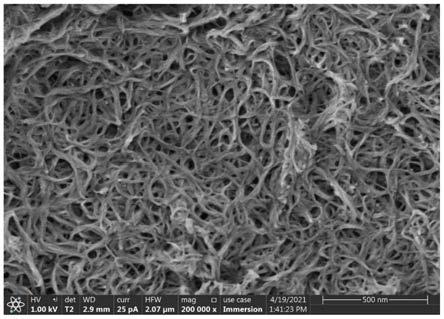
1.本发明涉及复合材料领域,尤其涉及一种对位芳纶纳米纤维复合增强水性聚氨酯复合材料及其制备方法。
背景技术:
2.芳纶纳米纤维具有特殊的分子结构,继承并超越了宏观ppta纤维的良好性能。具有芳纶纤维基本特性以外,其直径在10
‑
100nm之间,长径比在3000左右,具有尺寸小、比表面积大、表面能高、分散性好,保水率高,阻燃性能优异等特点,对位芳纶纳米纤维具备芳纶纤维优异的本体性能和纳米纤维纳米效应的双重优势,成为一种新颖的纳米构筑基元,可有效解决芳纶纤维化学惰性高、反应活性低和界面复合效果不理想的难题,而且易于分散,便于和其他材料复合,是很优秀的增强材料。
3.水性聚氨酯由于其拉伸性能较差以及较差的耐磨性、力学性,在实际应用中性能仍需要提高。研究发现,纳米粒子的加入能同时实现聚氨酯的增强和增韧,但同时也发现了纳米粒子与其间界面相容性较差的问题。
技术实现要素:
4.本发明针对现有聚氨酯复合材料增强改性会降低聚氨酯韧性以及复合物质与聚氨酯界面相容性差的问题,提供一种对位芳纶纳米纤维复合增强水性聚氨酯复合材料及其制备方法。本发明中将对位芳纶纳米纤维利用剪切分散法制备分散液并将其与水性聚氨酯混合,该方法下材料共混效果好,所得复合材料综合性能好且性能稳定,不会出现界面滑移现象。
5.本发明的技术方案为:
6.(1)制备对位芳纶纳米纤维分散液:将对位芳纶纳米纤维加入一定量的去离子水于高剪切均质乳化机内分散均匀,配置成质量浓度为2
‰
ωt~5
‰
ωt的对位芳纶纳米纤维分散液;
7.其中,对位芳纶纳米纤维优选采用cn106750265 a、cn105153413 a公开的制备方法制备。
8.(2)制备对位芳纶纳米纤维水性聚氨酯复合材料:将配置好的对位芳纶纳米纤维分散液与水性聚氨酯按比例混合,在室温下进行机械搅拌15
‑
30min(500r/min),再超声震荡10
‑
30min,制得混合溶液,将混合溶液干燥处理,制得对位芳纶纳米纤维复合增强水性聚氨酯复合材料。
9.步骤(1)中对位芳纶纳米纤维直径在10~100nm之间,长径比在300~3000。
10.步骤(1)中所述对位芳纶纳米纤维分散液为2
‰
ωt
‑5‰
ωt。
11.所述对位芳纶纳米纤维与水性聚氨酯质量比(按照绝干重量计)为(0.1
‑
1):100,添加较多对位芳纶纳米纤维会导致溶液流动性较差,成膜不均匀,同时影响分散性,其中最
佳的比例为0.7:100
12.步骤(2)中所述干燥方式优选为真空干燥,温度在30
‑
80℃,时间12
‑
48h。固化温度与时间直接影响复合材料性能,温度过高、时间过长导致复合材料变脆,易产生气泡,温度过低固化效果不好,导致复合材料性能缺陷。
13.本发明所采用的对位芳纶纳米纤维可根据cn106750265a、cn105153413a公开的制备方法制备得到。
14.本发明的有益效果是:常规的短纤维与水性聚氨酯混合后只能在物理空间上给与一定的力学支持,而本发明采用对位芳纶纳米纤维作为增强材料添加到水性聚氨酯基体中,线性的芳纶纳米纤维对水性聚氨酯基体形成氢键的同时会和水性聚氨酯大分子相互缠结,增强体系的强度,与纯水性聚氨酯膜力学性能相比,本发明所得水性聚氨酯复合材料的杨氏模量、拉伸强度和断裂伸长率均得到大幅提高;与颗粒状的其他纳米粒子相比,芳纶纳米纤维呈线性,与水性聚氨酯基体相容性好,不存在界面力学性能下降的情况。本发明工艺简单,反应条件温和,时间短,易控制,制备效率高。所制备的复合材料力学性能优异,非常适宜作为涂料及各种耐磨领域广泛应用。
附图说明
15.图1为实施例2纳米纤维分散液扫描电镜图片;
16.图2为复合材料对比图,从左到右分别为纯聚氨酯、实施例2材料、实施例3材料。
具体实施方式
17.以下通过实施例形式的具体实施方式,对本发明的上述内容做进一步的详细说明,但不应将此理解为本发明上述主题的范围仅限于以下的实例。凡基于本发明上述内容所实现的技术均属于本发明的范围。除特殊说明外,以下实施例中均采用常规技术操作完成。
18.所述聚氨酯为黄河三角洲京博化工研究院精化所生产j
‑
157型号,但并不只限定于该种聚氨酯。
19.实施例1
20.1)制备对位芳纶纳米纤维分散液:将对位芳纶纳米纤维(直径在10nm左右,长径比为3000左右)加入去离子水,于高剪切均质乳化机内分散均匀,配置成浓度为2
‰
ωt的分散液;
21.2)制备对位芳纶纳米纤维水性聚氨酯复合材料:将配置浓度为2
‰
ωt的芳纶纳米纤维分散液与50g水性聚氨酯(固含量为30%ωt)按比例0.2:100混合,在室温下进行机械搅拌15min(500r/min),再超声震荡15min,制得混合溶液,将混合溶液导入聚四氟乙烯浅平板中,放入真空干燥箱60℃干燥24h,制得芳纶纳米纤维水性聚氨酯复合材料。
22.实施例2
23.1)制备对位芳纶纳米纤维分散液:将对位芳纶纳米纤维(直径在30nm左右,长径比为1000左右)加入去离子水,于高剪切均质乳化机内分散均匀,配置成浓度为2
‰
ωt的分散液;
24.2)制备对位芳纶纳米纤维水性聚氨酯复合材料:将配置浓度为2
‰
ωt的芳纶纳米
纤维分散液与50g(固含量为30%ωt)水性聚氨酯(wpu)按比例0.5:100混合,在室温下进行机械搅拌20min(500r/min),再超声震荡15min,制得混合溶液,将混合溶液导入聚四氟乙烯浅平板中,放入真空干燥箱60℃干燥24h,制得芳纶纳米纤维水性聚氨酯复合材料。
25.实施例3
26.1)制备对位芳纶纳米纤维分散液:将对位芳纶纳米纤维(直径在30nm左右,长径比为1000左右)加入去离子水,于高剪切均质乳化机内分散均匀,配置成浓度为2
‰
ωt的分散液;
27.2)制备对位芳纶纳米纤维水性聚氨酯复合材料:将配置浓度为2
‰
ωt的芳纶纳米纤维分散液与50g(固含量为30%ωt)水性聚氨酯(wpu)按比例0.5:100混合,在室温下进行机械搅拌20min(500r/min),再超声震荡15min,制得混合溶液,将混合溶液导入聚四氟乙烯浅平板中,放入真空干燥箱45℃干燥48h,制得芳纶纳米纤维水性聚氨酯复合材料。
28.实施例4
29.1)制备对位芳纶纳米纤维分散液:将对位芳纶纳米纤维(直径在100nm左右,长径比为300左右)加入去离子水,于高剪切均质乳化机内分散均匀,配置成浓度为5
‰
ωt的分散液;
30.2)制备对位芳纶纳米纤维水性聚氨酯复合材料:将配置浓度为5
‰
ωt的芳纶纳米纤维分散液与50g(固含量为30%ωt)水性聚氨酯(wpu)按比例0.7:100混合,在室温下进行机械搅拌25min(500r/min),再超声震荡15min,制得混合溶液,将混合溶液导入聚四氟乙烯浅平板中,放入真空干燥箱45℃干燥12h,制得芳纶纳米纤维水性聚氨酯复合材料。
31.实施例5
32.1)制备对位芳纶纳米纤维分散液:将对位芳纶纳米纤维(直径在100nm左右,长径比为300左右)加入去离子水,于高剪切均质乳化机内分散均匀,配置成浓度为5
‰
ωt的分散液;
33.2)制备对位芳纶纳米纤维水性聚氨酯复合材料:将配置浓度为2
‰
ωt的芳纶纳米纤维分散液与50g(固含量为30%ωt)水性聚氨酯(wpu)按比例1:100混合,在室温下进行机械搅拌30min(500r/min),再超声震荡15min,制得混合溶液,将混合溶液导入聚四氟乙烯浅平板中,放入真空干燥箱30℃干燥48h,制得芳纶纳米纤维水性聚氨酯复合材料。
34.对比例1
35.将配置浓度为5
‰
ωt的对位芳纶短纤维(2mm)分散液与50g(固含量为30%ωt)水性聚氨酯(wpu)按比例0.5:100混合,在室温下进行机械搅拌30min(500r/min),再超声震荡15min,制得混合溶液,将混合溶液导入聚四氟乙烯浅平板中,放入真空干燥箱60℃干燥24h,制得对位芳纶短纤维水性聚氨酯复合材料。
36.对比例2
37.将配置浓度为5
‰
ωt的对位芳纶短纤维(5mm)分散液与50g(固含量为30%ωt)水性聚氨酯(wpu)按比例0.5:100混合,在室温下进行机械搅拌30min(500r/min),再超声震荡15min,制得混合溶液,将混合溶液导入聚四氟乙烯浅平板中,放入真空干燥箱60℃干燥24h,制得对位芳纶短纤维水性聚氨酯复合材料。
38.将实施例1
‑
5所得芳纶纳米纤维水性聚氨酯复合材料膜和及对比例1
‑
2所得芳纶短纤维水性聚氨酯复合材料及纯聚氨酯膜(wpu)分别裁剪成哑铃状样条(国标哑铃型,规格
是长11.5cm夹具宽度2.5cm)通过万能电子拉力机进行相关力学性能分析,如表1和表2所示。
39.表1.膜力学性能对比
[0040][0041]
表2.复合材料膜相较纯聚氨酯膜力学性能增率
[0042][0043]
通过上述数据,可知复合材料膜的杨氏模量、拉伸强度及断裂伸长率与纯聚氨酯膜相比都得到了很大提高,其中断裂伸长率最大增率为36.1%,杨氏模量最大增率为79.1%,而拉伸强度增强效果最为显著,最大增率可达到88.2%;但对比例1和2以对位芳纶短纤维与聚氨酯配比得到的复合材料膜,其力学性能并没有得到改进,反而其拉伸强度及断裂伸长率均有所下降。也就是说,常规的芳纶纤维并不能对聚氨酯起到力学性能增效效果,只有本发明所述的对位芳纶纳米纤维才能获得相应的技术效果。
[0044]
以上所述仅为本发明的较佳实施例,并不用以限制本发明,凡在本发明的精神和原则之内,所作的任何修改、等同替换、改进等,均应包含在本发明的保护范围之内。
再多了解一些
本文用于企业家、创业者技术爱好者查询,结果仅供参考。