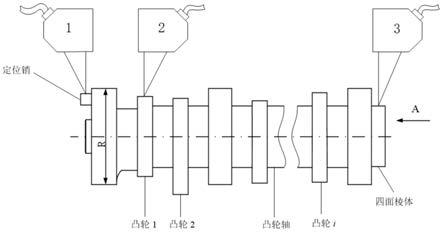
1.本发明涉及加工领域中轴类工件的测量方法,尤其涉及一种大型凸轮轴凸轮相位角及轮廓的非接触测量方法。
背景技术:
2.船用柴油机的凸轮轴是活塞发动机的部件,其作用是控制气门的开启和闭合,凸轮轴的主体是一根与气缸组长度近似相同的圆柱形棒体,上面有若干个轴颈以及轴颈间套有若干个凸轮,用于驱动气门。相位角误差是凸轮轴常见误差,相位角的作用是精准控制燃油机喷油嘴以及进气门与排气门的开合。相位角加工误差大,会严重影响燃油机的正常运转。因此,能否在加工现场快速准确地测量凸轮轴的相位角已成为提高加工质量的重要环节。而传统光学机械量仪、三坐标机测量仪器及样板测量效率极低且多数需要离线进行,无法适应当今高精高效规模化生产模式的需要。
3.因此,亟待解决上述问题。
技术实现要素:
4.发明目的:本发明的目的提供一种可避免加工工件损伤和检测仪器损耗,同时还可避免多次装夹所带来的定位误差的大型凸轮轴凸轮相位角及轮廓的非接触测量方法。
5.本发明公开了一种大型凸轮轴凸轮相位角及轮廓的非接触测量方法,包括如下步骤:
6.(1)、利用已知尺寸的四面棱体建立起凸轮轴上定位销以及各凸轮之间的旋转角度关系;
7.(2)、利用激光位移传感器对凸轮轴上定位销、凸轮以及四面棱体进行位移变化监测及数据采集;
8.(3)、对采集数据进行分析,识别并提取特征点的位移数据,基于角度传递、尺寸传递和几何原理,利用四面棱体的几何特征尺寸及其位移变化数据,求解出第三激光位移传感器的零点位置与轴心的相对位置;
9.(4)、根据几何原理,对特征点位移数据进行补偿修正,再求解所对应的相位角。
10.其中,所述步骤(1)的具体步骤包括:根据凸轮轴轴颈直径,设计相应的四面棱体;凸轮轴的一轴端具有定位销,该定位销为凸轮轴的定位基准,四面棱体同轴固定于凸轮轴的另一轴端或凸轮轴的任一轴段上,四面棱体的侧面为被测量表面;凸轮轴旋转时,定位销、每一凸轮与四面棱体沿着轴线同时进行刚性旋转,通过角度与尺寸传递,建立起凸轮轴上定位销以及各凸轮之间的旋转角度关系。
11.优选地,所述步骤(2)的具体步骤包括:使用激光位移传感器同时检测四面棱体与零件上的几何特征:使第一激光位移传感器正对定位销,并调整第一激光位移传感器的示值在合适范围;使第二激光位移传感器正对待测凸轮,并调整第二激光位移传感器的示值在合适范围;使第三激光位移传感器正对四面棱体,并调整第三激光位移传感器的示值在
合适范围;低速转动凸轮轴,使激光位移传感器可连续且同时采集四面棱体侧面及凸轮的特征表面在旋转过程中的位移变化量,则当第一激光位移传感器测到定位销最高点m时,同时第三激光位移传感器会测到四面棱体上的m1位置的位移数据;当第二激光位移传感器测到凸轮最高点n时,同时第三激光位移传感器会测到四面棱体的n1位置的位移数据。
12.再者,所述步骤(3)的具体步骤包括:首先分析四面棱体的位移数据,识别并提取出四面棱体侧面对应的最高点的位移数据x
a
,x
b
,x
c
,x
d
与最低点的位移数据x
e
,x
f
,x
g
,x
h
;四面棱体的长l
ab
和宽l
bc
是已知的,根据四面棱体的几何特征关系,可得公式(1):
[0013][0014]
解公式(1)可求得d和r0的值,第三激光位移传感器零点位置与旋转中心的距离r可以通过公式(2)求得:
[0015][0016]
进一步,所述步骤(4)的具体步骤包括:从四面棱体上的m1点到第三激光位移传感器测量的旋转中心o的距离ρ
m1
通过公式(3)求得:
[0017][0018]
以四面棱体上e点为0
°
起点,则获取与m1点相对应的旋转角度α
m1
,可由公式(4)求得:
[0019]
[0020]
与n1点相对应的距离ρ
n1
和旋转角度α
n1
,可由公式(5)求得:
[0021][0022]
那么四面棱体上的点m1与点n1之间的角度α,则可由公式(6)求得:
[0023]
α=|α
n1
‑
α
m1
|
ꢀꢀꢀꢀꢀꢀꢀꢀꢀꢀꢀꢀꢀꢀꢀꢀꢀꢀꢀꢀꢀꢀꢀꢀꢀꢀꢀ
(6)
[0024]
而与点m1与点n1对应时刻的定位销上的m点与凸轮上的n点之间的角度θ与角度α为:θ=α,则凸轮轴的相位角即为角度θ。
[0025]
优选地,还包括步骤(5)、最后反向定位轮廓特征数据,进行极坐标系下的轮廓拟合。
[0026]
再者,所述步骤(5)的具体步骤包括:最后通过凸轮轴轮廓设计升程要求,使用凸轮设计的理论升程角度α
s
和回程角度α
e
,代入公式(4)可以求得对应时刻四面棱体上点的理论位移值x'
ns
和x'
ne
,即公式(7):
[0027][0028]
依据理论位移值采用分割逼近法对实际测量的移数据进行反向定位,提取出凸轮上实际测量的位移值x
s
和x
e
;
[0029]
最后根据曲率或升程要求选择适当的角度间隔,定位与提取出凸轮上所需要的位移点,并计算出对应的角度,再在极坐标系下进行轮廓拟合。
[0030]
有益效果:与现有技术相比,本发明具有以下显著优点:
[0031]
(1)、本发明使高精度的加工精度检测过程直接在加工现场上进行,非接触测量避免了对加工工件的损伤和检测仪器的损耗,同时还避免多次装夹所带来的定位误差;
[0032]
(2)、本发明采用激光位移传感器以及四面棱体,建立起定位销及各凸轮在空间上的角度关系,可实现传感器的灵活安装与在线标定;并且仅利用位移数据,通过几何分析,求解出几何特征在不同空间平面上的相对位置,从而避免了用角速度求解时零件转速不稳定的影响;最后特征点定位大幅减少了数据处理量与处理时间,通过对凸轮轮廓起始与终止位置的反向定位及分割逼近特征点,使得轮廓拟合效率大幅提高并减小影响其拟合效果;
[0033]
(3)、相比于其他检测方法,本发明可靠性高、检测效率高且时间短,可实现对大尺寸轴类工件的在位非接触检测,且自由度高不依赖大量的固定夹具约束,并具有广泛的适用性。
附图说明
[0034]
图1为本发明中测量系统模型的结构示意图;
[0035]
图2为本发明a方向的示意图。
具体实施方式
[0036]
下面结合附图对本发明的技术方案作进一步说明。
[0037]
如图1和图2所示,一种大型凸轮轴凸轮相位角及轮廓的非接触测量方法,包括如下步骤:
[0038]
(1)、利用已知尺寸的四面棱体建立起凸轮轴上定位销以及各凸轮之间的旋转角度关系;具体步骤包括:根据凸轮轴轴颈直径,设计相应的四面棱体;凸轮轴的一轴端具有定位销,该定位销为凸轮轴的定位基准,四面棱体同轴固定于凸轮轴的另一轴端或凸轮轴的任一轴段上,四面棱体的侧面为被测量表面;凸轮轴旋转时,定位销、每一凸轮与四面棱体沿着轴线同时进行刚性旋转,通过角度与尺寸传递,建立起凸轮轴上定位销以及各凸轮之间的旋转角度关系;其中四面棱体应便于安装,四面棱体具有高精度、易于检测且几何特征明显;本发明以四面棱体为例进行阐述方法,但不限于仅使用四面棱体,可以是其他任意具有特征点、形状和角度的标定物;
[0039]
(2)、利用激光位移传感器对凸轮轴上定位销、凸轮以及四面棱体进行位移变化监测及数据采集;具体步骤包括:使用激光位移传感器同时检测四面棱体与零件上的几何特征:使第一激光位移传感器1正对定位销,并通过软件调整第一激光位移传感器1的示值在合适范围;使第二激光位移传感器2正对待测凸轮,并通过软件调整第二激光位移传感器2的示值在合适范围;使第三激光位移传感器3正对四面棱体,并通过软件调整第三激光位移传感器3的示值在合适范围;低速转动凸轮轴,打开测量软件中的数据采集并设置数据存储的存储量与采样周期等参数,使激光位移传感器可连续且同时采集四面棱体侧面及凸轮的特征表面在旋转过程中的位移变化量,,并可体现出多面棱体和零件的几何特征的触发位置,如最高点和最低点;则当第一激光位移传感器1测到定位销最高点m时,同时第三激光位移传感器3会测到四面棱体上的m1位置的位移数据;当第二激光位移传感器2测到凸轮最高
点n时,同时第三激光位移传感器3会测到四面棱体的n1位置的位移数据;
[0040]
(3)、对采集数据进行分析,识别并提取特征点的位移数据,基于角度传递、尺寸传递和几何原理,利用四面棱体的几何特征尺寸及其位移变化数据,求解出第三激光位移传感器的零点位置与轴心的相对位置,实现激光位移传感器的零点位置的同步校准;测量软件可对传感器数据进行采集,数据采集结束后可在测量软件中进行保存,也可以读出存储数据,对采集数据进行分析;具体步骤包括:首先在测量软件中分析四面棱体的位移数据,在软件界面中识别并提取出四面棱体侧面对应的最高点的位移数据x
a
,x
b
,x
c
,x
d
与最低点的位移数据x
e
,x
f
,x
g
,x
h
;四面棱体的长l
ab
和宽l
bc
是已知的,根据四面棱体的几何特征关系,可得公式(1):
[0041][0042]
解公式(1)可求得d和r0的值,第三激光位移传感器零点位置与旋转中心的距离r可以通过公式(2)求得:
[0043][0044]
(4)、根据几何原理,对特征点位移数据进行补偿修正,再求解所对应的相位角;即在软件界面中识别并提取出四面棱体侧面对应的最低点的位移数据,根据几何原理,可利用算法对最高点位移数据进行补偿修正,提高数据的精度;在软件界面中分别识别并提取出定位销与凸轮对应的最高点的位移数据,再通过相位角求解算法计算,得到所对应的相位角;具体步骤包括:从四面棱体上的m1点到第三激光位移传感器测量的旋转中心o的距离ρ
m1
通过公式(3)求得:
[0045][0046]
以四面棱体上e点为0
°
起点,则获取与m1点相对应的旋转角度α
m1
,可由公式(4)求得:
[0047][0048]
与n1点相对应的距离ρ
n1
和旋转角度α
n1
,可由公式(5)求得:
[0049]
[0050]
那么四面棱体上的点m1与点n1之间的角度α,则可由公式(6)求得:
[0051]
α=|α
n1
‑
α
m1
|
ꢀꢀꢀꢀꢀꢀꢀꢀꢀꢀꢀꢀꢀꢀꢀꢀꢀꢀꢀꢀꢀꢀꢀꢀꢀꢀꢀ
(6)
[0052]
而与点m1与点n1对应时刻的定位销上的m点与凸轮上的n点之间的角度θ与角度α为:θ=α,则凸轮轴的相位角即为角度θ。
[0053]
如图1和图2所示,一种大型凸轮轴凸轮相位角及轮廓的非接触测量方法,包括如下步骤:
[0054]
(1)、利用已知尺寸的四面棱体建立起凸轮轴上定位销以及各凸轮之间的旋转角度关系;具体步骤包括:根据凸轮轴轴颈直径,设计相应的四面棱体;凸轮轴的一轴端具有定位销,该定位销为凸轮轴的定位基准,四面棱体同轴固定于凸轮轴的另一轴端或凸轮轴的任一轴段上,四面棱体的侧面为被测量表面;凸轮轴旋转时,定位销、每一凸轮与四面棱体沿着轴线同时进行刚性旋转,通过角度与尺寸传递,建立起凸轮轴上定位销以及各凸轮之间的旋转角度关系;其中四面棱体应便于安装,四面棱体具有高精度、易于检测且几何特征明显;本发明以四面棱体为例进行阐述方法,但不限于仅使用四面棱体,可以是其他任意具有特征点、形状和角度的标定物;
[0055]
(2)、利用激光位移传感器对凸轮轴上定位销、凸轮以及四面棱体进行位移变化监测及数据采集;具体步骤包括:使用激光位移传感器同时检测四面棱体与零件上的几何特征:使第一激光位移传感器1正对定位销,并通过软件调整第一激光位移传感器1的示值在合适范围;使第二激光位移传感器2正对待测凸轮,并通过软件调整第二激光位移传感器2的示值在合适范围;使第三激光位移传感器3正对四面棱体,并通过软件调整第三激光位移传感器3的示值在合适范围;低速转动凸轮轴,打开测量软件中的数据采集并设置数据存储的存储量与采样周期等参数,使激光位移传感器可连续且同时采集四面棱体侧面及凸轮的特征表面在旋转过程中的位移变化量,,并可体现出多面棱体和零件的几何特征的触发位置,如最高点和最低点;则当第一激光位移传感器1测到定位销最高点m时,同时第三激光位移传感器3会测到四面棱体上的m1位置的位移数据;当第二激光位移传感器2测到凸轮最高点n时,同时第三激光位移传感器3会测到四面棱体的n1位置的位移数据;
[0056]
(3)、对采集数据进行分析,识别并提取特征点的位移数据,基于角度传递、尺寸传递和几何原理,利用四面棱体的几何特征尺寸及其位移变化数据,求解出第三激光位移传感器的零点位置与轴心的相对位置,实现激光位移传感器的零点位置的同步校准;测量软件可对传感器数据进行采集,数据采集结束后可在测量软件中进行保存,也可以读出存储数据,对采集数据进行分析;具体步骤包括:首先在测量软件中分析四面棱体的位移数据,在软件界面中识别并提取出四面棱体侧面对应的最高点的位移数据x
a
,x
b
,x
c
,x
d
与最低点的位移数据x
e
,x
f
,x
g
,x
h
;四面棱体的长l
ab
和宽l
bc
是已知的,根据四面棱体的几何特征关系,可得公式(1):
[0057][0058]
解公式(1)可求得d和r0的值,第三激光位移传感器零点位置与旋转中心的距离r可以通过公式(2)求得:
[0059]
[0060]
(4)、根据几何原理,对特征点位移数据进行补偿修正,再求解所对应的相位角;即在软件界面中识别并提取出四面棱体侧面对应的最低点的位移数据,根据几何原理,可利用算法对最高点位移数据进行补偿修正,提高数据的精度;在软件界面中分别识别并提取出定位销与凸轮对应的最高点的位移数据,再通过相位角求解算法计算,得到所对应的相位角;具体步骤包括:从四面棱体上的m1点到第三激光位移传感器测量的旋转中心o的距离ρ
m1
通过公式(3)求得:
[0061][0062]
以四面棱体上e点为0
°
起点,则获取与m1点相对应的旋转角度α
m1
,可由公式(4)求得:
[0063][0064]
与n1点相对应的距离ρ
n1
和旋转角度α
n1
,可由公式(5)求得:
[0065][0066]
那么四面棱体上的点m1与点n1之间的角度α,则可由公式(6)求得:
[0067]
α=|α
n1
‑
α
m1
|
ꢀꢀꢀꢀꢀꢀꢀꢀꢀꢀꢀꢀꢀꢀꢀꢀꢀꢀꢀꢀꢀꢀꢀꢀꢀꢀꢀ
(6)
[0068]
而与点m1与点n1对应时刻的定位销上的m点与凸轮上的n点之间的角度θ与角度α为:θ=α,则凸轮轴的相位角即为角度θ;
[0069]
(5)、最后反向定位轮廓特征数据,进行极坐标系下的轮廓拟合;具体步骤包括:最后通过凸轮轴轮廓设计升程要求,使用凸轮设计的理论升程角度α
s
和回程角度α
e
,代入公式(4)可以求得对应时刻四面棱体上点的理论位移值x'
ns
和x'
ne
,即公式(7):
[0070][0071]
依据理论位移值采用分割逼近法对实际测量的移数据进行反向定位,提取出凸轮上实际测量的位移值x
s
和x
e
;
[0072]
最后根据曲率或升程要求选择适当的角度间隔,定位与提取出凸轮上所需要的位移点,并计算出对应的角度,再在极坐标系下进行轮廓拟合。
再多了解一些
本文用于企业家、创业者技术爱好者查询,结果仅供参考。