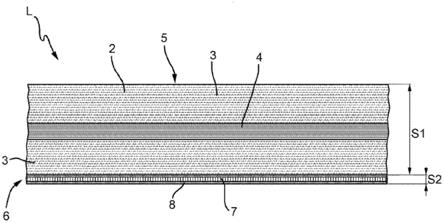
复合材料及其制备方法
1.相关申请的交叉引用
2.本专利申请要求于2018年12月20日提交的意大利专利申请no.102018000020521的优先权,其全部公开内容通过引用并入本文。
技术领域
3.本发明涉及一种复合材料,特别是用于航空应用的复合材料,以下描述将明确参考该复合材料,但不失一般性。
4.本发明还涉及一种用于生产上述复合材料的方法。
背景技术:
5.众所周知,复合材料用于各种工业部门,包括航空工业。特别地,通常称为“预浸渍”或“预浸料”的纤维增强复合材料是已知的,其通常由包含树脂基质和浸入基质中的增强纤维的半成品构成。纤维可以例如在单个方向上、在两个或更多个相互不同的方向上根据不同的构造布置,或者可以布置为形成织物。基质用于在生产期间将纤维彼此固定并且可能固定到其他部件。
6.预浸料通常以带的形式制备并卷绕成卷;为了实现所需的机械性能,预浸料必须通过加热并且还通常在压力下经受固结工艺。
7.主要用于航空工业的预浸料可以具有热固性材料或热塑性材料的基质。
8.在第一种情况下(热固性材料),基质由聚合物构成,该聚合物在适当的温度条件下和/或在某些物质的存在下转化为刚性、不溶性和不熔性材料。这种转化发生在交联反应(称为固化的工艺,通过该工艺,聚合物链经历在反应性官能团水平下在不同链之间产生键的反应)之后,该交联反应发生在聚合物链之间,形成强(共价或离子)键。
9.在聚合之前,热固性材料具有粘性的特性。因此,这些材料可用于通过将不同的层以一个放置在另一个的顶部的方式来产生层状结构,其中不同层具有适当的顺序或取向。然后使分层经受温度和压力循环(在真空袋中和在高压釜中,使用烘箱、模压机等),其使材料聚合,提高分子量并感应大分子之间形成键(交联),从而将其转化为具有适合于其预期应用的结构特征和机械性能的材料。
10.一些热固性聚合物仅通过加热或通过压力和加热的组合交联,而其他热固性聚合物可以在室温下通过化学反应交联(冷交联)。
11.分层可以用自动化方法完成,这在成本、生产率和重复性方面提供了显著的优点。对于平坦或适度弯曲的分层,使用自动带铺设(atl)装置。最近,允许使用相当小宽度的预浸料带(称为狭缝)在弯曲或甚至封闭(圆柱形)表面上分层的技术已经变得流行;这种技术被称为纤维放置(fp)。
12.在第二种情况下(热塑性材料),基质树脂具有高分子量,因此,一方面,它不需要经历聚合循环,另一方面,不具有粘性特性。
13.在第一种近似中,可以认为热塑性基质预浸料是由单个薄片形成的最终状态的制
造产品。为了能够形成层压材料,必须对其进行加热以引起其组成薄片或热塑性预浸料层的至少接触表面的熔化,在压力下将其压缩,然后使其冷却。熔融达到的温度是无定形热塑性塑料的玻璃化转变温度t
g
,和半结晶热塑性塑料的熔点温度t
f
。
14.目前,自动铺带(atl)和纤维铺放(fp)的技术仅用于具有热固性基质的复合部件。这些也是用于热塑性基质预浸料的概念上可能的技术,但具有一些额外的技术要求;事实上,在这种情况下,用于生产基于热塑性预浸料的层压件的设备还必须提供热量以达到一定温度(取决于材料,该温度可能过高),以便熔化树脂并因此获得将构成层压件的各层之间的粘附;此外,对于半结晶热塑性塑料,过快的冷却可能导致部件的非晶化,从而导致性能特性的损失。作为补偿,如果解决了这些问题,则atl和fp技术将能够在没有进一步的高压釜处理的情况下实现成品部件,同时显著降低部件的生产成本。
15.如前所述,预浸料的固结和结合形成最终部件的各种预浸料层的工艺通常在高压釜、烘箱或模塑机中进行。在非常大的部件的情况下,例如航空部门、海军部门等中的结构部件,已知的固结和结合工艺过于昂贵并且可能产生许多不期望的约束。
16.因此,需要开发允许实现复合材料中的部件的原位固结和结合的技术,特别是当这些部件非常大时。
17.用于具有热塑性基质的复合材料的最有希望的技术之一是通过电磁感应的固结和结合,其与其他技术(例如胶合)不同,不使用填充材料,而是仅待结合的两个部分(也称为粘附体)的两个边缘的重叠保持彼此接触,其中至少一个部分是导电的。
18.根据该技术,电感器(例如线圈)产生可变电磁场,该可变电磁场进而在待结合的粘附体(其中至少一个粘附体是导电的)的区域中引起寄生电流的感应;通过焦耳效应,这些寄生电流加热粘附体的基质,使其达到熔点或软化点;然后,当粘附体达到认为理想的温度时,可以施加机械压力(称为固结压力),其适于感应粘附体的粘附。
19.在传统的感应结合系统中,考虑到与距电感器的距离的平方相关的依赖性,由于寄生电流引起的加热作用倾向于集中在直接暴露于电感器的表面上。因此,产生了陡峭的温度梯度,这导致基质的表面熔化而不是粘附体的粘附区域的表面熔化:这对由此获得的结合的质量和机械特性产生负面影响。
20.此外,该温度梯度在厚度方向上的方向导致面向电感器的表面的最高温度和结合表面的最低温度。因此,为了在粘附体的粘附表面上达到理想温度,最外区域中的温度将过高,这可能导致复合材料基质的劣化。因此,该梯度的存在非常显著地限制了粘附体的可能厚度。
21.类似地,在待结合的部件的边缘上存在大的电流集中,因此在其上形成通常不可接受的温度梯度,这可能再次导致材料的劣化。
22.在任何情况下,粘附表面上达到的温度(通常为60
‑
70℃)相对于形成结合体所需的温度(约350℃)太低。
23.最终,通过电磁感应的复合材料的原位固结和结合技术的主要缺点在于难以优化通过结合体的厚度的温度分布。
技术实现要素:
24.本发明的一个目的是生产能够克服上述缺点的复合材料。
25.根据本发明,提供了一种复合材料,特别是用于航空应用的复合材料,如权利要求1及其从属权利要求所述。
26.本发明还涉及如权利要求10和11所述的用于生产上述复合材料的方法。
附图说明
27.现将通过以下附图描述本发明:
28.参考附图,附图示出了两个不同的非限制性实施例,其中:
29.‑
图1示出了待结合以形成根据本发明的复合材料薄片的第一实施例的两层起始材料的示意性透视图;
30.‑
图2示出了沿图1的线ii
‑
ii的高度放大的截面示意图;
31.‑
图3是类似于图2的截面示意图,并且表示通过结合图1和图2的两层起始材料获得的复合材料薄层;
32.‑
图4是示出了图3所示类型的复合材料的两个薄片的结合操作的可能实施方式的布局的透视图;
33.‑
图5示出了沿图4的线v
‑
v的高度放大的截面示意图;
34.‑
图6是使用显微镜获得的图4和图5所示的结合在一起的两层复合材料的一部分的照片;
35.‑
图7示出了图6的高度放大的细节;
36.‑
图8示出了在图4中的结合操作期间,在图4至图7的复合材料的两个薄片之间的结合界面处可获得的温度
‑
时间图;
37.‑
图9示出了在已知类型的复合材料的两个薄片之间的结合界面处可获得的温度
‑
时间图;
38.‑
图10示出了直方图,其中比较了根据本发明的复合材料薄片和不同类型的复合材料薄片的弹性模量;
39.‑
图11示出了直方图,其中比较了根据本发明的复合材料的薄片和不同类型的复合材料的薄片所计算的拉伸强度;
40.‑
图12示出了与图10相同的直方图,其中针对不同复合材料薄片计算的弹性模量之一被设置为1;
41.‑
图13示出了与图11相同的直方图,其中针对不同复合材料薄片计算的拉伸强度之一被设置为1;
42.‑
图14示出了比较不同薄片的厚度的直方图,针对该薄片已经在图10至13的直方图中计算了弹性模量和拉伸强度的值;
43.‑
图15是类似于图2的图,并且以高度放大的比例示出了两层起始材料的示意性截面图,所述两层起始材料旨在被结合以形成根据本发明的复合材料薄片的第二实施例;以及
44.‑
图16是类似于图3的截面示意图,并且示出了从图15的两层起始材料的结合获得的复合材料薄片。
具体实施方式
45.图1至图3示意性地示出了根据本发明生产的复合材料薄片l(特别是设计用于航空应用)的第一实施例。
46.复合材料薄片l包括第一预浸渍层2,其具有树脂基基质3,该树脂基基质3用纤维4或纤维材料增强以赋予层2预定的机械性能。
47.应当注意的是,表述“基”或“基于”意味着除了树脂,基质3还包含常用的添加剂,例如填料、稳定剂等。
48.基质3优选地基于具有预定熔点t
f
的半结晶热塑性树脂。该半结晶热塑性树脂是例如聚醚醚酮或peek,其具有约340℃的熔点温度t
f
。在替代方案中,该半结晶热塑性树脂可以例如是聚醚酮酮或pekk,其具有约370℃的熔点温度t
f
。
49.基质3还可以基于具有预定玻璃化转变温度t
g
的无定形热塑性树脂。该无定形热塑性树脂是例如聚醚酰亚胺或pei,其具有约215℃的玻璃化转变温度。
50.根据未示出的可能的替代方案,层2的基质也可以基于热固性树脂,例如环氧树脂、bmi(双马来酰亚胺)或酚醛树脂。
51.纤维4优选地是碳纤维,并且可以布置在一个或多个单向层中,在具有彼此不同取向的多个层中,或类似织物。
52.碳纤维4具有优选地包括在100g/m2与300g/m2之间的面积重量。
53.优选地,层2的纤维4是单向的;特别地,单向纤维4用于单向地增强薄片l的受应力部分,沿着载荷路径对其进行布置。
54.在替代方案中,航空领域中已知的其他类型的纤维(例如玻璃纤维或玻璃和碳纤维的组合)可以用于层2。
55.纤维4优选地是连续的或者可以具有包括在1mm与40cm之间的长度。
56.如图1和图2中可见,层2由彼此平行的相应相对面5界定;层2在与面5正交的方向上具有厚度s1,其相对于面5的尺寸(长度和宽度)较小。
57.复合材料薄片l还包括磁场增强材料的第二层6,其叠加并接合到层2的面5中的一个;导电纤维7在具有不同取向并且平行于面5的至少两个方向上分散在层6中,导电纤维7具有小于600μωm、优选地小于200μωm并且甚至更优选地小于100μωm的等效电阻率,以便于通过电磁感应进行局部加热。
58.对于复合材料的等效电阻率(等效电导率的倒数)的重要性和计算,可以参考例如以下出版物:
[0059]“calculation of an equivalent electrical conductivity tensor for multidirectional carbon fiber reinforced materials”,2012年8月19日,作者n.athanasopoulos和v.kostopoulos。
[0060]
在所示的示例中,层6包括基于半结晶热塑性树脂的基质8,该半结晶热塑性树脂与层2的基质3的树脂相同或与后者相容,纤维7分散在其中。更具体地,纤维7是碳纤维并且在多个方向上以随机方式布置在基质8中,其中一些方向平行于面5延伸,而另一些方向横向于面5延伸。
[0061]
横向于面5延伸的纤维7具有大于2,000μωm的等效电阻率。
[0062]
碳纤维7具有包括在10g/m2与100g/m2之间的面积重量。
[0063]
碳纤维7优选通过聚丙烯腈(pan)的氧化和热解获得。
[0064]
或者,碳纤维7可以通过蒸馏碳基材料(例如植物、原料油和碳(pitch))获得;在这种情况下,粘弹性材料由芳烃组成。
[0065]
纤维7也可以由另一种导电材料(例如金属材料)制成。
[0066]
纤维7优选地是连续的或者可以具有包括在1mm与40cm之间的长度。
[0067]
有利地,层6呈遮蔽物或膜的形式,并且在与面5正交的方向上具有在层2的厚度s1的1/10与1/100之间的厚度s2。
[0068]
层2和层6通过压缩模制并且优选地通过连续压缩模制结合。这种结合可以在热压机(已知且未示出)中以已知的方式进行,或者通过使待结合的层2和6在连续层压状工艺中在相应的热辊对(已知且未示出)之间通过来进行。层2和6的结合工艺发生的温度取决于所使用的热塑性基质的种类;在半结晶热塑性基质的情况下,其高于熔点t
f
,而在无定形热塑性基质的情况下,其高于玻璃化转变温度t
g
。
[0069]
图4示意性地示出了实现复合材料的两个薄片l的结合操作的基本装置。
[0070]
在该操作期间,电感器11(已知且仅示意性地示出),例如电线圈,被馈送电流,以便产生可变电磁场e(其磁通线在图4中由虚线示意性地示出)。
[0071]
同时,新的薄片l逐渐铺设在布置在支撑表面12上的另一个已经存在的薄片l上,或者可替代地,铺设在布置在支撑表面12上的一系列已经接合或结合的薄片l的上薄片l上。
[0072]
铺设新薄片l的步骤由围绕轴线a旋转并且平行于支撑表面12前进的一个或多个辊13(图4中仅示出其中一个)执行,该一个或多个辊13具有平行于该一个或多个辊13在其上操作的薄片l的轴线a。
[0073]
电磁场e基本上在新的薄片l的层6中感应寄生电流,然后新的薄片l的层6接合到位于支撑表面12上的其他薄片l。
[0074]
由于层6的纤维7是导电的并且在至少两个不同的方向上分散在基质8中,因此至少在新的薄片l的层6内部产生实际的“电路”,其通过焦耳效应加热层6的基质8和相邻的薄片l。
[0075]
局部加热是非常有效的,并且使得能够局部地(即在层6中和在与该层相邻的基质3的区域中)达到超过熔点温度t
f
或玻璃化转变温度t
g
的温度。
[0076]
相反,在基质3的最远离层6的区域中,温度明显保持低于形成这些基质3的树脂的熔点温度t
f
。
[0077]
一个或多个辊13的通过在待结合到布置在支撑表面12的表面上的其他薄片l的新薄片l中寄生电流的感应之后发生。
[0078]
以这种方式,在电磁感应之后在薄片l之间的界面处获得的软化之后并且在这些区域的冷却期间,压力逐渐施加在薄片l的待结合区域上。
[0079]
优选地,一个或多个辊13保持冷却,以便在结合步骤中逐渐从薄片l中去除残余热量。
[0080]
在结合操作结束时,结果如图5所示。
[0081]
图6和图7示出了薄片l的结合区域的显微镜图像,每个结合区域通过以下形成:
[0082]
‑
具有单向碳纤维4的pekk层2,其面积重量为200g/m2;以及
[0083]
‑
遮蔽物层6,其具有pekk中的基质8和在所有方向上以随机方式分散的面积重量为8g/m2的碳纤维7。
[0084]
可以看出,纤维7在层6的基质8中具有基本上各向同性的分布,其中一些纤维7相对于层2的面5横向定向。这使得能够实现结合材料的高电阻/韧性。
[0085]
图8和图9示出了两个温度/时间图,其在通过电磁感应的结合操作期间比较以下薄片的行为:
[0086]
‑
根据本发明的复合材料的两个薄片l;以及
[0087]
‑
两个已知类型的复合材料薄片。
[0088]
特别地,图8的图涉及两个薄片l,每个薄片l由以下形成:
[0089]
‑
具有面积重量为200g/m2的单向碳纤维的pekk层2;以及
[0090]
‑
具有pekk中的基质8和碳纤维7的遮蔽物层6,其具有在所有方向上以随机方式分散的8g/m2的面积重量。
[0091]
相反,图9中的图涉及已知类型的复合材料的两个薄片,其具有pekk中的基质和具有200g/m2的面积重量的单向碳纤维。
[0092]
如可以观察到的,在第一种情况下(图8),在几十秒(25
‑
30秒)内达到接近400℃的温度。
[0093]
在第二种情况下(图9),达到的最高温度低于60℃。
[0094]
申请人已经观察到,由于采用在层2的厚度的1/10和1/100之间的层6的厚度,一方面可以在薄片l中实现由层2确定的机械性能的基本保留,另一方面可以通过电磁感应非常容易地原位固结和结合材料。
[0095]
图10至图14示出了申请人在比较以下类型的薄片时在机械性能和厚度方面获得的实验结果:
[0096]
‑
单向pekk/碳薄片(apc(pekk
‑
fc)
‑
as4(wm%=34%,每平方米的面积重量或克数=145g/m2),下文称为ud并且对应于不形成本发明的一部分并且仅由层2构成的薄片的实例;
[0097]
‑
通过将先前的ud薄片(层2)与面积重量为4g/m2的遮蔽层6联接而获得的根据本发明的薄片(下文称为ud/veil_4);
[0098]
‑
通过将先前的ud薄片(层2)与面积重量为8g/m2的遮蔽层6联接而获得的根据本发明的薄片(下文称为ud/veil_8);
[0099]
‑
薄片,其不形成本发明的一部分并且通过将先前的ud薄片(层2)与面积重量为34g/m2的遮蔽层6联接而获得(下文称为ud/veil_34);以及
[0100]
‑
不形成本发明的一部分并且通过将先前的ud薄片(层2)与面积重量为145g/m2的垫层6联接而获得的薄片(下文称为ud/mat_145)。
[0101]
上述遮蔽物和垫具有半结晶热塑性树脂基基质,其与ud薄片的基质的树脂相同。
[0102]
上述遮蔽物和垫的浸渍水平为34重量%。
[0103]
在上述遮蔽物和垫中使用的纤维是碳纤维,并且在所有方向上以随机方式布置在相应的基质中。
[0104]
根据弹性模量e和拉伸强度σ确定了上述不同类型薄片的机械性能;两个量都是在平行于层2或ud薄片中的单向纤维的方向上计算的。
[0105]
所考虑的不同薄片的厚度是在与薄片正交的方向上计算的,并列于下表中:
[0106]
相反,下表列出了对上述薄片计算的弹性模量e和拉伸强度σ的值。
[0107]
薄片弹性模量e(gpa)拉伸强度σ(mpa)ud134.4642304ud/veil_4132.1462255ud/veil_8129.7532192ud/veil_34114.1521870ud/mat_14579.661152
[0108]
该表的结果在图10和图11中总结为直方图,并且在图12和图13中以归一化形式总结为直方图。
[0109]
特别地,如从前面的表以及从图10和图11两者可以观察到的,在层6的厚度等于层2的厚度的23%的情况下,机械性质的劣化开始变得明显,并且在两个层2、6具有相同厚度的情况下变得非常明显。
[0110]
图12和13的柱状图涉及图10和11中所示的相同结果,但是其中ud薄片的弹性模量e和拉伸强度σ用作与针对其他类型的薄片计算的相应量的值的比率中的分母。
[0111]
图14示出了不同类型的薄片的厚度与作为参考的ud薄片的厚度之间的比率。
[0112]
图15和16示出了根据本发明的不同实施例生产的复合材料薄片,其整体由l'表示;下面将仅就薄片l'如何不同于薄片l来描述薄片l',在可能的情况下,示出与已经用相同附图标记描述的部分相同、对应或等同的部分。
[0113]
特别地,复合材料的薄片l'与薄片l的不同之处基本上在于其包括没有树脂基质的磁场增强层6'。
[0114]
更详细地,层6'可以是碳遮蔽物,其中纤维7在具有不同取向的至少两个方向上延伸,优选地在至少三个方向上延伸,其中一个方向横向于层2的面5;在这种情况下,纤维7通过粘合剂或结合剂(例如pva(聚乙烯醇)或与层2的基质3化学相容的其他物质)保持在一起以形成遮蔽物。
[0115]
可替代地,层6'可以是具有在具有不同取向的至少两个方向上延伸的纤维7的织物。
[0116]
根据另一替代方案,层6'可以是无纺织物,例如类型的无纺织物。
[0117]
通过对根据本发明的原理生产的复合材料的特性的检查,由此可以实现的优点是显而易见的。
[0118]
特别地,如前所述,由于层6、6'的纤维7是导电的并且在具有不同取向的至少两个
方向上布置,因此可以通过至少层6、6'内部的电磁感应产生实际的“电路”;这些电路的产生使得能够通过焦耳效应实现层6、6'和相邻树脂基质3的有效加热,从而精确地在两个不同薄片l、l'的结合界面处达到树脂的熔点温度t
f
。
[0119]
实际上,在上述界面处达到树脂的熔点温度t
f
不需要在树脂的最靠近电感器11的区域产生甚至更高的温度,从而可能导致复合材料的基质的劣化。
[0120]
如图8和图9所示,在通过电磁感应进行原位固结和结合的操作期间,根据本发明的两个薄片l、l'之间的结合界面处达到的温度比已知类型的复合材料的情况下达到的温度高至少7倍。
[0121]
正是由于上述原因,申请人还测量了根据本发明的两个薄片l、l'之间的结合速度比传统预浸料的结合速度高十倍。
[0122]
由于层6、6'的厚度s2在层2的厚度s1的1/10和1/100之间,因此实际上实现了根据本发明的材料的容易的原位固结和结合,而不会由于层2的碳纤维的定向和布置而损害赋予薄片l、l'的机械性能。最后,清楚的是,在不脱离权利要求中限定的范围的情况下,可以对本文所述的复合材料以及生产该复合材料的方法进行修改和变型。
再多了解一些
本文用于企业家、创业者技术爱好者查询,结果仅供参考。