]
[图2]是根据本发明的电池组的第一构型的分解立体图;
[0031]
[图3]是图2中表示的电池组中使用的冷却板的前视图;
[0032]
[图4]是图2中表示的电池组的部分横截面图;
[0033]
[图5]是根据本发明的电池组的第二构型的分解立体图;
[0034]
[图6]是图5中表示的电池组的壳体面板中的一个壳体面板的立体图,冷却板已经固定在该壳体面板上;
[0035]
[图7a]是沿着图6的截面平面aa的截面图;
[0036]
[图7b]是沿着图6的截面平面bb的截面图;
[0037]
[图8]是根据图5的电池组的部分横截面图,其中冷却板的形状不同于图7a和图7b中表示的形状;
[0038]
[图9]是示出了根据图5的电池组内部的冷却剂回路的示意图;
[0039]
[图10]是图6表示的壳体面板的前视图;
[0040]
[图11]是图2表示的电池组的壳体的立体图;
[0041]
[图12]是表示根据现有技术的电池组中的冷却周期(以秒表示)的电池单元的温度变化(以℃表示)的图;
[0042]
[图13]是表示根据本发明的第一实施方式的根据电池组中的冷却周期(以秒表示)的电池单元的温度变化(以℃表示)的图;
[0043]
[图14]是表示根据本发明的第二示例性实施方式的根据电池组中的冷却周期(以秒表示)的电池单元的温度变化(以℃表示)的图;
[0044]
[图15]是表示本发明的第三示例性实施方式的根据电池组中的冷却周期(以秒表示)的电池单元的温度变化(以℃表示)的图。
具体实施方式
[0045]
参照图2,表示根据本发明的第一构型的电池组1。该电池组1包括多个电池单元2,这些电池单元2物理地组合成由泡沫壁8分开的两个电池单元2的模块2’。在本发明的其他可能的构型中,在模块2’中的每个模块2’中的电池单元2的数量可以大于两个,或者每个模块2’可以只包括一个单个电池单元2。电池单元2设置在塑料壳体3内,该塑料壳体3由设置在壳体3的端部中的每个端部处的两个端板34和置于所述端板34之间的多个中间板35的组件形成。所述板34、35大致具有长方体形状,并且各自包括分别为341和351的下壁和分别为342和352的上壁,所述下壁341、342和上壁351、352分别由侧壁343和353连接。端板34还包括横向壁344,横向壁344垂直于下壁341、上壁342和侧壁343。如此获得的壳体3,如图11所表示的,大致具有长方体的形状,并且包括设置在电池单元2下方的下壁31和设置在电池单元2上方的上壁32,所述下壁31和上壁32通过设置在电池单元2的两侧的侧壁33连接。如图4所表示的,板34和35是相连的,壳体3的下壁31、上壁32和侧壁33分别由板34、35的下壁341、351、上壁342、352和侧壁343、353并置而限定。壳体3还在每侧由端板34的横向壁344限定。此外,中间板35的侧壁353包括两个中央凹槽355,中央凹槽355具有向侧壁353中的每个侧壁353提供大致i形状的u型轮廓,中央凹槽355中的每个中央凹槽355面对相邻中间板35的中央凹槽355或形成在端板34中的一个端板34中的中央凹槽345。中央凹槽345和355构造成在壳体3的侧壁33中限定多个开口39,所述开口39允许电池单元2的电连接端子突出到壳体3外部,并且因此电连接至电动车辆的马达。
[0046]
如图4所示,壳体3的下壁31和上壁32中每一者被冷却通道4横穿,冷却剂lr能够沿着该冷却通道4流动。每个冷却通道4具体地从在端板34中的一个端板34的周缘处形成的入口孔口36延伸至在相对的端板34的周缘处形成的出口孔口37。每个冷却通道4将有利地构造成覆盖下壁31或上壁32的整个矩形表面。入口孔口36和出口孔口37分别允许冷却剂lr进入或离开壳体3的内部,并且入口孔口36和出口孔口37与对应的冷却通道4流体连通。因此,冷却剂lr将能够在壁31、32内部从入口孔口36至出口孔口37循环。为了避免冷却剂lr在壳体3的两个相邻板之间的接合部的位置处泄漏,有利地设置了与相邻板中的每个相邻板相互接合的密封件6。
[0047]
此外,如图2和图4所表示的,壳体3的下壁31和上壁32通过多个冷却板5连接,每个冷却板5设置在相邻电池单元2的两个模块2’之间或与至少一个电池单元2接触。这些冷却板5由塑料形成,并且将有利地与壳体3共挤塑。如图3所表示的,这些冷却板5被多个内部通
道53横穿,多个内部通道53从通向上壁32的冷却通道4的上端部52延伸至通向下壁31的冷却通道4的下端部51,从而允许冷却剂lr通过所述内部通道53从上壁32循环到下壁31。因此,由电池单元2产生的热将首先传递至冷却板5,然后直接传递至在所述冷却板5内循环的冷却剂lr,然后在壳体3的下壁31和上壁32内循环。
[0048]
参照图5,表示根据本发明的第二构型的电池组1’。该电池组1’包括多个电池单元2,为了简单起见,在图5中没有表示这些电池单元2,但是在图8和图9中可以看到这些电池单元2。与第一构型中一样,这些电池单元可以物理地组合成由泡沫壁8分开的两个或更多个电池单元2的模块。电池单元2设置在与图11表示的壳体大致相似的塑料材料的壳体3内。具体地,壳体3借助于螺钉7通过设置在壳体3的端部中的每个端部处的两个端板34和置于在所述端板34之间的多个中间板35的组件形成。所述板34、35大致具有长方体形状,并且各自包括分别为341和351的下壁和分别为342和352的上壁,所述下壁341、342和上壁351、352分别由侧壁343和353连接。板34、35的上壁342、352和下壁341、351分别有利地覆盖有防护板38和38’。端板34还包括横向壁344,横向壁344垂直于下壁341、上壁342和侧壁343。如图8所表示的,板34和35是相连的,壳体3的下壁31、上壁32和侧壁33分别由板34、35的下壁341、351、上壁342、352和侧壁343、353并置限定。壳体3还在每侧上由端板34的横向壁344界定。
[0049]
如图5、图9和图10所示,壳体3的下壁31和上壁32被单个冷却通道4横穿,冷却剂lr能够沿着该冷却通道4流动。具体地,冷却通道4从在端板34中的一个端板34的周缘处并且在其上部分中形成的入口孔口36延伸至在该相同端板34的周缘处并且在其下部分中形成的出口孔口37。冷却通道4特别是管状的,并且构造成在沿着端板34中的一个端板34竖向下降之前首先覆盖上壁32的整个矩形周缘,然后覆盖下壁31的整个矩形周缘。入口孔口36和出口孔口37分别允许冷却剂lr进入和离开壳体3内部并且入口孔口36和出口孔口37与所述冷却通道4流体连通。因此,冷却剂lr将能够在壁31、32内部从入口孔口36到出口孔口37循环。在图8表示的构型中,壳体3的下壁31和上壁32中的每一者被冷却通道4横穿。每个冷却通道4从在端板34中一个端板34的周缘处形成的入口孔口36延伸到在相对的端板34的周缘处形成的出口孔口37。每个冷却通道4特别是管状的,并且构造成覆盖下壁31或上壁32的整个矩形周缘。为了防止冷却剂lr在壳体3的两个相邻板之间的接合部处泄漏,有利地在两个相邻板之间的接合部处围绕冷却通道4设置管状密封件6。
[0050]
此外,如图5至图8所表示的,壳体3的下壁31和上壁32通过多个冷却板5’连接,每个冷却板5’固定到壳体3的板34、35中的一者,并且设置成与至少一个电池单元2接触。这些冷却板5’由具有高热导率的材料形成。该材料将有利地具有大于或等于20w.m
‑1.k
‑1的热导率。冷却板5’可以例如由铝或导热的塑料材料形成。然而,使用热导率小于20w.m
‑1.k
‑1的冷却板5’也是可能的。冷却板5’的热导率将根据它们的厚度而变化。
[0051]
在图6、图7a和图7b表示的构型中,冷却板5’是大致平坦的,并且在其端部与壳体3的板34、35包覆模制。因此,由电池单元2产生的热将首先传递至冷却板5’,然后通过壳体3的围绕冷却板5’的端部的部分间接传递至冷却剂lr。
[0052]
在图8表示的构型中,冷却板5’中的每个冷却板5’均是u形的,并且包括将上分支部52’连接到下分支部51’的基部53’。基部53’与至少一个电池单元2接触,并且分支部51’、52’中的每一者分别位于壳体3的下壁31、上壁32的冷却通道4中。在这种构型中,冷却板5’将有利地在其分支部51’、52’处胶合至壳体3的板34、35。因此,由电池单元2产生的热将首
先在它们的基部53’处传递至冷却板5’,然后在其分支部51’和52’的位置处直接传递至冷却剂lr。
[0053]
为了示出本发明的电池组相对于现有技术的电池组的优点,给出了以下比较示例。
[0054]
示例1:使用根据图1a和图1b中表示的构型的电池组。该电池组具有由长277mm、宽262mm、厚254mm限定的长方体形状。具体地,电池组包括24个软包型单元c(《软包电池》),这些单元c以12个由硅胶形成的泡沫板ps分开的两个单元的块的形式组合在一起,单元c设置在塑料壳体b内。壳体b搁置在支承件s上,冷却剂lr在支承件s内部循环。热传递借助于铝和l形传导板pc进行,每个板pc设置在两个相邻的单元块之间。每个单元c具有由长度227mm、宽度250mm和厚度10.5mm限定的长方体形状。每个单元c发出的热为10w。该电池组的各个组成元件的相应的热导率λ在下表1中给出:
[0055]
[表1]
[0056][0057]
参照图12,示出了表示根据冷却周期(以秒表示)的单元c的温度变化(以℃表示)的图。因此观察到的是,温度从45℃的初始温度逐渐升高到50.9℃的最终温度。这个最终温度太高,并且可能潜在地导致火灾风险,或者至少导致单元的严重劣化。
[0058]
示例2:使用根据图2至图4表示的构型的电池组。该电池组1具有由长度316mm、宽度330mm和厚度132mm限定的长方体形状。具体地,电池组1包括24个软包型单元2(《软包电池》),这些单元以12个由硅胶形成的泡沫板8分开的两个单元的块2’的形式组合在一起,单元2设置在塑料壳体3内,冷却剂lr在塑料壳体3内循环。热传递借助于塑料冷却板5进行,塑料冷却板5由多个内部通道53横穿,每个板5设置在相邻单元的两个块2’之间。每个单元2具有由长度100mm、宽度302mm和厚度11.7mm限定的长方体形状。由每个单元2释放的热为20w。该电池组的不同组成元件的相应的热导率λ在下表2中给出:
[0059]
[表2]
[0060][0061]
参照图13,示出了表示根据冷却周期(以秒表示)的单元c的温度变化(以℃表示)的图。由此观察到的是,温度从初始温度38.1℃略微下降到最终温度35.3℃。
[0062]
该相对较低的最终温度防止了单元劣化的发生,并确保了电池组的最佳运行。
[0063]
示例3:根据图5、图6和图7a、图7b中表示的构型使用电池组。该电池组1’具有由长度305mm、宽度330mm和厚度132mm限定的长方体形状。具体地,电池组1’包括24个软包型单
元2(《软包电池》),这些单元以12个由硅胶形成的泡沫板8分开的两个单元的块2’的形式组合在一起,单元2设置在由塑料材料hcpc制成的壳体3内,冷却剂lr在壳体3内循环。热传递借助于塑料材料hcpc的并且大致平坦形状的冷却板5’进行,每个板5设置在相邻单元的两个块2’之间。每个单元2具有由长度100mm、宽度302mm和厚度11.7mm限定的长方体形状。由每个电池单元2释放的热为20w。该电池组的不同组成元件的相应的热导率λ在下表3中给出:
[0064]
[表3]
[0065][0066]
参照图14,示出了表示根据冷却周期(以秒表示)的单元c的温度变化(以℃表示)的图。因此观察到的是,温度从38℃的初始温度略微升高到39.2℃的最终温度。这种相对较低的最终温度防止了单元劣化的发生,并确保了电池组的正常运行。
[0067]
示例4:根据图5和图8中表示的构型来使用电池组。该电池组1’具有由长度299mm、宽度330mm和厚度132mm限定的长方体形状。具体地,电池组1’包括24个软包型单元2(《软包电池》),这些电池组1’以12个由硅胶形成的泡沫板8分开的两个单元的块2’的形式组合在一起,单元2设置在由塑料材料制成的壳体3内,冷却剂lr在壳体3内循环。热传递借助于l型铝冷却板5’进行,每个板5设置在相邻单元的两个块2’之间。每个单元2具有由长度100mm、宽度302mm和厚度11.7mm限定的长方体形状。由每个单元2释放的热为20w。该电池单元的不同组成元件的相应的热导率λ在下表4中给出:
[0068]
[表4]
[0069][0070]
参照图15,表示了表示根据冷却周期(以秒表示)的单元c的温度变化(以℃表示)的图。因此观察到的是,温度从38℃的初始温度略微升高到40.9℃的最终温度。这种相对较低的最终温度防止了单元劣化的发生,并确保了电池组的正常运行。
再多了解一些
本文用于企业家、创业者技术爱好者查询,结果仅供参考。